As construction equipment ages and deteriorates while technology marches on, all heavy equipment and tools used in construction will inevitably become obsolete and be replaced by their newer, more efficient counterparts.
However, even when equipment is not made obsolete by a newer model, it may become outdated for many reasons, such as high maintenance and operating costs, declining performance, or loss of purpose due to other technological advancements.
But sometimes, pieces of equipment or their components are intentionally made obsolete and phased out by manufacturers using various planned obsolescence strategies.
This article will explain the different types of equipment obsolescence, the risks relevant to your business, and how you can efficiently manage them.
In this article...
What Is Equipment Obsolescence
For starters, equipment obsolescence could be defined as a naturally occurring process caused by the aging and deterioration of equipment, technological advancements, and changes in user preferences.
However, that process can also be manipulated to generate extra profits by making equipment obsolete before it should be (the so-called planned or intentional obsolescence).
Now let’s toss in another definition borrowed from the manufacturing industry, which further clarifies how otherwise functioning construction equipment can become obsolete:
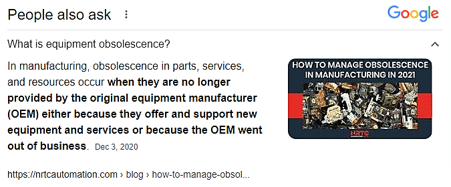
As you see, the primary focus is on those situations when spare parts, services, or other resources required to keep specific (construction) equipment in use are no longer available (whether intentionally or not), although they’re still required.
When contractors fail to take this into account, it can seriously affect their operations.
There is a risk of breakdowns of critical equipment without the possibility of repair, as well as delays and high replacement costs.
To sum up, construction equipment obsolescence should be viewed as a naturally occurring process caused by the aging of equipment, its components and materials, new technology innovations, and changes in requirements or preferences, unless that process is manipulated for profit.
Types of Obsolescence
So, we’ve established that construction equipment can become (or be declared) obsolete for various reasons.
Despite the topic’s complexity and many possible categorizations, we decided to boil them down to four types of obsolescence.
The first two, functional and technological obsolescence, could be broadly characterized as unplanned, i.e., resulting from different economic, social, and technological factors and trends.
Conversely, the other two, systemic and contrived obsolescence, could be classified as planned, i.e., arising from different efforts to deliberately induce premature equipment obsolescence and/or intentionally reduce its lifespan.
Let’s look at each type more closely.
Functional Obsolescence
Put simply, functional obsolescence covers the “usual” reasons why heavy machinery, equipment, and tools get replaced—because their performance has declined to the point where they can no longer efficiently perform their original function, and that loss of functional utility can’t be (cost-effectively) regained.
When a piece of equipment is used over time, including when it’s overworked, improperly operated, or poorly maintained, its materials and components deteriorate, its functionality declines, and maintenance and repair costs go up.
As a result, there comes a time when that equipment is no longer useful, meaning its original function is irreversibly impaired.
In other words, modifying or upgrading that piece of equipment to handle the current operational needs is either technically not possible (due to its outdated design features) or not cost-effective.
Thus, although not dysfunctional, the said piece of equipment is rendered functionally obsolete.
Technological Obsolescence
In essence, technological obsolescence happens because of technological advancements.
There are many examples of technological obsolescence around us, such as the evolution of computers and cars shown below, and the same applies to construction equipment.
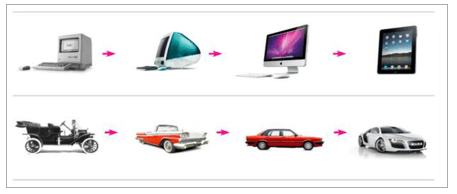
In other words, when manufacturers create new equipment intended to completely replace their predecessors, they will, at some point, stop manufacturing components for older equipment.
This means that spare or replacement parts required to maintain and repair the still functioning equipment become unavailable or difficult to find, and expensive to acquire.
Similar to functional obsolescence, when such issues impede the original function of construction equipment and can’t be remedied in a cost-efficient way, that equipment is technologically obsolete.
Systemic Obsolescence
We’re now venturing into the murky waters of planned obsolescence strategies that some manufacturers employ to deliberately make equipment obsolete before its time.
