The construction industry is notoriously dangerous.
Research shows that workers in the construction industry get injured at a 71% higher rate than in any other. What is more, one out of five worker deaths in the US happens precisely in the construction business.
Therefore, it is no surprise that safety is one of the most important concerns in the industry.
And one of the main ways to prevent accidents is to conduct regular heavy equipment inspections.
If you regularly check your equipment, not only will you make your worksite a safer place, but you will also save money by prolonging your equipment’s useful life.
So, without further ado, let’s learn more about heavy machinery inspections.
In this article...
Why Are Heavy Equipment Inspections Important
Although it’s sometimes hard to detect an equipment issue on time and prevent a malfunction (especially if the cause is a manufacturer’s mistake), machinery often gives off warning signs that a trained eye can catch and fix.
Inspections allow you to discover many of such underlying issues and potential problems on time, but only if you set up a schedule for them and stay consistent.
The first benefit you get from regular heavy equipment inspections is improved safety.
It’s obvious why: these checks enable you to eliminate problems while helping ascertain whether your team can use the equipment safely.
Without regular inspections, you risk dealing with a potentially dangerous malfunction that can injure, maim, or even kill one or more of your workers.
This is how high the risk is: in 2019, there were 15 deaths in the construction industry a day.
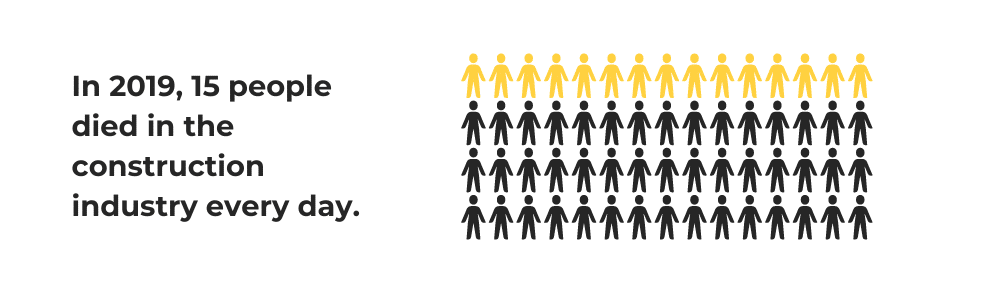
The worst part is that the number keeps rising, so you should invest in workplace safety as much as you can.
Your equipment operator should be instructed to check the machinery before and after every use, ideally with the help of a well-thought-out checklist covering all the possible hazards. After the operator finishes the check, they can determine whether any of the detected problems are urgent to fix.
If a critical issue is found during the inspection, the machinery needs repairs before you can safely use it again. So, the employee should notify the maintenance team of the issue and wait for them to repair the equipment.
Even if the operator finds non-critical problems, they should also notify the service team and schedule maintenance. In this case, the operator can use the equipment, but only if they are confident the problem won’t affect its performance and thus workplace safety.
When you promote daily inspections, you’re drastically improving workplace safety by reducing equipment-caused hazards. However, you’re also lowering repair costs while increasing productivity.
