Preventive maintenance isn’t exactly the most exciting part of owning and running a construction company.
Moreover, keeping track of equipment and its condition is often overwhelming, especially if you don’t have a comprehensive asset tracking system.
However, the benefits this type of maintenance provides are numerous.
Regular preventive maintenance improves equipment efficiency, helps minimize the number of emergency work orders as well as the amount of unplanned downtime, and promotes workplace safety.
Equipment that is regularly maintained has a longer life span and provides more cost savings for the company, enabling it to provide a more satisfactory experience to the customers.
All of these benefits greatly outweigh the difficulties associated with organizing maintenance activities—so let’s take a closer look at them.
In this article...
Improved Equipment Efficiency
Construction equipment subjected to regular preventive maintenance will not only function longer, it will also perform better while in service.
As the illustration below shows, equipment efficiency results in a chain reaction of other benefits.
When equipment is more available to the company, its performance improves, as does the quality of the end result.
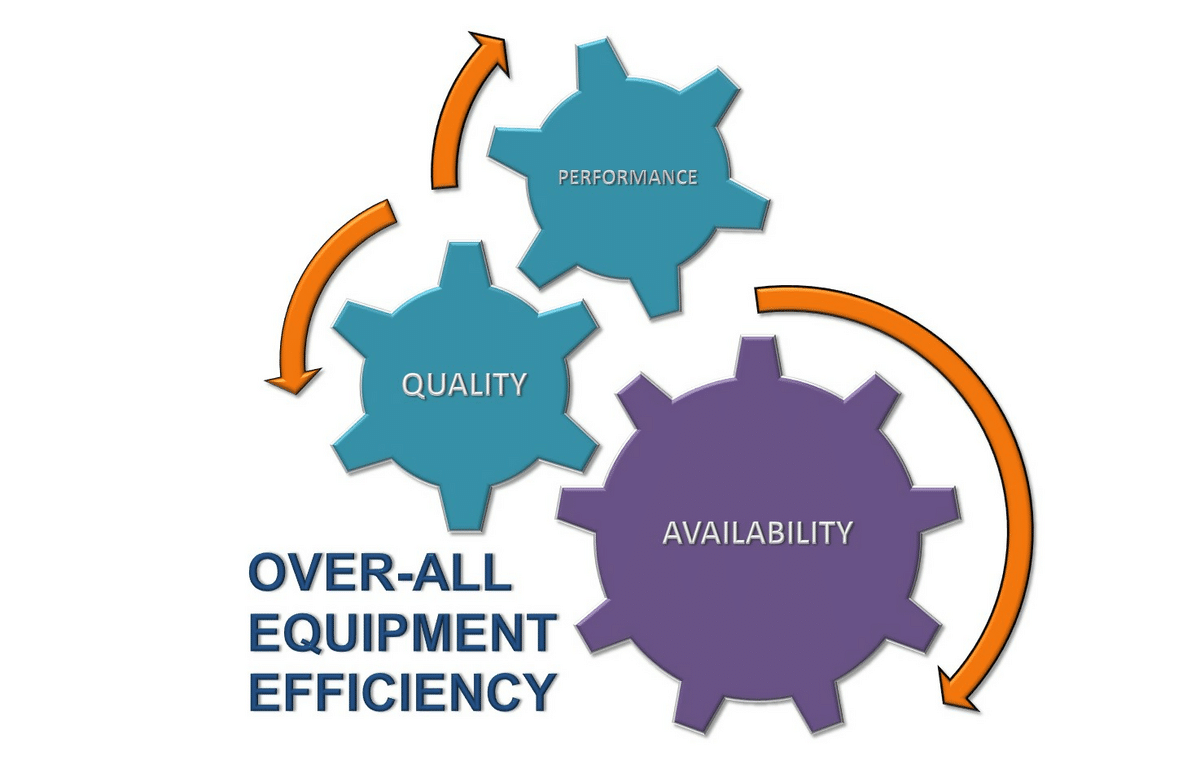
Improved mechanical efficiency isn’t the only advantage of preventive maintenance. Assiduous care of heavy equipment translates to decreased use of electricity, fuel, and water.
