Running a successful construction company means relying on the expertise and diligence of many people, from managers and accountants to workers and subcontractors.
Among them, equipment managers play a key role in ensuring that construction operations are productive, major delays and cost overruns are avoided, and projects are profitable.
To do so, they need to ensure that appropriate construction equipment is available, well-maintained, safe to operate, and optimally utilized, which can be a complex and challenging task.
So, what are the best practices equipment managers should follow to excel at their job, why and how they should be implemented, and what methods and tools should be used?
Read on to find out.
In this article...
Conduct Equipment Market Research
Whether deciding to purchase or rent new equipment or replace or repair the existing one, the choices made by equipment managers have significant financial implications.
Therefore, conducting thorough market research before making these decisions—or assisting top management in doing so—is a cornerstone of effective equipment management.
However, research won’t get you far without a solid understanding of factors that influence your decisions, such as your company’s long-term goals and budget constraints, the estimated frequency of equipment use, specific project requirements, and timelines.
For example, although buying a new excavator would certainly speed up operations, limited financials might steer your decision toward repairing the old one or getting a rental.
On that subject, here are the arguments for renting:

However, despite these advantages, renting is not always the best option, especially for core equipment and tools frequently used over an extended period.
For instance, the tax benefits realized by purchasing and depreciating an excavator can make owning equipment a more attractive opportunity for some construction companies.
That’s why, before conducting market research, equipment managers should also understand equipment ownership terms like:
- acquisition cost: actual purchase price of equipment, plus taxes, fees, transportation, and deployment costs
- depreciation: accounting term for the gradual loss of the equipment’s value over time crucial for financial reporting and tax compliance
- estimated useful life: the anticipated period during which the equipment will be profitable
- salvage value: residual value of the equipment at the end of its estimated useful life
For instance, here’s how these terms interact when using one of the methods for calculating annual depreciation for a new excavator.
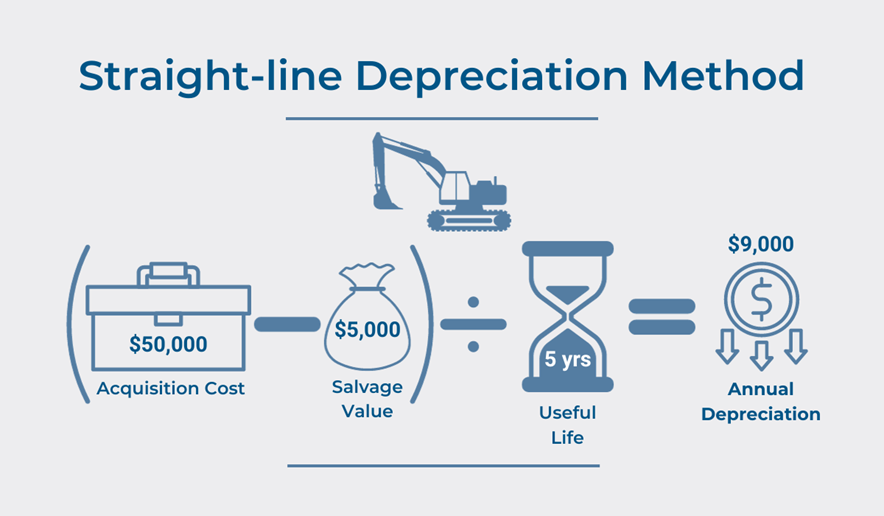
Coupled with other factors like usage intensity, wear-and-tear rates, and technological obsolescence, these considerations and calculations also help equipment managers determine whether to buy new or used equipment.
Moreover, they empower equipment managers to make informed repair-or-replace decisions when, for example, a machine with an expired warranty suffers a major breakdown.
The point of having a clear understanding of all these terms and factors is that it enables you to focus and refine your equipment market research.
Depending on the situation, this may also involve:
- researching the technology trends and innovations in construction equipment,
- assessing compliance with the latest safety standards and environmental regulations, and
- staying informed about market trends, manufacturer reputations, and customer reviews.
Overall, conducting effective market research requires a combination of financial knowledge, technical expertise, and a clear understanding of the company’s needs and goals.
When done right, this best practice allows you to make (or suggest) better-informed, data-driven decisions on when it’s most cost-efficient to buy or rent and repair or replace construction equipment.
