If you work in construction, you know how prone equipment is to breaking down.
Mechanical malfunctions that result in failure can stem from a lack of maintenance, harsh environmental conditions, poor fluid management, or improper employee training.
Whatever the case, if a machine stops working during construction, it can cause significant downtime, leading to extended production times and higher operational costs.
Therefore, to save money and prolong your equipment’s lifespan, you should strive to prevent construction equipment failure whenever possible.
In this article, we go through some of the crucial steps you should take to help keep your machines in working condition.
In this article...
Schedule Preventive Maintenance
Planning and following a preventive maintenance schedule can help avoid unexpected construction equipment failure.
According to a research paper from the International Journal of Engineering and Science Invention (IJESI), around 40% of total construction project cost overrun is due to poor equipment maintenance.
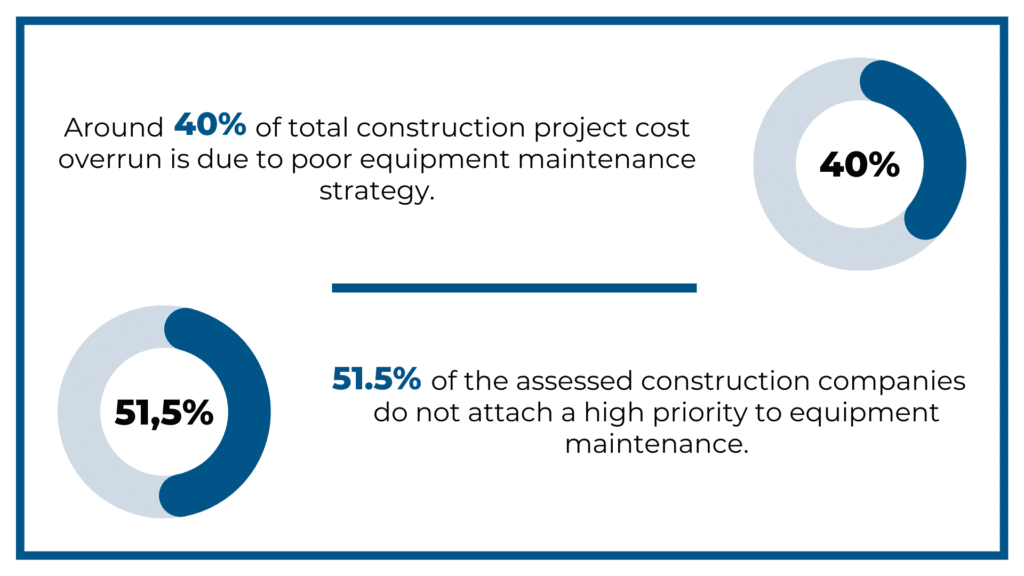
One of the contributing factors cited in IJESI’s study is that 51.5% of the assessed construction companies do not attach a high priority to equipment maintenance.
So, a well-thought-out maintenance plan can put you ahead of half of your competition.
But why is preventive maintenance the most suitable option?
It’s because this approach addresses the issues with the equipment before they become significant enough to cause your equipment to stop working.
Not every sign of potentially serious machine problems is readily apparent to workers.
What is more, they are sometimes unable to react even if they are properly trained to look for warning signs.
A preventive maintenance routine means that your assets are checked and repaired at regular intervals—which are calculated by usage, history, and the original manufacturer’s recommendation.
If you follow the recommended procedure, you can catch on to any equipment damage early on, instead of letting it escalate.
This way, you will have a higher chance of preventing unnecessary breakdowns during projects, extending your equipment lifespan and saving you time and money.
To ensure you keep up with the maintenance schedule, you can use an equipment tracking system like GoCodes.
GoCodes comes with QR asset tags which can be scanned to reveal the asset’s manufacturing date and maintenance history.
You can use this data to make accurate maintenance schedules for each piece of equipment.
GoCodes’ system also has a notification feature that alerts you of upcoming repair dates and saves you time on manual checks.
Overall, preventive maintenance can keep your equipment in good shape for a long time, and using an equipment tracking tool to help you manage the maintenance schedule will make this task easy and straightforward.
Be Mindful of Environmental Conditions
To avoid construction equipment failure, it is essential to pay attention to the environmental conditions in which your equipment operates.
Even large machinery designed for outdoor work in less-than-ideal environments can suffer damages brought on by extreme weather.