Although the above-described technological obsolescence can have some overlapping gray areas with systemic obsolescence, the main difference is that the latter is intentionally caused by manufacturers to reduce the compatibility of new products with older equipment.
As such, systemic obsolescence involves gradual alterations being deliberately made to new equipment, components, and accessories to render them incompatible with preceding equipment models.
For example, changing the design of new fasteners so they can’t be used with existing machinery.
In such cases, components are intentionally manufactured not to be backwards (or forwards) compatible, although it would have been reasonable to do so for profit because the market still requires them.
Thus, systemic obsolescence is a type of planned obsolescence where gradual changes are made that intentionally render equipment obsolete prematurely to boost the sales of new models.
Contrived Obsolescence
Contrived obsolescence is a type of planned obsolescence where manufacturers intentionally design equipment with a shorter lifespan, thus achieving higher turnover and profits.
As a result, such equipment will need to be more frequently replaced because it’s designed to deteriorate after a predetermined period past the point of (cost-efficient) repair.
Maybe the best-known case of contrived obsolescence is the great light bulb conspiracy, where the Phoebus cartel made of U.S. and European bulb manufacturers lowered the useful life of light bulbs from 2,500 to 1,000 hours, as explained in this video.
Naturally, such built-in or predetermined obsolescence strategies are not advertised and are often masqueraded as some type of technological or functional obsolescence.
So, this type of planned obsolescence covertly and deliberately reduces the equipment lifespan to increase sales without regard to end-users or environmental, sustainability, and waste management concerns.
Of course, when not managed properly, all the above types of obsolescence can expose construction companies to different risks.
Risks of Using Obsolete Equipment
Put simply, construction equipment is used in an environment (e.g., construction sites) where breakdowns, accidents, and interruptions can cause delays, cost overruns, and client frustrations.
Thus, the risks arising from using outdated or almost obsolete construction equipment are varied, ranging from costly downtime and delays to reduced productivity and higher operating costs.
In other words, continuing to use equipment that can no longer be properly serviced or operated for any reason carries the risk of that equipment eventually and unexpectedly breaking down.
When that happens, components needed to repair it might be unavailable, or difficult to find, and more expensive to purchase.
If that equipment is critical for project completion, the time needed for repair or replacement might cause delays that frustrate the client.
Moreover, we shouldn’t forget the risks associated with using outdated construction technology, whether hardware or software, and other obsolete IT equipment.
Similar to obsolete construction equipment, their use reduces productivity and increases costs while exposing contractors to the risk of unexpected failure, downtime, and delays.
Given all the above, the risks of using obsolete equipment should be avoided or minimized by proactive equipment obsolescence management.
How to Manage Equipment Obsolescence
In a perfect world, one word would be enough to answer this question and mitigate all the above-discussed risks: planning.
Namely, planning ahead allows you to keep a close eye on equipment obsolescence issues and proactively manage them to prevent the related risks and consequences that could’ve been easily avoided.
This means that, in the real world, equipment obsolescence should be managed by taking a proactive approach and focusing on preventive action.
Considering the number, variety, and increasing technological complexity of construction equipment, this is no easy task.
So, here are four tips to help you create an obsolescence management plan and efficiently address current and future equipment obsolescence risks.
Perform an Equipment Audit
In essence, performing an equipment audit allows you to find out when specific equipment was made, how long it has been in use, how many times it was serviced or repaired, and whether its components and spare parts are still available on the market (or in your storage).
Once collected, this information should be compared with life expectancy information provided by the original manufacturer to determine how long a piece of equipment has before becoming obsolete.
Of course, you may already keep an inventory list of all construction equipment with relevant information in some type of construction management or asset tracking software, which will accelerate the auditing process.
For instance, when construction equipment and tools are labeled with QR code tags and tracked via a cloud-based app like GoCodes Asset Tracking, equipment managers and other users can instantly see the information essential for an equipment audit.

Namely, they can see equipment information by scanning the tagged equipment with their smartphone or logging into the app and accessing the central inventory list on any device with an internet connection.
This easy-to-use and affordable tracking solution can, alone or integrated with other construction management software, ensure simple and quick access to equipment info, such as the date of manufacture, usage and maintenance history, and other data relevant for determining how exposed specific equipment is to obsolescence risks.
Finally, as part of a risk analysis that follows, the availability of its components and spare parts on the market (and maybe in storage) can be determined.
