Just because your machinery is heavy and robust, it doesn’t mean it will last forever. Construction equipment requires continuous care to function optimally as long as possible.
While the average lifespan is different for various heavy machinery and tools, how the owner handles them makes a huge difference.
Everything from preventive maintenance and the frequency of cleaning to operator performance and use plays a part.
So if one of your goals is making the most out of the money you’ve invested in acquiring the right construction equipment, read our tips on how to prolong the useful life of your machines.
In this article...
Prevent Dirt Buildup
After every construction job, you’ll inevitably have to deal with dirt. Mud and debris aren’t just unpleasant to look at; they can also cause significant damage to your equipment over time.
Soot and dust can clog filters and vents, decreasing the machine’s overall performance, while materials like sand and rock increase the wear and tear on the undercarriage.
By properly cleaning your equipment, you ensure that these materials don’t build up, minimizing damage to critical parts of the equipment.
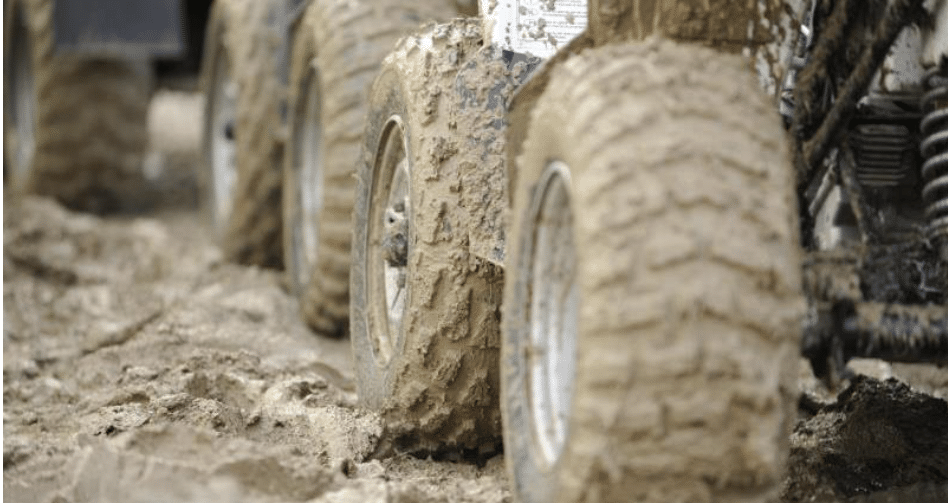
Another death trap for your machines is corrosion, but it’s not just the exposure to rain that causes it. Road salt, fertilizer, and deicers also cause problems if they’re not washed off immediately.
Finally, think about the message you’re sending to potential customers as they see your dirty trucks on the roads.
You want to be regarded as an organized, detail-oriented, and trustworthy service provider, but that’s not the message you’re sending with a dirty fleet.
Properly maintained, clean equipment makes a better first impression and improves your company’s image.
Now, we’ve established that cleaning your equipment is necessary. But is there a way to do it fast and effectively?
You can always invest in your own cleaning equipment that will consist of a dustless vacuum, a stiff brush (for removing rust), and a pressure washer. These tools will do a thorough job of keeping your equipment spotless.
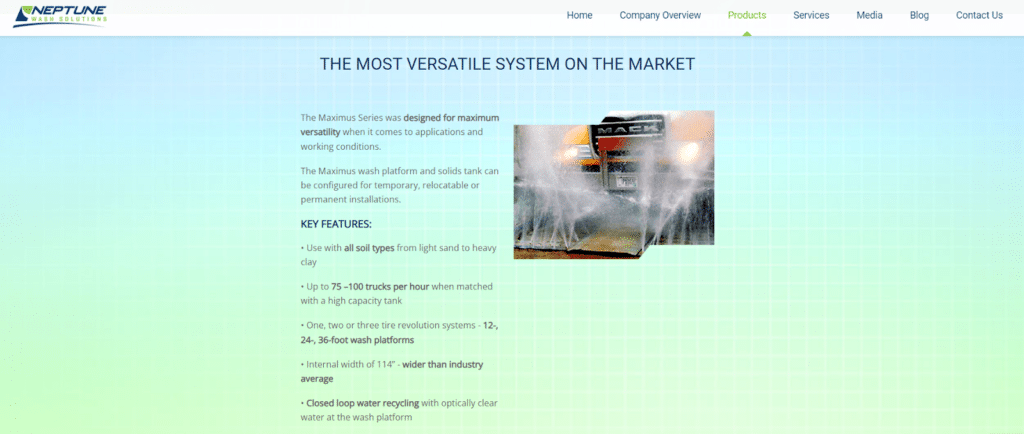
You could also invest in a wheel wash system that will take care of your equipment in a matter of minutes.
