According to the Occupational Safety and Health Administration (OSHA), workplace injuries cost companies a lot more than is normally assumed.
The insurance and medical costs alone can go up to $40,000.
But don’t forget that the indirect costs of a worksite safety issue can be anywhere from two to ten times more expensive than the direct ones, as they include unplanned downtime, possible OSHA fines, project delays, and a ruined reputation.
Nevertheless, all of those issues are easily avoidable if you choose to promote safety on the job site.
Keeping your workers safe should always be a priority, but it has the added benefit of helping you save money and keeping you in business.
Let’s see what steps you can take to make safety a priority on your construction site.
In this article...
Know Common Workplace Hazards
Raising awareness of common construction site hazards is key to worksite safety.
It all starts with understanding what threats exist at your jobsite, which is why you should assess the risks regularly. Doing it once and basing your entire safety plan, training program, and safety culture around it is not enough. Instead, you need to keep updating all these safety aspects.
Let’s take a look at the list of fatal injuries at construction sites from 2015 to 2020, as it will help you figure out whether the same hazards are present in your workplace.
Three out of OSHA’s fatal four construction injuries were at the top of the list in this period. These three injuries are falls (25%), struck-by vehicle (19%) or object (13%), and stuck in between (10%). Together, they account for 67% of fatalities in five years.
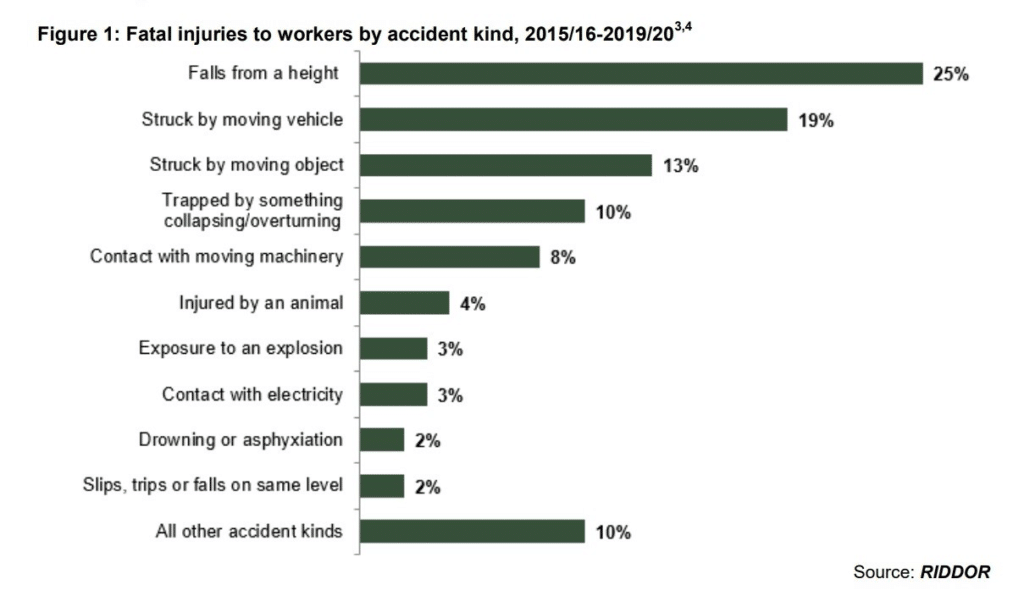
Electrocution, the fourth injury, is further down the list with 3%, after damages caused by moving machinery (8%) and those caused by animals (4%).
While this is not a definitive list of all possible hazards you can come across at the worksite, it can help you raise awareness among workers about the most likely problems. If you present this information to your team, they will be on the lookout for the risks.
Here’s what you can do to ensure your workers are aware of possible dangers:
- Use safety signs all around the construction site.
- Maintain a clean and safe working environment.
- Perform regular risk inspections.
The use of safety signs helps anyone who comes to the worksite understand the type of hazard they are around and what they can do to prevent it. Some signs warn you of imminent danger, such as wet floor signs, while others explain the mandatory precautions, like obligatory personal protective equipment (PPE) signs.
