If you’re in construction, you already know that most “heavy lifting” on projects is not related to actual construction but to keeping project costs under control.
Despite being the subject of many studies and countless articles, efficient cost control remains an unfulfilled dream for about 70% of all construction projects that typically exceed their budget by more than 10%.
Against this backdrop, we’ll cover six field-tested strategies and concrete steps within them that can help you achieve more effective control over project budgets and timelines.
In this article...
Develop Thorough Estimates
In construction, developing thorough estimates is akin to laying a strong foundation for a building.
If the cost estimates are inaccurate, the entire project could crumble, just like a building with weak foundations.
Therefore, investing time and resources into creating comprehensive and accurate cost estimates for each phase of the project is paramount.
Regardless of project size, complexity, and delivery method, cost estimation usually rests on the shoulders of estimators who work closely with other stakeholders, from the project owner to architects, engineers, and contractors.
The estimating team’s goal is to carefully consider all potential expenses, including materials, labor, equipment, permits, and overhead costs, to avoid budget overruns and delays in the construction phase.
So, let’s look at what steps are typically involved in creating accurate cost estimates:
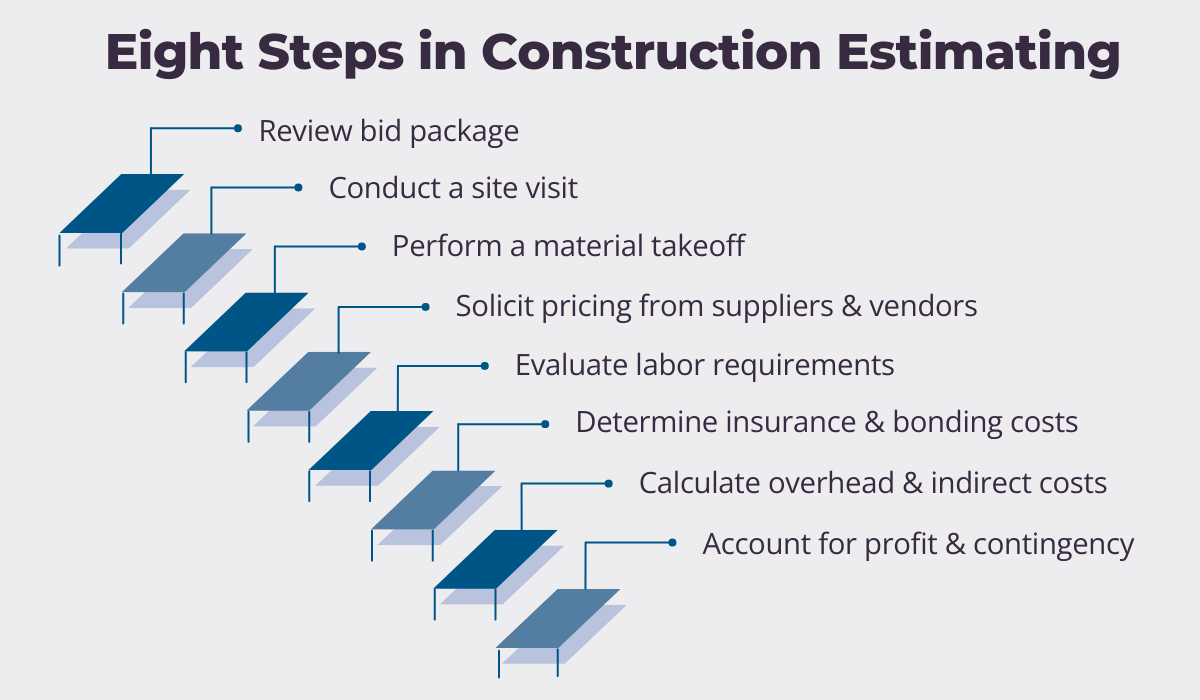
As you can see, this process is described from the perspective of a contractor preparing their bid under the design-bid-build (DBB) model, which is why the first step is to review the bid package provided by the project owner.
This implies the owner’s team already did their estimates and assessed whether the project can be realized within the budget they have in mind.
So, cost estimation starts by carefully examining the project specifications and requirements outlined in the bid package to understand its scope of work.
This is followed by the project site visit whose purpose is to:
- assess existing conditions,
- identify any potential challenges or constraints,
- gather crucial information for accurate estimation.
Next, the estimator will conduct a material takeoff, i.e., quantify the materials required for the project based on the project plans and specifications.
This process used to involve manual measurements of construction drawings but, nowadays, there is a range of software tools that automate the takeoff, making it much faster and highly accurate.
To illustrate, here’s just one of many takeoff tools used by contractors.
