In the highly competitive construction industry, contractors had to watch their operating costs even before the global pandemic and other ongoing geopolitical crises pushed the prices of all construction inputs—labor, materials, fuel, and equipment.
Against this backdrop, how can construction businesses reduce costs without compromising quality and reputation?
In this article, we’ve picked five tips to help contractors keep costs under control even in the current inflationary environment.
In this article...
Digitize All Documentation
Digitizing all documentation can generate cost savings across your entire business that far surpass the environmental and financial benefits of reducing the amount of paper and printing ink.
According to McKinsey, the construction industry is among the least digitized industries in the US, sitting just above agriculture and hunting.
This means that many construction documents still rely on printing, copying, modifying, sharing, and storing an endless array of construction documents in paper form.
Naturally, this is followed by the manual input of data into different digital systems that a construction business already uses, such as project management or accounting software.
Hence, digitizing documentation as much as possible and creating paperless workflows will not only reduce paper, printing, storage, and postage costs.
It can also prevent costly rework and cost overruns and protect you in case of any disputes.
With that in mind, here are the five key things contractors should do when digitizing their document workflows:
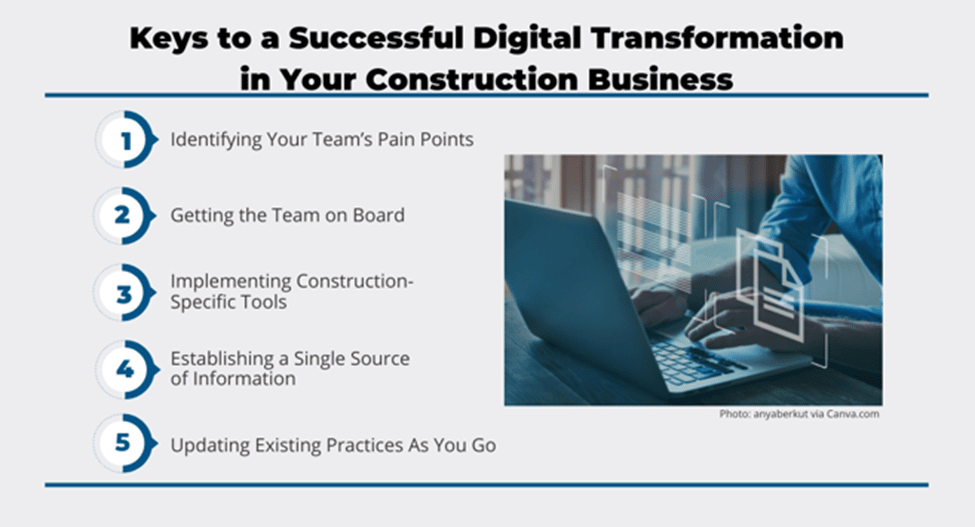
Applying the above steps in practice will, ultimately, result in an efficient document management system, which will enable contractors to reduce costs in myriad direct and indirect ways.
For instance, consider the potential cost savings of eliminating the need for construction crew members to go back to the office to find and review project documentation, and instead enabling them to log into an app and access the required document directly on-site.
Now combine those savings with reduced costs of rework and delays because everyone is using the same updated project documentation, which minimizes the chances of errors, omissions, and lost data.
Other than direct paper and printing costs, digitized documentation can also ensure lower equipment maintenance costs by allowing service technicians to review all warranty, maintenance, and repair documents in digital form. This empowers them to do their job more efficiently and generates cost savings.
Thus, when we add all the other benefits of digitizing documentation, such as establishing a single source of updated information for all stakeholders, it’s clear that going digital creates many opportunities for cutting costs in your construction business.
Manage Fuel Consumption
Faced with rising fuel prices, many construction businesses are rethinking their fuel management practices and finding ways to reduce consumption.
Optimizing fuel consumption may include measures like obtaining energy-efficient vehicles and heavy equipment, selecting the right fuel supplier, and using technology to monitor fuel usage, engine performance, and driver behavior.
