Since a construction company’s productivity is only as good as its equipment, regular inspections are integral to maintaining optimal equipment efficiency, safety, and longevity.
Given the vast array of construction equipment types and models that need to be inspected at varying intervals, it’s easy to overlook crucial inspection items that might prevent equipment breakdowns and project delays.
That’s where checklists come in.
In this comprehensive guide, we’ll cover the ins and outs of equipment inspection checklists, ensuring your inspections are thorough, streamlined, and consistent across your company’s operations.
In this article...
Why You Need an Equipment Inspection Checklist
Since any checklist is essentially a list of items that need to be ticked off (i.e., tasks that need to be done), the answer to why inspection checklists are so helpful lies in human memory and attention span limitations.
In other words, operators and service technicians need to inspect different, usually complex, equipment by checking a number of things (breaks, lights, fluid levels, attachment points, etc.).
To illustrate this abundance of inspection items, here’s a part of a scissor lift inspection checklist.
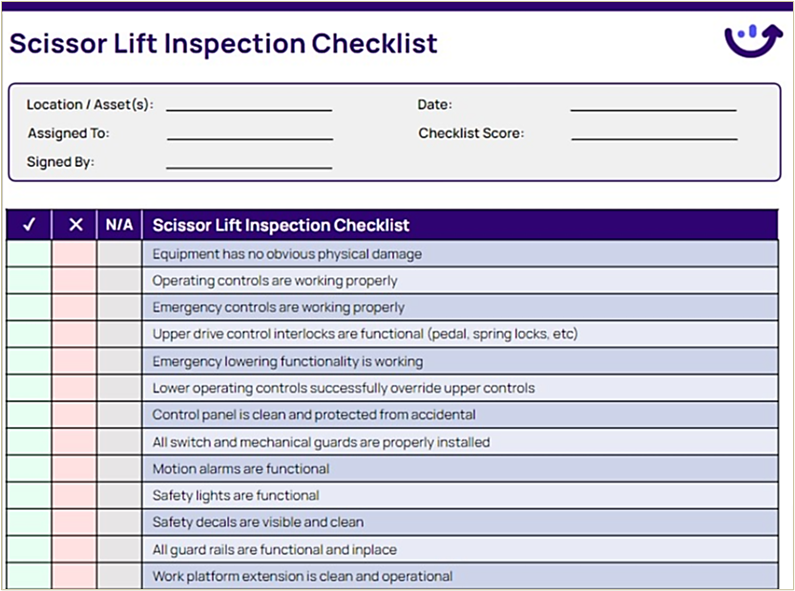
As it’s unlikely operators and technicians have a photographic memory, they can’t be expected to remember all the checks they need to do, let alone the order in which they should do them (when that’s relevant for proper inspection).
Therefore, well-designed, clear, and easily accessible checklists ensure that equipment inspections are thoroughly yet quickly performed while helping uncover hidden problems.
Let’s take a closer look at each of these advantages.
Ensures Inspections Are Done Right
As said, there are simply too many general and equipment-specific maintenance and safety inspection tasks for operators and service technicians to remember.
Moreover, when operators repeatedly use the same equipment type/model, it’s human nature to become overconfident and rush through, for instance, daily pre-use or post-use inspections.
To address these issues, checklists provide consistency, reminding operators of every essential inspection task they need to do.
Here’s an example of a pre-operation telehandler daily inspection checklist that clearly states what checks should be performed, how, and in what order (as highlighted).
