If you’re in construction, you know that keeping track of inventory across several job sites and warehouse locations can be, to put it mildly, frustrating.
Issues like running out of critical materials mid-project, missing tools and equipment causing delays, or wasting time on manual record-keeping often indicate it’s time to rethink your construction inventory management practices.
In this article, we’ll explore five common signs that you need inventory management software and explain how the right solution can streamline your operations, reduce costs, and ensure smoother project workflows.
In this article...
You’re Having Difficulties Tracking Inventory
If your construction business struggles to keep track of materials, tools, and equipment across multiple job sites or warehouses, this indicates a need for better inventory management.
Inventory tracking issues can manifest as:
- misplaced materials, stockouts, and overordering
- uncertainty about current stock levels,
- lost, stolen, or poorly maintained tools and equipment,
- challenges in determining which items are allocated to which projects or locations, and
- frequent discrepancies between recorded inventory levels and actual inventory counts.
The above problems are common to many construction companies, and usually stem from a combination of two factors:
- general complexity of construction operations (number of people, materials, and tools involved), and
- ineffective inventory management methods.
So, how can construction inventory management software help address these issues?
To answer, we’ll use our inventory management solution, GoCodes, as an example.
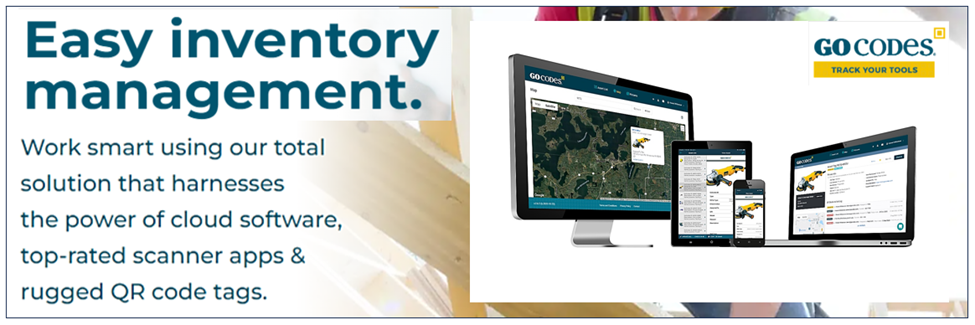
GoCodes is a cloud-based software solution that comes with an app containing a built-in digital scanner.
This scanner is then used to track and manage construction inventory by scanning the QR code tags attached to inventory items.
This means that GoCodes, unlike some more traditional inventory management systems, operates on devices you already own and requires no special, handheld scanners.
The only “hardware” you need are QR code labels, preferably made from durable materials that can withstand often harsh construction site conditions.
GoCodes offers a variety of label options, allowing you to choose the most suitable ones based on the inventory type you want to track.
You can see some examples of our labels in action below:
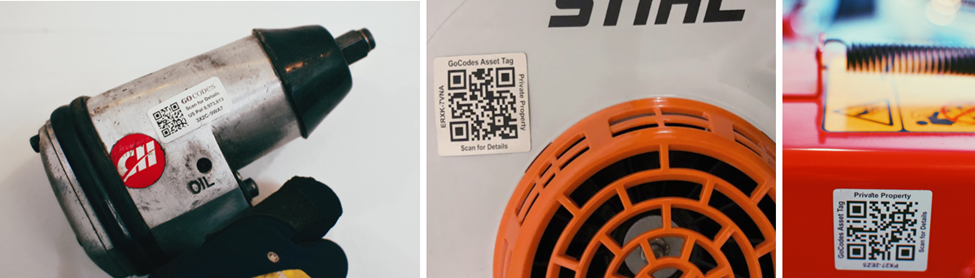
When these labels are attached to inventory items and connected with the software’s database, this opens up a range of tracking and management features.
For example, in the case of consumable inventory like materials and supplies, you can track their location (recorded every time the QR code label is scanned) and their current stock levels.
This minimizes cases of materials and other items getting lost, running out of stock, or being overordered due to poor record-keeping.
For more durable tools and equipment, you can use QR code labels to track their GPS location, users, and maintenance status.
