At first glance, equipment management systems are useful mostly for bringing order to assets and tools of all types.
However, equipment management systems bring many different benefits to both large and small businesses on different levels.
The efficiency of a good equipment management system and the data it provides can yield better visibility as well as more accurate decision-making.
In this article, we’ll explore six business benefits of equipment management systems in more detail.
In this article...
Better Remote Collaboration
Construction companies often conduct business across several sites, and the bigger ones even span their work across several time zones.
Equipment management systems greatly expand the possibilities of remote collaboration.
A single on-premise software system available in one location is no longer the most effective way to manage things or maintain up-to-the-minute data.
Today, equipment management systems are mainly cloud based, which grants users the ability to share updates instantly and look at the same information in real-time, regardless of where they are.
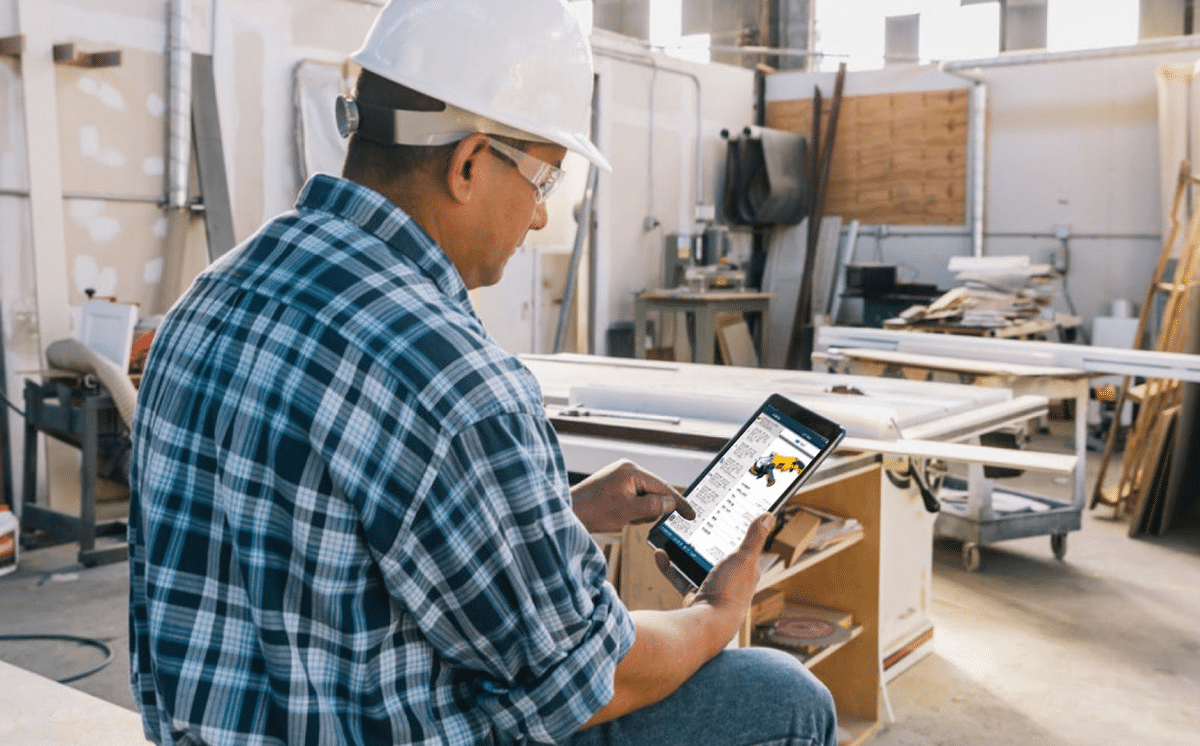
Sheer access to the same and accurate data results in better collaboration between team members.
This self-service process reduces the need for additional emails, calls, and on-site visits, which drastically cuts the time needed to convey a message.
This is especially important when problems arise. Using an equipment management system, employees can communicate or issue updates as needed.
Since equipment management systems are often equipped with GPS capabilities, they are invaluable when responding to safety concerns or attempting to untangle equipment locations.
Whether it’s best for your team to leave comments on a machine’s status page, use chat features, or share equipment status updates, remote collaboration doesn’t merely provide an edge–it is a must.
Increased Equipment Visibility
A robust equipment management system allows decision makers and other authorized employees to overview and study equipment management for an entire jobsite, or several field teams at once.
Cloud-based software ensures that all team members see the same equipment data at the same time.
