Giving up manual asset tracking and switching to asset tracking software is more than just a trend. These automated systems truly benefit your business on so many different levels.
If you’re thinking about making this transition, keep on reading to find out what kind of issues you’ll be able to solve or even completely avoid with the help of asset tracking solutions.
In this article...
Inaccurate Asset Data
Manually tracking your assets, i.e., relying on spreadsheets or different paper forms to monitor your equipment, tools, and construction materials, is known to be the source of bad data.
Autodesk and FMI define bad data as “inaccurate, incomplete, inaccessible, inconsistent or untimely,” and as such, warn that it “can’t be used to derive actionable insights.”
But what does this mean for you, exactly? To get an answer to that question, let’s take a look at some numbers.
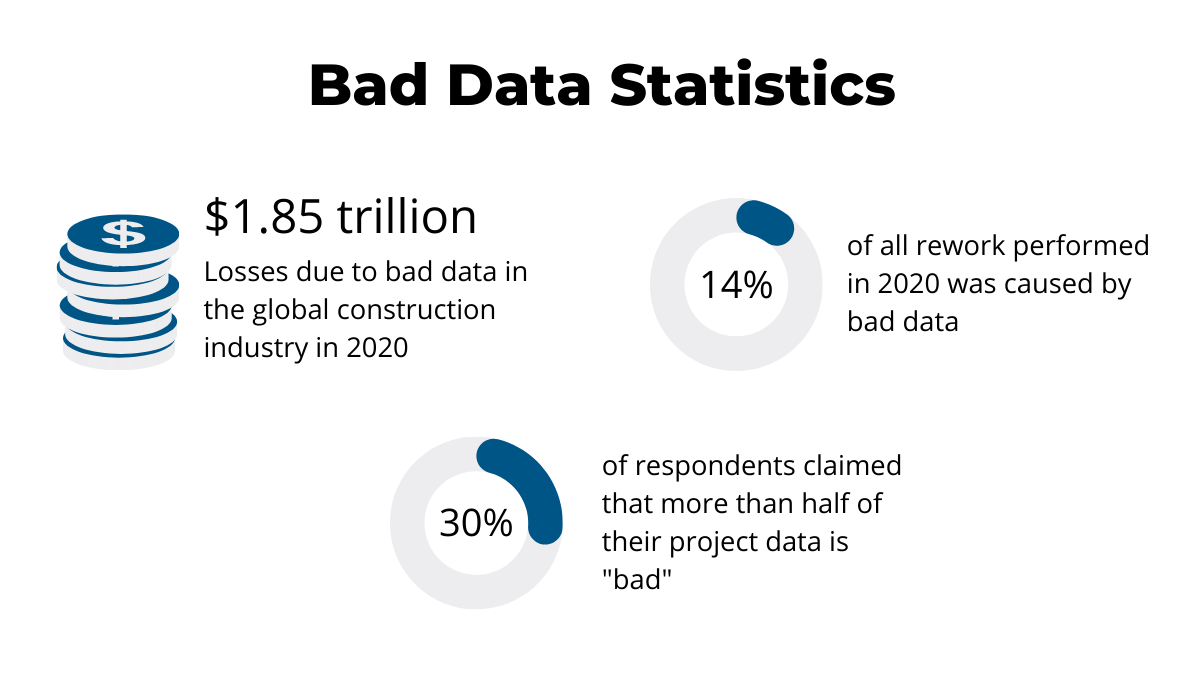
The survey, conducted by Autodesk and FMI on over 3,900 construction industry professionals, truly underscores the fact that bad data is not just some minor problem.
It has serious consequences because it negatively impacts decision-making and, in turn, costs the industry a lot of money.
And the evidence consistently points to the fact that manual asset tracking is simply no way to go if your goal is to gather accurate and up-to-date data.
For example, Acuity Training surveyed 1,000 UK office workers about their Excel skill levels, and although the survey was primarily centered around how proficient workers were in Excel or how often they use it, it also revealed that Excel errors could potentially turn out to be pretty costly in the long run.
