Governments worldwide are trying to tackle the problem of waste, and they found the main culprit in the construction industry. But that’s not without a valid reason.
Just in the EU, construction demolition and waste account for 35% of all generated waste. This means that more than 450 million tonnes of bricks, concrete, plastics, and even asbestos end up in landfills, polluting the environment and endangering the safety of communities.
But there’s light at the end of the tunnel. Simple changes on construction sites and adjustments in the way construction companies approach waste management can significantly contribute to global waste reduction.
What is more, these sustainable practices will ultimately save construction companies money and ensure compliance with local and national environmental regulations.
So, let’s dive into the best practices you can adopt today to manage your construction waste better and create a more environmentally friendly construction business.
In this article...
Designing for Material Optimization
Construction waste management should start from the very beginning of the construction project lifecycle.
Ideally, it should be integrated into the project’s design to account for maximum waste reduction, reuse of materials, and implementation of sustainable methods.
This means companies should:
- Plan for the deconstruction of materials and components
- Survey the existing site to determine the reuse of building components
- Construct building components off-site
- Standardize similar elements
But here is how it looks in practice.
The Resource Efficient House in Scotland demonstrates how construction companies can create more sustainable residential buildings when they incorporate sustainability from the design phase to the end.
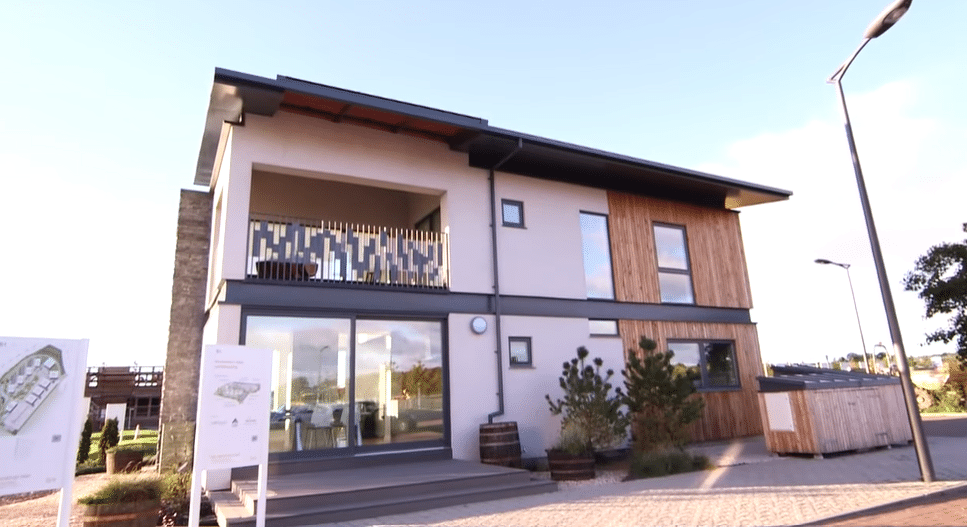
Today, an average house in Scotland creates 13 tonnes of construction waste during building. In comparison, The Resource Efficient House produced less than five tonnes.
To do that, the design of the house provided maximum recycling and reuse of construction products.
The house is a modular design, with most materials and components constructed off-site, which further enabled the construction company to reduce build time.
Insulation materials were made from recycled glass and plastic.
What’s more, some materials are locally-sourced and reclaimed, but the best part is that every material used can be broken down and recycled again.
Finally, the entire structure can be easily disassembled and moved.
But here are other achievements this type of planning and building accomplished:
- Modular design enabled more control over costs and waste management
- Overall recycling rate was 96%
- Exceptional building standards achieved Platinum level set by 2016 Scottish Building Standards (net zero carbon)
- Energy performance certificate (EPC) rating is A (the average in Scotland is D)
As governments enhance their building standards and sustainability becomes a top value driver for clients, creating houses like the Resource Efficient House will become the norm.
So, if you want to create better value propositions and reduce waste simultaneously, think about implementing sustainability in your project’s design from the beginning.
Inventory Optimization
While most construction companies deal with material shortages, it might be tempting to buy excess materials just in case.
However, if your goal is to reduce waste, such an approach is a recipe for disaster.
Though some materials look robust and long-lasting, they all have an expiration date. Or in other words, if they sit in storage too long, their quality decreases, and they’re no longer usable for construction projects.
For example, cement should be used three months after purchase because it loses strength over time.
Storage period | Fresh | 3 months | 6 months | 1 year | 5 years |
Reduction in strength | 0% | 20% | 30% | 40% | 50% |
A good strategy many companies use is a first-in-first-out method (FIFO). This means making sure that the materials that were purchased first also get used first.