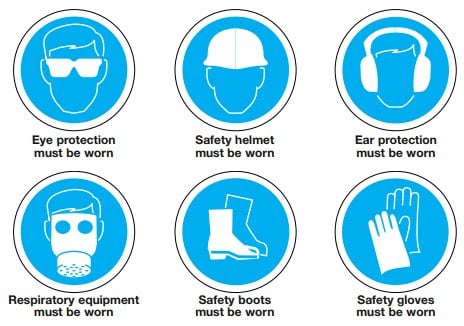
In any case, such signage warns the workers of potential hazards they should be on the lookout for as they work, making them more vigilant.
Your employees should also take responsibility for keeping the workplace clean. If they’re using a tool, they should return it to storage instead of leaving it on the worksite, where someone can trip over it. Similarly, in case there is debris lying around, the workers should be aware of how it can affect everyone’s safety and remove it.
Frequent risk inspections are another way to raise awareness of the importance of workplace safety. They help you promptly detect any new hazards that arise, which means you can notify your team, put up correct signage, and implement any new insights about them into your safety training.
Raising awareness of possible hazards contributes to creating a good safety culture in the workplace.
Create A Workplace Safety Culture
Workplace culture is what gets your employees to stay or leave the company.
We’re not just saying this: studies have shown that 15% of people have turned down a job offer because they couldn’t relate to the company culture, and another 35% say they would do the same if they were in a similar position.
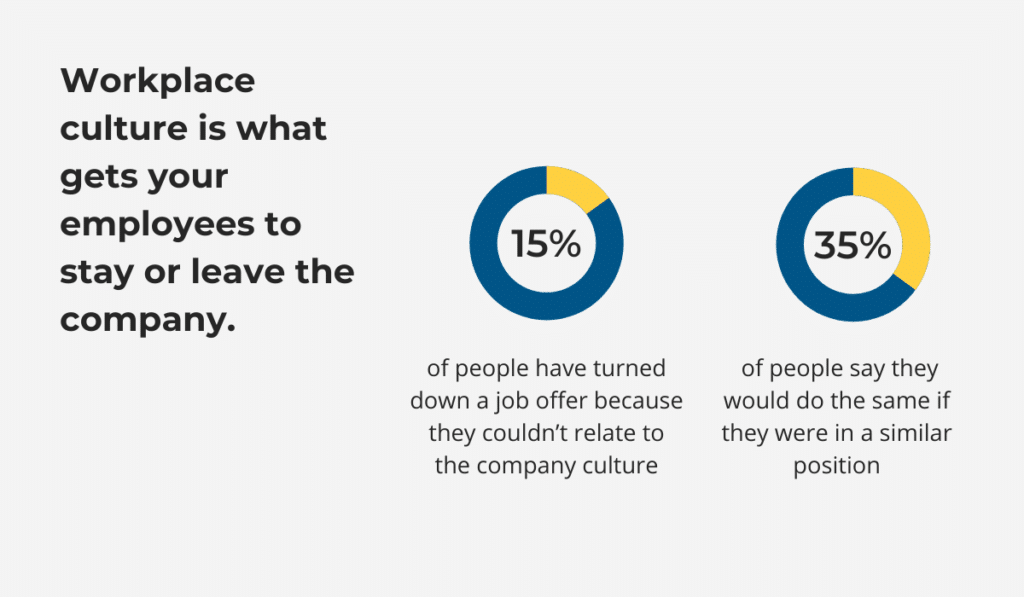
If employee satisfaction depends so heavily on the culture in the workplace, it’s clear that creating the right one is essential.
In the construction industry, safety is a crucial part of this: one in five worker deaths in the US happens on a construction site. Therefore, construction workers looking for a job will appreciate a company that prioritizes their well-being.
