Every company that owns inventory and uses it for projects or business dealings needs to keep tabs on its equipment and the state it is in.
Those who opt for manual tracking usually fail at this task as it is almost impossible to track so many tools and information efficiently.
This article will explain why asset scheduling is crucial for business while offering advice on how to go about it the right way, from creating a database and project schedules, to methods of prioritizing tasks, among other things.
If that is something you want to implement in your business, keep reading!
In this article...
Benefits of Equipment Scheduling
Equipment scheduling helps you organize and plan better, improving your effectiveness.
Before conducting a job, you need to plan and prepare for it.
Preparation includes mapping out the project phases and considering the materials and assets necessary to accomplish the goal. This is where equipment scheduling can come in handy.
You can’t perform certain aspects of your job without the necessary tools.
When you schedule equipment use, you are always aware of where the tools are, who is in charge of them, and how long they will use them.
Based on this data, you can plan your course of action and guarantee that a tool will be available when you need it if you’ve scheduled it on time, eliminating booking conflict.
Effective equipment scheduling will also let you know if the item will be available soon, helping you decide whether to wait until it’s available or rent or buy a new tool to get the job done.
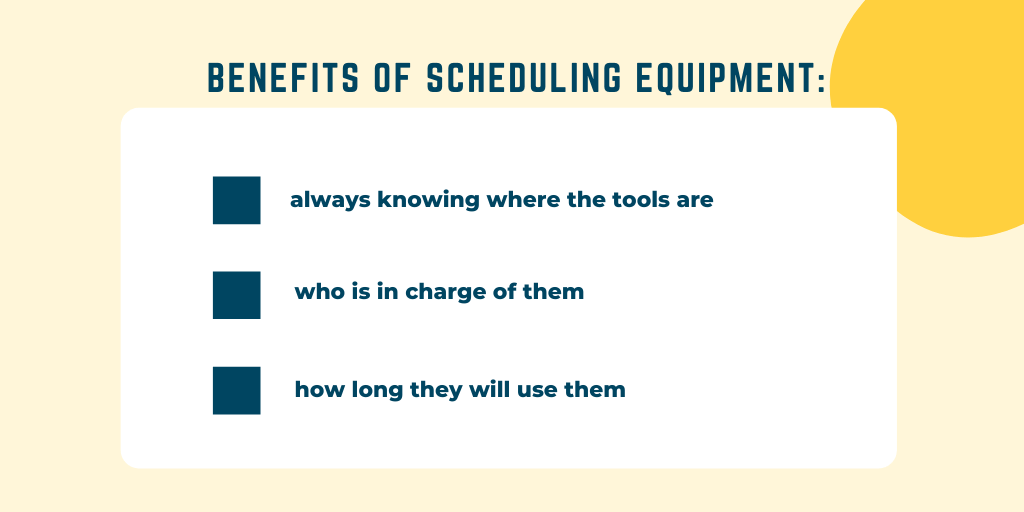
Of course, this depends on how urgent your project is and how costly the device is. If it’s inexpensive, buying a new piece of equipment will pay off more than postponing a project.
On top of all that, asset scheduling distributes responsibility among the employees.
They all have a way to check tool availability in advance, giving them sufficient time to make a backup plan or request help if the tool is crucial.
It’s a good idea to use software to help you schedule equipment.
Cloud software lets users access the system whenever and wherever they want, without having to return to the office or calling their supervisors.
There are affordable and productive solutions designed to help you avoid asset shortages and issues, helping you do your job better and faster.
How to Conduct Equipment Scheduling
When you use tool scheduling solutions, you eliminate the risk of double booking or shortage, so you can plan projects fully confident that all the necessary tools will be available.
Make a Central Database of Your Equipment
Have a database listing all your inventory and its current state before implementing equipment scheduling.
The first step is to make an inventory of all your equipment and create a database, which will take time and energy but will be worth your while.
A central database will be accessible to all employees, giving them insight into all assets, their state, and availability.
As a result, the employees will no longer have to check with you where a particular tool is or if it’s in use.
The database guarantees that you’ll know where the tools are, eliminating the risk of theft and misplacement.
The use of a database also facilitates maintenance.
In any type of business, it’s always good to know when the last service was and the tool’s condition.