That way, you’re always working with fresh and quality materials for your projects.
But what if you still have leftovers?
Just because you won’t have use for these materials, there is probably someone who will. So, the first thing is to work with your vendors and look if they have a flexible return policy.
You should always work with suppliers who are willing to take back any surplus materials but if that’s not possible, engage with your local community.
There are charities and local initiatives that you can contact and donate your materials to. What’s more, there could be entire networks where you can exchange or sell what you don’t need.
One such network is Construction Material Exchange.
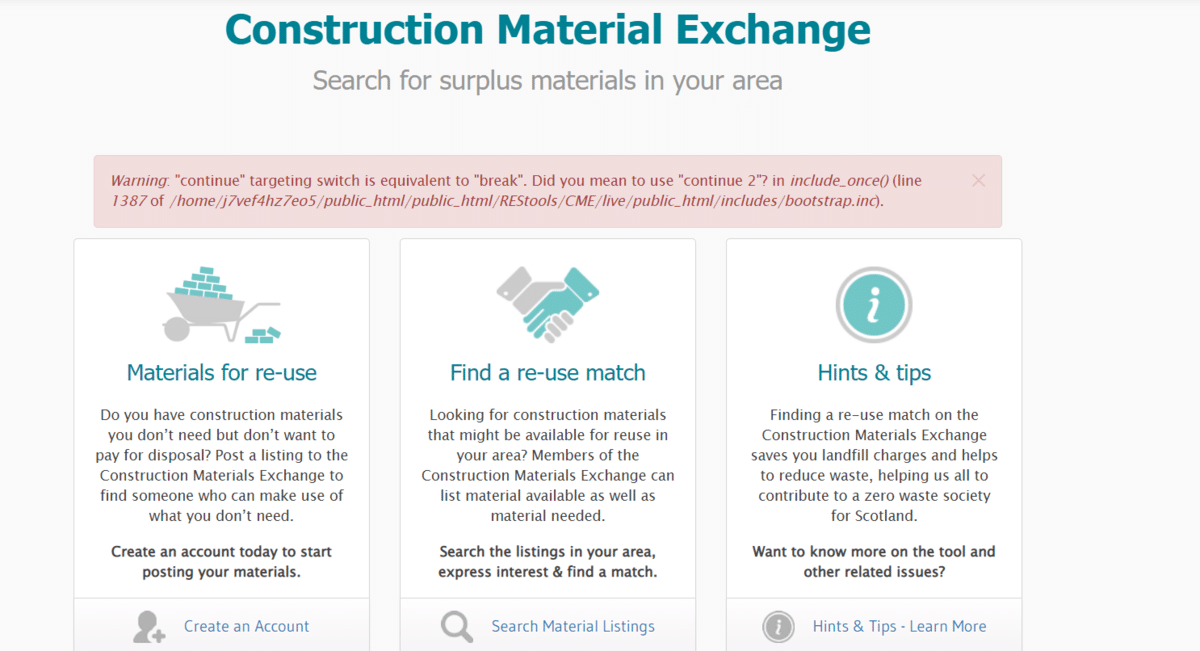
After you register, you can advertise the material you want to get rid of or look for materials other people post on the website.
The network works with local construction companies, so transportation costs are significantly decreased.
All in all, better inventory management has great potential to optimize resource usage and reduce waste. When you have a good overview of the materials you own and need for projects, it’s much easier to purchase, allocate and reuse them.
However, surpluses might still happen on projects, so coming up with a strategy to deal with them is another important step towards ensuring less material is dumped in landfills.
Planning Ahead Based on Your Project
Here’s an inconvenient truth: no matter how hard you try, you will always generate some type of waste on your projects. But the good news is that you can control the amount you produce.
Taking control in this case starts with setting tangible goals and milestones that consider waste management for each project, as well as outlining procedures for salvage, recycling, and disposal.
Keep in mind that every project is different, and the amount of unusable materials will vary.
Here’s an example of how a construction company planned for its waste management and met the client’s sustainability goals.
