Key Takeaways:
- Manual tracking causes errors and delays while contributing to higher staff turnover.
- Real-time inventory visibility is crucial for efficiency and security in construction.
- Digital solutions provide real-time location updates, mobile access, and stock alerts.
- With 27% of construction theft committed by insiders, automated tracking ensures employee accountability.
- Robust reporting enables better analysis and decision-making in the face of supply chain disruptions and potential shortages.
Lost tools, misplaced materials, and endless spreadsheet rows—if you think something’s holding back your construction business, look no further than manual inventory tracking.
Keeping track of your inventory across multiple storage locations and job sites is already a challenge, but relying on outdated methods increases the chance of errors and delays.
So, join us in exploring why manual tracking no longer cuts it and how switching to digital solutions can improve accuracy, streamline processes, and impact project success.
In this article...
Inefficiency of the Process
Manual tracking means workers spend hours counting inventory items, updating records, and cross-checking information.
Think about it: When inefficient processes take up a significant portion of your crew’s time, it ultimately impacts your core activities and project success.
Smartsheet’s 2017 research revealed that over 40% of workers across several industries waste at least 25% of their time on manual, low-value tasks such as data entry.
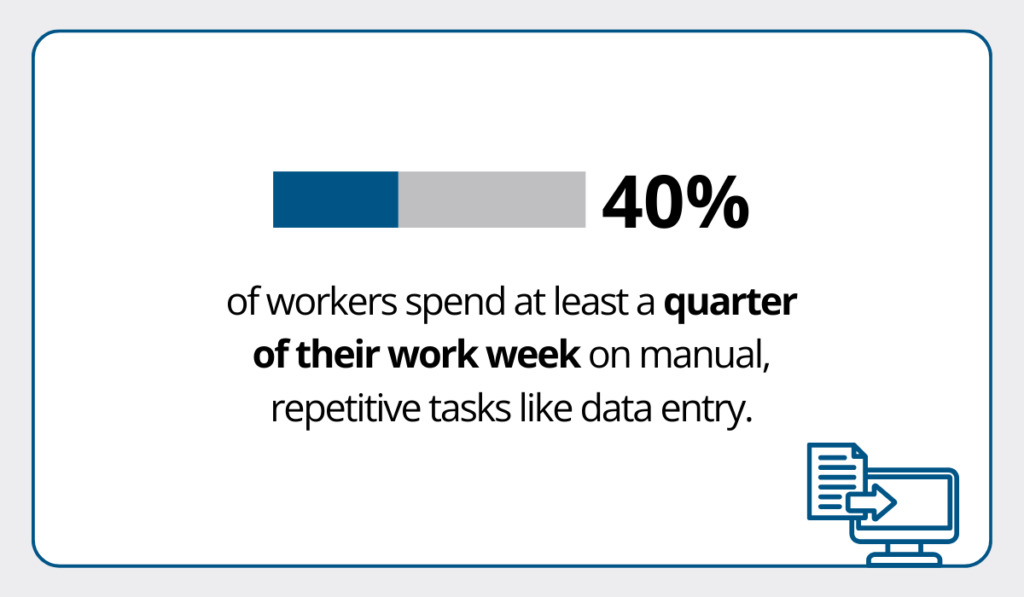
Illustration: GoCodes / Data: Smartsheet
Construction inventory tracking is no exception.
Despite the steady rise of digital tool adoption, many construction businesses still rely on traditional paper- and spreadsheet-based methods for various processes, including inventory management.
The worst part?
Spending extra time on inventory doesn’t lead to positive outcomes—it’s the opposite.
Manual counts can’t deliver the necessary inventory accuracy, and when discrepancies inevitably show up, they impact overall productivity and project timelines.
Plus, losing even non-essential inventory items takes a toll on workers’ morale.
Paul Heitlinger, General Manager of Nokia AIMS, explains that, when inventory gets lost, workers are expected to carry out time-consuming investigations to find these misplaced items.
Even if missing shipments or tools are located and recovered immediately, doing low-level, repetitive tasks takes its toll in the long run:
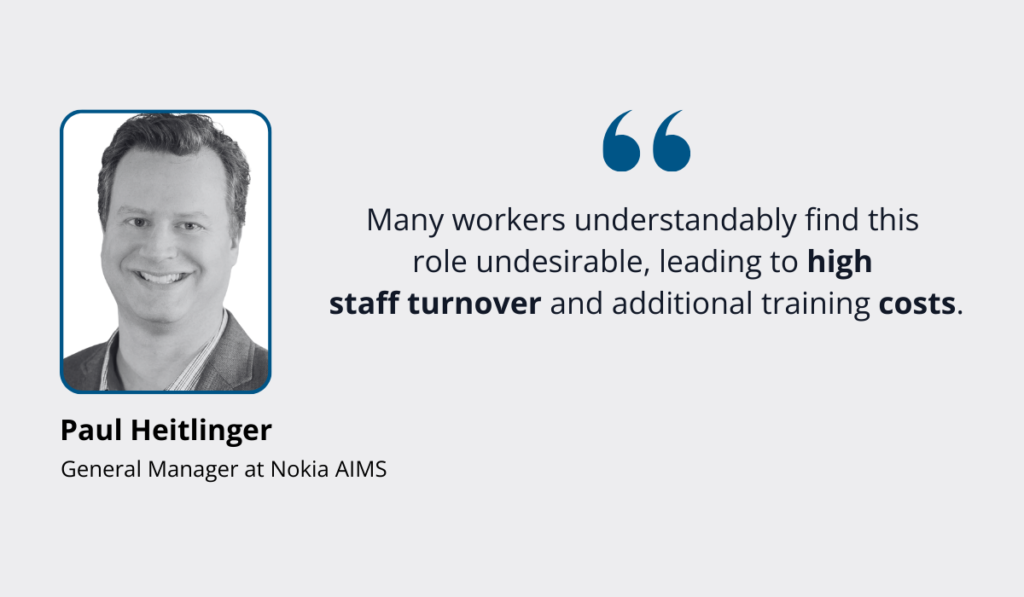
Illustration: GoCodes / Quote: Supply Chain Digital
No one wants to be stuck counting hand tools, spare parts, and materials to see if the numbers match, but if it keeps happening, you’re actively inviting staff turnover in the face of ongoing labor shortages.
Admittedly, manual tracking can be a cost-effective way to manage inventory, especially for smaller projects.
