As construction company owners and managers know, efficiently managing fixed assets like heavy machinery, vehicles, equipment, tools, and facilities can be challenging, particularly when the company is engaged in several projects at once.
Since construction is a complex endeavor and decision-makers have a lot on their mind, it’s not surprising that many companies make asset management mistakes which, in turn, hurt their productivity and profitability.
In this article, we’ll cover six frequent mistakes in fixed asset management and provide tips on how to avoid them.
In this article...
Lack of Regular Asset Audits
Asset audits involve a thorough examination and verification of a construction company’s fixed assets to ensure that its records reflect reality, i.e., the actual status of these assets.
As such, regular audits contribute to compliance with financial reporting standards, more effective asset management, and increased efficiency of construction operations.
For example, during an audit, the company might find that certain equipment or tools are missing (lost or stolen) or that their condition and value have changed due to wear and tear, breakdowns, or technological obsolescence.
This enables the company to reconcile its asset records, ensuring they accurately mirror the real-life status of its fixed assets.
Conversely, neglecting this critical practice can result in the following consequences:
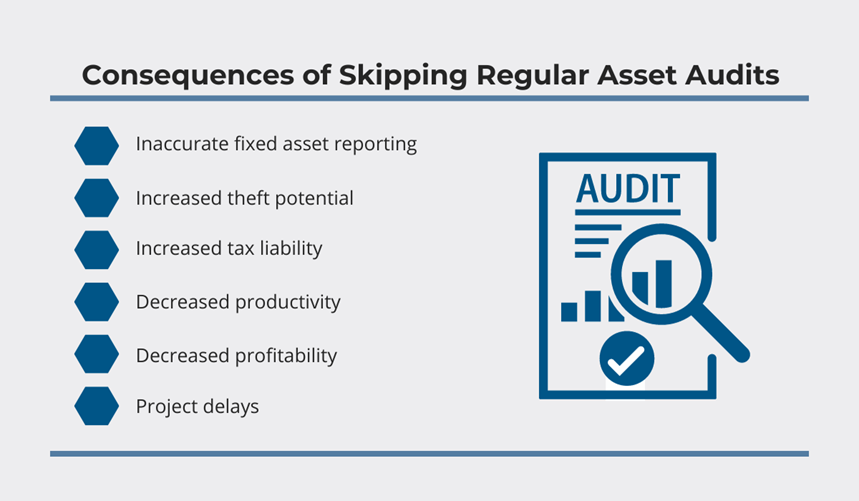
For instance, discrepancies between recorded information and actual asset status can lead to imprecise fixed asset reporting, with negative impacts on the accuracy of the company’s financial statements.
Moreover, a lack of regular audits may cause miscalculations in asset depreciation and valuation (as discussed later), potentially resulting in higher tax liabilities.
Likewise, if assets are neither tracked nor audited, this may create an environment where there’s an increased potential for theft.
So, what can your company do to prevent these consequences and streamline its asset audits?
The first step is to establish a regular audit schedule that will ensure audits are conducted at appropriate intervals (most often annually, but larger companies may opt to do them semi-annually or quarterly).
Also, your audit processes should involve multiple stakeholders (managers, accountants, maintenance staff) as this ensures a comprehensive examination of asset records and promotes accountability.
By doing so, you can streamline regular audits, enhance the accuracy of your asset records, and mitigate the potential consequences associated with neglecting this vital aspect of fixed asset management.
Failing to Track Your Assets
Not tracking where your equipment and tools are and who is using them—or relying on manual, spreadsheet-based methods to do so—is another common error still made by many construction companies.
For instance, without a centralized asset tracking system, workers spend more time locating equipment and tools they need and establishing their availability, which reduces overall productivity.
Similarly, if an asset is misplaced on the construction site, fixed asset spreadsheets will provide no clue as to where that asset was left, forcing workers to lose time looking for it.
In fact, studies show that each worker spends about 38 working hours a year just on finding tools.
