Inventory management is a crucial part of any business. It’s a complex process that involves inventory acquisition, disposal, maintenance, and storage.
In other words, inventory control ensures you have just the right amount of tools and equipment for timely and effective project completion.
Not only that, but implementing a proper inventory control system can be quite cost-effective in the long run. Keep on reading to find out exactly how it can save your company money.
In this article...
Avoids Inventory Overstocks
When it comes to inventory, there is such a thing as too much.
If you work in construction, you know there are a lot of materials and tools you need to keep track of, and that without them, you’d never be able to complete your projects.
Still, the more items you have to handle, the easier it becomes to get bogged down, and soon, you may find yourself in a situation where you have more than you need.
This might seem harmless at first glance.
However, more is not always better. Inventory overstock has many downsides, all of which negatively impact your profitability.
Take a look at some of them in the picture below:
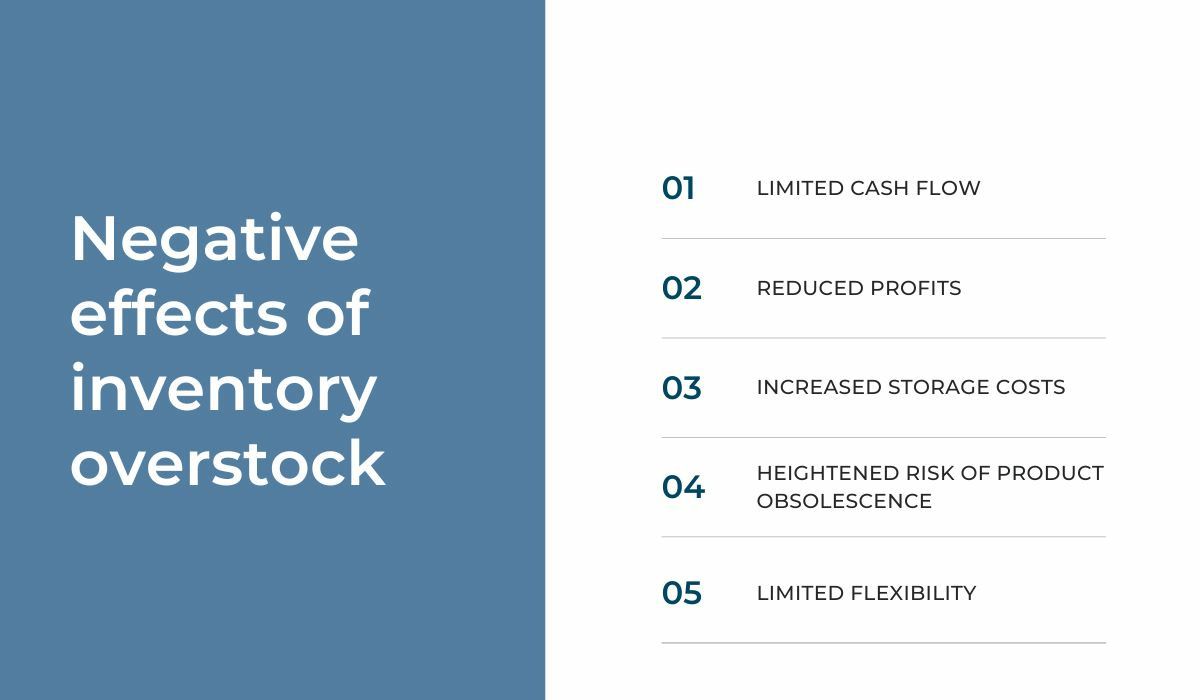
Firstly, having your money tied up in assets you’re never actually going to use can seriously limit your cash flow.
This could eventually put you in a situation where you struggle to pay for various expenses that are an indispensable part of owning a business, such as bills or payroll.
Moreover, having inventory sit in storage unutilized decreases its value over time. Even if you sell it, you’ll have to do it at a significantly lower price.
