If you’re responsible for a fleet of construction vehicles and heavy equipment, there are countless reasons why you should use GPS to manage your construction assets.
And even if you’re already using some form of GPS tracking to manage your fleet, there are now new reasons—or, should we say, tech solutions and applications—to consider.
In this article, we’ll cover productivity gains and cost savings that can be generated when construction businesses utilize GPS solutions to optimize construction fleet management at all levels.
More specifically, we’ll look at four ways in which GPS tracking creates these advantages.
In this article...
Planning the Most Efficient Routes
When your construction fleet is fitted with a GPS tracking system, it’s much easier to plan the most efficient routes for your vehicles and equipment on the road, and ensure timely delivery to construction sites.
And the efficiencies gained by using GPS for route optimization go well beyond fuel savings and improved driver behavior, as we’ll discuss below.
But first, let’s briefly explain that GPS stands for Global Positioning System, a series of satellites that can pinpoint the geographical location of anything equipped with a GPS tracker, from your phone to construction vehicles, equipment, and tools.
Here’s a simplified view of how the real-time location of these construction assets actually ends up on your smartphone, tablet, or laptop.
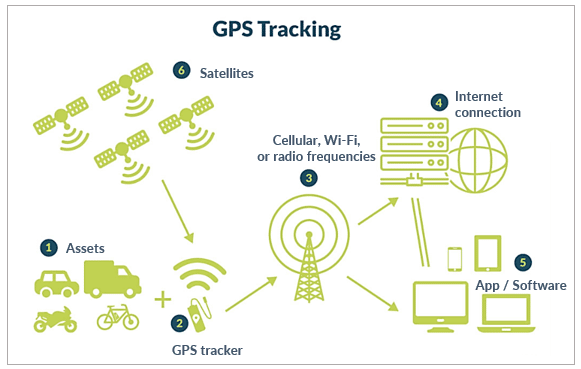
So, fleet tracking systems use GPS to track where various mobile assets are in real time.
When combined with other data, such as weather conditions, road closures, traffic jams, or accidents, the system provides route optimization features.
First, it allows drivers and dispatchers to plan their trips in advance and choose the shortest and fastest routes that avoid rough terrain and dense traffic to save fuel and time, particularly when transporting heavy equipment.
Next, historical data from past trips can be used to further optimize routes by, for instance, identifying less efficient roads for getting from storage facilities to different worksites.
Of course, there are many other parameters that go into planning the best routes in terms of cost and time, and many of them can change in real time, such as the road conditions mentioned above.
A GPS tracking system can suggest alternative paths in case of traffic jams or inclement weather.
On that note, let’s look at how an all-in-one GPS tracking and fleet management platform like Samsara can help you plan the most efficient itinerary for your fleet.
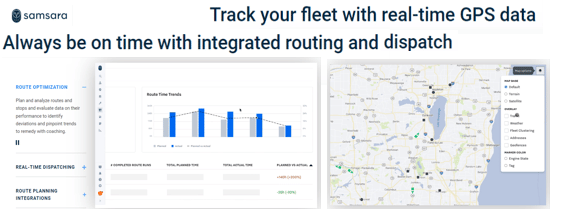
This GPS fleet tracking solution allows construction businesses to calculate the optimal route to a specific destination based on past route performance and current traffic information.
It also provides traffic and weather map overlays and sends alerts to drivers and dispatchers about traffic congestion, and enables them to make adjustments, take detours, or, when needed, combine trips on the go.
Furthermore, this and other GPS tracking solutions can be combined with other technologies to provide a host of other data that will allow driving routes to be further optimized.
Such technologies include built-in or external sensors, the Internet of Things (IoT), Artificial Intelligence (AI), and predictive analytics, all of which can be utilized to further save time and resources when your construction fleet is on the road.
Finally, GPS tracking can be utilized to optimize material and equipment deliveries to the site.
All of this greatly improves the operational efficiency of your projects.
Decreasing Your Fleet’s Idle Time
Being able to track the engine idle time of your construction vehicles and heavy equipment and analyze driver behavior enables you to reduce fuel costs, be environmentally responsible, and protect the health of your workers.
First, let’s clarify that idle time is when the engine of a vehicle or a piece of heavy equipment is running while the vehicle is not in motion.
Therefore, some idle time is to be expected, for instance, when the vehicle is waiting at traffic lights, being stuck in traffic, waiting in cold weather, or warming up the engine.
However, excessive idle time wastes a lot of fuel – and fuel is too expensive to waste.