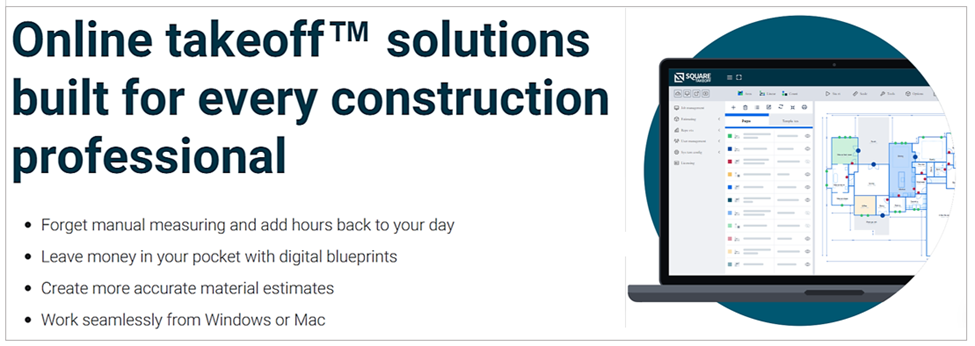
Now that the estimator knows exactly which materials will be required to complete the project and in what amount, the calculated quantities are used to solicit offers from suppliers to obtain competitive pricing for materials.
Additionally, since the contractor is now aware of what equipment will be needed, they can compare that with the equipment they own and its availability and, to fill any gaps, reach out to rental companies to get their prices.
The next steps involve:
- estimating the labor hours and skill levels needed to complete the project,
- factoring in insurance premiums and bonding requirements to protect against potential risks and liabilities,
- accounting for indirect expenses such as administrative overhead, utilities, and project management fees,
- including a reasonable profit margin and contingency allowance to mitigate unforeseen risks and uncertainties.
Each of these steps plays a crucial role in ensuring the accuracy and reliability of the final cost estimate, which becomes the foundation of a contractor’s bid.
In addition to developing thorough estimates, remember that they should be continuously monitored, refined, and updated as the project progresses.
This is also why open communication should be prioritized, which is the second key strategy for more effective cost control on our list.
Prioritize Open Communication
Establishing a culture of open communication is a cornerstone of effective cost control in construction projects.
When communication responsibilities are clearly defined and communication channels easily accessible, the likelihood of staying within budget increases significantly.
Conversely, poor communication is the main culprit behind the failure of about one-third of construction projects.
Moreover, inefficient communication also affects those projects that make it to completion.
Only 48% of projects with lacking communication manage to stay within budget, as opposed to 76% of those with effective communication.
Having set the stage, let’s see what you can do to enhance communication both within your construction team and with other stakeholders.
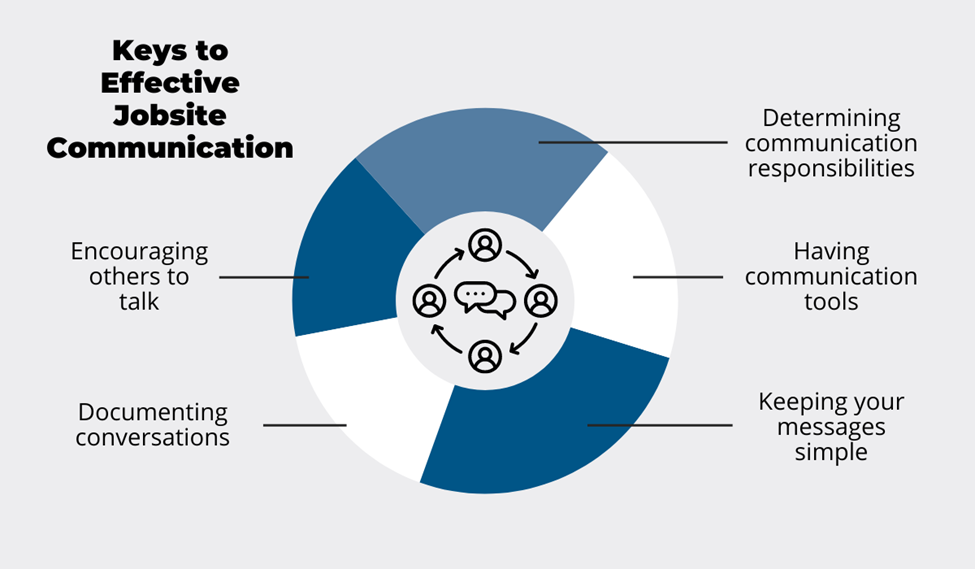
As you can see, everything starts with a clearly established communication chain of command.