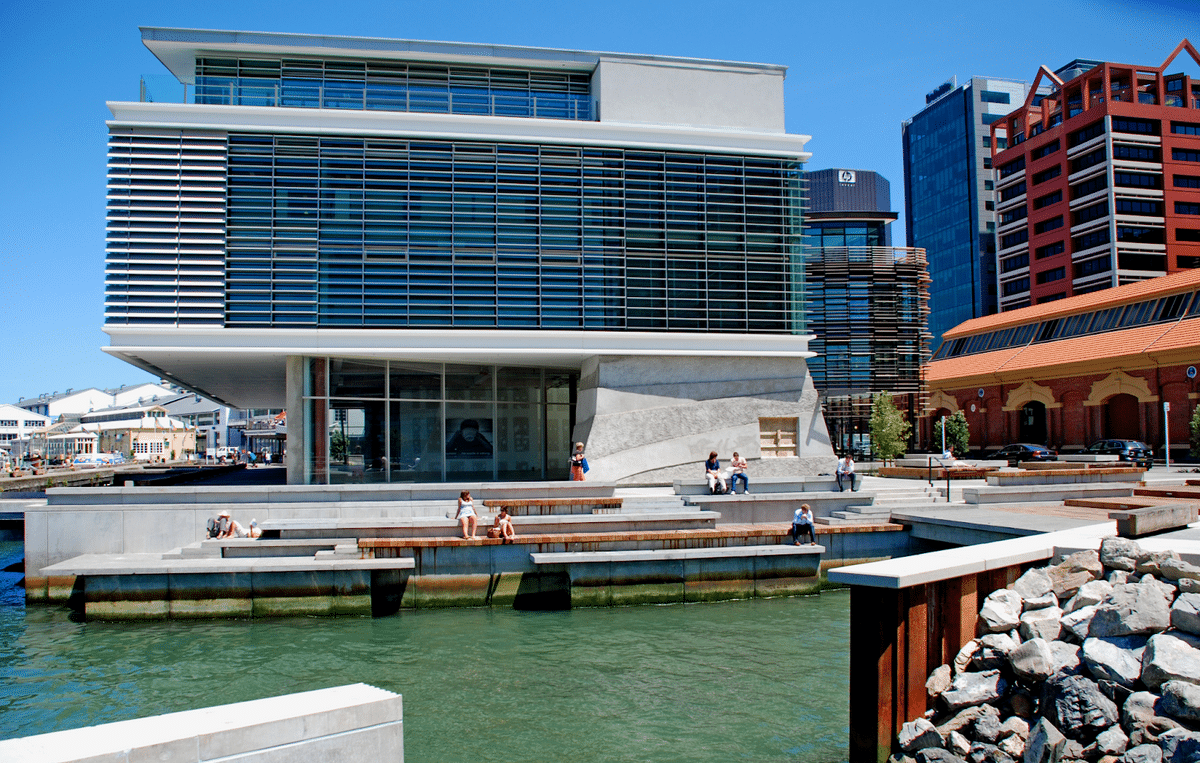
Meridian Energy wanted its new headquarters building to become more energy-efficient and showcase the company’s commitment to environmental responsibility.
That is why Fletcher Construction developed a waste management plan in which they accounted for types of generated waste, their reuse/recycling ability, and eventual disposal methods.
In the formation of their plan, the company used REBRI guidelines to plan their waste management procedure in advance.
You can see how these guidelines help construction managers plan how much waste will be created and the best ways to handle it in the highlighted columns below.
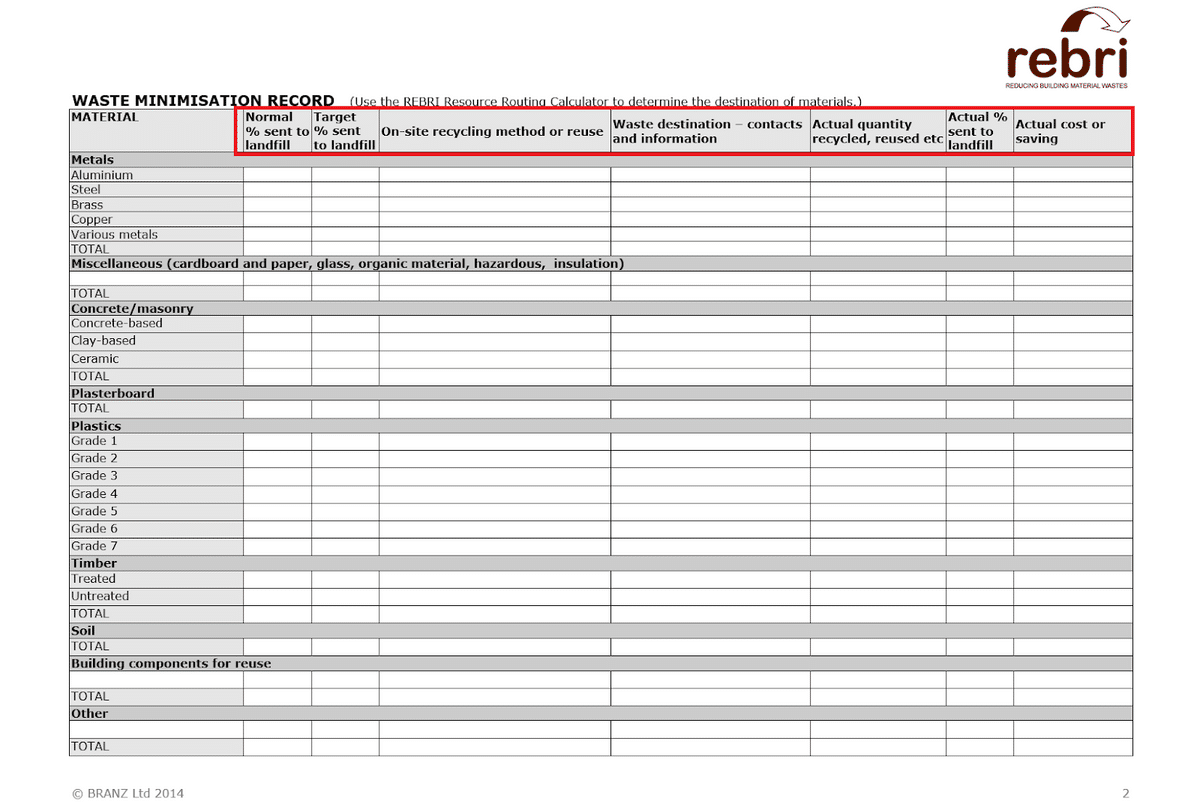
This template helped the company find better ways to reuse or recycle waste generated at each stage of the project.