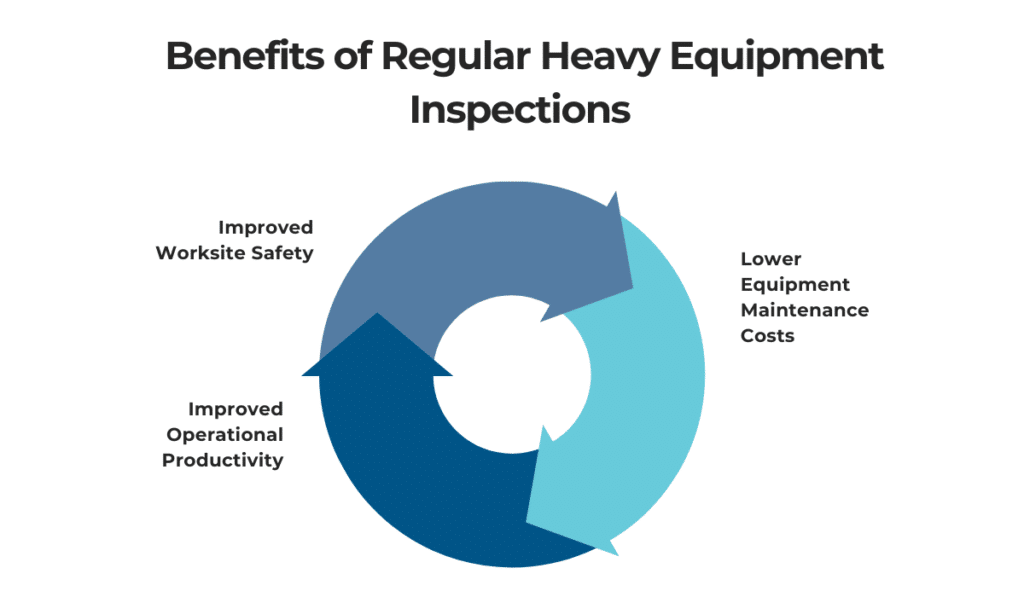
Faulty equipment can cause many problems for your company, starting from downtime to backlogs. When you regularly check your machinery’s condition, you prevent them from happening.
If equipment breakdowns occur, you might have to pay for the spare parts and invest time and effort into repairs. But at the same time, you have to continue paying the staff even though they can’t use that equipment, but instead, have to wait around at the worksite until you provide a replacement.
Additionally, unplanned breakdowns mean more irregular work for your maintenance team. If it’s an urgent matter, which is usually the case since equipment breaks down during use, your service staff will have to put everything else aside to work on the issue right away, thus creating a backlog in operations.
Of course, inspections are also necessary if you want to comply with Occupational Safety and Health Administration’s (OSHA) standards and avoid hefty fines for failing to do so.
In fact, OSHA raised its fines this year, and you could end up paying up to $13,653, which is the maximum daily fine per violation. However, should OSHA determine that you have willfully ignored their instructions or repeated an offense, you can be fined as much as $136,532.
As you can see, there is much financial risk involved in neglecting heavy machinery inspections.
Do them regularly to eliminate the risk of items breaking down mid-operation, decrease downtime and avoid backlogs.
Which Parts of Heavy Equipment to Check During Inspections
When performing heavy equipment inspections, you have to think of every detail, no matter how tiny.
Because of this, it’s best to create a checklist for each type of machinery, as this will ensure that your operators don’t skip a step or forget to check an important component, leading to potentially dangerous issues down the line.
When starting to inspect the equipment, your operators should first focus on the immediate surroundings of the machinery and look for any leaks and other signs that might point to an issue.
Next, they should check the equipment’s exterior for any damage and debris, inspect and report the damage, as well as remove any waste they find. Otherwise, the machinery might malfunction mid-use.
You should check all parts of the equipment as every single one of them affects safety in some way. That said, some elements, such as the electrical systems, brakes, fluids, tires, and warning devices, require a more detailed inspection.
