If you’re in construction, you already know that poorly maintained equipment can cause a myriad of problems that ultimately reduce the overall productivity of your construction operations.
More serious issues can even stop them altogether, leading to project delays and cost overruns.
Conversely, when construction equipment maintenance is well planned, closely monitored, and proactively managed, this results in improved efficiency of equipment, fewer breakdowns, and longer lifespan.
Improved efficiency, in turn, reduces upkeep costs and results in higher profits.
Against this background, it’s clear that proper maintenance should be one of the top priorities for construction companies.
In this article, we’ll explore the top six reasons why effective construction equipment maintenance is so important.
In this article...
Improving the Efficiency of Equipment
Regularly maintained equipment is much more likely to perform optimally, which increases its efficiency as well as the productivity of the workers, while also minimizing delays, and maximizing cost and time savings.
In other words, although a piece of equipment, be it heavy machinery or power tools, might seem to be running fine, its performance is lessened, and its risk of failure aggravated by improper maintenance.
In fact, corrective maintenance (fixing equipment only when it breaks down) is, according to some experts, between three and ten times more expensive than routine preventive maintenance.
Moreover, even if such equipment does not break down, it will work less optimally, be less safe, and last for a shorter period than specified by the manufacturer.
For example, if an excavator’s bucket teeth and cutting edges are not regularly inspected and replaced when needed, its digging efficiency is reduced, which places more stress on its engine and other components.

Of course, this slows down the work, and prolongs the time necessary to complete the task at hand.
The same applies to other regular maintenance activities when any similar heavy equipment is involved—like changing the hydraulic fluid, inspecting the engine, and ensuring the tracks are properly lubricated (or tires properly inflated).
As for smaller construction equipment, such as power tools, poor maintenance will also reduce their efficiency and users’ performance.
For instance, when cordless drills are concerned, dull bits and worn-out battery packs both overwork the tool and slow down the worker.
The point of these examples is that, by keeping their equipment well maintained, construction companies increase their operational efficiency, resulting in a higher return on their investment in equipment and improved productivity of their construction team.
Preventing Unexpected Breakdowns
Poorly maintained equipment runs a higher risk of unexpectedly breaking down, which can result in more extensive repairs and longer downtimes, and even cause project delays and budget overruns.
Therefore, it’s more cost-effective to invest in routine preventive maintenance as the cumulative price of repairs is often much greater, as confirmed by the exorbitantly higher costs of reactive maintenance we mentioned.
For example, when a bulldozer is regularly checked and serviced, a mechanic can prevent a minor issue, such as a small leak in one of its hydraulic system’s hoses, from eventually turning into a major breakdown that would result in unplanned and more expensive repairs.
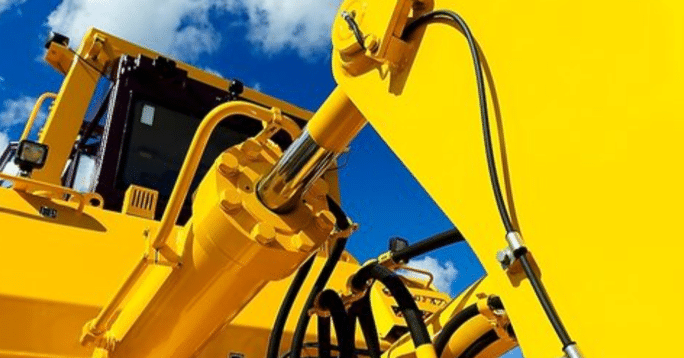
In other words, because the issue was identified early and the damaged hose was replaced before it caused any significant damage, the bulldozer kept running smoothly, avoiding a costly failure in the future.
Of course, this is true for any other types of construction equipment where the usual wear-and-tear of their components can, if left unchecked, eventually lead to more serious and disruptive problems.
So, preventive maintenance not only enables the timely performance of routine upkeep procedures, such as inspecting the engine or changing the oil filter, but also allows service personnel to identify and address potential issues before they escalate.
