As technology progresses, every piece of equipment will become obsolete at some point, meaning that all equipment is subject to the long-term risk of obsolescence.
However, perfectly functioning equipment can often become obsolete prematurely for varied reasons, such as loss of functionality, lack of critical components, various market forces, and regulatory changes, to name a few.
To ensure that these often complex equipment obsolescence issues are not detrimental to their operations and bottom line, construction company owners or managers should create and implement an effective equipment obsolescence management plan.
Here’s how to do that in six steps.
In this article...
Performing an Equipment Audit
Construction companies should begin by performing an equipment audit to understand the current state of their equipment and whether it might already be obsolete—or soon become so.
Of course, when it comes to construction, the term “equipment” covers a large array of machinery and tools, together with their components, spare parts, and accessories.
Combined with all the ways in which equipment obsolescence can occur, this means that determining which equipment is in more or less immediate danger of becoming obsolete can be, to put it lightly, a challenging task.
And that’s why the first step in this audit is to find out, for each piece of equipment:
- when it was made (date of manufacture)
- how long it has been in use
- its maintenance and repair history
This information can be collected manually, but it’s more likely that it already exists in digital form, whether in a spreadsheet or as part of inventory management or equipment tracking software.
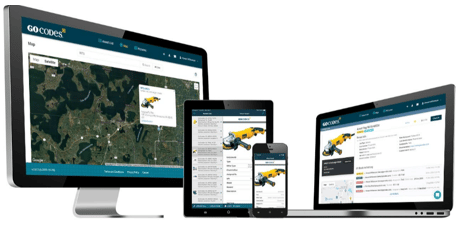
Naturally, that will make compiling an equipment inventory list and collecting the data necessary for this audit faster and easier.
However, it should be noted that, unlike spreadsheets, software solutions, especially cloud-based, will allow for future monitoring, updating, and reviewing of obsolescence-related equipment information by all users in real time, which makes them an essential part of any effective obsolescence management.
The second part of this equipment audit, which takes place once the relevant information is collected, aims to prioritize the inventory list by identifying equipment exposed to immediate and mid-term obsolescence risks.
Namely, the collected information is compared with the product lifecycle data (instructions, manuals, warranty info, website) provided by the original equipment manufacturer (OEM) to determine whether certain equipment or its components are already or may soon become obsolete.
To sum up, an equipment audit consists of determining the current state of all equipment and then, using the manufacturers’ data, narrowing the list down to equipment that an obsolescence management plan should prioritize.
Doing a Risk Analysis
A risk analysis is crucial for creating an obsolescence management plan as it helps companies assess and rank equipment according to its criticality for operations and risk of obsolescence.
This risk analysis begins by determining which equipment (flagged as outdated) is critical for continued business operations, as such equipment should be prioritized in the obsolescence plan.
Using the data gained in an equipment audit, construction companies should then assess the likelihood that critical equipment (i.e., its components or technology) will become obsolete and the impact (both operational and financial) of that happening, as shown in this obsolescence risk matrix.
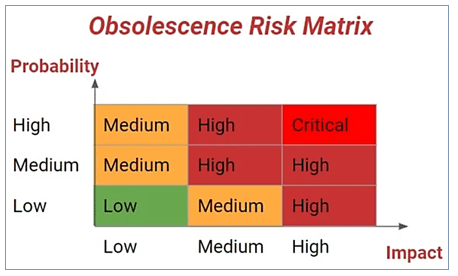
Furthermore, they should evaluate such equipment to determine its:
- risk of breakdown (high, medium, low)
- downtime costs in case of breakdown
- maintenance and repair costs vs. the cost of replacement
Construction companies should also research whether components needed to repair such equipment are still available on the market, either from OEMs or suppliers of compatible components.
Thus, a risk analysis allows companies to assess and prioritize equipment for obsolescence management purposes and provides the key elements for creating an effective obsolescence management plan.
Creating a Budget
The first two steps—audit and risk analysis—described how construction companies can prioritize obsolete or near-obsolete equipment according to its criticality for operations and the severity of associated obsolescence risks.
Now it’s time to decide what to do with such equipment, i.e., whether it should be replaced (and when) or kept in operation after maintenance and repair.
This decision will primarily depend on long-term and mid-term planning of equipment replacements, upgrades, or modifications and the funds available.
However, outdated equipment that will remain in use should be monitored, and different measures should be taken, such as preventive maintenance or stocking up on spare and replacement parts.
The latter often involves making last-time purchases of soon-to-be discontinued components because their useful life is often shorter than that of the equipment they’re a part of, as illustrated here.
