For better or worse, there is an abundance of inventory management solutions available in today’s market.
With so many options out there, choosing the right one can be somewhat daunting, as they all seem to blend together at first glance.
Still, not all inventory management software solutions are created equal, and there’s a method to finding the perfect fit for your needs.
But, to unlock that ideal match, you must kick off your journey by defining your specific software requirements.
This is where this article comes in.
In it, we outline the seven key qualities to prioritize when selecting your new inventory management system and explain why exactly they are so important.
We also offer some research-based insights and actionable tips to further aid in your decision-making.
Let’s dive in.
In this article...
User-Friendly Interface
Lack of user-friendliness can be a significant barrier to achieving widespread software adoption among personnel.
An interface that’s difficult to navigate, overly complex, or prone to frequent crashes breeds frustration, wastes time, and ultimately discourages the team from using the technology.
According to a survey from Userlane, three-quarters of workers across various industries believe that struggling with software use impedes their productivity and slows them down.
The survey shows that, on average, 2.33 hours per week are spent on addressing software-related issues.
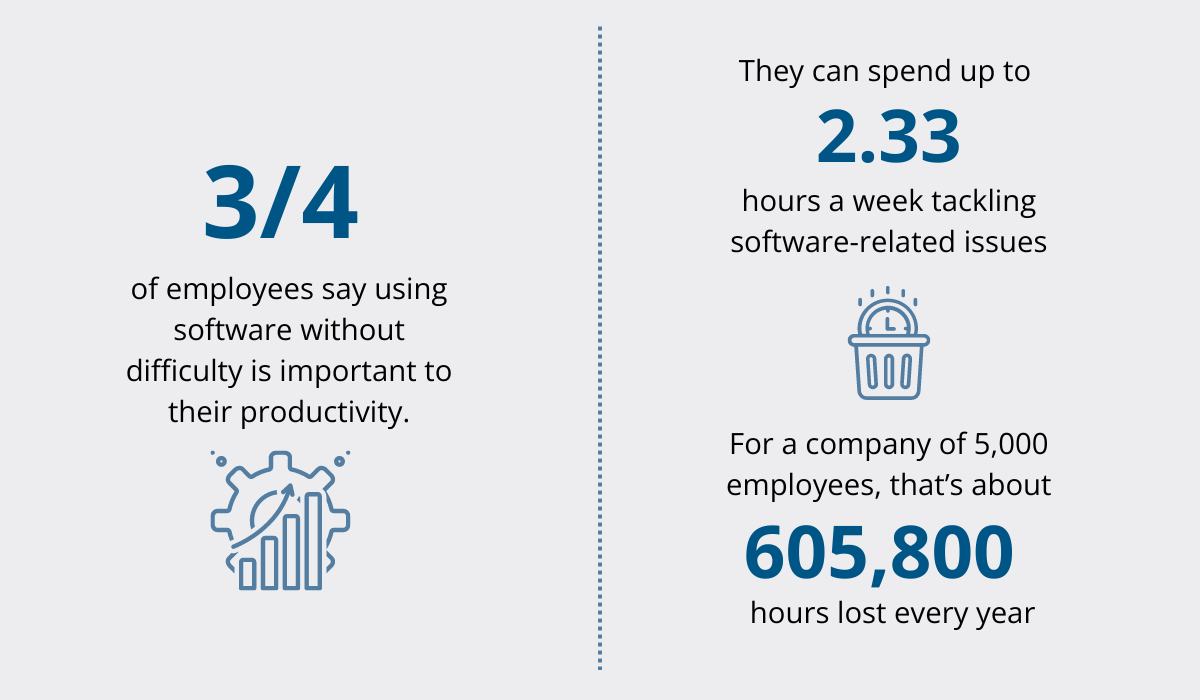
No wonder workers don’t exactly jump for joy at the thought of using systems that cause them that much trouble.
However, it’s not just individuals who suffer when software falls short on the user-friendly scale.
Companies feel the sting too.
Userlane highlights that inadequate technology adoption results in:
- increased training and system maintenance expenses,
- diminished return on investment from software purchases, and
- even more resistance to future attempts at technological improvements.