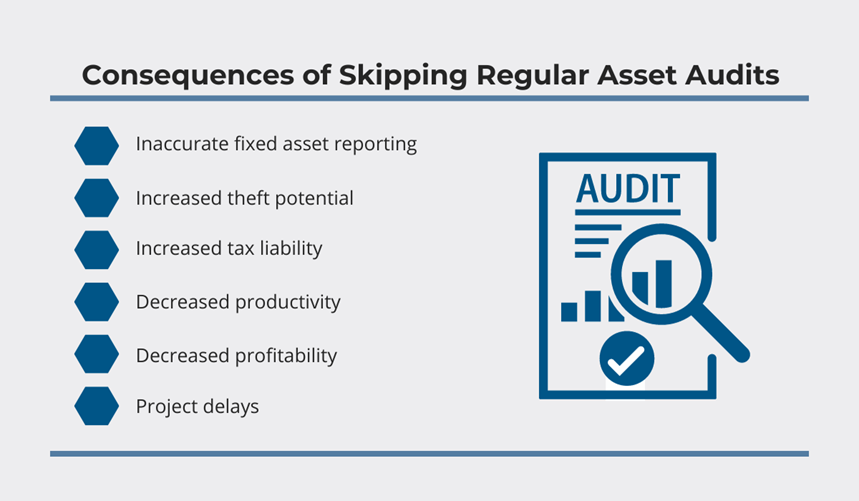
When combined with the time workers spend on finding things like project documentation, construction materials, or spare parts, all this can add up to 90 minutes a day of lost time per employee.
Expectedly, another major consequence of not tracking asset users and locations is a higher risk of theft, both internal and external.
In light of this, let’s see how contractors can utilize asset tracking solutions to save their workers time, increase their accountability, and minimize asset loss and theft.
For example, active GPS trackers attached to heavy equipment and vehicles provide real-time location updates globally while remote asset detection methods like RFID trackers and Bluetooth beacons do so within a limited area.
However, all these location-tracking methods need to be integrated with user identification solutions to ensure that asset users are also registered.
That’s why most of them are combined with the most affordable and simplest user-tracking method—QR codes.
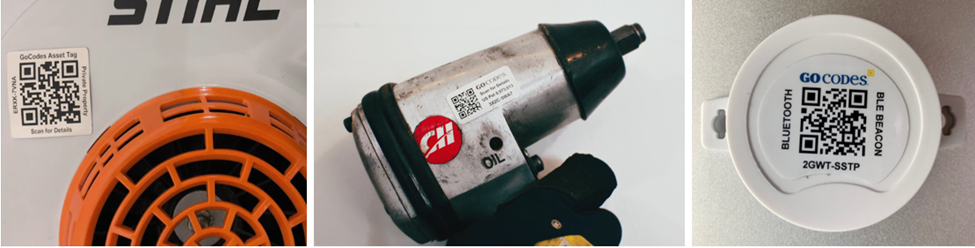
For example, when a worker checks out tools or equipment from the toolroom, they can simply scan the QR code with their smartphone or tablet, and the tracking software will record them as a user.
The same procedure is repeated when they check the assets back in after their shift.
That way, you not only know who is currently responsible for your assets but can also access the history of all previous users.
What’s more, when these QR code labels are scanned, the tracking app (installed on company-owned or workers’ smartphones or tablets) will automatically capture the scanned asset’s GPS location.
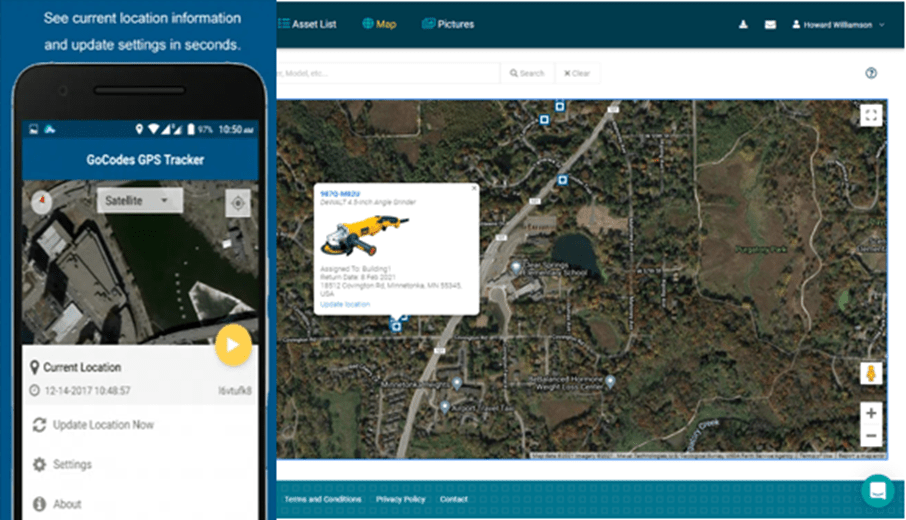
This scan-based, passive GPS tracking feature is ideal for quickly finding where needed or misplaced assets are and can also help in asset theft investigations.
