Determining the right time to replace construction equipment can be challenging, as there are various factors that come into play.
Those factors can include age and performance, short-term and long-term costs, as well as the benefits of getting a new machine.
However, there are also warning signs and reasons that can help construction company owners and managers determine the best time to replace equipment.
Here are five of them.
In this article...
Employee Safety Is in Question
Put simply, if employee safety is jeopardized, it’s time to replace your construction equipment.
As they say, safety comes first, and that’s especially true for construction as one of the most dangerous industries to work in, whether in the United States or elsewhere around the world.
Construction sites present workers with many hazards, but here we’ll focus on those related to using outdated or damaged equipment, which should be replaced due to safety concerns.
That’s because such equipment exposes employees to higher risks of accidents that can cause serious or even fatal injuries compared to new machinery.
Equipment ages and deteriorates through wear and tear compounded by overuse, improper operation, or poor maintenance.
Consequently, its components are more likely to wear out, get damaged, or even break off during operation.
This aggravates the already existing safety risks associated with operating perfectly functioning construction equipment and is a clear sign you should consider replacing such old or damaged pieces.
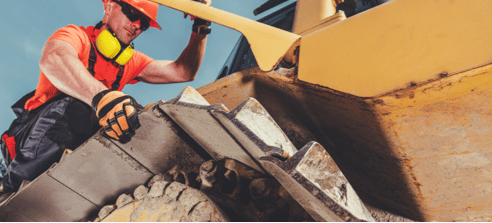
In addition to timeworn and damaged parts, electrical failures that can cause electrocution, burns, or fire become more likely as time passes.
To underline these amplified risks, let’s see what legal experts say about mechanical causes of heavy equipment accidents and injuries:
“Depending on how long the machinery has been used, the constant wear and tear on the machine can increase the likelihood of a machine accident. When employers fail to either replace or maintain their heavy machinery, the machinery is at risk of malfunctioning.”
And sometimes, maintenance isn’t enough to ensure safe operation, mainly because obsolete or near-obsolete equipment also comes with outdated, damaged, or worn-out safety features compared to new machines.
Given recent technological advancements, newer models are generally safer to operate and workers are safer in their vicinity due to new improvements, such as proximity-warning sensors, insulating guards, etc.
So, when equipment is run-down, damaged, or outdated to the point where it jeopardizes the safety of your employees, it’s time to consider investing in new, safer models that will significantly reduce the above-described safety hazards.
Maintenance Is More Frequent
When old and worn-out construction equipment requires frequent maintenance to keep it going, that jeopardizes the company’s operations and reduces its profit.
When maintenance costs are combined with other factors like longer downtimes, more frequent delays, or unplanned rental costs, old equipment might not be worth keeping.
Such productivity-lowering and cost-raising factors are particularly pronounced in cases of more frequent breakdowns of equipment which is critical for continued business operations (e.g., completing construction projects on time).
For example, a critical piece of equipment breaks down on-site. First, the task it’s been doing will be delayed, also postponing other subsequent tasks, ultimately resulting in project delays.
Then, a temporary replacement should be found as quickly as possible, meaning you might have to rent machinery, which is an unplanned cost.
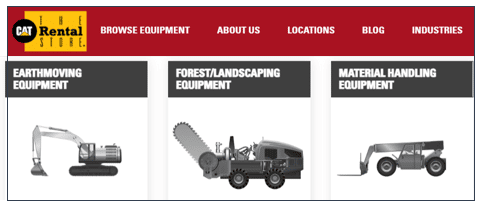
And naturally, there is the cost of repairing such broken equipment, including components, labor, transportation, and future maintenance.
When this happens regularly, it can seriously affect the company’s operational efficiency and jeopardize the expected profit on construction projects.
So, it’s a given that old and worn-out equipment will require more frequent maintenance, but the time it is replaced will depend on the priorities, strategy, and purchasing power of a construction company.
For instance, a company with enough capital (or credit) may use data-driven insights to routinely replace equipment when it reaches the point in its useful life when its maintenance and operation are no longer cost-efficient.
Moreover, useful life estimates for equipment and other assets also have major accounting and tax implications (depreciation), so it’s worth quoting the definition from Fundamental Accounting Principles (20th edition)
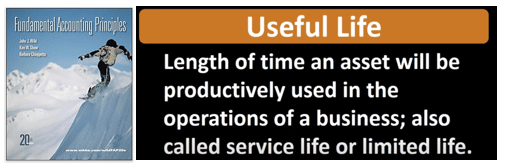
Thus, a company may choose to automatically replace a piece of equipment when its estimated useful life is up, regardless of how well it’s maintained, and therefore avoid many of the issues that older or worn-out machinery struggles with.
