If you’re here, you’re already aware of the critical significance that efficient management of heavy machinery, equipment, and tools has for your company’s success.
These valuable assets are the lifeblood of any construction company, enabling successful project completion and ensuring smooth operations.
However, when mismanaged, they can quickly become sources of frustration that hinder progress, generate revenue leakage, and result in jobsite accidents, project delays, and budget overruns.
With that in mind, we’ll explore five common equipment management mistakes your construction company should avoid and suggest ways to do that.
In this article...
Not Regularly Reviewing Equipment Needs
One of the typical mistakes in construction equipment management is the failure to regularly review your company’s equipment needs.
In the fast-paced world of construction, your company should frequently evaluate and identify its short- and long-term equipment needs.
To do that, you first need an accurate inventory list of equipment and tools.
This is a list of construction assets your company currently owns, along with crucial info about each asset, such as name, type, serial number, manufacturer, purchase price and date, warranty expiry date, and much more.
This list can be kept and updated on paper (rarely), spreadsheet (sometimes), or (increasingly) as part of your equipment management software’s database.
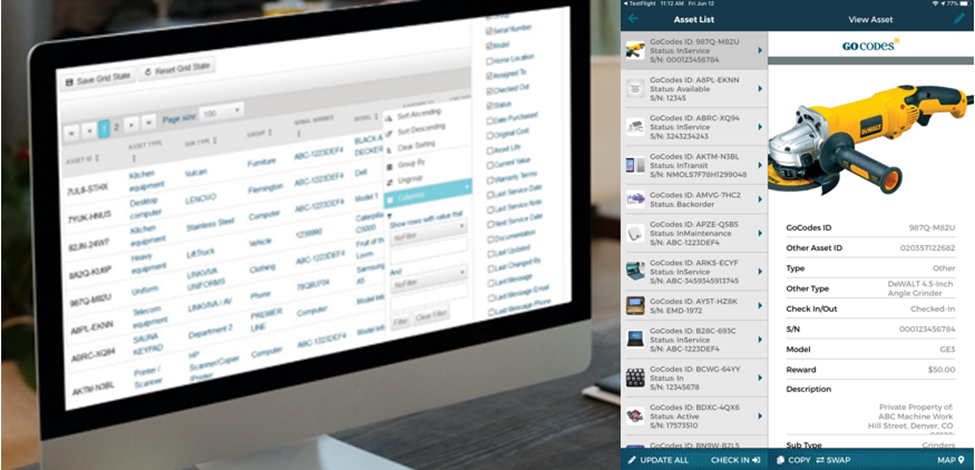
Either way, once your equipment inventory is up-to-date, you can start planning your equipment needs.
Effective planning includes evaluating the decision between owning and renting equipment and determining when to repair or replace existing assets.
Of course, your planning will depend on the specific needs of future construction projects already in the pipeline, being negotiated or announced, and your company’s business expansion plans.
In that sense, own-or-rent and repair-or-replace decisions are key aspects of equipment management.
They can significantly impact your company’s operational efficiency and bottom line.
For example, even though all upcoming construction projects might require the services of a large excavator, that still doesn’t mean that the most profitable thing to do is buy a new or used one.
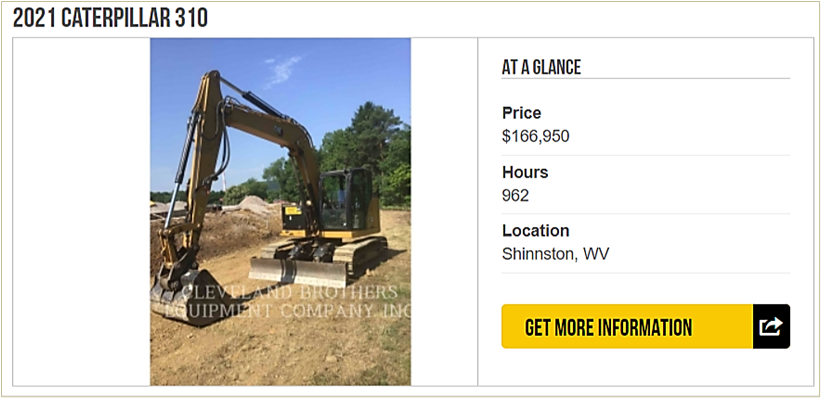
That’s because such excavators are often needed once during a project, so the one you bought would sit unused most of the time.