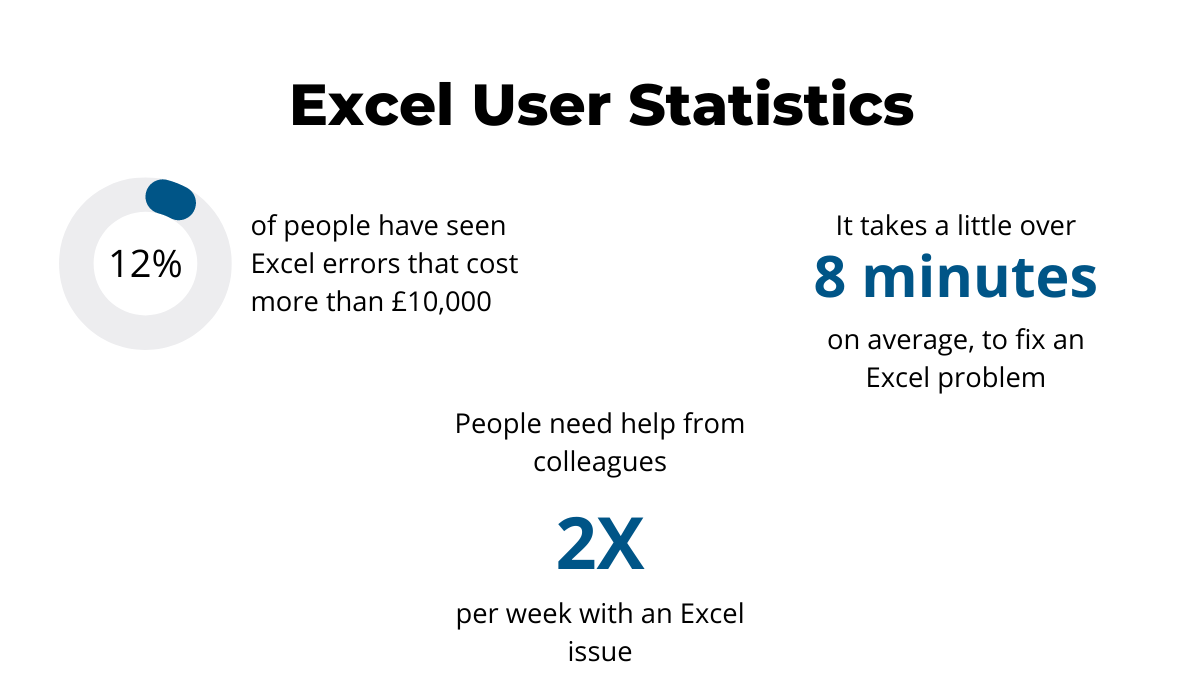
In fact, the Internet is full of stories that illustrate how expensive spreadsheet mistakes can be.
And this really comes as no surprise.
Manual asset tracking is notoriously time-consuming, and since it relies on people to manually enter each piece of data, the whole process is highly prone to human error.
Even the most diligent and meticulous employees can get tired or distracted and copy/paste information into the wrong cell or press a five on their keyboard when it should’ve been a four.
Simple, tiny mistakes like that accumulate over time, and before you even start to notice it, they begin to affect overall productivity.
That’s why asset-tracking software users see so many improvements to their operational efficiency.
Moreover, since manually updating spreadsheets is such a tedious process, employees are often reluctant to do it at all, which results in outdated data.
For example, once a worker notices a problem with a tool, he or she will probably have to wait until the end of their shift to report the issue if there are no automated and mobile-friendly systems in place.
Until then, the worker is highly likely to forget all about it, and the team will continue operating based on the assumption that the tool is available for use when it’s not.
Finally, performing different audits, such as asset inventory, compliance, and financial audits, without asset tracking software can be tricky and time-consuming, as it usually entails going through different records and spreadsheets looking for data you need at that moment.
And if it turns out your data is inaccurate, audits become an absolute nightmare—a nightmare that can have severe consequences for your business.
To illustrate, the OSHA standard 1926 Subpart E lists personal protective equipment that must be used in the construction industry, which means that listed items must be present at a job site.
Losing track of those items directly translates to non-compliance and possible penalties and fines.
And, of course, not having assets where they need to be frequently goes hand in hand with having inaccurate data.
Assets Going Missing
Missing assets are a common issue on construction sites. Did you know that construction workers spend a significant portion of their working hours looking for missing tools?