As your business grows, however, keeping track of all your assets, materials, and other inventory items across multiple locations becomes downright impossible.
The solution lies in automation.
To start with, digital tracking automates inventory updates, giving you instant access to stock levels.
For instance, barcode or QR code inventory systems improve workflows by enabling seamless quantity updates directly from the field, ultimately saving you time.
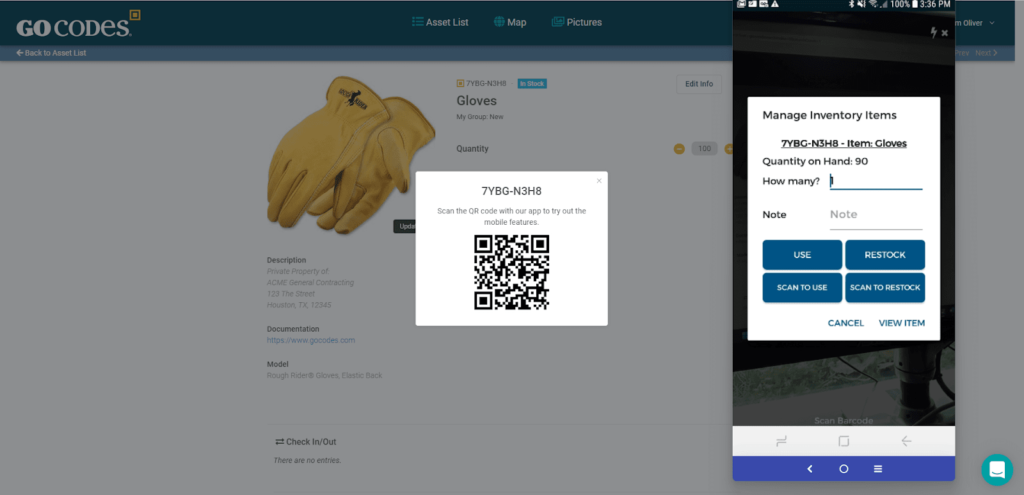
Source: GoCodes
Any worker with a smartphone can simply scan the item tag to update the stock quantity.
Since digital inventory systems excel at handling vast amounts of data, you won’t have to worry about inventory tracking even as your business scales.
And if you have any doubts about the effectiveness of these digital solutions, here are some concrete numbers related to another popular tracking alternative, RFID technology.
McKinsey’s research showed that using RFID readers and tags reduces the time spent on inventory management, freeing up precious labor hours.
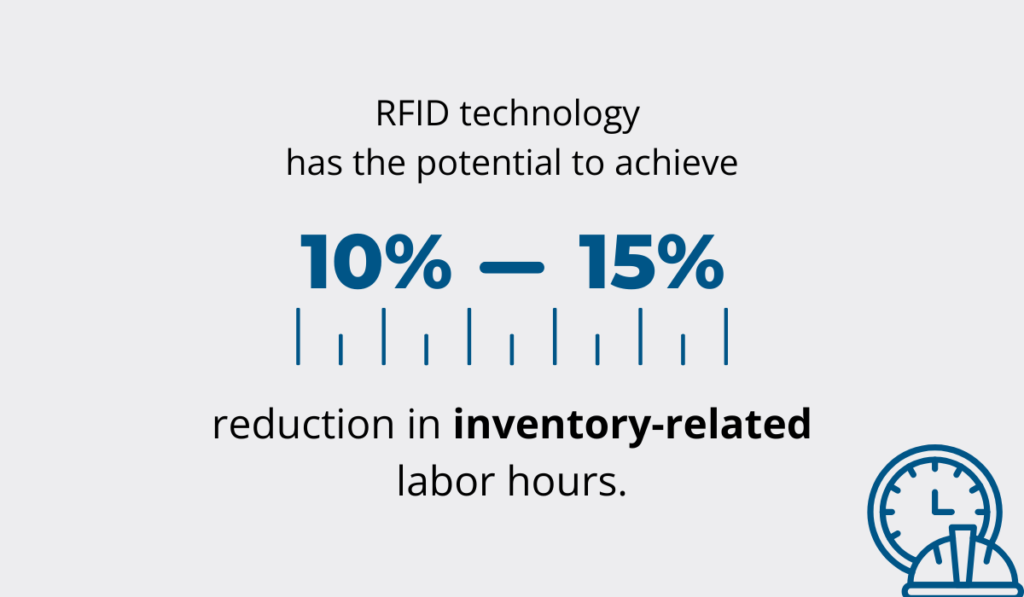
Illustration: GoCodes / Data: McKinsey
Although the study focused on retail, the overall effect is similar across several industries.
Efficient inventory tracking is essential in construction, and automation is the fastest (and only) way of getting there.
High Risk of Human Error
Using paper logs or spreadsheets to track construction inventory results in data entry errors, miscalculations, or forgotten updates.
To err is human, but there is a way to reduce, if not eliminate, mistakes—but first, you need to adopt a different system altogether.
Spreadsheets remain a staple in many processes and are still widely used, but one seminal study reveals why this shouldn’t be the case:
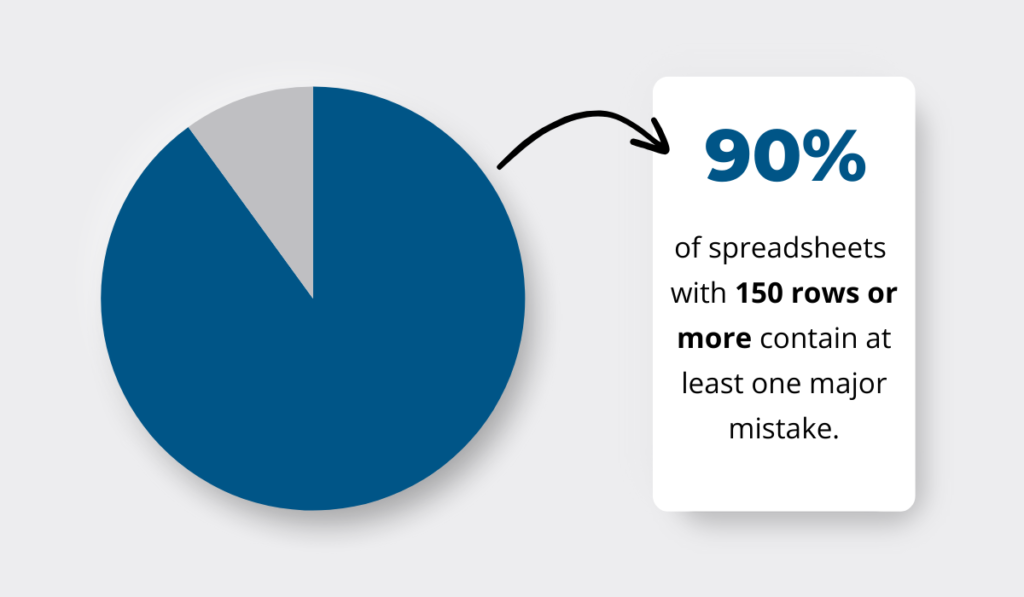
Illustration: GoCodes / Data: IGI
Even a minor error in stock levels can cause inventory shortages or lead to excess ordering, which can result in budget drain and higher storage costs.