In fact, a general rule of thumb for making own-or-rent decisions is to buy equipment if it is going to be used during 60-70% of your company’s construction operations.
The same could be said about deciding whether to replace a piece of equipment:
- when it unexpectedly breaks down
- due to its wear-and-tear and performance deterioration
- because it is outdated or obsolete (parts no longer available)
- due to safety concerns
In the case of warranty-expired equipment, conventional wisdom for making repair-or-replace decisions is the 50% rule where, if the repair would cost more than 50% of the equipment’s value, you should consider replacing it.
Of course, this rule works best for smaller and less valuable equipment or when outdated or older heavy equipment experiences a major breakdown.
Otherwise, there are plenty of other factors to consider besides the cost of repair, listed here courtesy of Kevin Smallridge, Managing Director at Medaco:
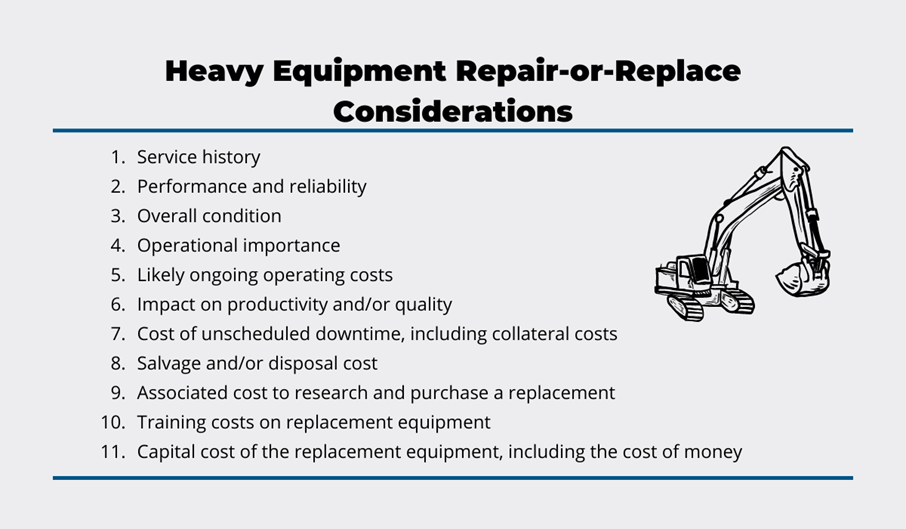
Making strategic choices based on these considerations can ensure optimal equipment utilization, cut maintenance costs, and increase overall productivity.
Considering all the above, your company should regularly review and evaluate its equipment needs, maintain an accurate and up-to-date inventory, plan ahead, and make informed decisions on whether to buy or rent a piece of equipment, and, when it starts malfunctioning, whether to invest in repairs or replace it entirely.
Neglecting to Manage Underutilized Equipment
Besides overlooking when specific equipment will be needed, whether to rent or buy it or—if already owned—when to replace it, another costly mistake is neglecting to manage your underutilized equipment.
Simply put, in terms of costs and benefits for your company, every hour a piece of equipment is sitting unused is perceived as an expense, i.e., money lost.
Naturally, there are many instances where specific equipment might be seldom used but still be considered crucial for construction operations, such as backup generators, concrete pumps, welding machines, and surveying equipment.
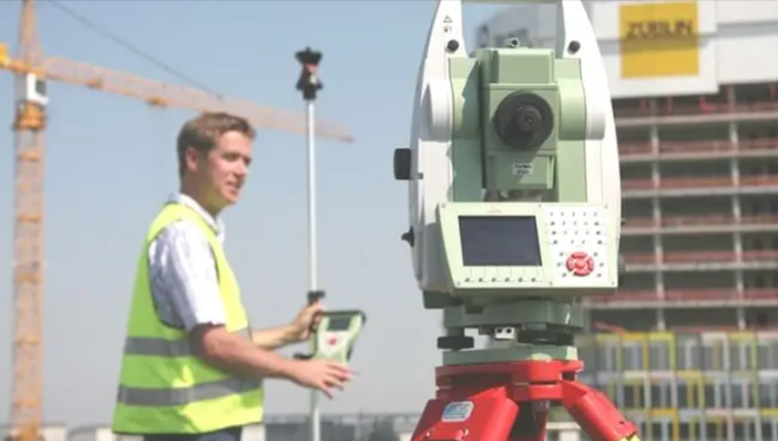
Therefore, you and your team should consider such factors when defining what “underutilized” means for each equipment category and type, or specific machine.
