If you’re in the construction business, you already know how valuable and crucial heavy machinery, equipment, and tools are for the success of your company.
Unsurprisingly, when such equipment is mismanaged, it can seriously jeopardize construction operations, cause accidents and injuries, and lead to project delays and budget overruns.
So, here are five equipment-related mistakes often made by contractors and some ways to avoid doing them.
In this article...
Keeping Equipment Idle
When the equipment you own, lease, or rent is sitting unused on-site, it’s wasting money in more ways than one.
To see how this happens, and explain how to counteract it, let’s start with a definition of equipment idle time, courtesy of Linarc:
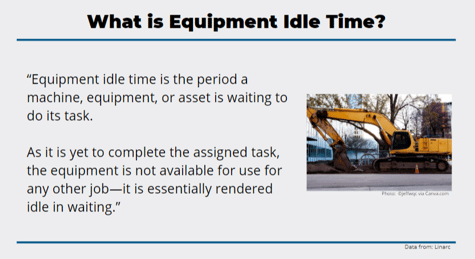
In other words, any functioning equipment that goes unused for whatever reason costs you money, particularly when it could be utilized on another project.
Even when that’s not the case, there are still storage and maintenance costs to consider.
Moreover, the negative effects of keeping equipment idle aren’t limited to the equipment you own.
If leased or rented equipment is kept idle, you’re also losing money while it waits to be put into operation.
Equipment can end up being idle for a variety of reasons, which can be roughly classified into two major categories—external factors, such as unexpected site conditions or last-minute change orders, or internal ones, such as poor equipment management.
External factors include on-site accidents, unexpected breakdowns involving other equipment, or natural disasters, any of which can delay the ongoing construction operations or even the entire project.
As for internal reasons, the equipment can be kept waiting because the preceding task takes more time, whether due to human factors (e.g., slow or inadequately trained workers) or scheduling issues.
This brings us to a great way that contractors can improve their productivity and equipment management, as well as minimize idle time caused by their operational inefficiencies—utilizing software to track the usage and location of heavy machinery, equipment, and tools.
For instance, using an asset tracking app like GoCodes Asset Tracking allows contractors to track where all their equipment and tools are and whether they’re being used.

By using this or similar equipment management software, contractors can improve their equipment scheduling, thus helping them minimize the costs of unused owned, leased, or rented equipment.
Overall, although equipment idle time can’t be completely avoided, using asset tracking software is a great way to ensure that all your equipment and tools are optimally utilized from the start.
Leaving Equipment Exposed
One of the most common mistakes contractors make is leaving their equipment exposed to the elements or failing to store it properly.
Such actions can damage even large and durable equipment.
Even though construction equipment is made to withstand harsh conditions, that doesn’t mean all of its components are meant to endure them for prolonged periods of time.
In other words, some equipment components can be sensitive to extreme weather, especially extreme temperatures.
During the summer months, the negative effect of heat and sunlight can be substantial, which can be mitigated by, for instance, ensuring more frequent breaks for machines prone to overheating.
As for winter months and the adverse impact of freezing temperatures, here’s what you can do to protect your equipment:
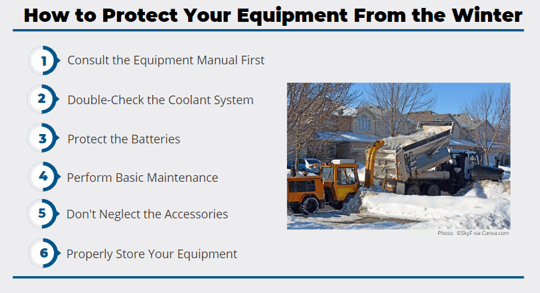
Your equipment’s coolant systems, batteries, and accessories are most vulnerable to freezing temperatures.
Given all of the above, you’d do well to protect your equipment from extreme temperatures after it’s done its job for the day, particularly through proper storage, regardless of the season.
That way, you can significantly prolong its lifespan and save money on maintenance and repairs.
Naturally, it would be ideal to store equipment indoors, in a dry and cool place with temperature and humidity control.
Such storage conditions protect the equipment from the heat and the cold, and also prevent the corrosion of components due to temperature fluctuations and moisture.
Since that’s often not possible, especially for heavy equipment, outdoor storage options include different types of protective covers, like tarps, canopies, and tents.
They can be used to keep equipment away from direct sunlight in the summer and prevent snow and moisture build-up in the winter.
Overall, leaving equipment exposed to weather changes and extreme temperatures or failing to provide optimal storage conditions can damage it and cause unexpected breakdowns, which can jeopardize the project timeline and budget.
Failing to Train Equipment Operators
Failing to train operators properly can not only damage the equipment but harm the equipment operator as well, thus affecting both productivity and safety on your construction sites.
It’s never safe to assume that operators, even experienced ones, will know how to operate a similar and/or a new piece of equipment.
