When you rent out a piece of equipment for a construction project, you count on that machine to do its job.
What would you do if it malfunctioned in the middle of service, causing delays and monetary losses for your company? Chances are that you wouldn’t be too thrilled about it.
In the same vein, if you’re in the business of renting equipment, you don’t want to put your clients through such an experience.
If you want your rental business to be lucrative, you have to strive to keep your machinery in top condition.
Otherwise, you’ll get swarmed with bad reviews and unhappy customers. Even if your clients stay silent about the bad experience, they will not do business with you again.
Let’s look at the six ways to improve your maintenance and equipment performance!
In this article...
Keep the Manual at Hand
If you want proper equipment care and maintenance, you need to provide your team with the manufacturer’s manuals.
Even if you have the best team, you can’t expect them to know every single piece of information about your machinery by heart.
So, ensuring that the instructions are always easily accessible is an excellent start to improving maintenance.
Such manuals explain how to properly use and care for equipment, when to replace specific parts, and how to recognize an issue.
These points affect the maintenance team’s job and will therefore be of great use to them, primarily if they haven’t worked with a specific machine in a long time or ever.
For example, Komatsu’s operation manual for a hydraulic excavator explains the problems one might encounter with the machine and gives possible causes and solutions for them.
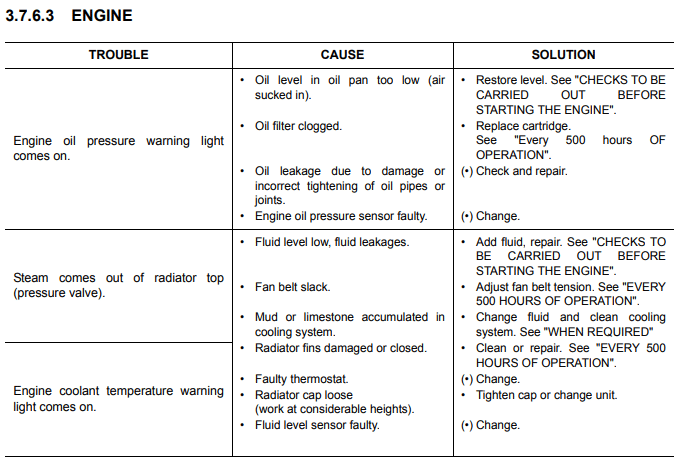
In this specific section, the manufacturer focuses on the engine and its problems. They list more than a few root causes of the issues and offer a solution for each one.
This way, even an inexperienced service specialist will be able to fix the problem quickly.
A way to keep these manuals close by is to keep physical copies.
However, this might not always be the easiest possible solution, especially if more than one employee has to see a specific manual or needs the information fast.
A viable alternative is using asset tracking software that allows your team to:
- Know who is using a certain machine and when it will be available
- Track maintenance sessions
- Upload service logs so each team member is informed
- Schedule future maintenance dates
- Access machine-related documentation, like manuals
Software like GoCodes allows you to upload documentation to an asset’s page. That way, any of your team members can access these documents and find the information they need.
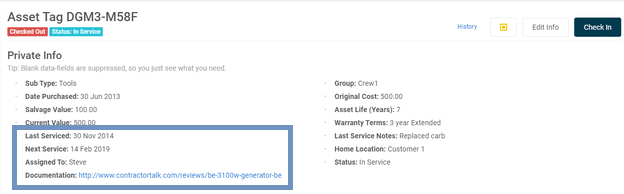
After a simple scan of the QR code using a smartphone, the maintenance team will access all the details regarding the machine in question.
This step lets them quickly check what kind of problems the equipment experienced before, when it was last serviced, and what the manual suggests.
You’re leaving little to no room for improvisation with the manual close by, improving maintenance quality.
Monitor Fluids Consistently
A great way to ensure your equipment is always ready to rent is to keep an eye on fluid levels.
Your maintenance team needs to check and refill hydraulic fluids, oil, and coolant fluids regularly.
When their levels fall below recommended, the machine might experience an expensive malfunction or a breakdown, which you cannot afford in the rental industry.
The Heavy Equipment Guide asked industry experts for tips on equipment fluids. Unsurprisingly, they advised sticking to the type of fluid the manufacturer recommends.
Brent Battaglia from CNH Industrial claims that using automotive fluids for heavy equipment puts more stress and wear “on the engine, the fluids, the filters and the machine as a whole,” which is why it’s not recommended.
