So, you’ve opted for buying reliable second-hand equipment instead of allocating your hard-earned resources for purchasing fresh off the conveyor belt.
After extensive research into the used equipment market, you find a respectable supplier who offers the make and model of a machine you’re interested in. But, how can you be sure that you’re making a wise investment?
Don’t worry! We’re here to help you determine what to check for before signing that contract.
When deciding whether to buy a used piece of equipment, you need to be as informed as possible. Otherwise, you risk wasting your money on machinery that’s bound to fail and leave you without a solution in the middle of a project.
Let’s get into it!
In this article...
Inspect Equipment for Visible Signs of Wear or Damage
When buying used machinery, you should first look for any evidence of wear and tear.
Take the time to do this, and you’ll be sure you’re buying something the previous owner looked after well. On the other hand, if you notice any visible damage to the equipment, the item might not be the right choice for you.
Wade Porter, an ADSD motor grader application specialist, explains why the visual inspection is so important:
“Overall cleanliness of the machine will give a good indication of how well it was kept up. Structural damage, gouges, etc., can indicate the grader was used in heavy applications (e.g., rock), which will reduce its life expectancy before major repair and/or overhaul.”
And he is right—you have to understand how well someone maintained the equipment before you. This information can make or break your deal as you do not want machinery to last a lot less than expected.
When you notice that the equipment is slowly degrading because of wear and tear, you can expect to spend more cash on replacement parts shortly. Avoid this by opting for a different piece of machinery instead.
Here’s what you should inspect to determine whether the equipment’s in good condition:
Part | What to inspect? |
Engine | Always check if the engine is dirty or if there are any loose parts, as none of those should be present in a well-maintained machine. |
Tires | The tires have to be in good condition and functional, so check for punctures and tread wear (the latter points to an alignment issue). |
Brakes | Damaged brakes pose a considerable safety threat. |
Fluids | Low fluid levels and impurities are clear signs of the previous owner’s neglect. |
Undercarriage | The repair of the undercarriage is very costly, so ensure that it isn’t damaged prior to purchase. |
Welding | Visible traces of welding on the machine are a sign that the owner had to replace something, i.e., that the equipment has experienced considerable damage. |
Exhaust fumes | You shouldn’t be able to see the exhaust fumes at all; if they’re white, black, or blue, there are likely problems with fuel burning. |
If you notice any of the issues we’ve just listed, purchasing the equipment is not a good idea.
In addition to all of these, you should be on the lookout for any leaks. We’ll explain why this is important in the following section.
Look For Any Noticeable Leaks
Clearly, if the machinery you’re inspecting is leaking, it’s not a good sign.
Proper-functioning equipment won’t leak any fluids; otherwise, you might be racking up costs sooner than you know it.
For example, if you lose a drop of oil every 20 seconds, you end up paying $168 a year for replacement oil alone.
While this doesn’t seem like much, it’s still money you didn’t have to lose—and that’s only for a single leak point. If you have six, you’re already up to $1,000 worth of wasted oil yearly.
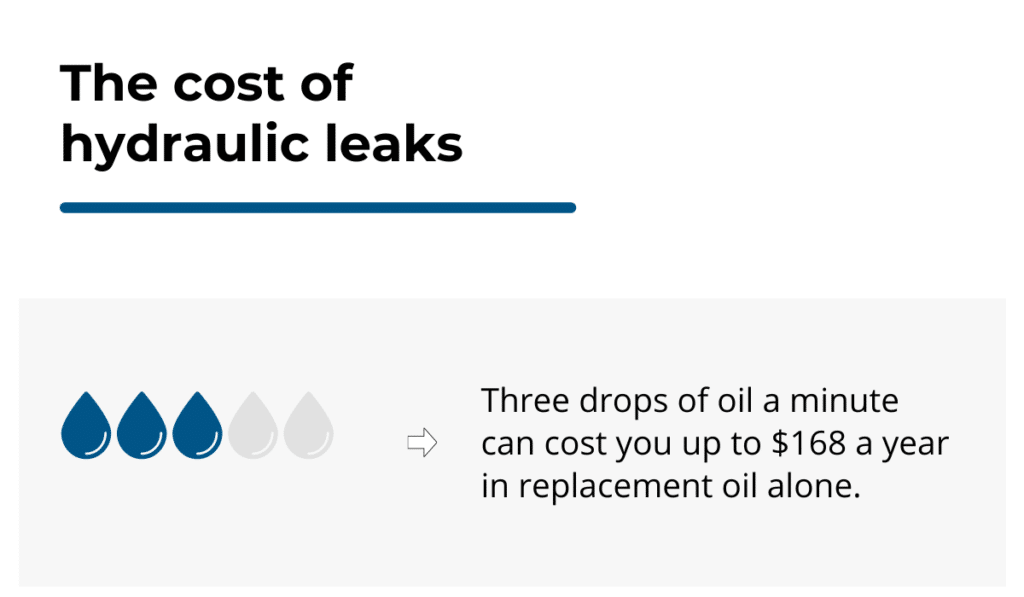
You can calculate how much your leaking equipment will cost you here.