Conduct a Risk Analysis
Conducting a risk analysis is essential for planning how to best manage equipment obsolescence in order to reduce equipment costs, enhance overall productivity, and keep your projects on budget and schedule.
This analysis should answer what equipment is exposed to the risk of becoming obsolete, including the type(s) of obsolescence affecting it.
Then, all equipment identified as outdated should be ranked according to different criteria, including the probability and impact of obsolescence risks combined with how critical specific equipment is for construction or other related operations.
Here’s an example of a risk analysis matrix for obsolescence management where outdated equipment prioritized by criticality can be assessed.
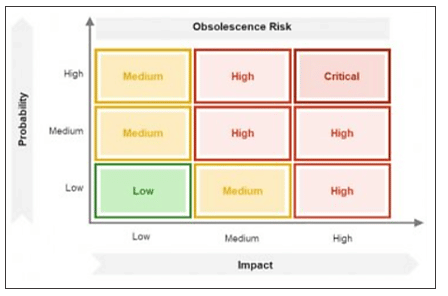
Furthermore, this risk analysis should determine whether such equipment is safe to operate and if it has a high risk of failure.
Next, it should assess how difficult it would be to maintain or repair such outdated equipment in the future (including the availability of replacement or spare parts on the market) and whether it would be cheaper to replace it.
Thus, conducting a risk analysis provides essential elements for evaluating and managing construction equipment obsolescence.
Communicate With Suppliers
Any audit and risk analysis aimed at establishing the obsolescence status of construction equipment wouldn’t be complete without updated information from equipment suppliers and manufacturers.
When a piece of equipment is assessed as obsolete but still safe and efficient enough to keep in use, it’s best to take both a proactive and reactive approach.
Both approaches include open communication with different equipment manufacturers and suppliers.
For instance, a construction company can be proactive and ensure that the components necessary for repairing an obsolete piece of equipment are still manufactured and available, preferably in stock, meaning they can be sourced and shipped in a reasonable amount of time when needed.
Likewise, suppliers can notify the company about product change notifications, end-of-life announcements and product discontinuation notifications, or last-time-buy notices.
Here’s an example of dates and notices sent when Korenix discontinues a product.
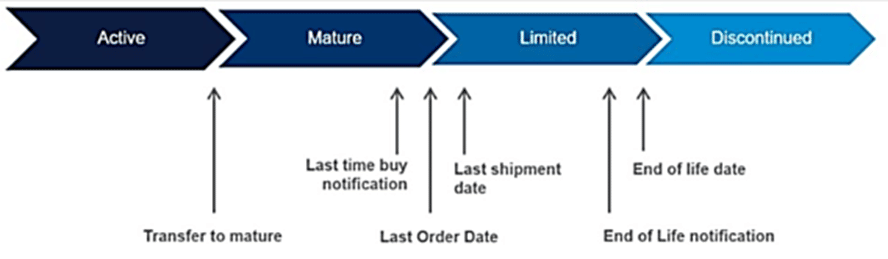
When timely notified, the company can react and order spare parts, components, and accessories that will not be available in the future, thus extending the useful life of outdated equipment.
That’s why keeping open lines of communication with suppliers is essential for effective obsolescence management.
Stock up on Components
Armed with relevant insights on the obsolescence status of their construction equipment, contractors shouldn’t wait for a piece of equipment to become obsolete or to hear about it from their suppliers before stocking up on components for such equipment.
In other words, when contractors identify obsolescence risks to their equipment, they should evaluate whether it would be prudent to stock up on spare parts, components, and accessories while they’re still relatively available on the market.
These can be sourced from equipment suppliers, component brokers, or original manufacturers before they become unavailable or too expensive.
To sum up, the three previous actions—equipment audit, risk analysis, and communication with suppliers—will allow construction companies to use the insights gained to stock up on necessary equipment components, spare parts, and accessories while they’re still affordable and available on the market.
Conclusion
So, in the first three sections, we explained what equipment obsolescence is, the different types of obsolescence, and the risks of using obsolete equipment.
In the last section, we explored how contractors can use this better understanding of equipment obsolescence to efficiently manage it, thus avoiding or minimizing operational and financial risks for their business.
We hope this article will help you improve equipment obsolescence management in your business, leading to reduced equipment costs, higher employee productivity, and happier clients.