For example, the wheel wash system used by Neptune Automated Wheel Wash Systems from Hot Springs, Arizona cleans all soil types and can handle up to 100 trucks in an hour.
It has also saved some of their customers’ time on regular washing cycles.
Before installing their system, one of those customers spent an hour washing truck tires by hand every day, but that was reduced to 15 minutes when they started relying on Neptune’s wheel wash system.
In the end, what you need to remember is that clean equipment lasts longer and performs better. Making sure that your equipment is well-kept is the easiest way to protect your assets and keep them in top working condition.
Perform Regular Parts Lubrication
‘’Running like a well-oiled machine’’ is more than just a saying. Properly lubricated equipment works better and lasts longer because it’s designed to move joints on a layer of grease.
Basically, lubricants are vital for your heavy equipment. These machines operate under challenging conditions, from extreme weather and temperatures to muddy job sites.
So, it’s necessary to protect them from excessive friction to keep them working smoothly.
Maintenance experts recommend that you grease your equipment daily. Jeff Payne at CAT advises that you clean zerks with a rag and remove any dirt before you pump in new grease.
Then you put the grease gun on the zerk and give from four to five pumps or as soon as you see the grease get out.
According to Payne, the most common mistake operators make is to over-grease the equipment. More grease will only allow more dust to collect on joints, so you’ll have to clean it more frequently.
Other things you can do to ensure your machines are lubricated enough is to:
- Check lubricant levels frequently.
- Use prescribed lubricants by the equipment manufacturer.
- Look for oil leaks and grease buildup.
Now, choosing the right lubricants is just as vital as regularly greasing your equipment. An all-purpose grease isn’t the optimal solution, so you should carefully look at different types and brands on the market.
Here are some things to keep in mind when looking for the right grease:
Different Seasons | In the summer, it’s recommended to use thicker grease as it tends to thin out under high temperatures. In the winter, grease with lower viscosity performs better. |
Extreme Pressure | Equipment that works under heavy stress will benefit from grease with molybdenum disulfide, commonly known as ‘’moly’’. This additive can get into the smallest machine pins and bushings. |
Different Parts | Some components of your machines get heated while others stay cool. For parts that operate at high temperatures, use more viscous grease. For others, use synthetic grease. |
Wet Conditions | If your equipment frequently works in wet conditions, try using marine grease. These lubricants have lithium complex thickeners that protect from salt and fresh water and help prevent rust. |
The bottom line is that greasing should be one of the main tasks in your daily maintenance routine. Some joints might have different lubrication intervals, but you mustn’t skip the process.
Otherwise, you can damage your machines and decrease their expected lifespan.
Train the Operators Well to Prevent User-Made Errors
Equipment misuse is one of the most significant reasons machines don’t last as long as they should.
When operators run the machines in ways they’re not supposed to, they can put extra strain on the equipment, resulting in more frequent breakdowns and the need for parts replacement.
Did you know that you can expand your motor grader’s lifespan if you switch to the left lead during grading along curbs?
Only properly trained employees will know this. So as the equipment gets upgraded, your employees also need to be updated on how to operate them.
Motor graders are easy to keep in good condition, but it’s up to your employees to ensure they work in the most appropriate way possible.
