Understanding different types of maintenance and various strategies of undertaking and tracking them enables a company to make the most of its assets.
This information is especially useful for COOs of companies with inventory or physical assets, businesses with a great deal of equipment, and businesses involved with fieldwork projects.
Maintenance can be either preventive (also referred to as proactive), which protects and prolongs an asset’s life cycle, or reactive, which involves repairs or corrective maintenance.
Mechanical assets are prone to failure, but this can be mitigated by diligent preventive maintenance. Rendering good decisions regarding corrective maintenance also prolongs the life of an asset.
In this article...
Preventive Maintenance
Preventive maintenance entails scheduled actions on an asset that help keep it in efficient working condition. It can involve filter changes, inspections, specialized cleaning, or calibration.
It usually happens on a regular, pre-planned basis, and is sometimes required for warranty or regulatory compliance.
Benefits of Preventive Maintenance
The benefits of preventive maintenance often manifest quickly and across many departments. The proper implantation of the actions is important; when preventive maintenance is rushed or conducted incorrectly, it’s often as if it hasn’t taken place at all.
Preventive maintenance leads to the following advantages:
- Extended asset life
- Greater awareness of service interruptions among employees and managers, resulting in more efficient planning
- Better workplace safety
- Increased efficiency
Applying preventive maintenance measures requires careful thought and preparation.
Check our preventive maintenance checklist to make sure that you cover all grounds.
Here are some ways to ensure such maintenance takes place correctly:
- Assign the same employee to perform the tasks to ensure familiarity and consistency.
- If an outside contractor is used to perform the maintenance, take note of the contact information of those who undertake it.
- Keep a careful log of who performs the maintenance and when.
- Maintain a list of items of concern or repeated issues to prevent reoccurrence.
Regular and efficient preventive maintenance is vital. Inconsistency can lead to damage or falling out of compliance. To ensure the appointments are met when necessary, it’s best to plan and schedule it through such asset management apps as GoCodes.
When to Use Preventive Maintenance
Manufacturer’s guidelines or operator’s manuals provide the best information about when preventive maintenance should take place. It can be time-based or usage-based.
Time-based preventive maintenance occurs no matter how much an item is used, and takes place by the calendar at regular intervals, for instance, every six months.
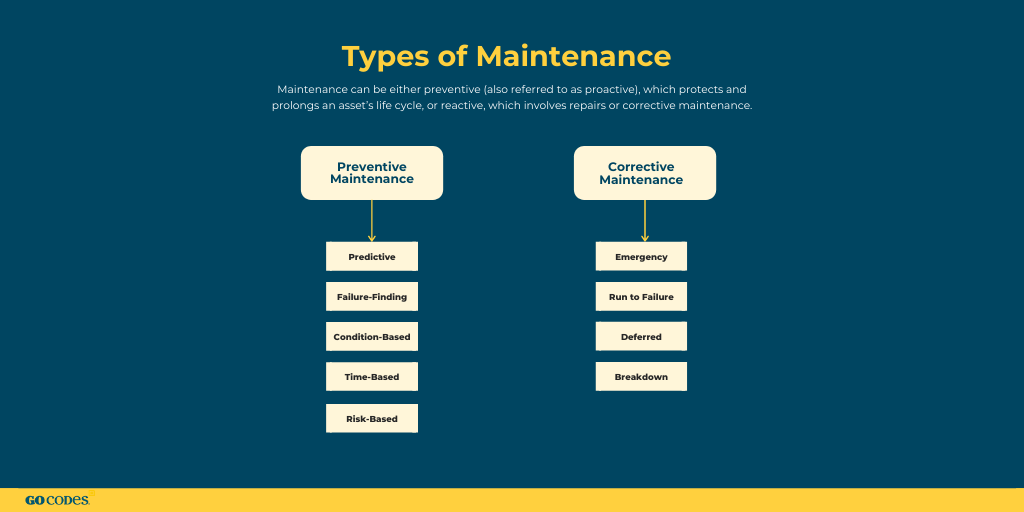
Different tasks can take place at different times and can be as frequent as a fluid refill every two weeks, or as major and spaced apart as a complete rebuild once a decade.