Therefore, if care for the environment is important to you, your clients, or your third-party contractors, this is an easy innovation to claim.
Keep in mind that mechanical efficiency is only one way in which preventive maintenance can lower bills for construction companies.
Therefore, prioritizing it can help to protect and improve your company’s reputation.
Finally, since the focus on efficiency can help prevent critical breakdowns, dedicating time to preventive maintenance facilitates the effective use of employee time.
On the surface, it might seem as if taking a perfectly “healthy” machine off the line isn’t a wise idea, but considering the immense time and money savings that stem from good preventive maintenance, a few hours or a day off the job when necessary eventually makes the decision worth it.
Fewer Emergency Work Orders
Emergency work orders are a nightmare for construction companies in a number of ways. To begin with, they are almost always an expensive occurrence.
First, the broken machine requires repair, and in times when labor shortages add time to nearly every maintenance action, that lost time can easily lead to missed project milestones.
In addition, depending upon the necessary repairs, paying for parts and labor often adds to the financial outlay of the job, especially when the appropriate replacement parts for machinery aren’t widely available.
And the cost of parts is only one aspect of the negative impact of emergency work orders and unplanned downtime, as the bar graph below indicates:
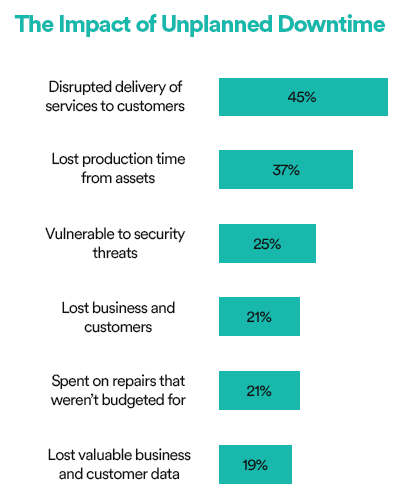
This visual aid represents the frustration clients often experience in the event of emergency work orders.
Equipment that is not maintained can impact customers in three ways: disrupted delivery services, lost business and customers, and loss of valuable contracts or customer data.
The negative effects of emergency work orders, then, echo far beyond the immediate repair costs.
Customer exasperation can cost your company much more, especially if those dissatisfied clients speak to others about their aggravating experiences.
If repairing the asset is more expensive than purchasing a new one, the decision makers of your company must complete an emergency machinery purchase.
Since time is now a factor to meet construction milestones or to assuage upset clients, the typical deliberate phase of the life cycle process is sped up immensely.
That can easily lead to bad decisions and overspending.
Decreased Unplanned Downtime
Every mechanical asset experiences at least some downtime, even if only to undergo shipping from one construction site to the next.
However, some machines break down more than others, and there is always the possibility of unplanned and extended downtime.
Regular construction equipment maintenance can help to forestall this.
Unplanned downtime can stem from many sources. The visual below demonstrates the average downtime by mechanical assets and shows some typical causes.
You’ll notice that, while some of them are staff-related, a noticeable amount is not:
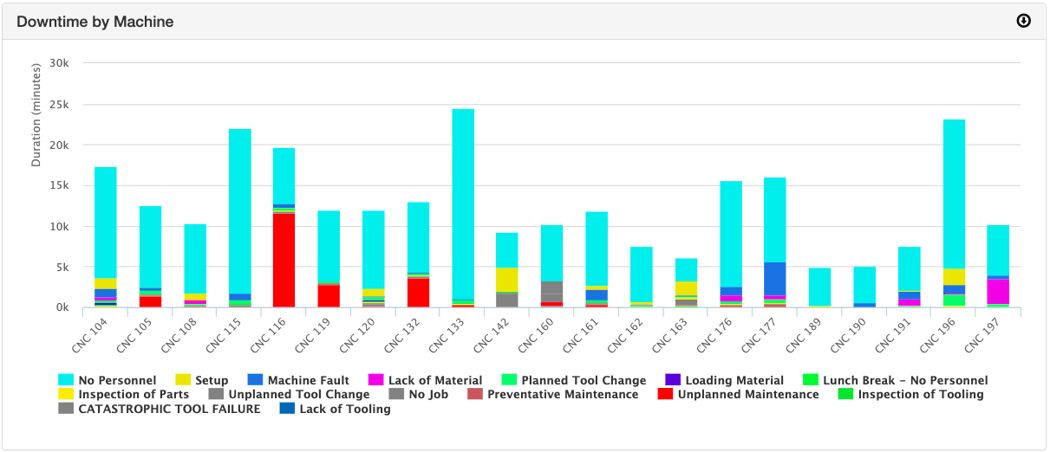
The amount of unplanned maintenance (indicated by the red bar), as well as machine fault (shown in light blue), is significant.
