Cost control is an essential part of any construction project.
It ensures that project managers avoid going over budget or the deadline by operating with accurate estimates of the necessary labor, material, and other resources.
However, cost control is also one of the biggest challenges in the construction industry.
If you’re among the many companies that struggle with staying on budget while conducting a project, take a look at these five tips for better cost control in construction we’ve gathered to help you out.
In this article...
Do Cost Estimation Upfront
Let’s start with the basics: do the cost estimation upfront. Why? Because working with precise initial estimations will inform the decisions you make once the project is already underway, ultimately giving you more control of the spending process.
This is something experts definitely agree on.
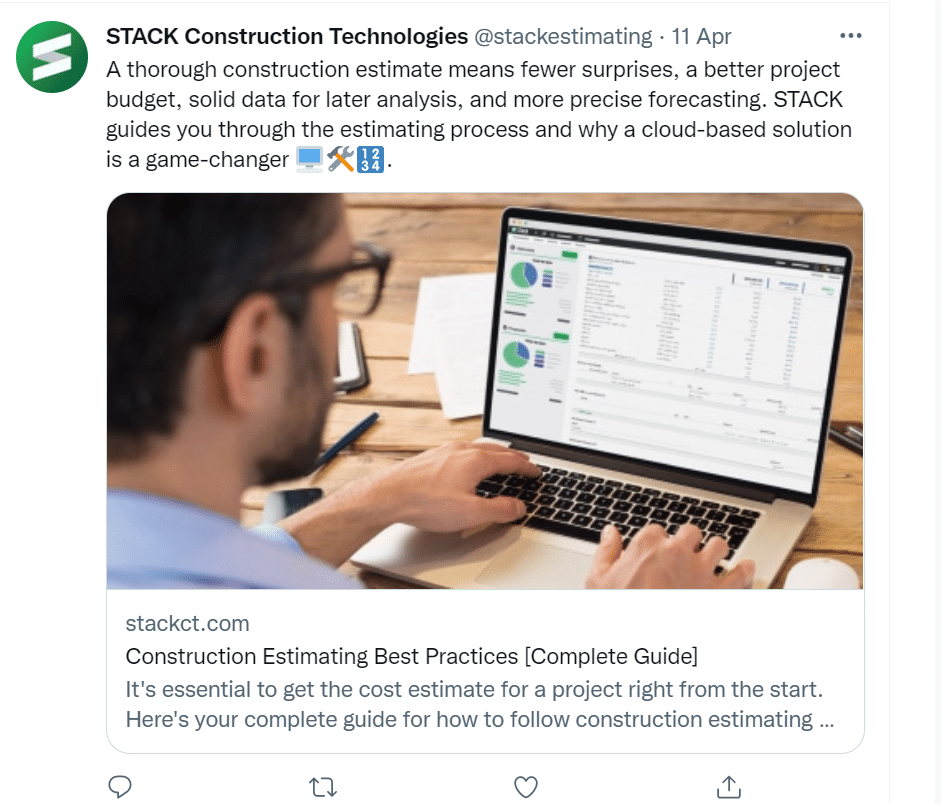
Moreover, the more projects you undertake, the easier it will be to make correct assessments.
With every project you work on, you collect valuable data.
So, look at total expenses from previous projects and use them to realistically predict the amount of labor, materials, equipment, and any other costs that will almost certainly be incurred.
For example, if you track labor productivity, you can predict how much it would take for a particular crew to do a specific job, as well as how much it would cost.
This, in turn, would go a long way in helping you plan future projects.
However, inaccurate cost estimations can have serious consequences, like losing competitive bids or damaging your reputation.
Nevertheless, there are many ways to improve the accuracy of your predictions through model-based estimation platforms.
These platforms rely on 3D models for their calculations instead of the traditional 2D drawings.
Nowadays, many construction companies use platforms of this type, including Pepper Construction.
They have recognized the flexibility they provide in making changes to project details in real-time, which leads to greater efficiency and accuracy and sets the stage for successful cost management in the future.