For businesses relying on manual tracking and spreadsheets, these mistakes are much more common and disruptive, ultimately contributing to a widespread culture of blaming.
Thabo Rebang, Distribution Team Leader at Caterpillar Inc., also warns about this tendency to assign blame to workers, suggesting that mistakes are a way to pursue improvement instead.
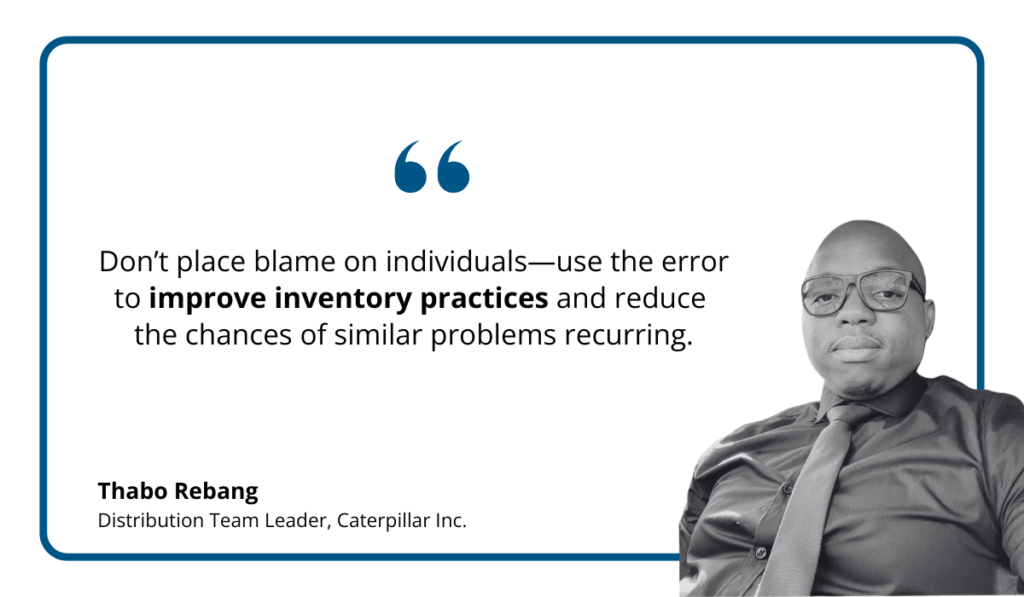
Illustration: GoCodes / Quote: LinkedIn
In other words, when an inventory issue arises, ask yourself:
- What type of mistake occurred (e.g., a typo or oversight), and what caused it?
- Is there a pattern: specific items, team members, or situations?
- What’s one immediate step we can take to prevent it from happening again?
Asking and answering these questions gives you clear pointers on what kind of tweaks you need to make to improve your inventory tracking.
While implementing a digital inventory system takes some time and effort, it’s one of the most effective ways to reduce human errors through automation.
It all boils down to automating data entry and updating stock levels or asset details in real-time.
This can be done using customizable QR code trackers that can be attached to any tool, piece of equipment, container with spare parts, or pallet with materials.
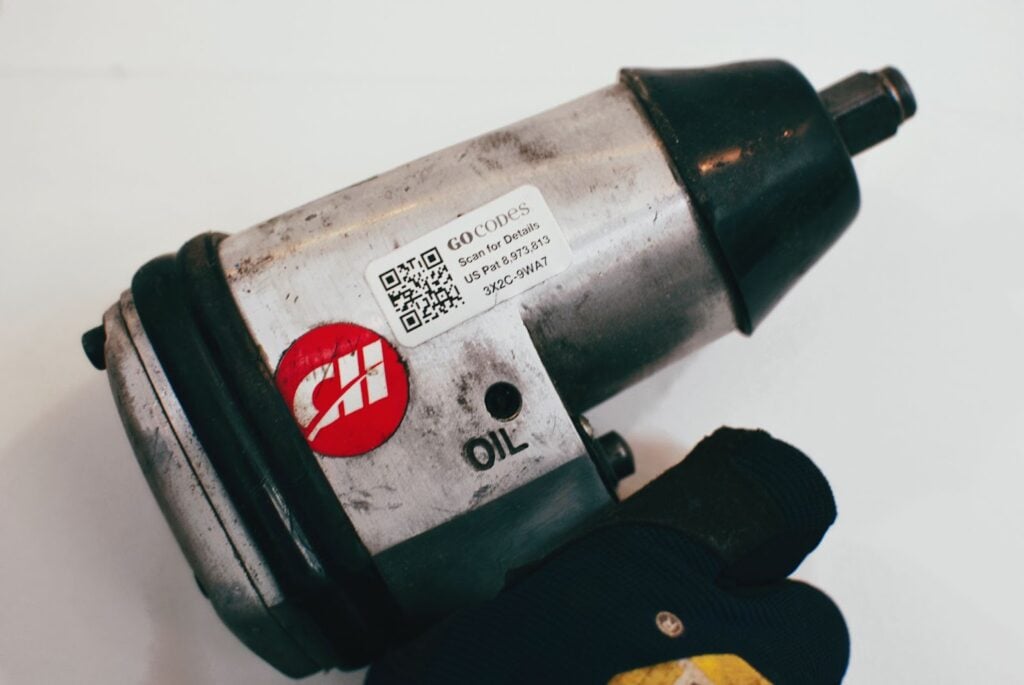
Source: GoCodes
When coupled with a mobile inventory tracking app with a built-in QR code scanner, these tags instantly increase visibility and control over your entire construction inventory.