Dealing with both of these categories costs a great deal of money, but preventive maintenance can help to lessen their occurrence.
In the event of a total breakdown, the emergency work order associated with it might demand specialized technicians. Also, significant supply chain delays can contribute to downtime.
In contrast, common sense preventive maintenance is easily scheduled and organically lends itself to efficient planning.
Planned downtime can then take place when the machine is not needed on a job, or during the specific hours when operators are present at the work site.
Visual evaluation of an asset’s exterior and interior is an important part of preventive maintenance.
It is easy for those who work with the same equipment day after day to miss breakdown warning signs such as cracks, chipped paint, or tire punctures, so a dedicated inspection is necessary.
Preventive maintenance ensures that for at least a few hours, the machine is offline and examined with a thoroughness that normally wouldn’t be applied.
That way, minor defects and warning signs are tended to and documented before they can become major problems and result in a breakdown.
Prolonged Equipment Lifespan
While no asset lasts forever, preventive maintenance will prolong the lifespan of the equipment, so that your construction company can more reliably maximize the value of your expensive equipment.
Understanding the average lifespan of valuable assets and their components helps with planning preventive maintenance and projecting a useful timeframe as to when preventive breakdown replacements should take place:
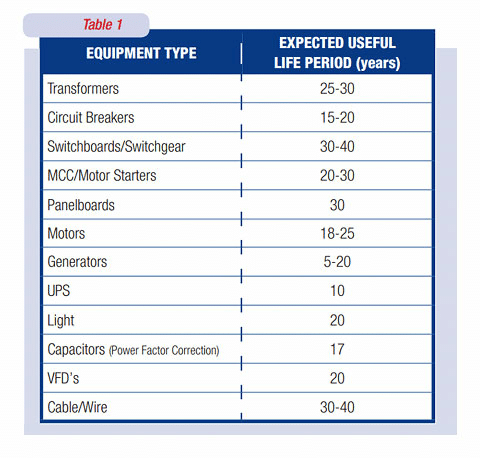
Scheduling service notifications through a robust asset tracking system such as GoCodes is a fast and simple way to extend the lifespan of your equipment.
Moreover, with GoCodes’ scannable QR codes, operators and maintenance staff have quick access to an incredible amount of information about the equipment, including operators’ manuals, manufacturer information, and a record of maintenance actions.
GoCodes also enables you to create tasks for individual assets and assign them to specific maintenance team members, who can then update the status once they complete the necessary inspections and repairs.
Arranging for automatic service notifications is an easy and low-effort way to ensure that preventive maintenance takes place.
Prevention of Workplace Safety Incidents
Construction equipment that does not undergo regular preventive maintenance has a higher chance of malfunctioning or breaking down.
This endangers the safety of the construction company’s equipment operators as well as other employees in the vicinity.
Because of that, and many other dangers that lurk at the construction site, authorities, including the Occupational Safety and Health Administration, insist on the adherence to various safety regulations.
Without proper maintenance, safety hazards can fly under the radar until they escalate.
For instance, a frayed electrical cord that goes unnoticed can electrocute a worker that handles it and have long-term consequences on their quality of life, or even result in death, and consequently lead to lawsuits that affect the reputation and the finances of the construction company.
Research has shown that 61% of all workplace injuries caused by electricity take place in the construction industry.