It helps you plan your operations and conduct both maintenance and any new purchases without losing efficiency.
Some companies use spreadsheets to track their equipment, which is accessible from laptops and computers.
However, such spreadsheets pose a high risk for human error, as entries can be deleted or wrongly entered, making it difficult to understand the current state.
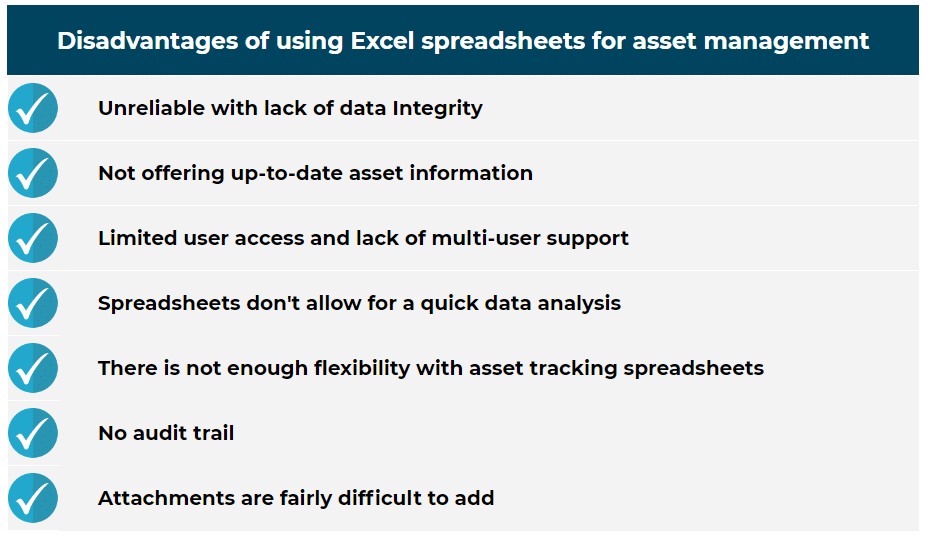
Besides, looking through spreadsheets can take a lot of time if the items are listed individually— in fact, 80% of employees spend at least half an hour a day looking for information.
Software solutions like GoCodes are an excellent way to make this data more accessible and make processes more time-efficient.
Such solutions let companies list all the equipment along with such important details as the condition of the item and maintenance information, use, and date of return.
The data is saved in the cloud, letting anyone with authorization access it.
Such software also decreases the risk of human error and data loss, which is extremely important for inventory management, as inventory checks take a lot of time.
Creating an inventory database takes time, but it pays off due to the ease of access to all equipment-related information.
Create a Project Schedule
Creating a project schedule allows you to track your daily progress, ensure that you have enough resources to finish on time, and helps you understand what stage of the project, if any, is problematic.
A project schedule is a planned timeline of your work which helps you understand when you need to do each individual task to finish the project in time.
Scheduling keeps you aware of how well you’re progressing and whether you’re behind with work or not. This makes it indispensable for all industries, although maintaining a schedule is complicated for some.
You have to notify all stakeholders in case of any delays, so they can manage their expectations.
When you notice you’re running late with something, you can decide at which stage to organize your work differently—and in what ways.
You can also plan the use of assets, materials, and workforce.
If you know that a project starting next week involves 25 people and five larger pieces of equipment, you will take that into account when deciding whether to agree to a new project that will need some of those people and tools.
Schedules help you manage your employees better as some team members might not be necessary throughout the entire project timeline.
For instance, you might need some people only at the project’s beginning, which means they’ll be involved with it for a couple of days and take on a new project after that.
The same thing applies to equipment, as not all of it is necessary during the project.
Maintenance is an important factor in asset availability.
Serious companies rely on regularly scheduled preventive maintenance to guarantee that their tools are in good condition and reduce the risk of malfunctioning or breakdowns.
If the need for servicing occurs in the middle of a project, you need to know this in advance. This is where software solutions can help you.
Take a look at the video below to see how GoCodes lets you schedule maintenance and receive a reminder beforehand.
Let’s look at the practical aspects of creating an effective schedule for a project.
Tips for Making a Good Schedule for an Upcoming Project
First, agree on the terms with the contractor while taking into account the number of employees you can count on and equipment availability.
Ensure that you can provide the service you are promising.