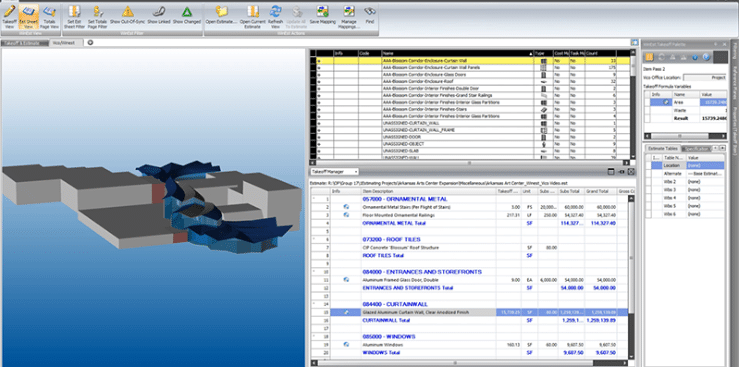
A picture is worth a thousand words; the experts from Pepper Construction claim that visualization improves accuracy, allows them to plan their projects better, and helps them complete them faster.
“At that point, our preconstruction team realized how much a picture is worth. In the 3D image, you can see all of the returns—a detail that inexperienced estimators can miss.”
In conclusion, planning your expenses in advance helps you stay on track and gets the entire project off to a better start.
Use Construction Management Software
In construction, as in many other industries, one of the most common ways to track project budgets is to use spreadsheets, with Excel being the most common.
The problem with these solutions is that they are siloed, resulting in a disconnect between cost management practices and change order workflows, and the rest of the project information.
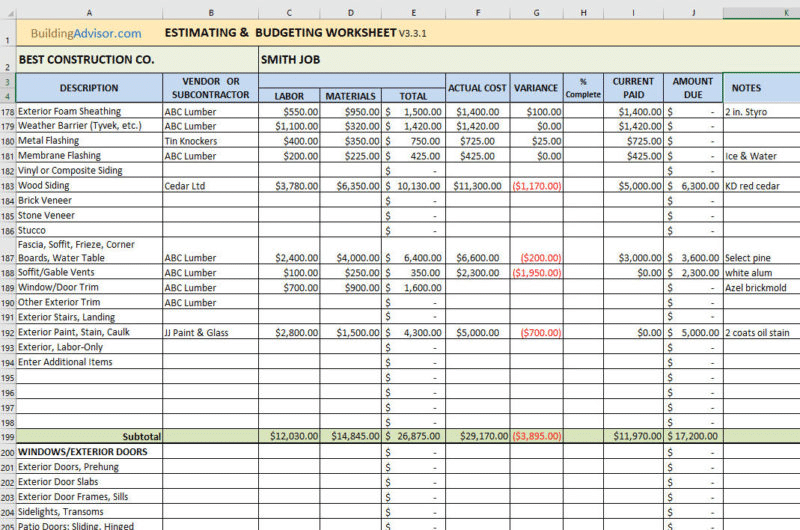
This increases the risk of errors, including duplication of effort, passing data to and from accounting systems, and the inability of team members to see data in real-time.
Craig Boudreau, director of project controls at a global engineering and construction company AECOM recognized these problems as well.
“I think with both Microsoft Access and Excel templates, you run into this situation where it solves the problem you have immediately in front of you, but it really doesn’t scale well. It also creates a single point of failure.”
Instead of using simple spreadsheets and wasting time and money, we recommend that you follow his example and opt for construction management software.
AECOM has reduced its expenses per project by 25% in two years through a combination of process improvement and system implementation.
The use of construction management software was a big part of that.
