Construction equipment costs extend well beyond the purchase price of a new machine.
Any industry professional knows machinery expenses are much more complex than that.
If it were simply about the point of purchase, meticulous planning and the constant struggle to adhere to a budget during each and every project wouldn’t be necessary.
In this article, therefore, we’ll take a look into the intricacies of equipment costs, shedding light on six cost centers that every project manager, contractor, or stakeholder should carefully consider.
Let’s get started.
In this article...
Equipment Repairs
Heavy equipment is a construction industry staple and without it, meeting project deadlines would be nearly impossible.
That’s why, when a machine breaks down unexpectedly, it’s always a huge blow not just operationally, but financially as well.
Repairs come with a hefty price tag, potentially reaching thousands of dollars annually, particularly when you take a deeper look into these expenses and realize they go beyond just paying for spare parts and labor.
Those are, in fact, only the tip of the proverbial iceberg.
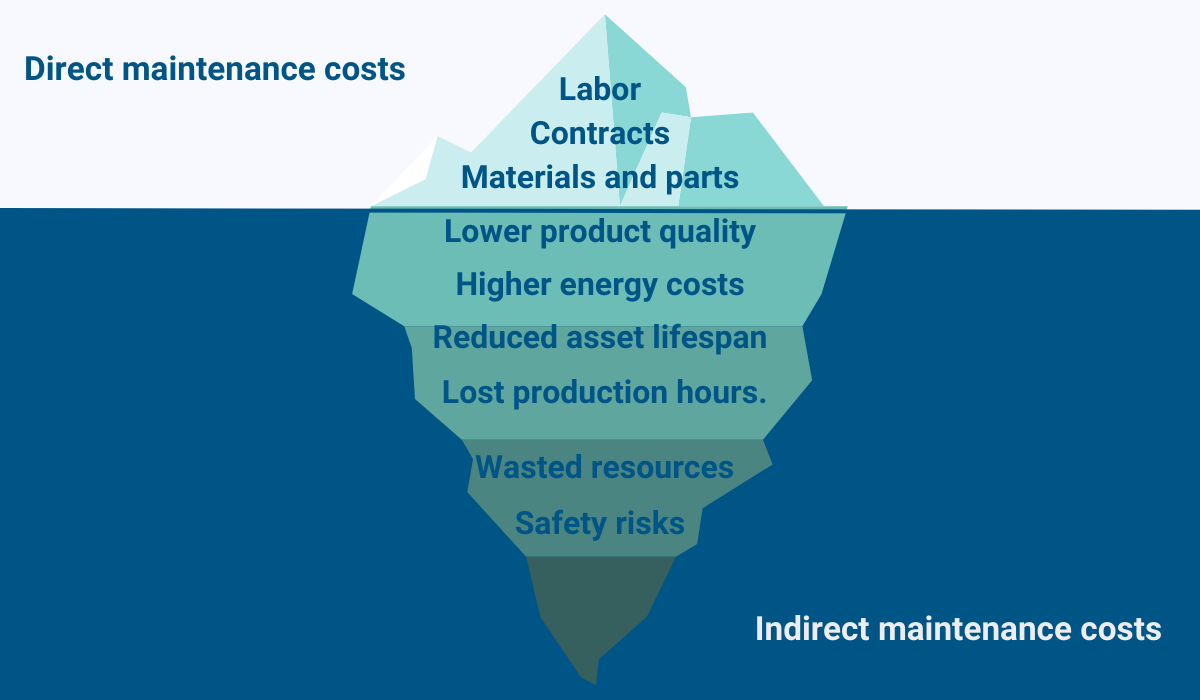
Numerous effects of sudden asset failure, such as compromised work quality, reduced asset lifespan, and project delays, are not immediately apparent, but create additional expenses in the long run, affecting your bottom line.
And, naturally, the bigger the problem, the bigger the repair costs.
They can be mitigated, though, but an efficient maintenance strategy is necessary.
If you, too, are still approaching machine servicing reactively, and fixing equipment only when it’s already broken, consider conducting frequent preemptive check-ups and calibrations instead.
Putting in the work now will prevent major problems in the future.