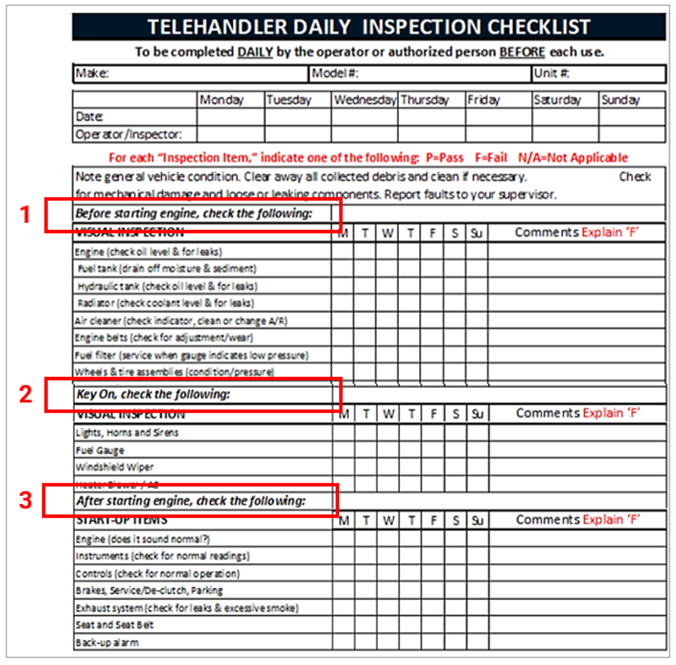
This clear list of inspection tasks, supported by straightforward instructions on performing them and recording findings, ensures that nothing will be overlooked or rushed through, at least in theory.
Naturally, although technicians usually service many different construction equipment types and models, they’re not exempt from becoming too relaxed or complacent when performing preventive maintenance inspections.
In such cases, more comprehensive and technical checklists assist technicians in going through all the inspection items and following prescribed safety (lockout) and maintenance procedures.
Therefore, whether they’re meant for the operators or maintenance technicians, checklists help ensure that the inspections are done right.
Speeds up Inspections
Another benefit of checklists is that they enable operators and technicians to complete their inspections faster, especially when they are digital and can be easily accessed from any device.
Of course, even pen-and-paper inspection checklists will accelerate inspections, but the accessibility and convenience of digital checklists further simplify and speed up the process.
More precisely, paper checklists require workers to bring/find them on-site, fill them out, and submit them.
Then, the administrative staff needs to input data manually, i.e., digitize the info in checklists for record-keeping and data analysis purposes.
Conversely, an operator or technician can, for example, scan a QR code attached to the equipment and easily access the digital checklist that will automatically capture the entered data.
You can see the described process here.
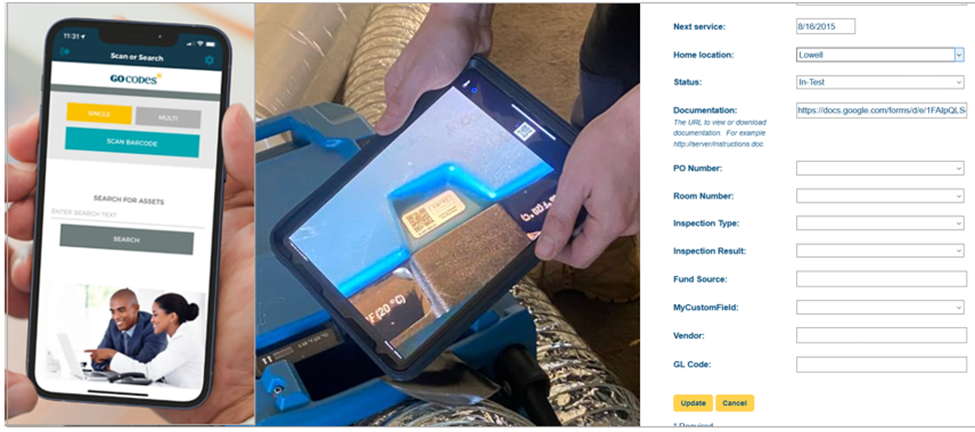
For example, our asset-tracking app, GoCodes, utilizes QR code tags affixed to equipment and tools as fast and convenient gateways to the equipment’s info page, from where workers can easily access and complete the relevant checklist using their smartphone or tablet.
Regardless of their format, checklists also minimize the time and supervision required for new operators and technicians to start doing inspections independently.
Additionally, guidance notes in checklists can accelerate the process by providing less experienced workers with explanations and instructions on how to record their inspection findings.