As for new workers, the insurance company Hartford analyzed workers’ compensation claims in a five-year period and found that they accounted for 35% of workplace injuries across all industries.
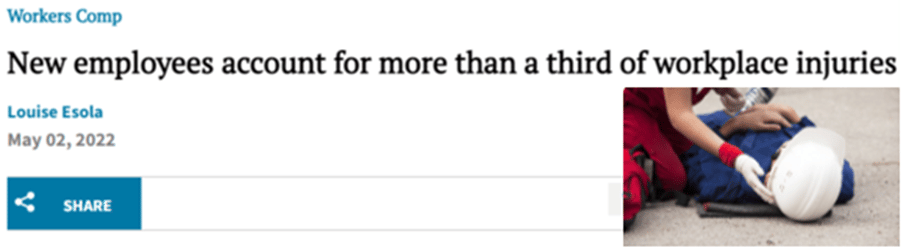
However, in the construction industry, nearly half of all claims came from workers in their first year on the job.
Moreover, the analysis found that, on average, construction workers, regardless of their experience, lost the most work days on sick leave compared to other industries.
All the above just emphasizes the importance of providing proper training for new operators and new equipment, because it can quite literally be a lifesaver.
Of course, the hazards posed by operators who received little or no training don’t stop there.
As they are more likely to mishandle the equipment, they can damage it, as well as the surrounding equipment and structures.
Additionally, unqualified operators can cost you money in fines if you don’t follow the operator training requirements for certain types of equipment that the Occupational Safety and Health Administration (OSHA) has prescribed.
Thus, inadequately trained equipment operators represent a significant risk to the safety, operational, financial, and regulatory aspects of construction projects.
So, the wise thing to do is to make sure that the operators are well-trained.
One of the best ways to do that is to get your operators trained by the same people who made the machine in question, like in the case of Volvo CE.
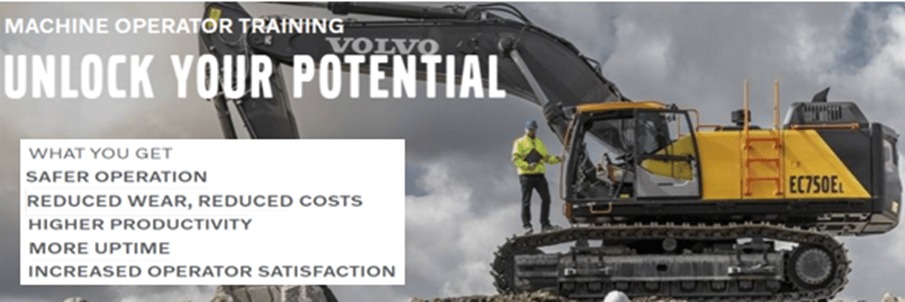
This approach is great not just for contractors, who will profit from the above benefits, but also for their operators, who will receive in-depth training that includes both theory and practice.
Operators can do the practical part through exercises or during their daily work on-site, both of which are supervised by Volvo CE’s instructor.
We should add they also offer simulation training, which is quickly becoming popular as a safer, more efficient, and affordable alternative to traditional training methods enabled by technological progress.
To sum up, poorly trained operators are more likely to mishandle equipment and cause accidents, which can end up costing you much more than any training, so don’t make the mistake of neglecting it.
Overlooking Preventive Maintenance
Overlooking preventive maintenance is a practice that persists among many contractors, but it often proves to be a costly mistake.
That’s because, although cutting corners on regular maintenance might be cheaper in the short-term, such actions can have expensive long-term consequences.
For instance, when equipment is neither regularly maintained nor inspected, minor problems can go undetected and snowball into larger ones, which are often more expensive to repair and result in longer downtimes.
Conversely, focusing on preventive maintenance can extend the equipment’s lifespan, and following regular maintenance schedules can prevent future malfunctions and failures.
Therefore, investing in preventive maintenance actually saves money, as David Auton, senior reliability engineering director at Cushman and Wakefield, says:
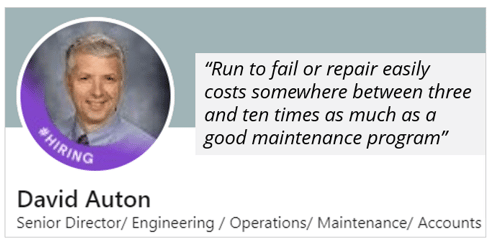
We should add that, due to still ongoing supply chain issues and rising prices, extending the useful life of their equipment has become a necessity for many construction companies.
And one easy fix that contractors use in their preventive maintenance practices is asset tracking with apps like GoCodes Asset Tracking.
One of the major advantages of this and other equipment management software solutions is that they enable contractors to collect, analyze, and utilize equipment data.
This makes it easier to establish or improve their preventive maintenance programs.
So, what best practices can help contractors identify potential defects before they snowball into significant problems?
