Whether you’re overseeing a small construction site or managing a large-scale project, one thing remains the same: the project needs to be finished on time, with minimal to no unnecessary downtime and operational glitches.
In other words, maintaining job site productivity and uninterrupted workflow is non-negotiable.
That’s why, in this article, we’ll explore five useful productivity tips, tailored specifically for equipment managers, that will help you achieve just that.
From asset utilization management to leveraging advanced technologies, we’ll cover essential strategies to enhance efficiency and ensure your machinery and tools operate at their peak performance.
Let’s begin.
In this article...
Optimize Equipment Utilization
One of the most important responsibilities of equipment managers is to guarantee that key equipment is at the right place, at the right time, and in the best condition possible, for every single project.
Failing in this duty poses a direct threat to overall operational efficiency.
Equipment shortages, whether due to machines being misplaced or insufficient in quantity, for example, translate to work delays, thus jeopardizing timely project completion.
Similarly, neglecting proper maintenance escalates the risk of unexpected machinery failures, yet again delaying teams and potentially grinding projects to a halt.
Surprisingly, research indicates that unplanned downtime due to inadequate maintenance is the primary productivity killer in the manufacturing industry.
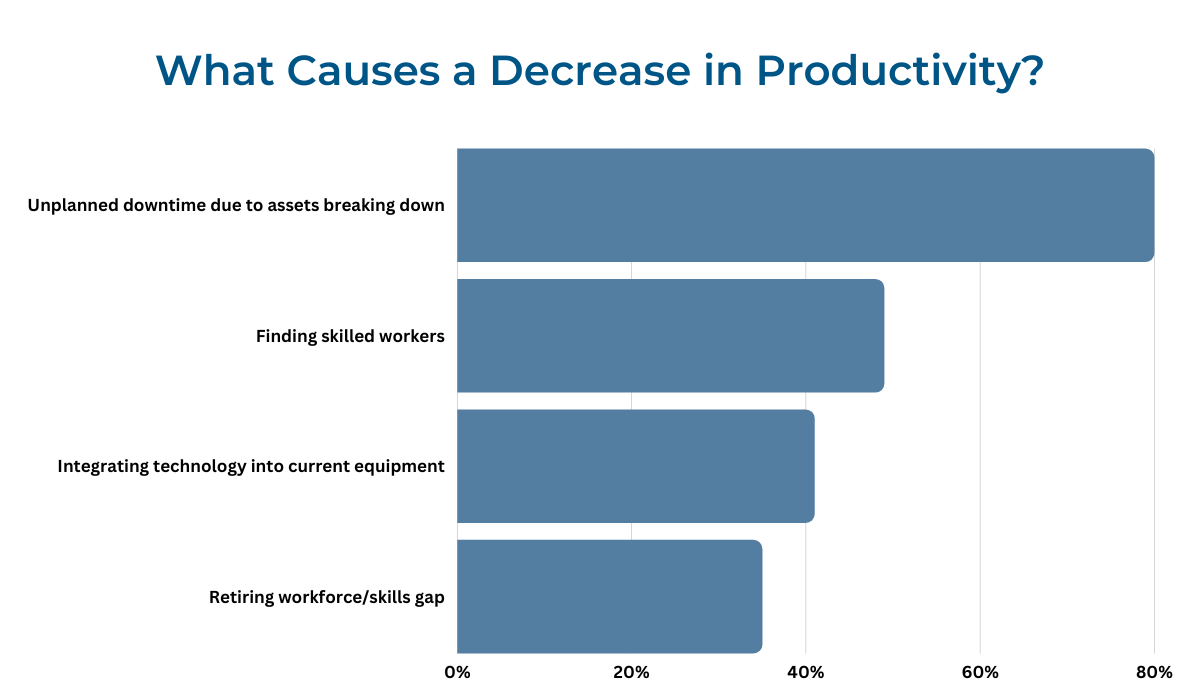
The construction sector, being equally asset-intensive, faces the same challenge.