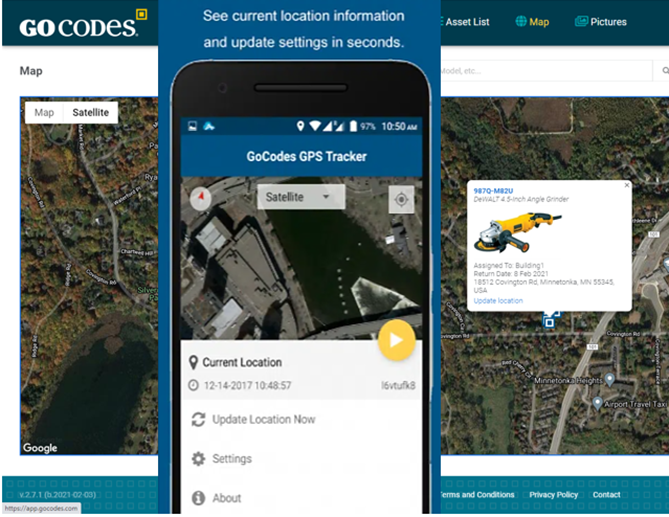
As illustrated, the current user and location will be recorded automatically when a worker scans a tool using their smartphone or tablet.
This is ideal for tracking smaller, less costly inventory items, while heavy equipment and expensive machinery can be further protected by our active GPS trackers.
From an inventory management perspective, scan-based tracking is often sufficient to minimize inventory misplacement, theft, and poor maintenance.
As you can see, the right inventory management software allows you to address all the inventory-tracking difficulties we outlined, including allocation issues and mismatching records when doing inventory counts.
You Waste Time Using Manual Inventory Management Methods
Another sign that you need inventory software involves relying on time-consuming and error-prone paper logs or Excel spreadsheets to manage your inventory.
For instance, handwritten inventory logs can result in illegible entries, misplaced documents, and difficulties in accessing real-time inventory data.
Even though they’re digital, spreadsheets are also cumbersome to maintain and prone to errors, especially as your inventory grows and becomes more complex.
To illustrate, here are some downsides of using spreadsheets for inventory management:
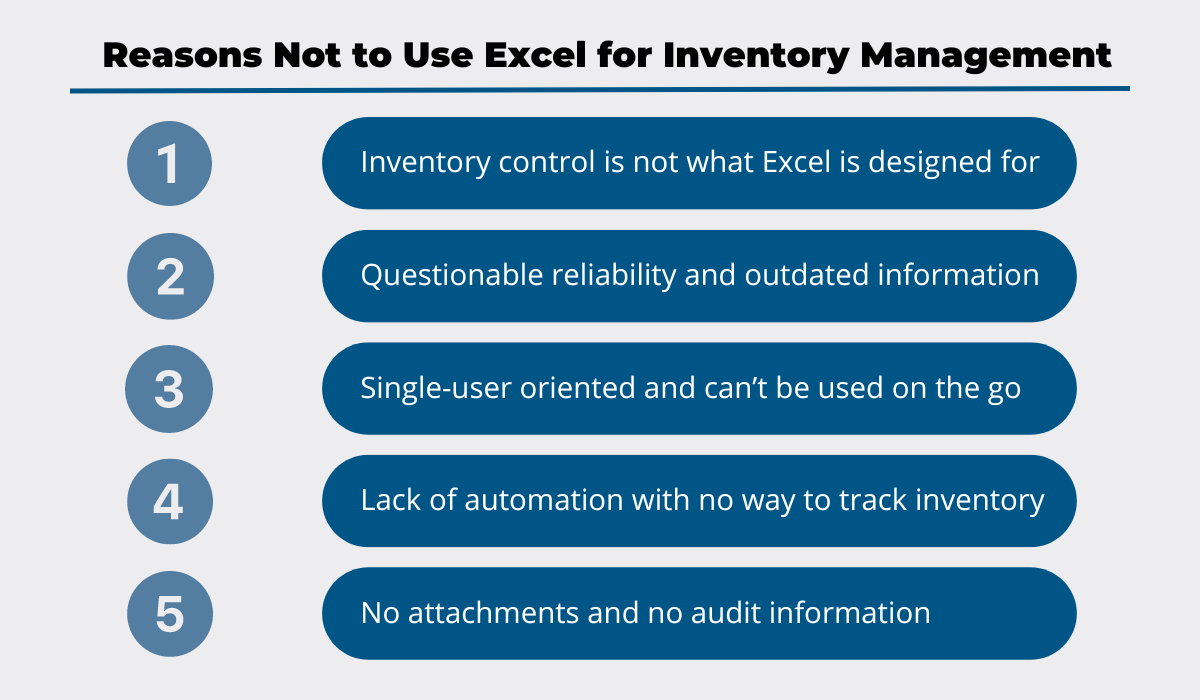
Since these disadvantages apply to paper-based inventory records as well, it’s clear that both of these manual methods have serious drawbacks that result in errors and wasted time.