They facilitate easy check-in/out of items and a smooth auditing process, ultimately ensuring that no item is overlooked or mistaken for another.
Additional features like audit scanning mode and low-quantity alerts strengthen your safety net further.
In this way, you can update item locations in a single step and adjust minimal quantity levels for each inventory item.
To illustrate, here’s what the setup looks like in our inventory tracking app, GoCodes.
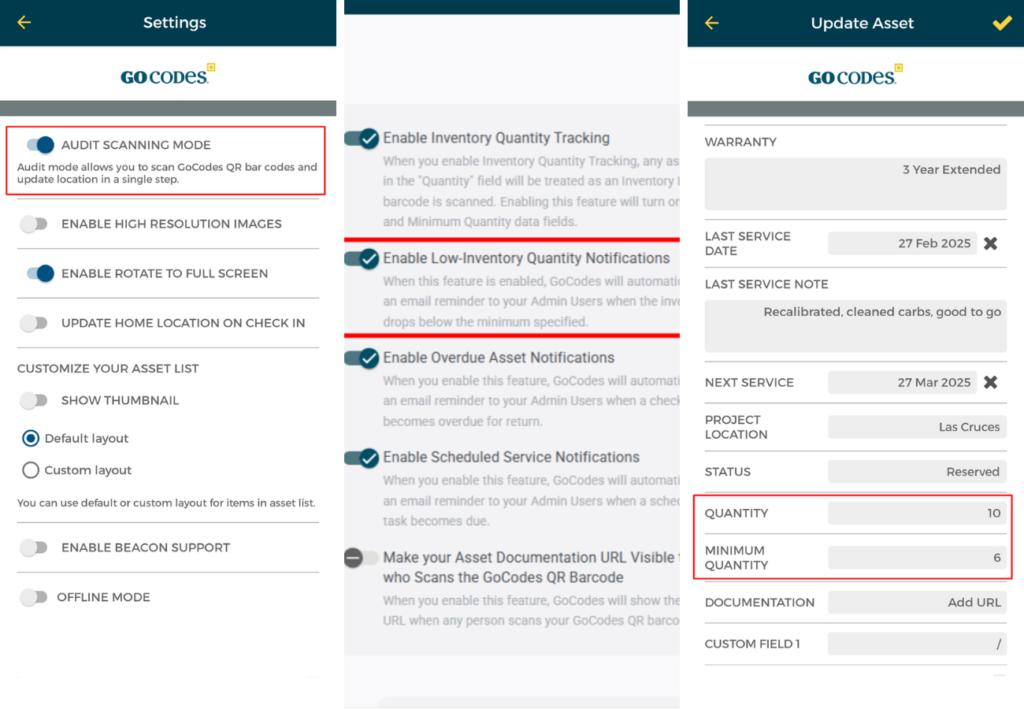
Source: GoCodes
To sum up, by reducing reliance on manual tracking, you minimize errors, save time, and keep your inventory accurate without the constant worry of mistakes.
Lack of Real-Time Visibility
Manual tracking doesn’t provide real-time insights, which makes it difficult to monitor inventory levels across multiple job sites.
Lack of visibility doesn’t reflect only on efficiency—it leads to poor decision-making and impacts the overall resilience of your operations.
It’s no wonder Standvast’s research found that 45% of respondents see real-time inventory visibility as the biggest challenge in coordinating inventory across multiple sales channels.
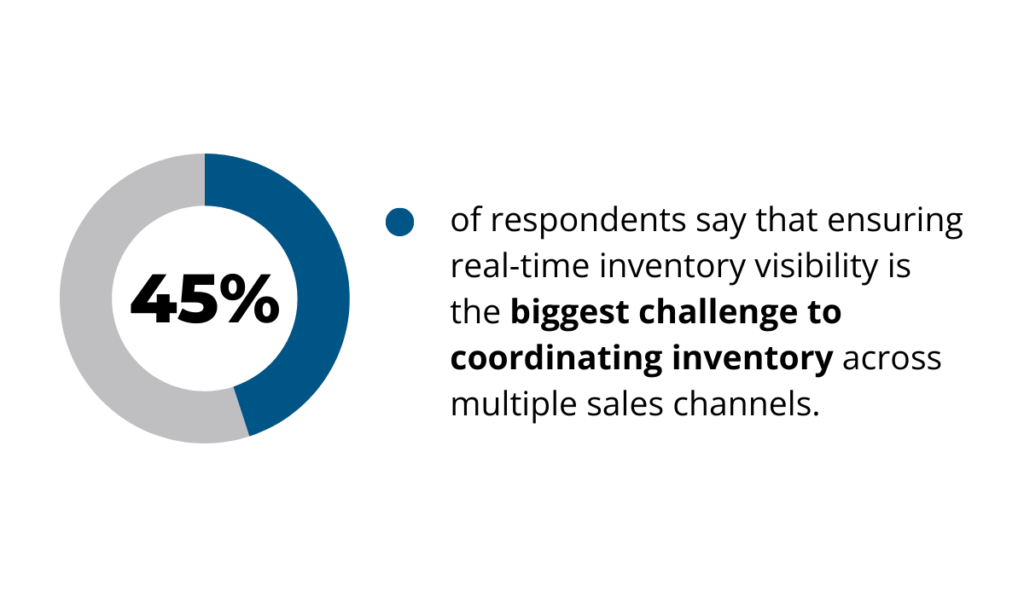
Illustration: GoCodes / Data: Standvast
Now replace “sales channels” with “jobsites”.
Real-time inventory visibility is crucial in e-commerce, but it’s just as vital in modern construction, where poor resource management can lead to costly delays.
Every construction business owner and project manager knows the struggle—when inventory moves across multiple projects and locations, staying on top is a real challenge.
With manual tracking, that challenge can feel overwhelming.
Luckily, having a digital solution that offers real-time access to inventory data takes the edge off, enabling your team to make quick, informed decisions that prevent disruptions.
One Reddit user highlights the difference between relying on spreadsheets and adopting a digital solution.