So, how can managers navigate these hurdles and steer clear of unanticipated downtime and dips in productivity?
The answer lies in a twofold strategy that focuses on boosting equipment utilization.
Firstly, the adoption of a proactive approach to maintenance through regular inspections is paramount.
Known as preventive maintenance, this method addresses smaller issues through frequent repairs and servicing, stopping them from snowballing into major problems that could disrupt your operations.
Secondly, the implementation of robust asset tracking is equally important.
Lonnie Fritz, senior market professional at Caterpillar, emphasizes that effective asset monitoring goes beyond knowing just the quantity and types of equipment a company owns.
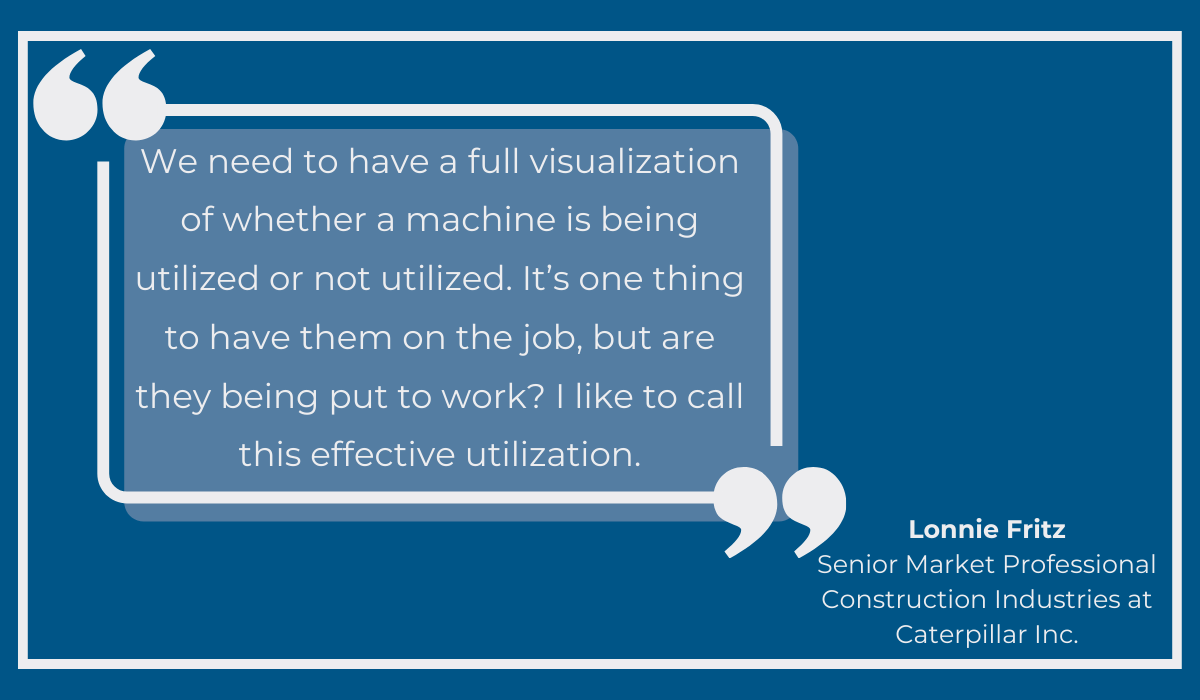
Instead, it involves tracking various parameters like location, status, condition, availability, and fuel usage.
Armed with this data, equipment managers are able to make better-informed decisions to optimize asset allocation and utilization.
For instance, if data reveals that an excavator lies idle at one job site, it can swiftly be redeployed to another.
If project deadlines are at risk due to equipment shortages, additional machines can be strategically rented to meet peak demand periods without unnecessary capital investment.
In construction, we often hear the saying: more uptime, less downtime.
The equipment manager’s key task is ensuring the company assets align with this goal, preventing hindrances such as breakdowns at critical moments or inefficient resource distribution.
In other words, the solution for boosting productivity lies in the delicate balance of a meticulous maintenance regime, strategic asset allocation, and proactive decision-making.
