Equipment maintenance KPIs are a step towards reaching your goals, no matter what kind of company you’re leading.
They help you understand what you need to do to improve your company’s performance.
First, however, you have to ensure that each KPI relates directly to a goal and that it is measured using specific metrics.
This article will explain what maintenance KPIs are, how you can set goals and choose the right KPIs for your business, and describe seven of the most used upkeep performance indicators.
In this article...
What Are Equipment Maintenance KPIs?
The key performance indicators (KPIs) in equipment maintenance determine how efficient your maintenance processes and your team are over time.
This data helps you understand whether you need to make some adjustments to reach your maintenance goals.
For example, you might want to reduce your maintenance costs as a company, which is a maintenance goal.
Your maintenance KPI will help you understand how successful your strategy is, i.e., whether your work affects this goal and reduces costs.
Maintenance KPIs are relevant, quantifiable, objective, and attainable, among other things.
What this means is that the indicator you’ve chosen relates to your goal and affects it in a measurable way.
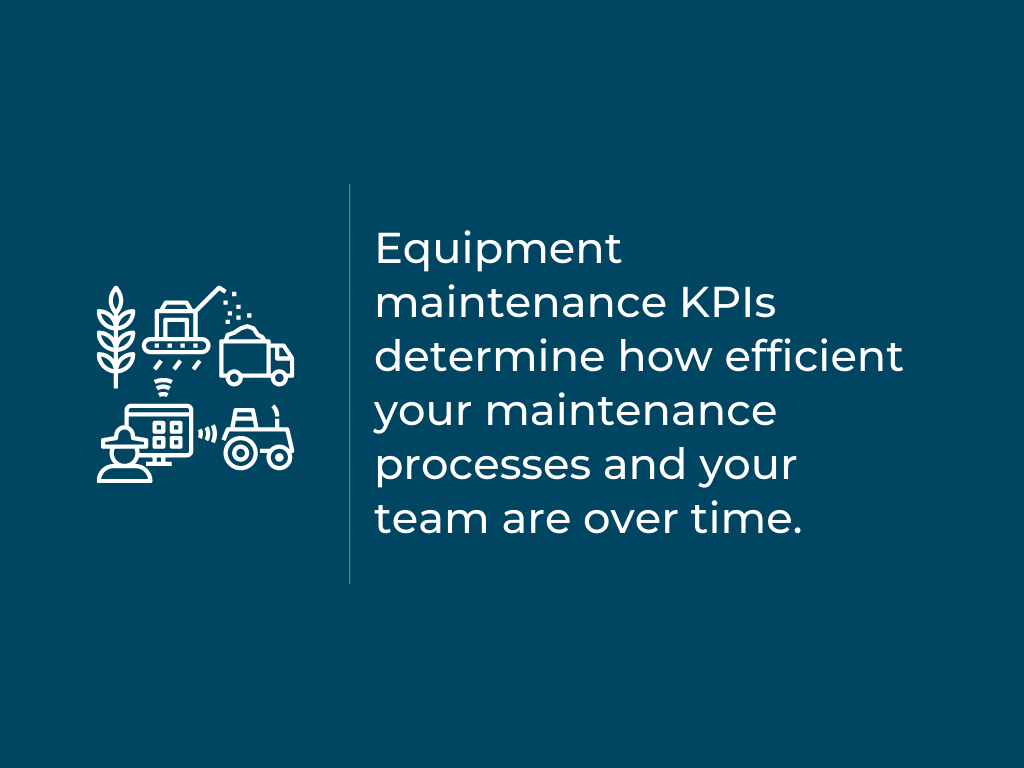
The calculations of such KPIs are expressed in numbers, meaning that you can track progress and compare the results to the industry or company standards.
The objectivity of a KPI lies in the fact that they are indicators used without subjective additions.
Whatever you choose to measure needs to be something that you can continue evaluating over time.
If an indicator is attainable, you can reach the set goal and notice the progress you’re making towards achieving that goal.
When a KPI has these characteristics, you can be sure that it will serve its original purpose and help you understand if you’re on the right track towards your goal or not.
How to Choose the Right Maintenance KPIs?
The process of selecting the right KPIs for your company might be challenging, but it brings many rewards.