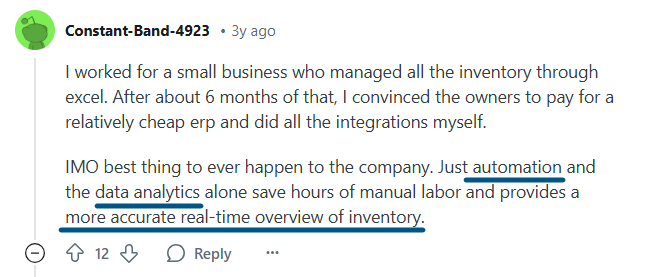
Source: Reddit
The automation and data analytics available through an ERP system make it easier to manage several business processes, also increasing insight into inventory.
For instance, Workday’s ERP solution provides easy access to on-hand inventory quantities while enhancing overall resource allocation and financial planning.
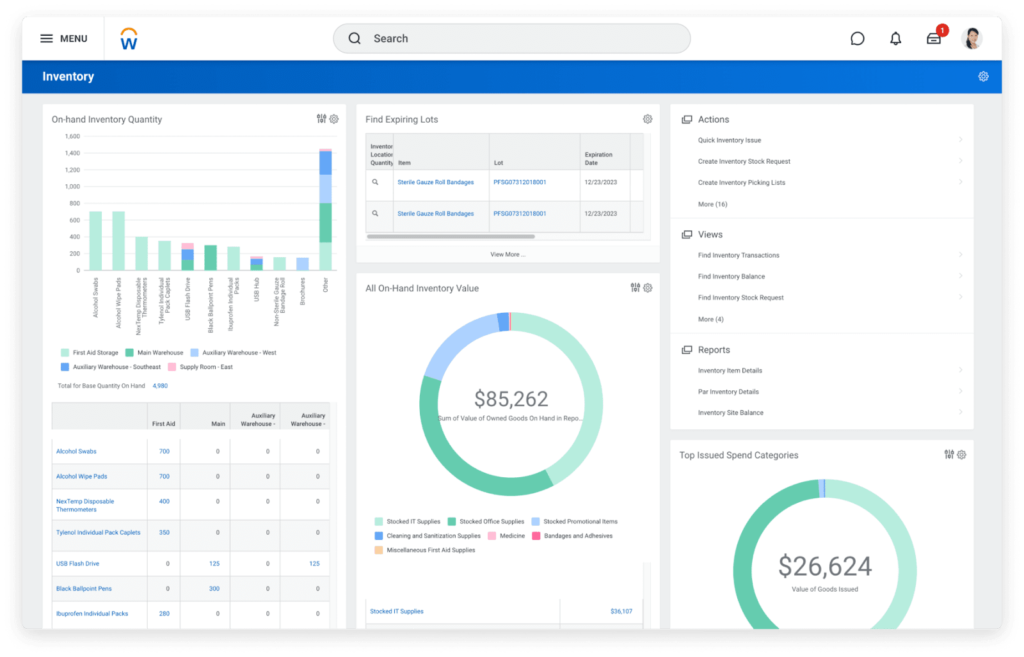
Source: Workday
While this type of inventory data is valuable, ERP solutions that aren’t designed for the construction industry often lack field-level tracking capabilities.
Luckily, solutions that offer real-time location updates and mobile accessibility for on-site teams bridge this gap naturally.
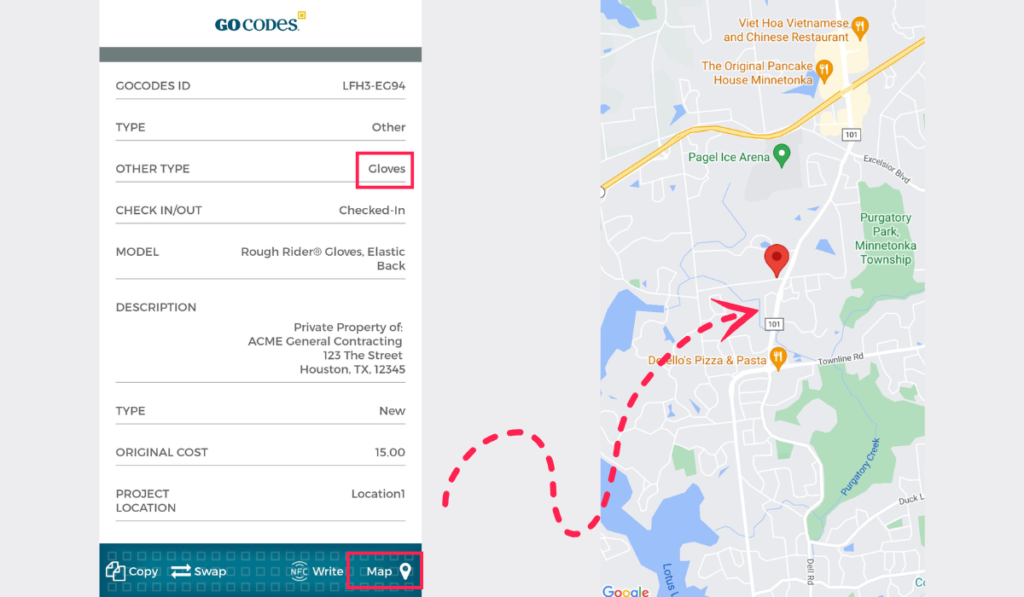
Source: GoCodes
One thing’s certain: real-time inventory visibility minimizes delays and enables smarter decisions.
Choose the right digital solution for your company, and you’ll move away from manual tracking quickly and successfully!
Increased Risk of Inventory Loss
A higher risk of inventory loss is another compelling reason to forego manual tracking.
Consider this scenario: stock leaves the building, but has been mistakenly taken to the wrong construction site. Once it’s there, no one acknowledges the receipt of the wrong shipment.
In the end, you’re left to play a guessing game of who took the shipment, and where it’s now.
Without a digital tracking system, it’s harder to monitor material and equipment usage, which leads to:
- Potential theft
- Item misplacement
- Unauthorized access
Preventing inventory loss, and the additional costs that go with it is one of the foremost challenges of construction inventory management.
In many cases, inventory loss can be attributed to thieves who scout out (unprotected) job sites until they have the opportunity to strike.
Bauwatch’s recent report on construction crime confirms as much, but it also reveals that many thefts are carried out by insiders.