Make Use of Technology
The good news is that, as an equipment manager, you don’t have to handle everything on your own.
Today, numerous digital tools are available that streamline different processes on the job site, pushing overall productivity to unprecedented heights.
Neglecting these tools would mean forfeiting a plethora of efficiency-boosting benefits, including better-informed decision-making, effective resource allocation, and improved coordination among all team members.
Deloitte’s research on digital adoption in construction reinforces this perspective, with a majority of survey participants acknowledging how vital it is to embrace technology in order to stay relevant in the industry.
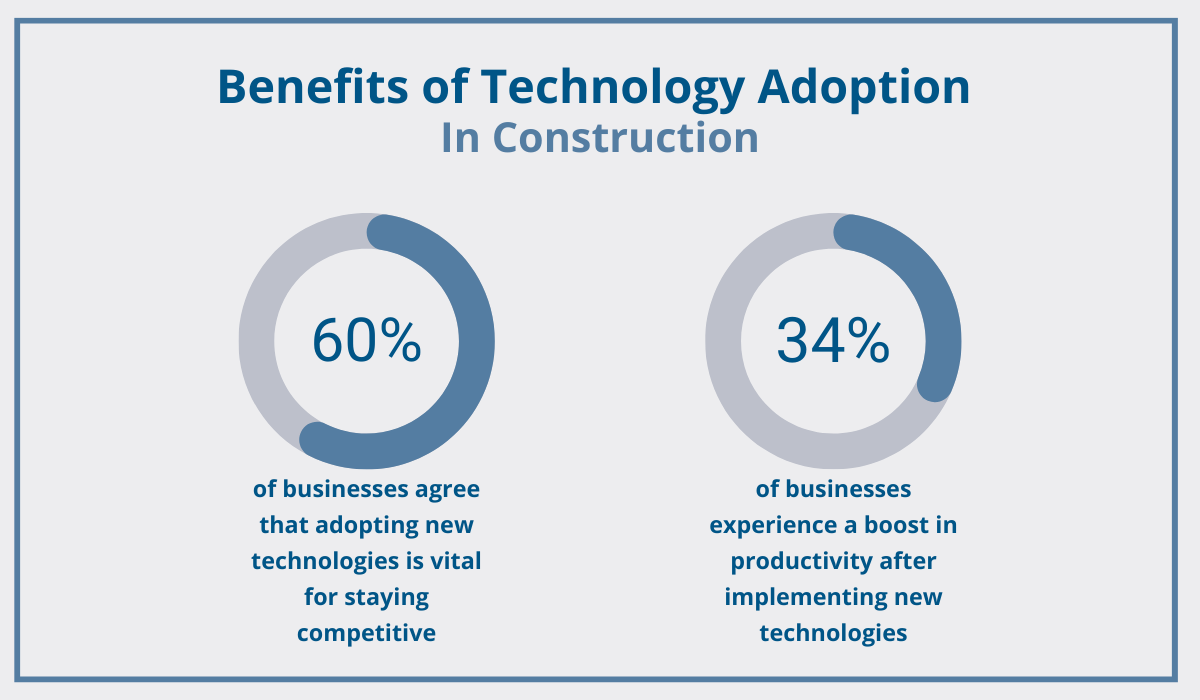
Interestingly, over a third reported tangible boosts in productivity through the implementation of tech solutions.
While the research takes a broad approach to technology, covering a spectrum of systems for various processes, we need to, of course, underscore the pivotal role of asset management software in the context of equipment management.
Our very own system, GoCodes Asset Tracking, offers a myriad of easy-to-use features designed to transform workflows and enhance productivity through streamlined collaboration and effective asset monitoring.
These include:
- QR code asset tracking
- GPS location monitoring,
- Easy-to-use check-in/check-out system
- Reporting
- Task management
Getting started with GoCodes Asset Tracking is a straightforward process—attach our QR code asset labels to your equipment and start scanning with our smartphone app.