However, problems requiring frequent maintenance can occur before that, maybe even when a piece has only been in operation for a few years.
In that case, it’s worth checking if the equipment (or its components) in question is still under warranty.
If not, it’s good to stick to the 50 percent rule, where you replace equipment if its repair would cost more than 50% of the price of a new machine.
However, this rule doesn’t account for maintenance costs, delays, and cost overruns caused by equipment before it reaches the point when you might apply the rule.
A more precise way would be to calculate all the past costs directly and indirectly caused by such “high maintenance” equipment or conduct a life-cycle cost analysis (LCCA).
Of course, most companies will look to get the most out of their investment before replacing expensive heavy equipment, so there could be even more factors at play.
But, when it comes to old and worn equipment that needs frequent maintenance with rising operational and financial consequences for the company, it’s time to think about new machines.
Repair Costs Are High
It follows from the previous section that when repair costs are high, it’s a sign to consider purchasing new equipment.
As covered above, high repair costs can be a result of frequent breakdowns, but maintenance and repair can also become more expensive for various other reasons.
For instance, the necessary components may be discontinued or otherwise hard to find, and, as a result, become very expensive or even impossible to acquire.
This process is called equipment obsolescence, and we’ll consider how it can make the repair more difficult and costly to the point where getting new equipment would represent a more viable option.
So, to simplify this complex topic, we summarized the different types of equipment obsolescence from our article on that topic:
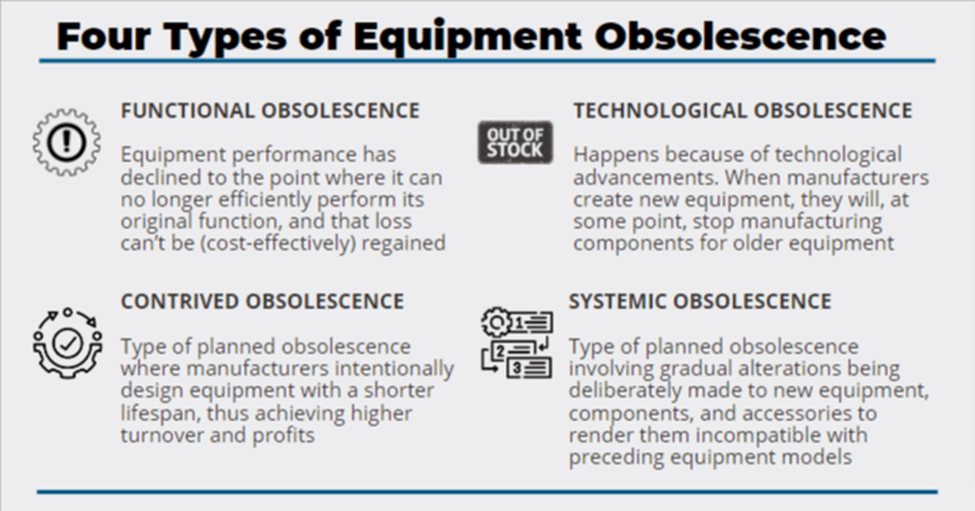
As you can see, equipment can become obsolete as a result of spontaneous processes such as loss of function or technological progress.
However, obsolescence can also be deliberately caused prematurely for profit in the form of contrived or systemic obsolescence.
In any case, regardless of type, obsolescence leads to the same thing: higher repair costs.
For instance, when the original equipment manufacturer (OEM) launches a new equipment model intended to completely replace its preceding models, continuing to manufacture components or provide related services for older models will become unprofitable at some point.
Consequently, technologically obsolete components needed to repair these older models will become more difficult to find and more expensive to acquire, provided that they’ll be available on the market at all and won’t need to be specially made.
Similarly, sometimes contrived obsolescence can be the reason why one particular piece of equipment keeps breaking down and increasing repair costs.
So, when repair of old and worn-out equipment becomes more difficult, and the cost of servicing it becomes more expensive for any reason, that’s a sign to replace it with new pieces.
Fuel Consumption Is Increased
Older and run-down equipment might not be as efficient at using fuel compared to newer equipment and might use more fuel to do the same amount of work, whether because of inferior fuel economy or excessive wear and tear.