When you keep track of the maintenance KPIs that are relevant to your company and relate to your goals, you have a clear way of understanding whether you are on the right track.
KPIs represent the numbers you have to hit if you want to achieve your goal.
The first step in choosing maintenance KPIs is understanding your goal.
Think of what you want to achieve and how you can improve.
For example, you might aim towards higher productivity. A maintenance KPI related to such a goal is increasing downtime—the less downtime, the higher the productivity.
Experts suggest sticking to a four to ten KPI limit to ensure that you have a manageable amount of priorities that you can work on and consistently measure.
Over time, your goals and, consequently, your KPIs can change.
It would be wise to consult your company managers to set the right KPIs for your company and teams. The managers can have valuable insight, which you can use to shape and select a KPI.
Keep in mind that you need to have a plan of action for each KPI, decide which metrics you will use to measure your progress, and set milestones, so you’re able to track progress efficiently.
Defining SMART Maintenance Goals
When setting goals, and consequently, the related KPIs, many companies use the SMART principle.
The acronym stands for:
Specific
Measurable
Achievable
Realistic
Timely
These are the characteristics the companies should aim for when setting them.
When a goal is specific, it means that your maintenance objectives are clear, defined, and coherent.
Anyone involved understands what each target is, what steps to take to achieve it, its time frame, and who is responsible for it.
In other words, when you express your objective in a clear and concise manner that leaves no room for doubt, you’ve managed to make it specific.
This goal also has to be measurable—there has to be a way for you to measure the results to determine whether you’re moving forward and at what pace.
If there is no consistent way to calculate your progress towards it, it will not produce results and will only hold you down.
You should select the most applicable metrics for each goal to ensure you have a way to measure your effectiveness.
Having an achievable goal means being able to follow through with it.
Of course, the objective shouldn’t be so easy to reach as to be insignificant, but it shouldn’t be impossible to do either, as this is demotivating and doesn’t help your company improve.
If you can accomplish your objective within the given timeframe without investing in additional resources, that objective is realistic.
Let’s say you can achieve your goal only if you hire more people, increase your budget, and implement a whole new system.
In that case, the goal needs some adjusting, as working towards it as it is currently defined would only mean wasting money and resources on creating the conditions for the objectives.
Finally, a timely goal is one you can accomplish within the established deadlines.
Without a deadline, it’s a lot less likely you will ever reach your targets. Defining a timeline helps you put things in perspective and work towards achieving the goal.
Goal-setting takes some time and energy as the outcome has to be SMART, but it benefits you in the long run.
Crucial Maintenance KPIs
Now that you understand how to set a clear, achievable goal, you need to decide which maintenance KPIs to focus on if you want to monitor your progress.
The following KPIs are the most frequently used and crucial for maintenance, and you can use them to see how effective you are at reaching your own company goals.
Unscheduled Downtime
Efficient maintenance processes, whether scheduled or unplanned, help you eliminate downtime.
Unscheduled downtime is an unexpected breakdown or failure which leads to you having to stop using equipment so your team can repair it.
The less such downtime you have, the more productive you are.
By eliminating downtime, you ensure that you don’t have to stop working with the asset and wait for the team to fix and test it before deciding it’s safe to use again.