However, there are situations where underutilization is a given, such as:
- when company-owned equipment is sitting idle on one site while it could be used on another one (either delaying that project or requiring the use of rentals)
- when rented equipment is not used as planned
Generally, this can happen for many reasons, starting with external, unpredictable factors like unexpected site conditions, on-site accidents or breakdowns involving other equipment, or severe weather.
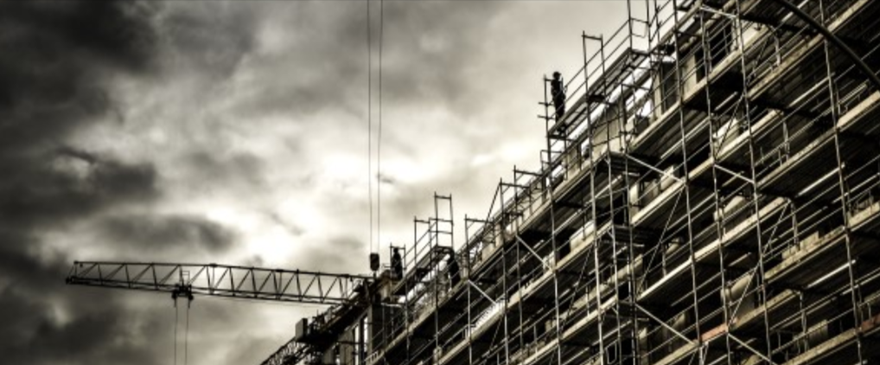
These external factors are typically beyond the direct control of a construction company, but preventive measures and insurance can effectively mitigate such risks.
However, you should be more interested in internal reasons for not using equipment when scheduled, which include delays in preceding tasks due to planning issues or human factors, last-minute project changes, or poor equipment management (discussed next).
These factors are within the control of your construction company and can be addressed through improved equipment planning, coordination, and management practices.
To avoid equipment underutilization, you and your team should calculate the current equipment utilization rate, track and analyze equipment usage, and allocate equipment more effectively.
Sometimes, you should even consider renting out or selling seriously underutilized equipment.
Overall, you should proactively manage equipment to maximize its utilization by ensuring it’s always put to use in a way that increases your company’s productivity.
Ignoring the Importance of Timely Maintenance
Skipping regular maintenance of their construction equipment remains a common mistake made by many contractors.
Generally, the reasons why a construction company may choose to ignore timely maintenance can be:
- operational (heavy workloads or tight project schedules)
- organizational (inadequate maintenance prioritization, scheduling, and tracking, lack of accountability)
- financial (limited budget, cash flow issues)
Irrespective of the reasons, the consequences of poor maintenance typically include higher safety risks for operators and workers, increased equipment downtime, higher repair costs, and reduced equipment lifespan.
Conversely, when a construction company keeps its equipment in good condition through timely maintenance, this results in a range of benefits.
Here are the top six reasons why regular preventive maintenance beats reactive, irregular maintenance practices every time.
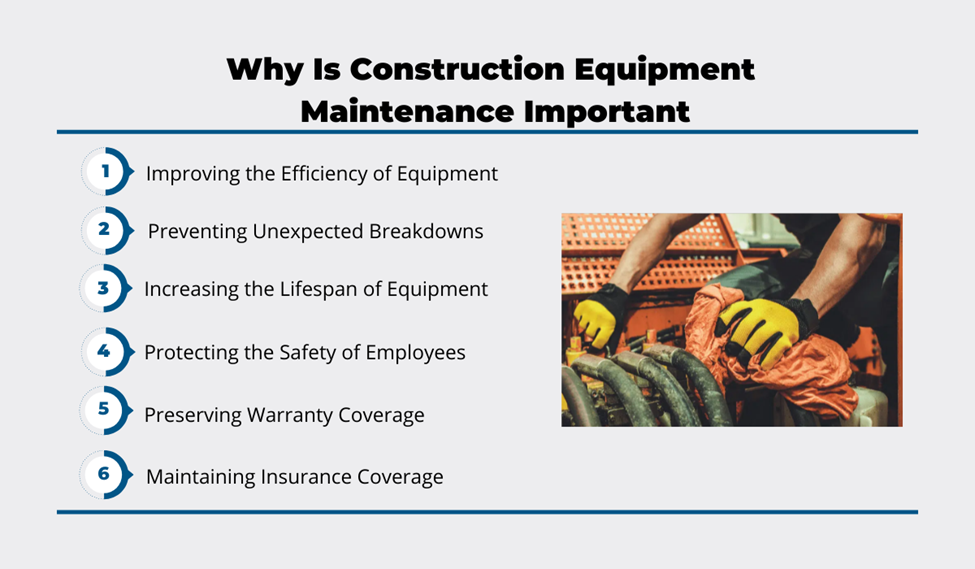
Having clearly established the importance of timely maintenance, let’s turn to how your company can avoid this common mistake.