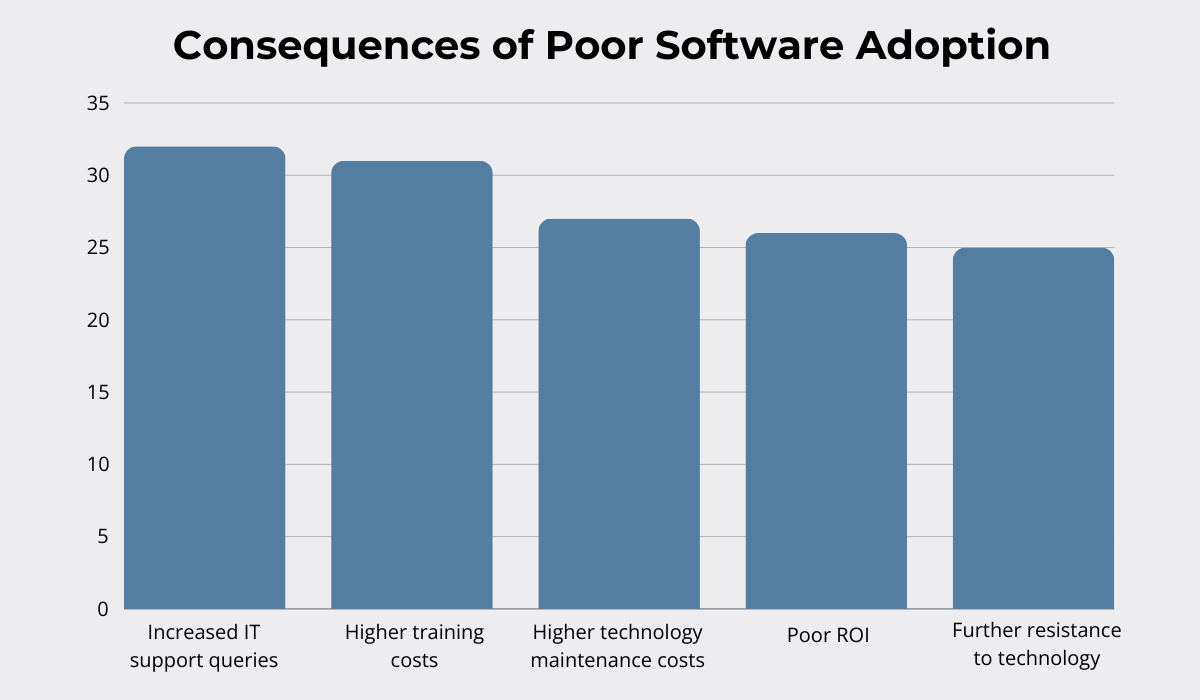
Put simply, user-unfriendly solutions can detrimentally affect both employees and overall company performance.
To mitigate these challenges, look for a solution that has the following attributes:
- Intuitive navigation
- Seamless update processes
- Appealing visual design
- Minimal training requirements
The best way to ensure you’re getting what you need from your new system is by taking advantage of the free trials typically offered by software vendors.
This will allow you to thoroughly explore all of the solutions’s capabilities without an immediate financial commitment.
Once the whole team is on board, then you can take the plunge and make it official.
Comprehensive Inventory Tracking
Robust inventory tracking capabilities are another absolute must.
This entails the ability to keep tabs on everything: from heavy machinery to tools, materials, and even everyday consumables.
And it’s not just about knowing where they are, either.
The system must also track who’s using them, how much, when, and for what purpose.
Without this level of insight, an inventory management system falls flat and, in a way, defeats its purpose.
You need such information to properly allocate your resources, protect them from theft, and, ultimately, ensure the job gets done on time and within budget.
For example, a lack of visibility into tool usage can cause a serious dip in productivity, says Michael McGowan, Region Head and CEO of Hilti North America:
“Our research shows that each job site loses on average one day per month of productivity due to workers searching for tools. In addition, the contractors end up spending up to 90 hours per month tracking tools: in essence, productivity loss for both workers and contractors due to lack of an effective asset/tool management platform.”
The same goes for all types of assets.
