If there is one thing without which your crew simply cannot start working on a new construction project, it is the materials.
But to be able to procure these materials without ordering too much and compromising your profits, or too little and bringing the project to a halt, your estimator needs to perform a construction material takeoff.
So, what is construction material takeoff, and how does it compare to a construction estimate?
Why does it play a pivotal role in enhancing construction project efficiency, and what methods can you use to perform it?
If these are the questions you’re looking for the answers to, this article is for you.
In this article...
Construction Material Takeoff Vs. Estimate
Construction material takeoff, also known as quantity takeoff, is the process of quantifying and listing all of the materials needed to execute the construction project.
It was named after the task of manually counting and “taking off” items from a construction drawing and then recording them in a comprehensive list, like in the image below.
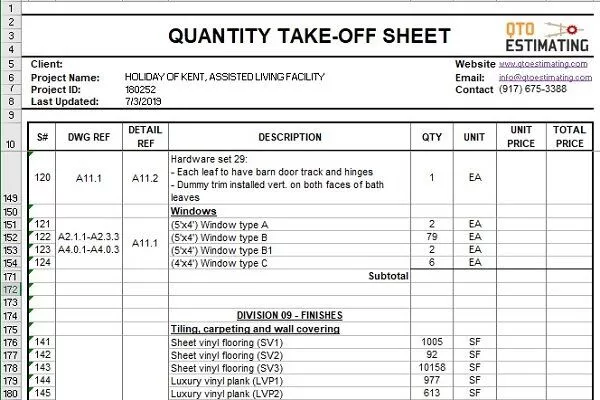
Construction material takeoff is going to serve as a foundation for each construction project you take on, allowing you to accurately estimate the cost of the project, ensure timely procurement of materials and equipment, and stay on top of the project schedule.
All of this makes material takeoff an important first step of the construction estimation process.
A construction estimate is an assessment and calculation of “the required costs for a construction project, including direct costs (e.g. materials and worker wages) and indirect costs (e.g. equipment depreciation and office worker salaries).”
Once your estimator knows what materials the project requires and in which quantities, they can go ahead and gather information about current material prices in order to build a construction estimate.
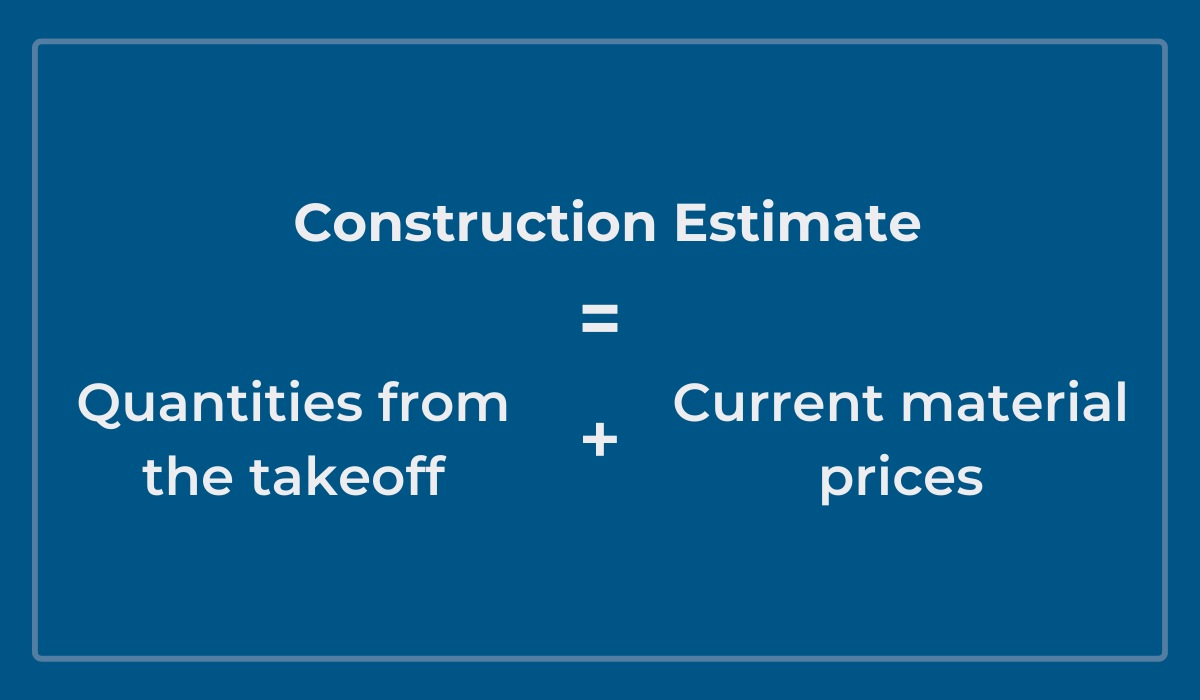
So, we can conclude that construction material takeoff and construction estimation are two separate, but closely related processes.