Therefore, proper equipment maintenance prevents unexpected breakdowns, as well as, consequently, longer downtimes and higher repair costs, helping you keep your construction projects on budget—and on schedule.
Increasing the Lifespan of Equipment
Naturally, regularly maintained equipment will last longer than equipment that is sporadically, if at all, inspected and serviced.
Therefore, proper maintenance will help extend the average lifespan of construction equipment and save companies money because they won’t have to replace their equipment as often.
Just like it maximizes equipment efficiency and minimizes breakdowns, preventive maintenance will help identify potential problems early, address them promptly, and keep the equipment in great shape for longer by replacing worn parts and servicing it at regular intervals.
Here is a graph that shows the impact that applying preventive maintenance (green line) has on the lifespan of equipment versus not applying it (red line):
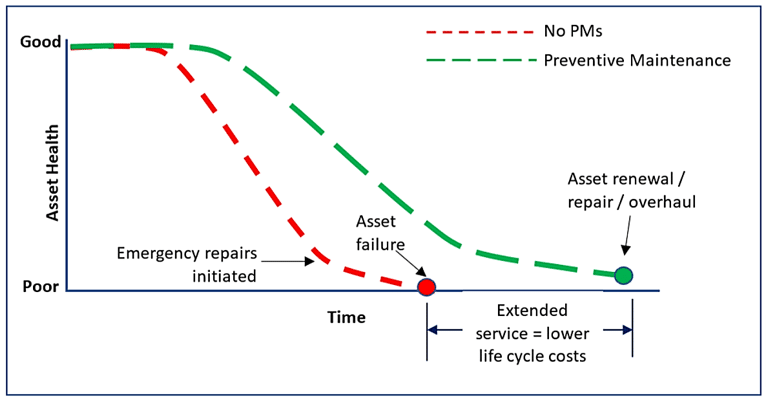
As you can see, when the point of asset failure is postponed with preventive maintenance actions, this allows companies to use the equipment for longer.
As a result, overall life cycle costs are lowered.
Regarding how such maintenance programs should be established to prolong the equipment’s life cycle, today’s software tools offer plenty of ways to schedule and keep track of maintenance.
For instance, our asset tracking software, GoCodes, uses patented QR code tags attached to different tools and equipment to track their location and usage and also keep track of their maintenance schedule.
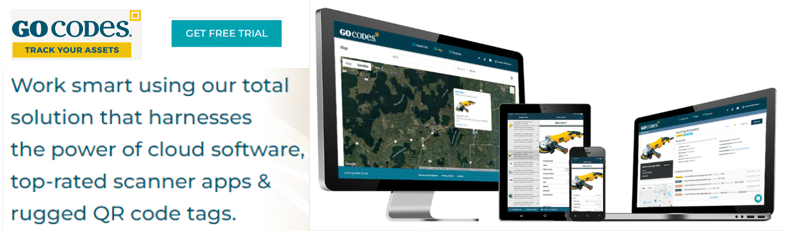
Simply put, GoCodes allows construction and equipment managers, as well as service technicians, to scan the asset tag or log into the tracking app using their smartphones to access relevant information about the equipment.
For instance, this can include the equipment’s last and next service date, entire maintenance history, list of replaced components, and service manuals.
It also enables you to automate maintenance scheduling, setting it up so that the assigned technician and other responsible persons receive notifications when maintenance is due.
This way, no one will forget, skip, or neglect equipment maintenance, thus extending the useful life of the items.
Overall, regular maintenance (when properly scheduled and tracked) helps increase the lifespan of the equipment, saving construction companies money in the long run.
Protecting the Safety of Employees
Perhaps the most important aspect of regular construction equipment maintenance is that it helps protect the safety of construction workers and everybody else on the job site.
In other words, poorly maintained equipment is less likely to work properly and can endanger the safety of your employees. It can lead to job site accidents, injuries, or even fatalities.
Of course, safety should be a priority in all professions, but particularly in construction, which is among the most dangerous industries in the US.