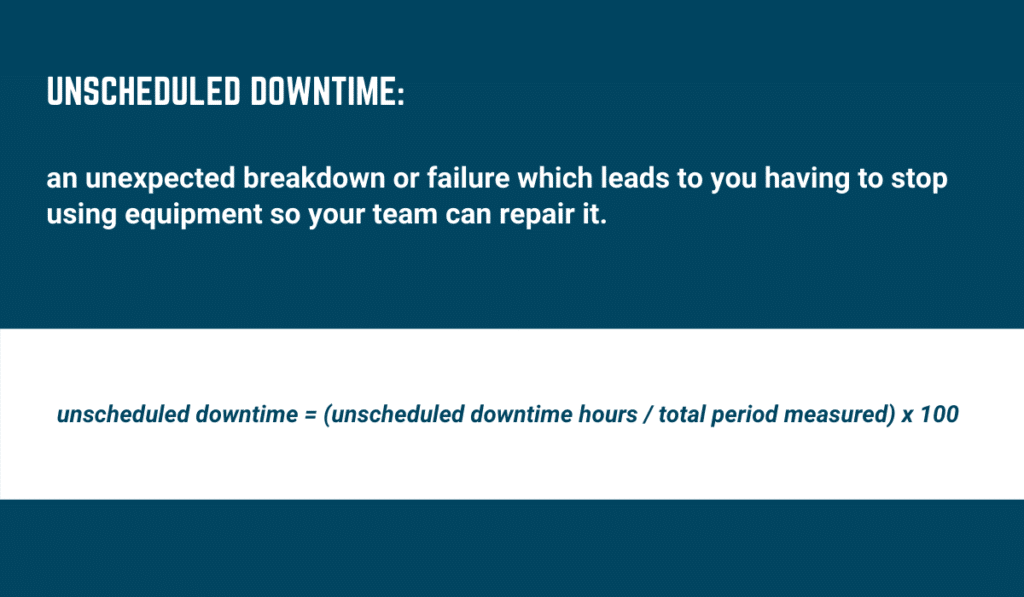
When your scheduled upkeeps are successful, your unscheduled downtime should be down to a minimum as the team discovers issues on time or prevents them from happening.
If the numbers are high, you need to dig deeper into your upkeep processes and find why your equipment breaks down so often.
You can calculate the percentage of unscheduled downtime hours using this formula:
unscheduled downtime = (unscheduled downtime hours / total period measured) x 100
The total period measured includes all maintenance hours, both planned or unscheduled.
The formula lets you understand the percentage of downtime you didn’t plan for or prepare, which causes monetary losses in terms of parts, replacements, and staffing.
Suppose your team worked on maintenance for 25 hours this week, but out of those 25, 5 hours were unplanned.
According to that, your unscheduled downtime percentage is 20%, which is 10% above the standard.
The unscheduled downtime KPI lets you understand how many hours your team has spent on unplanned maintenance, which points to different maintenance process issues.
Maintenance Backlog
The maintenance backlog KPI lets you understand how behind you are on your maintenance tasks.
This KPI is essential as it lets you understand the workload of each employee.
If your employees are overburdened, you risk low morale, decreased productivity, and longer downtime periods.
When you calculate the backlog, you can determine whether you have a problem with equipment, spare parts, current maintenance processes, or whether you need to hire more technicians.
As many as 87% of businesses choose to outsource some maintenance tasks.
This helps them reduce their backlogs because of a lack of workforce.
After you implement changes to upkeep and outsource or hire more people, the KPI will show your progress or the lack thereof.
To calculate upkeep backlog, consider all the planning your team does and the time it takes to repair the asset and test the fix, which counts as available work.
Then, think of your team’s weekly capacity.
Use the following formula to calculate your maintenance backlog:
backlog = available work hours / weekly capacity hours
For example, if the work hour you need for your backlog is 100 and your team’s capacity is 80 hours a week, your backlog is 1.25 weeks.
The industry standard is two weeks per employee. If you have more than that, look into the quality of the processes, availability of parts, and hiring more maintenance specialists.
The maintenance backlog KPI helps you determine the amount of work your employees have, allowing you to plan for new hires, improve current processes, or spare parts management.
Reactive Maintenance Work Hours
The reactive maintenance work hours KPI shows you how many hours your team has spent on reactive upkeep instead of the planned one.
Your team should have a schedule for the week and follow it to avoid a backlog.