While material takeoff is focused solely on accurately assessing the quantity of materials needed for the project, estimation is more concerned with predicting overall costs associated with the construction project—including the cost of materials.
Measurements Used In Material Takeoff
Given the diverse range of materials needed to complete a construction project, your material takeoff sheet can quickly get messy and difficult to follow.
Not ordering enough of a certain material, or ordering too much because it was accidentally listed multiple times throughout the sheet is the last thing you want to deal with.
On top of that, each material needs to be quantified differently, based on whether it is countable or uncountable and what unit of measurement is typically used for it.
For instance, you can order 30 pieces of lightbulbs, but if you try to order 30 pieces of concrete, you’re bound to cause a lot of confusion.
That is why it is important to categorize the materials into fundamental measurements used in material takeoff.
This will allow you to gain clarity and consistency, as well as contribute to a more accurate estimation process.
Below are the four main measurements you need to know about—count, area, volume, and length.
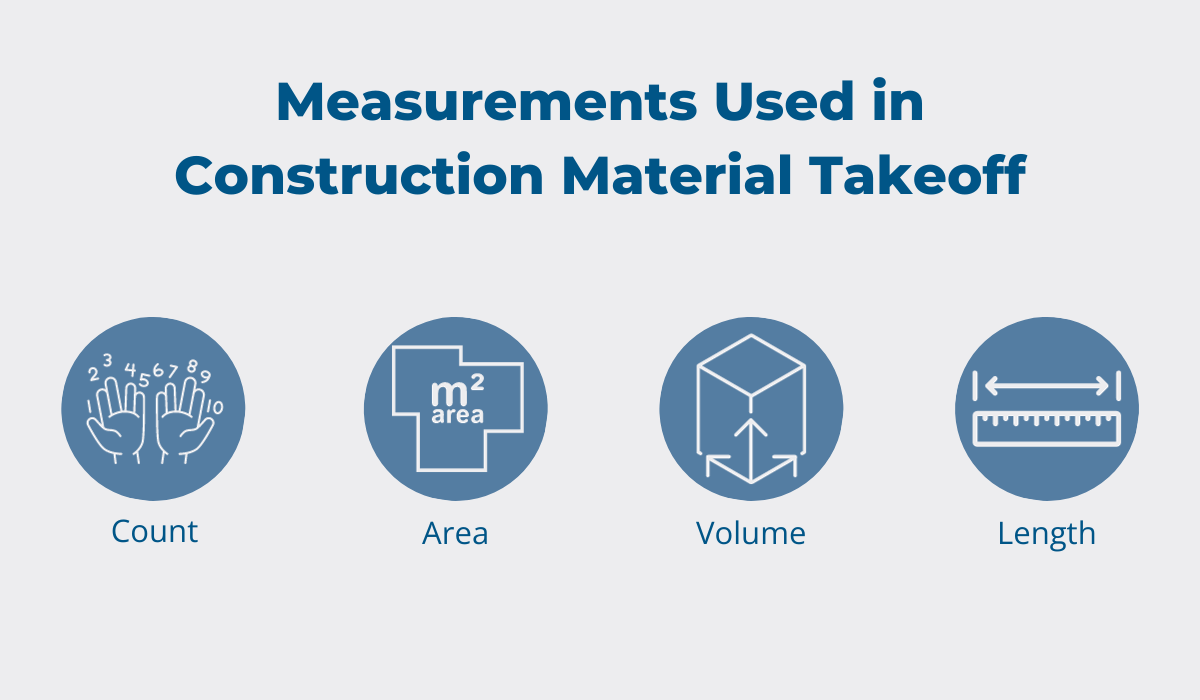
So, let’s dive deeper into each one.
