Running a successful and profitable construction business requires the strategic consideration of many different elements, and perhaps none are more critical than the costs associated with construction equipment ownership.
Besides the initial purchase price, there’s a host of other expenses that can significantly impact a project’s financial landscape.
In this article, we’ll delve into the often underestimated facets of construction equipment ownership, exploring six distinct costs that can cast a long shadow on your budgets and timelines.
Let’s get started.
In this article...
Initial Equipment Cost
Initial equipment costs represent a capital investment that’s necessary to own a particular asset.
Owning construction equipment entails buying it, sure, but it also includes transportation, assembly, and installation of the asset, as well as the sales tax, which is sometimes applied during purchase.
Those are all some basic expenses you’ll have to cover when embarking on your journey as a construction equipment owner.
Now, you may be interested in some specific figures.
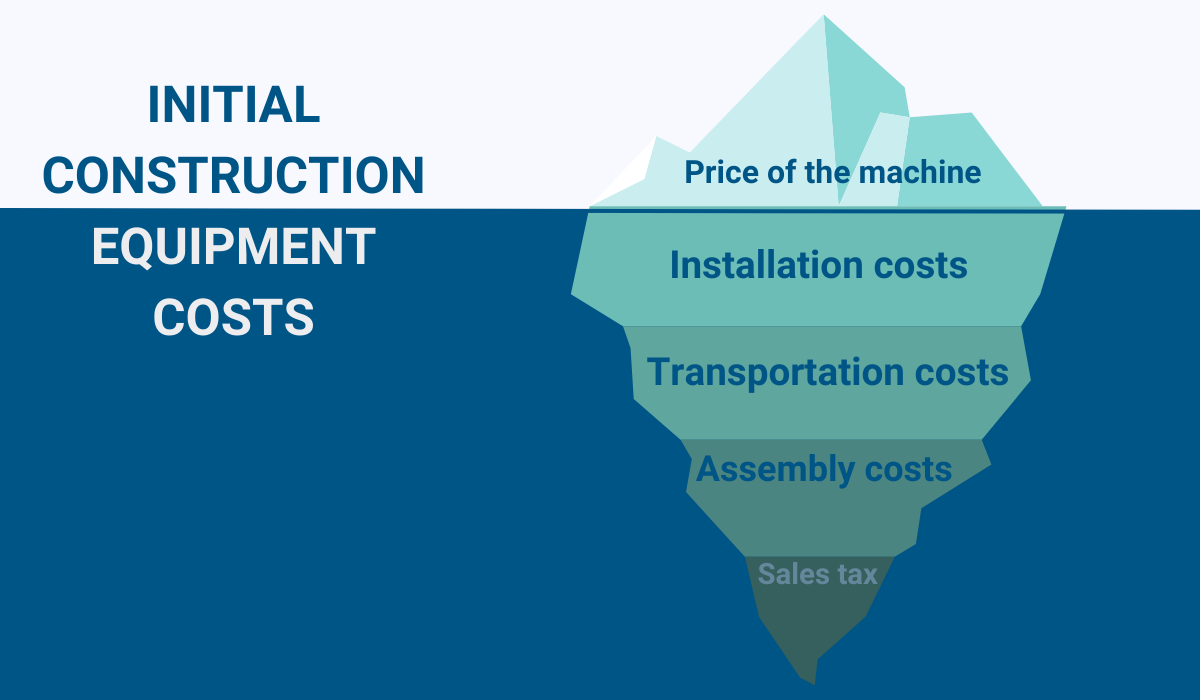
However, they are not so clear-cut.
Whether you choose to buy or rent, and whether you opt for new or used equipment, all influence the overall initial cost.
And let’s not forget the type, make, and model of the machine, either.
To illustrate, if you decide to buy a new excavator, it can set you back anywhere from $100,000 to $500,000, while a used one may be acquired at a discount of 25-50% off the original value, depending on the hours worked and logged.
All in all, remember that going after the lowest price isn’t always the best course of action.
Buying a used piece of equipment might be tempting because of its lower initial cost, but this won’t do you much good if the machine is on its last legs.
Prioritizing quality is paramount when investing in company assets.
After all, without them, timely project completion would be impossible.
Insurance Cost
After you’ve bought some new construction equipment, the responsible next step should be to get it insured.
Insurance acts as a financial safety net, covering potential losses stemming from unforeseen events like fire, theft, or accidents involving your valuable assets.
Contemplating such scenarios may be unpleasant, but it’s crucial to be prepared for the unexpected.
Senior Vice President at National Interstate Insurance Company, Chris Mikolay, agrees.