For starters, in the first half of 2022, the prices of gasoline and diesel fuel rose 49% and 55%, respectively, causing a cascade of price hikes that resulted in the highest inflation rate since 1981.
For example, here’s how the price of retail diesel changed over two years, courtesy of Statista:
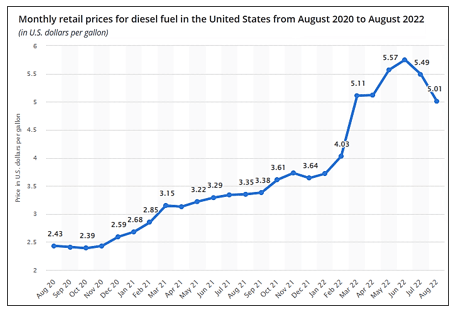
As a result, managing fuel consumption has become a top priority for construction businesses striving to keep their overhead costs under control.
One way to improve fuel economy is to look for opportunities where older gas-guzzling equipment can be replaced with newer, more energy-efficient models.
For example, this can mean buying a new generator, opting for an electric-powered mini excavator, or selling older equipment and renting new models.
Another way to manage fuel costs is to select the right fuel supplier.
Naturally, you should start by ensuring that the supplier’s service area fits your current and future needs. For instance, if you were in Illinois, one of your options would be Feece Oil Co.:
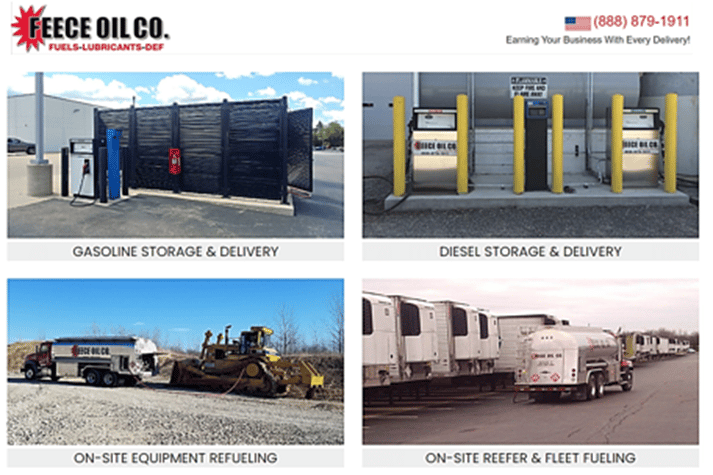
After that, the main factor to consider is the price they offer per gallon, along with potential quantity and loyalty discounts.
However, things like fuel quality, prompt delivery, efficient jobsite fueling, and reliable and transparent services and pricing should also be considered, as problems in these areas can increase fuel and other operating costs instead of reducing them.
Finally, maybe the best way to save on fuel costs is to invest in technology that allows you to monitor fuel usage, engine performance, and driver behavior.
For instance, GPS tracking of vehicles and heavy equipment, coupled with various sensors for engine diagnostics, will tell you exactly where a machine is, whether it’s moving, idling, or not used, and how its engine is performing.
Thus, you can identify whether increased fuel consumption is caused by the machine or its operator.
Overall, despite higher prices, contractors can still find ways to manage their fuel consumption more efficiently.
Reduce Material Waste
This is another way to both minimize costs and show that your construction business is committed to environmentally responsible behavior and sustainability.
For instance, material waste can be reduced by utilizing just-in-time (JIT) delivery practices to prevent excess materials and packaging from ever arriving on-site.
However, such methods require a bulletproof construction schedule, fixed prices, and secured availability of construction materials, all of which are in short supply right now.
And that just underlines the importance of sustainable waste management practices.
Put simply, saving, salvaging, reusing, and recycling leftover materials from previous construction projects can help you reduce future construction costs.
With that in mind, we looked at what the Environmental Protection Agency (EPA) says about materials on construction sites that can be salvaged and reused.