How can you manage them effectively and make sure your team has what they need if you don’t have your eyes on the inventory utilization patterns?
Now, you might be wondering: is it possible to find software that’s both user-friendly and packed with all the right features?
It’s a valid concern.
Too many bells and whistles can sometimes make a software solution overwhelmingly complex. This is called feature creep.
However, worry not.
There are solutions that offer a perfect blend of robust functionality and simplicity.
Just take our inventory management solution, GoCodes, as an example.
It combines cloud-based software, a scanner smartphone app, and QR code asset labels to provide up-to-date, detailed, and always accurate inventory data.
Using the system is straightforward, too: affix labels to assets, scan them with the app, and access features such as:
- Asset check-in/out
- Location tracking
- Consumable quantity updates
- Asset assignment to users or projects
- In-field maintenance requests
- Access to data like service history, warranty information, salvage value, and more
- Reporting
In short, GoCodes gives you access to rich asset data and empowers you to take charge of your inventory from any Internet-connected device.
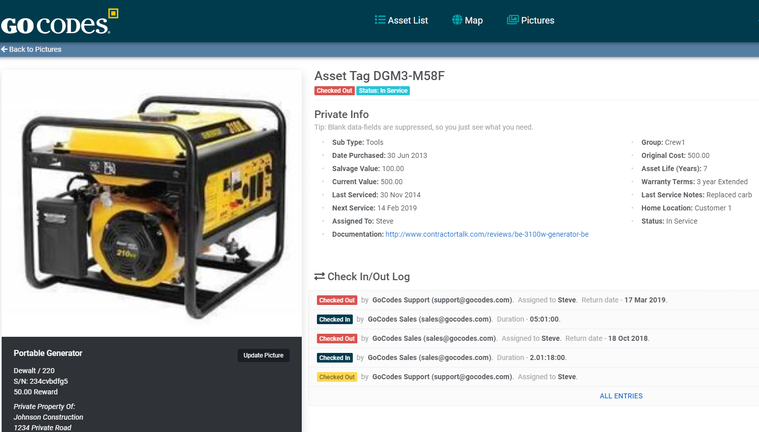
This can be extremely helpful when it comes to risk management and mitigating issues like delays, stockouts, and over-ordering.