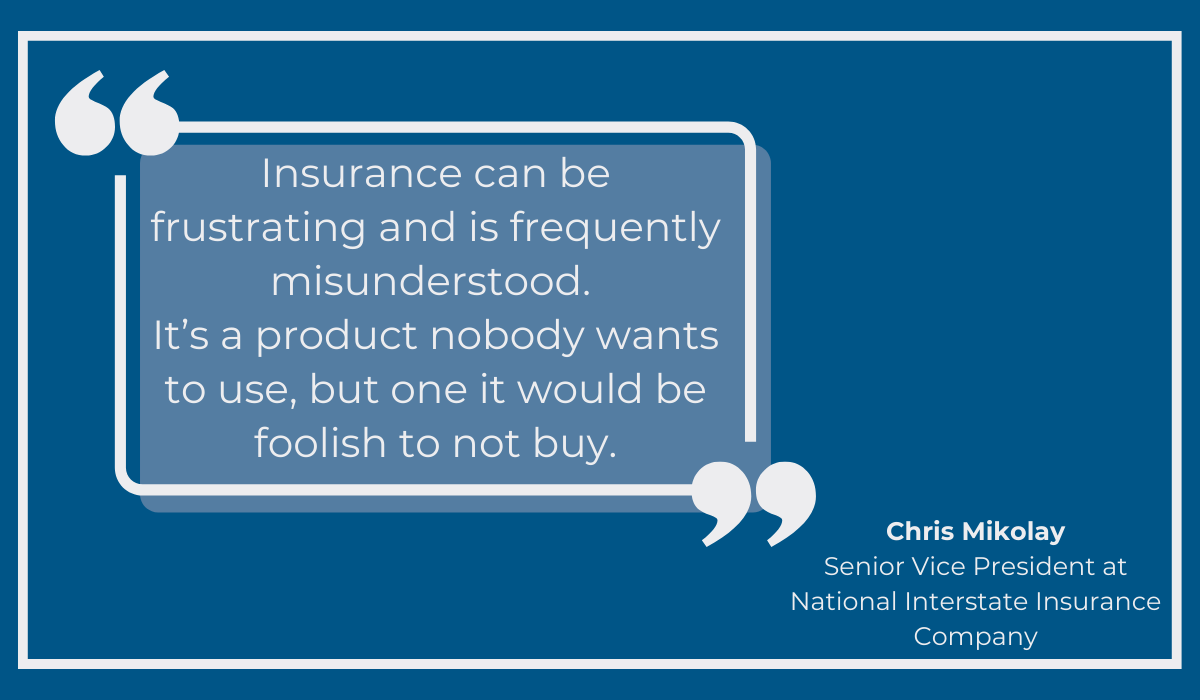
Skipping out on insurance would not be the wisest choice so make sure to take the time to shop around and talk with the agents until you find what works best for you.
It’ll pay off in the long run.
However, it’s also important to recognize the limitations of insurance.
While it does provide monetary compensation for repairs and replacement, it can’t physically retrieve a machine, which is a significant concern in cases of, for example, theft.
What about the ongoing projects that cannot continue without that stolen piece of equipment?
Project delays and consequent reputational damage, unfortunately, cannot be undone by insurance companies so consider looking into other additional means of asset protection.
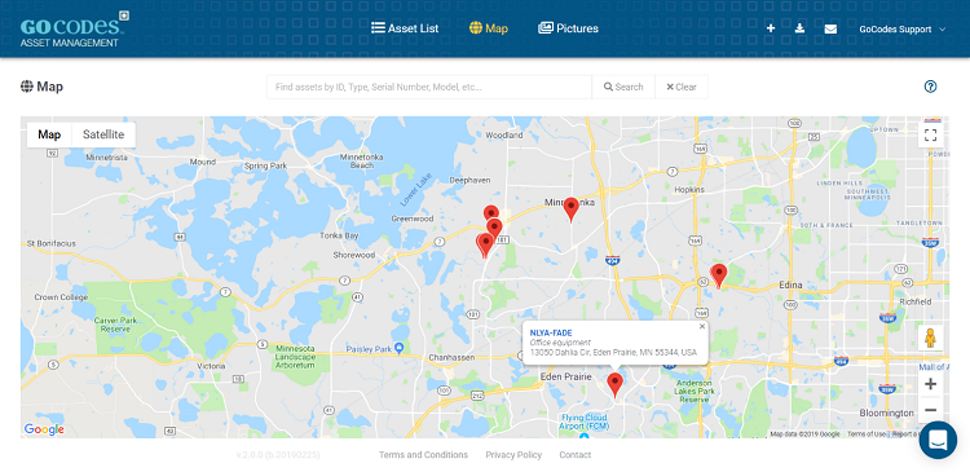
For instance, tagging heavy machinery with asset tags and using software to track its GPS locations is really effective in retrieving stolen equipment.