To simplify this process and ensure your team sticks to regular inspections, use the GoCodes’ Tasks feature, which enables you to set up service tasks and assign them to the employees.
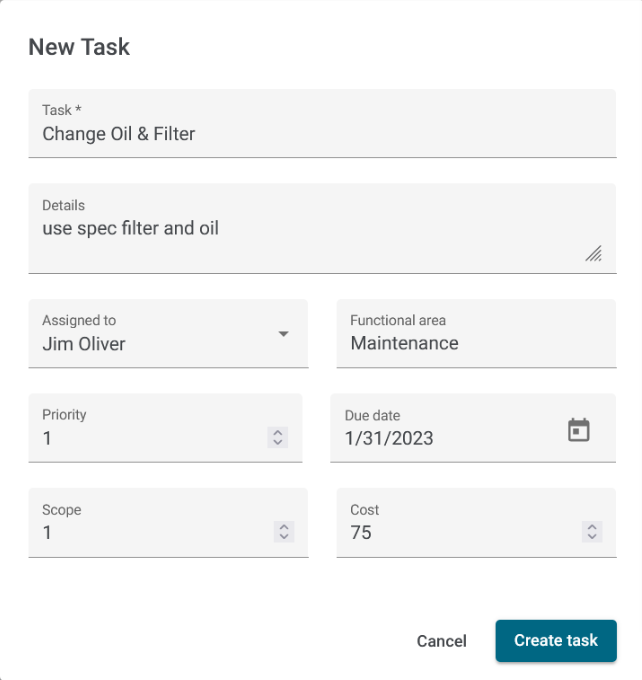
It also allows you to monitor the progress of the assignments, as well as edit, copy, delete, or even reassign them.
Moreover, the GoCodes App sends out email reminders the day before scheduled service, ensuring the workers are always prepared for and aware of their responsibilities.
No more excuses for missing that oil change.
At the end of the day, adhering to a maintenance regime doesn’t have to be cumbersome or time-consuming, as many wrongly assume, but it can certainly help streamline your operations and make substantial long-term cost savings.
Repurchasing Equipment
If we were to ask you how many ladders or jackhammers are currently being used for each of your projects, would you know the answer to that question?
More specifically, would you be able to confidently locate this information in your asset register and vouch for its accuracy?