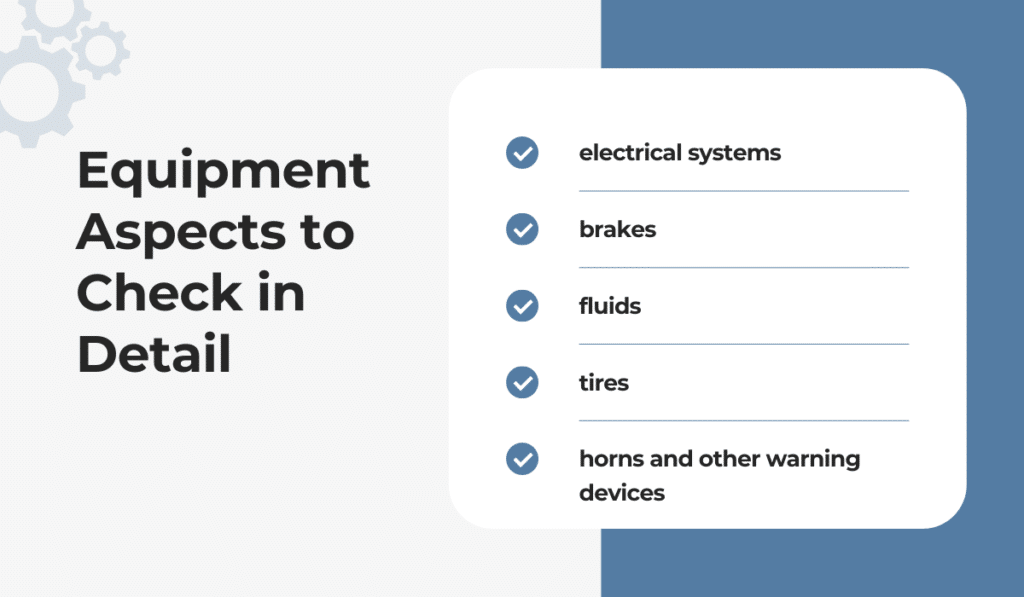
By electrical systems, we mean the engine, battery, lights, and any other electrically powered components. Of course, if one component is not working correctly, you can’t guarantee that the equipment as a whole will perform its intended function safely.
So, if you notice any issues with the electrical systems, report them right away.
Brakes are what helps your equipment operator stop the machine on time and avoid accidents or damage.
Since getting caught in or between objects is one of the fatal four causes of construction site injuries, it’s essential to check your braking system.
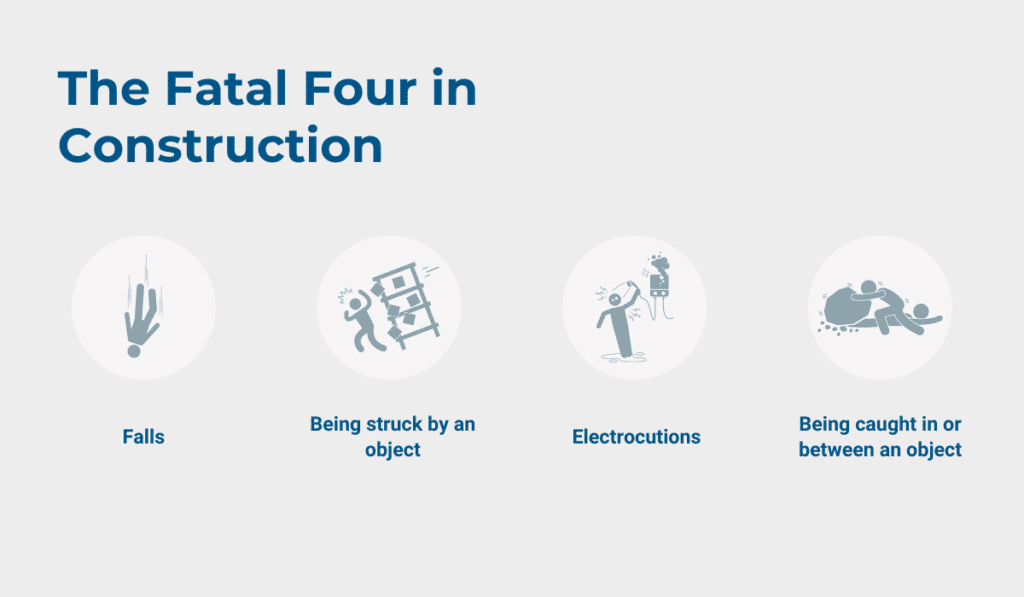
That way, you’ll prevent your machinery from injuring your workers by hitting or trapping them.
Fluids keep your equipment running smoothly. When your machinery isn’t well lubricated, perhaps because it leaks oil or other liquids, this increases the wear and tear. If this goes unnoticed, it can lead to extremely dangerous malfunctions.