This allows you to effortlessly view or update data and check assets in or out, with each update recording the location of the asset, too.
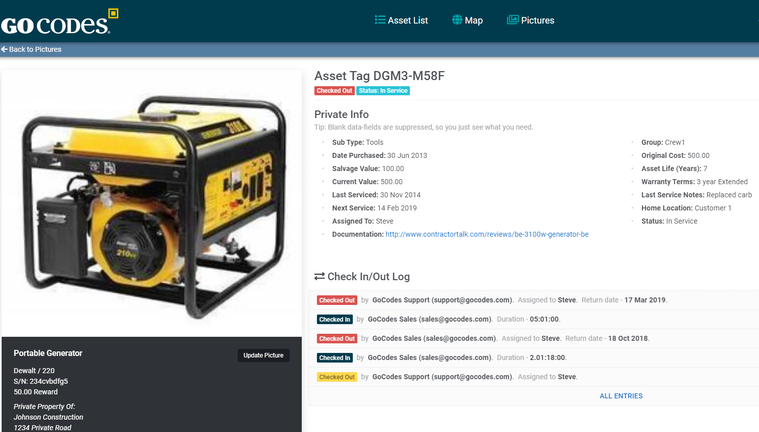
Consequently, you gain crucial information, such as who is using a particular machine, its whereabouts, and condition, as well as expected return time, all conveniently accessible in one place.
This facilitates better coordination among your workers and enables more efficient equipment allocation.
No more wasting hours looking for that missing tool.
At the end of the day, there’s no excuse for not using these modern systems, especially because they have the power to elevate construction businesses to whole new levels of efficiency.
Savvy equipment managers wholeheartedly embrace these systems, make the most out of them, and, in turn, reap all the benefits that come along with them.
Focus on Collaboration
Productivity in construction is heavily reliant on high-quality collaboration and communication among team members, a fact any experienced equipment manager will attest to.
Prioritizing cooperation not only enhances relationships with colleagues but also yields numerous benefits that help boost overall efficiency.
By focusing on an open and continuous exchange of ideas and data with operators, maintenance staff, and project managers, you can achieve:
- Smoother operations
- Timely project completion
- Reduced rework
- Adherence to budget constraints