Considering that diesel fuel prices went up 55% and gasoline prices 49% in the first half of 2022, construction businesses are compelled to rethink their fuel management practices and find ways to cut fuel costs.
And decreasing your fleet’s idle time is one of the easiest ways to do that, provided you’re using a GPS tracking system like, for example, WirelessLinks.
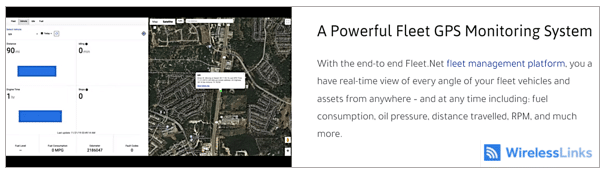
In other words, this and similar fleet management systems use GPS trackers that, when connected to the engine’s internal sensors in your vehicles and equipment, can track engine idle time, fuel consumption, and many other aspects of engine diagnostics.
Furthermore, such systems can generate different reports that allow you to analyze when and how your fleet’s idle time occurs, including vehicle locations, driver logs, fuel reports, and speed reports.
This valuable information can help you devise measures to cut excessive idle time and other fuel-wasting behaviors.
Finally, some GPS tracking software enables you to set up automated alerts to be sent to the driver after exceeding a certain engine idling period, prompting them to turn off the engine.
In fact, a report by the U.S. Department of Energy states that over 10 seconds of idle time for personal vehicles burns more fuel than turning the engine off and restarting it.
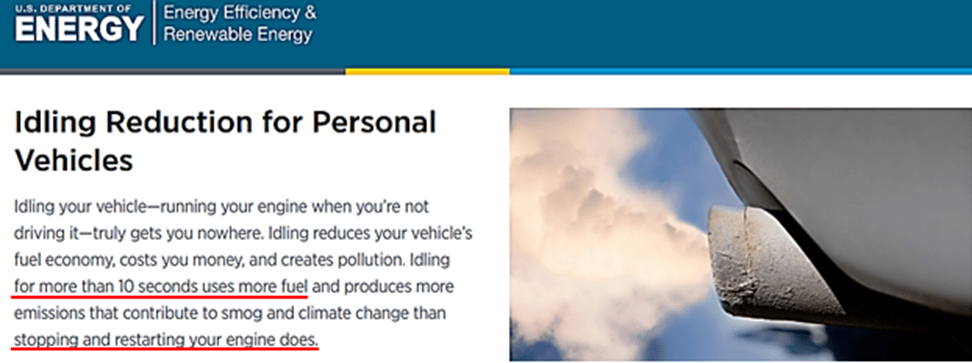
As you can see, decreasing your fleet’s idle time also reduces harmful emissions that contribute to climate change and can negatively affect your workers’ health.
Thus, to cut fuel costs, it’s time to dispense with some still persisting myths about idling—for instance, that idling is better than restarting the engine or that a vehicle should idle to warm up in cold weather.
This may have been true for older vehicles and machinery, but that’s no longer the case with the starters, batteries, catalytic converters, and other components of today’s vehicles.
And, again, when GPS tracking is used to monitor idle time and driver behavior, it’s much easier to identify excessive idling in your construction fleet and take action to reduce fuel costs, fight pollution, and protect the health of your workers.
Shortening Your Fleet’s Downtime
As we’ve seen, when GPS trackers are integrated with internal or external sensors on vehicles or equipment, the fleet tracking system allows you to track their location, engine performance, and driver behavior in real time.
The system then analyzes this data, and produces actionable insights.
This gives you unprecedented opportunities to increase overall productivity and reduce fleet running costs by shortening your fleet’s downtime.
In simple terms, downtime can occur because of inadequate scheduling, e.g., machinery sitting unused on one site while being needed on another, or poor maintenance when a vehicle or machine breaks down.
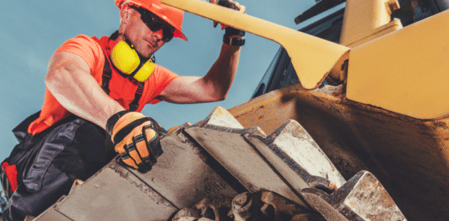
Either way, many GPS tools can help you successfully address these problems and reduce downtime by improving the utilization and maintenance of your construction fleet.
When you know where all your vehicles and machinery are at all times, and have an understanding of their condition and maintenance status, it’s much easier to create more accurate fleet schedules.