Tires also have to be in good condition as construction equipment often operates on uneven or rough terrain. Your operator should check for premature wear and tear and other types of damage to ensure they can use the vehicle safely.
A good practice you can implement is failure analysis, which helps determine why you had to replace the tires on previous occasions. You can fix the problem more effectively once you understand the cause unless it’s the usual wear and tear.
Horns and other warning devices help your operators notify others on the worksite if they get in the way of equipment, so it’s important that they are in working order at all times. You should test and check them regularly.
OSHA recently fined a company $5,390 for failing to remove equipment from rotation even though it didn’t have functioning headlights or warning signals, which is sign enough of how dangerous it can be to neglect this part of the equipment.
Now that you know what parts you should check, let’s find out when it’s best to inspect them.
When to Conduct Heavy Equipment Inspections
There are no definitive answers to when it is best to inspect your heavy equipment, but there are certain recommendations you can follow if you want to achieve optimal performance.
The safest way to go is to conduct quick general inspections of heavy equipment before and after every use, so your operators know whether it’s safe to use a particular piece of machinery in the first place.
After use, the team can check if the machinery has experienced any damage. If so, the operator can immediately notify the maintenance team and get the equipment fixed before any subsequent use.
But, the machinery should also go through an inspection whenever you move it or install it in a different place. Even if it was in optimal condition before the move, a part of it could get damaged in transport, which is why it’s essential to check the equipment before operating it again.
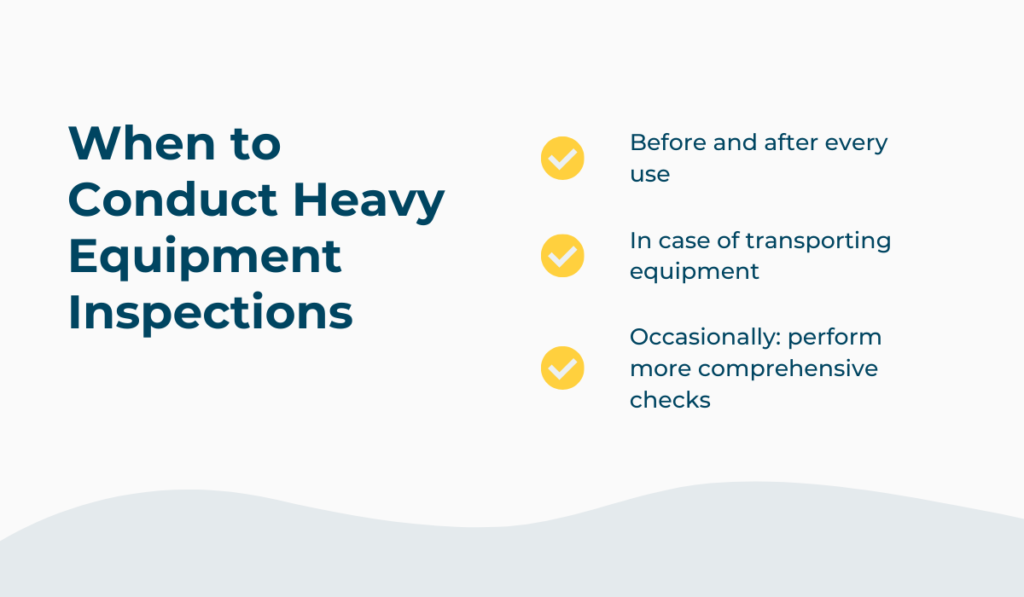
On top of all this, you should schedule comprehensive equipment inspections regularly.
These checks should be a lot more thorough than the ones your operators do before and after every use, as your maintenance team should carefully inspect each part of the equipment to see what effect being in use had on them.
Your operators and maintenance staff can also tell you whether a piece of machinery has a recurring flaw that makes it require more frequent maintenance and that needs to be addressed.