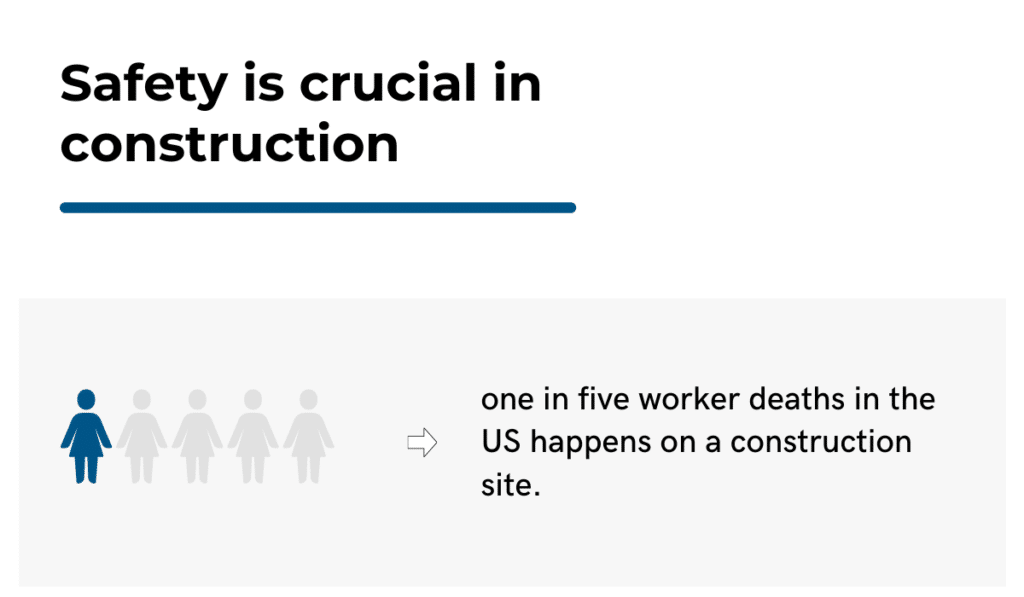
What constitutes safety culture?
E. Scott Geller, a behavior-based safety expert, thinks of it as a culture where “everyone feels responsible for safety and pursues it on a daily basis.”
If that’s what you’re striving for, your entire team should first understand what safety means for and in your company. The employees should also know how to adhere to the relevant standards and have a say in safety solutions that get implemented.
You’ll achieve this through encouraging frequent and seamless communication with all team members, not just those in charge.
When trying to create a safety-oriented culture, you need to find ways to ingrain it in your employees’ mindsets. You should devise a bulletproof safety plan, encompassing every aspect of a project, from its preparation all the way to completion.
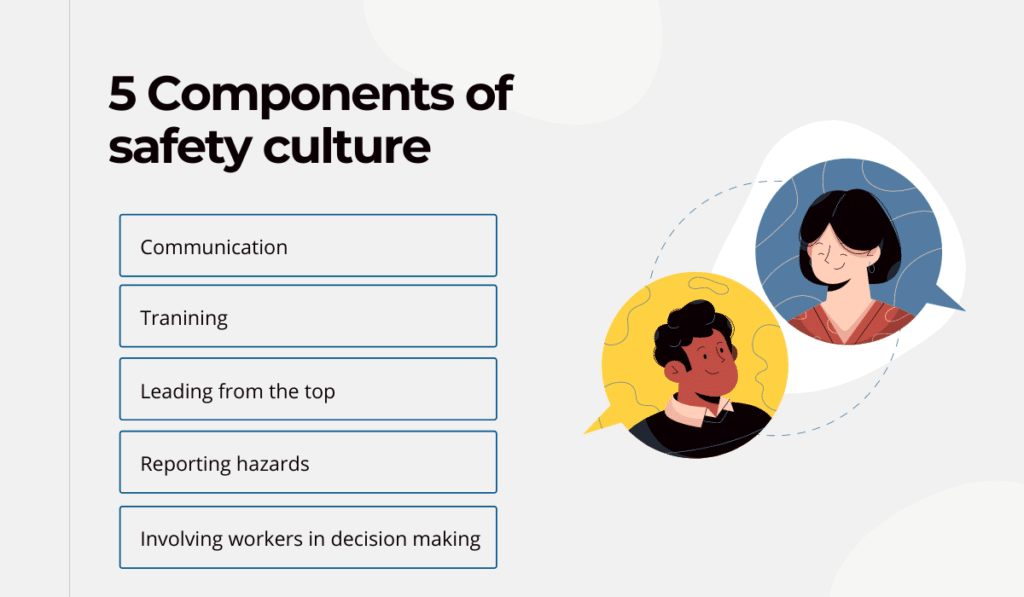
Of course, this plan should include regular training, which should be updated with new insights after every risk inspection.