We listed some of them here:
- Create a preventive maintenance plan
- Be disciplined about your maintenance schedule
- Gather data on previous equipment failures
- Use only trained technicians
- Monitor future equipment performance
When properly applied, these practices can cut corrective maintenance costs by up to 70%, according to Limble, which also provided this comparison of reactive (corrective) and proactive (preventive) maintenance costs of a forklift:
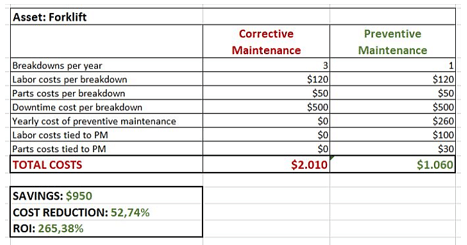
To sum up, short-term savings generated by overlooking preventive maintenance can have expensive long-term consequences.
On the other hand, creating a preventive maintenance plan and sticking to it is one of the best ways to improve equipment performance and prevent breakdowns.
Not Keeping Track of Spare Parts
Contractors often neglect to keep track of the availability of spare parts, both in their storage and on the market, which results in issues that occur on two major levels.
The first one is failing to ensure that spare parts are available on-site or in storage in case a machine breaks down.
If the parts are unavailable, companies have to deal with longer downtimes as they source them.
The second level is not keeping track of whether the necessary components are available on the market, particularly in the case of older equipment.
To prevent these mistakes, contractors should try to keep a reasonable stockpile of essential spare parts for all or at least the critical equipment in their storage to quickly deal with any failures/issues.
Additionally, they should practice open communication and good business relationships with original equipment manufacturers (OEMs) and component suppliers.
They can also try one of the online spare parts dealers, like Fortis HD, a company that promises to deliver quality heavy equipment parts in three days.
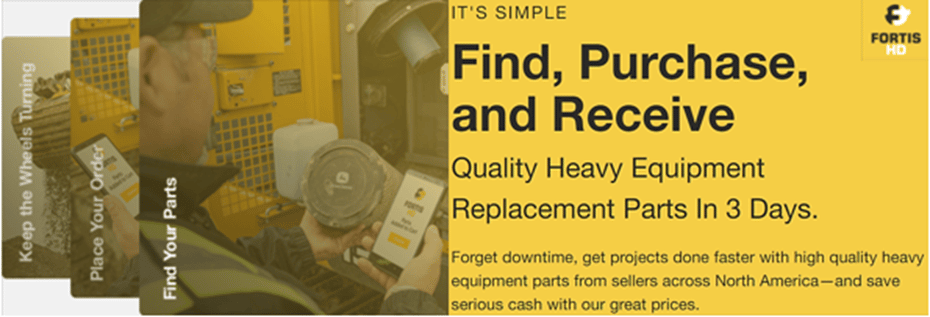
A website like this can be especially beneficial when older or obsolete equipment models break down.
In such cases, when spare parts are potentially hard to find, it can be very handy to use a website which features products from multiple vendors, as that increases the chances that some of them might stock the parts you’re looking for.
So, having a strategy for getting spare parts in situations when near-obsolete or obsolete equipment breaks down is essential in preventing longer downtimes.
Against this backdrop, construction company owners or managers can create an obsolescence management plan in six steps, thus ensuring they will keep track of spare parts as part of a wider strategy:
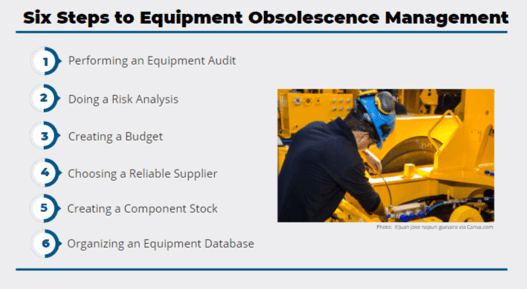
As you can see, the process starts with an equipment audit and risk analysis, where you identify, assess, and prioritize obsolescence risks to all equipment, including the availability of their spare parts, other components, and accessories in storage and on the market.
To compile all the data necessary to establish the plan and create a dedicated budget, you will need the support of OEMs and reliable suppliers.
Finally, you consider what components to stock up on, and organize an equipment database for future monitoring, thus ensuring that changes in the obsolescence status of equipment and components are tracked.
In summary, contractors should ensure they have the necessary spare parts available in storage to enable quick repairs, and they should monitor the availability of spare parts on the market as part of their equipment obsolescence management.
Conclusion
As said in the opener, equipment is a valuable investment and equipment-related mistakes not only eat into the company’s profits but can endanger the safety of their workers and the quality of their work.
However, even if your company is making one or more of these mistakes, there are many actions you can take to correct them.
These include reducing equipment idle time, protecting your equipment from the elements, properly training your operators, implementing a preventive maintenance routine, and keeping track of spare parts and other obsolescence issues.