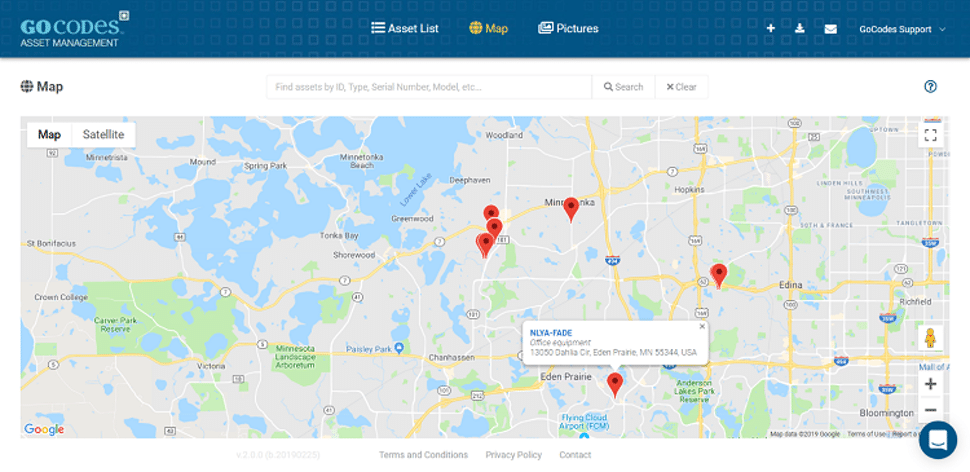
Having visibility of all company equipment decreases chances of miscommunication and gives each team member the ability to do his or her job without waiting for information–information that might arrive too late to affect an outcome positively.
Equipment management systems are also useful in remaining up to date on how much inventory is present in various locations–warehouses versus construction sites, for example.
This can help prevent over-ordering supplies, which is especially important when working with perishable items or those requiring expedited handling.
In this example below, a real-time overview of equipment is of great use to an auto repair shop.
The information is easily sorted and available to employees as necessary, and they can quickly spot the low quantity of a particular car part:
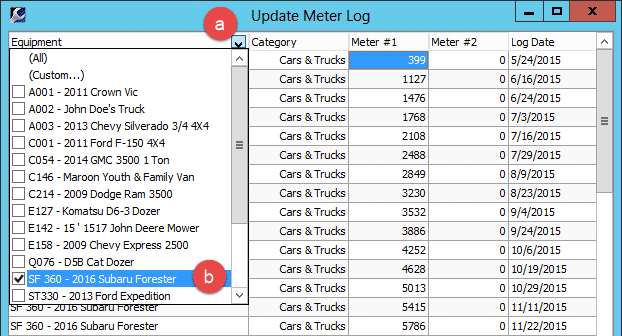
Construction employees can enjoy the same benefits if the company opts to use a modern equipment management system.
GoCodes, for example, is a system that can even alert users on low quantities of your equipment, so you never have to worry about your workers ending up without the stuff needed to do their job.
Better inventory management assists in avoiding the disastrous happenstance of not keeping enough equipment or materials in stock, resulting in delayed projects, scrambling employees, and sunk costs in rush shipping.
Construction resource management overall becomes much easier with better equipment visibility.
Easy Tracking of Equipment Utilization
Equipment management systems let you easily. track equipment utilization. They usually have an equipment checkout feature, which creates a reliable chain of custody for each item.
A check-in/check-out feature can record and compile the following important information:
- The exact piece of equipment used
- Which employee has checked out or checked in equipment
- Time of custody exchange
- Place of custody exchange
- Jobs with which equipment was associated
- Readings on equipment, such as mileage
- Reports on malfunctions or maintenance needs
Knowing the utilization of each item increases security in a number of valuable ways.
For once, a constantly updating record of the employee chain of custody discourages theft from within the company.
