Simply put, construction projects can’t be completed on time, within budget, and to the client’s satisfaction without efficient project management.
This includes properly planning, scheduling, and managing the resources—labor, equipment, and materials—needed for successful project completion.
In other words, the efficient management of equipment is a critical part of streamlined project management.
Therefore, there are many reasons for scheduling your construction project equipment in advance.
Here are five of them.
In this article...
Improving Project Estimates
In essence, scheduling equipment ahead of time helps contractors and project managers determine what items will be needed for a specific construction project.
It helps them assess how much of the equipment will be required, when and how long, and at what project stage.
This knowledge allows decision-makers to compare their equipment scheduling with previous projects of similar scope and identify constraints, interdependencies, and risks associated with equipment management throughout the project lifecycle.
All the above enables project managers to create a more accurate budget and schedule estimates for their projects, better allocate equipment and make adjustments on the go, thus avoiding delays and cost overruns.
Nowadays, most construction businesses use all-in-one or specialized software solutions that fully or partially automate and streamline the creation of project estimates.
For instance, one such end-to-end construction management software with strong estimation, budgeting, and scheduling features is Stack.
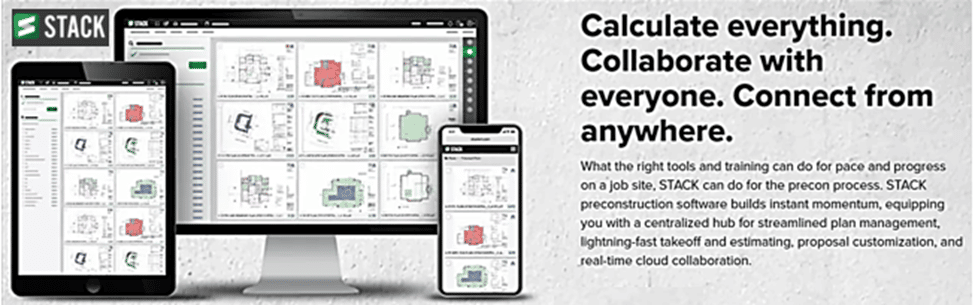
This and other similar software solutions allow company owners and managers to plan the entire project, from identifying all project tasks to estimating the resources, including equipment, needed to perform each one.
Thus, they help project managers determine exactly what equipment, where, when, and how long will be required for smooth task completion.
Moreover, such solutions, alone or combined with an asset tracking system, allow managers to check equipment availability by accessing the equipment inventory list and schedule.
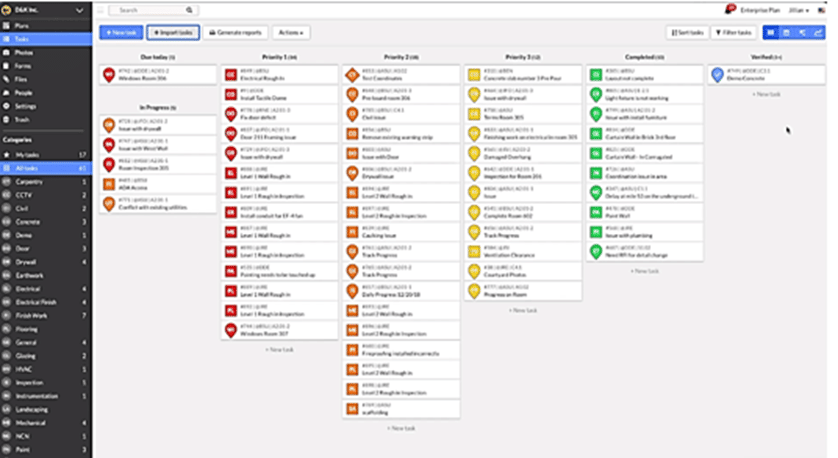
This enables them to easily cross-reference their list of project equipment against the current equipment schedule and book the required equipment in advance.
Once that’s done, it opens different avenues for creating more accurate project budget and schedule estimates.
For instance, the costs of operating and maintaining own equipment during the project can now be better estimated, together with the costs of equipment that needs to be rented for the project, which results in more accurate project budget estimates.
These cost estimates can be compared with previous similar projects to assess their accuracy and identify potential constraints and risks, which also helps estimate the size of budget contingencies for unexpected equipment-related situations.
Likewise, knowing how long past projects with a similar scope took and what equipment was required to complete them enables managers to create more precise project schedules in the future, along with better equipment allocation and utilization.