And let’s not forget storage costs! Inventory overstock directly translates to you losing money paying for storage, instead of making money using those items.
Furthermore, the longer a product stays stored away, the higher the risk of obsolescence, i.e., the chance of some equipment becoming completely unusable increases over time.
Finally, inventory overstock limits your flexibility because the more you spend on something you won’t use to turn a profit, the less you’re able to invest in new machinery, tools, and other equipment that would actually take your business to another level.
Having all this in mind, it’s clear that inventory overstock is a giant profitability killer.
Therefore, be mindful of your needs and implement a proper inventory control system to accurately forecast the right amount of inventory for every project.
This will help you prevent overstocking.
Prevents Inventory Stockouts
On the other hand, not having enough inventory could cost you a lot, too.
Imagine realizing you’re out of certain tools or materials in the middle of a project.
All you can do in a situation like that—besides trying not to panic—is place a last-minute order, probably pay extra for expedited shipping, and wait for your order to arrive, while your paid workers remain idle because they cannot continue with the project due to the lack of resources.
Needless to say, this would cause significant project delays.
And project delays cost a lot.
In fact, a survey has shown that, in the construction industry, delays can balloon the cost of the project to 20% more than the initial estimate.
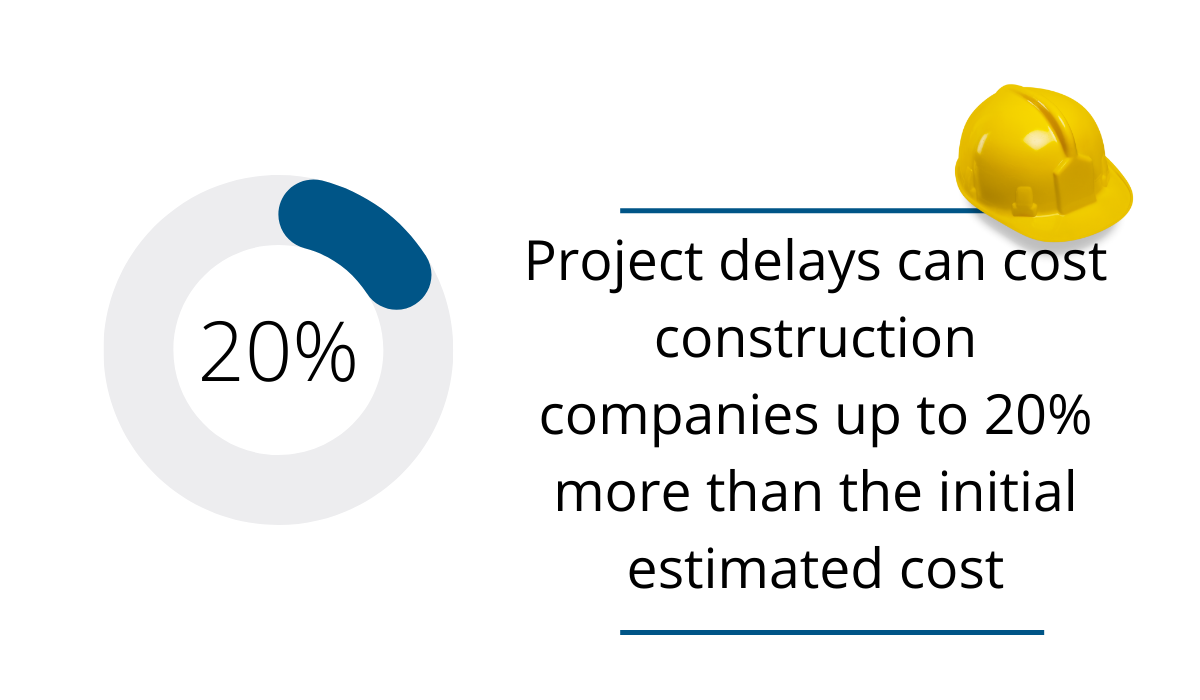
This is certainly not an insignificant amount of money. To avoid such a scenario, work on improving your inventory control.