Furthermore, it gave the entire team motivation and insight into how they were performing and complying with the initial waste management plan.
What were the results?
The total generated waste was 1,151m³, but 60% of construction materials were diverted from landfills.
The rest of the materials, such as timber or plasterboard, were composted, while paper, plastic, and metal were recycled.
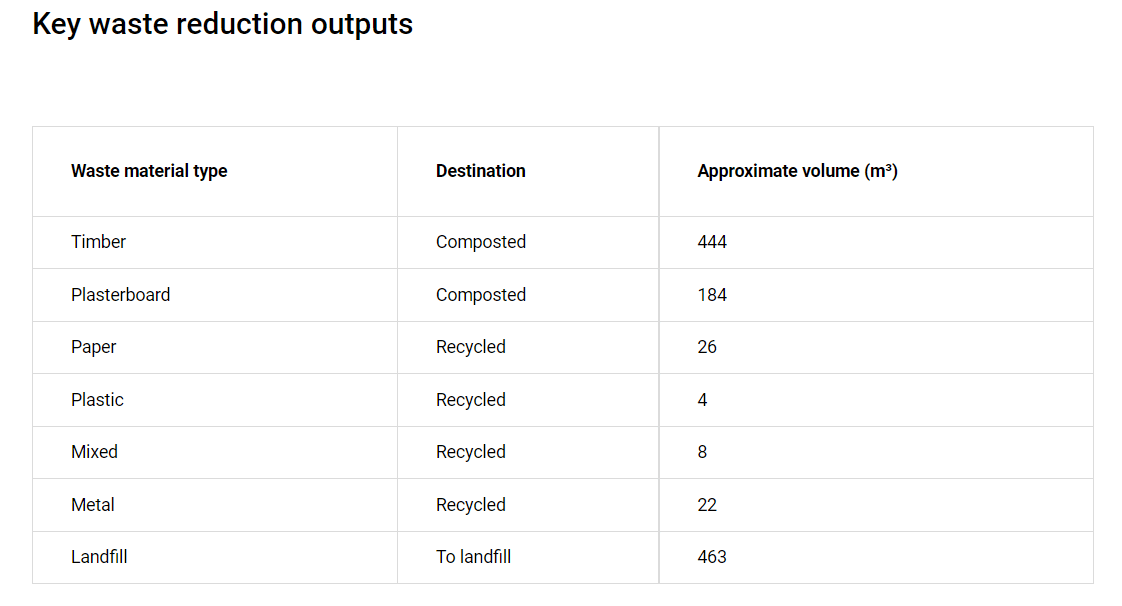
Additional benefits were in savings, namely $14,000 from waste management and $20,000 from waste diversion from landfills.
What you can learn from this is that planning ahead for waste management can help you in multiple areas.
Not only are you going to create less waste on your construction site and build an environmentally friendly project for your client, but you can also profit from the effective waste diversion.
Remember that it’s not enough to say: “I want to create less waste.”
Plan ahead and assess what that means for the project you’re working on. In some cases, you might salvage 70% of your construction material, in others only 30%.
The key is to have a plan and improve with each project you undertake.
Storing Your Materials Properly
Salvaging excess materials and finding another use for them is an excellent strategy to reduce waste.
But the problem is, where do you put it until you can find a use for it?