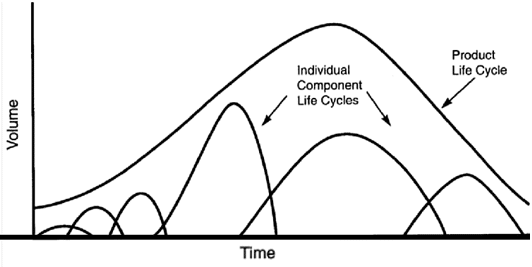
Naturally, such obsolescence management measures require resources, and that’s why companies should create a dedicated budget for maintaining and repairing obsolete or near-obsolete equipment.
So, companies should first identify the resources (people, monitoring tools and methods, and funds) that can be allocated for obsolescence management.
They should then create a corresponding budget to operationalize their obsolescence management plan.
When tasking people, establishing monitoring tools and allocating the funds budgeted for obsolescence management, companies should keep in mind that most of the available resources should be dedicated to equipment with the highest risk of obsolescence.
Thus, creating a budget for short-to-mid-term obsolescence management allows construction companies to put their plan into action and take proactive measures to maintain the outdated equipment’s performance and extend its useful life.
Choosing a Reliable Supplier
The next step in implementing the obsolescence management plan is finding one or more reliable suppliers that will help minimize adverse impacts arising from obsolescence.
Let’s first note that all preceding steps—audit, risk analysis, and budget—couldn’t be done without the information provided by OEMs and various other equipment and component suppliers.
Thus, keeping open lines of communication with them is crucial for continuous monitoring and effective obsolescence management, and reliable suppliers can be invaluable in a pinch.
As for obsolete or near-obsolete equipment, companies should contact component suppliers and brokers and make a list of those that stock rare components that might be needed in case of breakdown.
Knowing where to acquire such components and who to contact to get them delivered quickly helps minimize downtime and delays, especially when critical equipment breaks down.
When trying to find reliable suppliers, companies could benefit from incorporating some of these tips into their selection criteria:
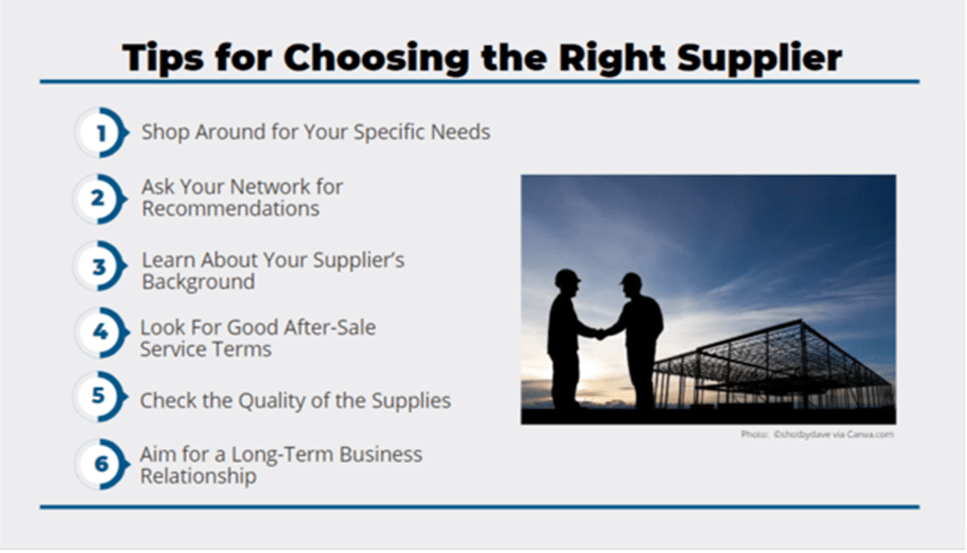
In these times of supply chain disruptions and rising costs, open communication and good working relationships with reliable suppliers are often crucial, particularly when critical equipment breaks down and work grinds to a halt.
So, to minimize downtime, delays, and cost overruns when that happens, companies should find out in advance where they can (reliably, quickly, and at a reasonable price) acquire rare components or components for obsolete and near-obsolete equipment.
Thus, finding and picking one or more reliable suppliers of hard-to-find components that might need to be delivered quickly in case of breakdown allows companies to proactively minimize the adverse impacts of obsolescence.
Creating a Component Stock
By creating their own component stock, companies ensure they’ll have the components, spare parts, and accessories needed to keep their outdated equipment going before they’re discontinued or go out of stock.
This can be accomplished by taking proactive and reactive obsolescence management actions, both of which involve the above-highlighted good collaboration with manufacturers and suppliers.
In the previous section, we suggested that companies should proactively contact suppliers ahead of time to ensure that components for older equipment are still manufactured, still in stock, and can be quickly obtained.
Another proactive measure is to list components, spare parts, and accessories for equipment with the highest obsolescence risk and consider creating a strategic stock while they’re still relatively affordable and available on the market.