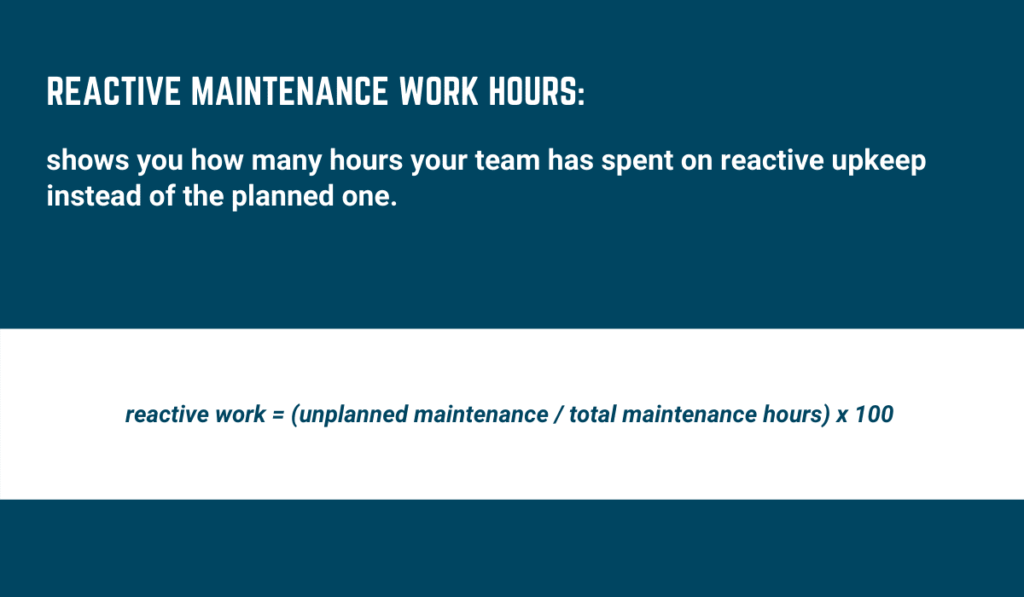
Any reactive maintenance tasks are unplanned, which means they slow the team down, affect productivity, and increase downtime.
If you spend a lot of time on reactive maintenance, you need to look into your upkeep processes—quality preventive maintenance decreases the risk of having to resort to reactive measures.
If the number is constantly high, one or more parts of your upkeep process are inadequate.
You can calculate the reactive maintenance work hours percentage using the following formula:
reactive work = (unplanned maintenance / total maintenance hours) x 100
The total should be as low as possible. However, keep in mind that you can’t eliminate unplanned work unless you opt for preventive maintenance.
With that type of upkeep, the reactive work hours should be down to a minimum. If you are relying on reactive maintenance, your reactive work hours will be very high.
Understanding how much you spend on unplanned activities can help you discover an issue with your maintenance processes or equipment.
Maintenance Costs
Another critical KPI you can use to determine the efficiency of your maintenance process is the maintenance cost indicator.
It lets you know how much you spend on your maintenance.
You invest in your upkeep, especially the preventive type, to save on costs like downtime, expensive urgent repairs, and getting spare parts later on.
However, if you invest a lot in maintenance but dealing with repairs still keeps draining your budget, there is a problem with the process.
Maintenance costs are context-specific, meaning that there isn’t a standard every company can strive to achieve.
However, you can determine the company’s standards using the industry standards and the expected costs of equipment.
There are different metrics you can use to determine upkeep costs, but one of the most popular ones is the cost vs. unit output formula:
maintenance unit cost = total maintenance cost / units produced
The formula allows you to calculate how much it costs you to maintain equipment based on how much it produces and how much time you’ve invested in its maintenance.
Once you know how much you spend on equipment upkeep, you can understand what you can change to decrease the costs.
Work Order Cycle Time
The work order cycle time KPI shows you how much time passes from when your team starts dealing with a work order until they finish it., i.e., until they complete the task and the equipment is ready for use.
This KPI is easy to calculate as you simply have to deduct the start date from the completion date:
work order cycle time = work order completion date – work order creation date
Once you understand the average work order cycle time, you know whether the numbers are acceptable or if you need to do something to improve them.
Work orders often take longer to complete if you’re missing spare parts, are understaffed, or didn’t train your team well.
Once you determine that the work order cycle lasts longer than expected, you can analyze specific work orders to determine what went wrong.
When you get to the bottom of the issue, you can prevent or eliminate the problem in the future.