This contractor thought ahead and rented a warehouse as a way to store leftover materials. This is a good approach because you want a controlled environment to store different materials.
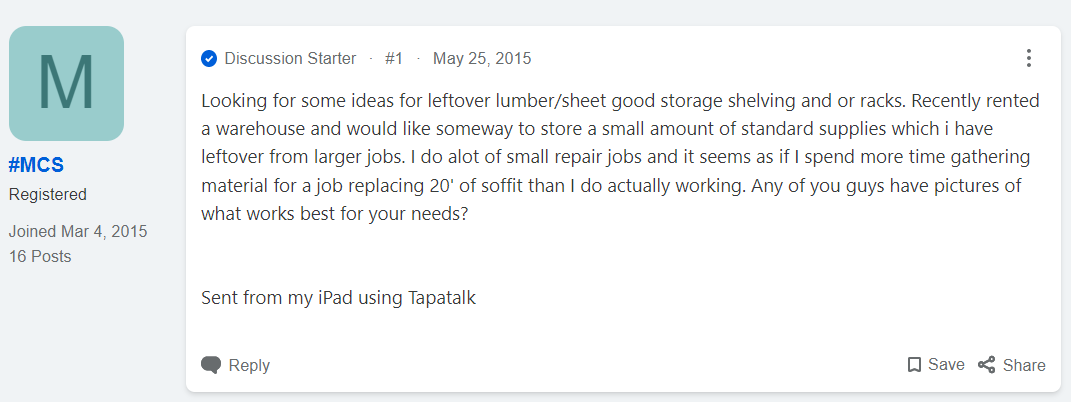
The worst you can do is leave your construction materials outside to combat extreme weather conditions. That is a surefire way to ruin their quality and create unnecessary waste.
Moreover, since you bought the materials, you’re essentially throwing away the money you invested.
The point is that whether you use new or recycled materials, you need to have adequate space to store them.
What does this mean for this contractor?
Because they need to store wood, their main concern is to avoid rot and warping. This can happen if the storage unit is too humid or collects moisture.
Therefore, it’s useful to have hygrometers in the storage unit to keep track of humidity levels or cure the wood so it’s completely dry before storing it.
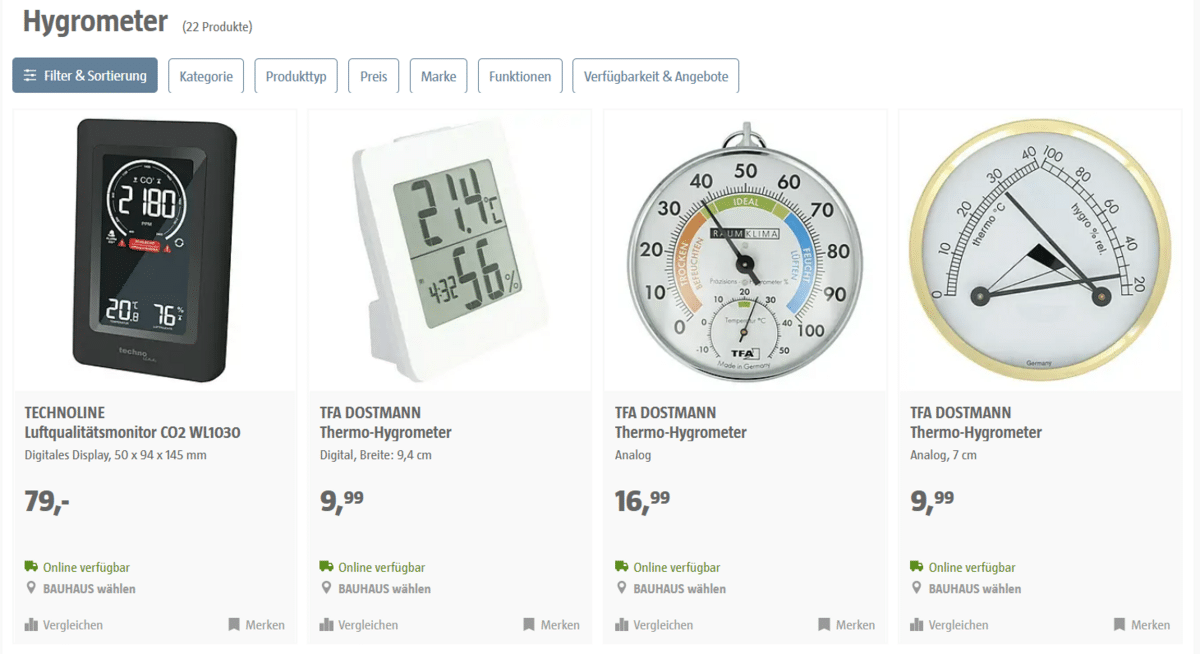
Another problem the contractor is facing is stacking lumber. The way the wood is stacked also has an impact on its quality. In this case, you need a bit of ventilation between the pieces of wood to ensure dryness.