Successfully tracking your inventory will give you important insights that will help you reduce unnecessary delays due to stockouts.
One thing that can help you with inventory tracking is GoCodes—a cloud-based inventory management software.
GoCodes provides you with all the necessary information about your inventory, such as the types of inventory, its locations, quantities, etc., while also sending you notifications for low inventory quantities.
In fact, it’s perfect for tracking the quantity of stock and consumable items, because it allows you to update the information in seconds.
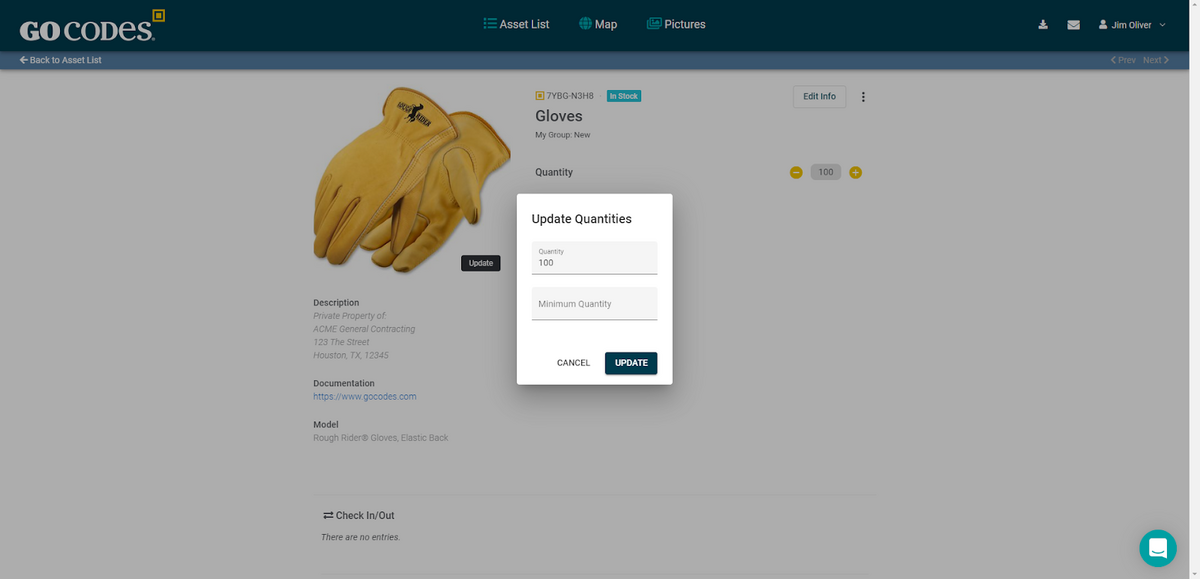
Thanks to the GoCodes app, this data can be updated on the go from your mobile device and it can be accessed by anyone on the team in real time.
All in all, inventory stockout can be quite damaging to your profitability.
Try avoiding last-minute orders and expensive project delays by using an inventory control system that will help you make timely and informed decisions about inventory acquisition.
Identifies Unreliable Suppliers
You may do everything in your power to make your project go smoothly—ordering the right amount of the right inventory at the right time—but even that does not always guarantee everything will go according to plan.
Suppliers play a vital role in the construction industry, and a mistake on their part, such as, for example, a late delivery, or a delivery of wrong materials, can have a domino effect on a project’s success and profitability.
While situations like these are out of your control, their result is your responsibility.
In other words, if a delivery is late, you will be the one that will have to remedy the project delay that will occur because of it.
Therefore, it is up to you to identify the weak links in the supply chain by establishing proper inventory control.
Data gathered through an inventory control system can help you detect and manage risks associated with the supply chain and generally impact your decision-making in a positive way.
For instance, construction managers can, by monitoring different supply performance metrics over time, discover which of their suppliers might be underperforming.