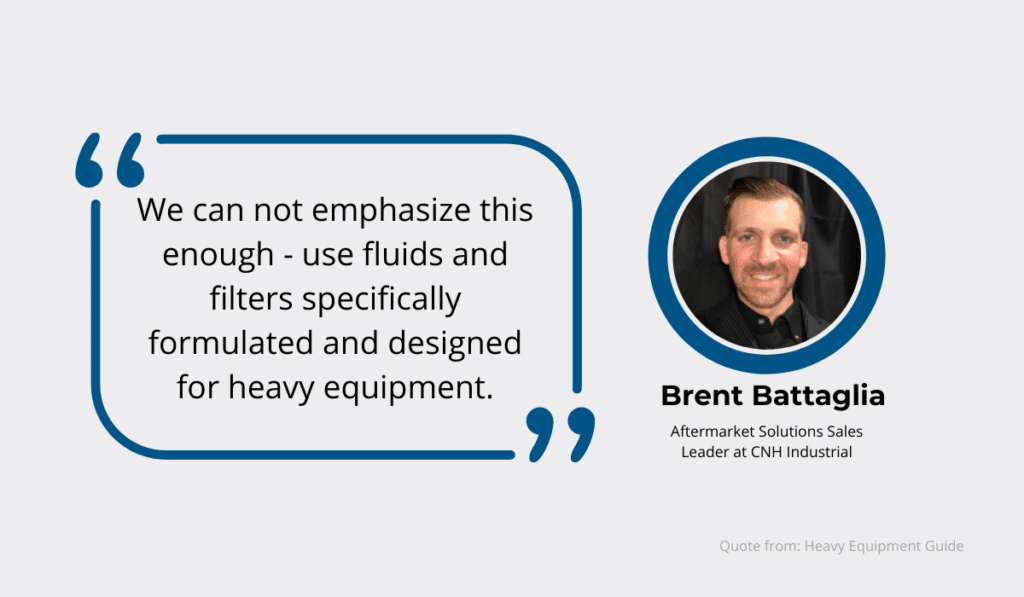
If you’re only using automotive oil on your heavy equipment, you could be damaging it with every refill, leading up to an expensive malfunction or irreparable damage.
Therefore, it’s easier to pay more for heavy equipment fluids and avoid costly machine breakdowns.
The best way to monitor fluid levels is to make it a part of your routine.
Reece Hill from CNH Industrial advises that “everybody does their daily operational checks, their pre- and post-operation checks” with the goal of spotting “any issues before they become a downtime event.”
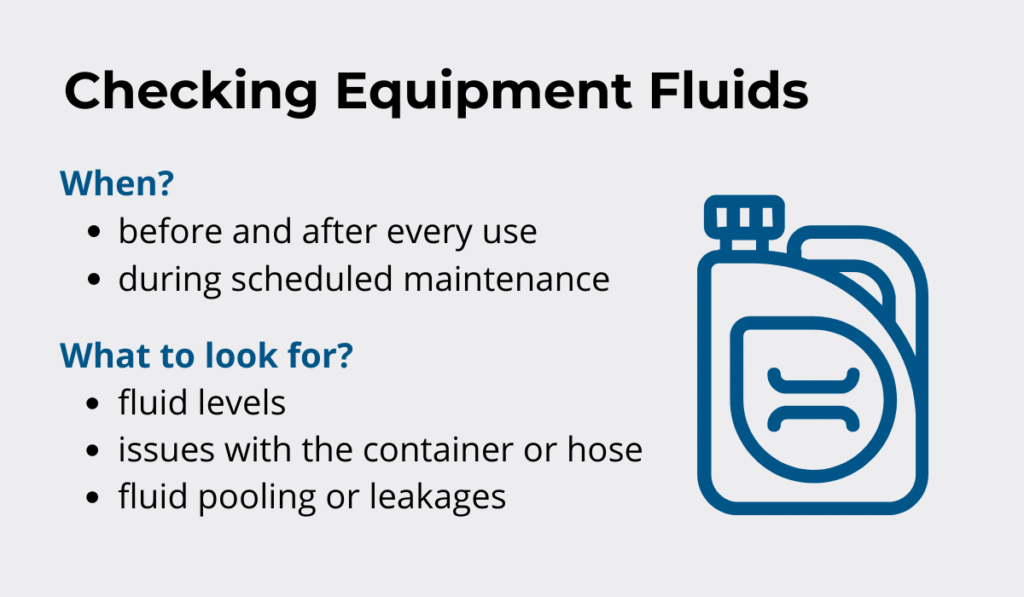
In other words, your maintenance team can perform these checks during scheduled service sessions, but the operators should do the same daily.