All in all, when equipment is scheduled in advance, it helps contractors or managers to provide more accurate project estimates.
Long Term Planning Capabilities
The long-term planning of construction resources, including equipment, is simply not possible without resource management, including equipment scheduling.
In other words, the ability to monitor and schedule construction workflows and resources helps contractors plan ahead by allowing them to identify their current resource capacity and future availability, understand trends, and anticipate future demand.
As with project estimates, long-term planning usually requires using one or more software solutions (the tech stack) that enable construction companies to track, analyze, plan, and schedule their operations and resources ahead of time.
In turn, this generates many far-reaching benefits on both company and project levels.
Let’s look at the key benefits of construction project scheduling and consider how scheduling equipment in advance contributes to each of them, thus enhancing the company’s long-term planning capabilities:
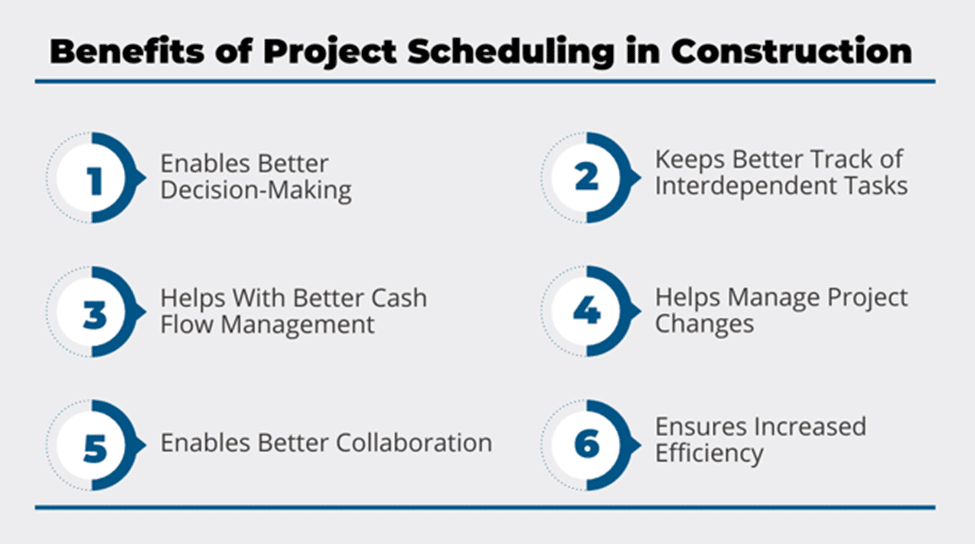
For instance, equipment scheduling improves decision-making by allowing managers to see if specific equipment will be overbooked on several future projects at once.
From there, they can either reschedule specific future project tasks to ensure the equipment is available or decide to rent the equipment and include the cost in their bid.
Likewise, knowing which equipment is available and at what times is extremely useful when managing project changes caused by incorrect estimates, design errors, unexpected site conditions, and the like.
Faced with many risks and uncertainties, scheduling resources that will be needed in the future (labor, materials, and equipment) allows construction companies to efficiently manage their utilization and allocation, identify potential bottlenecks or constraints, and plan accordingly.
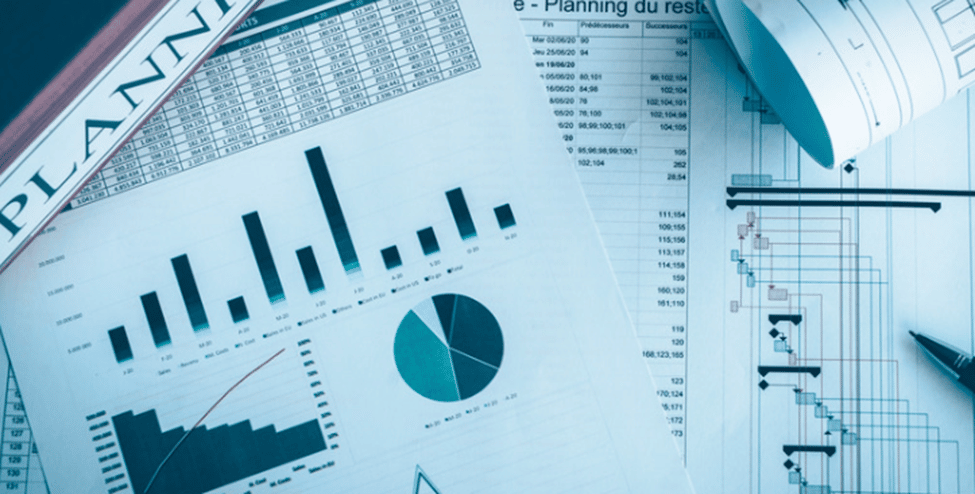
For instance, the project manager or team preparing a bid will be able to better determine whether the planned project deadline is achievable and what equipment will need to be used or rented during that period to complete the project on schedule.