To recap, checklists speed up equipment inspections, especially when they’re digital, i.e., easily accessed and filled out using any internet-connected device.
Uncovers Hidden Problems
Inspection checklists are not just about ticking off boxes; they’re essential for uncovering hidden problems in construction equipment.
In doing so, the critical factor is consistency, i.e., all equipment operators regularly perform inspections using the same checklist.
For instance, while an operator is performing a routine bulldozer inspection, one item on their checklist instructs them to check the machine’s hydraulic fluid level.
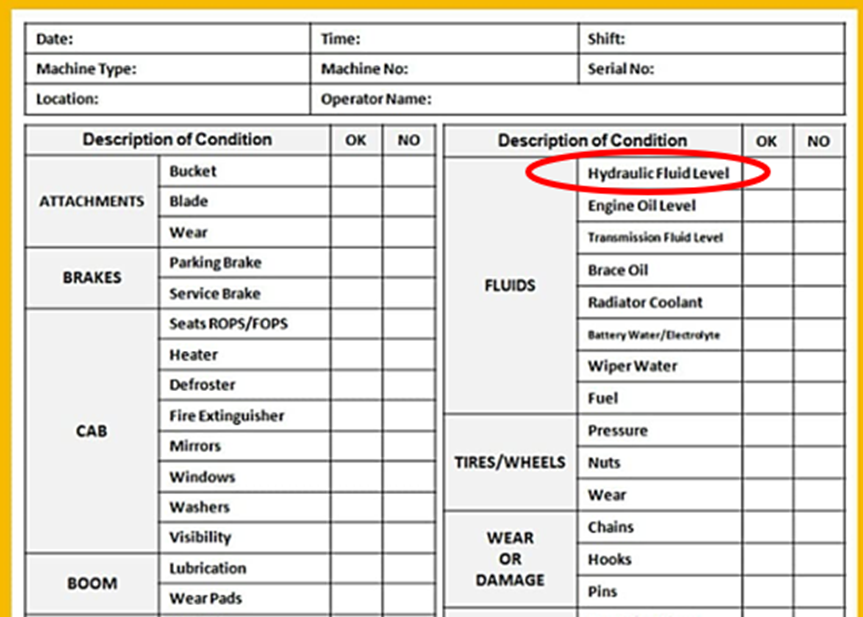
Upon inspection, they notice that the fluid level is significantly lower than specified in the checklist, which prompts them to investigate further and ultimately leads to discovering a leaking hose.
Without a checklist, this issue might’ve not been immediately detected because the bulldozer was fully operational, showing no other signs of malfunction.
Naturally, replacing the damaged hose promptly prevents more extensive damage, costly repairs, and potential safety hazards.
Therefore, checklists also act as a proactive tool, helping operators and technicians identify hidden problems early, saving both time and resources in the long run.
Now that it’s clear why you need inspection checklists, let’s see what types of equipment should have them.
What Types of Equipment Should Be in a Checklist
Basically, any equipment type and model that should be regularly inspected to ensure it’s safe to operate and functioning correctly should have its checklist.
Therefore, although checklists are typically associated with heavy machinery, any piece of equipment, device, or tool subject to inspection can have a checklist, meaning the list of potential equipment types is practically endless.
To illustrate, here are only a few equipment types that need an inspection checklist.