Simply put, you need to create an effective preventive maintenance plan and establish procedures to monitor its implementation.
If you’re starting from scratch, here’s how to do that in seven steps.
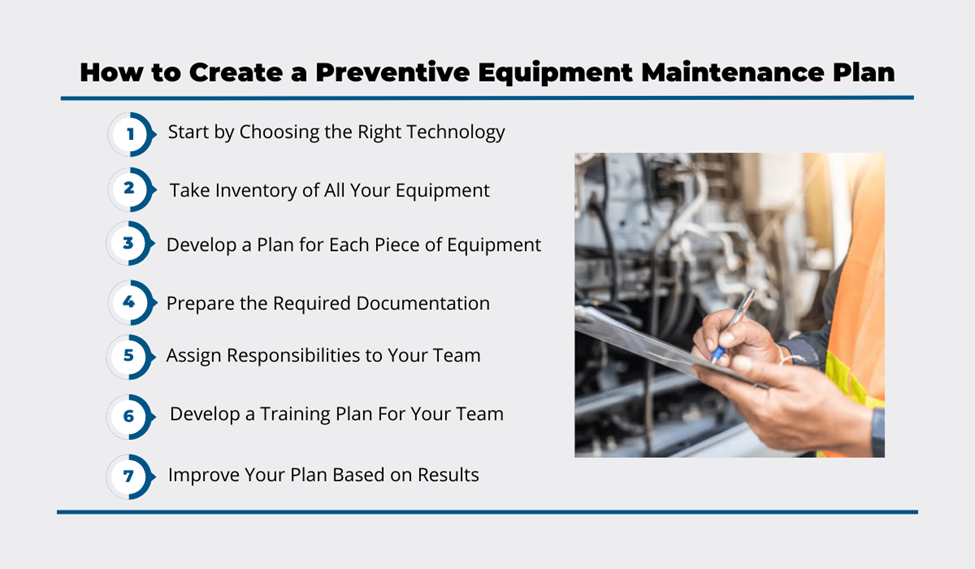
As you can see, your path starts with selecting the right technology that will allow you to turn your plan into reality.
In other words, you need a software solution that will allow you to organize, (re)schedule, track, and document all maintenance activities, both planned and unplanned, and thus help you tackle common equipment maintenance challenges.
In the final section, we’ll look into what solutions might best fit your needs.
As for the plan, the second step is to create an inventory list of all your equipment that will, together with the initial equipment info, be used to populate the software system’s database.
Once that’s done, the system will contain non-changeable info about each piece of equipment (shown below on the left) and a range of data that will be tracked and updated over time (shown on the right).