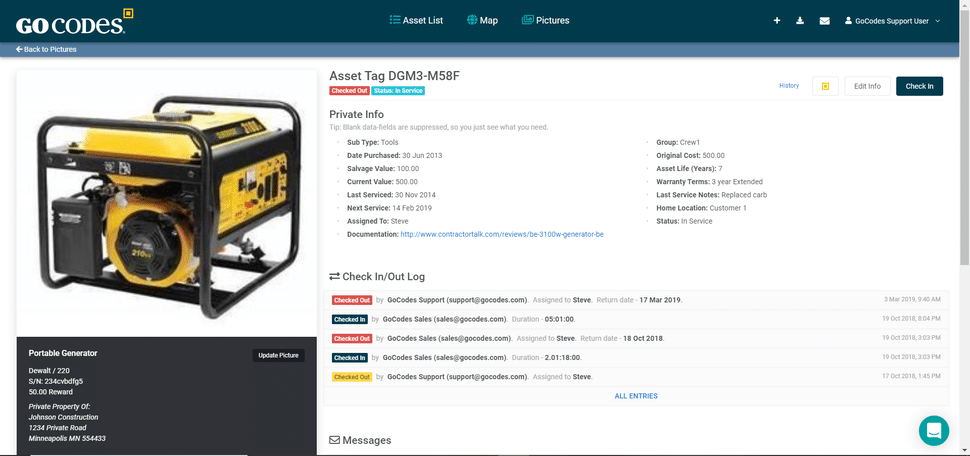
It also instantly narrows a search if theft has taken place; just a few clicks will reveal where the item was last seen.
Equipment checkout systems outfitted with GPS capabilities can turn lengthy search time into much more manageable retrieval time.
In addition, such information is usually useful to law enforcement investigations and filing insurance claims in the event of theft.
However, as the above list indicates, tracking equipment utilization offers much more than better security.
Regular reviews of such information yield valuable data into which items are used more than others or provide insight into recurring maintenance problems.
For example, if a piece of equipment constantly requires recalibration after a certain employee has used it, perhaps some re-training is in order.
Or, if an item goes unused because it is not a good fit for a job or the skills of your team, the equipment is possibly better off eliminated from your fleet or inventory.
Such knowledge can result in a more streamlined and efficient tool room.
Easier Equipment Inspections
Some equipment management systems are designed especially for digital inspections, while others have helpful features for audits.
GoCodes, for example, has a specially designed “audit mode” that can make your equipment auditing much more efficient.
A digital equipment inspection is one performed using an electronic device, such as a tablet, rather than paper and a clipboard.
Not only do digital inspections decrease the danger of record loss or illegibility, but their results are also easily uploaded to the cloud for fast retrieval and quickly create a valuable cache of equipment information.
Here is an example of a digital inspection report:
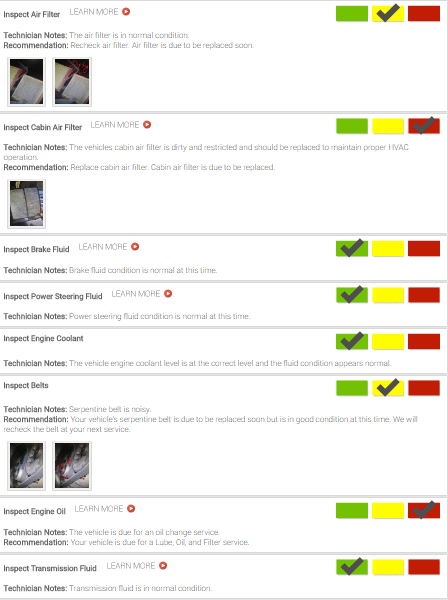
As you can see, this type of digital inspection allows employees the ability to upload pictures, provide comments, and add or delete customized items.
Digital equipment inspections can standardize the inspection process across a company.
They add to transparency in reporting and are extremely useful during audits or when working with equipment in far-flung job sites.
Companies who must prove compliance with unions, federal regulators, or local codes may easily rely upon digital inspection reports as accurate, up to date, and easily accessible.
Better Maintenance Monitoring
Equipment management systems can easily bring order to a chaotic or constantly last-minute equipment maintenance.
A robust but user-friendly asset tracking system such as GoCodes’ can greatly support maintenance actions from start to finish.
Work orders, repair scheduling, and preventive maintenance checks are all easily aided by GoCodes’ features.
A simple scan with a smartphone or tablet can reveal vital information for maintenance monitoring.