In summer, excessive heat and extended exposure to sunlight can cause machines to overheat.
Hot oil gets even more heated when passing through hot metal, leading to pump flow problems and wearing down the machine.
Furthermore, coolant systems can only handle so much heat before they become ineffective.
If the temperature becomes too high and the machine is unable to cool down, it will simply stop working.
Winter conditions can also be as damaging to your equipment, if not more so.
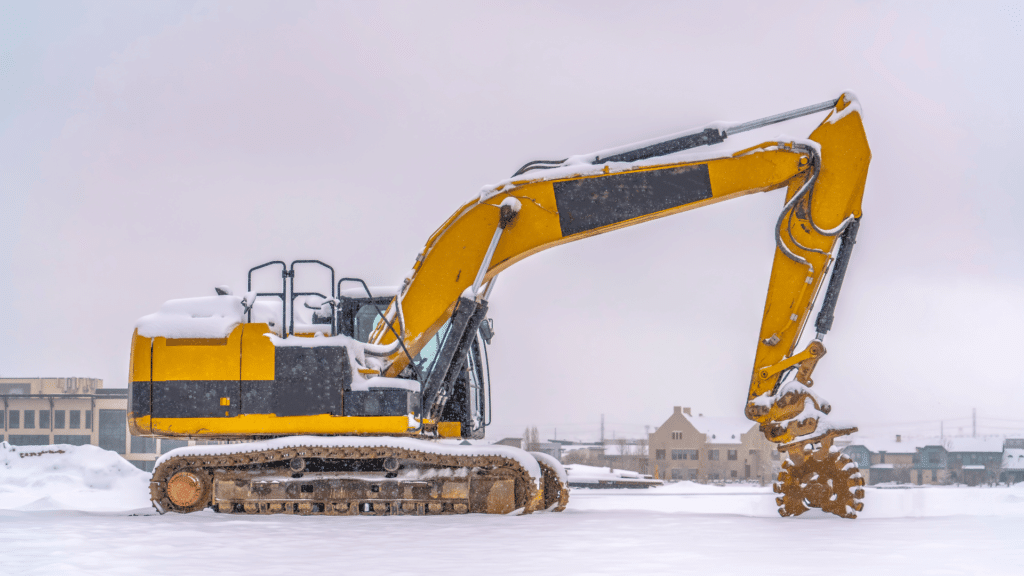
First of all, extreme cold, combined with low visibility, is taxing on the battery, causing it to drain more quickly.
Also, in low enough temperatures, your machines will need defrosting before starting daily operations, which requires a lot of energy.
And if your workers aren’t used to working in similar conditions, they may overlook these factors and quickly drain the battery, leaving the machine inoperable.
Another important point to consider is that intense cold affects the viscosity of fluids like engine and hydraulic oil, which are essential for machines to function correctly.
However, there are steps you can take to mitigate these issues.
If the job involves working in extreme weather conditions, you should schedule maintenance more frequently to make sure all your fluids are clean and at the proper level.
Moreover, you should always properly store your equipment, so it doesn’t get exposed to the damaging elements when idle.
Your employees can leave the equipment in a building, like a warehouse, but even an ordinary shed would make a difference compared to leaving it outside.
Failing to protect your equipment from environmental conditions can lead to equipment failure, which can also happen if you don’t regularly clean it from excessive dirt, mud, or other debris.
Let’s cover that topic next.
Keep Your Equipment Clean
To prevent unexpected equipment failure, your machinery should always be kept as clean as possible.
Construction sites are full of various contaminants that, if not removed on time, can cause damage to multiple parts of your machines.
Cameron Jewell, an assistant field service coordinator for Caterpillar, manages a fleet of Cat machines and is acutely aware of the importance of regularly cleaning your equipment.