Not to mention that seeing the tag or label with your company name on it will indicate to the thieves that the machine is being monitored and protected, potentially deterring them from their endeavor.
This is certainly something insurance companies can’t do.
Equipment Depreciation
Over time, the monetary value of your assets will drop, no matter how well you take care of them.
This decrease in financial worth is due to either machinery wear and tear, age, or the continuous emergence of new, more technologically advanced models on the market.
Depreciation, therefore, signifies the amount of value equipment loses each year.
However, remember that, despite this inescapable depreciation, there is a silver lining after all—the ability to claim it as a legitimate business expense on taxes.
Let’s, therefore, discuss how to calculate the reduction in your assets’ value.
Calculating the annual depreciation rate involves a couple of key factors.
For starters, determine the initial cost of a machine. This entails all the elements we outlined in the first section.
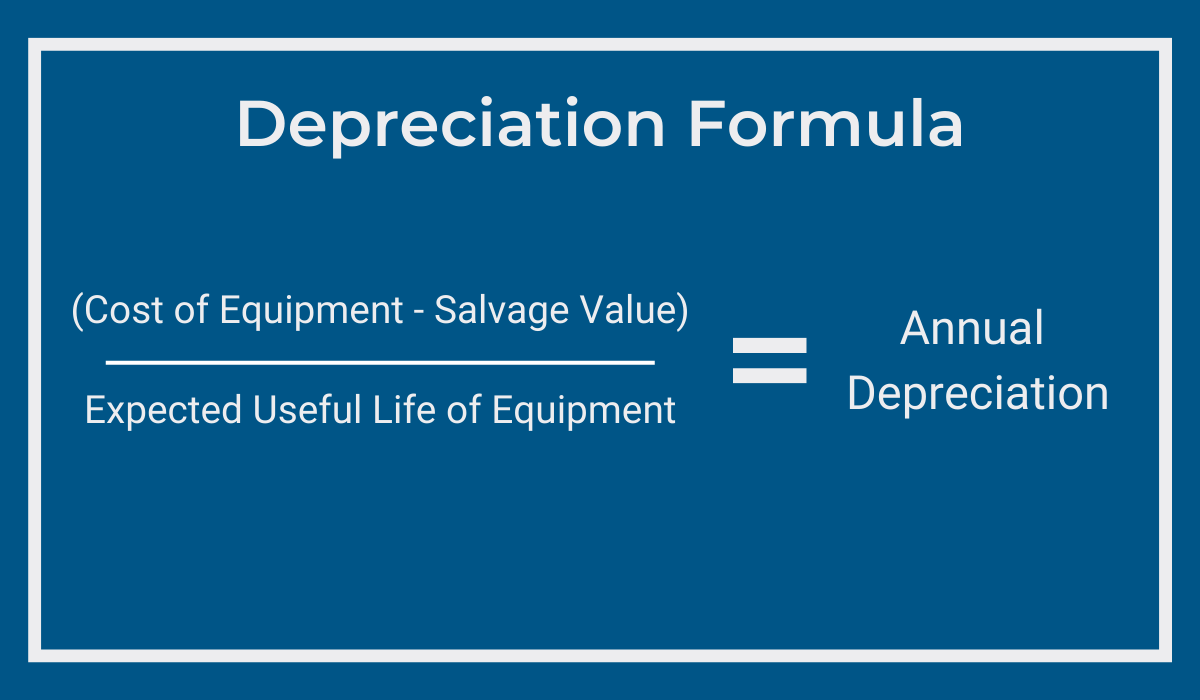
Then, the salvage value, which is the money you’d get for the asset if you were to sell it at the end of its useful life, needs to be subtracted from the initial cost.
Finally, divide this resulting figure by the expected equipment lifetime, i.e., how long you expect to use it for its original purpose until it depreciates fully, and you get your depreciation amount.
There are different depreciation strategies, such as for instance, straight-line depreciation or double declining balance depreciation, and choosing which one to adopt is best done in collaboration with your accounting team.
Keep in mind that, in most cases, it’s difficult, if not impossible, to alter the strategy later on.
Another good news is that different modern solutions that can streamline and simplify depreciation calculation are now widely available.
All these tools require from you is to input the above-mentioned data and they will promptly generate calculations for:
- The prior year’s depreciation
- The current year’s depreciation
- The total depreciation for all years
- The balance remaining to be depreciated
It doesn’t get any simpler or more efficient than that.