Moreover, managers and supervisors should be held to the same standards as workers in the field, as this helps people understand that they all need to follow the same rules when it comes to safety.
Fostering this type of culture will also make people feel personally responsible for their safety, which means they will be more involved in the process from the very beginning. Your employees will feel obligated to report incidents or issues that might threaten the company’s culture.
However, the benefits you get out of such a culture go beyond safety. John White, a certified safety professional, explains:
“[A] world-class safety culture improves employee morale. When an employee feels valued and truly cared about, his or her outlook towards the organization and organizational goals is different.”
In other words, your employees become more engaged when they feel like you care about them.
Why should this matter?
Well, engaged employees are almost 50% less likely to cause accidents and 60% less likely to make errors while working.
Such employees can also earn your company a 202% increase in productivity, which means you’ll get a lot more work done while staying safe.
Another thing you can do to improve your workplace safety culture is to be aware of and promote preventative measures.
Focus on Preventative Measures
One of the best ways to improve safety at the construction site is to invest in preventative measures. That way, you’ll get to eliminate the hazards before they can harm your team members.
To start understanding preventative measures, you first have to make a written note of all possible safety hazards at the worksite. When doing this, include team members who work in the field as they have firsthand knowledge of these safety problems.
Even if you are just planning a new project, your employees can give you some invaluable information on issues that might pop up.
Once you have the bigger picture, you can start to determine how to address each type of hazard. According to OSHA, there are different ways you can do so.
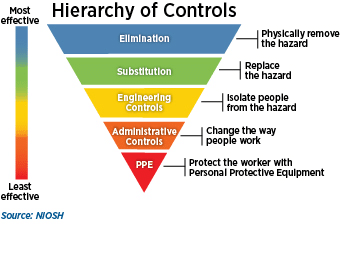
Clearly, the most effective way is to do away with the problem entirely, so it no longer poses a threat. For example, if you have a faulty machine on the construction site, the best course of action is to remove it before it damages someone’s health.
Another efficient way of getting rid of a safety issue is to replace the item that causes it with something less dangerous. In the case mentioned above, you could replace the malfunctioning piece of equipment with one in good condition, thus removing the risk of injury and accidents.
These two options are the most effective, but they are not always feasible. Not all threats can be entirely eliminated in those ways.
For example, the risk of falls is high on every construction site, but your workers can’t avoid using scaffolding if they have to work on taller buildings.
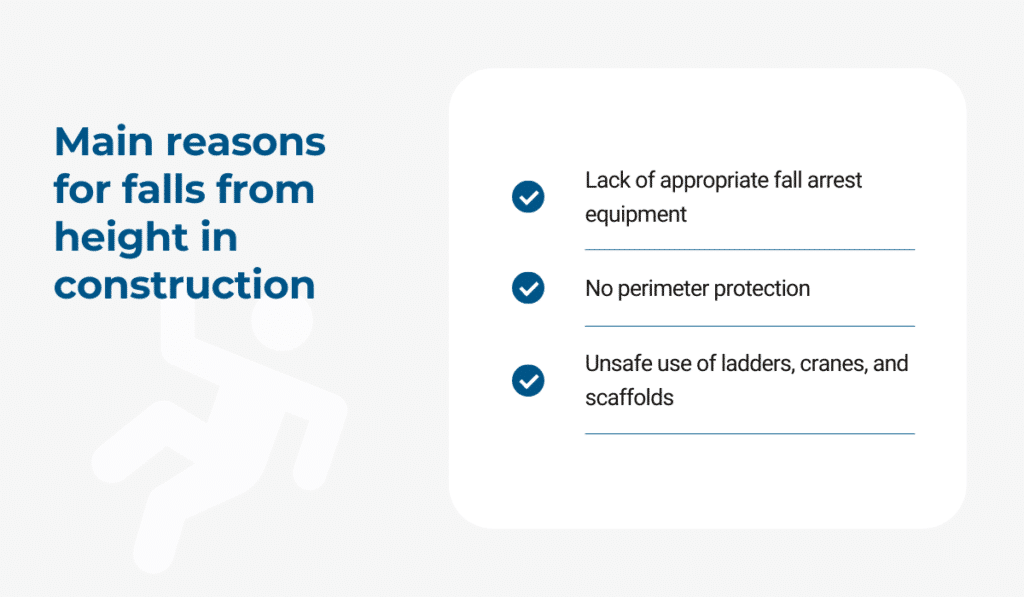
At specific worksites, working at great heights is simply a requirement. However, you can protect your employees by ensuring that they have PPE and that they adhere to the previously agreed on safety protocols.