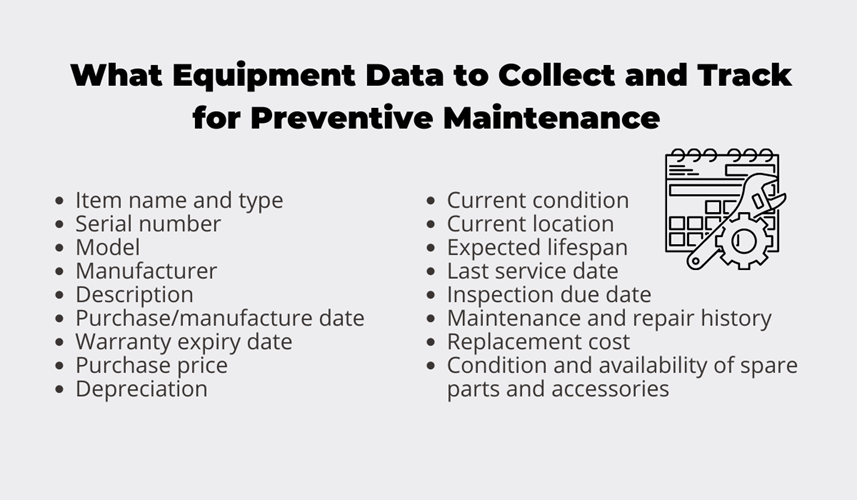
After that, you and your team should, based on the manufacturer’s recommendations, warranty conditions, and previous experience, establish a maintenance plan for individual pieces of equipment.
Furthermore, you should collect relevant documentation, and assign maintenance team responsibilities.
Finally, you should train your workers and managers on how to implement the preventive maintenance plan.
In other words, you should teach them to perform and document their activities using the selected technology, and keep improving your plan based on achieved results.
To recap, ignoring timely maintenance is simply too expensive and damaging for your company.
Instead, you should establish a comprehensive preventive maintenance plan and ensure the tools/procedures for its effective implementation are in place.
Failing to Protect Equipment Against Theft
Not protecting equipment against theft is another common mistake that hampers productivity and reduces the profitability of small and large construction companies alike.
We won’t bore you with construction equipment theft statistics, but simply assume that you’ve already experienced some form of jobsite theft.
If you’ve dealt with heavy machinery, vehicles, or high-value equipment or tools being stolen, you’re aware of the resulting lost time and operational disturbances.
These usually involve putting workers, the police, and your company’s insurance provider on the case.
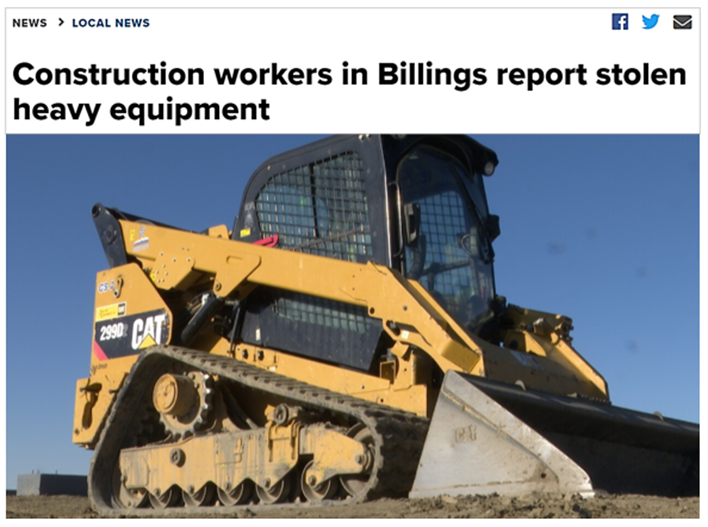
In such cases, your actions might not be enough to prevent the consequences of equipment theft, such as costly project delays, high replacement costs, and increased insurance premiums.
That’s why larger and more expensive equipment is typically GPS-tracked and protected in other ways (security measures and insurance).
However, construction companies shouldn’t ignore the cumulative value and productivity-lowering effects of losing many less expensive tools, such as power tools, through either external or internal theft.
Now let’s turn to anti-theft solutions.
Simply put, there is a whole range of security measures (some of which you’re probably already using) that are at their most effective when combined.
As a reminder, here are just some of them.