Conversely, automation through inventory management software can streamline processes, reduce human error, and free up your staff’s time for more strategic tasks.
For example, instead of spending excessive time on data entry and paperwork, you can utilize in-app scanners to automate inventory tracking and data capture.
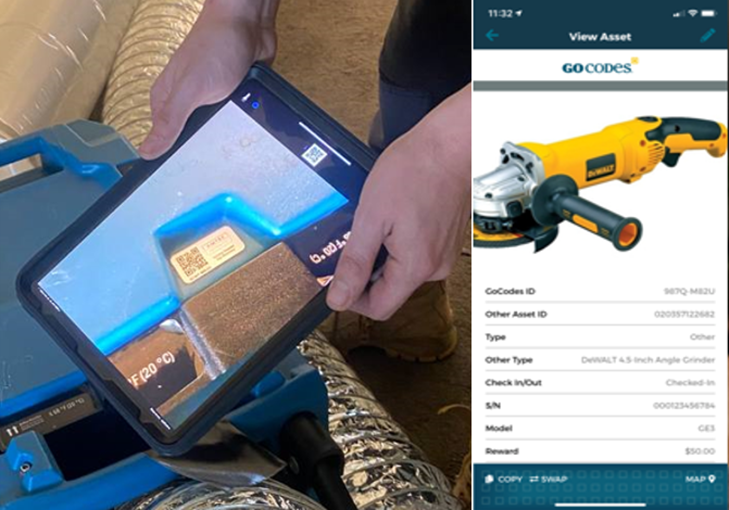
In practical terms, this means that a worker can take and return inventory like tools and equipment with a few clicks in the app.
This not only saves time when inventory is checked out and back in but also minimizes record-keeping mistakes associated with manual methods.
Another important time-saving functionality of digital inventory management software is its central database, or the list of tracked items.
More precisely, all stakeholders—workers, managers, and service technicians—can use any internet-connected device to access the software’s database and find exactly what they’re looking for in a few seconds.
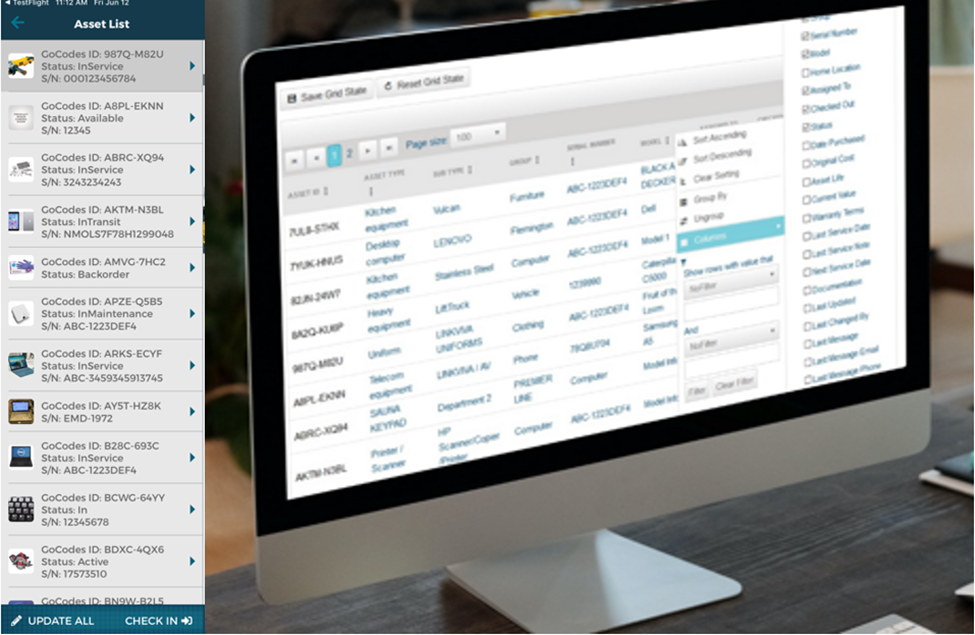
For example, when an on-site worker needs a special tool, they can use the app to check whether that tool is available, who is using it, and where it’s located.