More precisely, many problems arising from miscommunication can be avoided when everyone knows who to contact for specific inquiries or issues.
Likewise, providing communication tools, such as smartphones with project management software or other communication platforms installed on them, facilitates real-time information exchange.
Furthermore, if you as the project manager keep your messages simple and concise—and emphasize to your team to do the same—this reduces the likelihood of misinterpretation or confusion.
Equally, you should encourage open dialogue among team members to foster collaboration and problem-solving at all levels.
Finally, documenting conversations and decisions helps maintain accountability and provides a reference for future actions.
By prioritizing open communication and implementing these strategies, you can proactively address cost control issues as they arise, helping you ensure that the project stays on budget and schedule.
Introduce Daily Reporting
In addition to fostering open communication, introducing daily reporting is another strategy that can help you spot cost control issues early on.
Daily reports are concise documents that provide a snapshot of daily activities, progress, and events on the construction site.
Typically prepared by field personnel, they include information on workforce attendance, equipment usage, material deliveries, safety incidents, and any other relevant updates.
Daily report forms used to be printed, picked up by the crew, filled out by hand, and returned to the office at the end of the day, which made this practice time-consuming and error-prone.
Nowadays, there are many reporting apps workers can use to complete daily reports on their smartphones, enabling them to also add relevant photos.
For example, here’s how a report looks like in Raken, a construction daily report app and software.
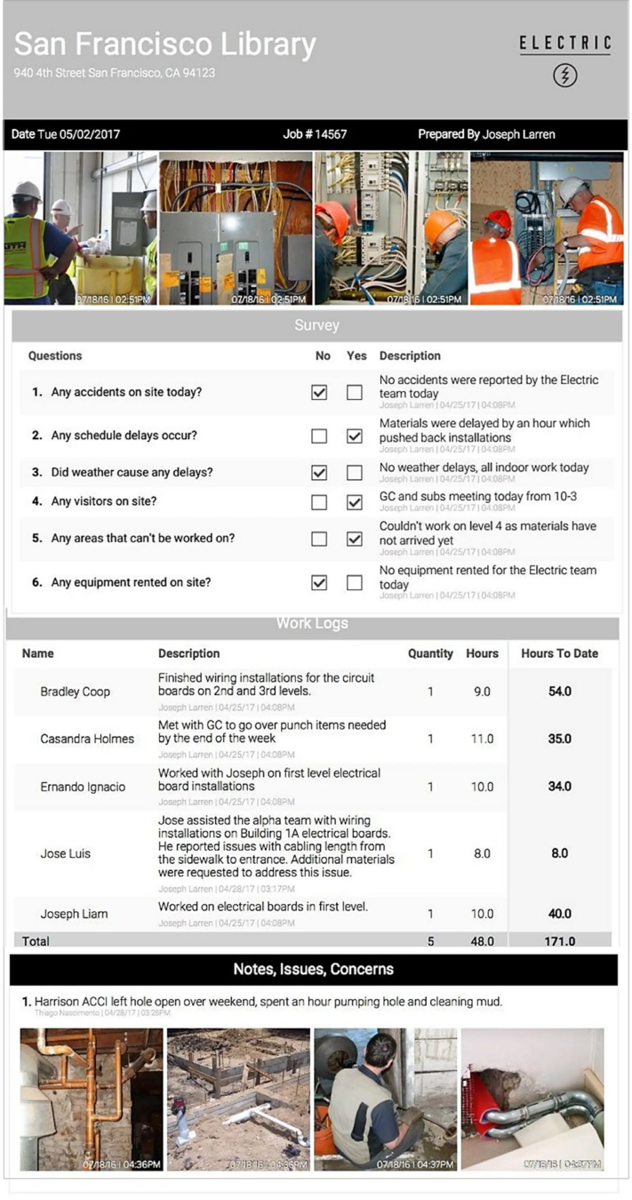
As you can see, such apps enable field crews to easily record and submit daily reports, which results in:
- streamlined data collection,
- improved data accuracy, transparency, and accessibility,
- enhanced communication,
- early identification of potential cost control issues.
Alongside other cost-related information, these daily reports serve as valuable inputs for creating regular (e.g., weekly, bi-weekly, monthly) cost reports, which provide a comprehensive overview of the project’s financial performance over time.

Usually prepared by project managers or other team members (e.g., cost engineers and financial analysts), these reports allow stakeholders to track expenses in real time, identify trends, and make informed decisions to keep the project within budget and on schedule.
Ultimately, combining daily reporting with regular cost reports creates a powerful cost control mechanism, allowing you to proactively monitor project costs, identify deviations from the budget, and take corrective actions as needed.
