GPS tracking is extremely useful for the construction industry. It has completely changed many facets of it, including security and the inner workings of the supply chain.
Using GPS tracking for construction equipment can help to prevent theft and ensure that equipment is properly maintained.
It can also monitor employees’ driving behavior and reduce construction equipment idle time.
Keep reading to find out more about how you can use a trustworthy and robust asset tracking system such as GoCodes to make the most out of your construction equipment.
In this article...
Preventing the Theft of Equipment
One of the most important uses of GPS tracking for construction equipment is preventing construction equipment theft.
Thieves are discouraged from visiting construction sites if they understand that the equipment is tracked.
Even if construction equipment does go missing or is stolen, it is usually much more easily found using GPS tracking.
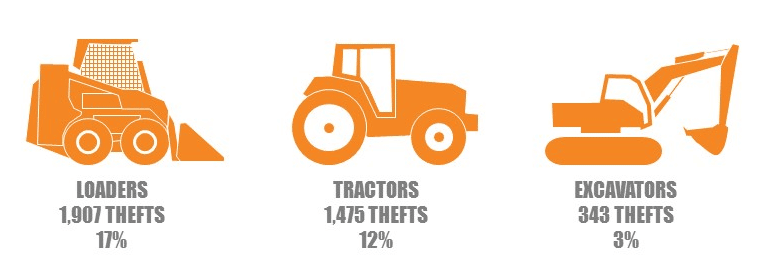
This infographic gives an idea of the expensive construction assets that are stolen from storage yards and build sites.
According to Charter Capital, a single excavator can cost anywhere between $100,000 and $850,000.
That’s a tremendous financial hit even for a large construction company, and the replacement cost of the vehicle does not take into account the potential consequences of halting work on projects, sourcing a rental replacement to fill the gap, and training team members on safe operation of the new or temporary excavator.
The cost of asset tracking or installation of a GPS system is minimal compared to the catastrophic loss of one major piece of heavy equipment.
GPS technology is also deployable for keeping construction equipment within a certain area in addition to tracking its location when away from its home base. This is known as geofencing.
When defined for security purposes, geofencing marks off an invisible boundary based on physical coordinates. When this perimeter is breached, the geofencing system sends an alert.
If administrators receive a notification for a certain piece of equipment that was not scheduled for movement, private security or law enforcement can quickly become involved.
This increases the chance of the equipment being recovered.
Ensuring Equipment Is Properly Maintained
Maintenance is a vital aspect of helping to keep expensive equipment in good working condition.
It is easy to forget to schedule such appointments when a machine is working well, and it’s tempting to push equipment past its maintenance date in order to meet a project milestone.
However, with proper preventive maintenance, it’s possible to greatly extend asset life and save on repair costs.
GPS tracking solutions such as GoCodes can automatically track equipment maintenance, allowing construction companies to efficiently conduct regular upkeep.
This can be done by creating maintenance schedules.
The system then alerts you when a certain piece of equipment is up for maintenance, so it can be inspected and any issues can be dealt with immediately, before the asset starts to break down.
This can help decision makers maximize the asset and also ensure that employees are handling a faultless piece of equipment.
Monitoring Employees’ Driving Behavior
The most obvious way to monitor your employees’ driving behavior is to track their location and ensure that they are spending adequate time at a job site.
In the event a team member is lost, GPS tracking can assist in providing precise directions. This monitoring can provide many advantages, as shown below:
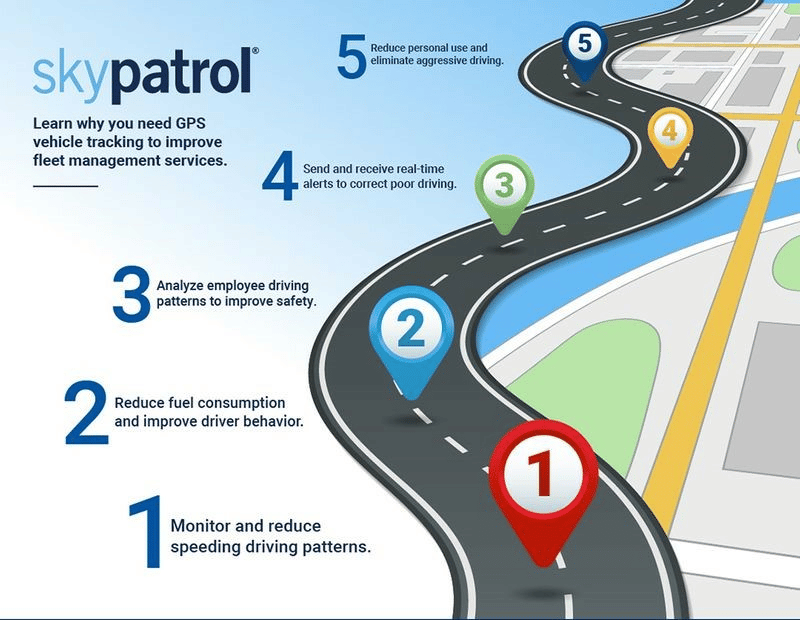
GPS tracking doesn’t merely let managers know where an employee and a vehicle are.