If seeing those numbers didn’t deter you from buying machinery that’s leaking fluids, maybe the fact that the Occupational Safety and Health Administration (OSHA) can fine you for such a malfunction will.
In 2015, for example, a company was fined $6,600 for five violations, including a hydraulic liquid leak and subsequent accumulation of it on the cylinder.
As if all that wasn’t enough, know that leaks also affect the equipment’s efficiency, which means you won’t get what you’re expecting out of your new purchase.
Up to 80% of machinery and component stoppage is caused by fluid contamination, which often happens due to leaks.
So, why purchase such equipment in the first place?
When trying to figure out whether the equipment’s leaking, start by checking the ground under it to see if there were any leaks while the machinery wasn’t operating. Do the same after running the equipment.
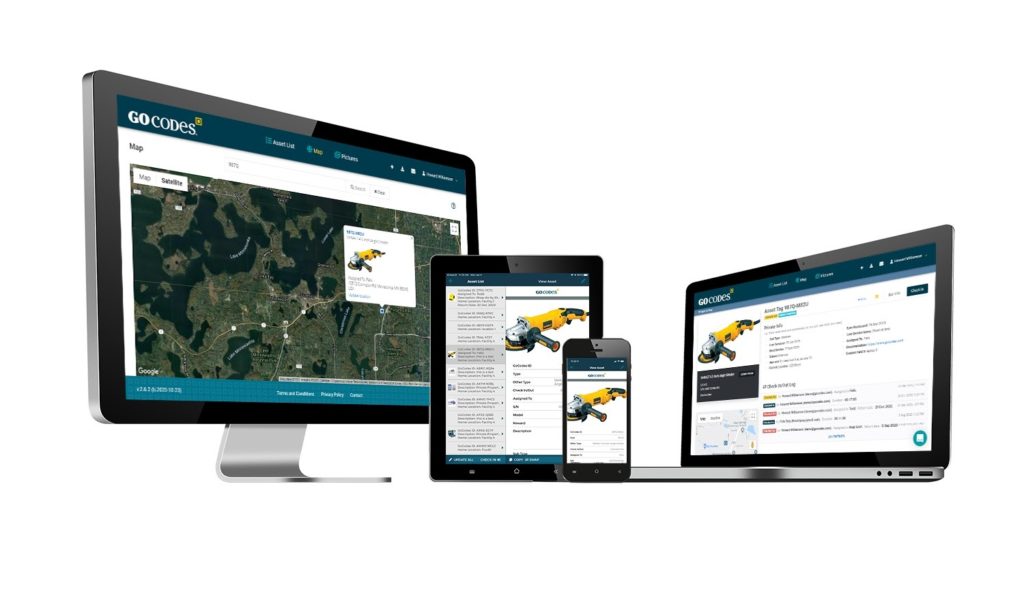
We make tool and equipment tracking easy! Try GoCodes for free
Next, check all hoses, arms, and cylinders to ensure there’s no oil or any kind of equipment liquid gathering there.
Of course, you should also inspect the fluids themselves to see whether they’re leaking into each other.
For example, if you find oil in your coolant, you should think twice before making that purchase as there’s something wrong with the engine—which is the next thing you should inspect in detail.
Make Sure the Engine Starts
Before you purchase used machinery, you have to test its engine.
Otherwise, you might be buying something that won’t even start, which means you’re simply wasting money.
The engine runs the equipment, so you should ensure it’s in optimal condition. Merely checking it by sight, the way we described earlier, isn’t enough. You have to test it thoroughly.
Dennis Howard, the vice president of Fleet and Remarketing for RDO Equipment Co., says it’s best to “run it hard enough to know what you’re getting.”
Of course, turning the machine on and running it for a couple of minutes won’t tell you everything you need to know about the engine.
So, you should try to run it for as long as possible to see if everything goes well. If you experience sudden stalls, strange noises, or any other issues with the engine while you’re testing it, the machine probably isn’t a wise investment.