Compared to calling the site supervisor or equipment manager and waiting for a response, using the app provides instant access to real-time information, thereby saving time for all involved.
So, if you’re still using time-consuming and inefficient manual methods, that’s a clear sign you need a mobile inventory management app.
Ultimately, such software will streamline inventory-related processes, automate data entry, minimize errors, and seriously cut down the time spent on administrative tasks.
You’re Experiencing Project Delays Due to Inventory Issues
When projects encounter delays due to inventory issues, this indicates inefficiencies in management processes.
For instance, let’s say your construction project requires a specific quantity of steel beams to be delivered to the site by a certain date to meet the construction schedule.
Without an efficient inventory management system in place, the project manager has to rely on manual record-keeping to track the inventory of steel beams.
If the inventory data is not updated, they can easily miscalculate the required number of steel beams and order insufficient quantities, leading to stockouts and delays in construction progress.
This is more common than one would expect, which is evidenced by the findings from a 2022 survey by Cornerstone Projects:
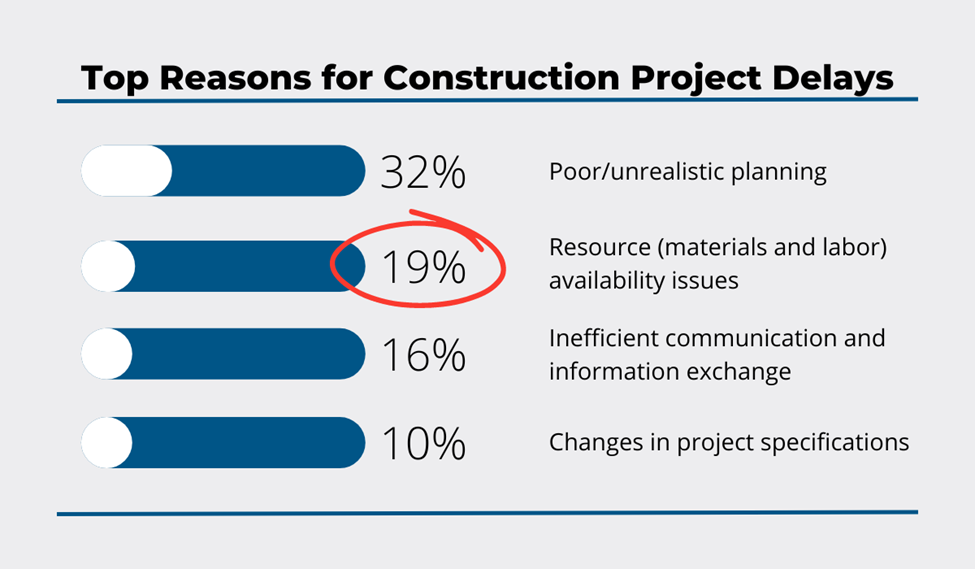
As highlighted, inefficient resource management ranks second among the top causes of project delays provided by the surveyed construction professionals.
Moreover, the cited percentage does not account for delays caused by poor allocation and scheduling or substandard maintenance of tools and equipment.
