Heavy equipment is usually one of the largest investments construction companies make, and naturally, they want to get the most out of it.
However, as time marches on and equipment deteriorates, construction company owners and managers will inevitably face the question of whether it is better to repair, rebuild, or replace their heavy equipment.
To answer this question, you need to review the pros and cons of each option and carefully consider the factors affecting your decision.
This article will cover those factors and discuss when it is better to repair, rebuild, or replace your heavy equipment.
In this article...
What to Consider When Making a Decision
In this section, we’ll focus on the factors construction companies should consider when deciding what to do with their deteriorating heavy equipment, from the rules of thumb to the questions that can guide their decision.
But before we move on, here’s a short overview of the three options.
When we say repair, we refer to fixing only what’s broken, i.e., replacing faulty components.
Conversely, rebuilding equipment means restoring its major and minor components to revamp it into a like-new condition.
Finally, replacement refers to purchasing a new or used piece of heavy equipment.
Now, let’s start with two general rules of thumb and top considerations when deciding what’s best in terms of cost, performance, and your company’s specific needs.
The first general guideline is to check whether the heavy equipment in question or any of its components are still under warranty.
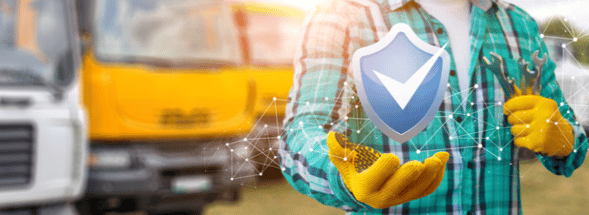
Although we’re primarily talking about older equipment whose warranty has expired, there might be cases where newer models break down or the failed component of an older machine is still covered by an extended warranty, so it’s wise to check.
Otherwise, a possible rule of thumb for simpler out-of-warranty equipment is the 50% rule.
The 50% rule states that if repairing a piece of equipment would cost more than 50% of its replacement value, you should replace it.
However, this rule may be applicable to some smaller and less expensive items, such as power tools, but it’s too general for most types of heavy equipment and doesn’t account for the middle option—rebuild.
So, when a piece of equipment breaks down, companies should ask themselves at least the following questions:
- Is the heavy equipment in question still under warranty?
- Has it been entirely paid off?
- How much would the repairs cost (including many of the above considerations)?
- Are its replacement parts still manufactured/available on the market?
- What is required in terms of the equipment’s future performance (same or better)?
- Would repairing or rebuilding improve its performance?
- What is its resale or salvage value without repairs?
- Would buying a new model give the company a competitive advantage?
Of course, these are just warm-up questions, as many more financial and operational issues come into play.
Kevin Smallridge, Managing Director at Medaco, listed his top considerations, besides the cost of repair:
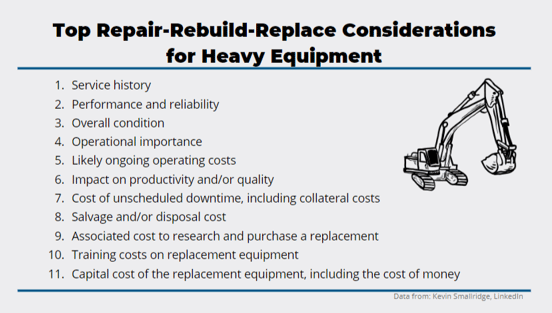
Yes, there is a lot to consider. And if you need even more information, you can check out equipment life-cycle cost analysis (LCCA).
This research analyzes a plethora of different factors you should take into account when making your decision.
In summary, repair-rebuild-replace decisions will primarily depend on the company’s specific needs, priorities, strategy, and spending power.
Given all the above, it’s clear that making such decisions for heavy machinery is usually more complex than the 50% rule indicates, and there’s much more to consider in order to decide what’s best in terms of cost and performance and your company’s priorities and finances.
So, let’s take a closer look at each option.
When to Repair Equipment
When should you decide to repair heavy equipment?
In essence, when the equipment is otherwise in good condition, aside from a few dysfunctional components, you should choose to repair it to save money as well as time.