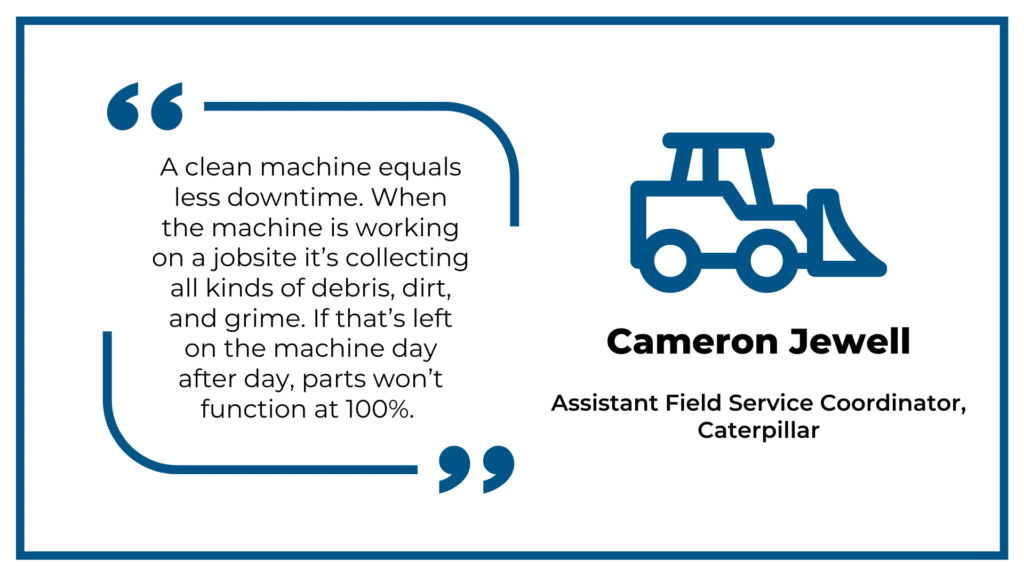
A buildup of dirt and grime around the moving parts can limit your machine’s range of motion, if not block it altogether.
Jewell also warns about rocks and larger debris which become stuck in the machine’s undercarriage, causing wear to some parts and shortening their usability.
Cleaning your machines also keeps them cooler, as mud, dirt and grease are notoriously good at trapping heat.
If the equipment is being used in hot weather, giving it a thorough cleaning can go a long way in avoiding machine failure due to overheating.
How you go about cleaning your equipment is up to you, but here’s some basic advice everyone should follow.
It is vital to check that its seals and filters are in working condition. After all, they are the first line of defense in stopping foreign elements from entering the machine’s more sensitive parts.
If they leak, other parts have a higher chance of getting contaminated as well, meaning a lot more work and time will be required to clean them.
And another good idea is to invest in specialized cleaning equipment. Water cannons and pressure washers are extremely useful for cleaning large, heavy assets.
They can help you eliminate most of the debris quickly and effortlessly, leaving just small areas that require manual sponge-washing.
Following these two steps should generally result in a clean piece of equipment, prolonging its lifespan and reducing the need for costly repairs.
Be Sure to Check the Fluids
Checking the fluids is another major component in avoiding construction equipment failure.
Shell, one of the world’s largest oil companies, commissioned a survey of construction sector staff that work with greases and lubricants, which found that more than 56% of the participants experienced equipment breakdowns due to ineffective lubrication.
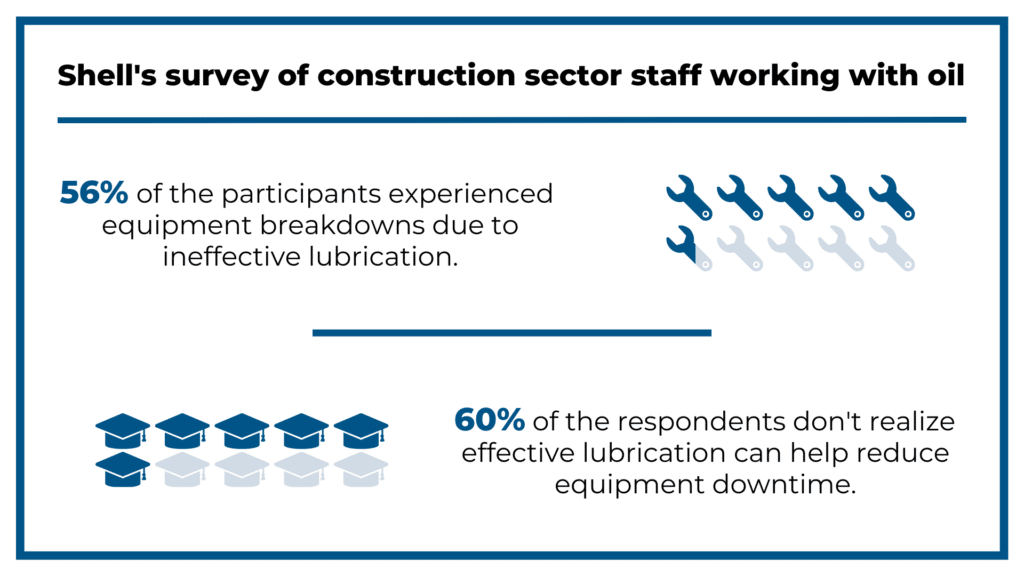
This is hardly surprising given that 60% of the respondents don’t even realize effective lubrication can help reduce equipment downtime.