Make sure the software you choose can do the same.
It may surprise you how much of a game-changer such capabilities can be.
Integration with Other Systems
When on the hunt for your new inventory management software, don’t overlook the importance of its integration capabilities.
Without smooth integration with vital systems like project management, accounting, or scheduling, you might find yourself stuck in a maze of inefficiency, costing you precious time and money down the line.
According to a 2023 survey conducted by Yooz, almost 20% of workers across diverse industries hit roadblocks in their tasks due to system incompatibility.
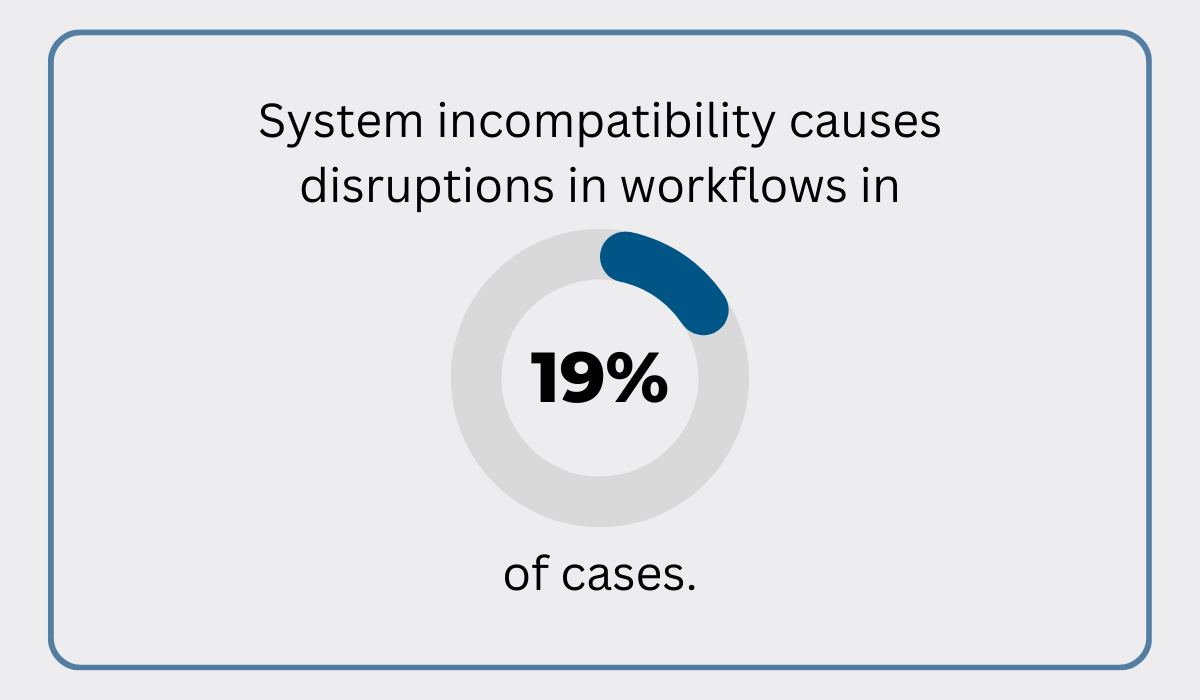
But why does this decrease in productivity happen?
Essentially, it’s because, without integrations, employees are forced into clunky, time-consuming methods of information transfer between systems.
JBKnowledge Construction Technology Report reveals that many individuals turn to manual data entry and spreadsheets when faced with software lacking integration capabilities, methods notorious for their unreliability and susceptibility to human error.
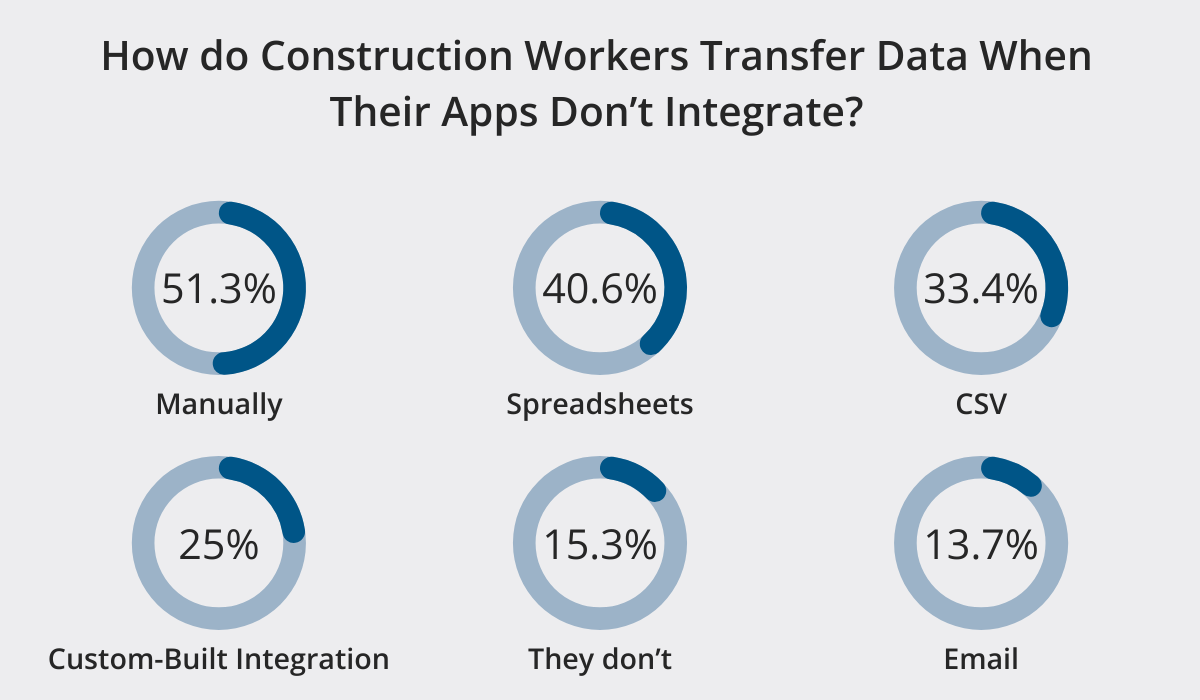
Shockingly, around 15% of users opt not to transfer their data at all in such scenarios, leading to significant data discrepancies and gaps across different systems, ultimately resulting in flawed decision-making processes.