If you can’t eliminate or substitute the hazardous element, you can at least isolate people from it, so they do not get hurt.
Let’s say your workers have to use a loud machine that can potentially damage their hearing if they’re exposed to it for a longer time.
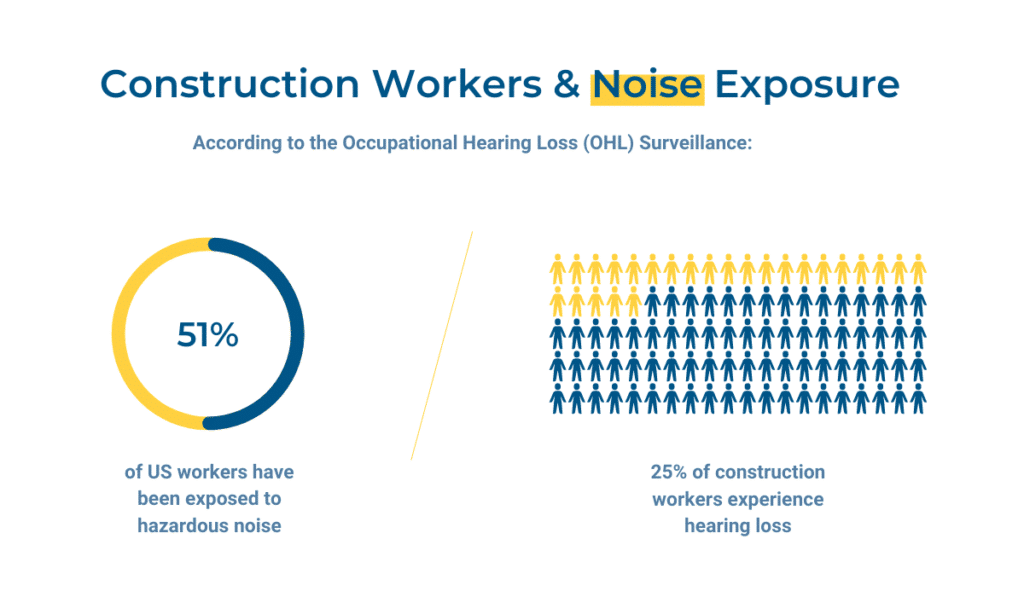
In that case, you can remove those who do not have to operate the machine from the site while the machine is in use, and provide protective equipment, such as noise-canceling earphones, to those who do. That way, you minimize their exposure.
Finally, be sure to explain those changing work practices to your employees before implementing them.
You may not be able to remove them from the situation, but you can help them stay safe with proper equipment and training.
Never Use Faulty Equipment
The key to safety lies in well-maintained equipment.
Think about it: a faulty machine is bound to malfunction sooner or later, and the consequences could sadly be fatal. If equipment stops working mid-service, you can’t predict what will happen, so it’s not a risk you should take lightly.
How does a machine become defective in the first place?
First, this happens due to wear and tear. You use the equipment for its original purpose, and along the way, it gets damaged. The best way to prevent or reduce the damage caused by wear and tear is to invest in preventive maintenance.
You have to create a servicing schedule and put the machine out of use so your service team can inspect it. During the servicing, your employees will fix any issues they find.