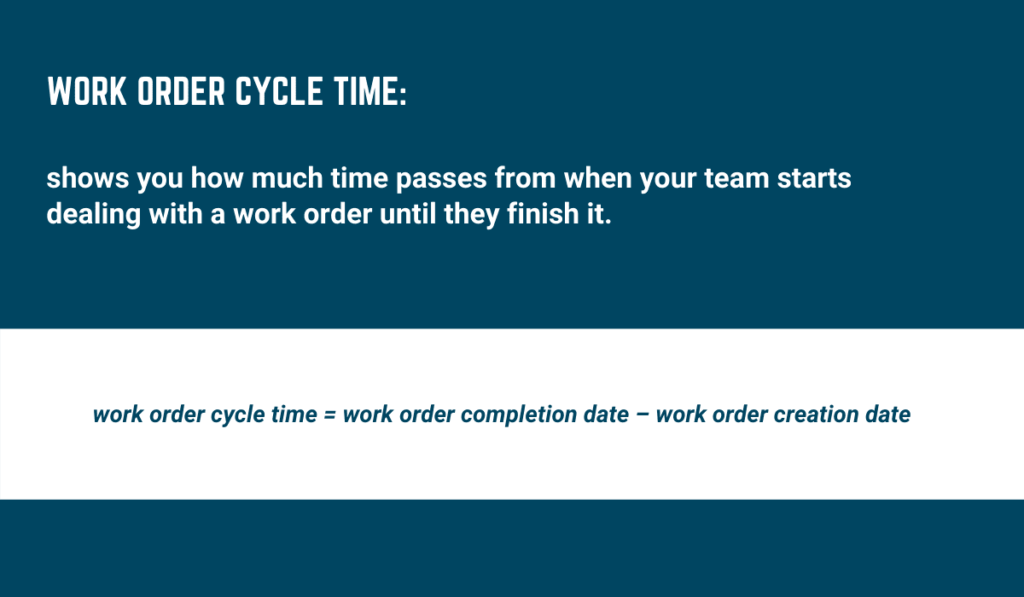
For example, if an employee took three days to finish a task that usually takes one day, you can look into it and determine what happened.
If the employee lacks skills for that specific task, you can invest in training for the employee.
Sometimes, spare parts are the issue.
The employee can’t finish the work order because they are missing a piece and have to wait for the delivery, for instance.
In that case, you can invest in spare parts management to eliminate these risks and help your workers be faster and more productive.
Understanding the duration of your work order cycle helps you find the weak points of your maintenance process and improve them.
Scheduled Compliance
Similarly, the scheduled compliance KPI shows you how well your team sticks to their schedule.
It measures how many of the planned tasks they accomplish within the designated time. The value is expressed in percentage.
The formula is:
scheduled compliance = (number of planned tasks / number of executed tasks) x 100
If your team was supposed to perform 50 maintenance tasks this week, but they managed to do 43, your scheduled compliance would be at 86%.
The aim of any company should be to have a maintenance schedule compliance rate of at least 90% to stay on the right track.
This KPI allows you to understand what you can expect from your team and whether you can rely on them to complete at least 90% of their tasks on time.
If you cannot, you have to understand the reasoning behind it—you need to invest in more employees, outsourcing, in-depth training, more spare parts, or simply rethinking the weekly schedule.
The scheduled compliance KPI allows you to understand whether your maintenance team performs most of their weekly tasks successfully.
Maintenance Overtime
The maintenance overtime KPI lets you know how many overtime hours go into the maintenance process.
To calculate this KPI, you need to consider the total overtime hours and the total hours spent on maintenance during a particular period.
Calculate maintenance overtime using this formula:
maintenance overtime = (total overtime hours / total maintenance hours) x 100
For example, if your team spent 250 hours on maintenance, 30 of which were overtime, your maintenance overtime percentage is 12.
The goal is to have 5% overtime maintenance hours or fewer.
When the number is constantly increasing, you need to improve at least one part of your upkeep process.
If your team creates attainable schedules but still has to put in many overtime hours to complete tasks on time, there is an issue with your maintenance.
The issue can be in the quality of maintenance, staff skills, availability of parts, or any other aspect of the process.
You need to inspect the whole process to understand what is going wrong.
If your maintenance overtime percentage is decreasing, it’s a sign that your maintenance process is improving.
Conclusion
Each company has specific goals they’re working towards, whether it’s to gain more profit, increase productivity, or any other aim explicitly related to the company.
When deciding on your company goals, make the goals SMART (specific, measurable, attainable, realistic, timely) to ensure your teams fulfill them.
If you want to keep track of your progress towards the goals, decide which KPIs you want to use and find a way to measure them.
Some of the most popular KPIs are unscheduled downtime, reactive work hours, scheduled compliance, work order cycle, maintenance costs, backlog, and overtime.
Whatever KPIs you choose, make sure to use the right metrics to calculate your efficiency.