If you’re still using manual asset tracking tools like spreadsheets, it’s likely the answer to those questions would be a resounding no.
The problem with these outdated methods is that they are highly susceptible to human error, time-consuming, and cannot be updated on the go, which means they produce inaccurate, incomplete, and untimely data.
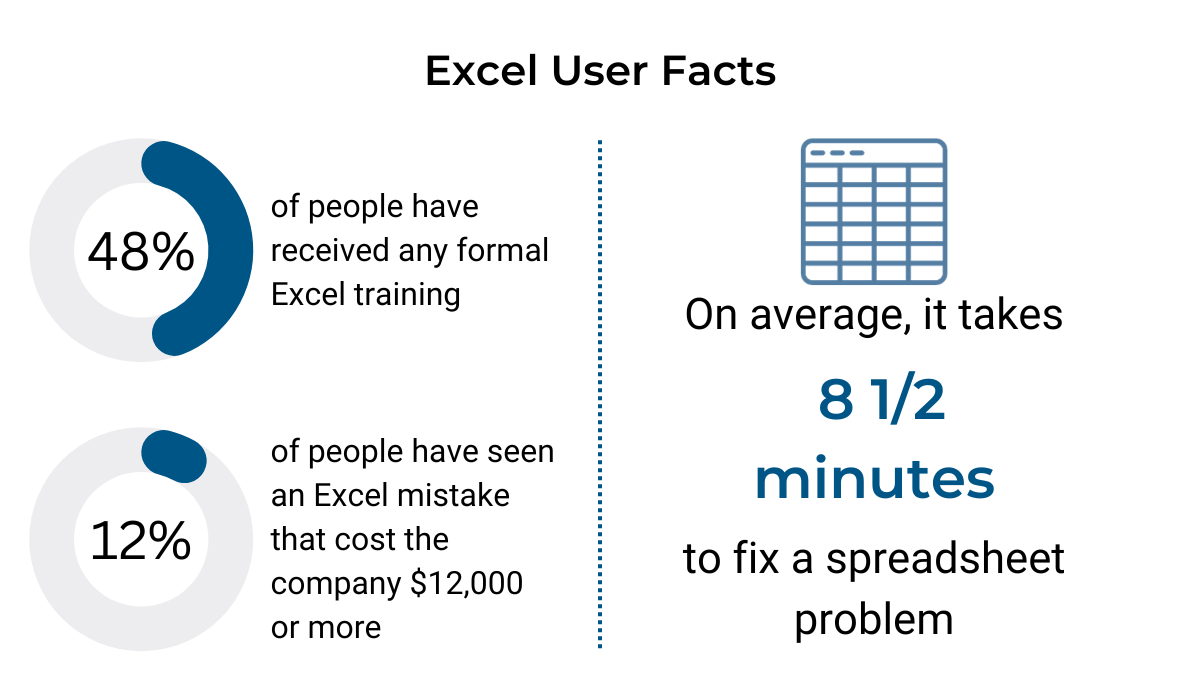
Consequently, managing assets with spreadsheets often directly translates to the inability to detect missing or even surplus tools, leading to unnecessary purchases, and diverting funds from more essential areas.
Consider the following scenario: a demolition saw disappears, prompting a hasty replacement purchase.
Over time, the new saws also vanish, yet again causing repeated acquisitions, while the cycle of purchasing assets only to lose them continues, draining resources.
If this rings a bell, maybe it’s time to switch to an automated equipment management system.
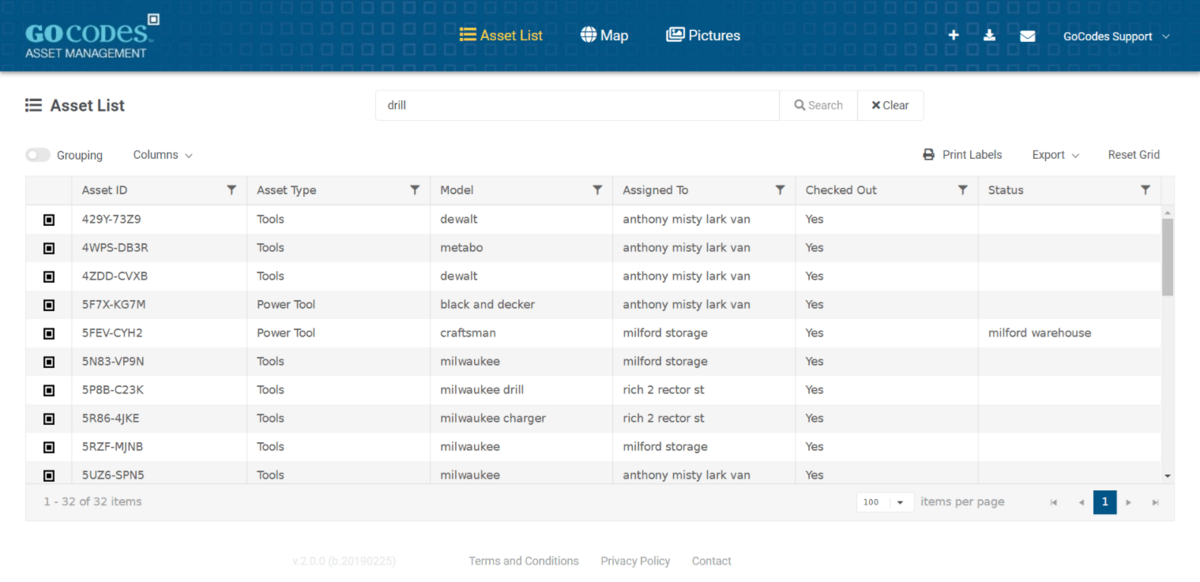
This centralized, cloud-based solution maintains an accurate and continually updated asset list, offering comprehensive details about your tools and machinery, including quantities, locations, warranty terms, and more.