With such technology, mastering depreciation finally becomes a manageable task, accessible to anyone.
Taxes
In addition to the sales tax that’s applied during the purchase of an asset, there are some additional taxes associated with owning and operating construction equipment that may apply to you.
Let’s see what they are.
One such cost is the property tax, remitted to the state or central government and determined by both the machine’s financial worth and the tax rate, which varies from jurisdiction to jurisdiction.
Typically, the tax rate ranges from 2% to 5% of the asset’s book value in a given year and is assessed based on its age, condition, and current market value.
In certain jurisdictions, using heavy machinery may also incur the so-called use tax.
Just to illustrate, the city of Thornton mandates that contractors file an Equipment Declaration Form, obtain a permit, and pay the tax upon its issuing if they use and store their gear within the city limits.
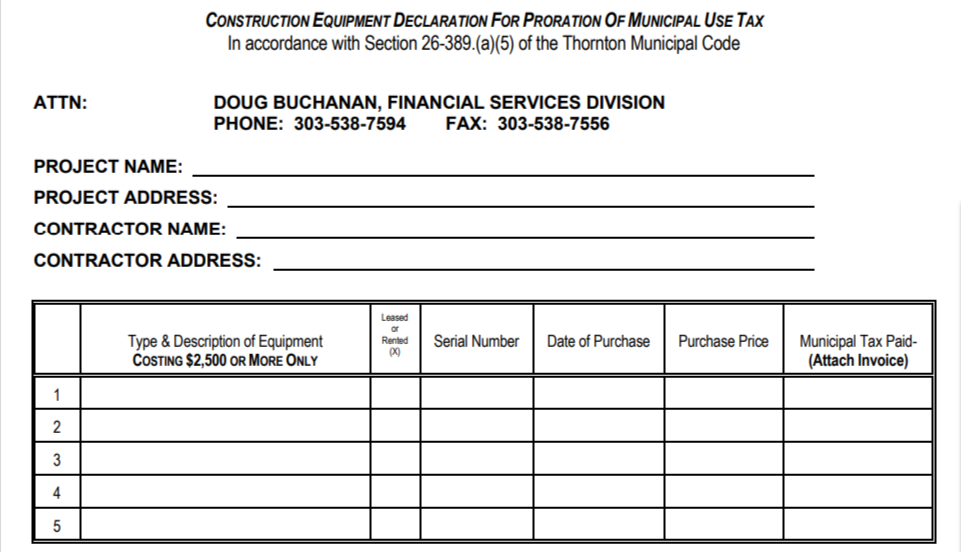
How much contractors have to pay to the city depends on the estimated value of the project and is applicable to all purchased, rented, or leased equipment with a minimum purchase price of $2,500.
Various other taxes should be taken into consideration, like fuel tax imposed on fuel purchases, registration fees when registering assets with the appropriate authorities, and specialty taxes levied on specific types of construction equipment, such as cranes, heavy machinery, or other specialized equipment.
Overall, it’s essential for you to be aware of the relevant tax requirements in your area to ensure compliance, but also to factor these costs into your budgeting and financial planning.
Consulting with tax professionals or accountants familiar with local regulations can help you navigate these complexities.
Storage Cost
Given the financial commitment involved in acquiring construction equipment, it’s only natural you’re going to want to protect your valuable assets, even (or especially) during periods of non-use.
Secure storage space is irreplaceable in this regard.
It defends your machines from the unpredictable forces of nature, as well as the ever-present threats of theft and vandalism.
As such, it’s well worth investing in.
Monthly expenditures for such spaces can range between $500 and $1,000, however, it’s important to note that this price doesn’t cover only the physical warehousing space but encompasses a spectrum of other elements, like wages for security personnel and other staff, utilities, or insurance.
What’s more, storage facility providers may offer incentives like discounts for extended rental durations or, on the other hand, impose additional charges for cleanup and maintenance.
The ultimate bill, therefore, will depend on a multitude of factors, including the type and size of the equipment, the geographical location, the duration of storage, and the quality and amenities of the facility.
Equipment Management Software Cost
On top of all the costs outlined so far, we see an increasing number of construction businesses investing in equipment management software.
The trend is driven by the efficiency, user-friendliness, and cost-effectiveness of these tools, which are proving to be indispensable for any company aiming to optimize resource allocation and utilization.
At GoCodes Asset Tracking, we prioritize making the most out of your construction equipment, as well as the ease of use—the idea that inspired us to develop our own asset management solution, comprising only two components: QR code labels and cloud-based software.