Plan Regular Equipment Inspections
Regular equipment inspections are the bedrock of proactive equipment management, serving as a preventive measure against potential breakdowns, ensuring safety compliance, and maximizing the lifespan of construction assets.
In other words, routine inspections help unveil potential issues before they escalate into major problems, thus reducing the risk of unexpected equipment failures, costly repairs, and project delays.
So, what factors should you consider when planning regular equipment inspections?
Here are five of them:
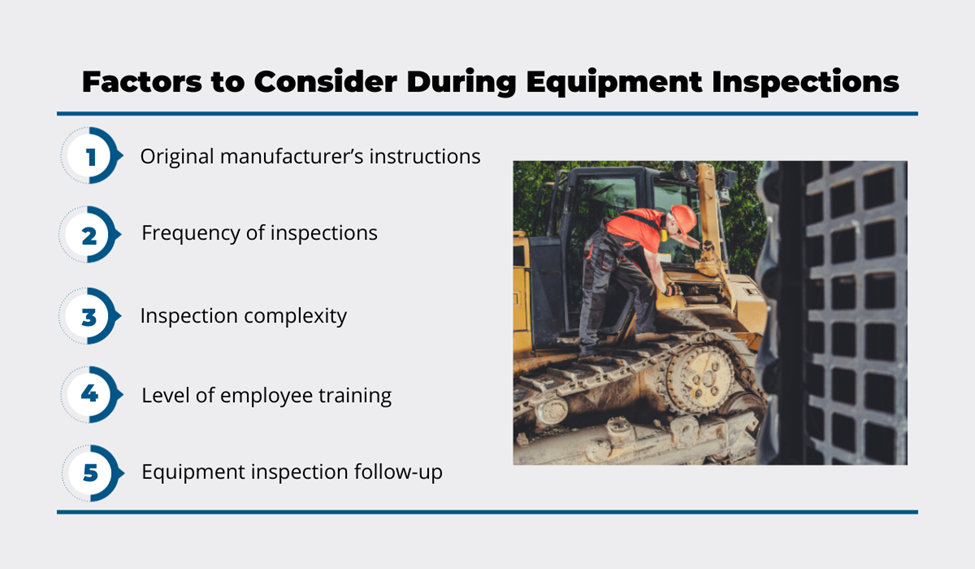
As you can see, the inspection planning process starts with the original manufacturer’s manual, namely recommendations on what inspections and regular maintenance should be performed and how often.
If the equipment is under warranty, not complying with the manufacturer’s minimum recommended frequency of inspections may render the warranty inapplicable, resulting in significant costs in case of a breakdown.
As for the complexity of worker-performed inspections (as opposed to those performed by maintenance technicians), you should strike a balance between simplicity and covering the key inspection items that affect equipment safety and performance.
The inspection forms with such items should be easily available to workers, usually in the form of a paper or digital equipment inspection checklist.
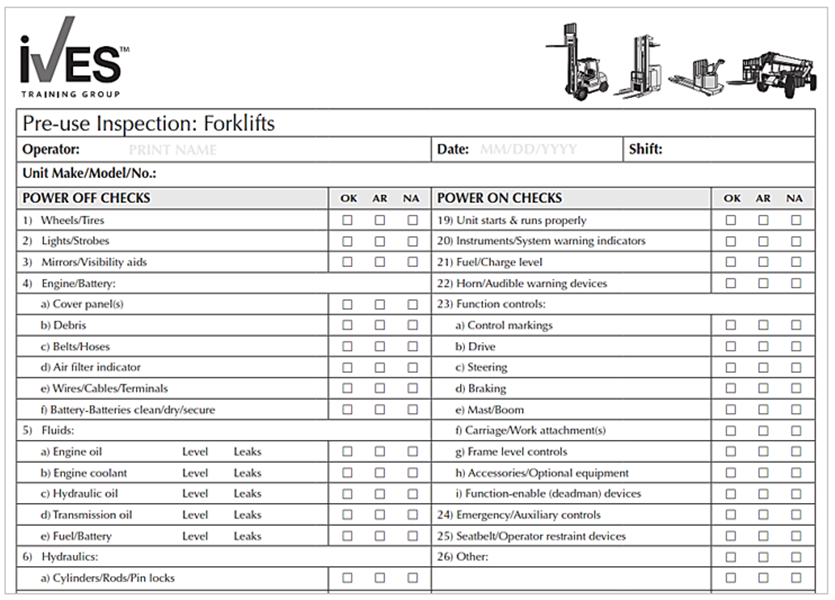
Keep in mind that, when workers can access and complete digital inspection checklists on-site, this will reduce inspection errors, automate the process, and save time on manual data entry required when paper forms are digitized.