Of course, sufficient storage space should be secured, which should be considered when allocating resources and budgeting for obsolescence management.
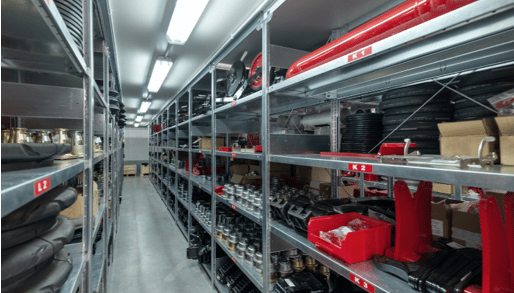
Another, more preventive approach to creating a component stock is looking out for, or arranging to get, product change notifications, end-of-life, and last-time-buy announcements from OEMs and suppliers.
In this way, companies can stay informed on components being discontinued or going out of stock, so they can react appropriately and use this opportunity to stock up on components that will ensure they can keep servicing and repairing their outdated equipment.
As OEMs often change, update, or discontinue equipment models and/or stop manufacturing their components, it’s best to check and agree with OEMs and suppliers that you’ll receive such notifications in due time.
So, when construction companies know the obsolescence status of their equipment, they can take action to create a component stockpile that will ensure they have everything they need to maintain and repair their obsolete equipment and keep it going for a long time.
Organizing an Equipment Database
Last, but not least, construction companies should compile all gathered data on the obsolescence status of their equipment and organize an equipment database.
This database can be established in a simple spreadsheet, as part of an end-to-end construction management software, or a practical equipment tracking mobile app.
In any case, it should allow companies to monitor, update, and review the obsolescence status of all their equipment, with special emphasis on equipment critical for operations and/or at high risk of mechanical breakdown or obsolescence of components.
We already said there can be no effective obsolescence management without continuous monitoring.
Likewise, we hinted that spreadsheets are less effective than current software solutions and mobile apps construction companies use in their operations, which can be easily adjusted to track and manage obsolescence risks.
For instance, a mobile app like GoCodes enables construction companies to track all their equipment and tools by using rugged QR code tags, smartphone scanners, and cloud software.
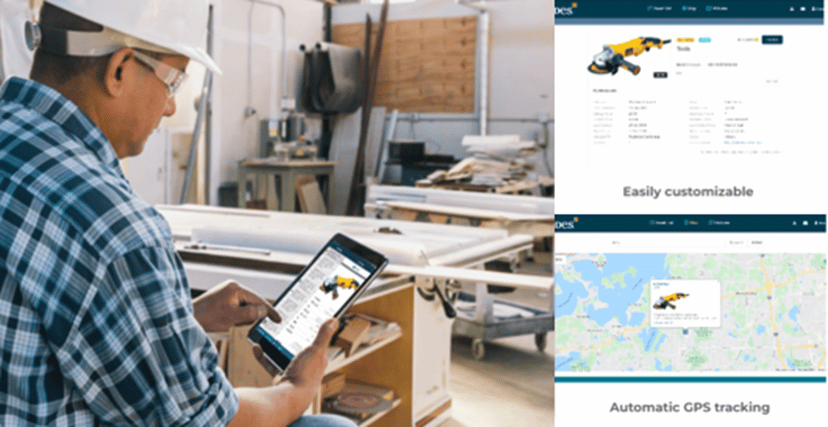
For individual equipment, GoCodes enables users to simply scan the tag with their smartphone to access all relevant information like its date of manufacture, usage info, last service date, and maintenance and repair history.
As this app is highly customizable, the obsolescence data gathered in all previous steps can be easily added to the equipment information.
What’s more, it allows managers to organize a central equipment database they can access at any time to monitor, update, and review the obsolescence status of their equipment.
In any case, this database should contain, both for outdated equipment and its components, information like:
- assessed level of breakdown and obsolescence risk
- expected availability of components on the market
- components and spare parts available in storage
- who to contact if components need to be delivered
Thus, whether organized in a spreadsheet, as part of an end-to-end construction management software, or as an easy-to-use app, an equipment database enables companies to monitor the status of their equipment continuously, thus enabling effective obsolescence management.
Conclusion
So, now you know what construction companies should do to keep equipment obsolescence issues under control.
Remember, this process starts with an equipment audit and risk analysis, where you identify, assess, and prioritize obsolescence risks to all equipment, and flag high-risk pieces crucial for everyday operations.
Then, based on the data you compile, you create a dedicated obsolescence management budget.
To do that properly, you’ll need to communicate with OEMs, find reliable suppliers, consider creating a component stock, and organize an equipment database for future monitoring.
Ultimately, these steps will allow you to effectively manage equipment obsolescence, thus avoiding or minimizing operational and financial risks for your construction business.