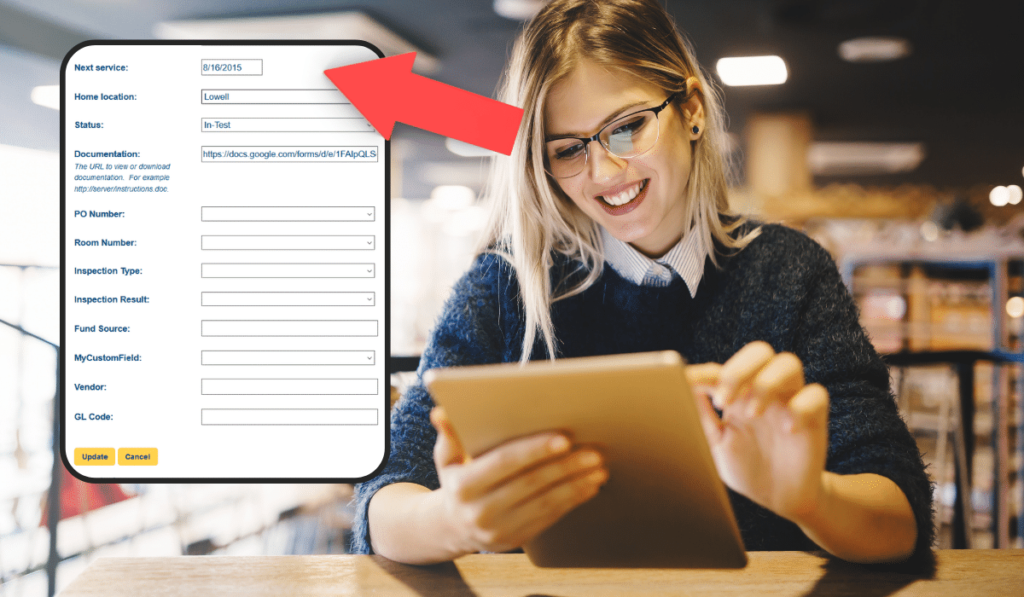
With the Gocodes asset tracking app, you can easily see when the next service is due, and when the previous ones occurred.
There’s always a possibility that the machinery was faulty from the very beginning, but this is something your servicing team or operators won’t be able to miss if they perform detailed inspections. This type of damage isn’t something you can prevent.
However, you can point it out to the manufacturer and ask for a replacement asset, especially if the warranty is still valid.
Your team’s inexperience could also cause problems. If the operator doesn’t know how to use the equipment safely, they could damage it, for instance, by using it for something other than its original purpose.
Additionally, an inexperienced and untrained operator won’t recognize the warning signs of machine damage, which puts them in direct danger.
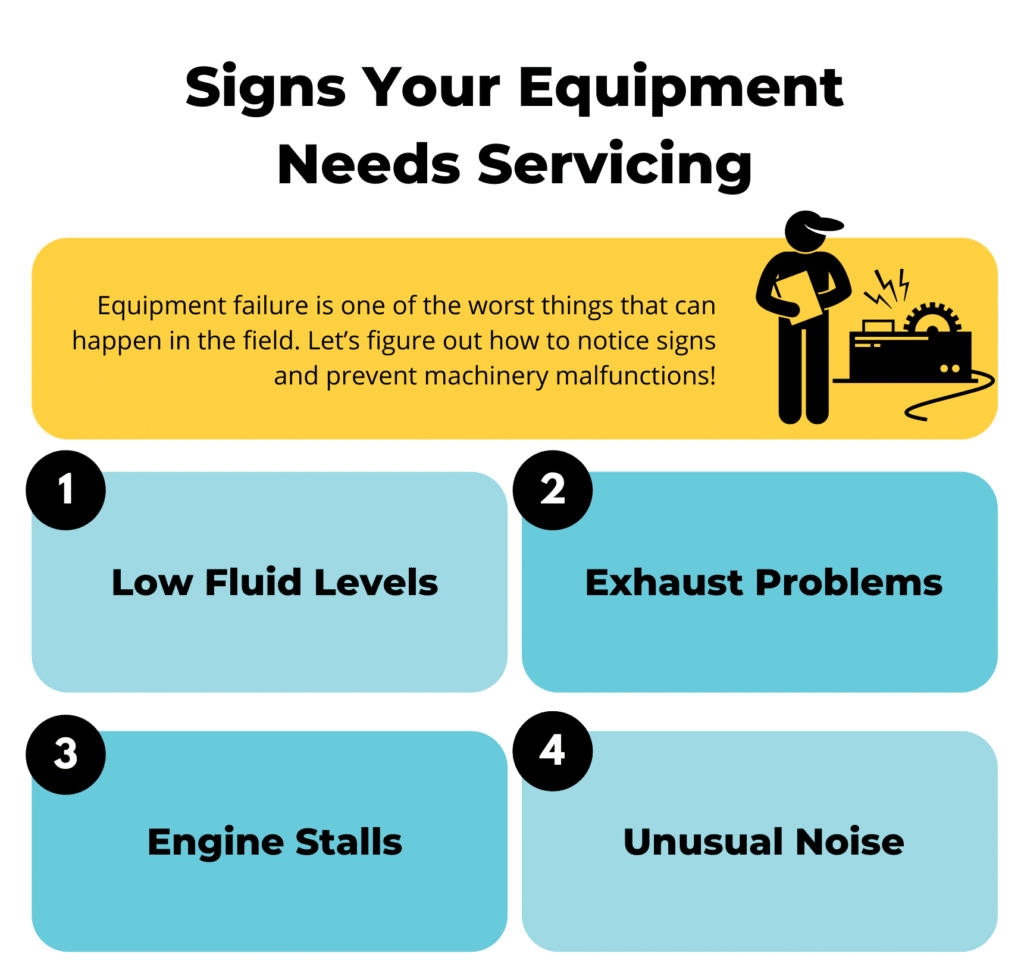
On top of that, if your maintenance team doesn’t receive proper training, they won’t be able to recognize nor fix malfunctions in their early stages, which only leads to further damage. If you want to ensure that your team knows what they’re doing, instruct them to keep maintenance logs.
When you have previous service records for each piece of equipment, you’ll be able to analyze the maintenance team’s effectiveness. Give your entire team access to these logs, so everyone is equally informed on equipment details.