That way, your team will notice pooling liquid, broken hoses, loss of fluid, or similar issues and report them right away.
Industry professionals agree that you should check fluids daily, pre- and post-operation, and do a refill and more detailed checks according to the manufacturer’s instructions.
Regularly Grease Movable Parts
A great way to minimize equipment downtime and issues is to always grease the machine’s moveables.
The moveable parts are there to prevent other equipment parts from failing, which is why it’s essential to always keep them well-lubricated.
By doing that, you:
- Protect the equipment from rust and corrosion
- Reduce friction
- Help control temperature
- Prolong its lifespan
Lubricating moveables doesn’t take a long time, and it’s something that can make or break your equipment, so incorporate it into your daily routine.
Here’s how McAllister recommends you do it:
During the daily pre-use equipment checks, check all the lube points, as they refer to all the moveable parts that need greasing.
If you’re unsure of where they are, turn to the manufacturer’s manuals, which always list the acceptable options for fluids and grease.
Below is an example from the same Komatsu manual we’ve referred to before.
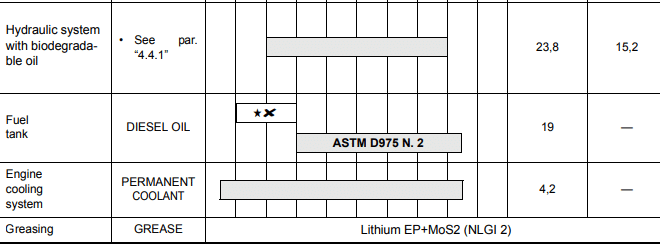
After locating all the relevant points, it’s time to grease each one for optimum performance and protection. The easiest way to do this is to get a grease gun and use the type of grease the manufacturer recommends.
That way, you won’t be causing damage to your equipment without realizing it.
Inspect each moveable part to ensure none of them are damaged or missing. After the check, wipe the pieces to remove any dirt and then apply grease.
When you follow all these instructions and grease the moveable parts of your equipment regularly, you’re making life easier for your maintenance team and customers.
Correctly Set Machine-Specific Adjustments
When your machine-specific adjustments are not correctly set, your equipment is at risk of malfunctioning.
Each machine has a different set of adjustments that are unique to it.
When you get new equipment, you should always have your maintenance team thoroughly check the manuals to determine which parts they need to adjust for that particular machine.
One of these adjustments is wheel alignment for trucks and other machines with wheels.
If the wheels are not correctly aligned, your equipment will run into issues with steering and handling, extended tire wear, and increased fuel consumption.
These issues can lead to bigger problems with the machinery and even cause breakdowns.
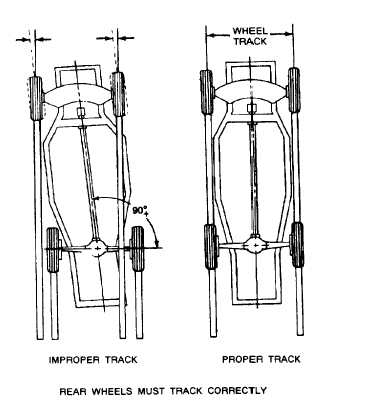
So, your service team should always check whether the wheels are tracking correctly. If they are not, your company shouldn’t rent such equipment to customers.
If you’re unsure when to check wheel alignment, Levanta gives the following pointers.
Check the alignment:
- When getting new tires
- After changing one or more steering components
- Before an inspection
- Before renting the machine to customers
- After the operator/customer complaints
If you follow this logic for other adjustments, your maintenance team should see a decrease in the number of complaints and adjustment-related issues with heavy equipment.
No matter the specific adjustment, it’s never a one-and-done deal, so your team should have a set schedule for them.
That way, you will always rest assured that everything is aligned the way it should be and that your customers are not in danger.
Check the Engine Air Filters
If you don’t regularly check the air filters on your machinery, don’t be surprised if you experience engine failure down the road.
Filters are there for a reason—to filter out dirt, silica, and other particles that might interfere with your engine.
However, for filters to be effective, you have to regularly clean and replace them. Otherwise, it’s as if they are not there.
Most equipment has two-part filters where the inner part serves as the final barrier if something manages to go through the first filter. Because of this, this filter always needs to be clean.
If it gets dirty, you should replace it.
However, the trick with air filters is recognizing when to change them. Replacing them too soon will damage your engine the same way forgetting to do so will.
That’s because filters work best when they are not completely clean.

So, the key is to find the golden median, which an experienced maintenance technician or a seasoned operator shouldn’t have a problem with recognizing.