Therefore, the hypothetical situation we’ve described above is less uncommon than we might hope for, and does well to illustrate the importance of adhering to safety guidelines and approaching maintenance with the care it deserves
Workplace safety guidelines can also address proper storage of hazardous materials, clearing unprotected outdoor areas during inclement weather, and ensuring that team members are properly credentialed or trained.
More Cost Savings
It is more cost-effective for your construction company to invest in preventive maintenance because the cumulative cost of repairs is often much higher.
Your company will not have to replace equipment as often, and efficiency savings in fuel, equipment movement, and water will accumulate.
Statistics on equipment maintenance indicate that predictive maintenance can save up to 40% on overall maintenance costs.
Not only that, an optimized preventive maintenance program can forestall breakdowns by up to 75%. In some cases, companies can avoid complete mechanical breakdowns completely.
And if you keep in mind how expensive it is to replace pieces of construction equipment—for instance, a boom lift can cost up to $200,000 to purchase and between $2,000 and $9,000 per month to rent, depending on the type—the savings are not insignificant.
Higher Client Satisfaction
Happy clients are a construction company’s most valuable resource. Personal recommendations of contractors and construction services are the way in which many potential clients become actual clients.
Having important equipment in action at all times quickly leads to higher overall quality of the project. Projects are more likely to reach completion on time or even early.
What is more, there’s a direct correlation between the quality of the project and customer satisfaction, as shown in the chart below.
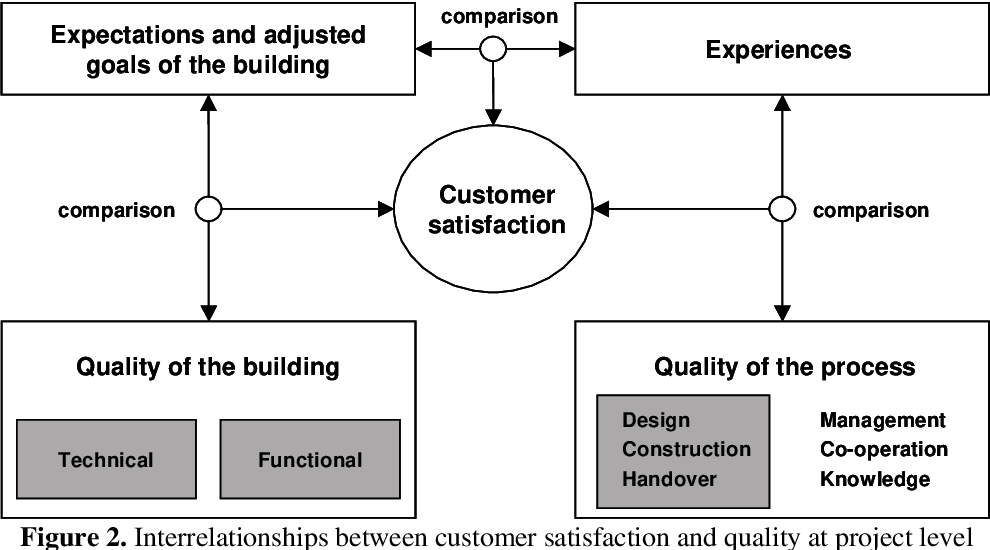
As this chart shows, attaining customer satisfaction in the construction industry is sometimes a complex process.
Making sure that your client sees you’re able to deliver quality in the way you manage the work processes, as well as in the final result is key.
Keeping equipment in good condition is an important part of this. It is also important to pay attention to your customers’ expectations so that your team can manage and even surpass them.
And when clients are satisfied with the way a company conducts business, they’re more likely to recommend it to others.
Conclusion
Paying attention to preventive maintenance for construction equipment is a vital part of maintaining a healthy company.
When contractors and business owners take the time and effort to take care of their mechanical assets, they will enjoy less unplanned downtime.
Their team members will experience fewer emergency work orders and enjoy a safer workplace.
Equipment will last longer and the company will experience cost savings as well as greater efficiency and higher client satisfaction.