The count (or quantity) measurement is going to be applied to materials that can be counted.
This includes individual items like doors, sinks, outlets, light fixtures, and other prefabricated items, and this measurement is typically expressed in units such as each (EA).
Next is the area measurement, used to determine the amount of material needed to cover a surface area.
The material takeoff for this measurement is usually expressed in square meters (SM) or square feet (SF), as you can see in the example below outlined in red.
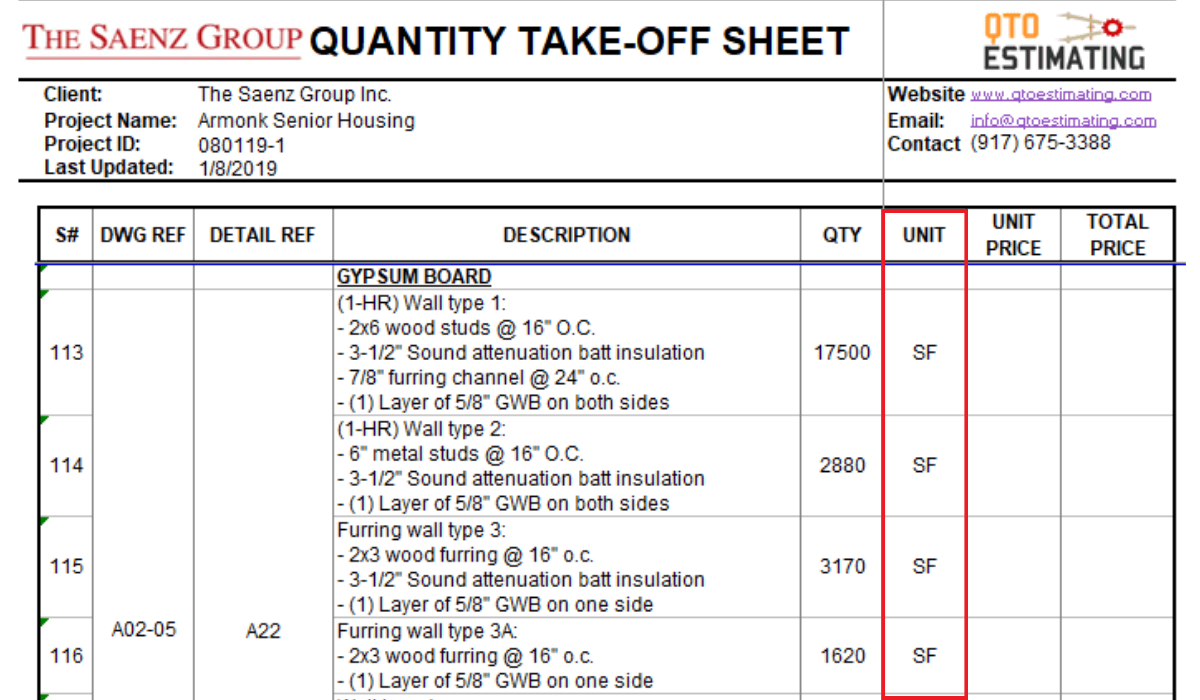
This measurement is used for determining how many square feet/meters of materials like drywall, flooring, tiling, or roofing you’re going to need for the project.