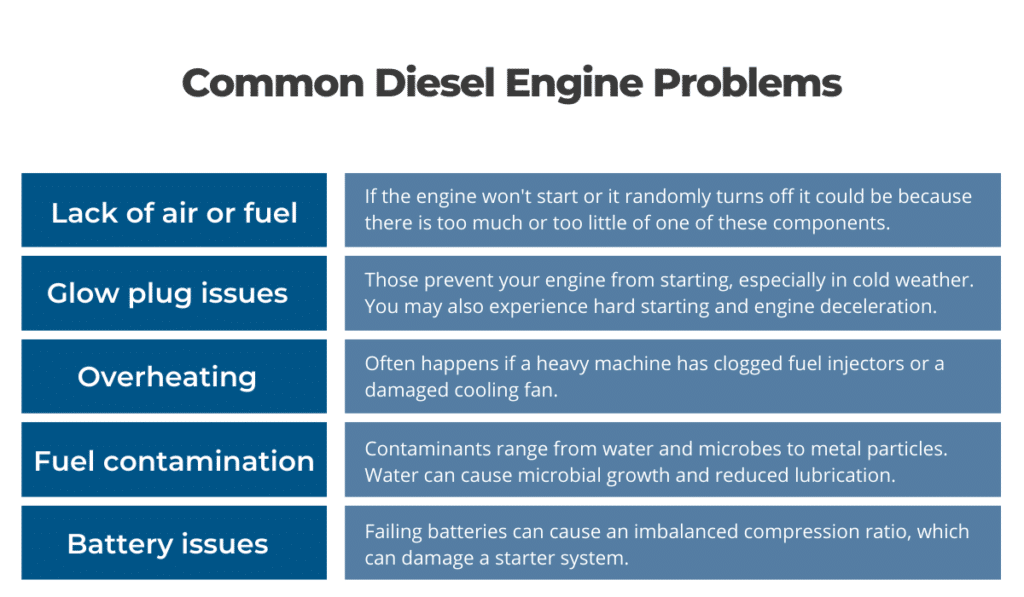
After all, remember that you’ll have to invest in continuous maintenance and repairs, which will happen a lot more often in equipment with faulty engines. Is that something you can afford?
While testing, you should also try every speed the machine has. Otherwise, your equipment operator might experience issues in the field with your new machine, which will slow your entire project down.
Also, test every movement the machinery is supposed to make. If the machinery’s range of motion is limited when you first buy it, it can only go downhill from there, and that’s not promising.
Finally, if you have any doubts or uncertainties regarding what the machine has to offer, you should ask the seller. Your questions can serve as a good test of their knowledge.
A seller who doesn’t know their equipment well probably didn’t spend much time working with it or maintaining it.
Compare the Equipment’s Condition to Records
Testing the machine is a key aspect of determining whether to purchase it, but so are its records. The records provide valuable insight into the condition and worth of the machinery.
After all, an owner who invests in their equipment will keep and have access to all documentation related to the machinery, and continuously invest in its upkeep, which the aforementioned records can prove.
Besides, you can tell a lot about the equipment by looking into its records, and find out if its history is more complicated than what meets the eye.
Howard also shared his company’s experience when looking for used machinery to buy:
“We have seen tractors that look really nice and then we’ve looked into the history and find they have been underwater, totaled or rebuilt.”
Those are all issues that could cost you a lot in the long run if you decide to purchase such equipment. A machine that has suffered anything mentioned by Mr. Howard simply doesn’t function as well as it had before, and its condition deteriorates faster.
On top of that, by checking equipment records, you can find out more about the original owner of the machinery, which is vital. Don’t forget that there’s always a chance that the machine has been stolen.
Thieves get their hands on construction machinery worth anywhere between $300 million and $1 billion every year.
Since less than a quarter of all stolen goods are recovered, you have to keep an eye out for any signs of wrongdoing when purchasing used equipment. Therefore, always ask to look at the records to see if the seller can prove ownership.
So, ask to see equipment records to see where the machinery’s been and what kind of consequences it suffered as a result.
Review Inspection and Maintenance Reports
Does the owner you’re buying from record and keep maintenance reports? If not, you cannot be sure that the seller has serviced the equipment at all, let alone did a good job.
Companies that care about their equipment will most likely use a software solution that helps them stay on track with their maintenance process.