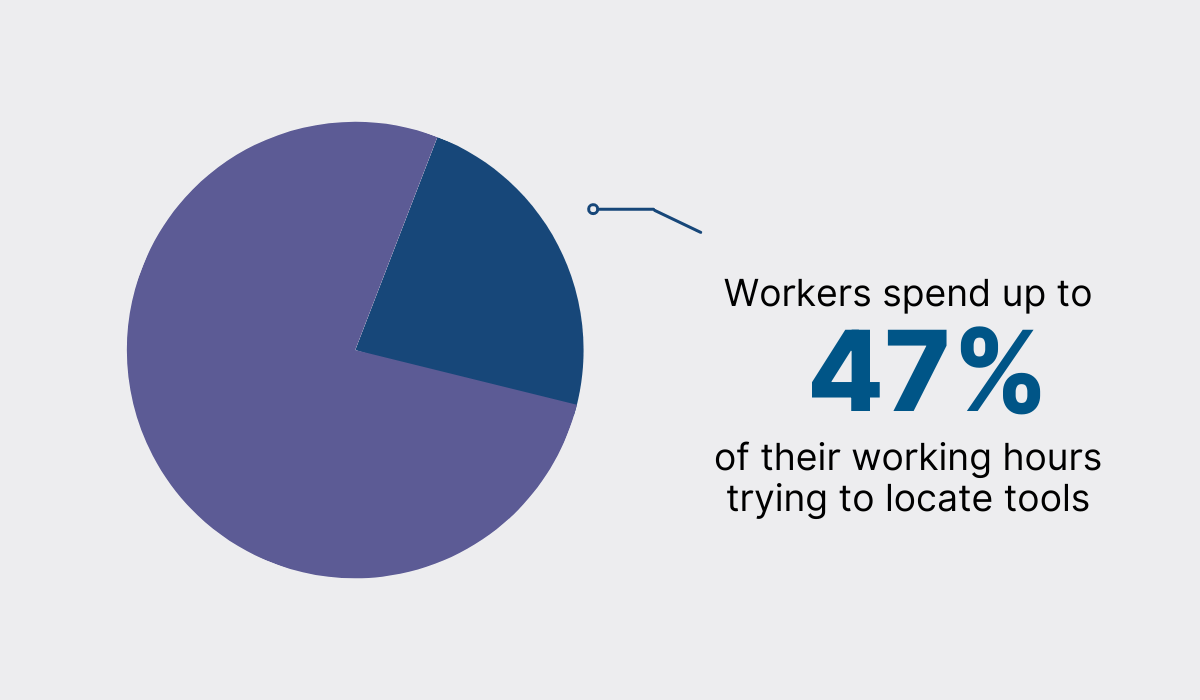
Misplaced tools cost companies a lot of money on many different fronts. Firstly, they cause significant costly project delays.
Then, if the lost tool is never retrieved, the company needs to buy a new one, probably pay for expedited shipping, and wait for the delivery, which even further delays work and increases costs.
To continue, another serious issue construction companies face is theft. Just like tool loss and misplacement, this issue can also be attributed to improper asset tracking.
Just to illustrate the prevalence of theft in the industry, 11,504 burglaries were reported on construction sites in the US in 2021 alone.
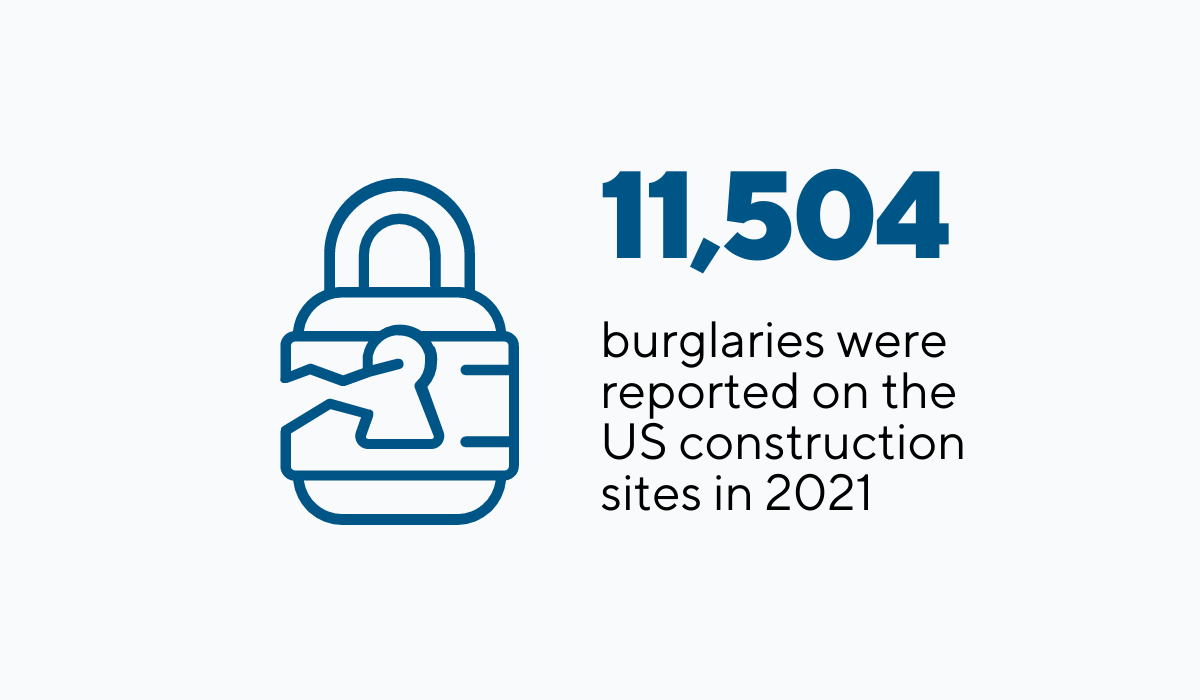
For example, in Middletown, Ohio, a contractor suffered a loss of $20,000-30,000 after robbers stole his equipment, and in Clinton Township, a $165,000 Caterpillar loader was stolen that same year.