If you don’t have an automatic indicator that shows you need to change the filter, you can always install an air filter gauge. When neither of these options is applicable, you should check the filter manually.
Other times, the machine’s performance will fluctuate, or you will see more fuel consumption, black smoke, or a decrease in engine power.

Any of these machinery problems can point to air filters being too clogged, which calls for a manual check. When checking the filter that way, make sure to clean the area around it before pulling it out.
That way, you don’t risk clogging the filter even more as you’ve removed all the dust from its surroundings.
Keeping your air filters clean prolongs the life of your engine and, therefore, the piece of equipment itself.
Keep the Equipment Clean
The best way to keep your machinery in good condition is to keep it clean.
When your equipment is full of dirt and grease buildup, dust, ice, or similar debris, the risk of a malfunction or breakdown keeps increasing.
If the operators don’t do daily checks before running the machinery, every time the equipment works could cause irreparable damage.
Cleaning equipment depends on the machine at hand, but some general cleaning tips apply to all equipment.
For example, you should have a designated cleaning station at your workplace, a space for operators to inspect and clean the machinery they are about to or have just used.
When cleaning, your crew should dismantle the removable parts to clean every possible nook and cranny.
The cleaner your machine is, the lower the chance of a piece of debris getting stuck where it shouldn’t and causing a malfunction.
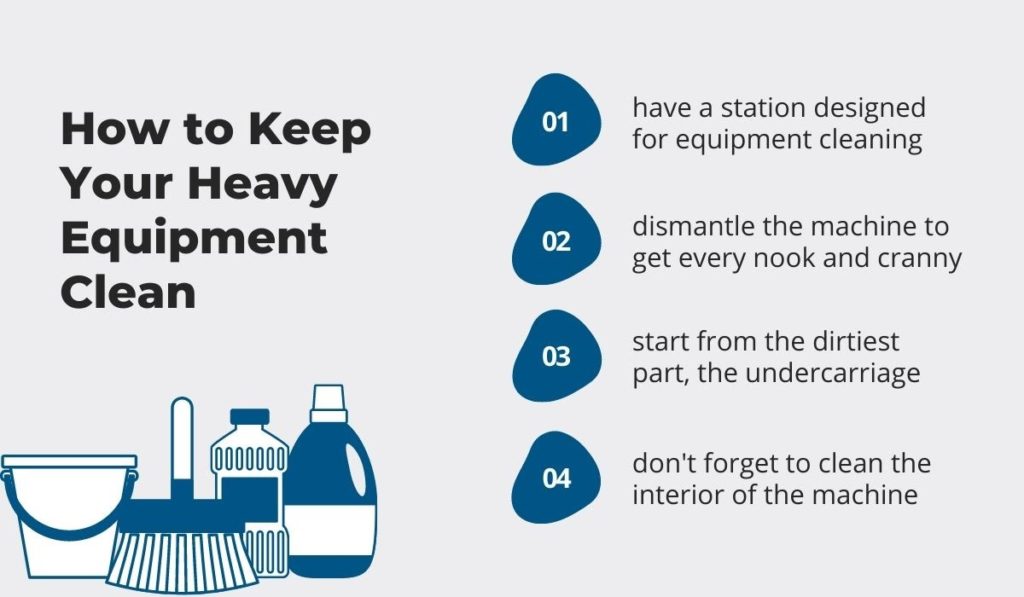
The best way to clean your machine is to start from the part that is guaranteed to be the dirtiest, usually the undercarriage. After that, move up until you get all the dirt off.
It’s a good idea to use a pressure washer combined with different cleaning agents.
Generally, before selecting a detergent or cleaning solution, ensure that it’s recommended by your manufacturer and suitable for the machine in question.
For example, Komatsu warns that using oil to clean equipment can leave a greasy film that collects dust while using a solvent can corrode the machine.
In other words, these two agents can cause more damage than good.
An important thing to remember is to clean the inside of the machine cab as well, just like you would with a car.
After all, these are closed spaces where bacteria and viruses can breed, so it’s necessary to clean and sanitize this part of the workplace.
Conclusion
When you’re in the business of renting equipment, said equipment needs to be in top condition and reliable. Otherwise, your customers won’t be happy with your services, and you may even go out of business.
A good maintenance team is what can make or break your company, which is why you should teach them to regularly inspect the machinery following the manufacturer’s manuals.
Don’t skimp out on fluids or maintenance sessions because such decisions could cost you a lot more in the long run.
The advice in this article should help you and your service team see a difference in equipment performance!