Moreover, this implies that checklists for specific equipment, the records of previous inspections, instruction manuals, and maintenance and repair history are available in a central cloud database where they can be reviewed at any time.
Overall, solid planning and efficient management of regular equipment inspections is a crucial best practice for reducing the risk of equipment failure, minimizing unplanned downtime, improving worker safety and productivity, and prolonging equipment lifespan.
Track Equipment Usage
The practice of tracking equipment usage and condition is a fundamental aspect of the equipment manager’s job, ensuring that equipment is optimally utilized, timely maintained and repaired, and available when needed.
For example, by tracking how many operating hours an excavator clocked in, the equipment manager can anticipate and schedule when regular inspections and preventive maintenance should be performed.
However, the manager can also track the type of construction environment (e.g., dusty, extreme heat or cold) and the conditions (e.g., heavy loads, continuous operation) the excavator is operating in.
By doing so, they can adjust inspection and maintenance schedules to ensure the excavator will maintain its optimal performance and safe operation throughout its useful life.
Moreover, this allows equipment managers to make informed decisions on, as we mentioned, whether to repair or replace specific equipment and when it’s best to do so.
For instance, here are just some considerations that go into making these decisions:
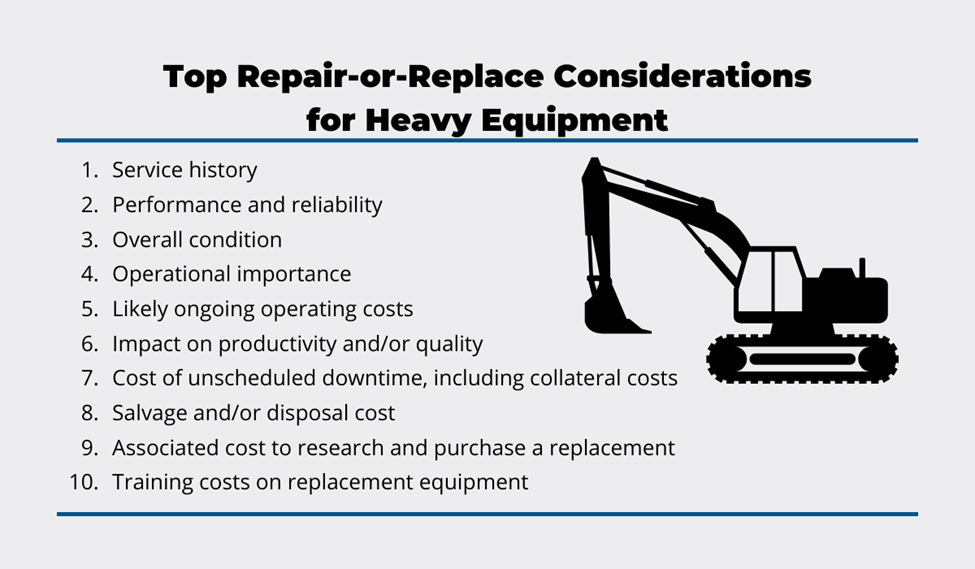
As it’s clear from the above list, making data-driven, cost-efficient decisions on repairing, rebuilding, or replacing your older, out-of-warranty construction equipment would be impossible without closely tracking its usage.
More specifically, the equipment’s info that should be tracked for improved decision-making, planning, and budgeting includes initial, unchangeable data like equipment model and purchase date and constantly changeable data like equipment users, locations, and maintenance status.