Here’s a summary:
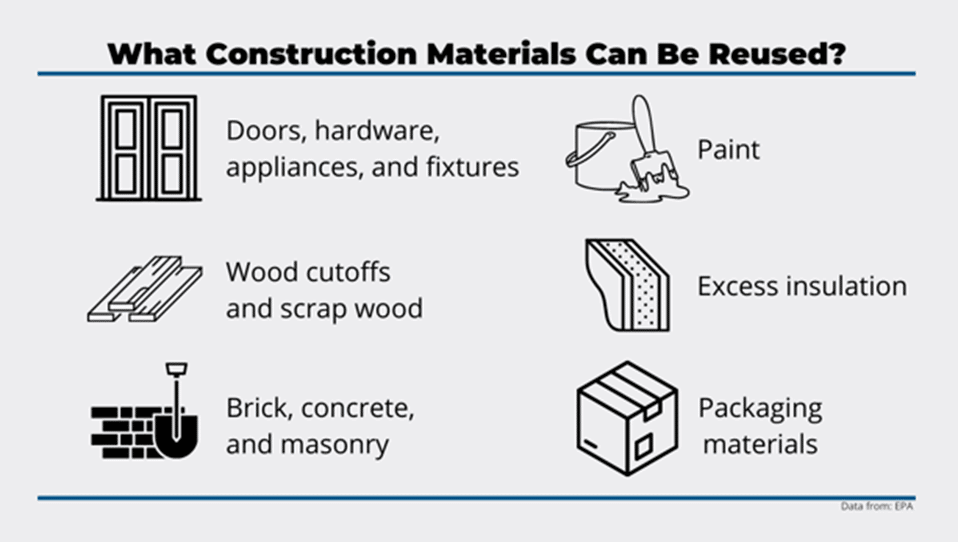
For instance, doors, fixtures, hardware, and appliances can be salvaged and used during the rebuild or on other jobs, or they can be donated.
Bricks, concrete, and masonry can be recycled on-site and used as fill, driveway bedding, or subbase material, while scrap wood can be chipped and used as mulch or groundcover.
Naturally, procuring reclaimed, repurposed, or recycled materials and products also has its place in achieving sustainable management of construction and demolition waste.
Likewise, proper material management is crucial in reducing material waste and waste management costs by streamlining the entire construction material lifecycle, from procurement to disposal.
And nowadays, effective material management practices can’t be achieved without the help of different software solutions and other technology.
One such solution is our asset and inventory tracking software, GoCodes.
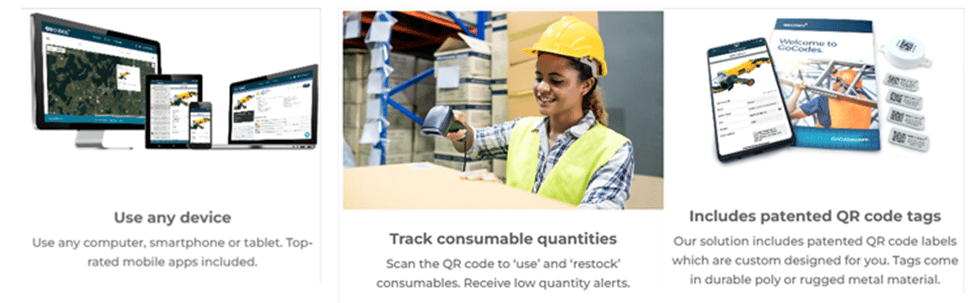
GoCodes is a cloud-based app that allows you to track the quantities of materials your business has in stock (or on specific jobsites) and receive low quantity alerts when restocking is required, which helps you ensure all crews have enough materials without creating excess waste.
Of course, there are numerous other software tools that streamline all construction project workflows, including sustainable material and waste management.
To sum up, minimizing material waste is a great way to reduce costs and boost your reputation as an environmentally friendly business.