Then you need to put them on flat foundations and cover them with a material that will keep the wood dry.
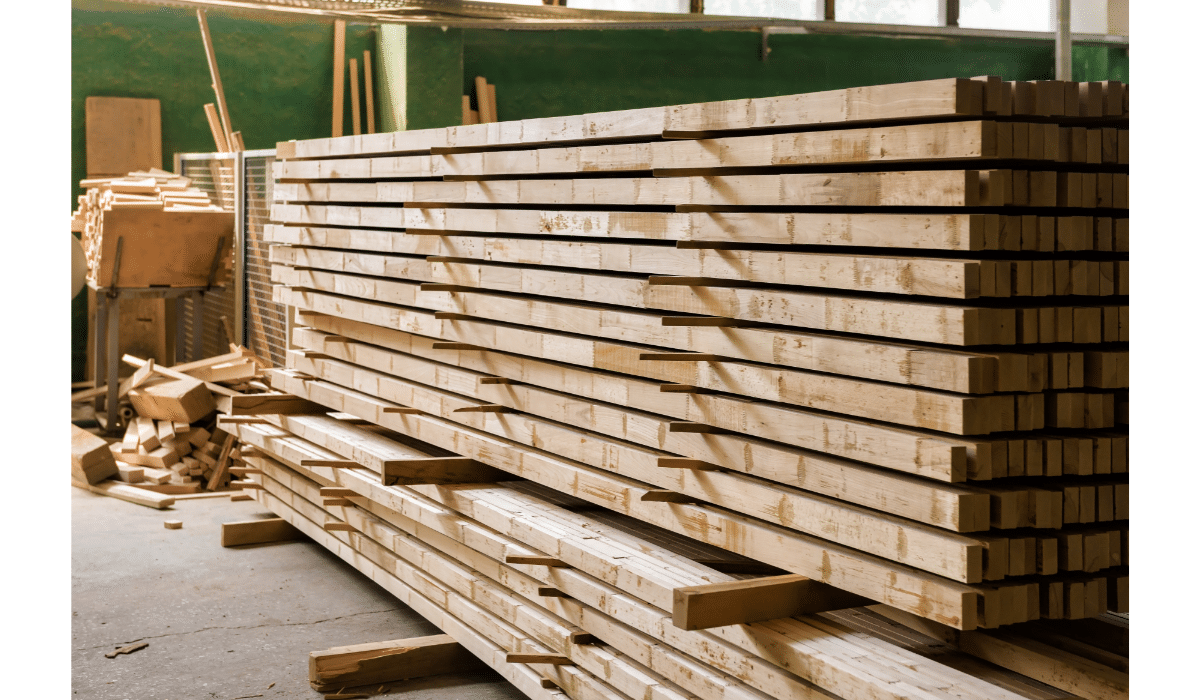
Curtis Lumber and Plywood also recommend that you stack together wood of the same thickness and put weight on the woodpile to prevent cupping.
In this section, we focused on the storage conditions of timber, but every material will have its specific conditions.
The bottom line is that you need to pay special attention to your storage methods to avoid ruining valuable and costly material. That way, you can optimize your inventory further and reduce unnecessary waste.
Investing in Employee Training
All your plans and waste management goals mean nothing if your employees are not sticking to them. Developing good habits is a long process, but it starts with getting the right information and proper training.
For example, you can enroll your employees in waste management courses.
Many trade associations and construction consultants offer training courses that can give you basic and in-depth knowledge about handling different types of construction waste.
One such organization is the Construction Industry Federation (CIF) in Ireland. Their Training and Development department offers members and non-members education about various topics to meet legislative and compliance requirements.
