Construction companies rely heavily on a wide array of tools, equipment, and other assets to complete their projects on time, within budget, and with a healthy profit margin.
However, it’s no secret that the loss, theft, or inadequate maintenance of these valuable resources can significantly impact any of the parameters listed above.
If you’re a construction company owner or manager who understands the gravity of these challenges, you’re likely looking for practical tips that can help you establish an effective tool management system.
Here are seven of them.
In this article...
Go Paperless With Tool Management Software
To start with, it’s important to replace pen-and-paper and spreadsheet-based tool management processes with digital, cloud-based, automated tool management software.
Simply put, manual tasks required to keep track of your tools and equipment through paper forms and Excel spreadsheets are too time-consuming and error-prone to enable effective tool management.
Conversely, the automation provided by tool management software will save valuable time, reduce the risk of human error, improve worker accountability, and increase productivity.
Moreover, when the software is cloud-based, it provides instant accessibility and real-time updates on the location and status of each tool to all users (workers and managers) at any time, from any place, and using any internet-connected device.
So, what features should an effective tool management software have?
Here are some essentials.
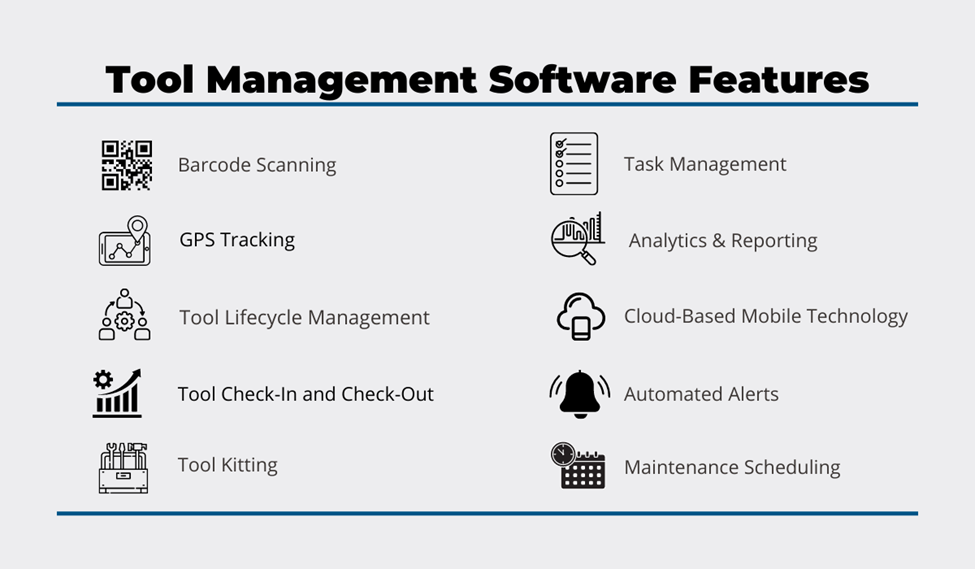
We won’t go into specifics of each feature (other than the cloud technology we just covered) as they’ll be revealed in later sections.
Instead, here are some tips on what to do when selecting the right tool management software for your company:
- get your team on board
- identify your tool management pain points and specific needs
- determine whether short-listed software solutions have all the above features
- prioritize the software’s ease of use (and affordability)
Finally, as nothing beats a practical example, it’s worth noting that our tool management software, GoCodes, provides all these features—and more—in one package, coupled with a simple setup, minimal training, and strong customer support.
