Tracking valuable construction assets like heavy machinery, equipment, and tools as they change hands and move from site to site has long been a priority for construction companies that want to reduce costs and maximize asset utilization.
However, the tracking process is typically wrought with mistakes that hamper their efforts, decrease productivity, and reduce profitability.
That’s why we’ll describe seven common asset-tracking mistakes and explore how your construction company can avoid them.
In this article...
Relying on Tracking Assets Manually
The first—and biggest—mistake some construction companies make is relying on manual asset-tracking processes.
In fact, it could be said that all the other issues mentioned here stem from this mistake.
Conversely, they can be successfully addressed by adopting easy-to-use and affordable asset-tracking software.
When a company uses paper forms and/or spreadsheets to track its assets, this usually involves a lot of manual data entry, which is time-consuming, resource-intensive, and leaves plenty of room for human error.
More specifically, here are the main reasons Excel shouldn’t be used for asset management.
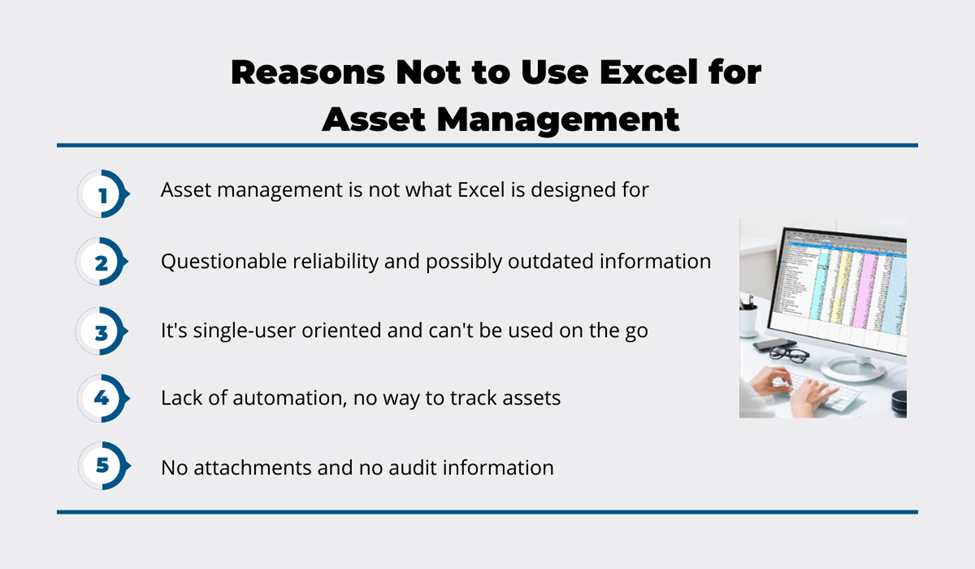
As you can see, when comparing Excel to modern asset-tracking software solutions, it clearly lacks the features necessary for effectively tracking and managing your construction tools and equipment.
Moreover, spreadsheets are intended for a single user, which poses a difficulty in terms of updating the data, potentially corrupting the asset data accuracy.
On the other hand, simple and cost-efficient asset-tracking software will minimize the need for manual data entries and updates, allowing even your less tech-savvy workers to operate the system with ease.
Our asset-tracking platform, GoCodes Asset Tracking, is an excellent example of a software solution that has all it takes to digitize, automate, and streamline your asset-tracking operations.