The list of examples like these goes on, but it becomes pretty clear right away how costly this issue can become for construction companies.
Asset tracking software is an effective way of preventing both asset loss and asset theft.
Not using it virtually means giving up on ever finding your lost assets or retrieving them should theft occur.
Not only that, but since the software relies on tagging your assets, asset tracking systems often deter thieves from ever committing the crime because seeing a tag on an item immediately tells them its location is being monitored.
In other words, asset tracking software doesn’t only help with stolen asset retrieval, but it also plays a role in theft prevention.
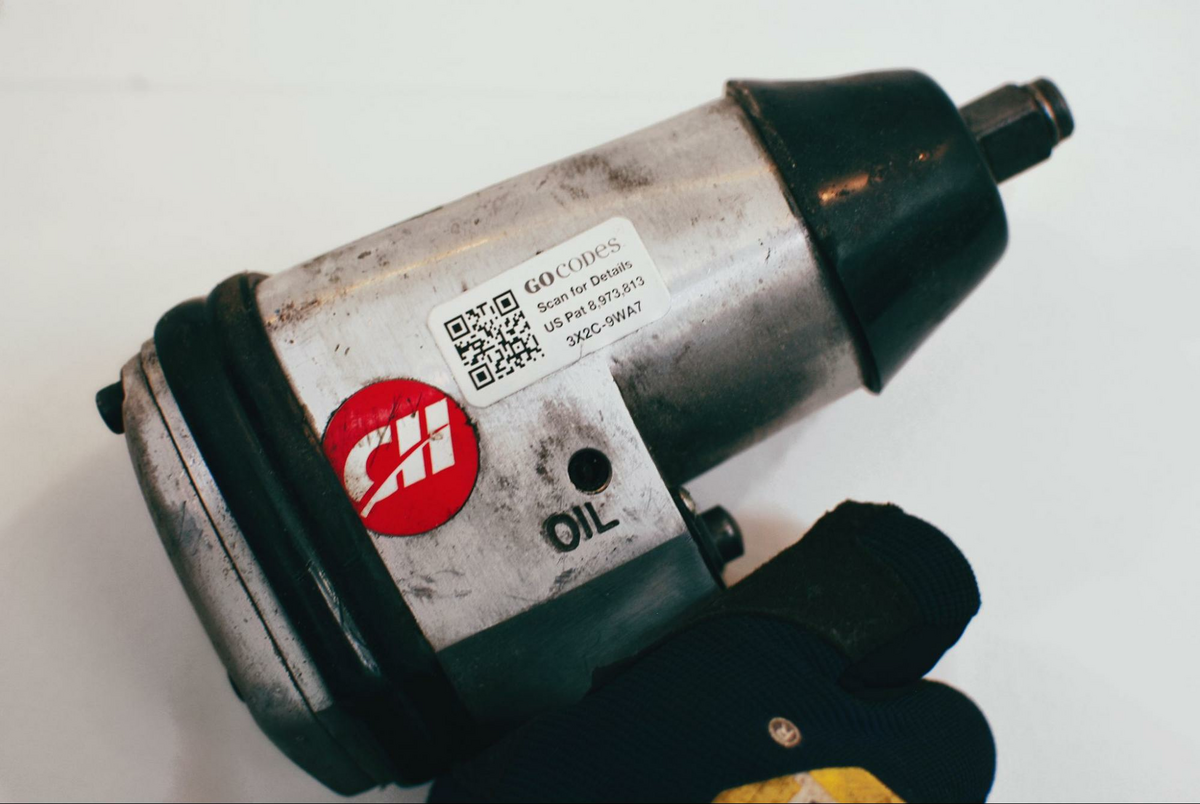
Our asset tracking solution—GoCodes—relies on durable customized QR code tags that emit asset location information once scanned with our scanner app.