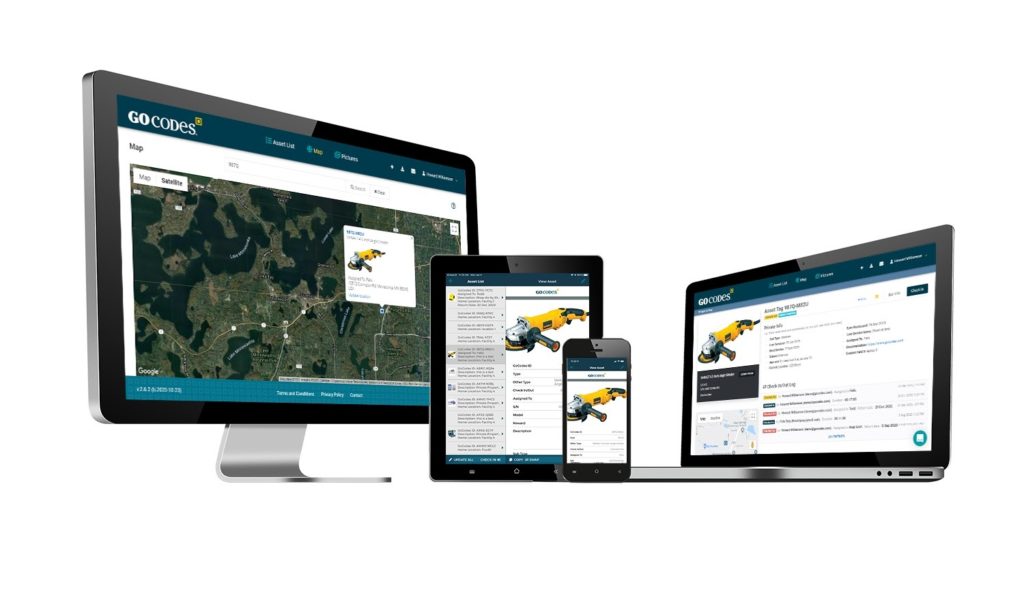
The said process includes past maintenance records, current maintenance schedules, and planning future service sessions.
So, when deciding whether you can rely on the used equipment of your choice, ask about its maintenance. A seller who has invested in their machinery should know how often it needs servicing.
If the owner didn’t practice preventive service, the type of maintenance that relies on regularly inspecting a machine to detect any potential problems with it, the equipment is not in good condition.
And if an issue does occur, the equipment will only be available for further use after your service team fixes it.
Maintenance records also indicate how often the owner changes the equipment’s fluids. If those aren’t changed regularly, the machine experiences more wear and tear than expected and is generally in worse condition.
Even if the fluid levels are correct when you inspect the equipment, the service logs will show whether that has always been the case.
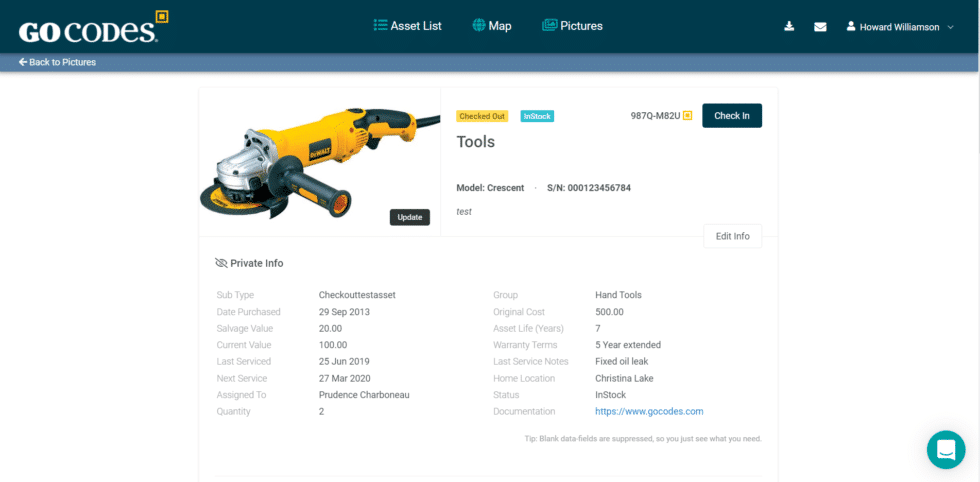
In the GoCodes’ asset view, you can see that the last service note was a fixed oil leak.
A quick look at the maintenance records will also let you understand how dependable the machinery is. If it often malfunctions and has to be put out of service, will you really get the most out of your investment?
After all, an hour of unexpected downtime costs $260,000 on average, which will surely make you think twice about buying a piece of equipment that didn’t get regular service.
Therefore, you should always ask to see the maintenance records before making a final decision on purchasing used equipment.
Conclusion
While buying used machinery can be challenging, there are ways to make the process easier for yourself.
Start by understanding that you have to know what the machine has been through before signing off on the purchase.
What this means is that you have to inspect the machine’s exterior and interior, as well as go through the equipment’s records and maintenance reports to determine if you can rely on the machine to do its job.
Only then will you be able to judge whether purchasing it would make a wise investment.
We hope that the article will help make the process of buying used equipment easier!