With such a system in place, you gain the certainty of knowing exactly what you have, who’s responsible for it, and what you need, making wasteful spending a thing of the past.
Equipment Hoarding
Working in construction, you’ve probably had to occasionally deal with the issue of equipment hoarding.
Superintendents, whether knowingly or not, often find themselves holding onto machinery, creating a situation that sometimes evolves into a significant financial drain over time.
Just picture an idle excavator, with a monthly rental fee of, say $6,500, sitting unused for extended periods at a job site.
Not only does this result in ongoing rental expenses for that idle piece of equipment, but it also necessitates the additional cost of renting another excavator for a different project where it’s actually needed.
Obviously, the best strategy here would be to move the excavator from job site A to job site B, but without a system that provides insight into equipment utilization, such decision-making becomes challenging.
How can you know the excavator should be moved when you don’t even know it’s not being used?
However, this problem is easily remedied with QR code-based asset management systems.
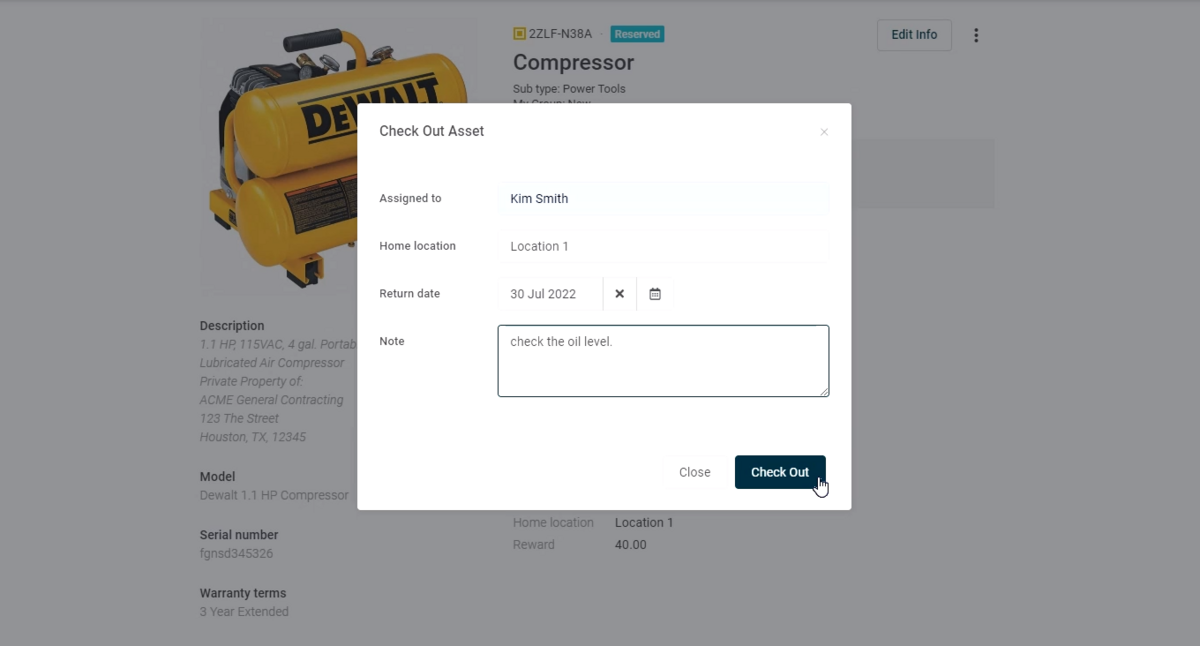
Every time a worker needs to use a tool or a machine, he or she scans the QR code asset label with a smartphone to check the asset out.
The process is the same when returning equipment.
Every time this is done, the asset’s user and location are updated, generating a detailed checkout log over time, shedding light on when, how often, and by whom your assets are used, all on a per-project basis.