To elaborate, each time an employee scans the label, for instance, during asset check-out or check-in, a record in the asset’s History is created, and it shows who made the update, as well as the time and place of the update.
Moreover, our newest high-tech feature—Bluetooth Beacons—takes asset location tracking to another level.
These battery-powered sensors utilize radio technology to broadcast asset information to nearby Bluetooth-compatible devices, such as smartphones.
This eliminates the need for manually scanning the codes, making the whole process even easier and faster.
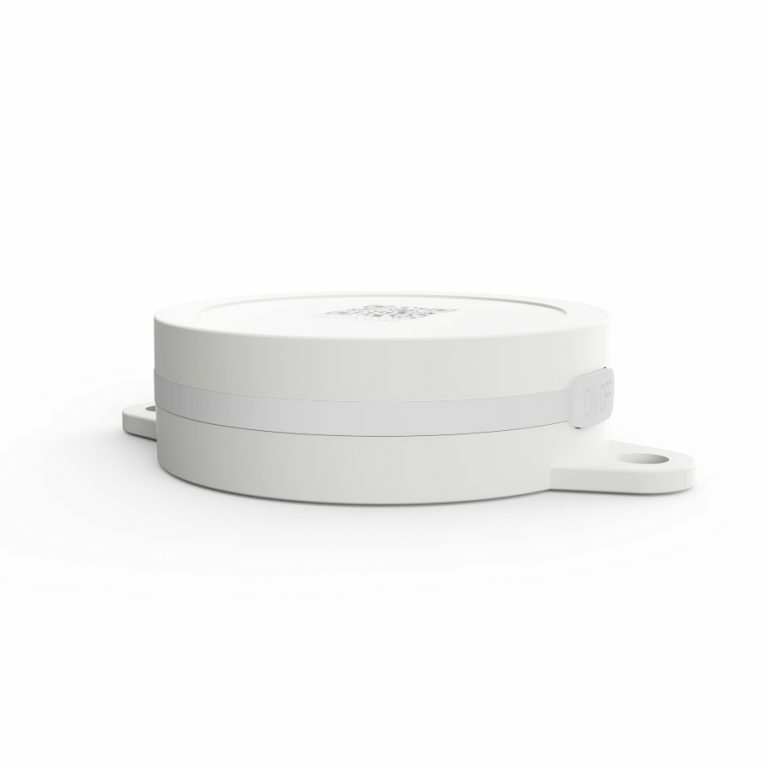
Not only that, but thanks to our Guardian feature, you’ll be immediately notified if an asset’s been removed from within the range of the app.
All in all, your assets are a significant investment, and as such, they need to be protected.
Part of taking care of the assets means working towards loss and theft prevention, which is almost impossible without asset tracking software.
Poor Asset Maintenance
Taking good care of your assets also entails proper asset maintenance.
An important thing to note is that poor maintenance isn’t only harmful to your assets but to your employees as well. Let’s take a look at some of the reasons to avoid it.