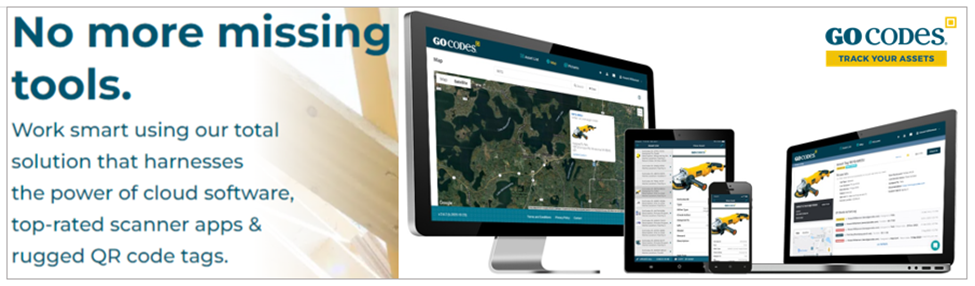
Simply put, tool management software like GoCodes allows you to go paperless, generating benefits like time savings, accurate tool inventory data, and real-time visibility into the location and status of your tools.
To recap, our first tip is to digitize and automate your tool management workflows with the help of software that’s easy to use, affordable, and has all the essential features for effective tool management.
Attach QR Code Labels to Your Tools
A crucial component of any digital tool management system is the unique identifier—typically a barcode/QR code label—affixed to individual tools and equipment for tracking and management purposes.
After such labels/tags are attached to your tools, they can be scanned with smartphones and tablets using a built-in scanner provided as part of your tool management solution.
Although some construction companies still use traditional barcodes and special handheld barcode scanners, these technologies are quickly being replaced by their more advanced and cost-efficient counterparts—QR codes and in-app scanners.
Below, you can see all the components of a practical tool tracking and management system, namely the cloud-based app, built-in scanner (in action), and rugged QR code labels.
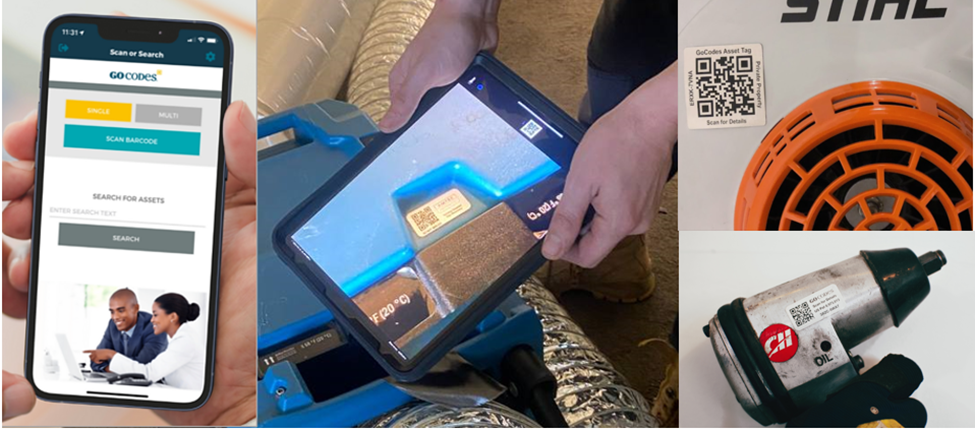
Once labels are attached and the tool management system is populated with initial data, they’re used to track assets (their location, usage, availability, maintenance status, etc.) in real-time.
In other words, workers and managers can scan the QR code label—or log into the app—to access the individual tool’s info page and the software’s central database of all tracked tools and equipment.
Tool labels/tags can be made from various durable materials that can withstand the often harsh jobsite conditions.
They are the backbone of effective tool management as they enable your company to deploy a range of other tool management features we’ll discuss below.
Best of all, when these QR code labels are GPS-enabled, they can be used to automatically record the GPS location of a tool every time someone scans its label.