It can also report on real-time speed in various zones and study driving behaviors to determine whether or not an employee is operating safely—for example, whether they’re switching lanes quickly and too often.
Over time, this technology can lead to a reduction in both unauthorized personal use as well as dangerous or illegal driving behavior.
In addition, when GPS monitoring is combined with telematics, it can track fuel consumption, and this data can be easily studied to find ways to improve it.
Concentrating on this goal can increase employee efficiency and save money on fleet fuel costs.
GPS monitoring can even detect when operators accelerate or brake too aggressively.
This information can help to curb behavior that might lead to extra repairs and replacement part costs.
Such accountability is also useful for warranty claims, company defense in legal actions, and providing information to law enforcement.
Reducing Construction Equipment Idle Time
When equipment stands unused, it is not contributing to profits for your construction company. Increasing efficiency in equipment movement can yield many financial gains.
Optimizing which vehicle is moving to and from a site, as well as where it is scheduled to arrive next, often greatly reduces time wasted in traveling.
If an asset is scheduled to travel from site to site, using GPS data is effective in planning the route and order of stops.
Another form of idle time is easily reduced with the application of GPS data. Monitoring engine idle time can help to reduce maintenance and fuel costs.
This benefit of GPS equipment is a diagnostic gold mine for better understanding the stress on the engines of valuable assets.
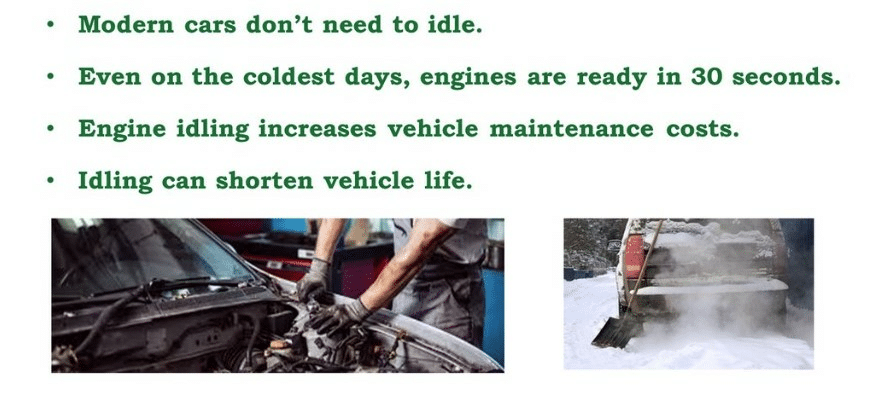
This infographic lists some good reasons to avoid idling.
When an engine idles, it wastes expensive fuel. In addition to the motives listed here, it’s important to impress upon employees that idling is prohibited in some areas, such as school zones.
Sitting with a vehicle’s engine on for an extended period in the wrong place can result in hefty fines.
Idling is also detrimental to the life cycle of a vehicle’s engine.
When an engine is not turning at its designed temperature, fuel does not burn as required, and the residue it leaves can cause frustrating and time-consuming maintenance headaches, in addition to contributing to engine underperformance.
Enforcing Contracts for Rented Equipment
GPS tracking is especially useful for enforcing contracts for rented construction equipment.
Tracking equipment rentals can help to avoid late fees (if renting from another company) and assist in avoiding theft or dangerous use (if renting to others).
Since some rental contracts are contingent upon the equipment remaining in an agreed-upon area, GPS tracking, like security geofencing, can alert both parties to a possible breach.
Even if your company does not currently enter into rental contracts, that might not always remain the case.