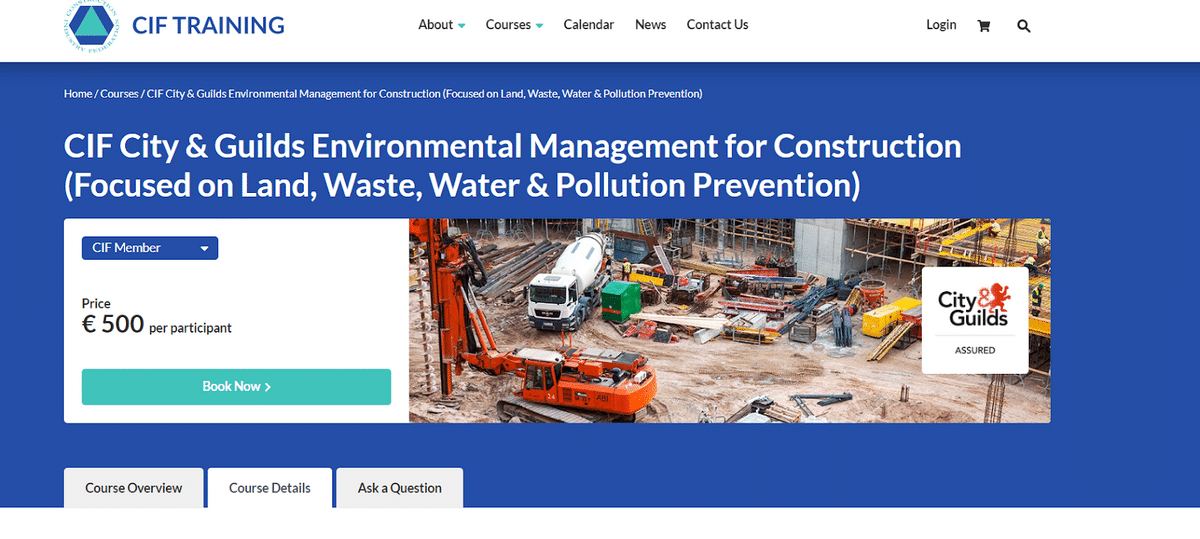
When it comes to waste management, they offer a two-day online course where participants can learn about land, waste, water, and pollution prevention.
They also have workshops to incorporate practical tools and advice for each participant.
While this course is aimed more at individuals directly responsible for waste management on construction sites, there are also some more general training programs like the Chartered Institution of Wastes Management (CIWM) Waste Smart that you can look into.
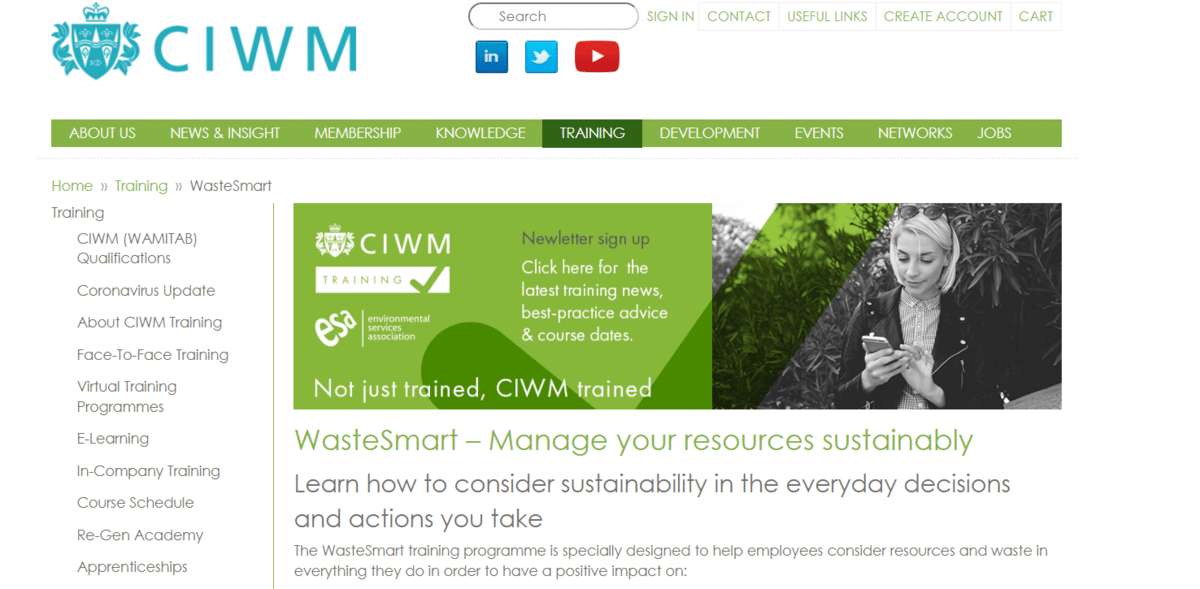
After your employees finish the course, they’ll be able to:
- Cut down waste
- Improve resource use
- Comply with waste regulations
- Understand and apply the waste hierarchy
Once your employees know the basics of waste management, material separation, and recycling, it’ll be easier to hold them accountable.
Additionally, when you establish your recycling goals, record how your employees are meeting the milestones.
If they’re doing a good job, reward their efforts. This makes employees more motivated to keep up with environmentally friendly practices.
Remember that waste management is a team effort, and your employees are one of the key factors in effective waste management.