That is why it is important to know how fluids affect your machine’s health and what you can do to prevent system failure due to improper fluid management.
First, fluids like gear oils, hydraulic and transmission fluids, coolants, etc., should always be used according to the original manufacturer’s specifications.
These can include the exact type and brand, as some fluids are made specifically for one manufacturer’s machines or even a single machine.
Using a cheaper or mixed variation of the product is potentially damaging to various parts of the system.
Manufacturers also usually specify the optimal fluids to use for different seasonal and environmental conditions, and the level at which the machines need to be maintained to stay effective.
However, even if you are using the prescribed type of fluids as intended, if they get contaminated, it could cause severe problems with your equipment.
For example, dirt, dust and metal mixing with hydraulic fluid can harm or disable your hydraulic system.
And since construction equipment relies heavily on hydraulics, this impairment can render your machine useless.
Contamination by water is also potentially dangerous, as it reduces the fluids’ lubrication properties, leading to increased friction around the machine’s moving parts.
By performing regular checks on fluids and analyzing how they perform, you will be able to determine if you need to clean them out or replace them altogether, saving the machine from further erosion.
Inspect for Wear and Tear
Regularly inspecting for wear and tear can also prevent construction equipment from suddenly failing.
Wear and tear is damage to a physical asset that inevitably happens as the result of daily usage.
It is a slow and gradual process, but if left unchecked, it can lead to equipment malfunctions.
Take excavators, for example.
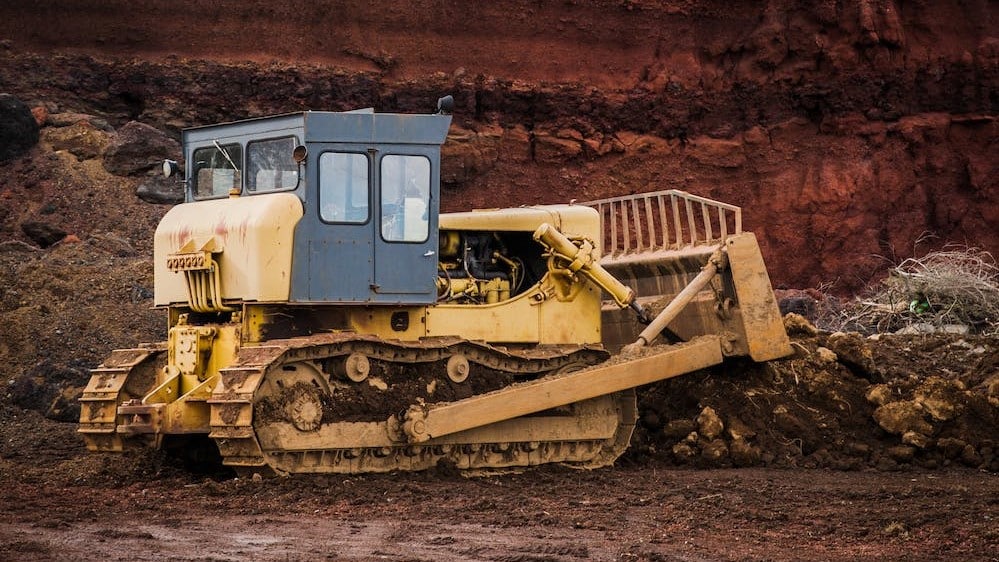
They are designed to operate in rough conditions, regularly in contact with dirt, mud, rain, and all kinds of debris.
Their tracks can get badly worn out over time, and therefore lose traction or power, causing your machine to work harder and strain.
Furthermore, bolts could loose, leading to trackpads falling off or breaking the track rail.
And in case of oil leakage, tracks will receive insufficient lubrication and jam, stopping the machine from moving.