To avoid these inventory issues, construction companies need to optimize their inventory levels and ensure that materials and other supplies are available when needed.
This is where inventory management software can help by allowing managers to maintain accurate inventory records, track material usage, and set up automated low inventory alerts.
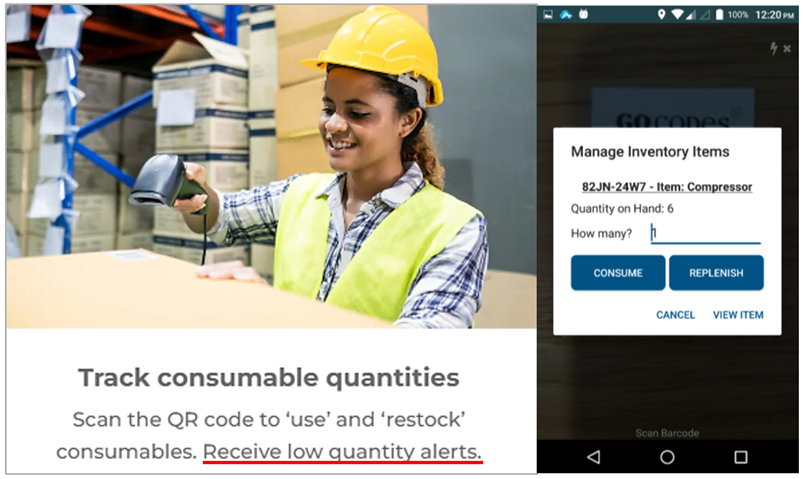
As illustrated, the software can be easily configured to automatically email the responsible persons you designate when a certain inventory item’s stock level reaches the predetermined number.
That way, they can order the necessary supplies on time, thus minimizing potential delays due to stockouts.
Overall, accurate and up-to-date inventory data—along with automatic inventory level monitoring and alerts—enables managers to make informed decisions and take proactive measures to prevent inventory-related delays.
You’re Incurring Unnecessary Costs
Standing opposite to delay-causing inventory shortages are unnecessary costs incurred by overordering or repurchasing materials or tools you already have.
Although this won’t cause project delays, it will tie up valuable capital and storage space unnecessarily, leading to wasted resources and extra costs.
Such unnecessary inventory costs are generated when a construction company is unaware that it already has specific items in stock due to inefficient inventory management.
For instance, if your company has unused cement bags in storage, but the staff involved in preparing the next project is unaware of that, they will order the quantity of cement estimated during material takeoff.
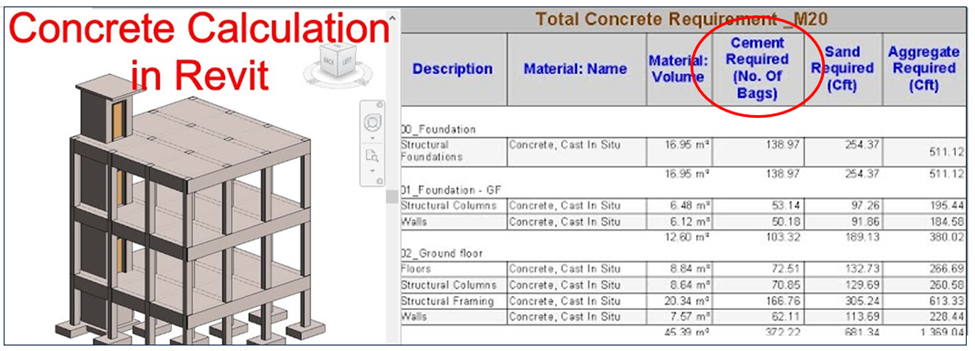
This miscalculation will then lead to your company having even more cement bags in stock.
Furthermore, cement and most other materials and supplies have an expiration date, and their quality deteriorates over time, making them unfit to be used in construction after sitting in storage for too long.