Obviously, this is something you’d want to avoid.
Therefore, before purchase, review the software vendor’s website to ensure compatibility with other systems, or inquire directly if necessary.
This information could prove crucial in determining whether the system aligns with your business needs and objectives.
Mobile Accessibility
Your inventory management software must be accessible not only via desktop computers but also through smartphones and any other internet-connected devices.
Think about it: a significant portion of construction work happens in the field, not in the office.
Mobile accessibility allows you to keep up with the dynamic rhythm of job sites, enabling you to record inventory levels, track material usage, update equipment GPS locations, and place orders on the go.
Essentially, having your inventory management tool in the palm of your hands means you’re always in the loop and ready to act.
It’s not surprising, then, that approximately one-third of construction and engineering businesses are already tapping into the potential of mobile apps in their day-to-day, according to a Deloitte survey.
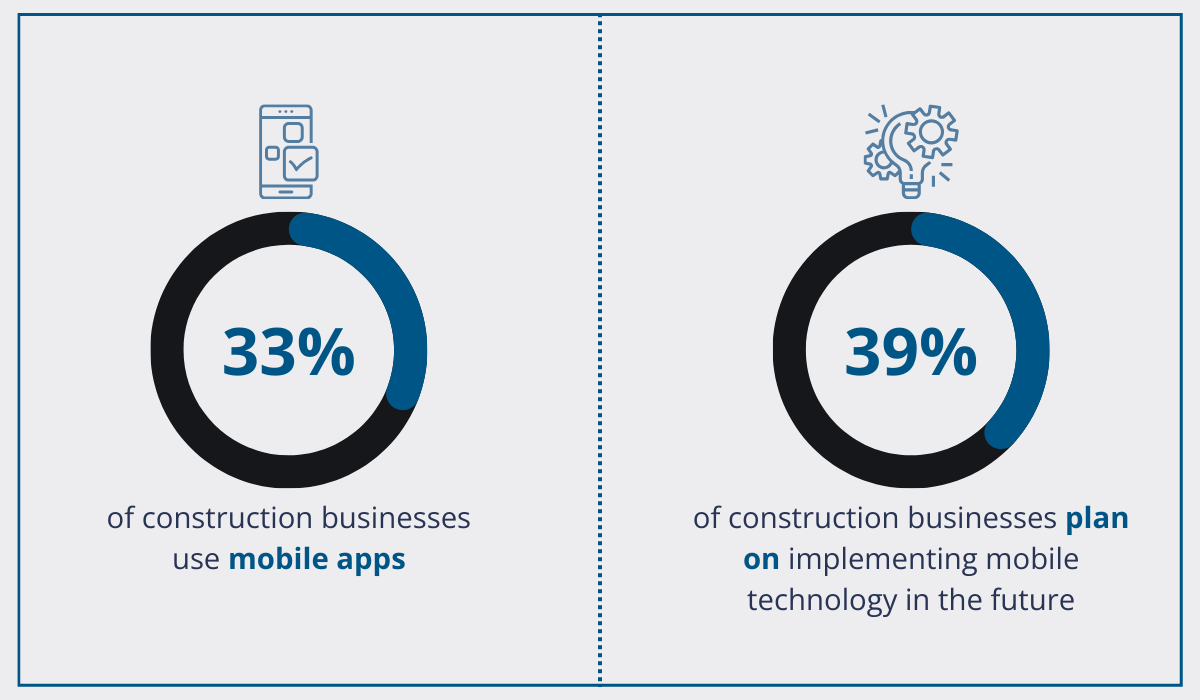
Moreover, the same survey indicates that mobile technology implementation is a top priority for many, with 39% of companies planning to integrate it in the near future.