Limit Rework on Projects
As rework on projects always leads to significant revenue and reputation loss, contractors should focus on limiting the occurrence of rework, thereby reducing its direct and indirect costs.
Although measures aimed at limiting rework span the entire project lifecycle, the most significant cost savings can be achieved in the project design phase.
As the construction industry spends around $178 billion per year on rework, it’s safe to say that almost no construction company can avoid its negative effects, but they can ensure that the biggest mistakes (and ensuing costs of rework) are prevented.
So, what can you do to avoid rework on projects and reduce costs? Here are five tips.
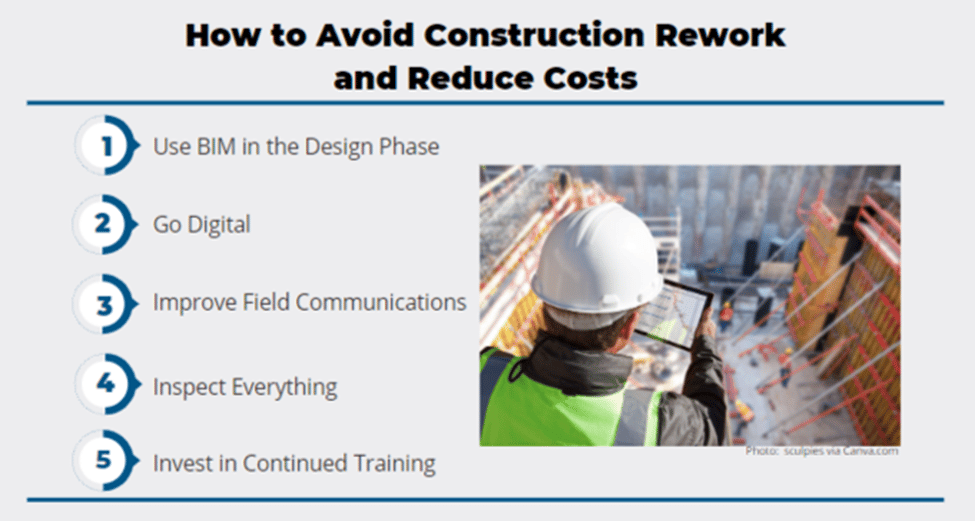
Using Building Information Modeling (BIM) in the project design phase is the ultimate tool for avoiding design errors that can account for up to 80% of all construction rework.
You probably already know that BIM software is used to create a digital 3D model of whatever will be built, allowing architects, engineers, contractors, and other project stakeholders to visualize all details of a construction project.
This enables them to identify design overlaps or clashes, which can then be rectified without ever causing costly rework.
It should be said that when designers use BIM, they report up to 73% fewer design errors.
At the same time, contractors report up to 79% fewer constructability issues on-site and up to 65% fewer defects at handover, which are, next to design errors, also major causes of rework.
There are many BIM-enabled software solutions to choose from, such as BIM360.
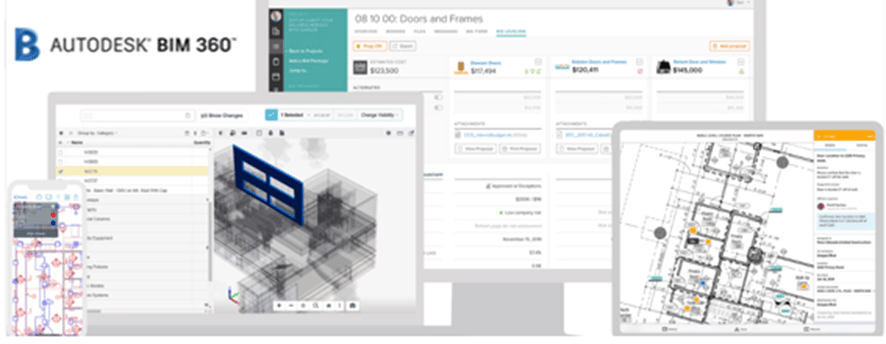
As BIM allows users to make changes visible to everyone, it also greatly enhances collaboration and communication between stakeholders, both of which are crucial when addressing rework on-site during the construction phase.