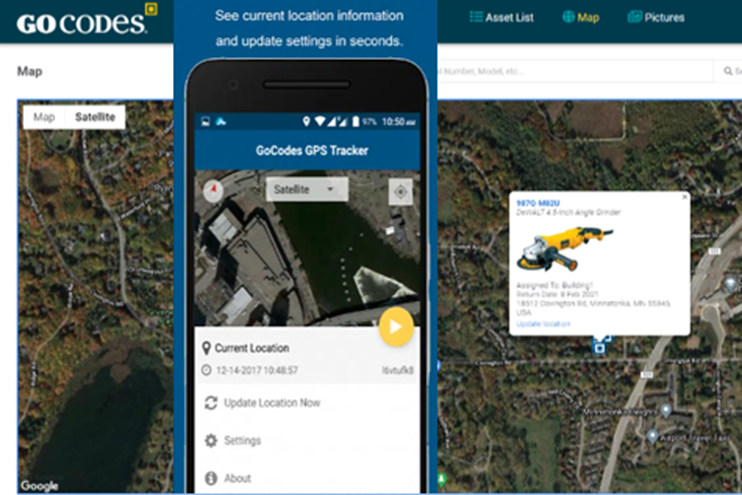
The fact that the software’s GPS tracker automatically records where tools are and who is using them gives rise to minimized tool loss and theft, increased worker accountability, and improved overall tool maintenance and management practices.
Furthermore, when tools are misplaced and left behind—or stolen and abandoned—rugged QR code tags serve as proof of ownership, and anybody who finds a tool and scans its tag can easily report their discovery.
To summarize, QR code labels are the simplest and most cost-efficient way to track the location and usage of your tools in real-time, thus enabling you to effectively manage them with the help of tool management software.
Make Use of Tool Kitting
Taking advantage of your tool management software’s kitting feature can further simplify and improve tool tracking and management practices, making the system more efficient.
But let’s first explain what tool kitting is.
Simply put, QR code labels can be attached to multiple tools, such as a toolbox, shipping container, or truck, and entered into the software system as a single asset (“kit”).
From there, you can add different tools to these kits, and they’ll cease to be treated as individual assets and start being regarded as the components of a specific kit.
For example, you might want to add a circular saw to the collection of tools destined for a specific jobsite that will be transported there in a particular vehicle.
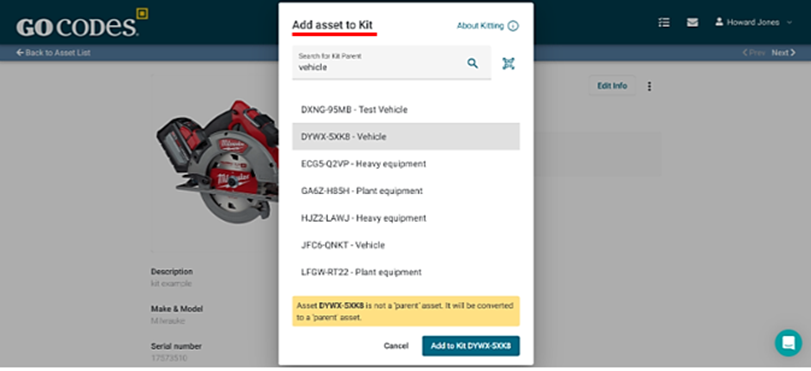
In essence, kitting allows you to track, allocate, and manage groups of tools instead of doing that for each tool.
For instance, the equipment manager can create a tool kit and assign it to a worker who will need those tools to complete a specific construction task.
Overall, making use of tool kitting can help you better organize and simplify tool allocation, scheduling, maintenance, and transport, thus making your tool management more effective.
Hold Employees Responsible for Tools
Holding employees accountable for the tools they’re using with the help of your tool management software’s check-in/check-out feature can significantly reduce theft, misplacement, or negligent handling of your construction tools.
Once you’ve replaced paper/spreadsheet-based tool management processes with cloud-based software and attached QR code labels to your tools, these elements allow you to establish a largely automated, simple, and quick tool check-in/check-out system.
In other words, workers can now simply scan a specific tool (or tool kit) with their smartphone when checking it out from a tool room or storage and scan it back into the system when they return it, creating a transparent chain of custody (as exemplified by the check-in/out log shown below).