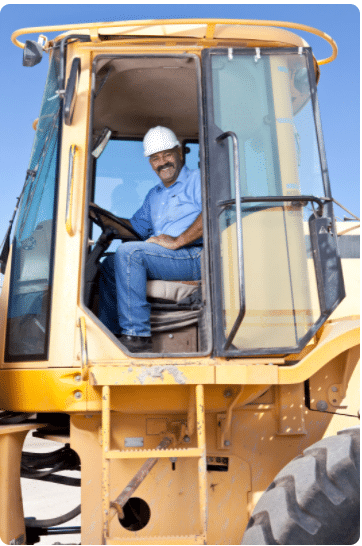
It goes without saying that construction equipment needs to be handled professionally and carefully to get the most out of it while prolonging its lifespan.
But sometimes operators make terrible mistakes in a rush to get the job done, or they’re simply not appropriately trained.
For example, a typical wheel loader’s lifespan is about ten years (7 000 to 12 000 hours). But excessive breaking, taking ramps, or short duty cycles can significantly reduce its lifespan.
Another typical mistake is neglecting to let the engine idle for a few minutes before shutting down the machine. This can result in a turbocharger failure which costs between $1000 to $5000 to repair.
Also, many operators often assume that operating in the highest work mode will give them more productivity. But they can achieve the same results when they optimize to lower work modes.
In fact, you can save thousands of dollars in fuel costs if you instruct the operators to switch to lower work modes.
So, the simple solution is to provide ongoing training to your operators so they can understand the equipment’s limitations and efficiently handle different construction tasks.
Now, while hands-on and one-on-one training is preferable, we’ve learned in 2020 that sometimes that is not an option.
Training programs can come in different formats, and one of them can be online education, with comprehensive videos like this one.
With videos like these, you can provide some basic instructions, supplemented with real-life experience where operators will work with real machines (once it’s safe to do so).
Operators have to know how to use different controls and implement safety precautions to help you expand the lifespan of your equipment.
To sum up, poorly trained employees are a hazard to themselves and everyone around them.
So, if you want to avoid damaging your equipment and attracting lawsuits for unsafe practices, ensure your equipment operators are adequately trained.
Don’t Overwork the Machinery
Even though your heavy machines are very durable, it doesn’t mean you should always push them to their limit.
This is fairly easy to forget when you’re rushing to complete tasks on time to meet project deadlines.
But remember that constant overwork will increase the wear and tear of your equipment, resulting in more downtime due to mechanical issues. Those will inevitably delay project completion.
Carefully consider how you’re using your machines. If you’re operating an excavator for a task that might be more suitable for a motor grader, you might eventually break your machine or significantly reduce its longevity.
The first step towards preventing the improper use of your machines is to read the owner’s manual for performance specifications. They will outline weight limits and provide instructions on operating the machine efficiently.
For example, this owner’s manual has specific instructions for a hydraulic excavator.
Among other things, you can find the maximum recommended speed (3.5 mph), pressure, and weight capacity for different attachments and components of the excavator.
You can also find the working ranges for this particular model. So, its maximum digging depth is 21’9’’, maximum cutting height is 30’7’’, and maximum loading height is 21’7’’ (these ranges are only applicable if you use a reach boom of 18’8’’).
So, if you want to achieve your goals, it’s more sensible to prevent the overuse of your equipment by instructing your workers to respect the equipment’s limits and take timely breaks to avoid overheating.
In the end, preventing overwork is a simple step towards keeping equipment from breaking down.
Develop a Maintenance Schedule
A regular maintenance schedule is indispensable for prolonging the lifespan of your equipment.
It ensures that you perform the tasks to keep your equipment in good shape in a timely manner, and prevent any significant problems in the future.
Basically, as long as you keep an eye on your equipment, you’ll have a well-performing machine that might serve you longer than you expect.