Best Practices for Heavy Equipment Inspections
Heavy equipment inspections are more than checks; they’re a process.
What do we mean by that? Simply that these inspections have to be regular and uniform.
You should have a plan for each check, yet be ready to change it whenever circumstances change, such as wear and tear, previous damage, or anything that can affect how frequently and in detail you have to inspect the machinery.
To get to the bottom of the ultimate heavy equipment inspection, you should first understand all the relevant regulations.
OSHA and the Department of Transportation (DOT) have equipment-related rules you should follow. Otherwise, you may be subjected to costly fines.
While OSHA regulates how often and who should check each piece of your machinery in detail to ensure safety, DOT focuses on transportation rules to keep everyone on the road safe.
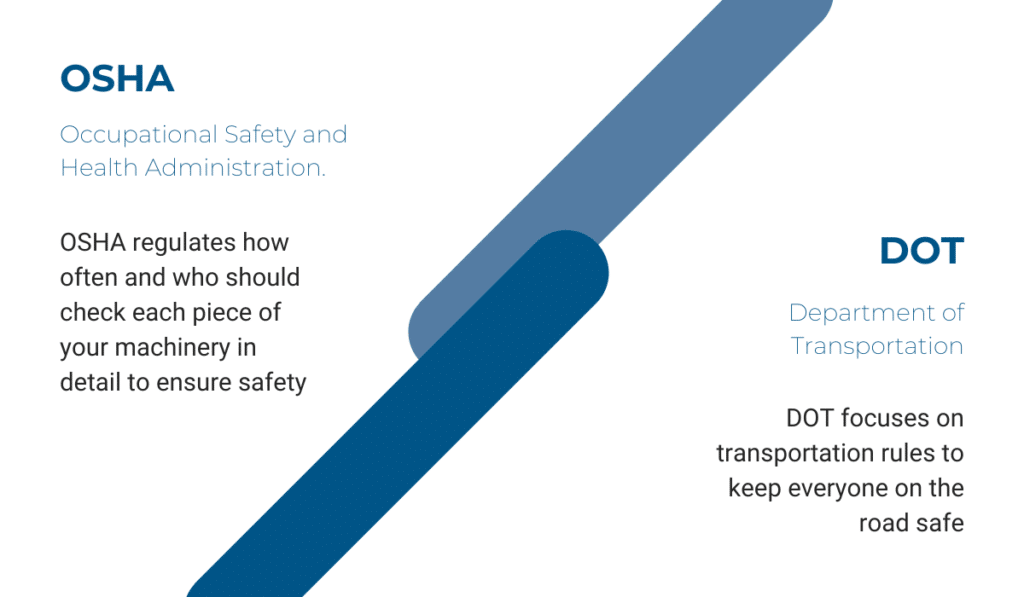
These rules change based on the type and weight of the equipment, so make sure to look up information concerning each piece of machinery you own.
That’s not all, though. Your state and county might have their own rules, so inquire about them too, to avoid breaking the law unknowingly.
Once you have a clear idea of the different regulations that are in force, you should study the equipment manuals to see the manufacturer’s recommendations.
Each piece of machinery comes with instructions written by those who designed and created it. So, instead of operating on assumptions, consult these manuals to better understand how the equipment works.
The instructions should contain information on how often you should perform inspections as the equipment ages. If instructions don’t come with the equipment, consult your team to determine the optimal schedule for detailed heavy equipment inspections.
Armed with the knowledge from the manuals, you should strive to understand how your equipment is used daily.
In other words, you need to know how often the machinery is used, whether it is over or under-used, and whether the operator knows what they are doing. These aspects can negatively affect the equipment, causing more wear and tear that you might not know about, impacting safety.
The best way to go about this is to invest in quality training, so your workers know how to safely and properly operate the equipment. That way, they’re not risking anyone’s safety. At the same time, your operators are taking care of the machinery.
To help your team stay on track and be uniform, create inspection checklists, including all the necessary steps that a worker needs to take before using the equipment.