For soil, concrete, sand, gravel, and other materials that occupy a certain space, the measurement used is going to be volume.
Volume is typically measured in cubic yards (CY), cubic feet (CF), or cubic meters (CM).
And lastly, length is going to be the measurement of choice for materials that are measured in a straight line.
Examples include wire, lumber, pipes, cables, and similar items that are listed by linear feet (LF), linear meters (LM), or linear yards (LY).
These four measurements are going to cover a wide variety of materials and components in an organized manner, as well as provide you and your team with a standardized way to assess the quantity of materials needed to complete your project.
How Accurate Material Takeoff Improves Project Efficiency
Accurate material takeoff—which is supported by the aforementioned use of measurements—is going to help you make sure that you don’t over- or underestimate the amount of material needed and therefore experience cost overruns or material shortages.
But aside from that, it is going to boost the efficiency of your construction project.
First, let’s consider how material takeoffs can affect your workflows.
If your estimator underestimates the amount of, let’s say, tiles that are going to be used for multiple rooms in the building, your crew will likely realize this once the project is already in motion.
They will then have to let the project manager know about the issue, and the manager will need to further follow the communication protocol in order to resolve the issue of material shortage.
This is not only going to incur additional costs, but also cause delays and completely derail the project, as your crew won’t be able to move forward until the tiles have arrived.
Conversely, procuring the right amount of materials from the get-go will ensure that everyone involved in the project stays productive and on schedule.
This desire to remain as efficient as possible inspires construction professionals to invest in software solutions that aid in creating accurate material takeoffs.
Jeremy De Paz, formerly a Project Manager at Waterloo City Construction, elaborates on the benefits of using construction takeoff software:
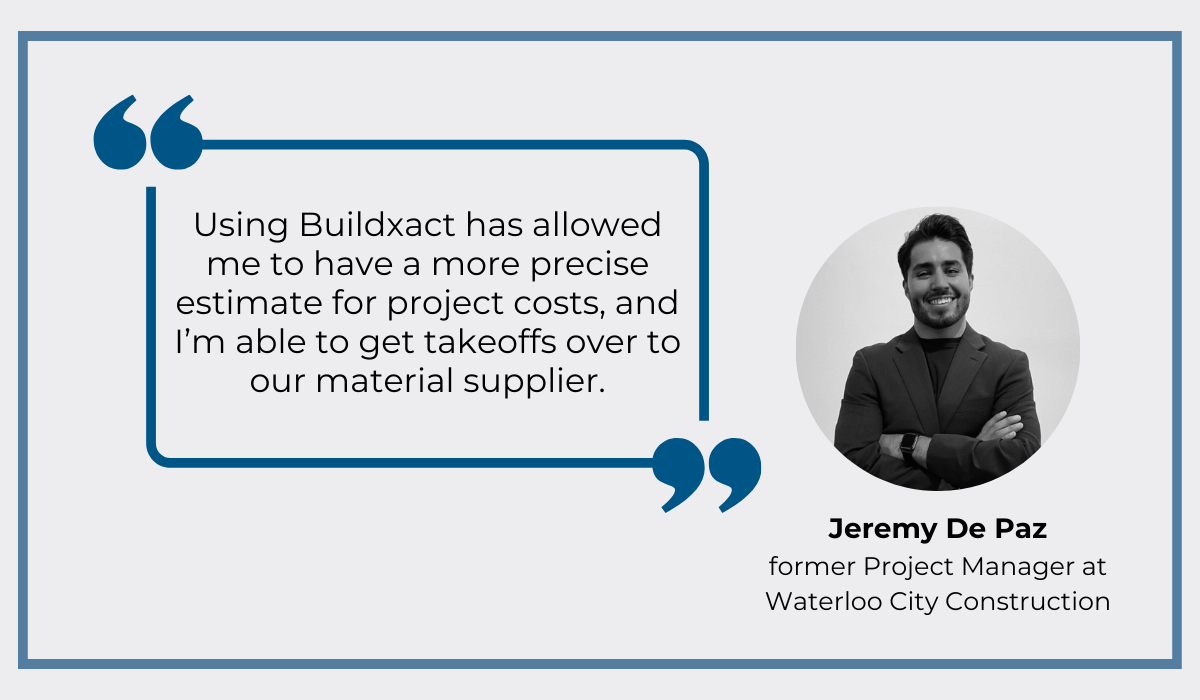
As you can see, using such software can help you not only achieve more precision with your estimations, but also streamline the process of getting the takeoffs to your material suppliers, thus enhancing efficiency.