This option is particularly good when the equipment is still under warranty, which would cover the cost of repairs, or when the equipment hasn’t been entirely paid off.
In any case, repairs are often the fastest and cheapest way to get the equipment fixed without causing longer downtimes, delays, and additional costs, especially when it can be repaired on-site by field service technicians.

So, if only one or two components have failed, and the machine can be put back into operation relatively quickly (depending on the type of failure), without being transported back and forth from the jobsite, repairing it will likely be the most convenient option in terms of time and money saved.
Again, this is your go-to option if the machine is still under warranty.
If the warranty has expired, but you’re still making payments on it, repair should still be among your top options, particularly when the piece of equipment can be fixed quickly and on-site.
This will usually produce the shortest downtime (while the equipment is being repaired) with no transportation costs for taking it to the service shop and back.
However, in some cases, when equipment is older, overused, or obsolete, repair might not be the best option.
In such situations, it may be difficult and/or expensive to find replacement parts, whether from the original equipment manufacturer (OEM), suppliers, or component brokers.
Another issue with such outdated equipment is that, if you want to restore a piece or upgrade its performance, repairing a few components will rarely do the trick.
In such cases, you should think about rebuilding or replacing your heavy equipment.
To sum up, if the equipment is in good condition, still under warranty or being paid off, and its repair would get it up and running again relatively quickly, you should consider repairing it to save money and time.
When to Rebuild Your Equipment
Unlike repair, rebuilding your equipment can restore it until it’s almost as good as new, thus extending its useful life, improving its performance, and saving money.
When several components of heavy machinery are dysfunctional, and the cost of repeated repairs becomes similar to, or even greater than, the cost of rebuilding it, you should consider this option.
Compared to repairs, rebuilding offers several advantages.
For starters, rebuilding equipment will allow you to prolong its useful life in a way that repairing a few faulty components can’t.
Why? Because when heavy equipment is rebuilt, many of its major and many minor components are replaced with new or refurbished parts.
That brings equipment into a like-new condition, and even allows you to replace some outdated technology with more efficient one, thus additionally improving equipment performance.
Of course, when opting for a rebuild, you should first explore whether the OEM offers rebuilding services, as that ensures the equipment will be rebuilt by expert staff using quality replacement components.
For instance, if you get your equipment from Cat, they offer to revamp it at a fraction of the cost of purchasing new.
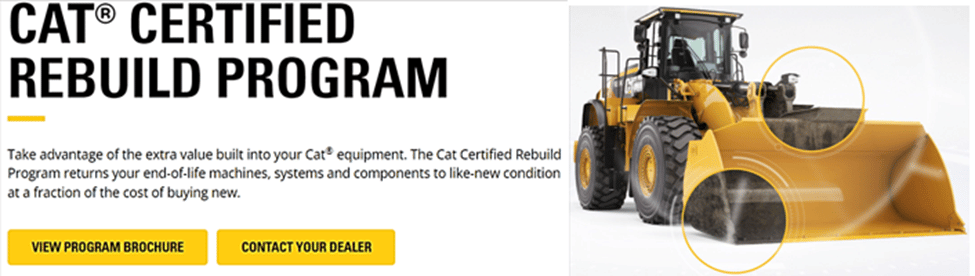
Other advantages include avoiding the quick loss of value after buying a new piece of equipment, similarly to how new cars depreciate after being bought brand new.
Rebuilding will also increase its resale or salvage value at the end of its useful life.
Of course, a rebuild will be more costly than repair and require a longer period while the equipment is out of order.
This means that it should be carefully planned, and all downtime, as well as the costs of replacement rentals should be considered.
One of the best ways to inform your repair-rebuild-replace decisions is to track the status of all your equipment, such as its maintenance and repair history, its usage patterns (whether it’s over- or underused), and other relevant information.
Nowadays, this can be done efficiently by employing asset tracking software.
For instance, our asset tracking app, GoCodes, allows you to track and collect information on your heavy equipment by using a combination of rugged QR code tags, smartphone scanner apps, and cloud-based software.