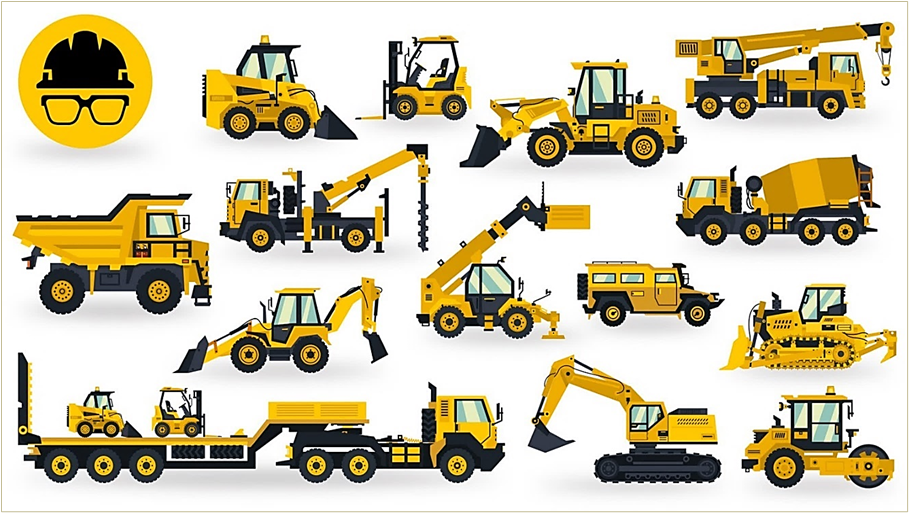
Moreover, as mentioned, one piece of equipment can have multiple checklists (e.g., operator’s pre-use and after-use inspections, maintenance technician’s inspections).
There might even be distinct checklists for the same equipment type and model, such as one designed for outdoor usage (checking for dust, debris, and weather effects) and another tailored for indoor use.
Long story short, the question is not what types of equipment should have a checklist but rather what types of simple tools and devices (if any) should not.
What to Include in an Inspection Checklist
As evident by now, a checklist should include all the equipment components, systems, and safety features that require inspection.
Naturally, these inspection items should be specific to the equipment type/model and its critical functions.
But, before consulting the manufacturer’s documentation to identify such tasks (covered in the next section), you should ensure that each checklist provides clear equipment identification, including its type, model, and any unique identifiers, like its serial number.
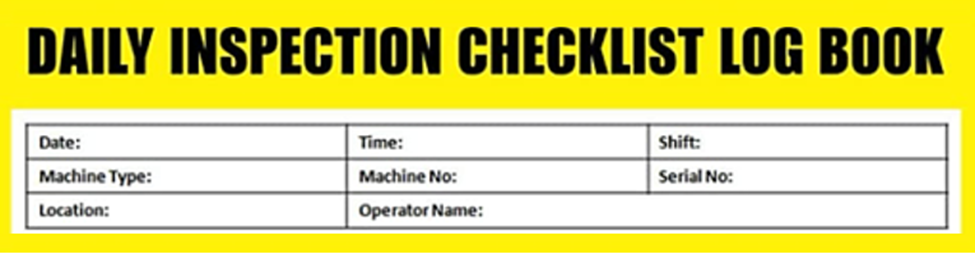
This should be followed by a list of the inspection items recommended by the equipment manufacturer (and your maintenance team).
Each item should have a checkpoint, i.e., fields/spaces/options to indicate whether the item passed, failed, or requires further action.
In the below example, “OK” means that the item passed inspection, “AR” means that further action is required (maintenance, repairs, further investigation), and “NA” implies that the item is not applicable to the specific equipment or situation.
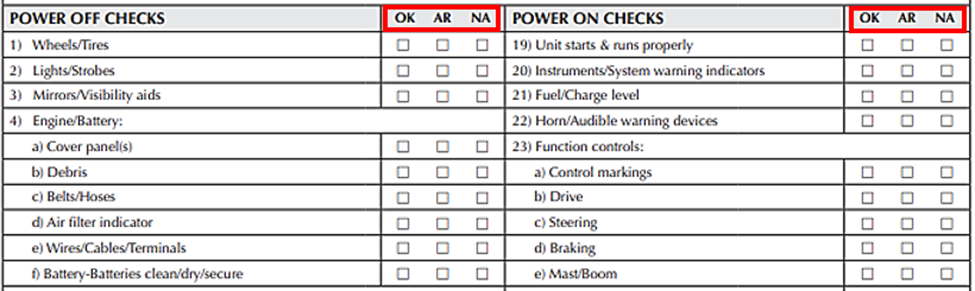
When checklists are digital, most software solutions will enable operators and technicians to attach photos or even videos for visual documentation.