Have a Safety Communication Plan
Open communication is key to workplace safety, especially at the construction site.
You may be wondering how promoting communication helps your company’s safety.
First, focusing on conveying information effectively means that you will ensure that each employee gets to hear about your safety plan. After all, the program is no good if you don’t share it with everyone and offer them ways of implementing it.
Moreover, if you stress the importance of communication, your team will become more connected.
Think about it: your field employees probably don’t often talk to the maintenance staff because they work in different areas. But shouldn’t they be connected? After all, one group fixes and cares for the equipment while the other uses it daily.
If you find a way for these two teams to share information in real time, you help everyone become better at what they do.
For instance, you can start using an app that lets your maintenance team upload servicing records in the cloud, directly connecting them to the machine.
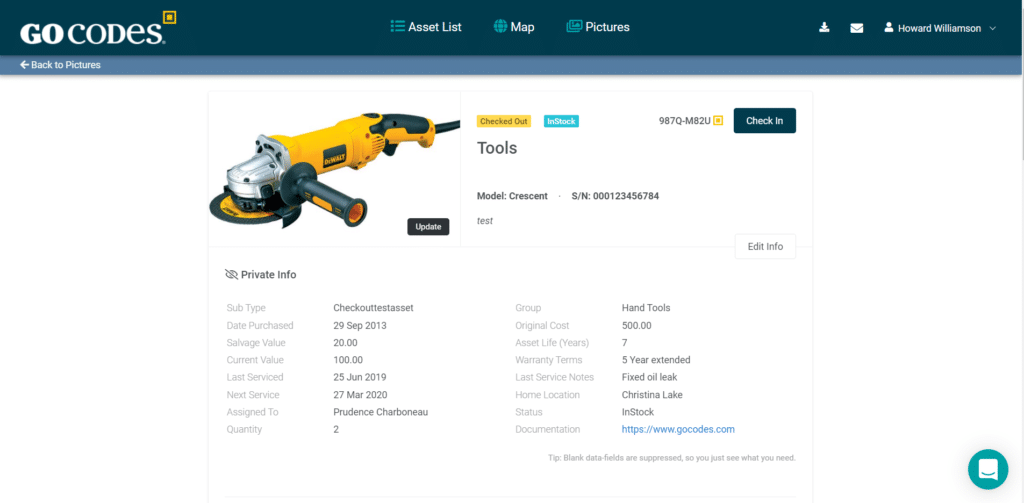
The team in the field can access this data by scanning the QR code that’s present on the equipment. That way, both teams can access data in real-time and leave comments regarding the machine’s state.