Our asset tracking solution, GoCodes, is a great example of how a single system consisting of cloud-based software, QR code tags, and an in-app scanner can be used to automatically track both asset users and locations.
In summary, the described consequences of not tracking your assets can be avoided by using automated asset tracking solutions, which can be affordable, easily implemented, and simple to use even by less tech-savvy workers.
Failing to Implement Preventive Maintenance
When heavy machinery, equipment, vehicles, and tools are not proactively maintained, the risk of unexpected breakdowns increases, resulting in unplanned downtime and project delays.
Additionally, the useful life of assets may be significantly shortened, leading to premature replacements and increased capital expenditures.
To mitigate these challenges, construction companies can leverage fixed asset management software to streamline their preventive maintenance efforts.
Such solutions enable managers to schedule routine maintenance tasks, maintain a comprehensive service and repair log, and set up automated reminders for upcoming maintenance.
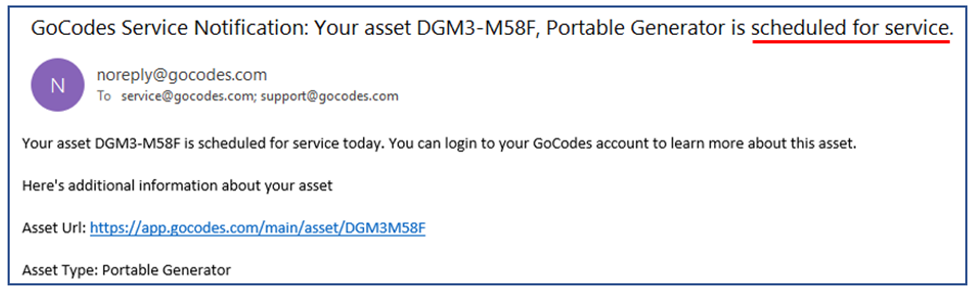
By utilizing asset management software, companies can shift from reactive to proactive maintenance, and generate the following benefits:
- improved equipment efficiency,
- fewer emergency work orders,
- decreased unplanned downtime,
- prolonged equipment lifespan,
- prevention of workplace safety incidents, and
- more cost savings.
In terms of expenditure, it’s worth noting that, according to MacAllister Equipment, companies that apply a preventive maintenance program see their equipment repair costs drop by 25% on average.
Given all these advantages, a proactive maintenance strategy becomes a crucial component of efficient fixed asset management.
To recap, failing to establish and implement a preventive maintenance plan can have severe consequences on a construction company’s efficiency and profitability.
Conversely, utilizing asset management software to schedule and track maintenance activities, assign service tasks, and ensure service technicians are automatically notified of upcoming service enables contractors to prevent such consequences from becoming a reality.
Neglecting to Account for Depreciation
Failing to properly calculate and report depreciation can result in misrepresentation of the actual value of fixed assets in the construction company’s financial statements.
This, in turn, may result in inaccurate financial reports and incorrectly calculated tax liabilities, potentially leading to financial penalties and audits imposed by the Internal Revenue Service (IRS) and other regulatory bodies.
Likewise, miscalculating depreciation adjustments can lead to bad strategic decision-making by the construction company, such as when it’s more economically sound to replace or repair a piece of equipment.
So, what is meant by fixed asset depreciation?
Here’s the definition by Appvizer:
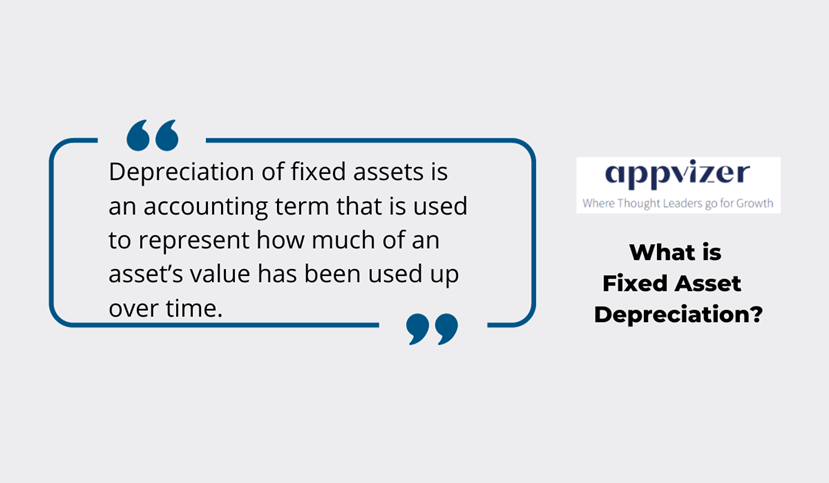
This loss in value occurs due to normal wear and tear, technological obsolescence, and other factors.