Have a look at the data on the rise of the construction equipment rental market:
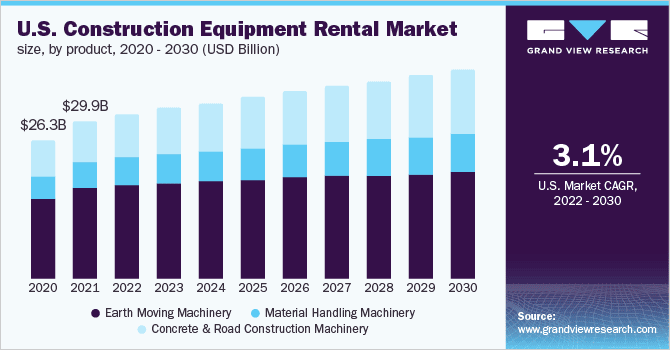
This chart includes concrete, road, material, and earth-moving machinery, all of which contribute to the fleet necessary for completing most construction jobs.
Becoming comfortable with the idea of using GPS equipment where rental equipment is concerned, then, is a smart business decision.
It can help prepare your company, no matter how small, for upcoming changes in the industry.
Rental theft affects the renter and the owner alike. Both are impacted financially, if only in the form of higher insurance rates.
According to the National Equipment Registry, about a thousand instances of theft of heavy equipment take place each month—and that number continues to increase.
Avoiding Client Disputes With Tracking Data
Construction companies can avoid and resolve client disputes using GPS tracking data stored within their asset tracking solution.
GPS data is applicable in resolving several client-facing situations.
When a client has suspicions regarding the construction project or wants to dispute an aspect of the job (such as the time or cost involved in the job), construction companies can use GPS tracking data as evidence to support itemized bills and price negotiations.
Data transparency is a company’s best defense against claims of fraud.
This graphic demonstrates how contract disputes can cost construction companies a great deal in terms of resources and legal fees:
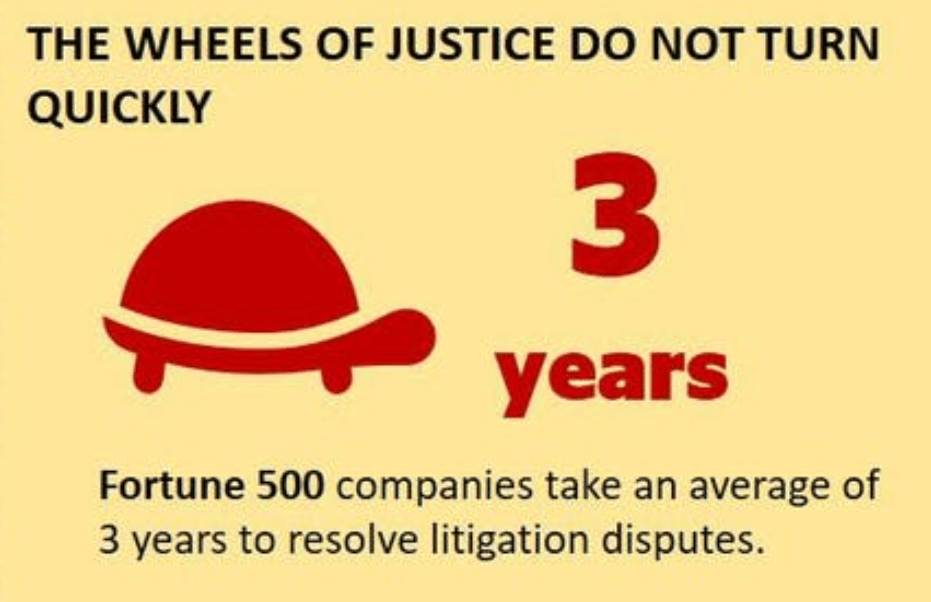
Since litigation is best avoided, deploying GPS trackers for tools, vehicles, and other assets can help to stop legal actions before they start.
Robust tracking systems not only pinpoint an item’s location—they can also establish its movements and verify how long the equipment was used.
Digital asset tracking records are far more accurate than those compiled by hand, and are automatically stored in the cloud for security and preservation.
Not all use of GPS-related data concerns legal action or complaints.
Clients might pose neutral questions about invoices, deadlines, and deliveries, or requests for bid packages might call for examples of average labor hours on a certain type of job.
The ability to quickly produce this information is extremely useful in maintaining a good relationship with your client.
It shows you are trustworthy, organized, and carefully tracking every aspect of the project you are completing together.
Conclusion
Using GPS tracking for construction equipment offers several benefits.
Asset tracking with GPS capabilities can help to prevent equipment theft and ensure that all items are properly maintained.
It can monitor employee driving behavior to encourage responsible road conduct in company vehicles.
Analyzing GPS tracking data is effective when attempting to reach goals regarding the reduction of equipment idle time, both in the sense of engine wear as well as asset underuse.
Finally, turning to GPS tracking for construction equipment is invaluable in enforcing contracts for rented equipment, settling client disputes, and providing excellent customer service.