When a construction company decides to implement GoCodes Asset Tracking, it will ensure that all future users (workers and managers) have downloaded the cloud-based software onto their smartphone, tablet, or any other internet-connected device.
Furthermore, the company will receive rugged QR code tags that it will affix to tools and equipment it wants to track.
Once the system is populated with initial asset data, workers can scan the tags using the GoCodes Asset Tracking in-app scanner on their smartphones or tablets and view and update the asset info.
Long story short, the components of an asset-tracking system allow you to replace many manual tasks with automated ones.
All in all, the mistake of relying on manual processes can be efficiently eliminated by the right asset tracking software solution.
Failing to Record Important Asset Data
Another common mistake arising from manually tracking assets using pen-and-paper and/or spreadsheet-based methods is the failure to record important asset data.
In other words, these outdated asset-tracking methods rarely allow construction companies to capture all the relevant asset information in one central database that can be easily accessed and updated.
This is only aggravated by the fact that some data (such as the asset’s current condition, location, and availability) can change quite frequently, but users might not be aware of that.
To illustrate, here’s a list of important asset data that should be tracked and regularly updated.
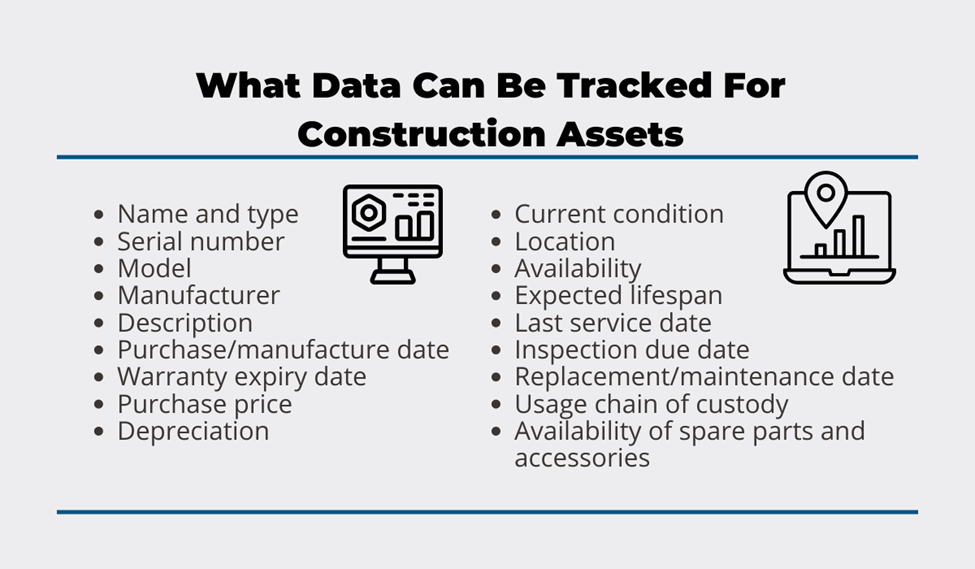
If all this information is kept in separate files or not regularly updated, this can lead to employees working with different data that’s missing (often crucial) details about your assets.
For instance, if the relevant expiry date is not recorded, this can result in missing the fact that a piece of equipment is still under warranty.
Another example is when the date is listed, but there is no link to the warranty terms and conditions, making finding them time-consuming.
On the other hand, your asset tracking software will keep all the data in one place that’s automatically updated when a manager, worker, or service technician makes any changes to the asset info.
To recap, important asset data can be quickly and easily recorded with the help of asset tracking software, ensuring you’re not missing any information needed for better decision-making.
Ignoring the Need for Accurate Location Tracking
Another common oversight refers to a construction company not (exactly) knowing where its assets are currently located.
This lack of real-time location updates typically does not apply to heavy machinery and vehicles (when their location is tracked with active GPS trackers) but can include other high-value equipment like backup generators and surveying equipment.
The point is that when asset locations are not accurately tracked and recorded, this opens up room for all kinds of problems, including not detecting asset theft or loss on time (or at all).
To prevent that, construction companies can utilize different tracking methods (e.g., GPS, Bluetooth beacons, or RFID tags), each with its advantages and costs.
However, the simplest and most cost-efficient way to achieve accurate location tracking is by implementing cloud-based tracking software that uses GPS-enabled QR code tags and an in-app scanner.

As illustrated, QR code labels are attached to construction assets, and—when an asset tag is scanned with a smartphone or tablet—the software will automatically record the asset’s current GPS location.
In other words, if a worker or manager is looking for a missing tool (or just wants to see whether a specific tool is present on-site), they can check the tool’s last known location in a few clicks.

Naturally, real-time location updates provided by the tracking software create many opportunities for your managers to prevent asset theft and loss, improve their allocation and utilization, and increase your company’s profitability.
Therefore, the problems arising from inaccurate location tracking can not only be eliminated with the help of the right software but can also bring a host of other benefits to your company.
Not Having Employees Check Assets Out and In
Another asset-tracking mistake is not keeping track of employees checking assets out and in.
Construction companies will typically skip this part—and suffer the consequences—because the process of recording who is using tools, equipment, and other assets at any given time is too time-consuming or impractical.
Naturally, not having an accurate record of past and present asset users can lead to many issues, including a lack of worker accountability reflected in (internal) theft, careless handling, and loss of assets.
Conversely, a host of problems can be avoided by establishing an automated check-in/check-out system where employees simply scan assets when taking and returning them, and the tracking software records it.
Here is what a check-in/out log looks like when tracked by the software.