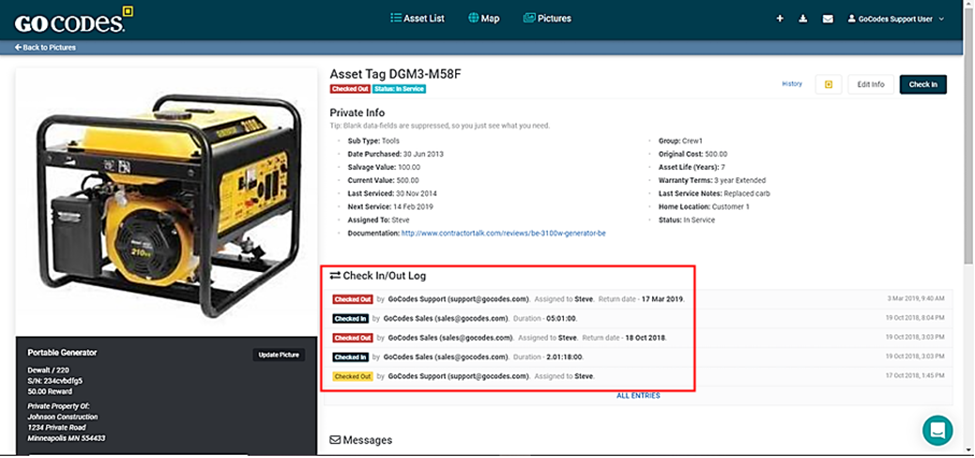
This functionality lets workers quickly assume responsibility for their tools when taking them from storage (as a self-service or under supervision) or exchanging them with another worker on the construction site.
At the same time, they can easily check the availability of any tool, see whether it’s used, by whom, and when it will be returned.
As for managers, they can use this feature to reserve and assign tools, set return dates and automated overdue reminders, schedule maintenance, and track tool utilization over time.
The ultimate result of this check-in/check-out feature is that you can hold employees accountable for tools, thus minimizing tool misplacement, theft, and careless handling and improving tool allocation, maintenance, and utilization.
Set Up Automated Maintenance Alerts
Another useful feature of your tool management software is the ability to plan, schedule, and monitor regular maintenance tasks related to your tools and equipment and set up automated maintenance alerts.
In other words, since the software enables users to view and update info on any asset’s mechanical health, maintenance status, and general performance, this allows managers to schedule and track the execution of future maintenance tasks.
Put simply, they can use the tool management app to set the date of an upcoming service task and assign it to a specific service technician, like in this example.
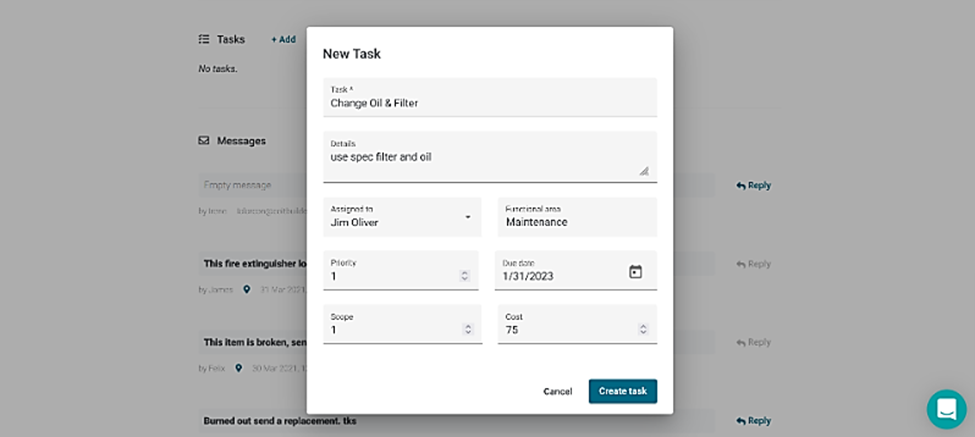
Moreover, they can ensure that they themselves, the assigned technician, and other relevant staff members receive an automated scheduled maintenance alert via email (and within the app), which ensures regular maintenance tasks will be done when scheduled.