They can be step-by-step or pass-or-fail checklists, whichever you opt for, just make sure they are easy to follow.
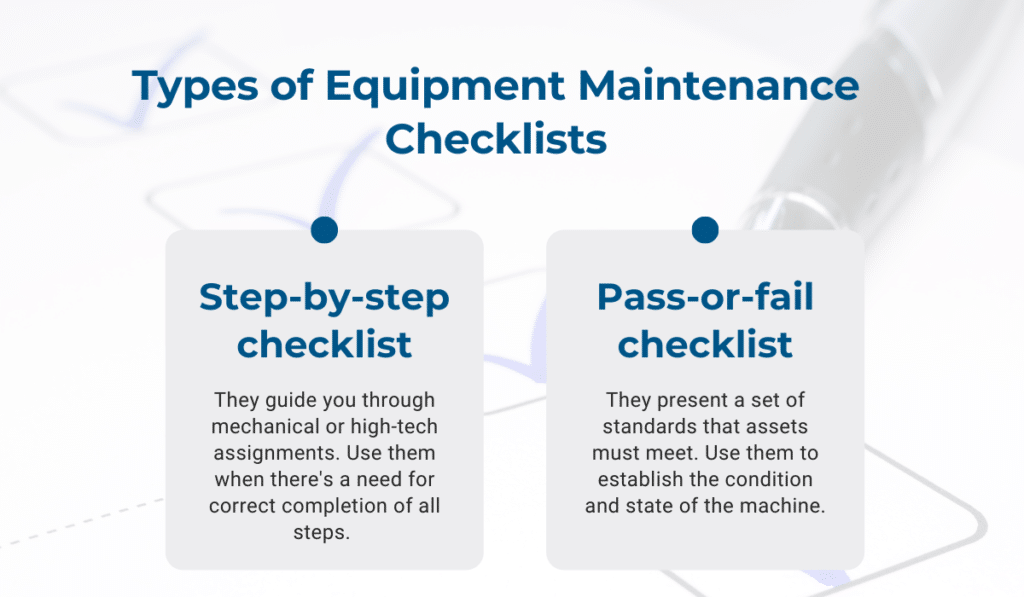
When creating the checklists, use the resources you have to make sure you create comprehensive material.
You should make a note of the following:
- Your operators and their experience with the equipment
- Your maintenance staff and their understanding of the machinery
- Previous maintenance records
- OSHA, DOT, and state regulations
- The manufacturer’s manuals
The instructions will let you know what the manufacturer recommends. Still, your team will be able to provide additional information, like the equipment’s current condition, previous damage, wear and tear, and other data that help you personalize a checklist for each type of machinery.
When performing safety checks, you first have to look out for signs your equipment needs servicing as explained in this article. As mentioned earlier, most machinery gives a warning before malfunctioning, so your operators should be trained to spot these signals.
Overall, there are many steps you can take towards efficient heavy maintenance inspections, but if you don’t record them, you won’t be able to make use out of them.
That’s why you should use a digital solution to track maintenance.
Over half of all contractors are already using software to monitor equipment inspections, and 79% of them believe it can improve safety.
So, reap those benefits yourself by introducing software that helps you keep records of previous repairs while allowing you to schedule future ones.

This step will ensure that you’re always on track by reminding you of upcoming maintenance, giving you time to plan the servicing, and minimize downtime.
Being consistent in your maintenance is something that helps promote safety and prolong your equipment’s useful life.
Conclusion
There’s no one-size-fits-all when it comes to heavy equipment inspections, but failing to conduct them can endanger your workers and cost you a lot of money in fines.
To make sure your inspections are at their most effective, the best thing to do is gather all your records and reports from the field to create detailed inspection plans for each type of machinery you own.
Train your staff to check equipment for malfunctions not only during detailed maintenance sessions but before and after every use.
That way, you will practically eliminate unexpected malfunctions and keep your workers safe, which is the point of heavy equipment inspections.