Other “must-have” checklist elements include:
- a specific sequence for doing inspection checks (if required)
- instructions on how to perform each inspection task
- notes for additional observations, comments, and details
- date and signature
In conclusion, a well-structured equipment inspection checklist should include clear equipment identification, specific inspection items and checkpoint fields, and additional elements we just covered.
Now that it’s clear what checklists should include, let’s see how you can create them.
How to Create an Equipment Inspections Checklist
Creating simple yet effective equipment inspection checklists is a process that requires a team effort.
It starts with gathering the existing equipment documentation, such as the manufacturer’s operation and maintenance (O&M) manual, then consulting your maintenance team and organizing the required equipment information into a checklist.
Let’s look at these three steps more closely.
Gather Existing Equipment Documentation
Whether you’re creating an equipment inspection checklist from scratch or want to improve the ones you already have, the first step is to collect all the existing equipment documentation.
In the case of brand-new equipment, this would be the original manufacturer’s technical documentation (O&M manuals, instructions, warranty, etc.).
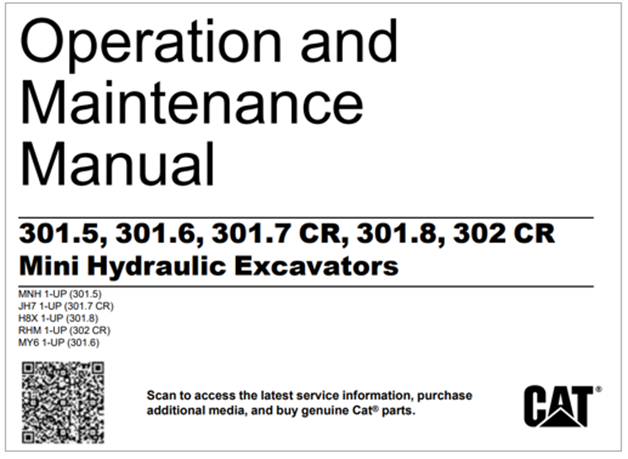
For used equipment you just bought, this would include the above original documentation, as well as the equipment’s maintenance and inspection records and other relevant usage details, such as the number of operating hours.
Finally, for your equipment, the existing documentation would include all the above and any other data you have on it (i.e., your own maintenance, repair, and usage history).
In any case, the manufacturer’s instructions should serve as your starting point for determining what inspections should be performed, when and how, and what items should each inspection checklist include.
When deciding on the type and frequency of inspections, adhering to the manufacturer’s recommended inspection items and intervals is essential for keeping the warranty valid.
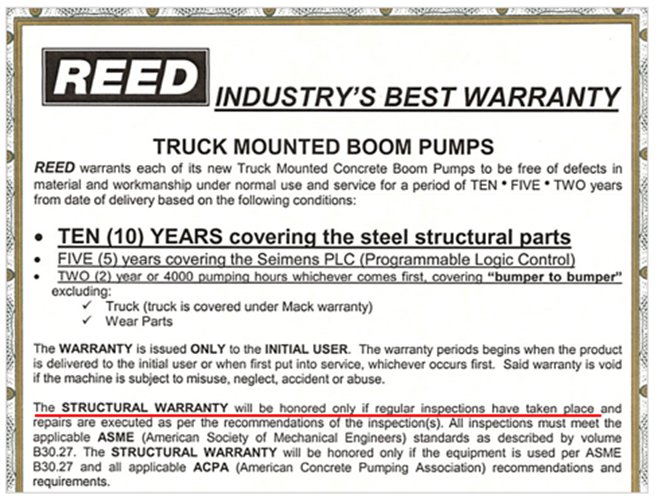
From there, you can use the data from other equipment documentation to refine your checklists.
You can adjust them in line with factors like the equipment’s condition, operating environment, local regulations, and—as we’ll see next—your maintenance team’s expertise and experience.