According to the US Bureau of Labor Statistics (BLS), there were 951 fatalities in the construction industry in 2021, as you can see here.
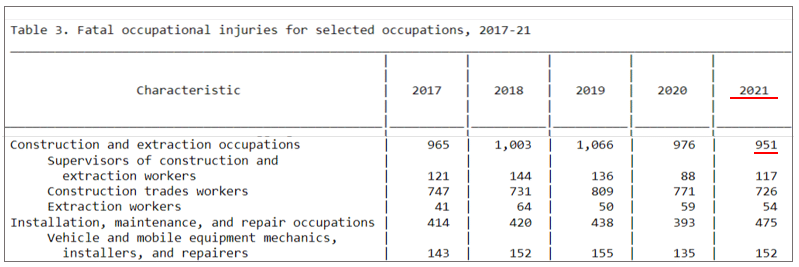
Although their data does not indicate how many of these fatal injuries resulted from poor maintenance, it highlights the importance of safety in all aspects of construction operations.
Therefore, regular equipment inspections are critical because they allow workers and service technicians to discover potential safety issues on time, before they cause accidents.
According to Howard Raphaelson, a construction accident lawyer, when maintenance is overlooked, the results can be fatal. In his words:
History tells us over and over again that poor maintenance at construction sites causes serious accidents.
For instance, quick hitches on excavators and other equipment, which help workers easily change the machine’s attachments, have caused a number of serious accidents when the bucket or other attachments suddenly detach and fall.
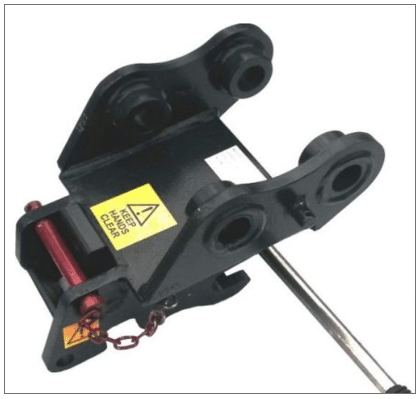
This is primarily due to responsible persons (operator, supervisor, service technician) not adequately inspecting, maintaining, and operating these quick coupler mechanisms.
To sum up, inadequate maintenance can endanger the safety of workers in many different ways. Regular upkeep minimizes those risks, helping construction companies keep their workers safe.
Preserving Warranty Coverage
When construction companies invest in new or used equipment covered under warranty, proper maintenance ensures that the warranty coverage will be preserved.
In other words, an equipment warranty will typically be void if the equipment was not adequately maintained prior to failure. The warranty provider will not cover the cost of repairs.
For example, let’s say your company has bought a new piece of machinery with a 2-year warranty, like this one, offered by Volvo CE.
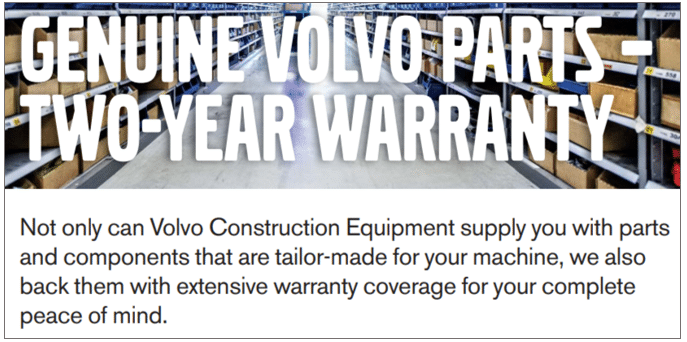
The machine is put to work, but after a few months of operation, one of its components fails.
When this failure is reported to the warranty provider (e.g., dealer or manufacturer), they will first have to determine why the component broke down in the first place.
This may be due to faulty workmanship when the equipment was produced or due to unauthorized modifications, improper operation, or poor maintenance on your part.
Therefore, you will need to provide detailed service records to prove that the machine was maintained according to the manufacturer’s recommendations.