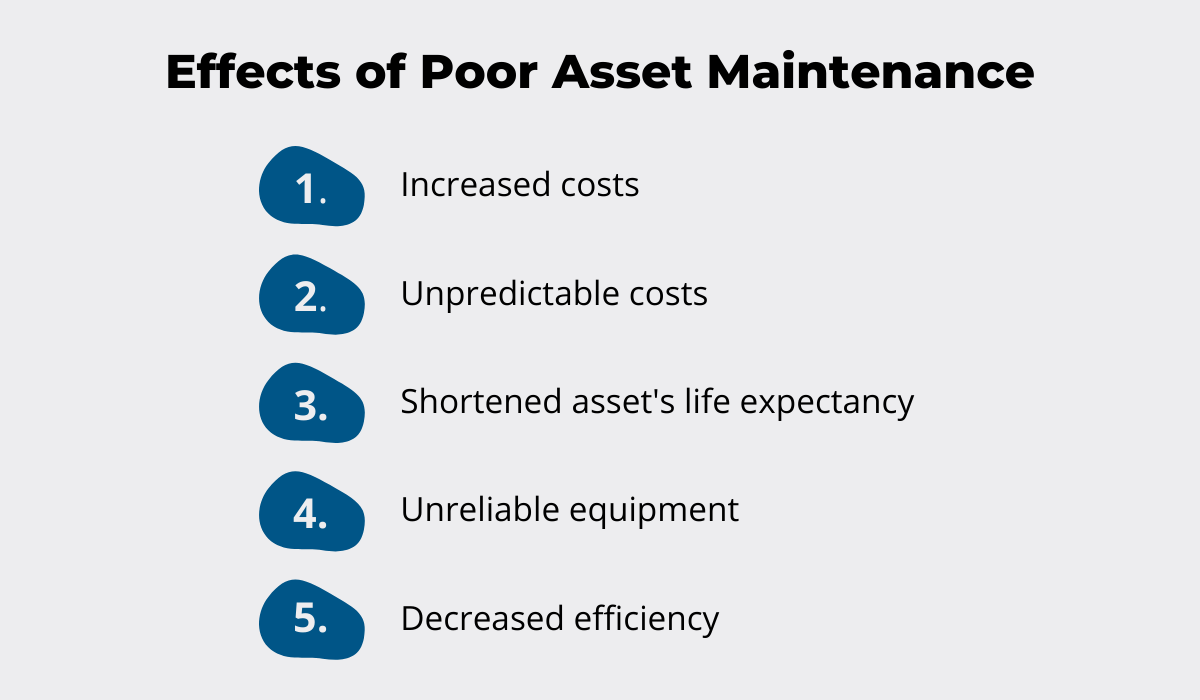
Poor maintenance is usually equated to reactive, unscheduled maintenance that is performed only when an issue with equipment already appears.
As such, it can be quite a profitability and productivity killer.
To elaborate, reactive maintenance costs are far more significant since having equipment that is improperly maintained also means the equipment will unexpectedly break down more often.
In turn, it’ll require more maintenance, shorten the assets’ lifespan, and cause even more unplanned downtime, all of which negatively impact your overall efficiency.
But most importantly, poor maintenance directly translates to unreliable and unsafe equipment, which can inflict severe damage to the other equipment and injury to your employees.
Preventive maintenance remedies all of these issues.
In fact, a University of Nebraska study showed that preventive maintenance could reduce repair costs of heavy machinery by up to 25%.
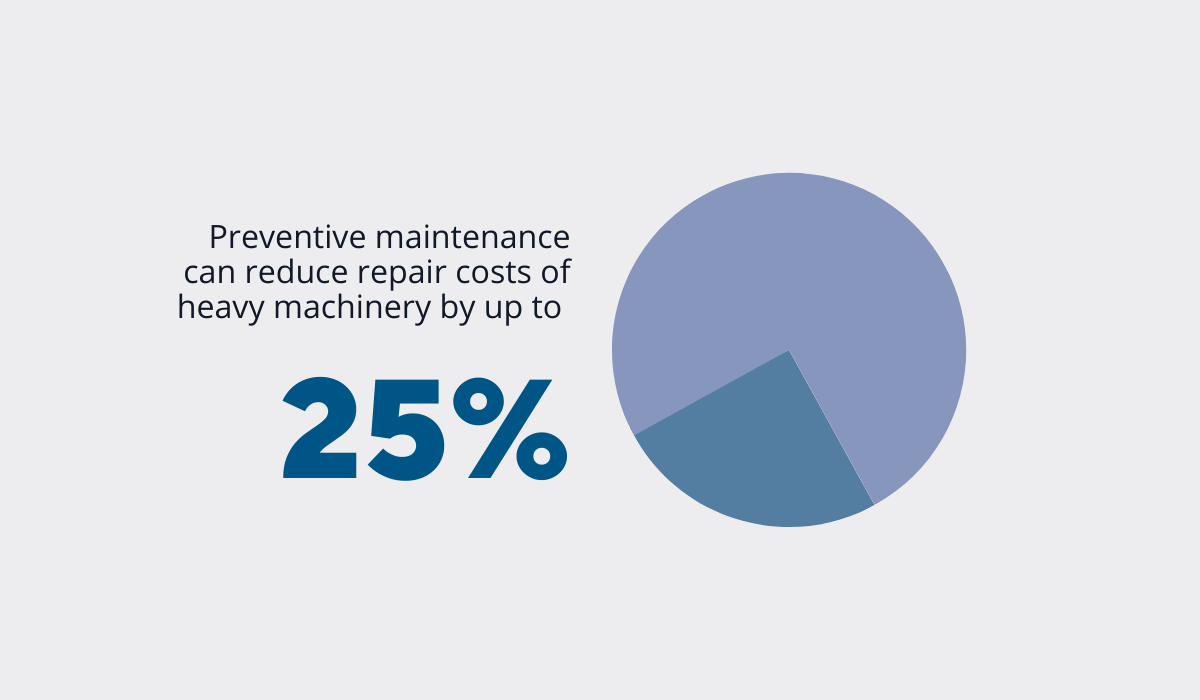
Preventive maintenance entails doing routine checkups on your assets in an effort to, as the name suggests, prevent any significant damage.