Identify Value Engineering Opportunities
Another effective construction cost control strategy involves identifying value engineering opportunities.
Value engineering is a systematic and structured approach to optimizing project costs without sacrificing quality or functionality.
This process involves exploring alternative materials, design options, and construction methods to achieve cost savings while still meeting project requirements.
Value engineering generates the most benefits during project design and planning, i.e., in the preconstruction phase.
At that stage, it’s typically conducted by architects, engineers, and contractors (whether already hired as the main contractor under the design-build (DB) model or acting as consultants).
As illustrated, the aim is to identify areas where the project parameters can be modified to achieve the highest advantages (cost-savings) at the lowest cost.
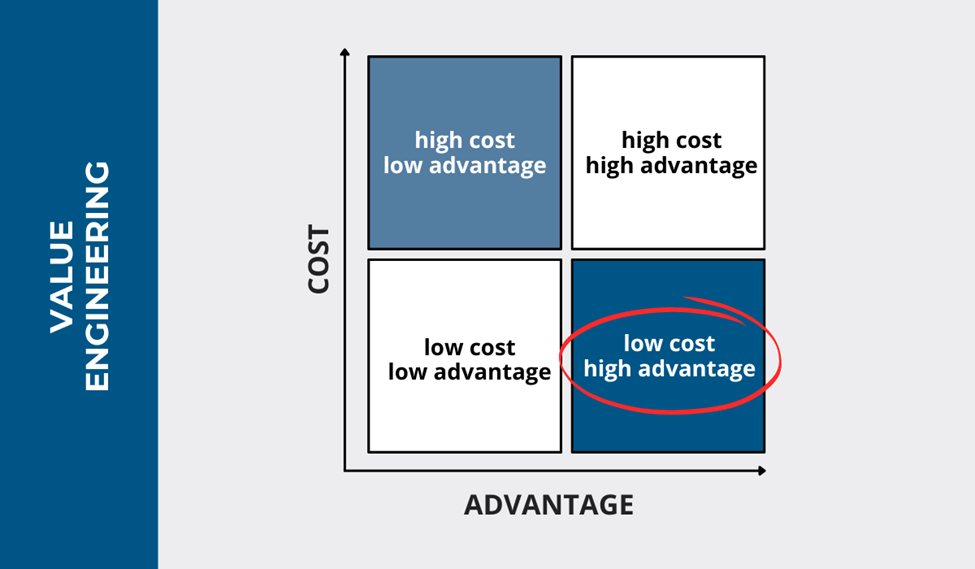
For example, the project team can engage in value engineering analysis of different roofing materials.
In doing so, the team evaluates the performance, durability, and cost of various roofing options.
This allows them to identify a roofing material that offers significant advantages in terms of durability and energy efficiency while having a moderate cost.
Extrapolating this example to other project parameters, stakeholders can optimize project costs early in the planning process, thus minimizing the risk of budget overruns and delays, and ultimately delivering better value to clients.
The same process can be leveraged when construction is underway.
However, while value engineering during the construction phase can generate significant cost savings and facilitate cost control, it also poses potential downsides.
Specifically, changes to project specifications or materials may require additional time and resources and should be carefully evaluated to ensure they don’t compromise quality, safety, or regulatory compliance.
This also implies more change orders, which can cause delays or disruptions, as discussed in the next section.
Overall, by identifying value engineering opportunities throughout the project lifecycle, construction professionals can optimize project costs, helping them achieve more efficient cost control.
Limit Change Orders
Change orders, i.e., modifications to the original project scope, can significantly impact project costs and schedules if not managed properly.
They can arise from the client changing their mind, or a slew of other reasons, such as design errors, incorrect cost estimates, or unexpected site conditions.
Whatever their cause, you should try to minimize the number of change orders issued during the construction process.
First and foremost, this can be achieved by clearly defining the project scope and discussing requirements with the project owner upfront.
Moreover, when change orders do happen, it’s crucial to ensure that each change is documented and approved by the client.
Again, this is where technology, i.e., a change order management app, can streamline the process.