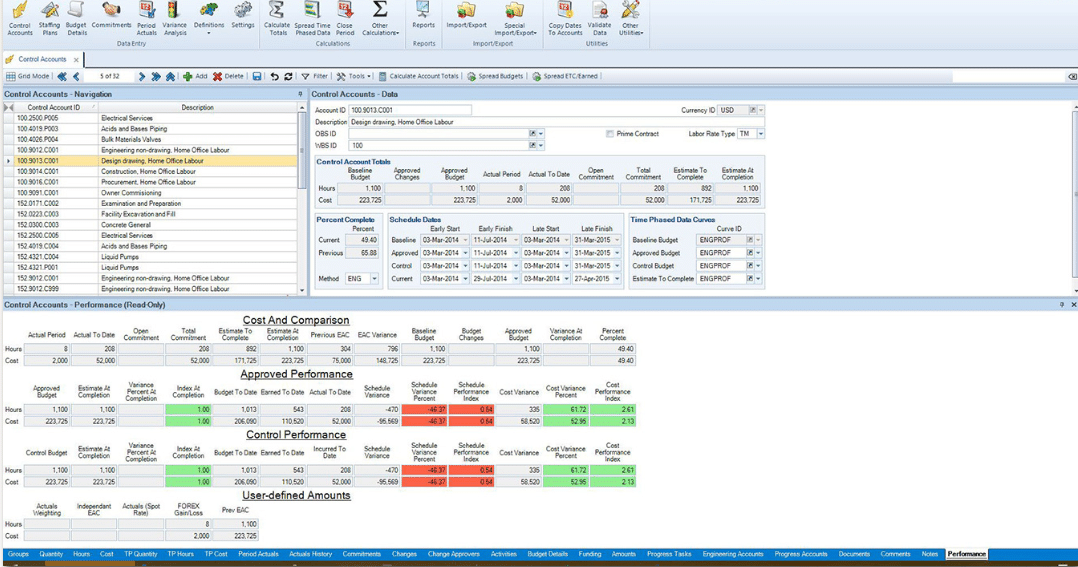
Construction management software can help you stay on top of project costs in several ways.
First, it can provide a single source of truth by centralizing all cost data in one easily accessible place.
For instance, with the use of Ares Prism software, AECOM was able to integrate its cost, schedule, and other data into one centralized location.
In addition, these platforms often offer solutions that allow for flexible customization of budget codes, hierarchical builds, and segment options.
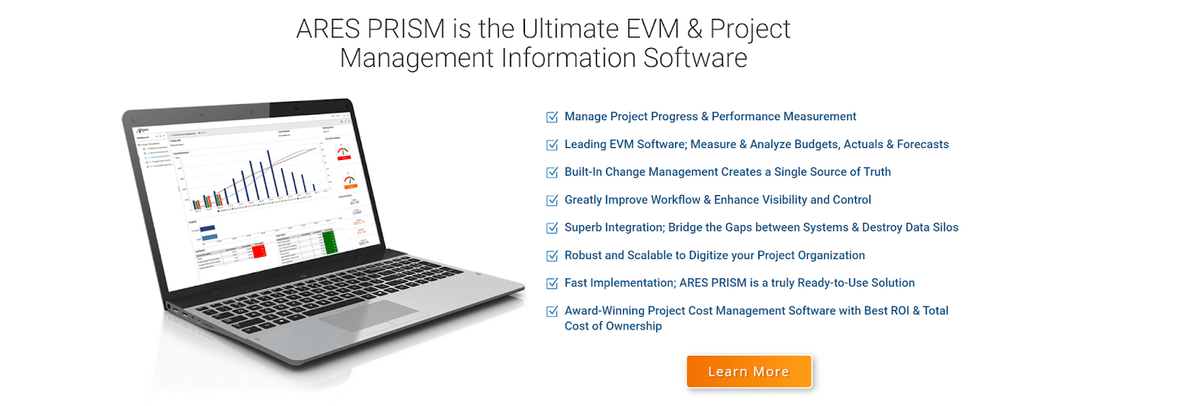
Another benefit of construction management platforms is increased transparency.
Cloud-based project management systems provide real-time access to information about the financial health of a project and allow team members to view a summary of all budget items and contracts.
So, cost control in construction is almost impossible with simple spreadsheets; you definitely need to start using construction management software to control your costs better.
Regularly Submit Cost Reports
Owners, contractors, and subcontractors have to remain well-informed about the project’s progress so that the appropriate decisions can be made on time.
Cost reports help streamline that communication.
Even though many construction companies submit their cost reports regularly, the frequency of those submissions is often insufficient.
This is why we recommend doing daily reports and incorporating them into your project cost reports.
However, many companies make the mistake of not keeping their daily reports detailed enough.
Often, daily reports contain only a rough description of the day’s activities.
They need to include more details, such as specific actions taken, the necessary equipment and the amount of materials used, hours worked, and so on.