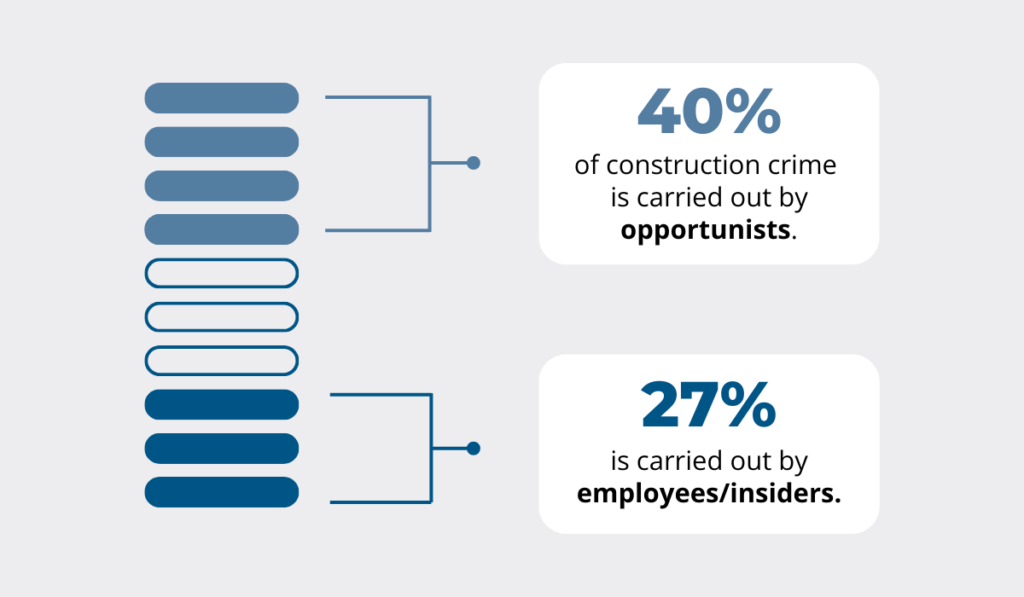
Illustration: GoCodes / Data: Bauwatch
Keeping these threats in mind, how can inventory tracking systems help?
While not the first security measure to come to mind, automated inventory tracking certainly helps lower the risks.
As mentioned previously, digital inventory solutions frequently utilize a variety of scannable labels.
Attaching anti-tamper tags that are difficult to remove helps deter theft—not only do they state ownership, but any attempt of removal leaves clear markings on the tools in question.
These systems also provide extensive records of who handled which assets or inventory items, enabling you to track movement and last known whereabouts while establishing a clear chain of custody.
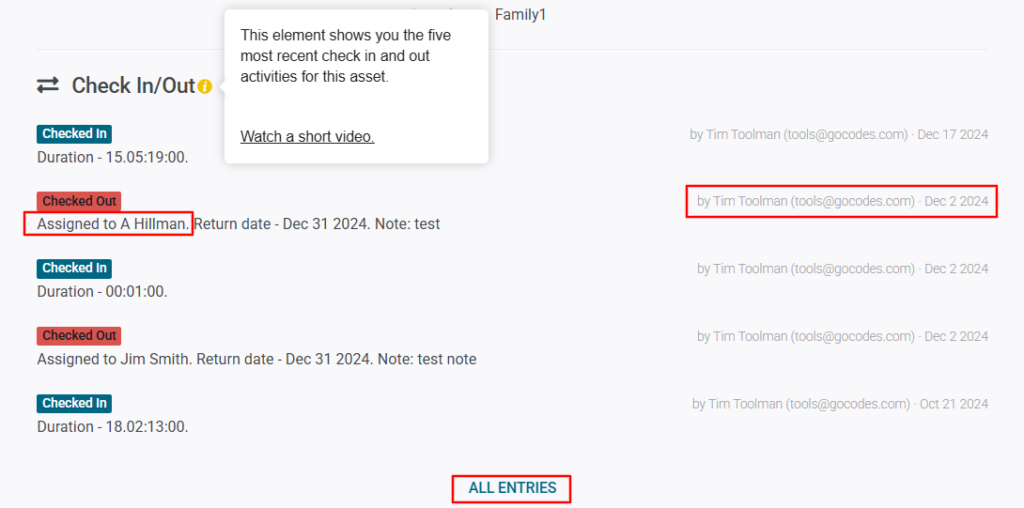
Source: GoCodes
Naturally, tracking material shipments and high-value equipment is a bit different.
A quarter of Bauwatch study respondents reported that the value of construction materials that were stolen from them ranged from £3,000 to £10,000 (nearly $13,000).
Given these losses, protecting valuable shipments requires an extra layer of security.
By equipping important shipments and pricier equipment with GPS trackers, you get real-time location data, allowing you to monitor movement across the globe.
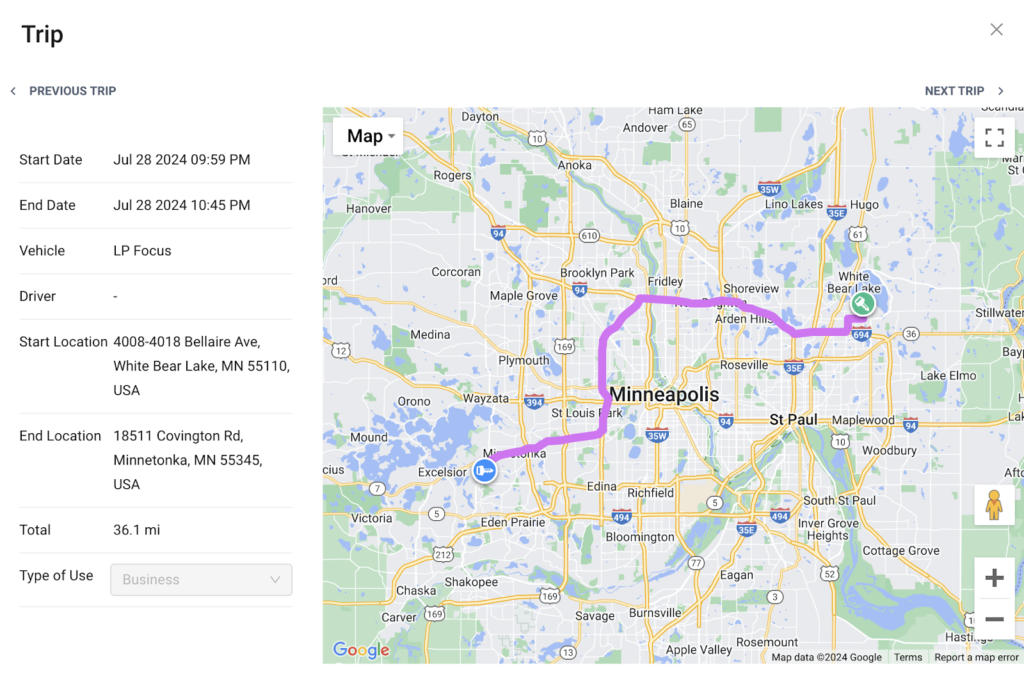
Source: GoCodes
Even more importantly, if theft occurs, these trackers enhance the chances of asset or shipment recovery.