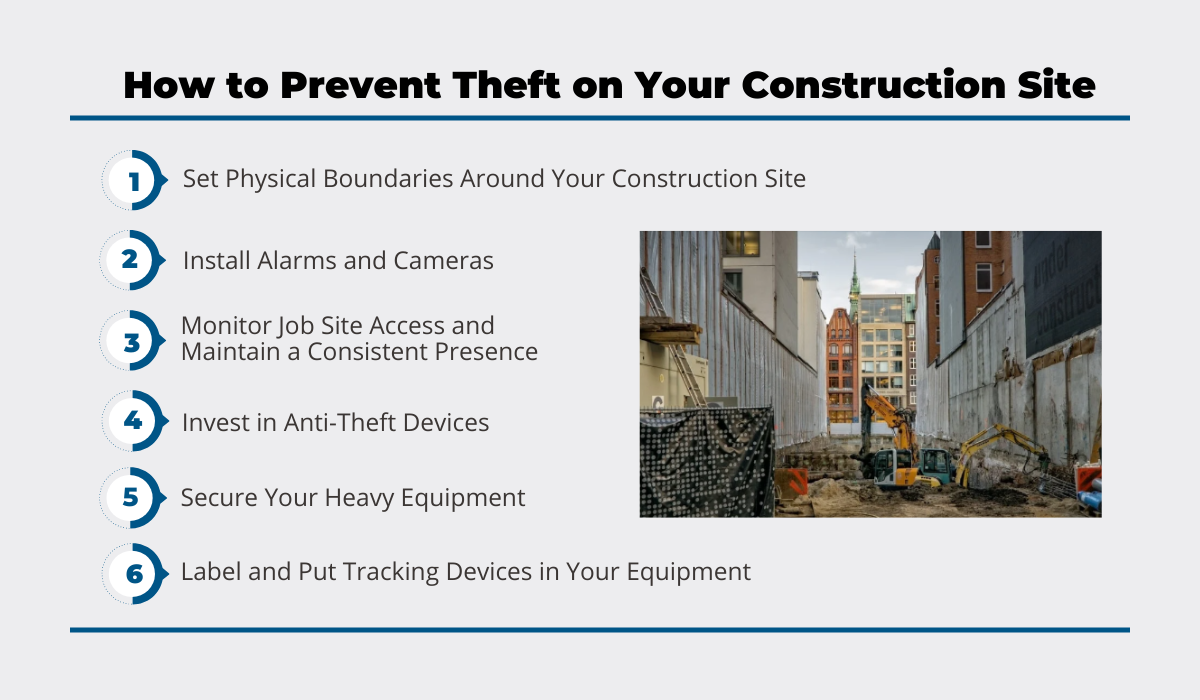
As some of these measures are self-explanatory, we’ll comment only a few for clarity.
For instance, anti-theft devices usually mean steering wheel locks, fuel cut-off systems, or ignition locks—all intended to prevent theft of heavy machinery—and a range of padlocks and other security devices for protecting other equipment and storage areas.
Likewise, “securing your heavy equipment” pertains to securing safe garage or fenced-off parking spaces for your machinery.
It can also involve establishing a security system that involves the daily actions of operators, such as removing equipment batteries and locking them up.
As for tracking your equipment, we already mentioned active GPS trackers that, when well-hidden (best solutions include bogus GPS trackers acting as decoys), can help the police catch the perpetrator, like in this case.
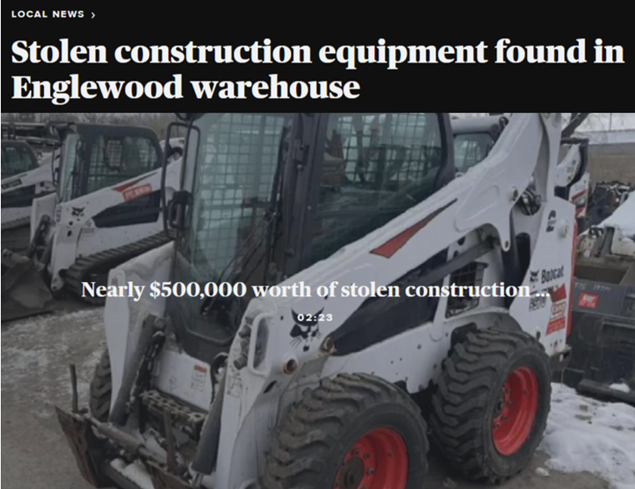
However, such trackers are typically too expensive and too large to be fitted on smaller equipment like power tools, specialized testing instruments, surveying equipment, and other high-value smaller-size assets.
That’s why construction companies resort to other theft-prevention measures, such as tagging all their construction equipment with asset tags.
Durable tags are difficult for thieves to remove and can serve as proof of ownership when stolen equipment is found.