If that’s the case, increased fuel consumption, aggravated by rising fuel prices, can indicate it is high time to replace such equipment with newer, more energy-efficient models.
In the first half of 2022, gasoline and diesel fuel prices went up 49% and 55%, respectively, which, combined with other health and geopolitical crises, sparked the highest inflation rate since 1981.
This increase (and recent decrease) can be clearly seen here, courtesy of Statista:
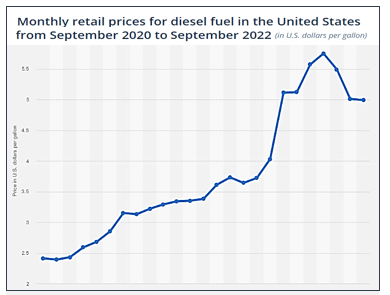
As a result, construction companies are doing all they can to reduce their fuel consumption, and one way is to replace older models with new ones.
Getting new machines can improve the company’s fuel economy in two ways.
First, in light of stricter environmental and sustainability standards, new equipment will generally use considerably less fuel (and time) to perform the same task compared to the older model.
Second, the company will avoid the situation where heavily used, overworked, or poorly maintained equipment needs more fuel (and time) to accomplish the same amount of work than before.
When replacement is considered, it might be good to look into other sources of energy, namely electricity from battery-powered construction equipment, like this new 5-ton mini excavator by Hitachi.
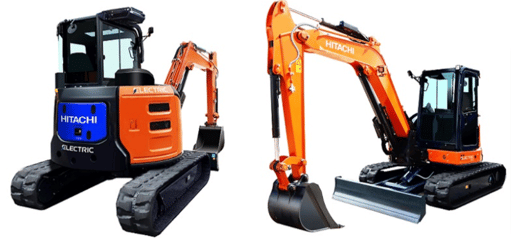
In addition to being more energy-efficient and environmentally friendly than their gasoline-powered counterparts, electric-powered equipment can be operated at night (low noise) and indoors (no emissions).
These features can give a competitive advantage to the company when bidding for projects.
However, when you’re not going electric, and even when the fuel usage between the old and new model doesn’t seem that different, new equipment can still provide benefits that should be considered.
For example, it can have a larger fuel tank capacity or, more often, perform its tasks faster than old or worn-out equipment, thus saving fuel and increasing overall productivity.
In summary, when fuel consumption of your equipment increases, whether due to inferior fuel efficiency or deterioration through heavy use, that’s a sign it should be replaced with newer, more energy-efficient models, especially in the current circumstances.
Efficiency Has Dropped
If the efficiency of old or run-down equipment has dropped to the point where it’s slowing down operations and jeopardizing productivity and profitability, that’s usually a sign to get new machines.
As said, older equipment can be outdated because its technology or its performance may have declined over time through wear and tear, so it will usually need more time to perform the same tasks than newer equipment.
Moreover, even when its efficiency might still be satisfactory, employees might find operating older or obsolete equipment more difficult and time-consuming, which decreases their productivity.
With that said, different construction management software or asset tracking apps allow companies to collect relevant data about the efficiency of their equipment, thus helping identify when performance has declined to the point that it warrants replacement.
For instance, if you want to track your equipment’s location, maintenance status, and utilization rate and gather pertinent equipment performance data, you could try our cloud-based tracking app, GoCodes Asset Tracking.

The GoCodes Asset Tracking app can even notify you when it’s time to service or upgrade equipment and can be used to monitor performance indicators and obsolescence risks, which contributes to making timely replacement decisions.
In that way, GoCodes Asset Tracking and other construction management software tools help construction companies identify operational inefficiencies, including old or worn-out equipment that’s underperforming or has become too difficult and time-consuming for employees to operate.
But, even when no tracking is involved, there will be indications that older or heavily used equipment has lost its efficiency, whether through the operator’s feedback, regular heavy equipment inspections, or incident and maintenance reports.
Another warning sign is when a company struggles to meet project deadlines or can’t take on as many projects because its outdated and run-down machines have lost their efficiency and are slowing down operations.
Overall, when the underperformance of equipment is affecting overall productivity and thus reducing actual and potential company profits, it’s time to acquire new machinery.
Conclusion
Remember, not replacing old or worn-out equipment in due time can lead to higher employee safety risks, more frequent maintenance, high repair costs, increased fuel consumption, and low efficiency.
So, after touring the different signs and features that point to the best time for replacing construction equipment, we hope this article will help you make better-informed decisions about when to get new machines.