Ultimately, manual tracking leaves you exposed to multiple risks of inventory loss while digital tracking solutions safeguard your inventory and operations, giving you peace of mind.
Difficulties with Analyzing Inventory Data
With manual inventory tracking, generating accurate reports and analyzing inventory data is a time-consuming process riddled with errors.
Want to understand trends, spot inefficiencies, and optimize your operations?
You need a single source of truth and robust reporting capabilities.
A lack of these capabilities often leads to fragmented data—a common challenge in inventory management.
In fact, a forum discussion on inventory challenges quickly shifted toward this very issue and the technology that can help address it.
One user noted that even when you have a system in place, without these features, you’ll be spending most of the time compiling the data, rather than analyzing it.
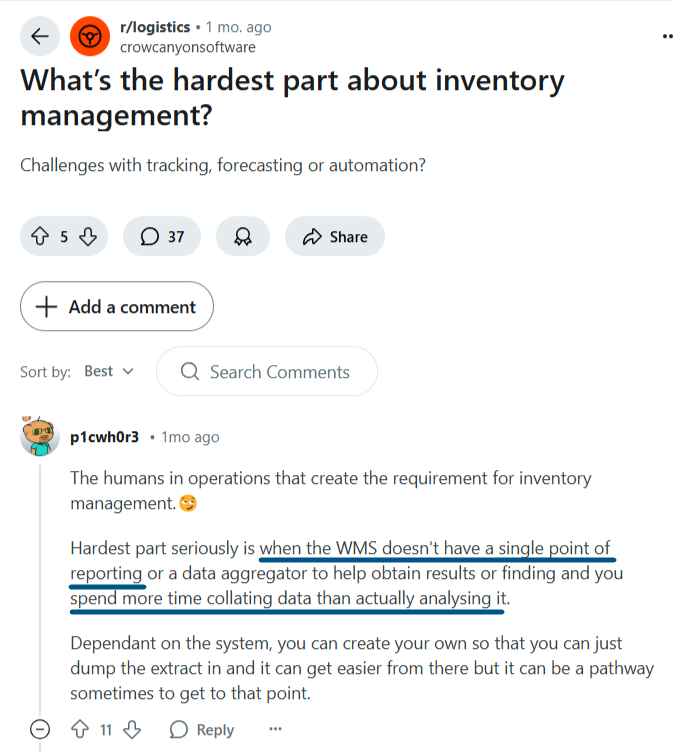
Source: Reddit
Without centralized reporting, your ability to extract and prepare inventory data plummets immediately, preventing quality analysis and informed decision-making.
Ongoing supply chain issues make the lack of actionable data especially crippling for businesses today.
The ongoing impact of the Red Sea crisis shows why this is no exaggeration.
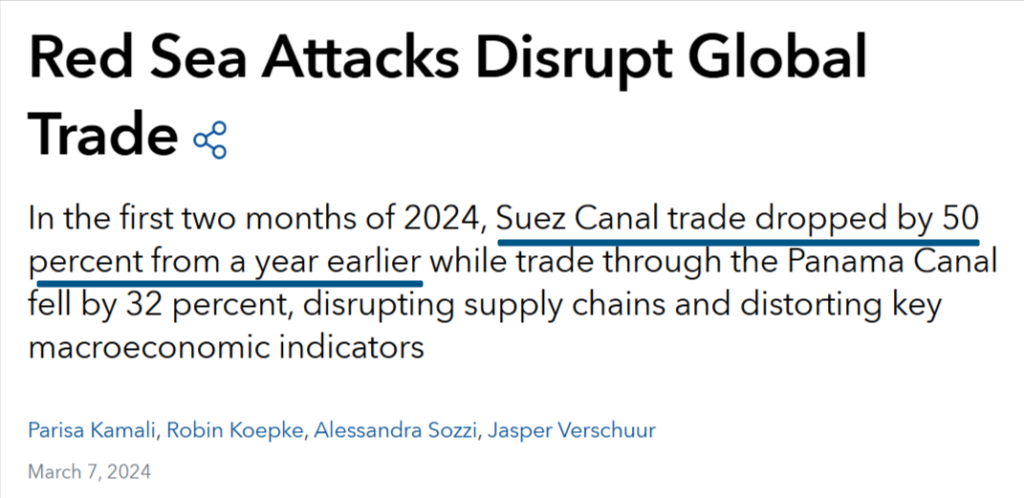
Source: IMF
In the face of the rising tensions, many contractors are concerned about the re-emergence of materials shortages and broader supply chain issues.
Anirban Basu, Chairman and CEO of the Sage Policy Group, explains that the crisis will have a ripple-like effect, leading to higher costs of transportation and insurance.
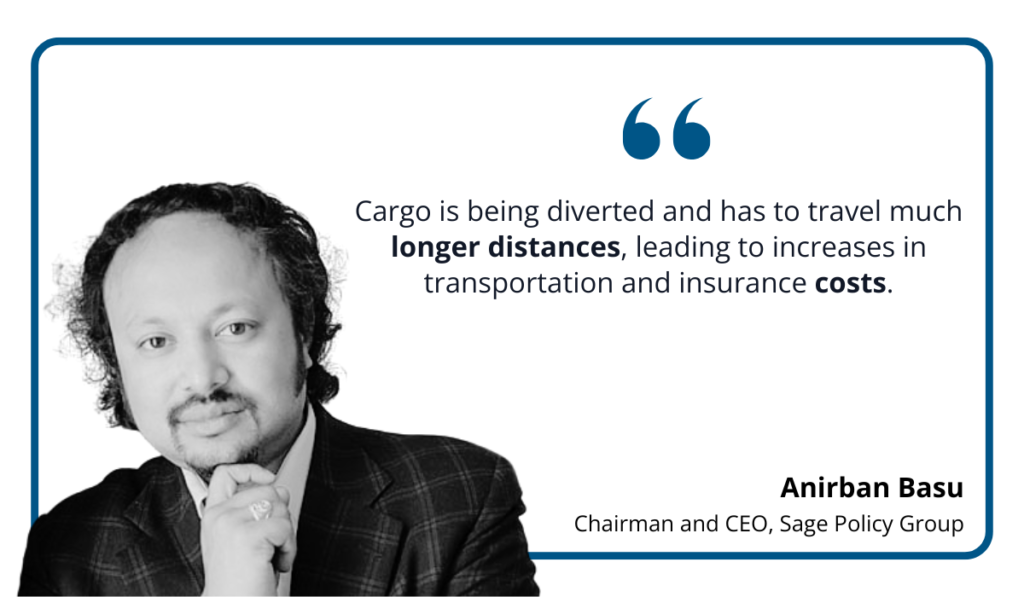
Illustration: GoCodes / Quote: Construction Business Owner
Conversely, these increases in costs squeeze the already tight contractor margins.