Of course, you can also instantly react to unexpected situations, such as finding the nearest available replacement in case of a machine breakdown.
On the other hand, a GPS tracking system joined with onboard diagnostic sensors, also reduces downtime by allowing you to remain on top of fleet maintenance like, for example, Teletrac Navman can do.
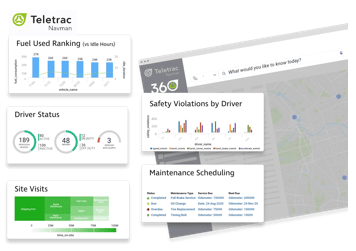
As you can see, it will allow you to basically track everything from fuel spending and engine performance to driver behavior, together with automated alerts for scheduled maintenance.
This means that regular maintenance and safety compliance of your fleet will not be an issue.
The system will also be able to identify certain issues before they turn into serious problems, be it a breakdown or excessive fuel use.
Therefore, using GPS tools to plan, monitor, and optimize fleet utilization and maintenance can improve overall productivity by shortening all kinds of downtime resulting from risks inherent to construction projects.
Protecting Your Fleet Against Theft
Of course, knowing the exact GPS location of your construction vehicles and heavy machinery, as well as any other pieces of equipment, tools, and other items of value, has an important role in preventing theft and increasing worker accountability.
In simple terms, if one of your trucks goes missing, you’ll know where it is and you’ll be able to alert the authorities.
Equally, different GPS tracking systems will also record who checked out the vehicle or a piece of equipment, thus enhancing employee accountability and establishing a clear chain of custody in case of theft.
Moreover, the latest GPS tracking solutions allow you to create invisible fences (geofences) or set time restrictions (time fences) to protect your construction fleet from unauthorized use and theft, enabling you to receive real-time alerts. One such solution is, for example, Verizon Connect.
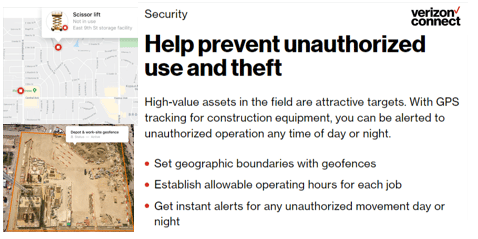
So, when it comes to your construction vehicles and equipment, GPS tracking allows you to take preventive measures against theft or unauthorized use.
However, GPS tracking doesn’t have to stop there. It can extend to all other equipment, tools, and other valuable items that tend to “disappear” on construction sites and end up affecting your business by reducing productivity and inflating costs.
One solution that can provide the latest known GPS location of every piece of equipment and tool, regardless of their size, is GoCodes.
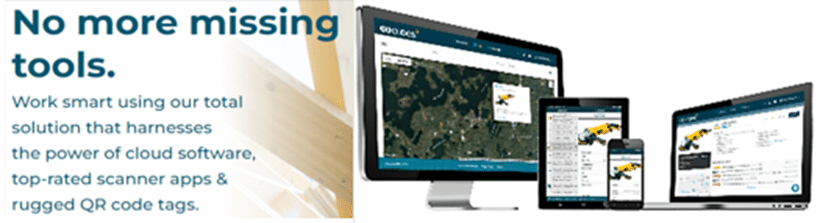
This cloud-based app comes with customized QR code tags (or Bluetooth beacons for added security) that are then attached to any item you want to track.
This GPS tracking solution is practical and affordable because, instead of using active GPS trackers, it automatically records an item’s GPS location every time a tag on it is scanned with a user’s smartphone or another compatible device.
It shows the location in Google Maps, so the tagged item can be located when needed or if lost, misplaced, or stolen.
GoCodes is also ideal for setting up a check-out/check-in system, which increases the accountability of workers and prevents theft even when tools exchange hands on the jobsite.
Therefore, various GPS tracking solutions will not only provide the location of missing property but enable a whole range of security features to protect your construction fleet and other assets from theft and unauthorized use.
Conclusion
In summary, if you’re responsible for a fleet of construction vehicles and heavy equipment, you should consider utilizing one or more GPS tracking solutions.
Why? Because they can save time and money by enabling you to use the most efficient driving routes, decrease idle time, reduce downtime, and keep your construction fleet secure.
At the same time, different GPS tools will enable you to improve overall fleet and asset management, enhance the accuracy of your estimates and schedules, increase productivity and boost profits.
So, as said in the opener, there are countless reasons why you should use GPS to manage your construction fleet.