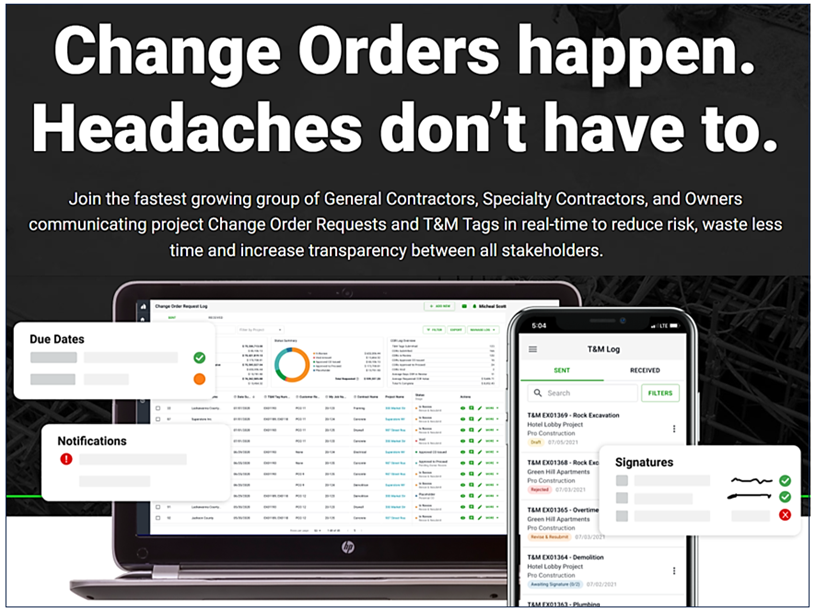
Such tools facilitate the submission, review, and approval of change requests digitally.
In addition to clarifying the client’s requirements in advance and establishing a robust change order process, you should also carefully evaluate change requests.
This will allow you to assess their potential impact on project costs and schedules before they’re approved.
By conducting thorough cost and timeline analyses, you can inform the client about the potential consequences of the agreed project budget and schedule.
That way, the project owner can decide whether to proceed with the proposed changes or explore alternative solutions to minimize additional costs or extended deadlines.
In conclusion, limiting change orders and implementing effective change management practices can help you mitigate the risk of budget overruns and delays, ultimately making your cost control more efficient.
Utilize Technology
In previous sections, we have shown examples of different technologies that can help you implement construction cost control strategies.
In light of this, it’s clear that embracing these tools, from material takeoff and cost estimating software to daily reporting apps and change management solutions, can:
- enhance accuracy and efficiency in cost estimating and budget management,
- streamline project scheduling and resource allocation,
- improve communication and collaboration among project stakeholders,
- enable real-time tracking of project progress and expenses,
- facilitate proactive risk management and issue resolution.
Naturally, all these benefits contribute to enhanced cost control.
Given the wide range of available construction management software solutions, including those we already mentioned, we’ll cover only a couple more that can help you achieve more efficient cost control.
The first one is Building Information Modeling (BIM) software.
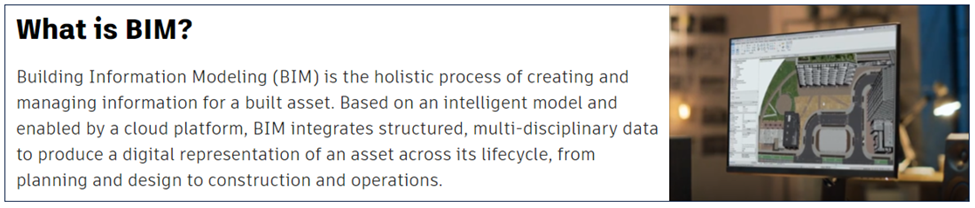
By offering a comprehensive digital representation of the project, BIM software allows for better visualization and coordination of design elements, which can help identify and resolve potential clashes or conflicts before construction begins.
This early clash detection can prevent costly rework and modifications during construction, ultimately saving time and reducing project costs.
Overall, BIM enhances cost control by improving project efficiency, reducing waste, and facilitating better decision-making throughout the project lifecycle.
The second solution that can improve cost control is asset-tracking software, like our GoCodes Asset Tracking, which enables you to cost-efficiently track and manage construction equipment, tools, and materials used on a project.

GoCodes Asset Tracking uses both patented GPS-enabled QR codes and real-time GPS trackers that, when attached to equipment, tools, or materials, allow you to track them.
This is enabled by cloud-based software and an in-app scanner (for QR code scanning) installed on mobile devices.
This contributes to better construction cost control by allowing you to:
- efficiently track equipment, tools, and materials,
- plan, allocate, and schedule resources effectively,
- optimize equipment and tool utilization,
- reduce loss and theft,
- conduct automated audits for asset accountability.
To recap, adopting advanced tech solutions is, in today’s world, imperative for enhancing cost control and streamlining construction processes, ensuring your business can keep up with the fast changes and fierce competition in the construction industry.
Conclusion
After all is said and done, implementing the six strategies outlined here can significantly enhance cost control in construction projects.
By embracing these practices and adopting the right technology solutions, you can mitigate budget overruns, streamline processes, and deliver projects more efficiently, ultimately ensuring your business’s success in an ever-evolving industry landscape.