This will prevent the company from placing underestimated bids or taking on projects with unrealistic timeframes.
Otherwise, it will inform project planning, budgeting, and scheduling decisions, thus reducing equipment management costs and increasing overall productivity.
Overall, scheduling equipment improves long-term planning on both company and project levels.
It allows for better monitoring, allocation, and utilization of company equipment across different projects, thus reducing operating costs and enabling better planning and coordination of future projects.
Smarter Task Organization
It’s clear by now that the ability to schedule construction project equipment involves much more than keeping an Excel spreadsheet.
To efficiently organize project tasks, construction businesses need to know the location, usage, condition, and availability of equipment across different projects in real time.
Furthermore, they need to be able to access the central equipment database, update the info, and communicate changes to their construction crews, preferably at any time and from any device.
When they can do that, it allows them to more accurately estimate, allocate, and utilize their construction equipment across multiple projects, thus enabling a smarter way to organize project tasks.
For example, let’s consider the benefits that an efficient equipment management system brings to contractors and see how it allows for better planning and organization of different project tasks:
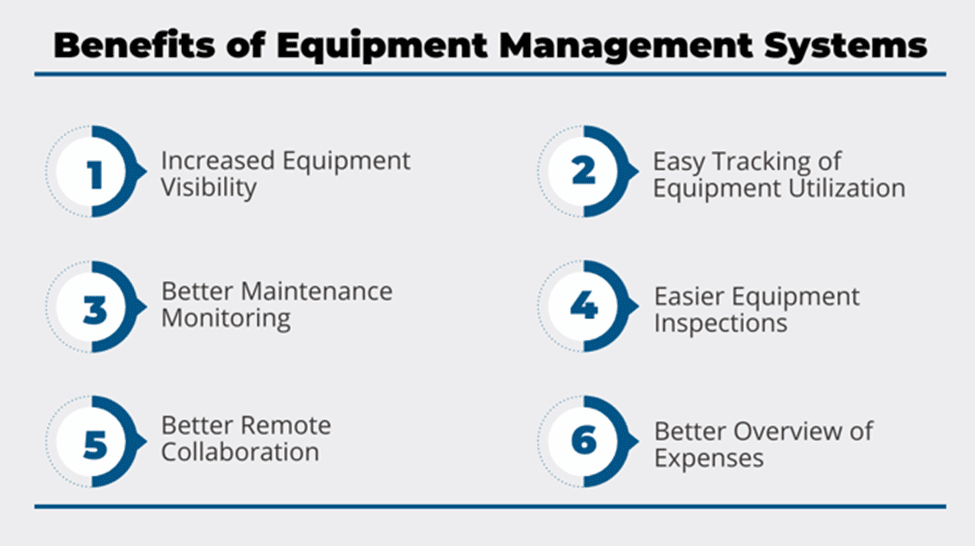
As for project planning, knowing where equipment and tools are, who is using them, and how long they will use them prevents project managers from scheduling activities that would require more resources, in this case tools and equipment, than available.
So, if the necessary equipment is unavailable at a particular time, the project manager can easily plan out some other activities that still need to be done but don’t require that specific type of equipment.
However, when plans go awry and threaten to cause project delays and cost overruns, knowing the location and availability of all equipment the company owns or rents at the moment contributes to smarter organization of tasks on ongoing projects.
And that’s where equipment management systems, namely asset tracking solutions, play a crucial role in enabling more efficient management of everyday construction operations.
One such easy-to-use and affordable solution that provides all the above advantages is GoCodes Asset Tracking.

Using GoCodes Asset Tracking, construction managers and workers can quickly check the location and availability of a piece of equipment to replace the one that broke down on-site, or has been misdelivered, misplaced, or stolen.
That way, the replacement can be easily found or delivered to the site from the nearest location, thus minimizing downtime, delays, and budget overruns.