Other methods of limiting rework on projects include inspecting everything and investing in regular training, and research shows that training leads to 11-22% lower rework costs.
Overall, careful planning in the project design stage is paramount for limiting rework.
Coupled with enhanced collaboration and coordination between stakeholders throughout the project, it can significantly reduce the risk of rework, thus also reducing unnecessary costs.
Outsource When Necessary
Finally, outsourcing when necessary can prove to be more efficient and actually cost less than doing some things in-house.
Naturally, the key is determining if outsourcing is needed and what aspects of your construction operations could be outsourced if such a need arises.
Accounting services are a good example of operations that are often outsourced by contractors because handling them in-house is usually more expensive than hiring an accounting company that specializes in construction.
Of course, whether and what services can be outsourced, under what conditions, and at what cost should depend entirely on your specific needs and plans.
They will preferably be supported by a cost comparison between doing something in-house and outsourcing it to third-party providers.
As for other potential outsourcing candidates, here are some common examples, courtesy of Cat Rental Store:
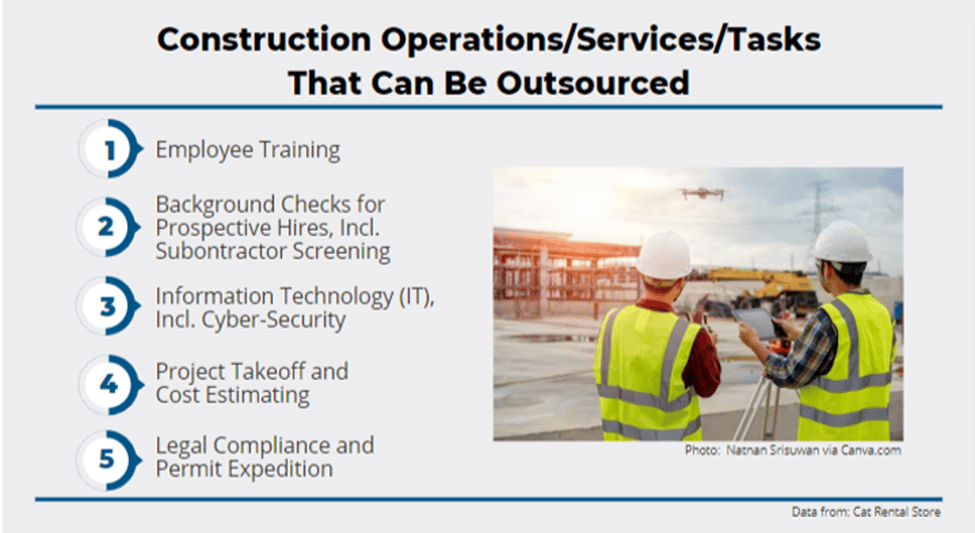
As each construction business is specific, there’s a host of tasks that could be outsourced at a lower cost than keeping it in-house, such as different cloud-based IT and cyber-security services.
Of course, another important aspect of outsourcing (as a way to cut costs) is knowing when it’s time to hire subcontractors for specific tasks that would require too many internal resources (or training) or could jeopardize the quality of other project works.
This requires a careful assessment of staff skills and qualifications, and a comparison of their estimated salary and training costs with the cost of hiring a professional to do the job.
Finally, one more way of outsourcing is to rent the equipment you don’t necessarily need to own, as you’re also externalizing purchasing, maintenance, and storage costs.
Hence, outsourcing some tasks can be an efficient way of reducing costs in your construction business.
Conclusion
As said in the opener, construction businesses had to keep their costs down even before the current price inflation, and that hasn’t changed.
If anything, it has become even more of an imperative.
After reading these tips, it could be said that all of them are directly or indirectly related to contractors seizing cost-saving opportunities offered by digital tools, software solutions, and other construction technologies.