Speak With Maintenance Technicians
The next step when creating checklists is consulting with those who know the equipment best—maintenance technicians.
Since they’re the ones maintaining the equipment, they might provide helpful insights into what operators should look for when performing a specific inspection task on their checklist.
For instance, an experienced technician might know that hydraulic hose connections on a specific excavator model are especially prone to wear and tear near high-stress areas.
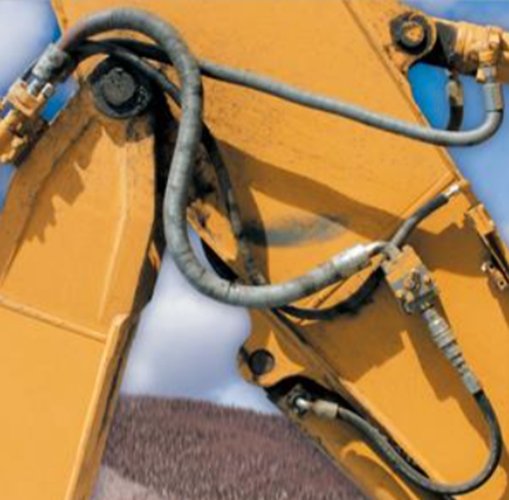
To ensure that operators regularly check for that specific issue, you can add a particular inspection item and instructions to that excavator’s checklist.
Overall, getting equipment-specific information arising from your maintenance team’s know-how and experience can help you enhance your checklists with practical instructions that lead to early detection of any equipment issues.
Organize Equipment Information Into a Checklist
Now that you have all the necessary elements for your checklist, it’s time to organize it in a logical and practical way.
In other words, if the sequence of actions during inspection is important, the inspection items should be ordered accordingly, as some of our previous examples show.
Even if the order is not essential, the sequence of inspection checks should follow a logical route an operator would take when inspecting equipment (e.g., from front to back or vice versa), like in this example.
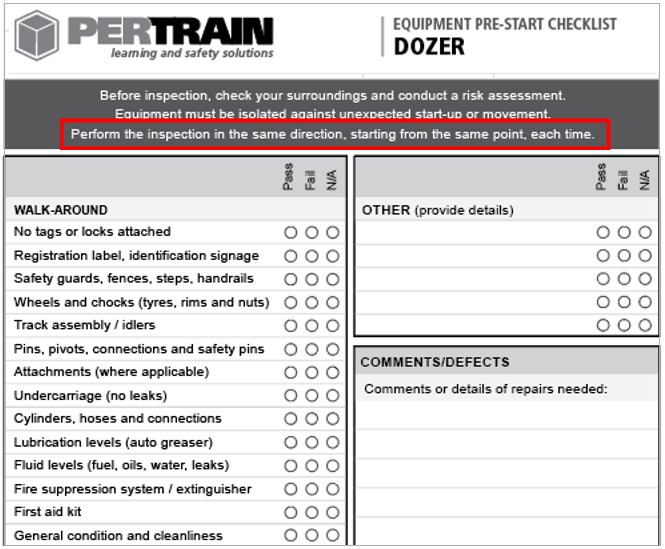
When checklists are ready, it’s best to test them on actual (newer and experienced) operators or technicians who will fill them out.
This will help you determine whether the information in your checklist is ordered logically, detect any unclear inspection items or instructions, and identify potential training gaps.
Lastly, you should decide how checklists will be made available (digital or paper) and how their users will access them (e.g., by scanning a QR code on the equipment).
To sum up, once you have gathered existing equipment documentation and consulted your construction team, the final step is organizing equipment info in a checklist in a logical and clear manner.
Conclusion
Finally, all that’s left is to remind you equipment inspection checklists are crucial for ensuring detailed, streamlined, and consistent inspections across your construction company.
We hope this guide will help you create well-designed and user-friendly checklists, as well as establish a (digital) system for efficiently tracking and managing them, helping your company improve the safety and efficiency of equipment while extending its lifespan.