Is there any good news?
For one, most inventory tracking systems enable you to generate detailed, customizable reports and leverage insights that fuel smarter resource management.
For example, one popular inventory tracking method is automated replenishment, which relies on historical data and forecasting models to predict future business needs.
Inventory replenishment solutions like Blue Ridge Platform can help you track stock levels, but also improve planning through predictive insights—take a look at the dashboard below.
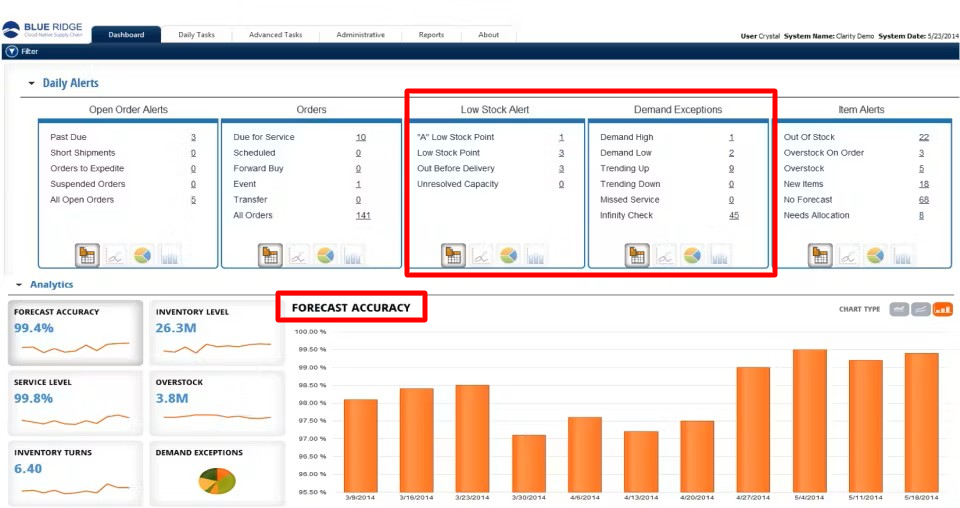
Illustration: GoCodes / Source: Capterra
With all the relevant data neatly in one spot, you can make accurate inventory predictions and adjust in line with the changing circumstances.
Of course, different software solutions offer different functionalities.
Historical trend analysis focuses on past usage data to predict demand, optimize stock levels, and prevent materials shortages.
Another approach to analyzing data inventory is real-time tracking that monitors current inventory locations and movements to improve visibility and reduce loss.
Finding a solution that excels at both is a challenge, so how do you make a choice?
Lidl Ireland’s Supply Chain Project Manager, Marcello Altisent, explains it in simplest terms:
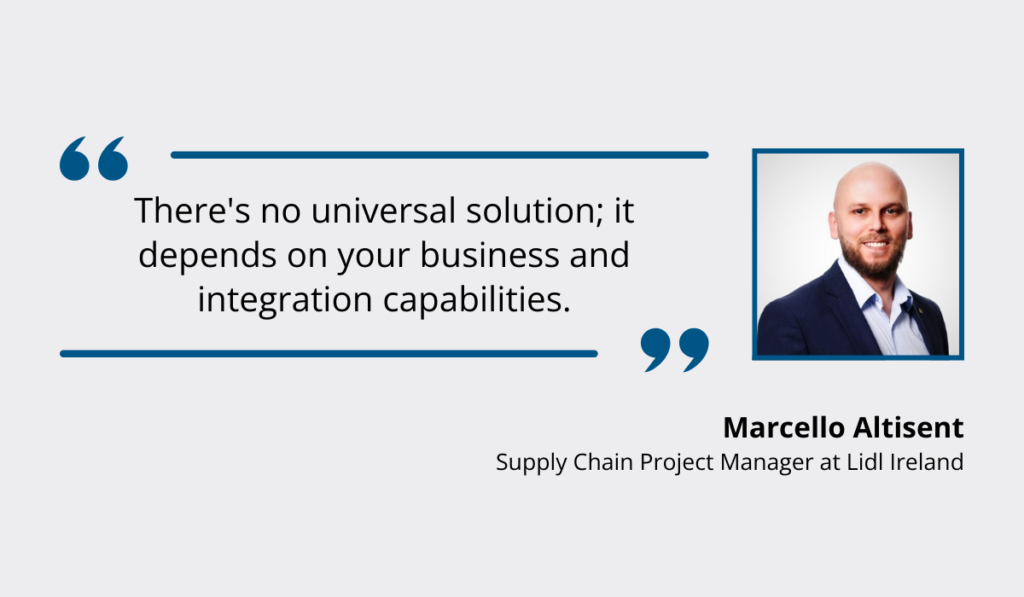
Illustration: GoCodes / Quote: LinkedIn
Since there’s no one-size-fits-all solution, it’s important to take a close look at your business and its inventory management needs and objectives.
Remember, manual tracking requires little upfront investment or effort, but it does nothing to simplify operations or address common construction inventory challenges.
With dedicated inventory tracking software, real change becomes inevitable!
Conclusion
Manual inventory tracking may seem convenient and cost-effective, but in reality, it leads to wasted time, costly mistakes, and limited visibility.
Construction projects demand agility and efficiency, and digital solutions provide the real-time inventory tracking and automation needed to stay ahead.
The key takeaway? Don’t let outdated methods slow you down.
Take the next step toward smarter inventory management and invest in a system that will keep your inventory accounted for and your projects running smoothly.