Usage-based preventive maintenance takes place depending on how much or how often an asset is used. This can include mileage, cycles of production, or the number of shifts.
Types of Preventive Maintenance
Preventive maintenance encompasses several different categories. Learning more about them helps people make informed decisions about the best way to extend the life of assets.
Predictive Maintenance (PDM)
Predictive maintenance involves techniques that dictate when maintenance should take place, such as data tracking and discussion with operators. It is usually used in combination with performance data to predict potential failures and prevent them through scheduled maintenance.
Failure-Finding Maintenance (FFM)
While this might sound like an “after the failure fact,” FFM is actually preventive maintenance. It involves close inspection of assets in an attempt to uncover compensated-for failures or hidden defects. Such assessments are also known as “functional checks.”
Scheduled Maintenance
Adhering to manufacturer recommendations and operator manual suggestions.
Planned Maintenance
Thinking ahead to which kinds of tasks must take place, as well as which tools and subtasks are involved. Predictive maintenance results in planned actions.
Routine Maintenance
Inspections, machine servicing, minor repairs—routine maintenance is usually undertaken on a regular basis by in-house employees as part of a daily or weekly schedule, and should be understood as part of a shift or a “typical day on the job.”
Time-Based Maintenance (TBM)
Also called periodic maintenance; as mentioned, it entails actions scheduled for an asset at particular intervals in time, no matter how much the item is used or what its current condition is
Risk-Based Maintenance (RBM)
Assigning resources to assets most at risk of failure or further breakage.
Condition-Based Maintenance (CBM)
This means looking for evidence of a pending failure through careful examination, either using a visual inspection or technical components such as radar or computer scans.
A combination of these techniques is usually best. However, this does not mean all of them will be appropriate for each organization, or every asset it owns.
For example, risk-based maintenance is in no way appropriate for assets like airplanes, medical equipment, or power grids.
On the other hand, if a company struggles for resources and uses no dangerous equipment or assets essential to core production, decision-makers might consider using that form of maintenance.
Simultaneously, time-based maintenance, routine, and scheduled maintenance might be used in connection with one another to keep assets in working condition. However, custom-built, rare, or historical assets are typically better served with predictive, failure finding, or condition-based maintenance.
The most important part of deciding on which types of preventive maintenance to use, as well as how to implement it, is maintaining the schedule, whatever it may be.
This demands careful coordination and communication with employees and managers. By letting operators, managers, and maintenance staff know what kind of tasks are expected, as well as how often, the schedule will fall more easily into place.
Providing clarity of expectations, in addition to the allocation of resources and time to correctly keep a preventive maintenance schedule, is the best way to set your system up for success and efficient operation.
Some business owners and decision-makers are surprised to discover that incorrectly implemented preventive maintenance can cost, rather than save, the company money.
In fact, according to ARC Advisory Group’s Enterprise Asset Management and Field Service Management Market Study, some companies overspend by 50% on preventive maintenance.
The problem here is not preventive maintenance itself.
Rather, these overages often take place when the tasks are not properly performed, schedules are incorrectly set, or the wrong form of preventive maintenance is chosen.
The data gathered through fixed asset tracking and real-time monitoring contributes to forming an efficient and workable preventive maintenance plan which tends to all assets in a strategic and effective manner.
Corrective Maintenance
Corrective maintenance typically takes place after an asset has failed, either in a catastrophic manner or as the result of a minor breakdown that would endanger operators or cause further damage in case of further operation.
It is usually not scheduled ahead of time.

This kind of maintenance returns an asset to the condition it was in before the breakdown or discovery of the fault, in contrast with the minor corrections, calibrations, and upkeep such as oil changes that characterize preventive maintenance.
In general, corrective maintenance takes place in three situations:
- Routine inspections, either in-house or by a third-party contractor or compliance officer, yield a hidden problem that requires attention.
- Condition monitoring, either through warning systems or data analysis, has found a possible fault that could result in further damage.
- The equipment has already broken down.
Corrective maintenance is not always a surprise to maintenance employees or decision-makers.
If a run-to-failure decision has been made regarding the asset’s life cycle, corrective maintenance is expected, although it likely does not take place on a schedule.