Then, promoting communication regarding safety ensures that you will get more safety and injury reports, which is essential.
You might think that getting such reports is a bad thing, but it benefits your company in the long run. Think of it like this: if nobody reports a possible issue or a sustained injury, you won’t be in the loop, meaning that you won’t be able to fix the problem and prevent a safety hazard.
After all, if one worker gets hurt at the workplace, you should know about it to warn others so they don’t find themselves in a similar situation. You should also eliminate the hazard.
Still, employees often don’t report the safety issues they find out of the fear of consequences. Research conducted by McKinsey shows that 60% of employees worry about the repercussions of reporting they were injured in the workplace, which is disheartening.
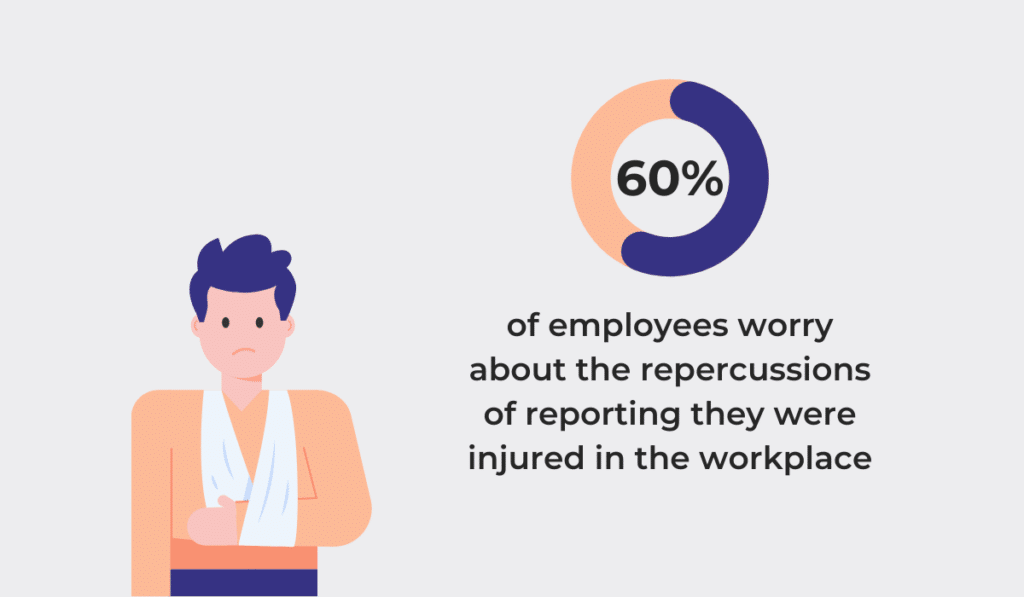
Promote communication by encouraging your workers to report any safety concern or injury at the worksite.
When people understand that flagging an issue is for their benefit and that they won’t be punished for doing so, you’ll get a lot more reports which will help you keep the workplace as safe as possible.
Conclusion
Staying safe at the worksite should be every construction company’s top priority. If it’s not, you’re risking low morale, poor efficiency, costly lawsuits, and an inevitable lousy reputation.
To protect your workers, you should put safety at the heart of your business and make it the cornerstone of your company culture. Do this by following the tips from the article, including raising awareness of possible hazards, focusing on preventative measures, promoting communication, and using only well-maintained equipment.
The point is that if you want your employees to think of safety every step of the way, your company should live and breathe safety. Only then will your team members be completely focused on keeping themselves and others out of harm’s way.