On top of that, accurate material takeoff documentation is going to provide all stakeholders with clarity about the materials needed for each component of the project.
For instance, working on a commercial construction project is going to require the involvement of various teams—from architects to structural engineers, contractors, and interior designers.
If they all get access to the material takeoff sheet—and the option to provide their input—they can better coordinate their efforts and determine when the materials for their part of the project need to be ordered and in what quantities.
That way, you don’t have to worry about materials being ordered too late or having ordered duplicates.
Fostering collaboration and communication between teams in this manner and early on in the project can significantly reduce the likelihood of mistakes and misunderstandings that are bound to reduce efficiency.
As you can see, accurate material takeoff plays an important role in ensuring your project runs smoothly, so don’t underestimate its value.
Methods for Construction Material Takeoff
Now that we have covered some basics about what construction material takeoff is and why it’s important, it is time to discuss the methods you can use to perform it.
There are two main methods for performing material takeoffs—manual and digital—so let’s dive deeper into each one.
Manual takeoff, as the name suggests, is performed by measuring and calculating the needed quantities of materials by hand, using pen and paper, based on project documents.
Some construction professionals like using this method because it comes with its own set of advantages.
For instance, performing material takeoffs manually allows the estimator to gain a deeper understanding of the project, as this requires them to fully immerse themselves in the task in order not to make any mistakes.
On top of that, the manual takeoff approach aids in developing skills that are essential in the construction industry, such as better attention to detail, visualization, and spatial awareness.
But despite these important benefits, more and more construction companies are abandoning the manual material takeoff method.
Bryan Stamp, Director of Product Sales at the software, hardware, and services technology company Trimble, explains:
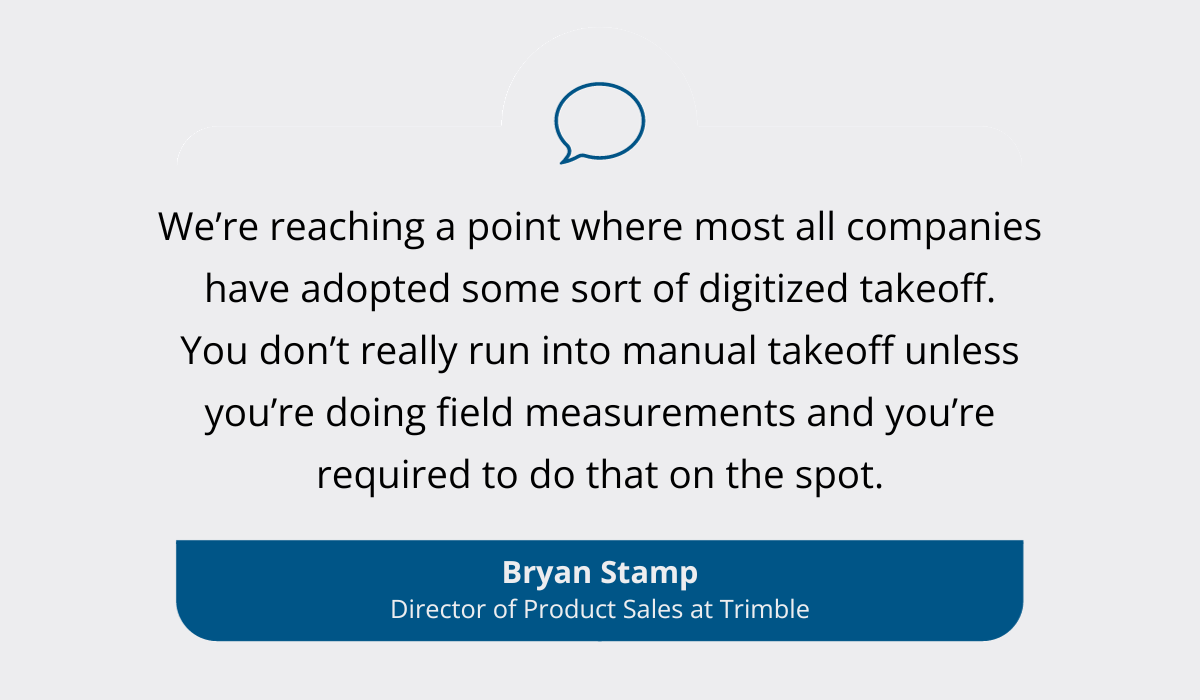
This is because the manual approach to material takeoff has certain limitations that, for many construction professionals, outweigh the skill-building benefits.