The checkups are always planned and scheduled during planned downtime so as not to cause any delays.
However, manually tracking maintenance schedules can be problematic.
Sometimes, it’s not clearly communicated who was supposed to do what, or people simply forget there was supposed to be maintenance in the first place.
Asset tracking software nips these problems in the bud.
Not only does it enable you to set up specific tasks and assign them to your employees, but it also sends out scheduled service notifications via email, either the day before or on the day of maintenance, depending on the settings.
Overall, proper asset maintenance is indispensable when it comes to increasing efficiency, job site safety, and profitability.
Asset tracking systems ensure you never miss scheduled service and help you make the most out of your assets.
Bad Inventory Management
Protecting and taking care of your assets is imperative; there’s no doubt about it. However, you also need to make sure they are correctly allocated.
Otherwise, all that hard work monitoring and maintaining them means very little.
To elaborate, you need to know at all times how much of each asset you have and then be able to, based on the data you have, accurately forecast how much you will need for the successful completion of each project.
As we already covered in the first section, manual asset tracking is the root of inaccurate data, so if you’re not using asset tracking software, the chances are you don’t have the grounds for precise decision-making.
How can you accurately predict your asset needs if you don’t have accurate data at your disposal?
Two problems most commonly stem from the inability to accurately forecast inventory needs: overstocking and understocking.
Yes, having too many assets is not always good, and overstocking can have serious adverse consequences.
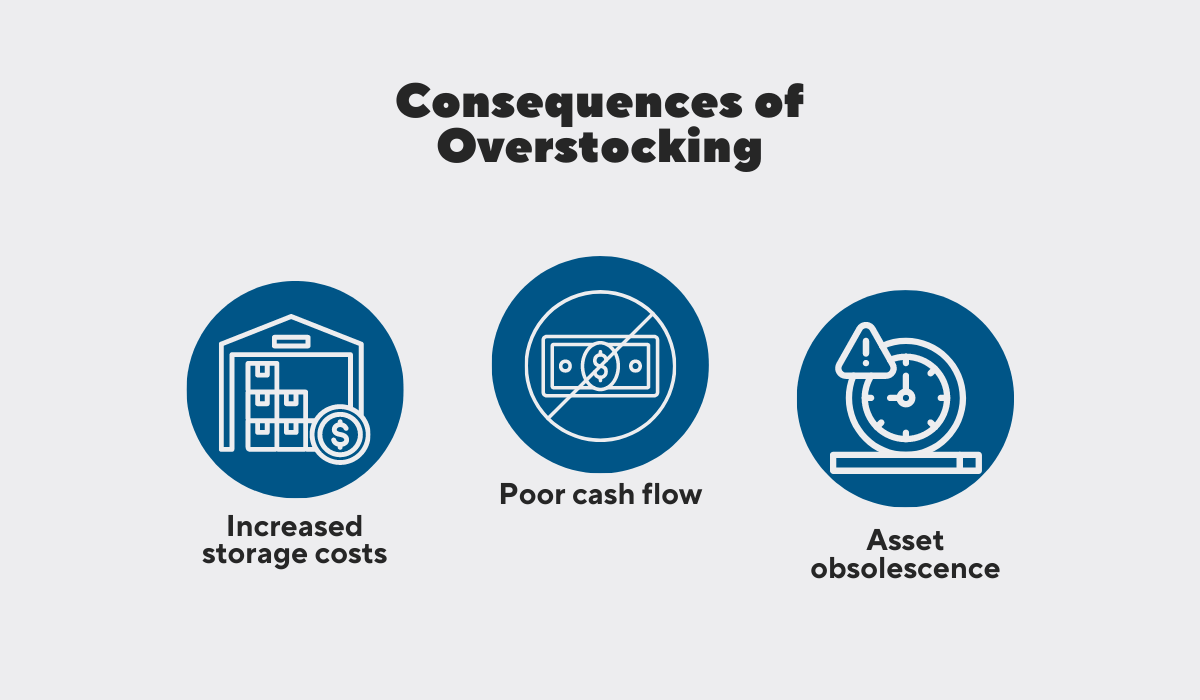
To begin with, overstocking effects first become visible through increased storage costs.