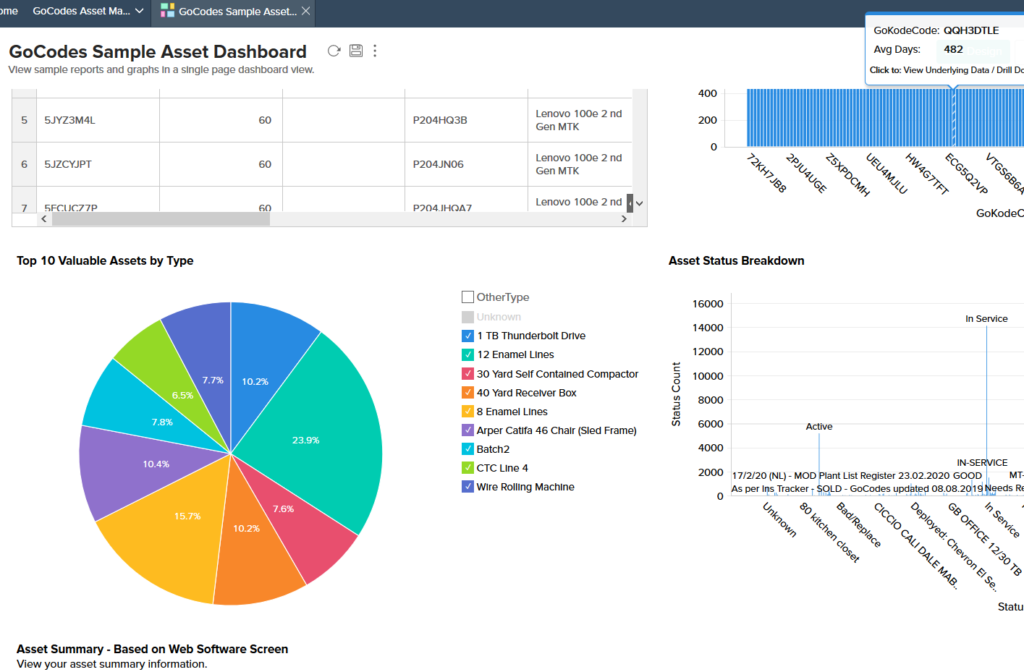
Then, with a little help from a good reporting feature, you can generate reports that will automatically total the cost of each project as well as flag equipment that might be due for maintenance, based on the equipment utilization rates.
This approach ensures that your assets are strategically allocated and utilized efficiently, guaranteeing optimal returns on your investment.
Idle Equipment
In fact, the importance of effective equipment allocation and utilization cannot be overstated when it comes to a company’s financial health.
Besides the obvious impact on rental costs, there’s another silent (yet damaging) profitability killer: the idling machine engine.
Fleet vehicles idling during traffic stops, loading and unloading procedures, or even during a driver’s phone call may seem harmless enough when occasional, but when idle time becomes a substantial portion of total running hours, it raises red flags.
Cat Simulators dove a bit deeper into the financial repercussions of this issue.
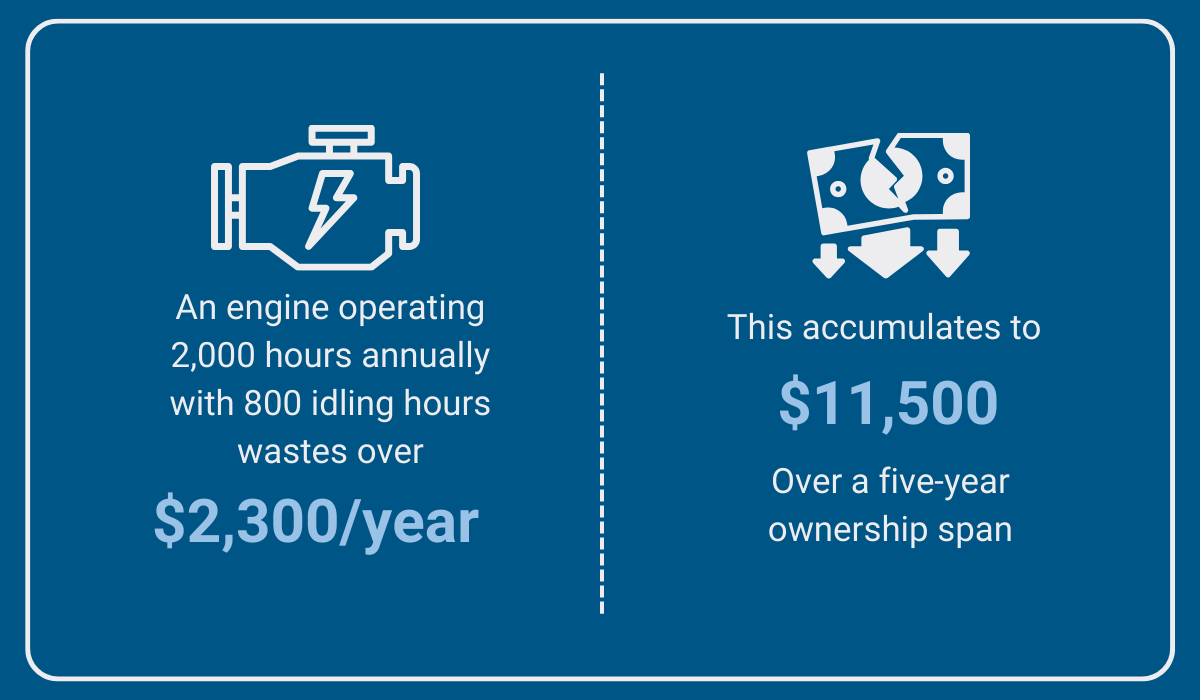
It turns out that, if a machine’s engine with 2,000 annual running hours, idles for 40% of that time (800 hours), it translates to a staggering waste of over $2,300 per year.
Over a five-year ownership span, this accumulates to $11,500.
And here we’re not just talking about fuel costs but also:
- Compromised component life
- Faster wear of tier 4 technologies
- Unplanned downtime
- Used warranty hours
- Lower resale value
To safeguard your bottom line, closely tracking equipment’s operating hours and fuel consumption is not just a good practice—it’s a must.