Here is an example.
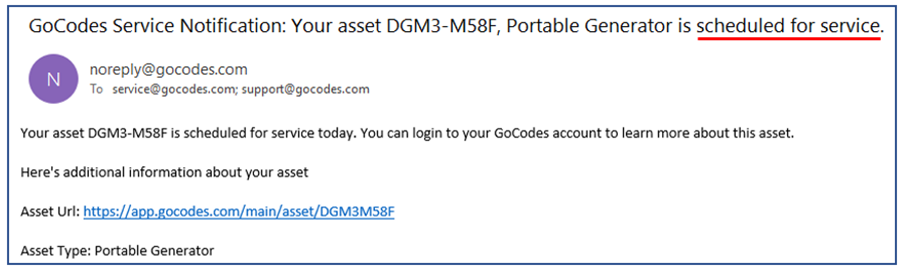
Naturally, these maintenance scheduling and notification functions help construction companies operationalize their preventive maintenance plan while enabling them to track tool usage and wear-and-tear and ensure timely repairs/replacements.
As for automated alerts, they can also be used to notify users of low inventory levels of spare parts, accessories, and other supplies needed for regular maintenance.
Therefore, the ability to schedule future maintenance tasks and set up service and low inventory notifications significantly contribute to more effective tool management.
Ensure Your Tools Are Stored Securely
Another tip for effective tool management is ensuring that your tools are correctly (i.e., safely and securely) stored.
In other words, your actions aimed at managing tools more efficiently might be derailed by something as simple as leaving tools unprotected from the elements and thieves, failing to clean tools before storage or conduct pre-storage maintenance.
For example, in the case of power tools, consider how these storage mistakes can reduce their lifespan and jeopardize their performance:
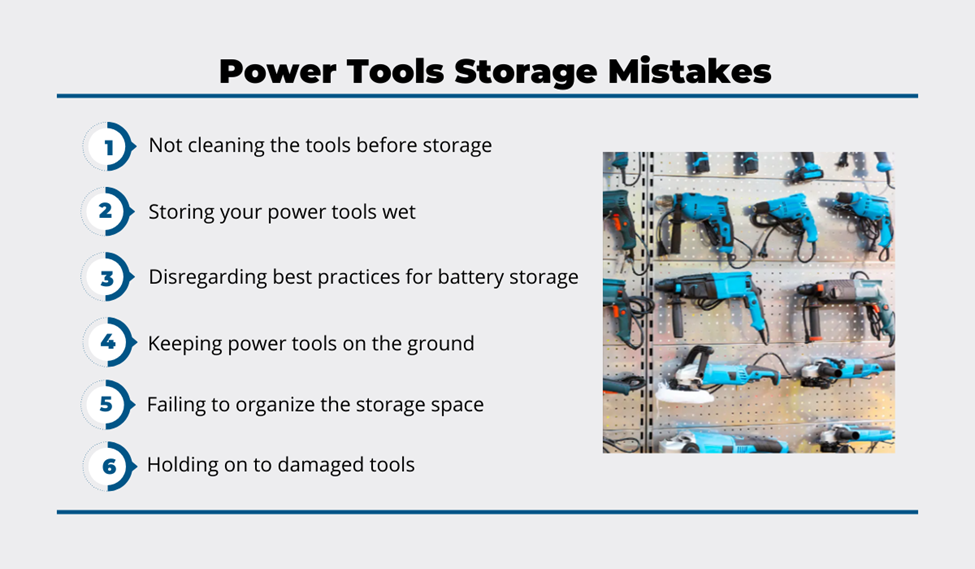
Therefore, avoiding such mistakes and ensuring appropriate storage conditions for your tools and equipment according to their specific requirements is an important part of effective tool management.
All in all, secure and organized storage of your construction tools will ensure they maintain their performance, prolong their lifespan, and enable workers to quickly find them when needed.