You can create a template to speed up the process and eliminate errors such as forgetting a step or overlooking something when you’re in a rush.
Consider all the necessary steps you need to take when dealing with a new project.
Write them down in a clear and concise but understandable way that can be applied to most, if not all, projects you handle. You can always expand the list later as you go along.
In developing the project template, it would be a good idea to involve other members of your team, especially those with hands-on experience in the field. They might remember more steps than you since they follow them on every project.
Also, take notice of the schedule’s structure. Are tasks organized in chronological order? If not, it’s imperative to manage them that way to reduce the risk of delays.
Wherever applicable, split the workload into sections—for instance, land preparation, rough framing, electrical and plumbing setup, and insulation.
Use software or tools that can help you track items and give you information on them, allowing the workers to keep track of them at all times—consider investing in software that lets you GPS track your tools, helping you locate them even when lost or misplaced.
A schedule helps you see all the tasks in advance and keep track of your progress, equipment, and worker needs.
Prioritize Tasks
Writing tasks down allows you to prioritize them based on the problem at hand and the ultimate goal.
When you’re writing down the tasks within a project, you’re listing them in a specific, chronological order since there are some steps that you need to complete before moving on to the next ones.
However, once you have all your project tasks ready, don’t get too comfortable.
You have to be prepared to adapt and prioritize tasks according to changes along the way.
You can prioritize by cost, meaning that you will have to reevaluate your course of action and find a less costly but still practical and quality solution.
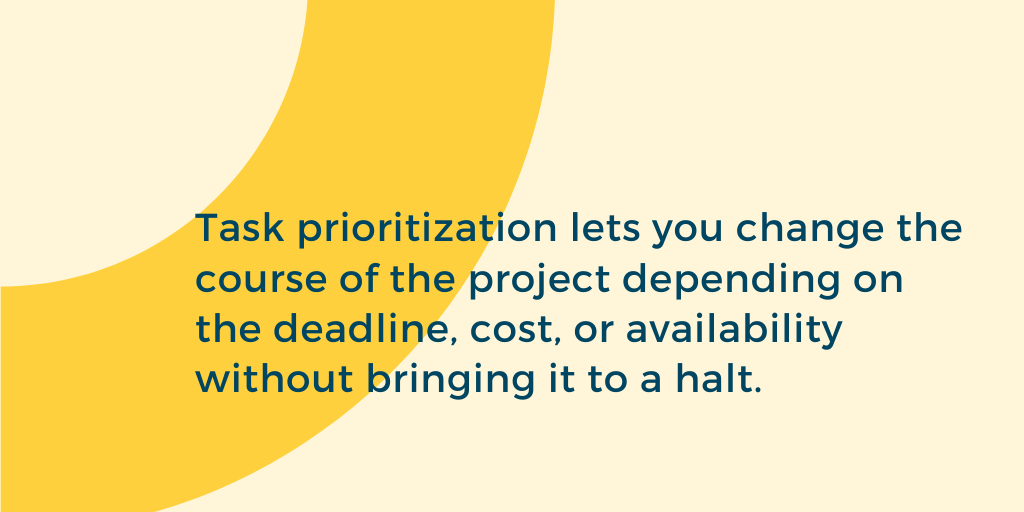
For instance, you might need to do that when you find yourself behind schedule on a project or exceed its budget, meaning that you cannot afford to spend as much as you first decided.
Priorities can also change depending on the main goal, such as the deadline.
If you’re behind on an important project with a strict deadline that contractors are willing to spend more on, you can use the extra budget to get more manpower and tools on the project.
However, you might also find yourself lacking equipment or people.
In this case, you have to prioritize the tasks you can accomplish with available resources, keeping the project on schedule while trying to get the necessary tools.
Of course, you can prevent asset shortage with tracking and regular maintenance, but sometimes, tools can fail in the middle of the project despite that.
However, prioritization helps you keep the project going while you find the necessary equipment or rent it.
Task prioritization lets you change the course of the project depending on the deadline, cost, or availability without bringing it to a halt.
Track Changes in Real Time
Tracking changes as they happen allows you to plan and reorganize.
In reality, you might have the assets necessary to finish a project, but if you can’t account for that asset when you need it, it becomes useless.
Because of this, many companies opt for tracking solutions that let them know where a tool is, who is using it, and when it will be free to use.