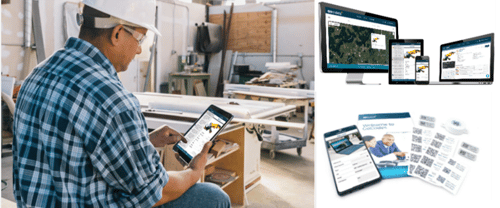
This and other construction management software can help you keep track of the location, usage, and condition of your heavy machinery, equipment, and tools, thus providing you with relevant data that will make the decision to rebuild much faster.
For example, when a piece of equipment breaks down, answering the initial set of questions (some of which we provided above) and accounting for other considerations will be greatly facilitated by having pertinent data on that piece of equipment.
More specifically, if its maintenance history indicates that multiple components keep breaking down despite their repair, that’s a clear sign to consider rebuilding heavy equipment.
Overall, when several components are dysfunctional, and the cost of their repair (and other upgrades, if possible) would be similar to, or higher than, the cost of repairing the equipment, it’s time to consider whether rebuilding it could extend its life and improve its performance at a considerably lower price than buying a new machine.
When to Replace Machines
In essence, replacing old equipment with new pieces is the most expensive choice that should be made when heavy equipment is beyond repair, outdated or no longer supported by the original manufacturer.
Another factor to consider for replacement is when the equipment’s ownership costs become lower than its operating costs.
More specifically, ownership costs include the purchase price of equipment (including transport and installation expenses), the costs of financing its purchase, taxes, and its resale/salvage/disposal value once it’s replaced.
Conversely, operating costs include running maintenance and repair costs, labor, fuel, and overhead.
Together, they produce the total cost of ownership (TCO), which can be used to calculate the machine’s costs per hour. This parameter is crucial for determining the actual cost of equipment.
Many OEMs will help you do that by using their online TCO calculator, like the one offered by Volvo CE for excavators.
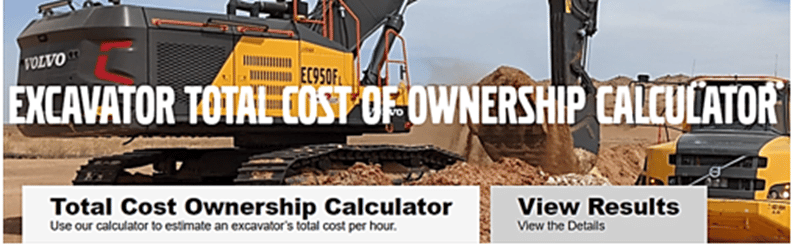
Armed with this knowledge, it’s much easier to estimate when to replace your heavy equipment, especially when different equipment metrics are tracked with the help of GPS trackers and internal or external equipment sensors.
Even without tracking and/or TCO calculators, if heavy equipment is beyond repair or even rebuild (e.g., because it is obsolete, so the OEM no longer manufactures its components), you should consider replacing it.
So, if you decided that replacement is the optimal choice, now is the time to examine the benefits of buying new vs. used models, which are listed below, courtesy of Quinn Company:
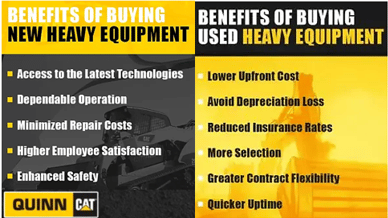
Of course, brand-new equipment will have the latest technology, a longer lifespan, fewer problems, and a warranty that covers the cost of repairs in the first few years of operation.
On the other hand, used equipment will have lower upfront costs and insurance rates and will not lose as much of its value over time compared to new machinery.
Overall, although replacement is the most expensive option, particularly when buying brand new items, such equipment can address many future issues and ensure improved safety, higher employee satisfaction, and enhanced performance of your new machine.
Conclusion
As said in the opener, heavy equipment is one of the biggest investments a construction company makes, so it’s logical to get the most out of it, which includes deciding what to do when it breaks down.
Now that you know what factors to consider when that happens and what specific circumstances make repairing, rebuilding, or replacing your equipment the most viable option, we hope that the information in this article will help you make the best decision for your business.