- Improved coordination among workers
Just imagine a work environment where crucial information, such as equipment availability, usage schedules, or maintenance needs and tasks, isn’t shared or adequately communicated.
Such a scenario inevitably invites chaos.
Construction projects, being time-sensitive and subject to changes in design, scope, or simply due to unforeseen circumstances, require complete transparency and constant communication among employees.
Grammarly’s research further underscores this, revealing that poor communication in any industry leads to decreased efficiency, missed deadlines, and increased costs.
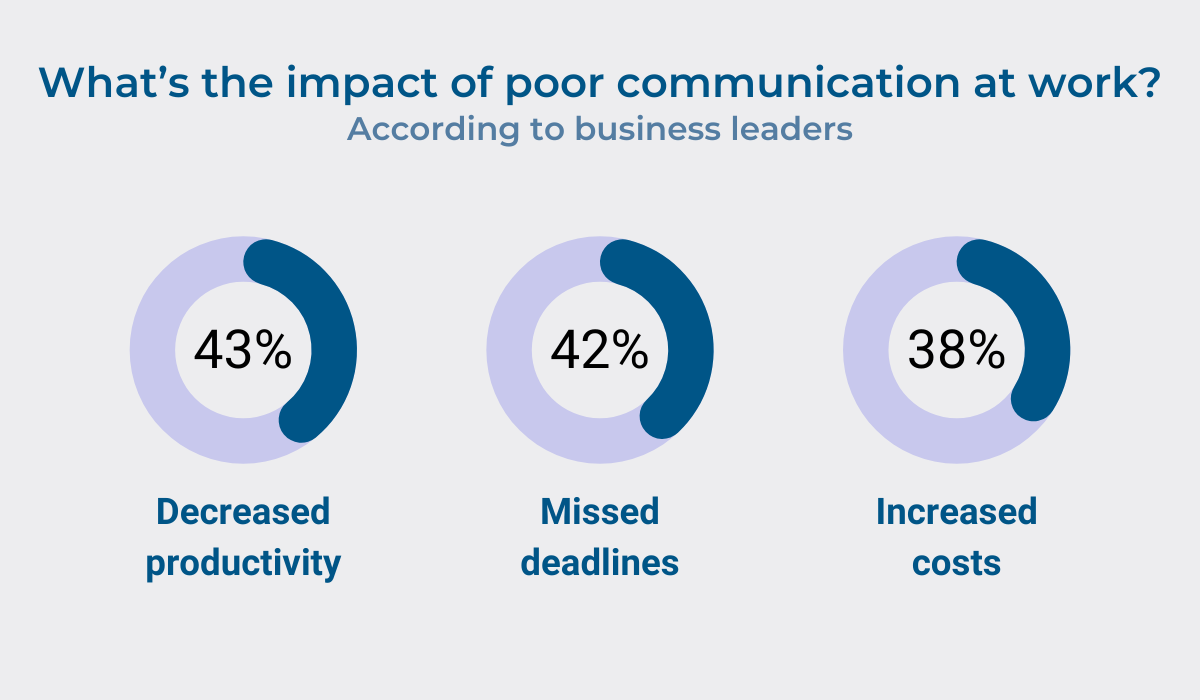
Therefore, to address such challenges and enhance collaboration, consider implementing systems that automate specific aspects of communication.
For instance, in the context of maintenance, workers often lose valuable time seeking assistance for a malfunctioning piece of equipment.
Making calls for hours, until you reach someone that can help, is just a waste of time in this case.
Instead, asset-tracking solutions that offer automated field service requests prove to be a much more effective solution.
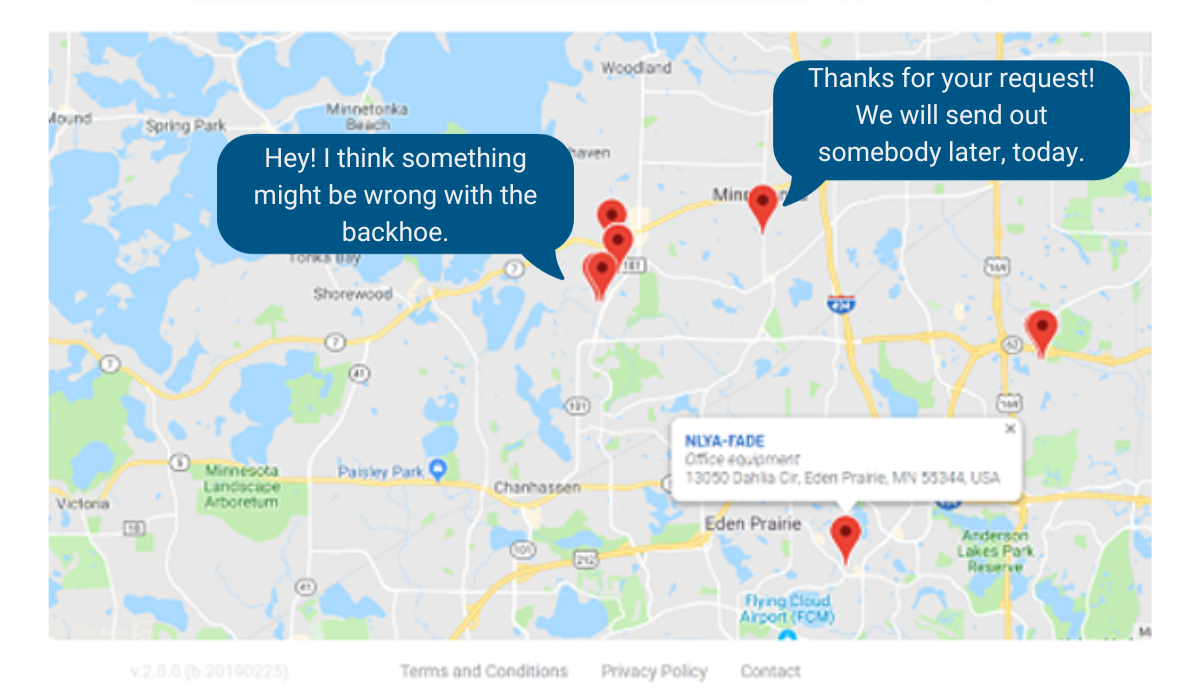
A worker can open the app, input the issue, and the designated maintenance personnel are promptly notified, with all the relevant details, including the asset’s location, the requester, and the description of the problem.