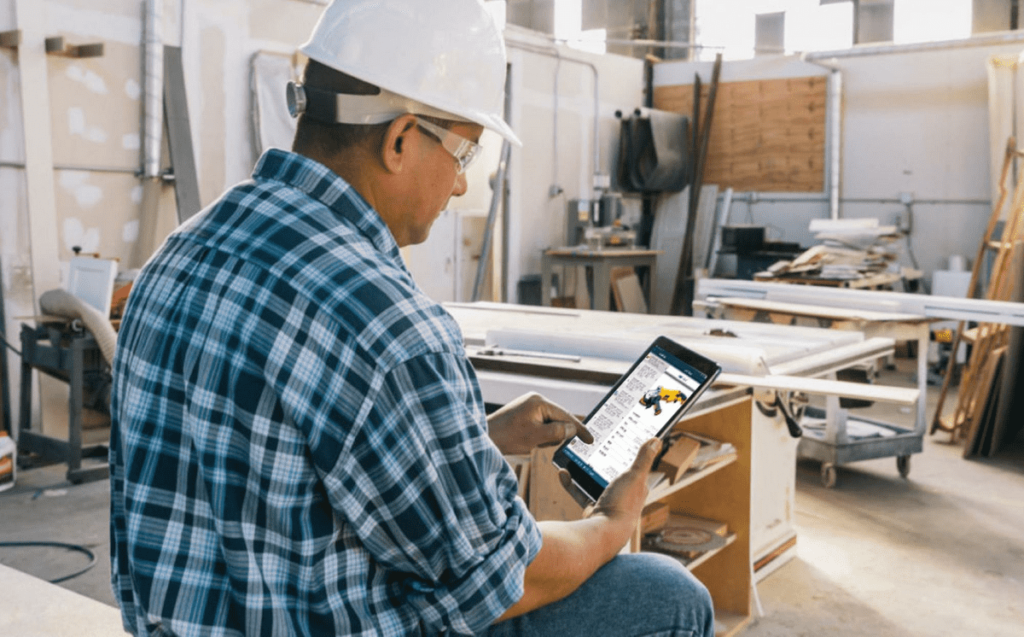
Here’s how it works: every time a worker scans the label to check an asset in or out, the location of the update is recorded, which means you get to monitor who’s using which machine at any given moment and where this is happening.
This significantly helps with preventing loss, theft, or even equipment hoarding. “No more missing tools” is GoCodes Asset Tracking’ motto, after all.
Moreover, the system provides you with a comprehensive, accurate, and up-to-date asset list with all the data you could ever need to effectively manage your machinery, such as maintenance logs, warranty information, equipment costs, and so much more.
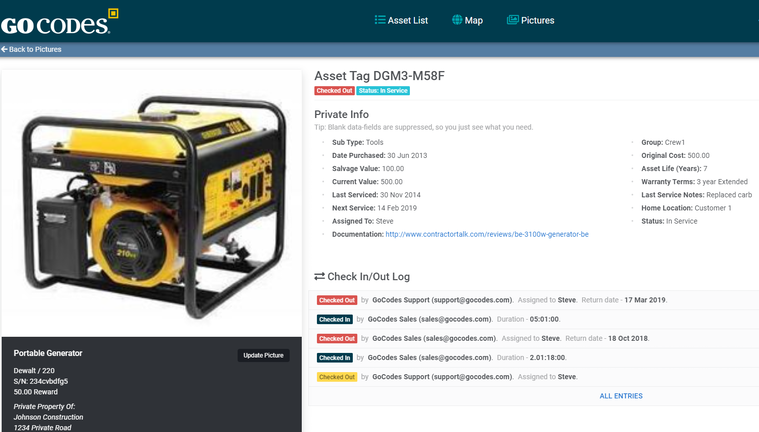
In essence, with GoCodes Asset Tracking, you and your team can make well-informed, data-based decisions regarding resource allocation, maintenance planning, and audits.
Returning to the subject of cost, we provide several different pricing plans based on service levels that can be easily upgraded at any time.
Before making this commitment, though, we encourage you to explore our system through a free trial, which will allow you to experience its features firsthand and assess whether or not GoCodes Asset Tracking fits your specific needs.
Conclusion
From purchasing a machine and choosing an insurance provider to tax obligations and storage considerations—every financial move plays a vital role in the construction equipment ownership landscape.
Only through meticulous planning across all these sectors can you guarantee your business’s sustained profitability.
Hopefully, this article shed light on some of the areas of equipment ownership that often go overlooked and empowered you to make better-informed choices in the future.