As you can see, this tracking software feature gives you a precise chain of custody, bringing many advantages to your company.
For instance, the fact that workers know there’s an official record of them assuming responsibility for specific assets acts as a preventive theft/loss measure.
Concurrently, the system ensures that assets are returned in the same condition since it’s much easier to identify who potentially mishandled a piece of equipment that is now not functioning properly.
Likewise, it ensures assets are returned on time.
Specifically, tracking software can usually be configured to send overdue reminders for tools that haven’t been returned when scheduled, thus notifying the “late” tool user and the responsible equipment manager.
Given all the above, this asset-tracking mistake with often expensive consequences can be avoided by deploying a simple, easy, and fast asset check-in/check-out system.
Neglecting to Track Asset Utilization
This mistake goes hand in hand with failing to track asset locations and users with sufficient accuracy and precision.
In other words, when records of what assets your company has, at which locations, and who is using them are non-existent, inaccurate, or can’t be obtained from a single source, tracking asset utilization is almost impossible.
On the other hand, when asset locations, users, and other parameters are tracked properly, your company can monitor asset utilization and reap benefits like optimal asset allocation, improved productivity, and cost savings.
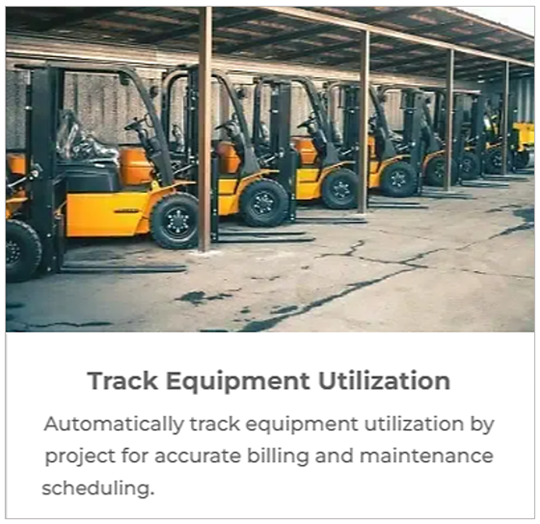
As suggested, asset utilization data collected by your tracking software allows you to, for example, track equipment usage from project to project, for accurate billing and future budgeting purposes.
Likewise, tracking asset utilization enables efficient maintenance scheduling (which will be discussed later).
Furthermore, it allows you to identify underutilized assets, reallocate them, and minimize the need for unnecessary purchases or rentals.
Similarly, you can use asset utilization data to make better-informed repair-or-replace decisions and eliminate asset allocation inefficiencies in your workflows.
To recap, tracking asset utilization—instead of neglecting it—helps companies increase operational efficiency while reducing asset procurement, maintenance, and depreciation costs.
Disregarding the Value of Work Order Tracking
Not tracking maintenance work orders and other asset-related tasks is another typical mistake that can have negative operational and financial consequences.
In other words, when different work orders are kept on paper and need to be manually entered into the system, it’s easy to lose track of what orders were executed and when, leading to missed maintenance, unexpected breakdowns, and project delays.
In comparison, when tracking software is equipped with a task management feature, managers can create, assign, and monitor the execution of work orders in real-time using the tracking app on their smartphone or another internet-connected device.
Here’s what a task representing a work order in the app could look like.

Naturally, this feature also allows assigned service technicians to access the details of their work order and update the info when their work is done.
This means that managers receive real-time updates on the execution of work orders and can address any maintenance issues using the tracking app that is instantly updated and always available to all users.
Ultimately, tracking work orders can lead to enhanced planning capabilities, higher employee productivity, improved safety compliance, and reduced costs, all of which help you get more value out of your assets.
Forgetting About Maintenance Schedules
Considering the complexity of even simpler construction projects, regular maintenance often takes a back seat to completing a project on time and within budget.
In other words, maintenance schedules are skipped, changes are not recorded on time, and service technicians end up unsure of what to do next.
In such circumstances, it’s easy to miss routine maintenance tasks, which can then translate into more extensive and expensive equipment breakdowns.
However, managers can ensure that scheduled maintenance tasks are always performed by “instructing” the tracking software to send automated email reminders of upcoming maintenance to the designated service technicians.
Here’s an example.

Naturally, the assigned technician will also see the same notification in the tracking app on their phone.
From there, they can access the asset’s info page, where they can view data on the mechanical condition, maintenance status, and performance of the asset under their maintenance.
When finished, they can use the app to record that the scheduled maintenance task is done, while the manager can schedule the next regular maintenance for that asset and set automatic notifications.
Likewise, managers can use low inventory alerts to ensure that maintenance staff has all the spare parts and supplies it needs for proper maintenance.
Overall, using reminders and other notifications to keep up with scheduled maintenance is paramount for achieving efficient and cost-effective asset management that ensures smooth operations and timely project completion.
Conclusion
The key takeaway of these seven asset-tracking mistakes is that they can be successfully avoided/eliminated/minimized by implementing the right software solution.
That solution should rely on digitized and automated processes instead of manual asset tracking and should collect and instantly update important asset data.
It should also provide accurate asset location tracking, allow you to establish an automated check-in/check-out system, and enable you to track asset utilization, work orders, and maintenance schedules.
Finally, it should provide all this and more in a simple, user-friendly, and affordable package.