Moreover, since depreciable fixed assets typically last much longer than the prescribed one-year minimum (e.g., 3, 5, 7, 10, 15 years or longer), the IRS mandates that an asset’s purchase cost should be spread over its estimated useful life for tax reporting purposes.
Therefore, construction companies should determine an asset’s acquisition cost, useful life, and salvage value, choose the appropriate depreciation method, and then update asset values accordingly in their financial reports.
Although this requires the expertise of accountants and tax advisors, asset management software can help companies avoid the pitfalls associated with manual depreciation calculations by automating the process.
For example, with GoCodes, all a company needs to calculate depreciation is the asset’s purchase date, cost, and useful life.
When this data is entered, users can choose between one of the IRS-approved depreciation methods shown below, and the software will automate calculations.
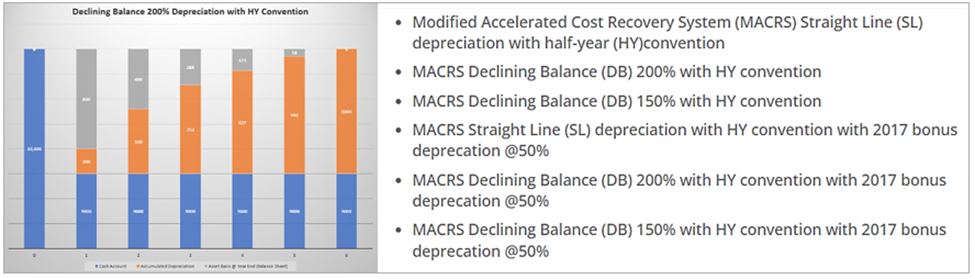
Such automated systems not only enhance the accuracy of calculating depreciation and ensure compliance with accounting standards but also save time and resources, allowing companies to focus on strategic planning and decision-making.
To recap, since depreciation errors can have far-reaching consequences on your company’s financial stability and decision-making, it’s best to automate this complex process by utilizing an asset management software’s depreciation feature.
Not Using Fixed Asset Management Software
By now, it’s clear that construction companies that don’t use some type of fixed asset management software will have an increasingly hard time keeping up with the competition in terms of their efficiency and data-driven decision-making.
In other words, manual asset management with the help of spreadsheets can lead to mistakes and inefficiencies like:
- increased likelihood of data entry errors in asset records,
- no real-time visibility into asset locations, users, and statuses,
- reduced ability to prevent and detect asset theft or loss, and
- difficulty in tracking asset depreciation accurately.
The above issues are, as they say, only the tip of the iceberg.
For example, spreadsheets lack the ability to easily generate custom reports and analyze asset data.
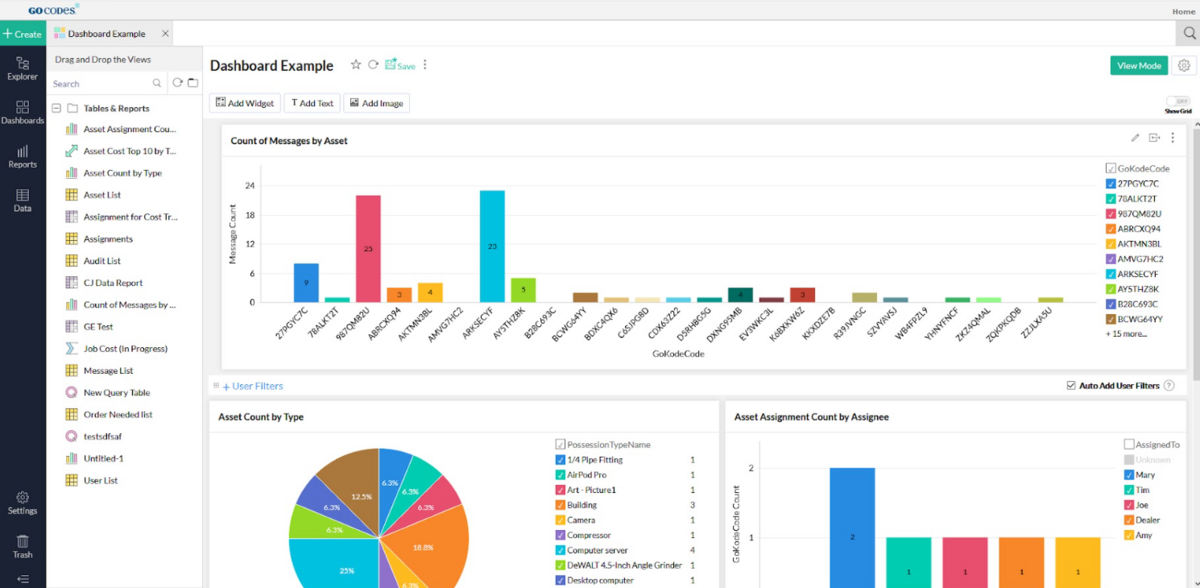
Likewise, spreadsheet-based asset management offers very limited options for integration with other software systems like accounting or project management tools, making it challenging to streamline overall construction operations.