Here’s what data should be tracked and recorded by the equipment manager:
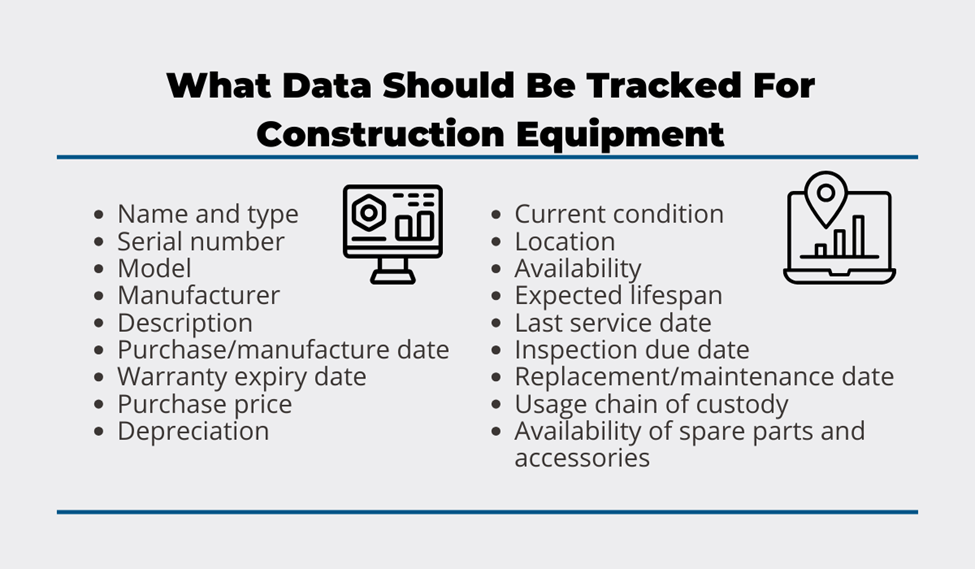
As you can see, to efficiently monitor equipment usage and ensure effective equipment allocation, utilization, and maintenance, managers have to track a series of data points, from the warranty expiry date to the availability of spare parts and servicing supplies.
Accepting that paper lists or digital spreadsheets are inefficient and time-consuming, equipment managers are turning to equipment management software to keep all this data in one central database available to all users at any time and from any internet-connected device.
This means users themselves can update the relevant equipment usage data while equipment managers can leverage the collected data to their company’s benefit.
Moreover, they can use the same equipment management software to plan, schedule, and track regular inspections and maintenance, keep an inventory of spare parts, and—as discussed next—implement anti-theft measures.
Implement Theft Prevention Measures
Unsurprisingly, the best practice all equipment managers should follow is ensuring that equipment and tools are not stolen, misplaced, or negligently operated.
Naturally, this includes ensuring that general theft prevention measures, such as installing fences and security systems, storing equipment in a safe location, or training employees on security practices, are in place.
Additionally, managers can utilize equipment tags and software to automate the tracking of equipment users and locations, allowing them to significantly enhance the security of their tools and equipment.
To illustrate how this can be achieved, we’ll use our equipment management software, GoCodes, as an example.
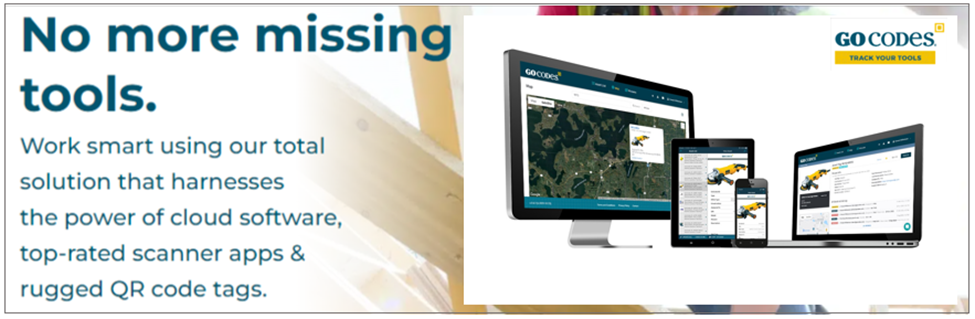
As you can see, GoCodes is cloud-based software that comes with a built-in scanner app, which is downloaded to mobile devices you already use, such as company-owned or workers’ phones and tablets.
It also comes with customizable, rugged QR code labels or tags that are attached to equipment and tools to be tracked.
When these QR tags are connected to their digital counterparts (each equipment’s info page) in the software’s database, the tracking system is ready to go, instantly enhancing the security of tagged equipment.