Those are usually contained in an equipment maintenance log.
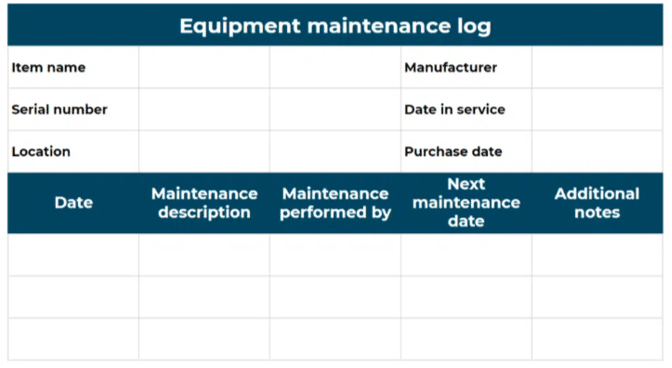
As a reminder, such maintenance records, i.e., dates and details about all maintenance tasks performed on your equipment, are best tracked and documented using equipment tracking software like GoCodes.
Continuing with our example, after the dealer or manufacturer is provided with proof of regular maintenance, such as the above log, receipts, and other documentation, they will approve your warranty claim and cover the repair costs.
Therefore, proper maintenance is not only needed to keep your equipment running smoothly but also to preserve warranty coverage in case of malfunction.
Maintaining Insurance Coverage
Similar to how warranties work, equipment insurance typically won’t cover the cost of repairs if the construction company neglected preventive maintenance that could’ve prevented the failure.
In other words, the insurance provider can, in some cases, deny coverage if the damage to a piece of equipment was, to some extent, caused by a lack of proper maintenance.
Therefore, keeping maintenance of your equipment up to date can be the deciding factor when the insurer decides whether to cover your insurance claim.
To better understand how equipment insurance usually works, here’s a simple explanation by Zensurance. We highlighted when damage would be covered (green) and when it wouldn’t (red).
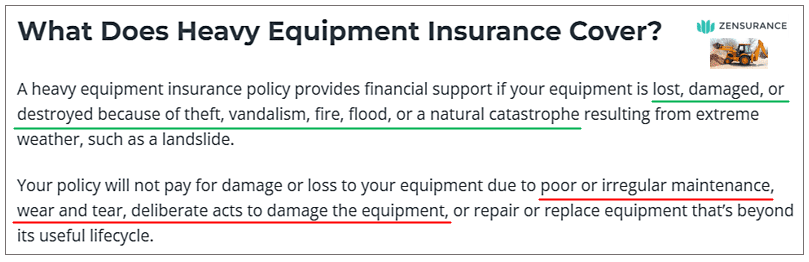
Therefore, if your insurance policy has a clause that excludes coverage for equipment damage caused by failure to perform routine maintenance, the insurance provider may refuse to provide coverage in such cases.
For example, let’s say your bulldozer caught fire by itself and got damaged, so you filed an insurance claim.
In that case, if the insurance investigator (claims specialist) determines that the bulldozer caught fire due to, for instance, a clogged air filter that hasn’t been changed for a long time (lack of maintenance), the insurance company would deny your claim.
If something like that happened, the repair or replacement of that bulldozer would need to come out of your pocket, thus defeating the whole purpose of having equipment insurance.
In conclusion, the fact that regular maintenance is often to maintain insurance coverage for construction equipment only underlines the importance of proper equipment maintenance.
Conclusion
So, we have described the six reasons why well-planned, closely monitored, and proactively managed equipment maintenance is of critical importance for construction companies.
Namely, it helps companies improve the efficiency of their equipment, prevent unexpected breakdowns, prolong its lifespan, increase the safety of employees, as well as ensure that the warranties and insurance claims are respected.
Given all these benefits, the ultimate result of a quality equipment maintenance program is improved overall productivity, reduced maintenance costs, and other life cycle management expenses, and hence higher profits.