You can see an example of things to include in your daily report in the image below.

After making a daily report, it’s time to make a quantitative analysis and enter it into the project cost report.
A cost report will generally include all the expenses incurred by the date of the report, as well as a forecast of the costs likely to be incurred during the rest of the project, in so far as these can be foreseen and estimated.
Finally, resources should be put aside for any unforeseeable circumstances.
In this way, you can identify costs that are starting to get out of hand or detect potential disruptions in the construction schedule and take action to mitigate the problem.
Constant monitoring helps you reduce the risk of any unpleasant surprises when it’s time to review your budget at the end of the project.
During this process, various tools, like the one in the picture below, can help you visualize cost-related risks by tracking budget items and cost-impacting factors as they arise.
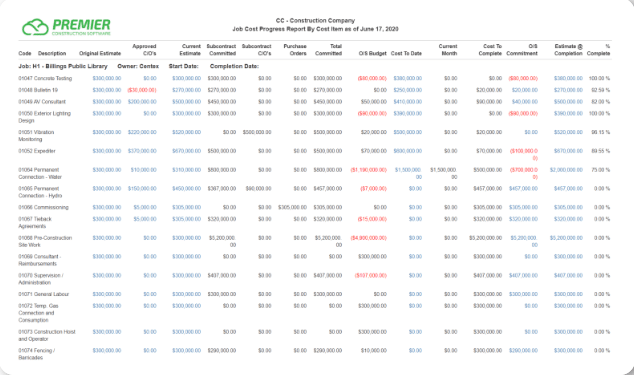
In short, it’s important that all stakeholders keep abreast of the cost reports as the project progresses so that if the project starts lagging or goes over budget, course corrections can be made on time.
Revisit the Cost Plans Regularly
Another tip we have for you is to revisit the cost plans on a regular basis.
Throughout the project’s life cycle, more information becomes available, and with continuous analysis, you’ll be able to determine if any changes are needed.
For instance, if costs are higher than expected in one aspect of the process, you can compensate by reducing costs in another area.
Consistently updating the cost plan will bring you many benefits.
For example, identifying and evaluating value engineering opportunities will become much more convenient, and approximate quantities will become easier to determine, whether for better cost estimates or for presentation design projects.
You’ll also be able to easily benchmark and inform bidders’ return on investment when cost plans are used as job-sum analysis.
Depending on the client’s specifications, you may need to consider the total lifetime cost of the project.
The total lifetime costs are different from the standard cost schedule, which typically considers costs through completion and delivery.
They include future costs such as:
- rent
- operating costs
- maintenance costs
- security costs
- repair costs
- management costs
For example, in the image below, you can see the total overall cost of ownership of a typical office building over a forty-year life cycle. Interestingly, the initial costs are only one-half of the total costs.
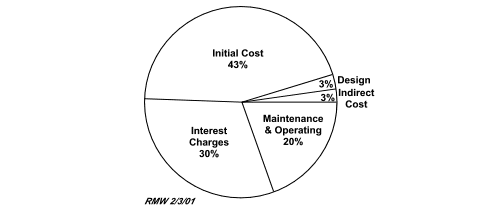
Be sure to keep this aspect of the project in mind when revisiting the construction plan.
After all, the project doesn’t end with delivery. Lifetime costs will inevitably occur and therefore need to be accounted for.
Also, remember that external forces can also change costs.
External factors such as inflation or material shortages can cause prices to change, so a project that was previously within budget may now be over budget.
This is especially true for the current state of affairs in the construction business, so definitely pay attention to how price increases will affect your project costs.
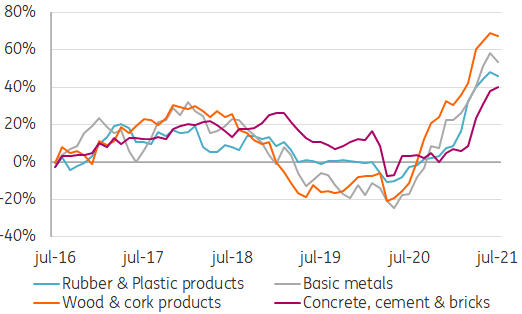
To sum up, by revisiting the cost plan on a regular basis, you’ll be able to spot the need for any changes early on and act accordingly.