Here are some of the metrics to look into:
- Late deliveries
- Low-quality inventory
- Incorrect amount of inventory
- Wrong type of inventory
In conclusion, your suppliers have the power to make or break your project.
More specifically, partnering with someone unreliable can negatively affect your business operations by causing delays or delivering lower-quality materials.
Therefore, track your suppliers’ performance and once you establish who the weaker links are, don’t be afraid to have some tough conversations and ultimately, if needed, make some changes.
Minimizes Inventory Shrinkage
To put it simply, inventory shrinkage is the difference between recorded and actual inventory.
This discrepancy usually stems from inventory being misplaced, lost, or stolen.
Naturally, this is a common problem in every industry—the construction industry included—and it can be pretty costly.
There are a lot of causes of inventory shrinkage, all of which are rooted in poor inventory management.
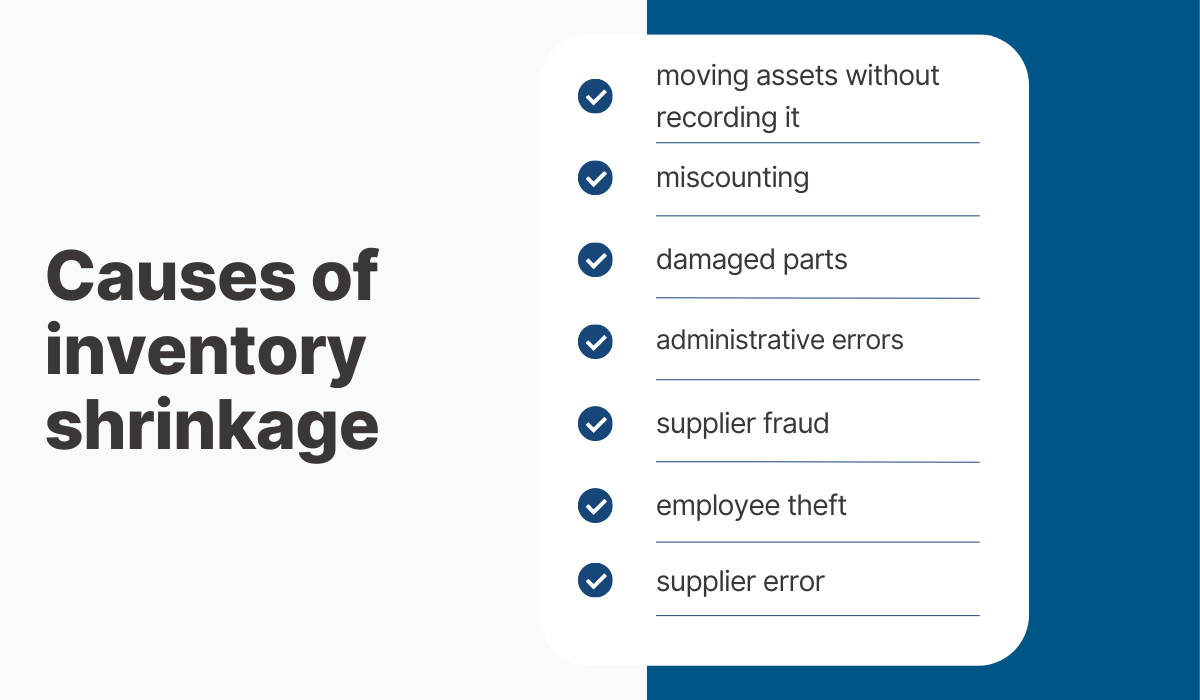
Determining your inventory shrinkage is very simple: just count your inventory, calculate its value, and divide it by the value recorded in the accounting books.
For instance, if, according to the accounting books, your company owns $1.000 000 of inventory—that’s your recorded inventory.
However, after counting your actual inventory, you might discover that the worth of what you currently have is closer to $950.000.
That would mean that, in this case, the amount of inventory shrinkage is $50.000, or 5% (50.000/1.000 000 x 100).