Conversely, leveraging asset management software addresses all the above inefficiencies and more.
For instance, we already established that asset tracking/management solutions can:
- streamline regular asset audits,
- track asset users and locations,
- enable preventive maintenance scheduling and management, and
- automate the asset depreciation process.
Moreover, they ensure accurate asset records, provide real-time accessibility to up-to-date information, help prevent theft, increase worker accountability, and facilitate seamless integration with various software systems.
Overall, using fixed asset management software is nowadays almost a necessity, allowing companies to digitize and automate workflows, enhance efficiency and decision-making, and stay competitive.
Following Poor Asset Disposal Practices
When construction companies dispose of end-of-life fixed assets like heavy equipment or vehicles, failing to follow proper disposal practices and document the process exposes them to potential fines and can also harm their reputation.
For example, if a company decides to abandon an old excavator instead of dispose of it properly, this poses environmental risks, as its fluids and materials could leak over time and harm the surrounding ecosystem.
Of course, this also violates environmental regulations, leading to potential fines and legal complications for the company.
Additionally, that company may suffer from reputation damage since, if the word on the abandoned equipment spreads, clients and partners may question its commitment to responsible practices.
To prevent these consequences, construction companies should apply one of the following proper disposal practices:
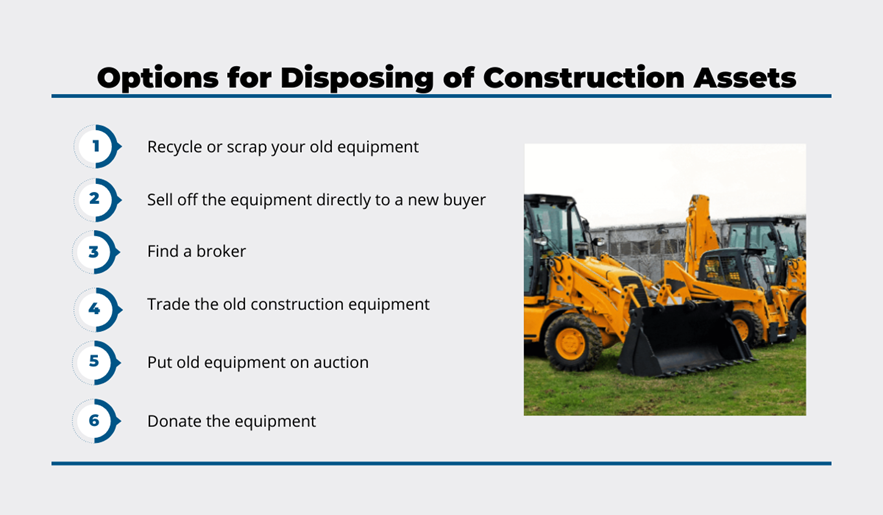
As these asset disposal options are elaborated in our article on that topic, we’ll just say that each of them, unlike asset abandonment, can produce a bigger or smaller monetary return, thus recouping some of the company’s initial investment.
For example, selling off the old excavator directly to a buyer or putting it on auction can, depending on factors like the equipment’s condition, market demand, and negotiation skills, yield a substantial financial return.
As for selling your obsolete equipment for parts or extracting recyclable materials, this will generate a smaller return but will ensure compliance with environmental regulations.
In conclusion, adopting responsible fixed asset disposal practices is crucial to avoid potential fines and financial losses while also protecting your company’s reputation.
Conclusion
So, we have gone through six mistakes in fixed asset management and suggested ways to avoid them from hurting your company’s efficiency, profitability, and reputation.
Having done so, it’s clear that utilizing asset tracking and management software can streamline most (if not all) asset management processes, thus enabling you to prevent many mistakes stemming from relying on manual, error-prone, and time-consuming data entry.
Conversely, having access to digitized, readily available asset management information in real-time allows your company to get the most out of its fixed assets, thereby boosting overall productivity and bottom line.