For one, now workers can be instructed to scan the equipment and tools when taking them from the toolroom or equipment yard and to scan them again when returning them.
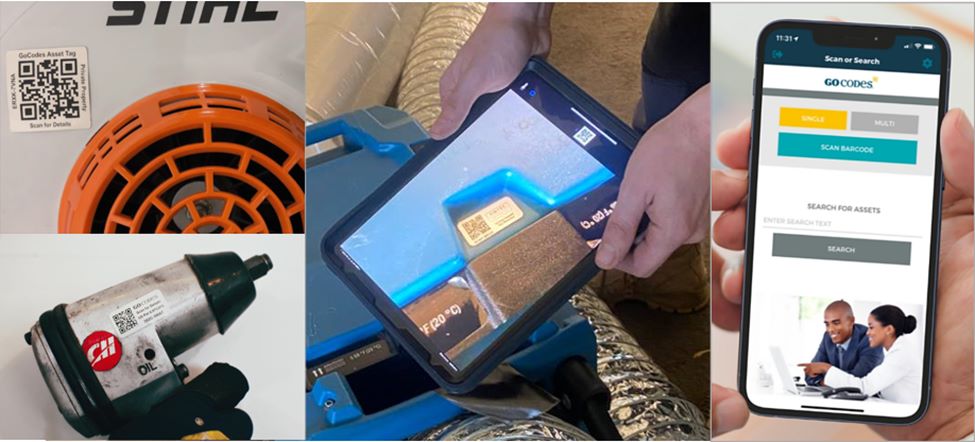
The fact that the software keeps a detailed check-in/out log (and workers are aware of it) typically has an immediate effect of minimizing cases of internal theft, misplacement, and negligent operation.
So, this automated check-in/check-out system acts as a preventive anti-theft and negligence measure and also gives you a clear chain of custody if equipment is damaged, lost, or suspected stolen.
Equally importantly, every time a QR code is scanned (using a smartphone or tablet with the GoCodes app installed), the software will automatically record the GPS location of the scanned equipment and show it on a map.
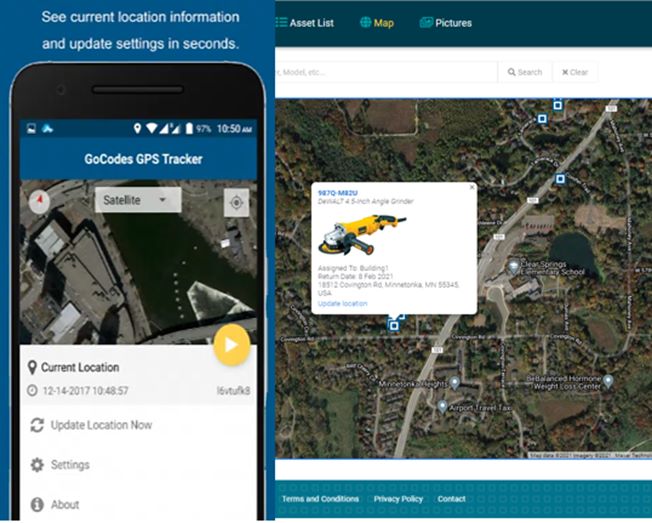
This scan-based GPS tracking enables workers and managers not only to swiftly locate specific tools or machinery when they need them but also when they’re lost or stolen.
For instance, the last-scanned location captured by the software can help you locate tools forgotten on the last job site or, if they’re not found, start your investigation from there.
Concurrently, tamper-resistant QR tags act as proof of ownership, making reselling harder and aiding in the identification of found equipment.
Overall, minimizing theft and negligence is a key practice for ensuring the company’s productivity and cost-efficiency, and managers can implement additional theft prevention measures by leveraging software to track equipment users and locations.
Have an Inventory of Spare Parts
Since equipment requires regular maintenance and may break down unexpectedly, equipment managers should ensure service technicians have everything they need to do their job efficiently.
Therefore, it’s wise to keep essential spare parts, accessories, and other consumable supplies needed for maintenance and repairs on hand, and also keep track of the inventory levels to ensure they’re restocked on time.
Again, the processes involved in inventory control can be digitized and streamlined by equipment management software.
In this setup, QR code labels are attached to containers with spare parts, and the initial number of items is recorded in the software.