However, if you perform regular track inspections, you can decide if you need to tighten the bolts, stop the leakage or replace the track, avoiding more dire consequences down the road.
Because heavy machinery contains many metal parts, corrosion is another cause for concern.
Lubricant oxidation produces acids that, over time, degrade metal components, break seals and cause damage to other components.
And humid environments and exposure to water also contribute to corrosion and therefore speed up the spreading of rust.
So, keep in mind that conducting regular checks of wear and tear on your equipment can reveal potentially harmful problems.
This will help you in the long run, allowing you to deal with these issues on time, before they become too complicated and expensive to solve.
Train Operators on Proper Equipment Use
Avoiding construction equipment failure can be as simple as training your operators on proper equipment use.
According to a survey conducted by FM Global, which included 200 business leaders at Fortune 500-size companies, lack of proper training accounted for 37% of the risk associated with equipment failure.
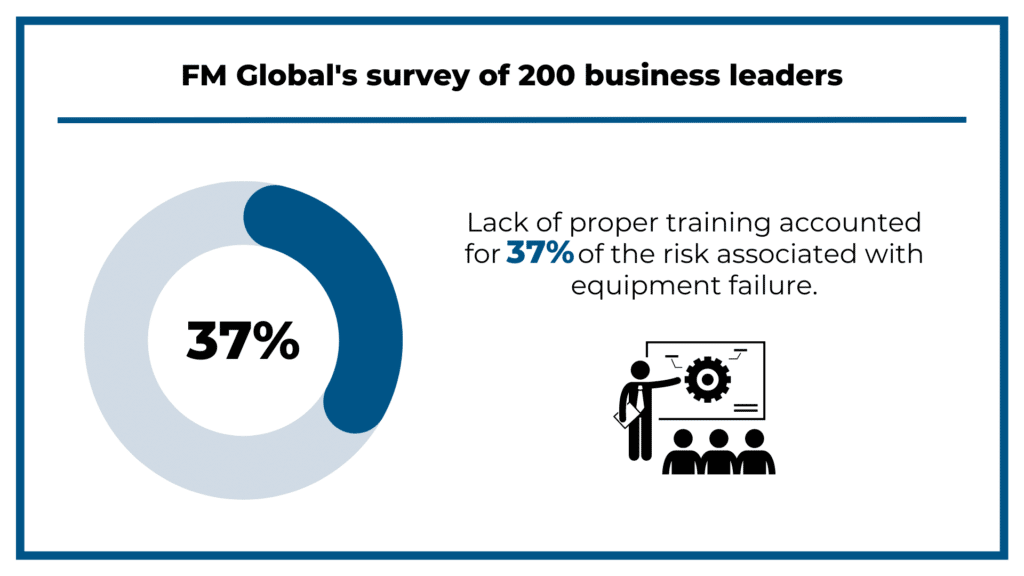
Luckily, many organizations offer legitimate certifications and operator training for specific machines, like the National Commission for the Certification of Crane Operators (NCCCO).
Whichever organization you pick for your employees, make sure it follows the Occupational Safety and Health Administration (OSHA) operator training requirements, which provide a legal standard for operating specific types of equipment and general occupational safety.
Proper training will usually include a thorough review of the operations manual, a demonstration of appropriate operating procedures, and detailed instruction in the use of controls.
Workers will also be taught basic troubleshooting techniques and what to do in case of an emergency.
An operator unfamiliar with his machine’s limitations can overwork it or use it in ways that it was not intended for, causing mechanical problems or a breakdown.
Other than being educated on the proper ways to use their equipment, operators are trained to spot potentially critical damage.
If a problem within a system exists, machines will typically give out warning signs.
Flashing lights could indicate low fluids, dangerously high temperatures, or issues with pressure.
Out-of-place noises or smells could mean that certain equipment parts are starting to malfunction.
In each of these cases, if a person operating the machine ignores obvious warnings and doesn’t take the necessary steps, it can lead to equipment failure in the field.
Conclusion
To keep a steady workflow and optimize costs on your construction projects, you should consider strategies to avoid equipment failure.
When a heavy machine breaks down in the field, it can temporarily shut down production, require expensive repairs, and stay out of commission for days or even months.
Investing in employee training, more regular checkups or washing equipment might seem costly at first, but it will save you time and money down the road.