The bottom line is this: in the fast-paced world of construction, knowing where your inventory is and how it’s used at all times is gold.
Mobile technology doesn’t just make it possible—it makes it easy, convenient, and fast.
Multi-Location Support
Construction projects often extend across different locations, including job sites, warehouses, and offices.
To keep everything organized, you need an adaptable inventory management software that can effectively keep track of all your assets, no matter where they are.
That’s where multi-location support comes in.
This capability empowers you to:
- Monitor inventory levels for various sites in real-time
- Prevent stockouts or overstocking more effectively
- Allocate resources efficiently according to each site’s needs
- Reduce the risk of asset misplacement or inaccurate stock counts
- Minimize excess inventory holding and transportation costs
Essentially, multi-location support boosts the overall visibility, efficiency, and accuracy of your inventory records, helping ensure that all sites have just the right amount of resources for successful project completion.
Imagine being able to catch an idle excavator at job site A just in time to reallocate it and help out employees at site B who desperately needed an extra machine.
With multi-location support, you can anticipate such scenarios more easily and take proactive steps to address them, ensuring smooth operations across the board.
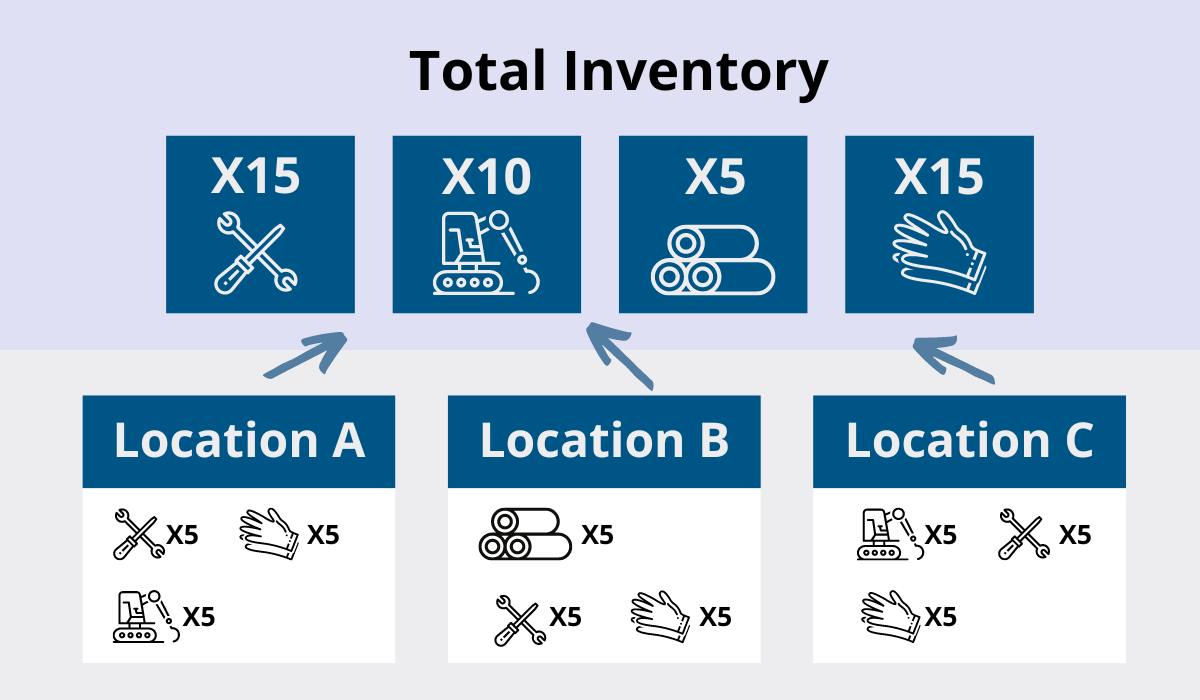
In short, software with this capability makes inventory management across various sites a breeze, helping you reach your project goals and targets with minimal material wastage, workflow disruptions, and budget overruns.
Robust Reporting Capabilities
Reporting and analytics features provide insights into your inventory performance, serving as a foundation for informed and data-driven decision-making.