Namely, manual takeoff can be time-consuming, resource-intensive, and prone to costly errors.
Imagine studying all of the construction documentation, manually measuring and calculating material quantities, developing a detailed list of materials, estimating costs, and getting in touch with suppliers—only to realize that you miscalculated something and have to start all over again.
This kind of scenario isn’t only frustrating, but also bound to derail your project schedule.
That is why more and more construction companies are opting for the second approach to material takeoffs—the digital one.
The digital takeoff method involves using construction takeoff software to handle the task of quantifying and estimating the materials needed to complete a project.
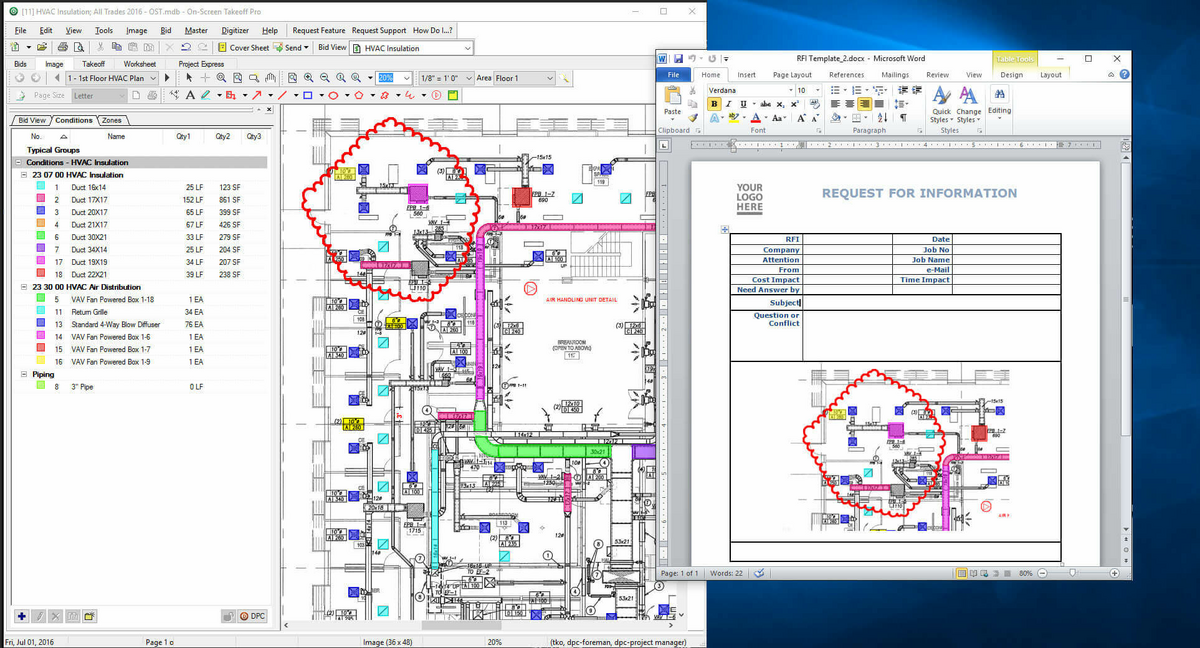
This kind of software solution allows you to import construction drawings and then calculate the required quantities of each material, thus making the process more efficient and accurate.