To sum up, when enabled by the right software, equipment scheduling allows for more efficient planning and management of different project tasks.
Maximizing Equipment Utilization
When construction businesses are able to schedule their machinery, equipment, and tools in advance, they can maximize their use, which leads to cost savings and productivity gains.
Again, this is best achieved by using one or several software apps.
Specialized apps allow contractors to establish a centralized schedule of all their equipment, forecast and optimize equipment utilization across multiple projects, identify and under- and overutilized equipment, and establish an effective check-in/check-out system.
For instance, using equipment scheduling software combined with different GPS tracking systems to monitor the utilization of various equipment in real-time will provide critical information on how to optimize their use to reduce operating costs and also enable contractors to do so.
One such equipment scheduling app is Saviom.
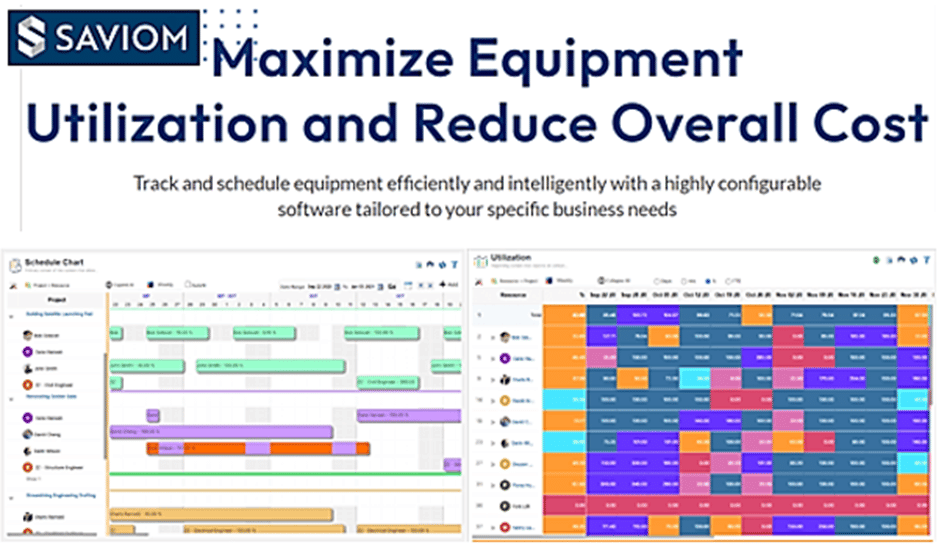
This and other similar tech solutions, alone or combined, provide a comprehensive insight into every piece of equipment they own (and currently rent), which is crucial for enhancing equipment efficiency and utilization.
For example, it allows managers to forecast future equipment use and identify constraints and potential shortages ahead of time.
Furthermore, it’s easier to detect when some equipment is underutilized, so companies can either put them to use or sell them.
Likewise, it’s possible to identify overworked equipment, ensuring better allocation and preventive maintenance, as well as more informed future equipment procurement decisions.
On that note, scheduling solutions allow managers to streamline virtually all equipment maintenance and inspection processes, further optimizing equipment utilization by, for example, reducing procurement and maintenance costs.
Finally, alone or integrated with other asset tracking solutions, they enable companies to track tools and equipment in real-time, enabling them to establish a check-in/check-out system.

When the process of checking equipment in and out is automated, there is full transparency of equipment utilization and results in increased employee accountability, more effective planning and maintenance, and higher productivity.
In light of all the above, it’s clear that equipment scheduling and tracking software solutions give businesses both the data and tools needed to maximize equipment utilization and reduce operating costs.
Preventing Project Delays
Similar to how it can help prevent budget overruns by improving project estimates, equipment scheduling can help avoid or minimize another stubborn issue plaguing many construction projects—delays.
In fact, we could say that equipment scheduling allows construction businesses to take full advantage of all the previously described benefits and use them to prevent project delays on both micro and macro level.
Simply put, to ensure that construction projects go according to the set timeline, construction businesses need to ensure that the required equipment is available and in good mechanical health.
That way, they can avoid unnecessary delays, such as waiting for specific equipment to become available or be repaired.
Looking even wider, scheduling equipment helps tackle the top reasons for project delays.
Let’s see what they are and how efficient equipment scheduling helps address them.