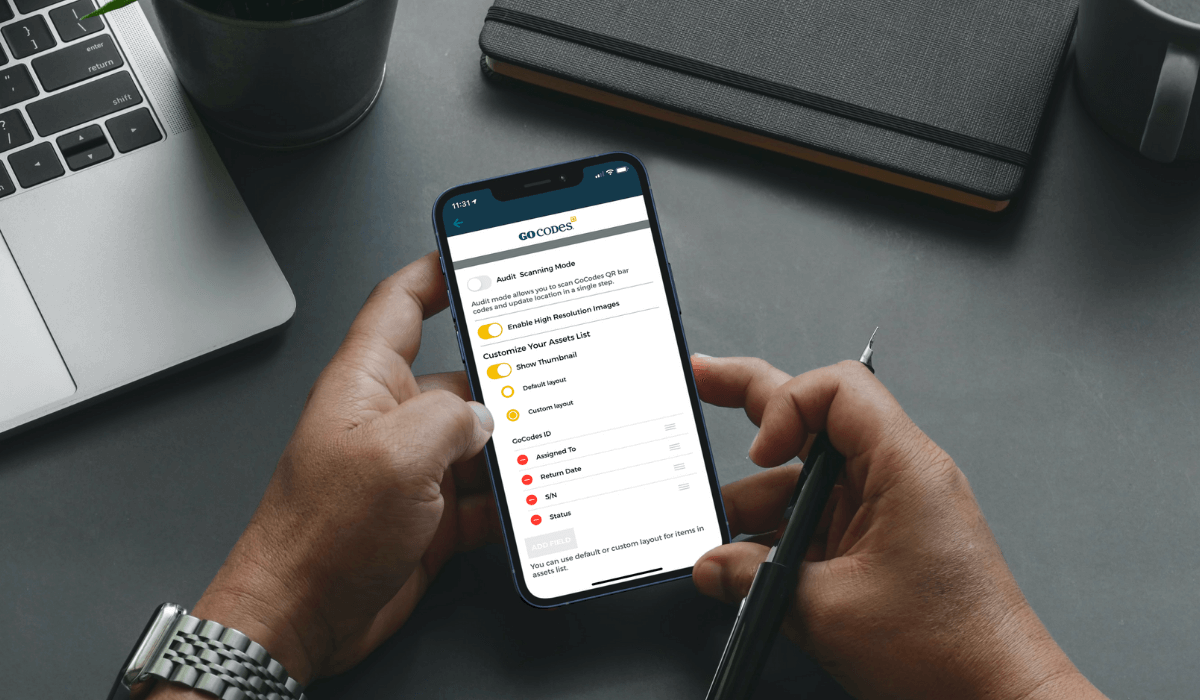
Warranty information is easily stored as well.
For example, employees can quickly call up an operator’s manual, the equipment’s service history, suggestions for troubleshooting, or dates of service for cleaning, inspection, and testing.
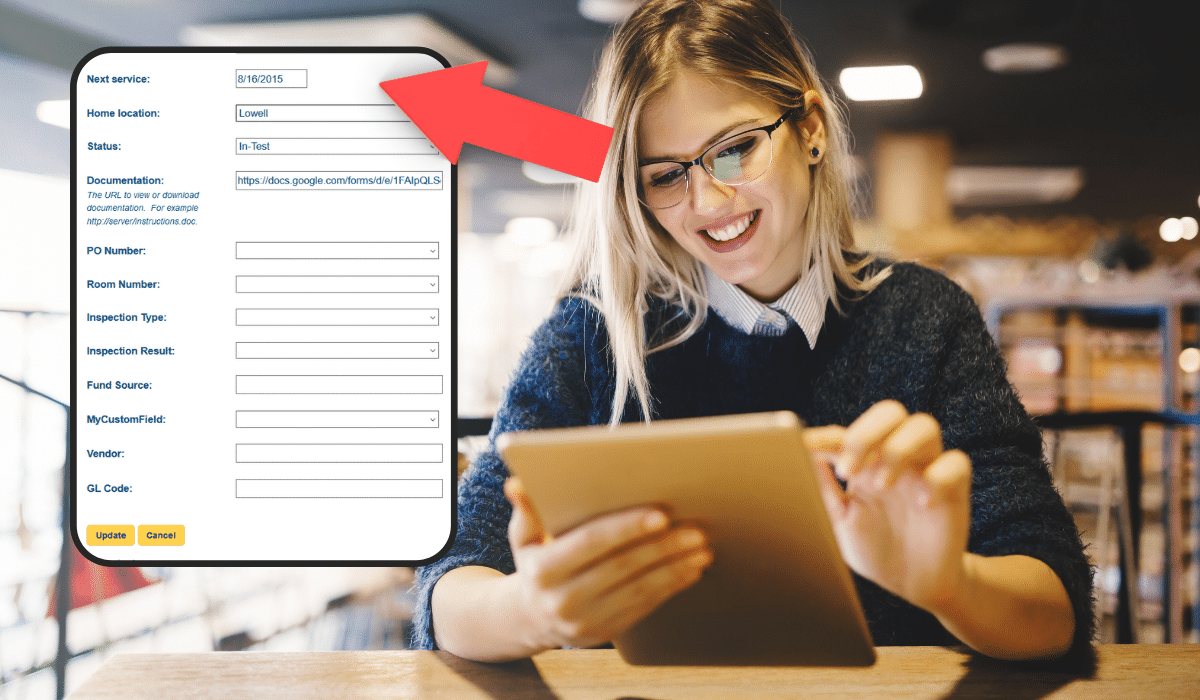
Companies can also automate service requests, which is especially useful in the field or when relaying accurate data is critical, particularly in a time crunch.