Have a Contingency Plan
Finally, we come to contingency planning.
A contingency plan is a strategic plan created to help you deal with an adverse event that may or may not occur in the future.
In other words, it minimizes the impact of unforeseen events and outlines a plan for how normal business operations can be conducted without interruption.
With such a plan in place, you can face unexpected scenarios without endangering your budget.
A contingency plan is also referred to as a backup plan, disaster recovery plan, or “Plan B.”
When you have a Plan B, you are better able to respond to events and minimize the damage.
You can not prepare for something if you do not really know what you are trying to prepare for.
Sit down with your team and brainstorm possible events that could negatively impact your construction project.
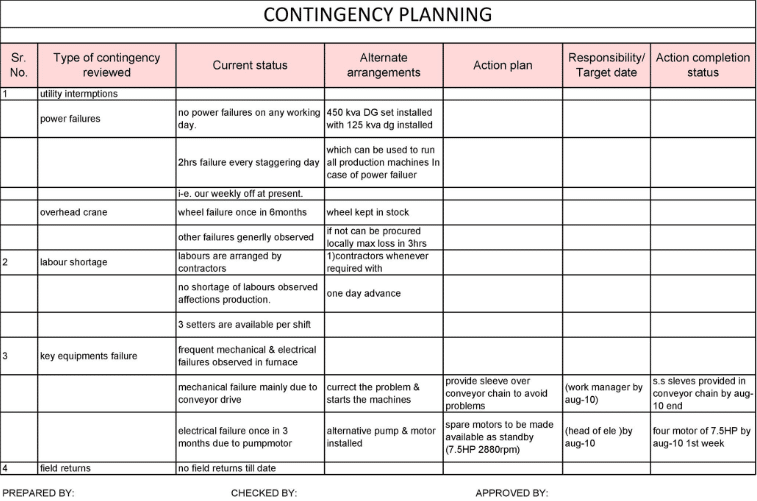
Think about all the possible risks to your project, including equipment malfunctions, natural disasters, sudden employee changes, and others.
You should list all predetermined costs for which the contingency will be used.
The list can include anything from incomplete designs, construction project delays, replacement subcontractors, price increases, and any other unexpected costs.
The contingency budget should also include a well-developed process for accessing unforeseen funds. It is best to have a detailed procedure for notifications, paperwork, and approvals.
The use of smart tools is on the rise to serve this very purpose.
They allow project managers to identify cost and budget risks before they become major problems.
For instance, tools such as Construction IQ have built-in machine learning and AI capabilities that feed into the BIM 360 construction management platform to identify high-risk issues that impact cost, schedules, quality, and safety.
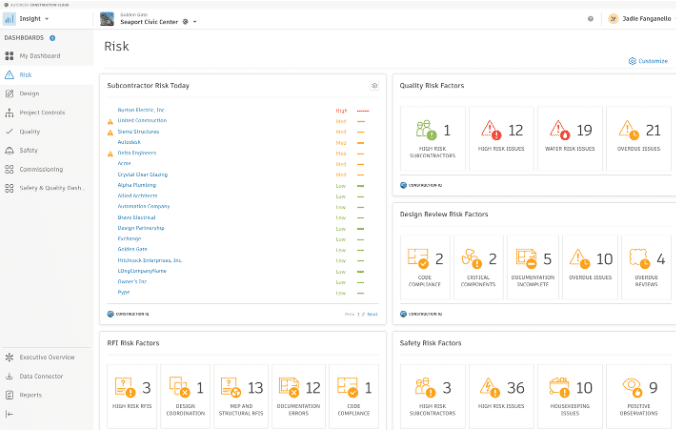
Established risk management procedures provide project managers with a plan of action they can implement if the project encounters any setbacks along the way.
Conclusion
The way you control costs in the project will ultimately determine whether you profit from it.
An accurate cost control plan and development budget are necessary to ensure success.
Basically, the use of cost control procedures is critical to ensure that a project is completed on time, within scope, and within budget, and by implementing the tips from this article, you’ll be able to achieve just that.