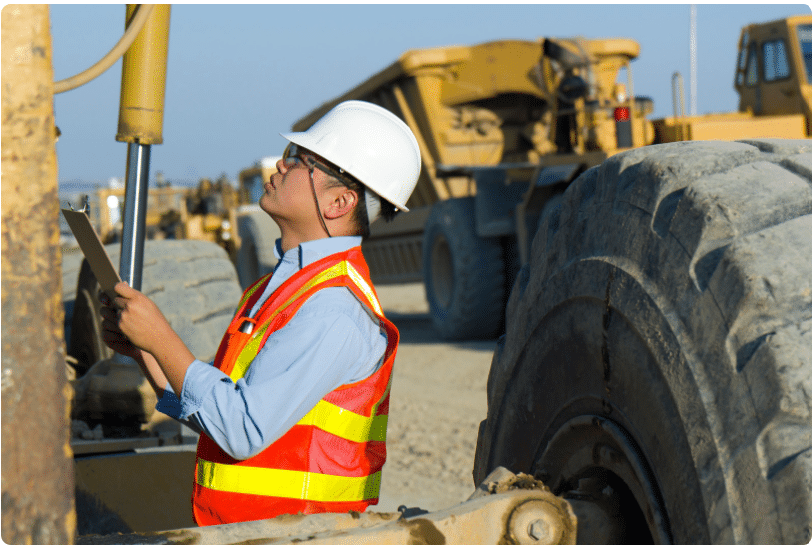
The first step includes having a detailed plan that will cover daily visual inspections and regular check-ups by the maintenance experts. You need to decide when these inspections will take place and how often.
Remember that different equipment will have unique needs, so consult the manual of each piece of equipment to get the right maintenance recommendations.
Next, train your operators to properly conduct visual inspections of the equipment. Give them a checklist as a reference, so they don’t miss a vital step and overlook a potential issue.
For example, they should check the oil and fluid levels, the condition of tires and tracks, and make sure that all lights and indicators are working.
Other issues they ought to report are worn belts, the engine taking longer to start, or even slower hydraulic responses.
On top of that, you also need an in-depth analysis that only an expert mechanic can give you. They will examine any weak points in your machines and repair them before they wear out and break.
But an essential aspect of regular maintenance is keeping accurate records for every piece of equipment.
Maintenance can become complicated if you have a lot of equipment, so don’t rely on spreadsheets but use digital solutions instead.
These online solutions will keep all the information about your equipment easily accessible and enable you to set maintenance schedules in a convenient way.
You can store individual records of the time, date, technical specifications, and detailed explanation of the problems that the operators and the maintenance team encountered.
Additionally, your maintenance team can easily access this central source of information through their mobile or desktop apps and decide whether equipment should be serviced more or less frequently.
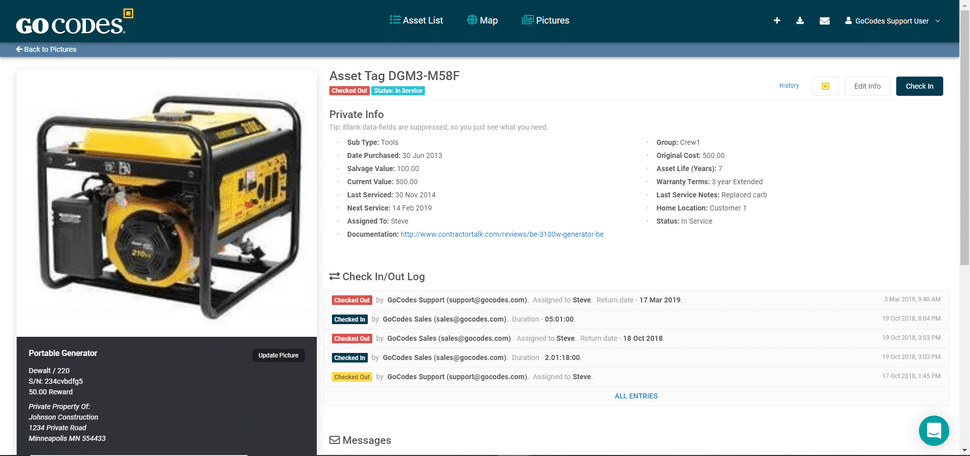
GoCodes can help you schedule preventive maintenance and extend the lifespan of your equipment.
In the end, a regular maintenance schedule is one of the crucial factors if you want to be able to use your equipment for years to come.
Conclusion
Machines and construction tools are essential investments for a construction company. This equipment allows such companies to continue their business operations successfully, so it makes sense to want to get the most out of them.
By applying our tips, you’ll ensure a long lifespan and enhanced performance for your equipment.