From there, when taking or restocking spare parts, users can scan the QR code to note how many they’ve taken or put in.
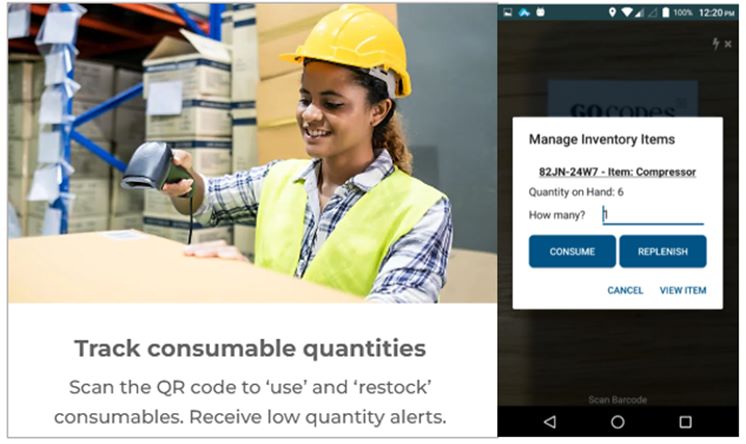
Moreover, equipment managers can define the desired minimum number of items in that container, and the software will send them a low-quantity alert when that number is reached.
That way, spare parts—and other consumable supplies—can be restocked on time, ensuring that technicians and other workers have what they need for efficient maintenance and prompt solving of issues.
To recap, having an inventory of spare parts is another best practice that equipment managers can streamline with the help of software.
Stay Current with Safety Regulations
As the construction industry is subject to many safety regulations and industry standards concerning the safe operation of equipment and tools, managers should stay current with them to ensure a safe working environment and the company’s compliance with legal requirements.
To stay abreast of safety regulations, managers should regularly review updates from relevant safety authorities, such as the U.S. Occupational Safety and Health Administration (OSHA).
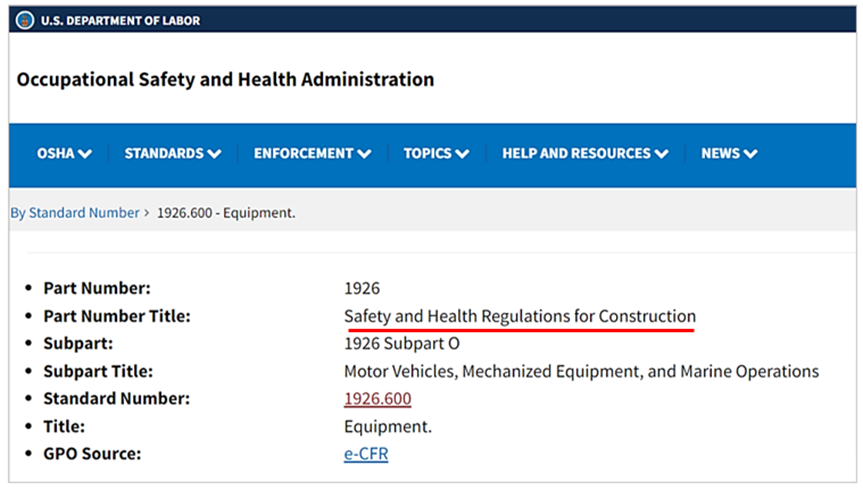
Equipment managers should also:
- conduct regular safety meetings and audits,
- provide ongoing safety training for equipment operators,
- incorporate safety compliance checks into routine inspections, and
- promote a culture of safety among equipment operators.
Again, they can utilize equipment management software to make safety guidelines and checklists available in digital format accessible to all users with a phone or tablet.
Overall, by integrating safety practices into daily operations and staying informed of the latest safety regulations, equipment managers enhance overall jobsite safety and efficiency and help keep their company compliant with legal standards.
Conclusion
To summarize, by following these best practices, equipment managers enable construction companies to optimize equipment procurement, allocation, maintenance, and utilization while preventing theft and ensuring workplace safety and regulatory compliance.
The key to seamlessly implementing these practices lies in, as discussed, leveraging an easy-to-use and affordable equipment management software to digitize and streamline processes and, by doing so, minimize costs and maximize productivity.