In short, the quest to improve team cooperation should prioritize not just the quantity but the quality of communication, too.
This is where automation comes in.
Overall, when it comes to enhancing productivity and propelling businesses toward success, the power of teamwork and effective communication shouldn’t be underestimated.
It’s the key ingredient that enables more streamlined operations, better coordination, and, ultimately, timely project completion.
Conduct Regular Safety Training
The symbiotic relationship between productivity and safety training is vital in construction.
By instilling safety protocols and guidelines within your team, you:
- Lower the potential for accidents and injuries
- Decrease employee absenteeism
- Reduce unplanned downtime
This, in turn, not only fosters a safer working environment but also amplifies overall efficiency by ensuring a steady and uninterrupted workflow.
But remember, educating your team on such protocols is an ongoing commitment, not a one-time task.
It requires regular and frequent updates to ensure your employees remain well-versed in all relevant guidelines, procedures, and regulations.
To make safety training more interesting and effective, consider incorporating technology specifically designed for this purpose.
Virtual Reality (VR), for instance, has proven to be highly efficient in reducing accidents and generally yielding better results with the learners by actively engaging them and enabling remote learning.
Andrew Kauser, Chief Product Officer and Senior Vice President of VR and online learning at Industrial Training International, also supports this approach.
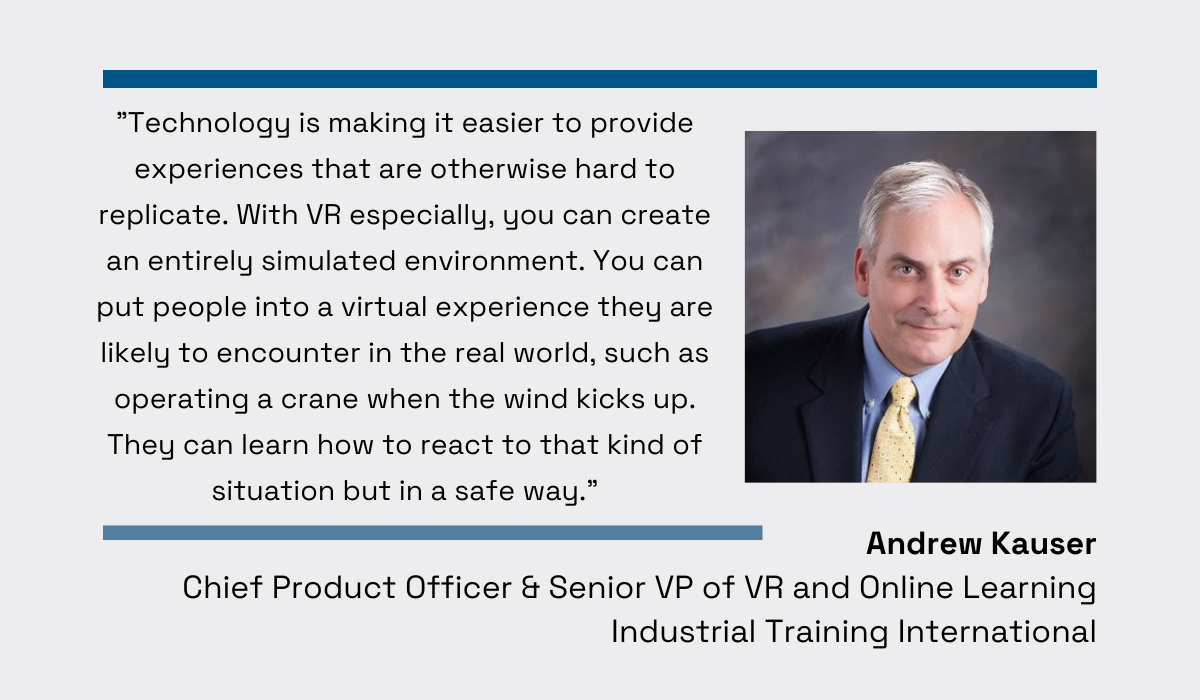
According to him, VR provides the safest means to experience real-world situations, better preparing individuals to tackle them once they actually occur on the job.