In other words, inventory control systems with such advanced capabilities allow you to work smarter, instead of harder.
Remember, reporting isn’t just about compiling information.
It focuses more on simplifying data interpretation and offering actionable guidance to optimize your processes.
Troy Dahlin, VP of Heavy Construction Segment US/CAN at Leica Geosystems, echoes this sentiment, noting that, while data collection is important, making it actionable is even more so:
“Contractors who take the time to carefully distill the great amount of production data down into decision-making information will improve their ability to ensure the right machines, materials, and workers are where they should be.”
The analytics function, in a way, bridges the gap between data gathering and implementation.
It automatically creates customized reports, charts, and dashboards that facilitate easier data visualization and comprehension, which, in turn, enables you to spot areas for improvement and mitigate risk with better precision.
Did you know that, according to a survey from Samsara, 95% of construction professionals say it’s precisely the technology that helps them weather various disruptions across all aspects of project management?
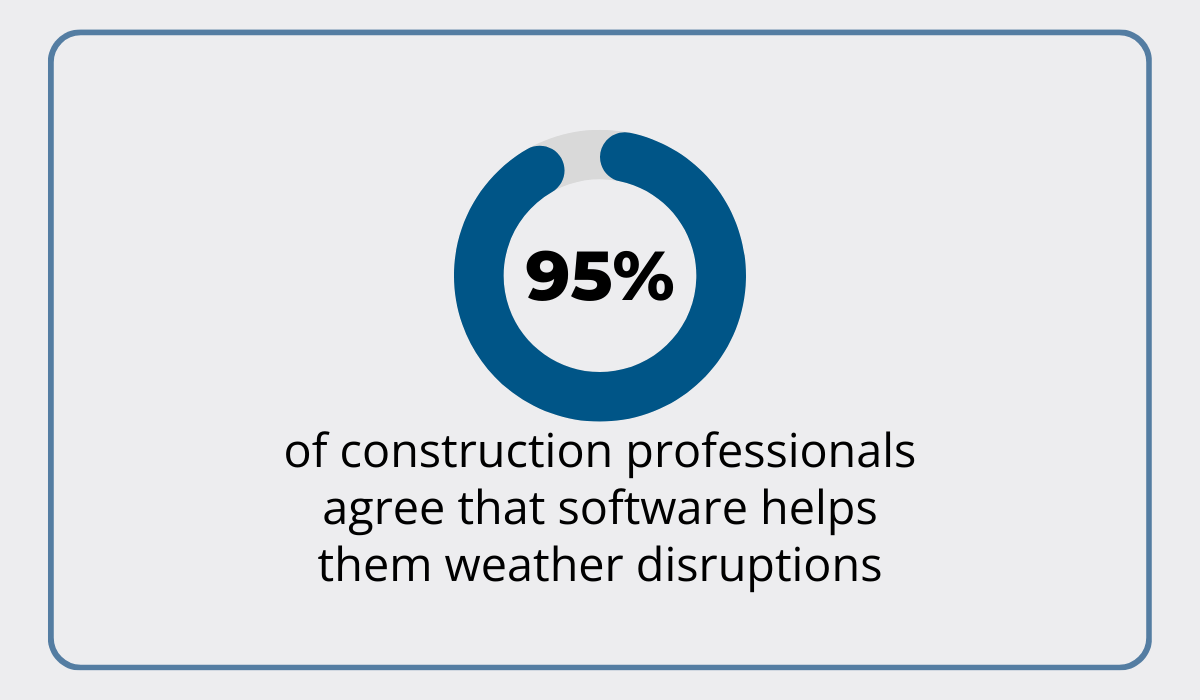
This is mostly because construction software, through its data analysis capabilities, helps you see exactly what’s working and what’s not, enabling you to steer your projects in the right direction before hitting major roadblocks.
Inventory management software with sophisticated reporting capabilities is no different.
It analyzes and provides insight into project resource needs, usage trends, incurred costs, supplier performance, and procurement patterns, eliminating guesswork and guiding you toward better project outcomes.
Scalability
As your business grows, it’s essential that your software evolves alongside it.