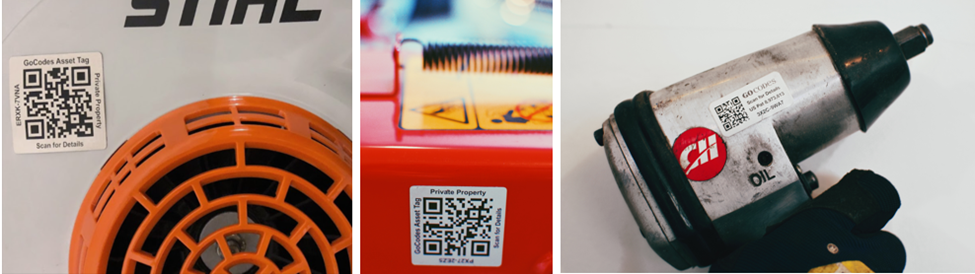
Strictly in terms of theft prevention, it’s best when such asset labels can be scanned using smartphones or tablets, and the tracking software automatically records the asset’s GPS location using the mobile device’s GPS function.
This provides you with the chain of custody (who used the equipment last) and the equipment’s last-scanned location, which can help you or the authorities locate the missing equipment.
Furthermore, when equipment is lost—or stolen and abandoned—anybody can scan the QR code tag and find your company’s contact info to inform you they found it.
In summary, considering the financial value and potential consequences of equipment theft, you should apply a combination of well-balanced, affordable, and multifunctional anti-theft measures that fit your company’s specific security needs and budget.
Relying on Manual Equipment Management
Of course, it’s clear by now that the ultimate equipment management mistake still practiced by many contractors is trying to manage all these processes using pen-and-paper or spreadsheet-based methods.
Without going into specific downsides of these methods, we’ll just say that manual equipment tracking and management is a time-consuming and resource-intensive process susceptible to human error.
Moreover, when compared to digital, cloud-based, automated equipment management software solutions, they lack real-time updates and instant accessibility from any internet-connected device provided by such systems.
Finally, spreadsheets—not to mention pen and paper—do not have a range of features that provide construction companies with all they need to efficiently manage their equipment.
Long story short, when selecting your equipment management software, you should ensure it has the following important features:
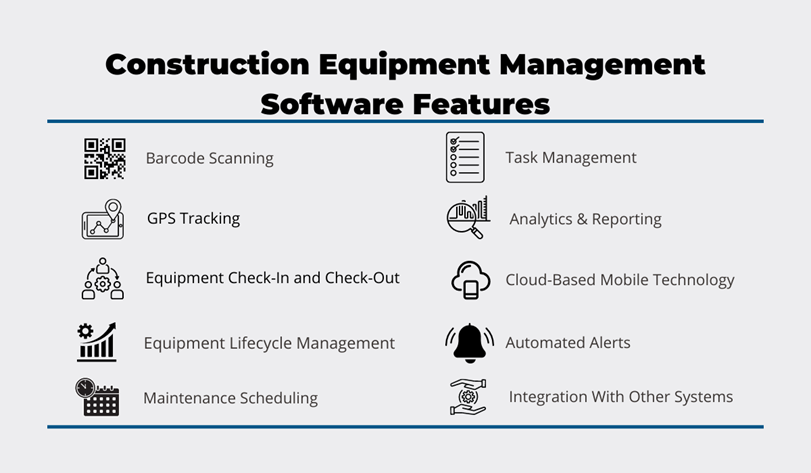
We already mentioned GPS-enabled QR code tags that, when attached to your equipment and tools, can be used for tracking the location, usage, maintenance status, and other details about each asset.
That same functionality allows you to establish an automated equipment check-in/check-out system, where your equipment management software keeps track of who took a piece of equipment or a tool and when they returned it.
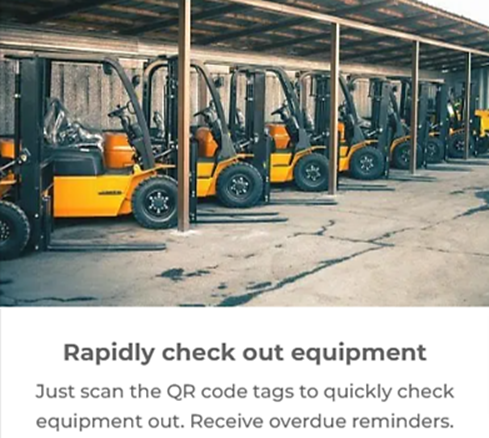
Furthermore, such software allows you to set automated alerts that, for instance:
- remind workers they should return the equipment they checked out
- notify service technicians about their upcoming scheduled maintenance task
- inform the inventory manager of low inventory quantity levels
These automated notifications have practical applications that lead to improved equipment management.