Ultimately, regardless of the chosen method—whether online or offline, using advanced technology or not—safety education is non-negotiable.
Making sure that employees comprehend, respect, and adhere to safety procedures isn’t only fundamental to operational efficiency but, more importantly, paramount to the well-being of the entire team.
Analyze Your Performance Metrics
To ensure your equipment is where you need it to be productivity-wise, it is crucial to systematically analyze its performance.
Vigilant monitoring of vital performance metrics and their in-depth analysis will help you pinpoint areas that require improvement, facilitating the strategic implementation of changes that will ultimately enhance efficiency.
This process can be succinctly summarized in three steps: measure, analyze, and implement.
You can’t analyze what you don’t measure, so, without tracking and keeping a record of key performance indicators (KPIs), you miss out on some important information that could potentially improve your processes.
Ivana Tudja, BIM and digital engineering lead at Mace, compares KPIs to health school, demonstrating how they aid in assessing the health of your operations.
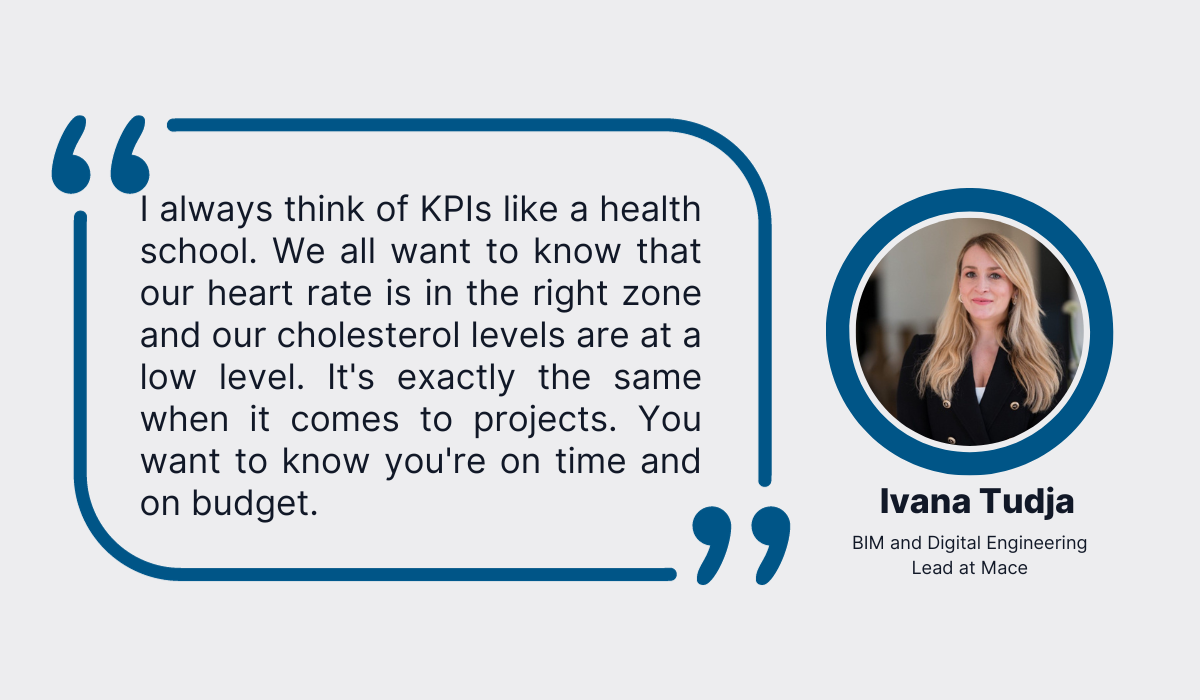
Data such as the number of repairs, maintenance costs, unplanned downtime, fuel consumption, or engine on/off times are, therefore, not just numbers on a paper or computer screen, but essential insights guiding decision-making and—if leveraged correctly—boosting productivity.