Through this vigilant monitoring, you might discover hidden expenses that were previously flying under the radar.
Equipment Hauling
Yes, the equipment is an essential part of your business operations, but let’s face it: transporting it to and from a job site can be a logistical nightmare.
And this is no cheap endeavor, either.
Most heavy equipment haulers set a per-mile rate, averaging at $3 per mile within a 500-mile radius and $5 per mile for longer distances.
Below you can see some examples of heavy equipment shipping prices provided by A-1 Auto Transport.
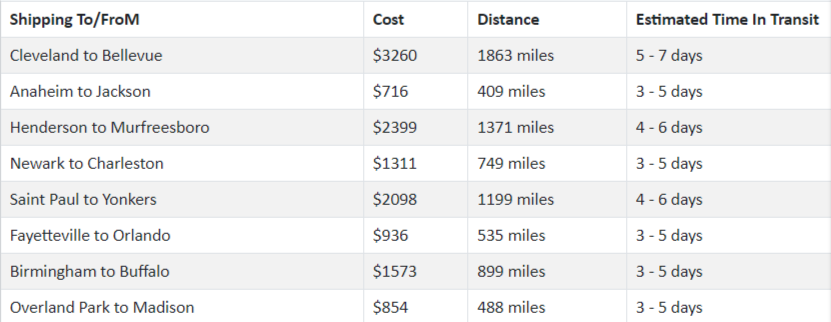
Keep in mind, though, that these figures apply to one-way trips; transporting machinery back and forth will increase the expenses.
In fact, on top of this base rate, several other factors will determine the overall cost of equipment haul:
- Height/width/length/weight of the machine
- Whether or not the piece of equipment is overweight or oversized
- Traveled distance
- In some cases, even the congestion of the area is factored in
In any case, when the need for equipment hauling arises, it’s best to take your time and do proper research on companies that offer these services.
Compare the prices and even reach out for a quote if necessary.
Don’t hesitate to ask around and look at the reviews, too. This will give you insight into the company’s reputation and the quality of its work.
After all, a lower price tag won’t do you much good if the equipment gets damaged along the way, so prioritize due diligence to ensure a seamless and secure transportation process for your assets.
Fleet Accidents
Every time your drivers take the wheel of a company-owned vehicle, the potential for serious financial repercussions looms over your organization.