Everything you buy, from construction materials to heavy machinery, needs to be adequately stored, and that doesn’t simply entail having the space where you’ll put all that equipment.
You also need to consider security, material handling, insurance, and utility bills, all of which cost money.
Furthermore, having your money tied up in assets you’re never going to use not only constitutes a lousy investment, but it also means you now have less money to put towards actually improving your business.
Finally, having your assets sit unused in a warehouse for too long can lead to their obsolescence.
They can deteriorate over time, especially if improperly stored, or a newer, more advanced model can become available on the market, eliminating the need for the one you have.
Moreover, understocking is a more obvious result of inventory mismanagement, and so are its consequences.
Not having enough materials, tools, and equipment to finish a project, especially if you realize this in the middle of the project, interrupts your work and impacts your productivity.
Simply put, thinking you have something you actually don’t have seriously slows you down.
Therefore, to ensure you have enough inventory for successful project completion at every moment, consider using asset-tracking software.
It serves as a centralized database with all the necessary information about your inventory quantities.
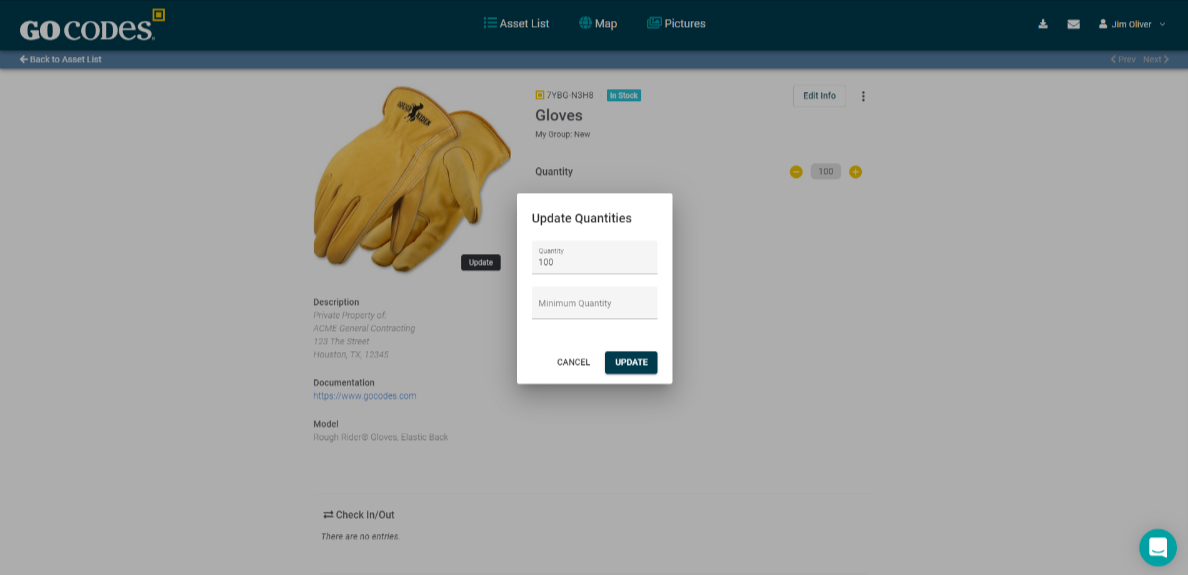
Not only that, but it also lets your employees easily update quantities on the go via their smartphones.
Plus, if a particular asset goes below the level you specify, it immediately notifies you, so you’re always on top of your inventory needs.
Conclusion
All in all, without asset tracking software, you potentially face a lot of issues that are harmful not only to your assets but to your employees, your productivity, profitability, and your company’s success in general.
There, why not try letting technology carry the heavy load of asset tracking while you focus on elevating your business even further?