There’s no denying that inventory shrinkage is quite an expensive problem, and the best way to solve this problem is by using an inventory control system.
The benefits of a proper inventory management system mitigate the most common causes of inventory shrinkage.
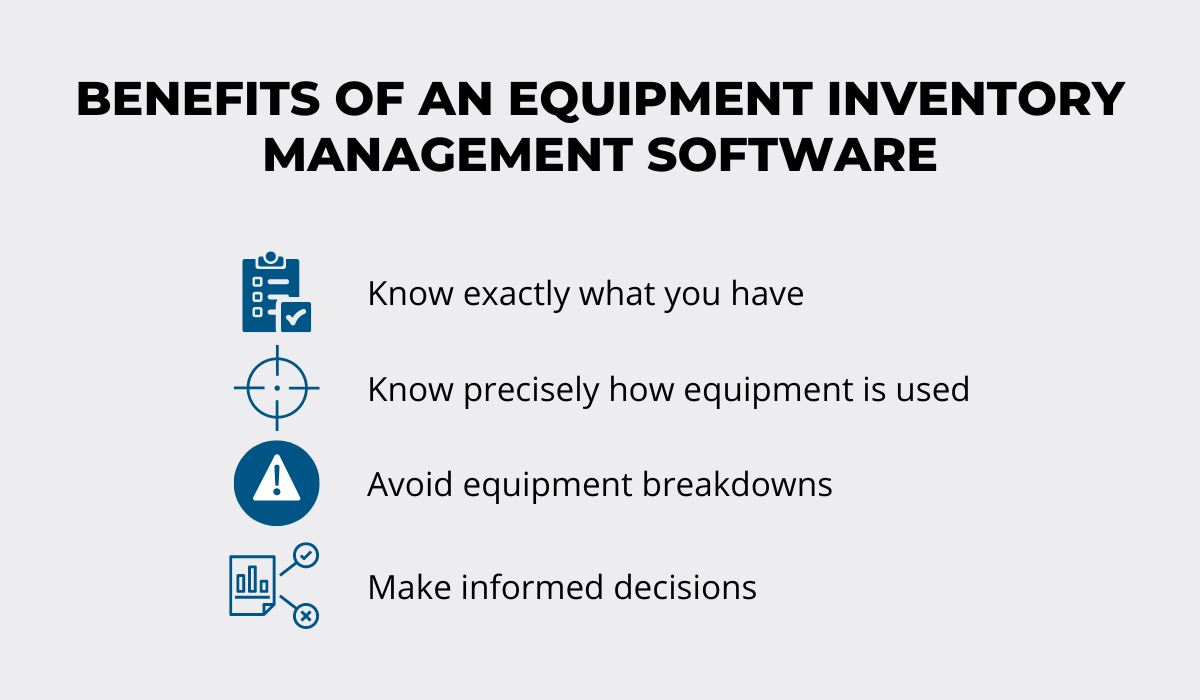
Inventory control or inventory management software allows you to track your inventory locations and quantities, thus minimizing the chances of inventory loss or theft.
Moreover, by monitoring your inventory, you’ll be able to schedule preventive maintenance and avoid equipment parts getting damaged, prolonging the lifespan of your equipment.
Overall, a high-quality inventory control system will let you know when, where, and how your inventory is used at all times and minimize costly inventory shrinkage.
Knowing where an asset is, after all, increases accountability among the team members, reduces chances of theft, and, most importantly, saves you money.
Conclusion
The mismanagement of your inventory can turn out to be pretty pricey in the long run. However, these costs are quite unnecessary and avoidable.
Mistakes such as ordering materials in inadequate amounts can easily be prevented by establishing a proper inventory control system.
Not only that, but inventory management software can help you identify the weak links in the supply chain and significantly reduce inventory shrinkage by providing you with all the necessary data for better-informed decisions on inventory acquisition.
Therefore, look into implementing a high-quality inventory control system and take your profitability to another level!