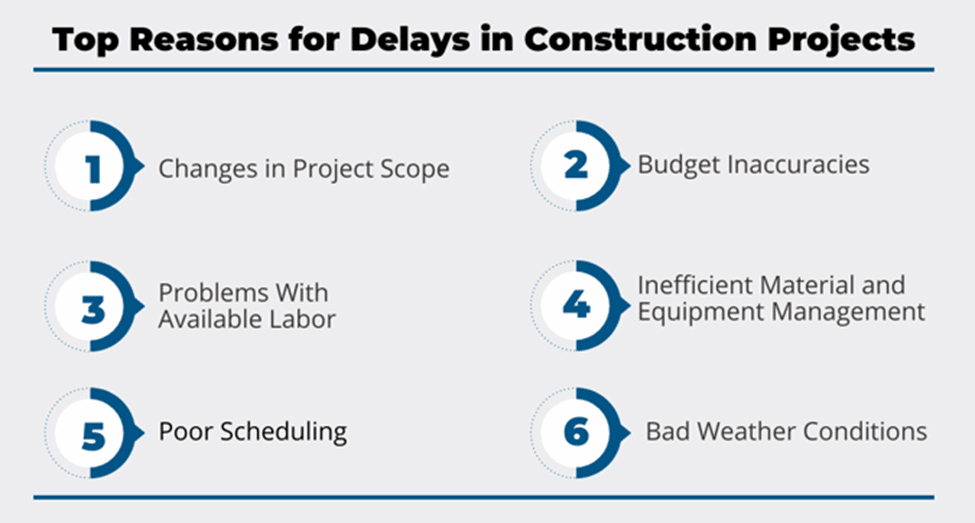
First, scheduling makes material and equipment management more efficient by default.
In other words, it ensures that the right materials, tools, and equipment are available at the right time and at the right jobsite. When one of these elements is out of place, delays ensue.
Second, it helps minimize budget inaccuracies and project scheduling issues related to equipment in the project planning stage.
This is particularly important when renting equipment.
Because the project manager knows what company equipment is available for a given period, they also know which pieces will need to be rented and when, thus allowing decision-makers to book equipment from their vendors ahead of time.
And, if the equipment is already rented out for that period or not available in sufficient quantity, it gives them more time to find the best alternatives, check their availability and cost, and include them in their budget and schedule proposals.
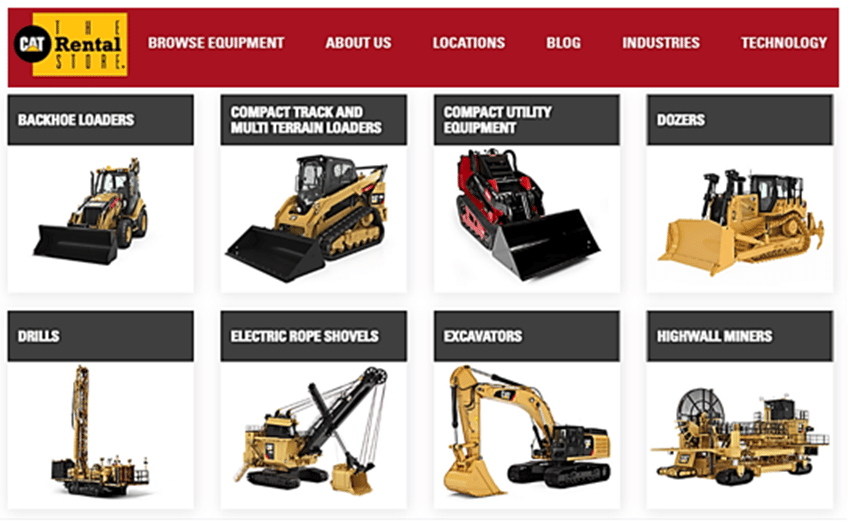
Finally, when faced with almost inevitable project changes, equipment scheduling, supported by real-time tracking and communication software apps, enables businesses to prevent, or at least mitigate, any number of equipment management challenges timely and efficiently.
As for project planning, efficient equipment scheduling helps prevent project delays by providing key information that can be used to improve project estimating, budgeting, and scheduling processes.
When this is coupled with full and instant visibility of equipment utilization and availability, businesses can use the insights to timely address any issues related to providing, maintaining, and scheduling equipment throughout the project lifecycle.
Conclusion
Remember that equipment scheduling helps ensure smooth project operations by improving equipment-related project estimates, long-term planning capabilities, task organization and utilization, and preventing project delays.
Finally, all this and much more can’t be achieved without the help of one or more construction management software solutions.