Otherwise, you’ll find yourself constantly replacing outdated systems or grappling with performance issues and crashes when your inventory data starts pushing system limits.
These hurdles can throw a wrench into your operations, leading to:
- Workflow interruptions
- Increased expenses for maintaining outdated technology
- Higher costs associated with technology upgrades
- Delays in project timelines
To circumvent these challenges, consider adopting cloud-based solutions.
By storing data in the cloud and operating on pay-as-you-go models, they possess the flexibility needed to seamlessly adjust to your company’s size and demands.
In contrast, on-premise systems, reliant on physical servers, struggle to accommodate changes in business scale.
Granted, they aren’t completely inflexible, but scaling them up means pouring resources into more hardware, which can be costly, resource-intensive, and time-consuming.
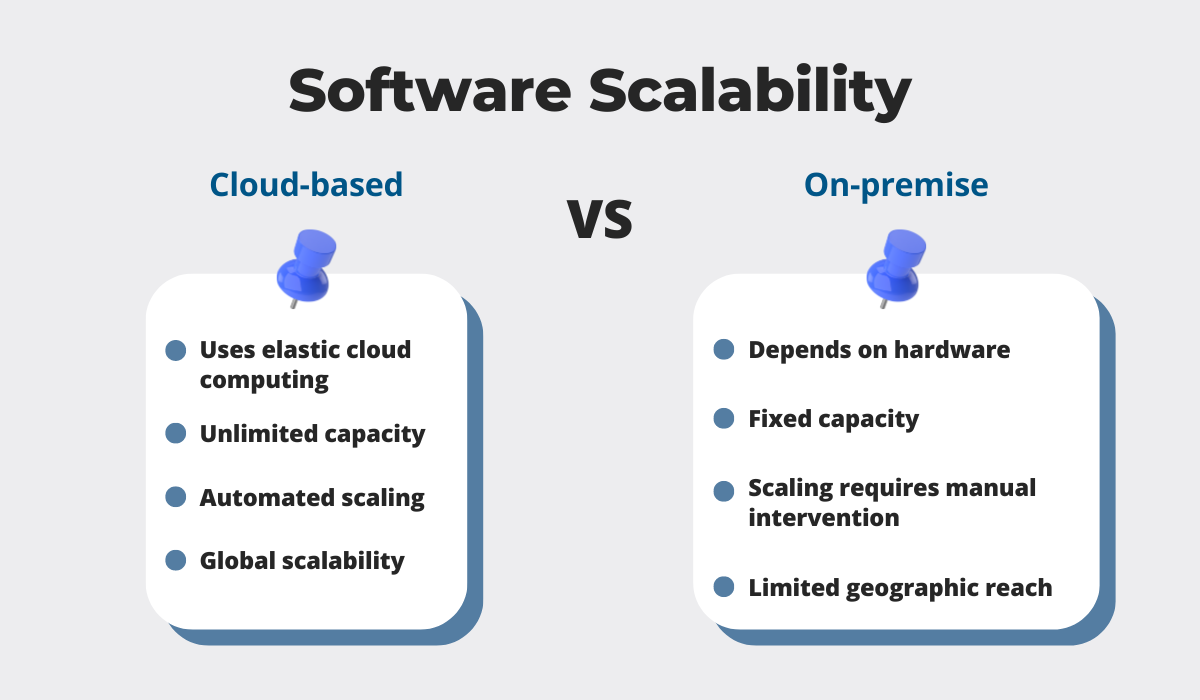
So, before you make a decision, carefully assess which option—on-premise or cloud-based—is better suited to your current and future needs.
A little pro tip: some software vendors offer both types of deployment.
Therefore, if you change your mind down the road but still want to keep the same software or provider, it’s not entirely impossible.
Just make sure you contact the vendor and explore your options beforehand.
Conclusion
We hope that, after reading this article, you’re now armed with renewed confidence to conquer the search for your perfect inventory management solution.
The key takeaway is this: thoroughly study software features, take advantage of those free trials and demos, and don’t hesitate to reach out to vendors if you have any questions.
Oh, and don’t forget the online reviews. They are quite a reliable way to assess a system’s quality.
Good luck!