Apart from this, digital takeoff tools can facilitate collaboration and communication among stakeholders, as all of them have access to the same, up-to-date information.
This allows them to make better business decisions, elaborates Casey Cyrus, Business Area Manager at Trimble.
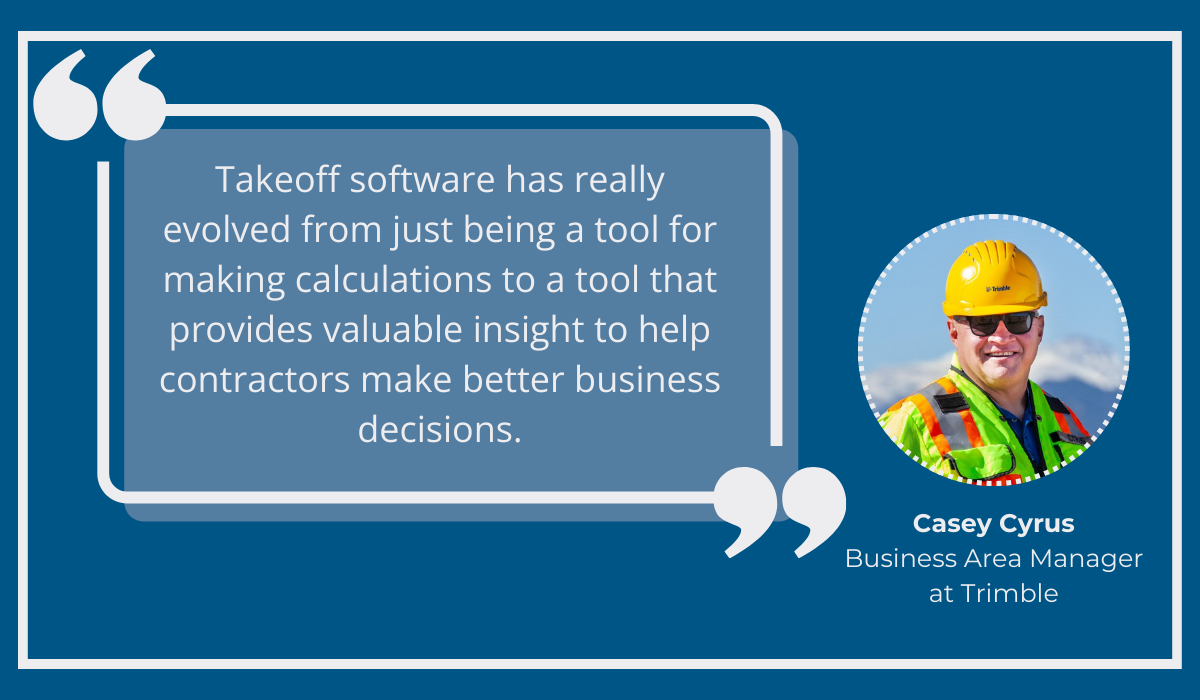
So, which method is right for you?
The answer is going to depend on how experienced your estimators are and how big a project is.
If the projects your company takes on tend to be more complex and involve a lot of stakeholders, the adoption of digital takeoff tools might be the right choice, as it is bound to make the task much easier and quicker.
Can You Automate Material Takeoffs?
While digital takeoff tools make the process of creating material takeoffs quicker, more accurate, and more efficient than their manual counterpart, they don’t fully automate this important task.
This begs the question, can material takeoffs even be completely automated?
As it turns out, they can—with the help of automated takeoff software solutions.