Perform Tool Audits on a Regular Basis
Performing regular tool audits—reviewing what tools you have, their current condition, and usage history—can make your tool management even more efficient, particularly when such audits are digitized and automated.
Of course, to get there, you need to choose and deploy your tool management software (QR code labels included) and populate the software’s central database with relevant data about each tagged and tracked tool.
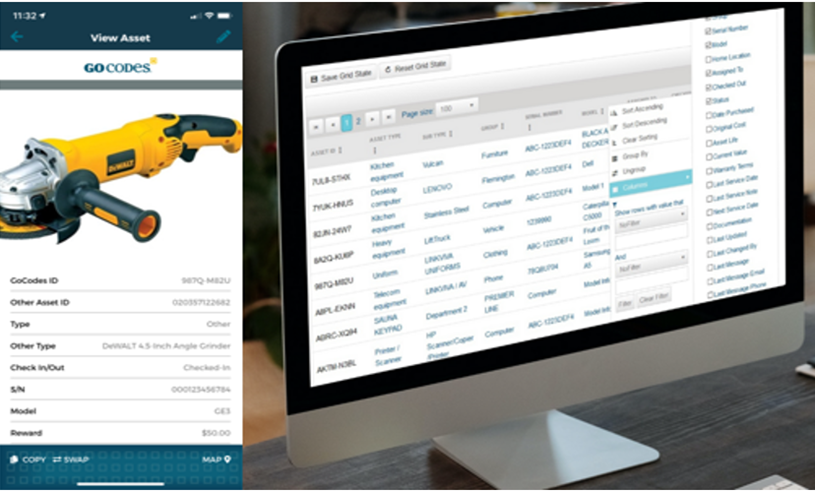
Simply put, all your future tool audits will be simpler, quicker, and more accurate if your initial audit is properly performed, ensuring that the data entered in the system is verified and up to date.
In practical terms, this means that each tool’s info page (and thus also the central database) should include basic data like its name, type/model, serial number, purchase date, price, and warranty expiration.
In addition, the initial audit—and all subsequent audits—should also collect data on all performed maintenance activities and/or inspections, the tool’s current condition, and its expected lifespan, to name a few.
Once the software system is established, your employees will be able to use the software’s audit mode, which allows them to scan multiple tools at once, which adds to the easy and quick performance of tool audits.
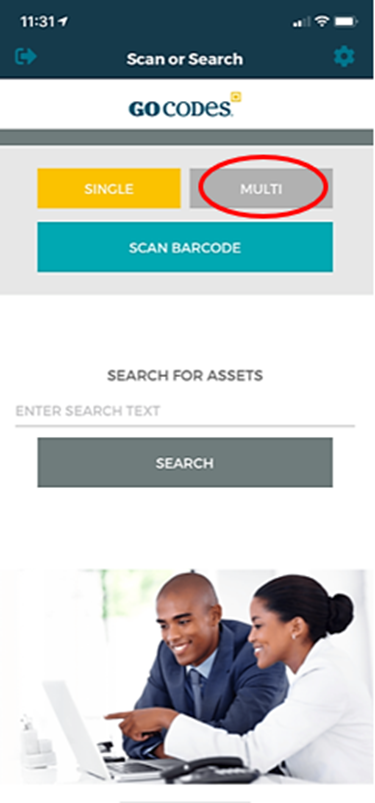
To sum up, performing digitized and automated tool audits on a regular basis helps you leverage tool tracking data and make better-informed decisions about your company’s future tool allocation, procurement, and maintenance practices.
Conclusion
If we were to roll these seven tips for effective tool management into one, the key message would be to get a simple and affordable tool management software with QR code labels, which will then provide you with efficient ways to improve your company’s overall tool management.
Our own solution, GoCodes, is a reliable option in this sense.
Naturally, real-time tracking and control of your tools and equipment will allow you to minimize tool theft and loss, maximize tool utilization, reduce maintenance and purchasing costs, and increase your company’s productivity and profitability.