Another advantage of tracking is being able to see changes as they happen, boosting transparency and productivity.
When you notice a change, you can plan accordingly, saving time and preventing halts and delays, which is crucial when you have a deadline.
When you stay on top of changes and notice even the smallest ones, you can see when a delay on one project can set another one back.
This is especially important when you’re dealing with a larger piece of equipment with limited quantities.
Suppose you estimated that you could count on it in a couple of days, but the project it’s currently on got delayed by five.
In that case, you will have to reorganize your project and focus on different, doable tasks instead of stopping it and waiting for the assets to become available.
While you can try to do all of this manually, it’s almost impossible for companies with many assets, employees, and projects.
Even if you have a limited amount of tools, there’s always the factor of human error to consider.
However, cloud software and apps can do the work for you.
They make your life easier by tracking equipment and save you money not only by letting you spot issues before they block the project but also by being cost-effective themselves as you pay only for what you use.
It also helps you eliminate costly downtime, as it enables you to reorganize your project points, and ensure that you handle tasks that don’t need that specific tool.
When you’re on track with all project-related changes, you can take measures to stay on track and get the job done.
Use Your Smartphone to Check Out Equipment
Businesses with physical assets can primarily benefit from modern technology, specifically software and mobile apps, that offer asset check-in and tracking.
Such solutions allow the end-user to scan the tool and check it out before using it, which then marks the asset as occupied in the system, letting other users know that the device isn’t available.
This feature also enables you to know who is responsible for the item.
Transparency increases employee accountability while decreasing the risk of theft or misplacement.
The users can see what condition the equipment is in and when it’s due for maintenance.
They also have the option to reserve a particular tool, which assures them it will be at their disposal when they need it.
Apps will also let the users know if a similar device is available for use, saving you time and money as work can go on uninterrupted.
A significant benefit of using mobile apps and software is that anyone with a mobile device can access them if you permit them.
Your employees in the field can simply scan items, and everyone else who uses the app will see where the tool is and who is using it, so you’re not the only one with the overview.
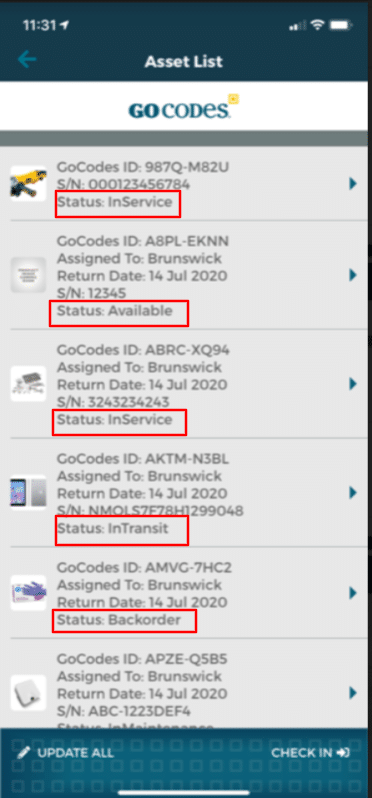
When you get software that lets you track your equipment and check it in and out, make sure to enter all your gear and its relevant data into the system.
Train your employees well, so they know how to use the software, which is necessary if you want it to function correctly.
If an employee needs a particular tool, they can scan it with their phone to mark it as unavailable.
Then, this data will be available to everyone else with access to the system in real-time.
After an employee returns a tool, mark it as available again, letting others know it’s free to use.
Using software and apps for asset tracking and checking in can help your team stay organized and be more productive.
Conclusion
Asset scheduling is a crucial part of any business that deals with physical assets. It lets you plan projects assured that the necessary tools will be available on the spot.
The most effective way to track and schedule assets is by using software designed for your needs.
Nowadays, software can help you do so much more with assets than ever before.
You can check equipment in and out, track it, be notified of maintenance dates, look into the tool’s condition, and reserve it for your next project.
Instead of doing all this manually and inevitably failing, opt for technological solutions that will help you deal with equipment effortlessly.
GoCodes Can Help
We use QR code tags with a unique visual code that you can scan with your smartphone. When scanned, GoCodes tags provide GPS information about equipment location and availability, making asset tracking and equipment scheduling easy.
Sign up for a free trial here.