However, the aftermath of a fleet accident extends far beyond the immediate repair costs.
According to OSHA, motor vehicle accidents inflict an annual toll of approximately $60 billion on employers, factoring in medical and legal expenses, property damage, and lost productivity.
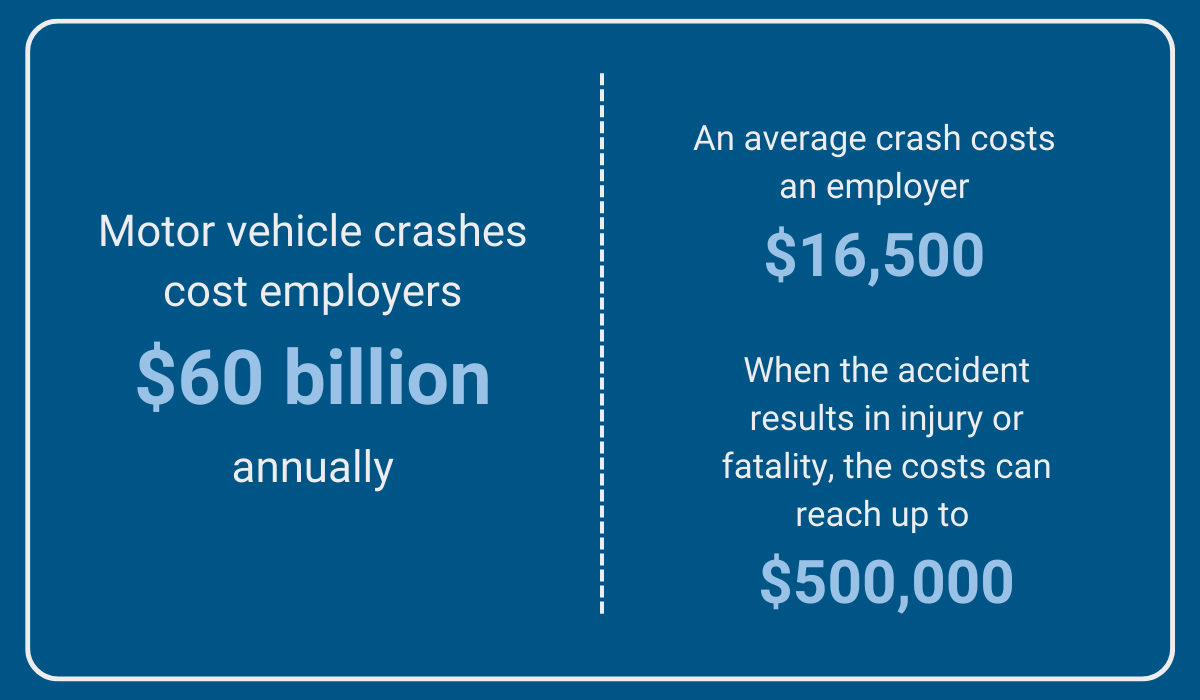
Moreover, the average crash, which sets companies back around $16,500, takes a sharp upward turn when it involves injury or fatality.
But how often do these incidents really occur?
The disheartening reality, as revealed by the 2021 Census of Fatal Occupational Injuries, is that transportation incidents rank as the most frequent occupational fatal events, with workers in transportation or material moving occupations experiencing the highest fatality rates across all sectors.
What’s even more sobering is that these accidents are entirely preventable through the implementation of efficient driver safety programs or technology that monitors driver behavior, logs routes, and ensures optimal vehicle conditions.
It’s vital, therefore, to explore and invest in such tools to protect your team and mitigate the human and financial costs associated with these avoidable accidents.
Conclusion
All in all, adopting a thorough approach to budgeting that accounts for both direct and indirect equipment costs is essential for the financial success of a business.
Some of the cost-centers outlined in this article may not be apparent at first but they can still pose a substantial long-term financial drain.
The good news is that by implementing meticulous monitoring and strategic management of your equipment, you can mitigate if not entirely eliminate, these financial challenges, setting the stage for long-term financial sustainability and efficiency.