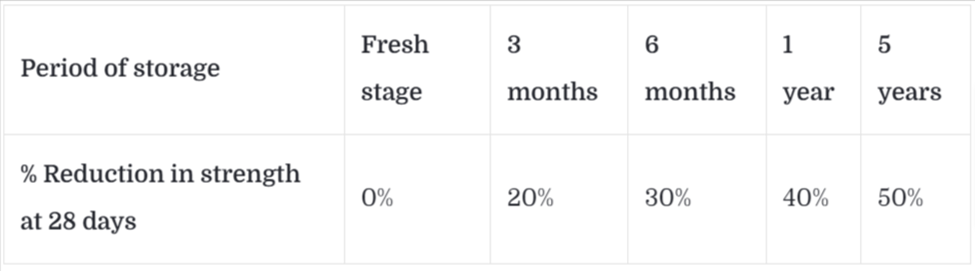
This simple example of how overstocking occurs and how materials lose their effectiveness again underlines the need for better inventory control and management using software.
More precisely, inventory management software enables you to avoid unnecessary inventory costs by:
- providing full visibility and real-time tracking of inventory to prevent overordering or repurchasing of supplies already in stock,
- receiving automated low-quantity alerts based on preset inventory thresholds to ensure timely replenishment of stock, and
- implementing mobile barcode or QR code scanning to accurately record and track inventory movement in real time, reducing the risk of misplaced or lost inventory.
By leveraging these software capabilities, you can optimize inventory levels, minimize waste, and reduce unnecessary costs.
As we’ll see next, you can also utilize the software’s demand forecasting features to anticipate future inventory needs and optimize stock levels accordingly.
You’re Unable to Forecast Future Inventory Needs
Without accurate data and analytics, it’s challenging for construction companies to forecast future inventory needs or plan procurement activities effectively.
This inability to anticipate inventory requirements can lead to stockouts and project delays, or unnecessary overstocking, all of which can impact a company’s operational efficiency and profitability.
To tackle this issue, you can leverage the data collected by inventory management software along with its predictive analytics and forecasting capabilities.
For example, by using historical data on average inventory utilization on past projects, you can generate detailed inventory reports and analytics.
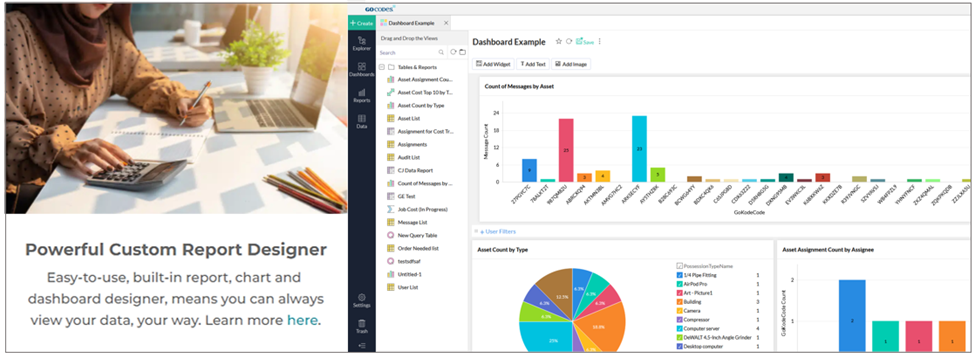
You can use the insights from these reports and analyses to compare them against inventory requirements and tentative schedules of upcoming projects.
When that data is cross-referenced with the latest info on the availability and pricing of materials and other supplies on the market, you can:
- create more precise inventory forecasts,
- make informed decisions about inventory levels,
- reduce the risk of stockouts or overstocking, and
- minimize inventory-holding costs.
All in all, inventory management software enables you to leverage data-driven insights and predictive analytics to forecast future inventory needs more accurately and efficiently.
Ultimately, it allows you to streamline inventory management processes and adjust your procurement strategies to align with anticipated inventory demands.
Conclusion
If you recognize any of these common signs of construction inventory challenges, it’s time to take appropriate steps and find the right software solution.
With features like location tracking, predictive analytics, and automated processes, inventory management software will empower your construction team to make informed decisions, optimize inventory levels, and improve overall project outcomes.
By leveraging modern inventory management software, you can streamline operations, minimize delays, and maximize profitability, which are key to staying competitive and successful in today’s construction industry.