For a thorough analysis, though, it’s best to rely on software with reporting capabilities, instead of using error-prone manual methods such as spreadsheets.
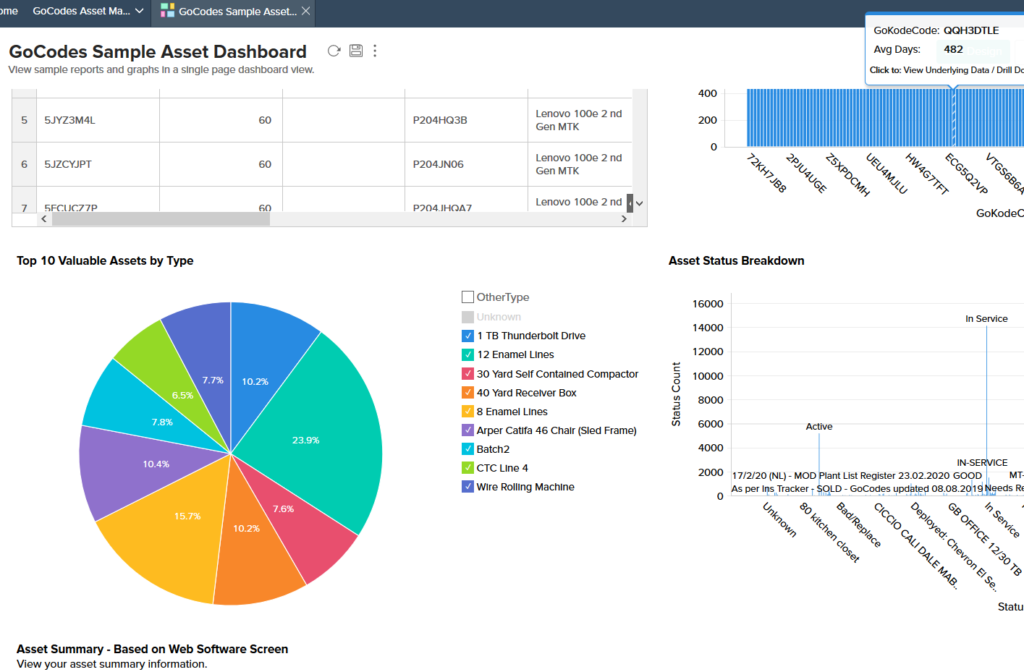
This will guarantee that the information you base your decisions on is accurate, complete, up-to-date, and presented in an easy-to-understand format.
With features like graphs, charts, dashboards, and customized reports tailored to your specific needs, these solutions make tasks such as maintenance planning, resource allocation, and optimizing utilization more manageable.
All in all, a defining characteristic of productive equipment managers is the ability to look at the current situation at a job site from all angles, analyze assets’ efficacy, and find the best course of action to make the most out of them.
They don’t just collect asset data; they use it to optimize and fine-tune every aspect of equipment management.
Conclusion
And there you have it, the ultimate equipment management toolkit to boost your productivity!
By incorporating these tips into your management approach, you not only enhance efficiency and productivity but also contribute to the overall success and profitability of construction projects.
Remember, a well-managed fleet of construction equipment is the backbone of a thriving construction operation.
Now, be proactive, embrace technology, and prioritize safety, and you’ll find your company reaching new heights in no time.