Benefits of Corrective Maintenance
While it might sound like an expensive and risky way to run a business and care for assets, relying on corrective maintenance carries certain advantages.
When used in conjunction with preventive maintenance and employed as part of a deliberate strategy, corrective maintenance might serve as strategic use of maintenance resources.
Here are some benefits of making the decision to use corrective maintenance:
- Lower maintenance operations (costs can shift to asset procurement and replacement or elsewhere)
- Shorter downtime, both planned and unplanned
- Costs are lower than with a reactive maintenance plan, which refers to repairing and addressing assets that have already broken down
Planned corrective maintenance, particularly for assets that are cheap to replace, already outdated, and awaiting an upgrade, or which have cost a great deal in repairs, tend to take place at the end of the life cycle of the asset.
After the item suffers a breakdown, it can be recycled, sold for parts, sold as-is, or disposed of in a responsible manner.
When to Use Corrective Maintenance
Corrective maintenance plans work best within an efficient and established workflow which employees, managers, and decision-makers understand well.
Here are some situations in which corrective maintenance is useful:
- Inspection of the asset, either by a third party or in-house operator or maintenance team member, indicates a problem.
- Visual, auditive, or other physical cues signal anomalies in the asset.
- The failure of the asset does not affect safety in any way, either for employees, end-users, or subcontractors.
- Redundancy systems provide a backup allowing for continuous operation even in the event of a breakdown.
- It is cheaper or part of an economic plan for the asset to run to failure, or it is fast and simple to repair a breakdown.
Corrective maintenance and preventive maintenance don’t need to work in opposition to one another. It is possible to use both within the same organization, depending on the assets in question and the resource-related stability of the company.
Types of Corrective Maintenance
As with preventive maintenance, several types of corrective maintenance are possible. Again, these can exist alone or in combination:
Emergency Maintenance (EM)
This is the worst possible type of breakdown. Emergency maintenance refers to urgent fixes. Usually, these involve matters of safety (replacing a shorn casing) or keeping the asset from freezing entirely (replacing an engine.)
Emergency maintenance upends schedules and quickly eats into maintenance funds, particularly if the breakdown was completely unforeseen. It might need to take place after operator error or unavoidable natural acts, such as a tree falling onto an ice-encased electrical wire.
Run to Failure (RTF)
A run-to-failure maintenance strategy includes allowing an asset to operate uninterrupted until it breaks down, at which point maintenance is conducted.
This strategy is acceptable in a few situations, such as when decision-makers have determined that the asset is cheaper to replace than to repair, or that the desired upgrade is imminent.
It is not a good plan for assets that are fairly new, important to safety, or already well cared for via preventive maintenance.
Breakdown Maintenance
Breakdown maintenance can be understood as a form of corrective maintenance.
However, while other forms of corrective maintenance generally take place when a weakness or potential fault is discovered, breakdown maintenance is specific in that it occurs only after the asset has already stopped working.
It is different from emergency maintenance in the sense that a backup is available, safety remains uncompromised, or alternative solutions are at hand until the asset is back online.
Deferred Maintenance
Deferred maintenance refers to preferable or necessary actions that can be postponed to a later date.
Perhaps the weakness in the asset will take a while to become critical, or the maintenance is largely cosmetic, as in a scratch in a car door’s paint, allowing the company’s resources to be allocated to different uses for the time being.
When a company decides to defer maintenance, it might be because in-house techs are stretched thin, third-party contractors to perform repairs are not yet available, staff members are waiting on the shipment of a part, or further diagnosis is needed to properly finish the job.
Effective corrective maintenance prolongs the life cycle of an asset and allows for more effective asset management.
Conclusion
The best type of maintenance plan is one that suits your organization, assets, and employees.
While it might not be possible to foresee and prevent every service interruption, even when applying a run-to-failure strategy, thinking through each type of maintenance and soliciting the opinions of operators and maintenance staff is key.
Working together can extend the life of your assets and provide an opportunity for strong communication and data analysis.
GoCodes Can Help
We use QR code tags with a unique visual code that you can scan with your smartphone. When scanned, GoCodes tags provide GPS information about equipment location, status, and any scheduled fixes, making equipment maintenance management a breeze. Sign up for a free trial here.