This can increase response time, build an invaluable data bank about the equipment’s life cycle, provide important information to third-party technicians, and document safety incidents.
A strategy of catching maintenance problems early saves money, increases worker safety, and extends the life of valuable equipment.
Better Overview of Expenses
Usually, equipment management systems can associate a purchase cost with any equipment; therefore, using an equipment management system helps companies track their equipment expenses.
And why does this matter?
The more thoroughly decision makers can understand expenses, the easier it can be to focus on profitability and control operating costs.
By monitoring and tracking expenses, even small ones, it is easier to see where a company might overspend.
Systems like GoCodes can track this information with up-to-the-second results, then instantly generate a useful report breaking down expenditures.
The report below shows a pie chart of the top 10 valuable assets a company owns.
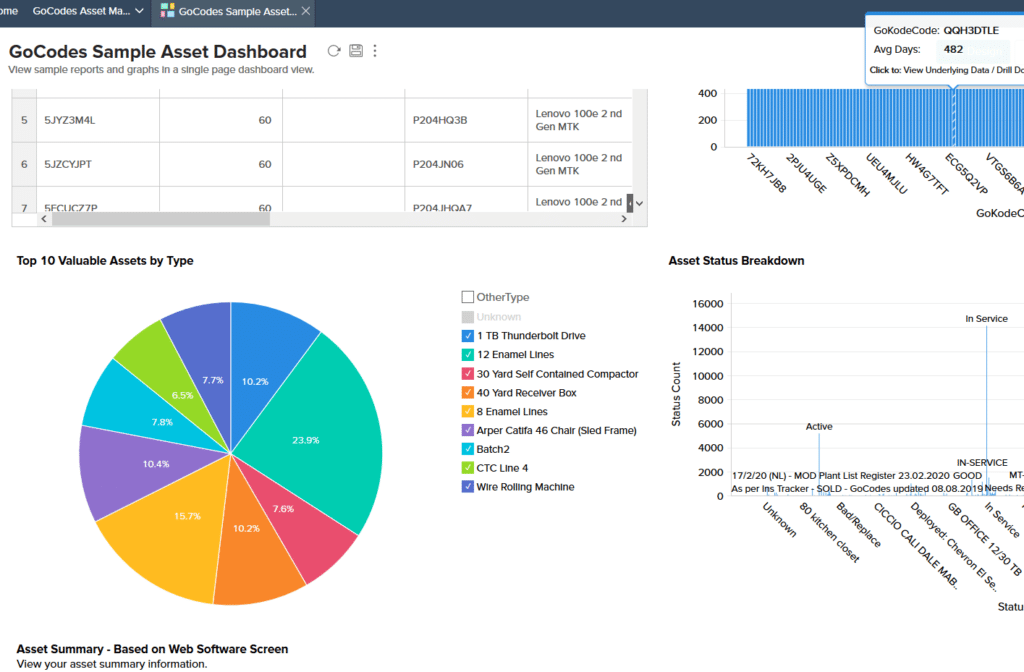
In addition, these systems can automatically calculate depreciation. Equipment depreciation is the amount of value an item loses on a yearly basis, assuming regular use.
Frequently used items usually depreciate faster, but the speed of this is curtailed by good preventive maintenance and careful employee training.
Using an equipment management system automates these calculations and can quickly show where an item is in its life cycle.
This data can help stakeholders make informed decisions about equipment replacement, repair, and recycling.
Conclusion
Equipment management systems can bring many benefits to businesses.
They provide for better remote collaboration and increase the equipment visibility to give decision makers an exact and exportable report about inventory levels and activity on multiple job sites.
Equipment management systems also offer easy and automatic tracking of equipment utilization, which is invaluable for security, warranty claims, and proof of compliance.
Inspections are easier, especially if they are conducted digitally.
Maintenance monitoring becomes more efficient, as equipment management systems can immediately provide information about scheduling, work orders, and repair actions.
Finally, valuable overviews of expenses are compiled much more accurately and with greater speed.
All of these benefits can make your life much easier, and help you take your company to new levels. Why not implement a quality equipment management system and enjoy these benefits?