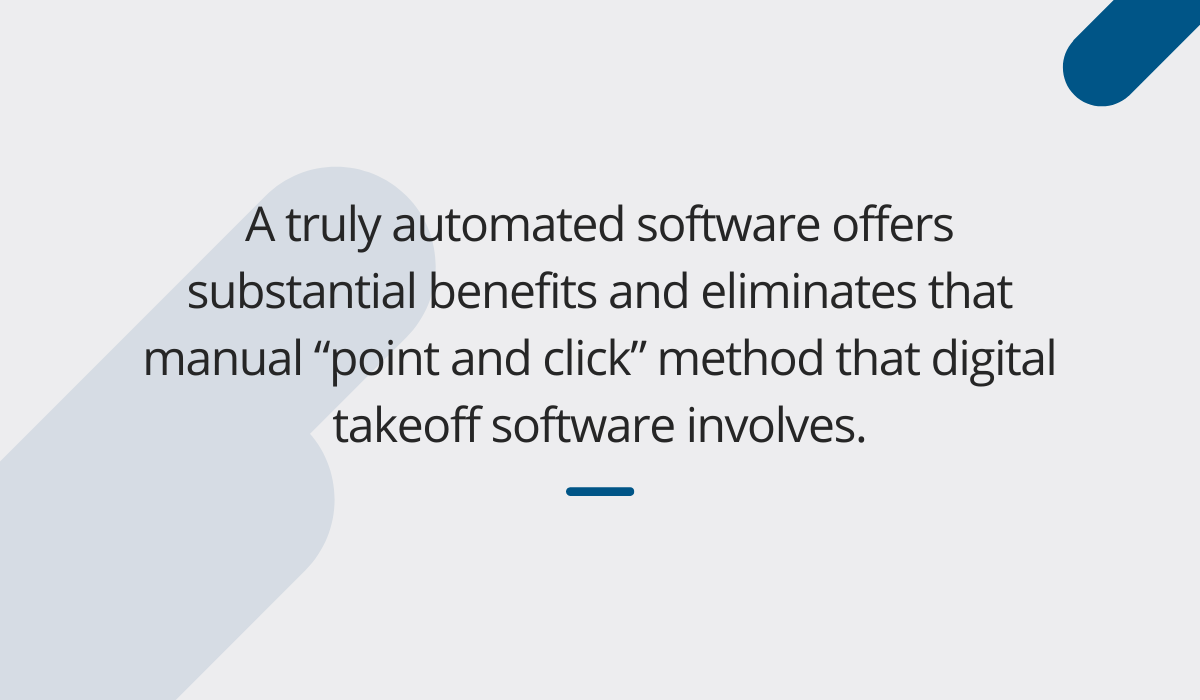
While digital takeoff software still requires you to manually input measurements and calculations, automated takeoff software utilizes machine learning algorithms to automate the process of extracting information from digital construction drawings.
For instance, when using a fully automated takeoff solution such as Countfire, you’ll have to click on a symbol representing a specific type of material only once.
Then, the software will automatically mark the remaining symbols for that material across every drawing you imported for that project, thus saving you time and making sure you don’t miss anything.
The video below demonstrates how this works:
As you can see, fully automating the process of measuring and calculating the amount of needed materials can significantly enhance accuracy and efficiency by taking over tasks that don’t require human touch.
This will leave your estimators with more time to handle value-added tasks.
Keep in mind, though, that when it comes to takeoff software, the terms “automated” and “digital” are often used interchangeably.
So if you’re looking to completely automate your material takeoffs, make sure you exercise caution.
Conclusion
In this article, our goal was to provide you with a comprehensive overview of the concept of construction material takeoff.
We started by defining what material takeoff is and how it compares to construction estimates, and then moved on to explaining what measurements are used in this process and why it is so significant.
Lastly, we elaborated on the differences between manual and digital takeoff, as well as provided you with insights on how you can fully automate material takeoff at your construction company.
With all of this knowledge at your disposal, we hope you feel encouraged to enhance your approach to this important process.