The same is true for all the other features listed above, coupled with prioritizing the software’s ease of use and mobile accessibility, simple system setup and training, and strong customer support.
For example, our equipment management software, GoCodes, provides all these features, and more, wrapped up in a simple, affordable, all-in-one package.
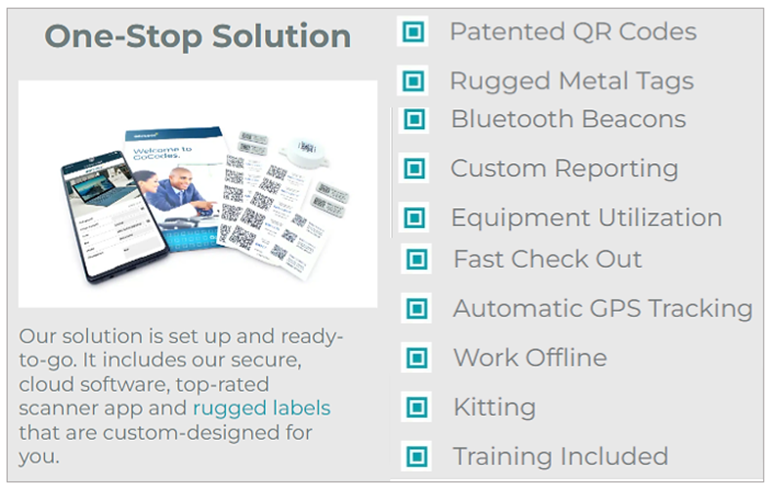
GoCodes uses an innovative combination of cloud software (accessible from any internet-connected device), an in-app scanner (that allows workers to use their phones as QR code scanners), and patented QR code labels (custom-designed and delivered to you).
This simplicity and versatility make GoCodes the only equipment management solution on the market that can help you address all the above equipment management challenges in a genuinely user-friendly and cost-efficient way.
For instance, your managers and workers will have instant access to the up-to-date central inventory of your equipment and tools.
There, they will be able to find information concerning the item’s location, current and past usage, maintenance and repair history, and other relevant data.
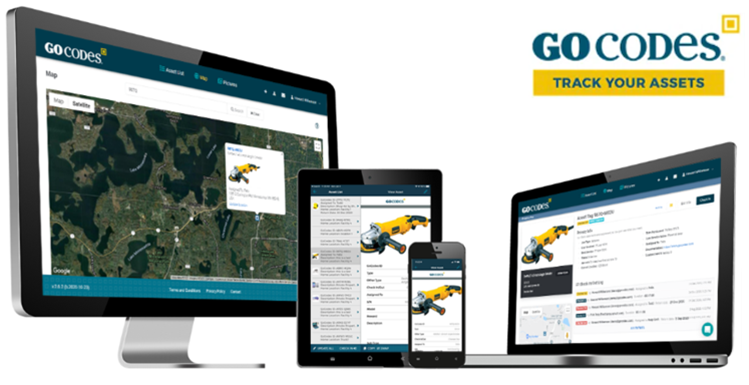
This alone allows you to regularly review your company’s equipment needs, more efficiently allocate and otherwise manage underutilized equipment, and plan and schedule timely maintenance.
Coupled with automatic GPS tracking, rugged labels, and an equipment check-in/check-out system, you can minimize equipment theft and increase worker accountability.
At the same time, you will have replaced manual equipment management processes with one easy-to-use, largely automated equipment tracking system.
The results will include minimizing errors, saving time, and allowing for data analysis and data-based decision-making.
Conclusion
To summarize, avoiding the mistakes we covered is much easier when a construction company uses equipment management software to collect data and track assets in real time.
Doing so enables it to automate, organize, and improve its equipment management practices.
In other words, your company gets everything it needs to efficiently maintain, protect, and manage construction equipment throughout its lifecycle.
As a result, you and your company will be able to reap a wide range of benefits ranging from reduced theft and loss, to lower maintenance costs and higher productivity.