Improving Site Logistics
An important aspect of waste management planning is accounting for on-site waste separation. This means organizing adequate space for recycling bins and planning how you’ll deliver, store, and transport materials around the site.
But separating your materials isn’t just recommended—in some cases, it’s mandatory.
You also need to consider the type of waste the construction site generates, namely non-hazardous and hazardous material. To put it simply, if you don’t handle your hazardous material properly, you could be facing hefty fines.
The US Environmental Protection Agency (EPA) recently penalized three companies with fines totaling $170 000 for multiple violations regarding hazardous waste management.
EPA Administrator Mike Stoker said that companies are responsible for protecting employees, the community, and the environment with proper hazardous waste management.
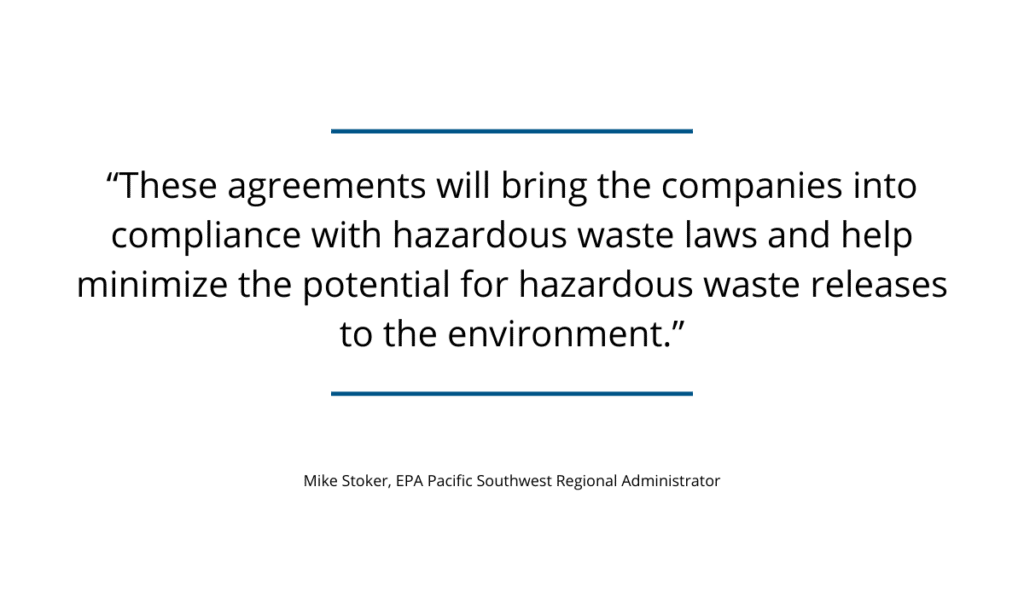
So, how do you do that?
As you’re planning and designing the construction project, also look for available areas where you can organize a waste material separation zone.
This is where you’ll place different bins to allow easy access for your workers and vehicles to transport them to a recycling facility.
Ensure the bins are labeled clearly so there’s no confusion about where each type of material should go.
You can also paint the containers according to the color-coding scheme developed by the Institution of Civil Engineers and Waste Aware Construction.
White | Gypsum and plasterboard products |
Gray | Inert waste (concrete, rubble, bricks, blocks, etc.) |
Black | Mixed general waste (any uncontaminated and non-recyclable waste) |
Blue | Metal |
Green | Wood (clean, untreated wood products) |
Brown | Packaging (cardboard, etc.) |
Orange | Hazardous material (asbestos, paint tins, tarmac, any product with a COSHH label) |
Finally, you can register how much waste you’re disposing to recycling centers or landfills by tracking their movement. Just like you’d put a tracking label on equipment, you can do the same for your waste bins.
GoCodes can help you with this.
Choose any waste container you want to track and put a tag with a barcode or QR code for easier tracking.
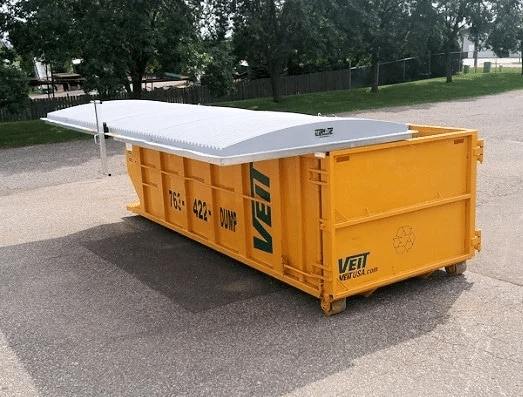
Insert relevant information about the container in the system so every time your employees scan the container, they have relevant data at their disposal.
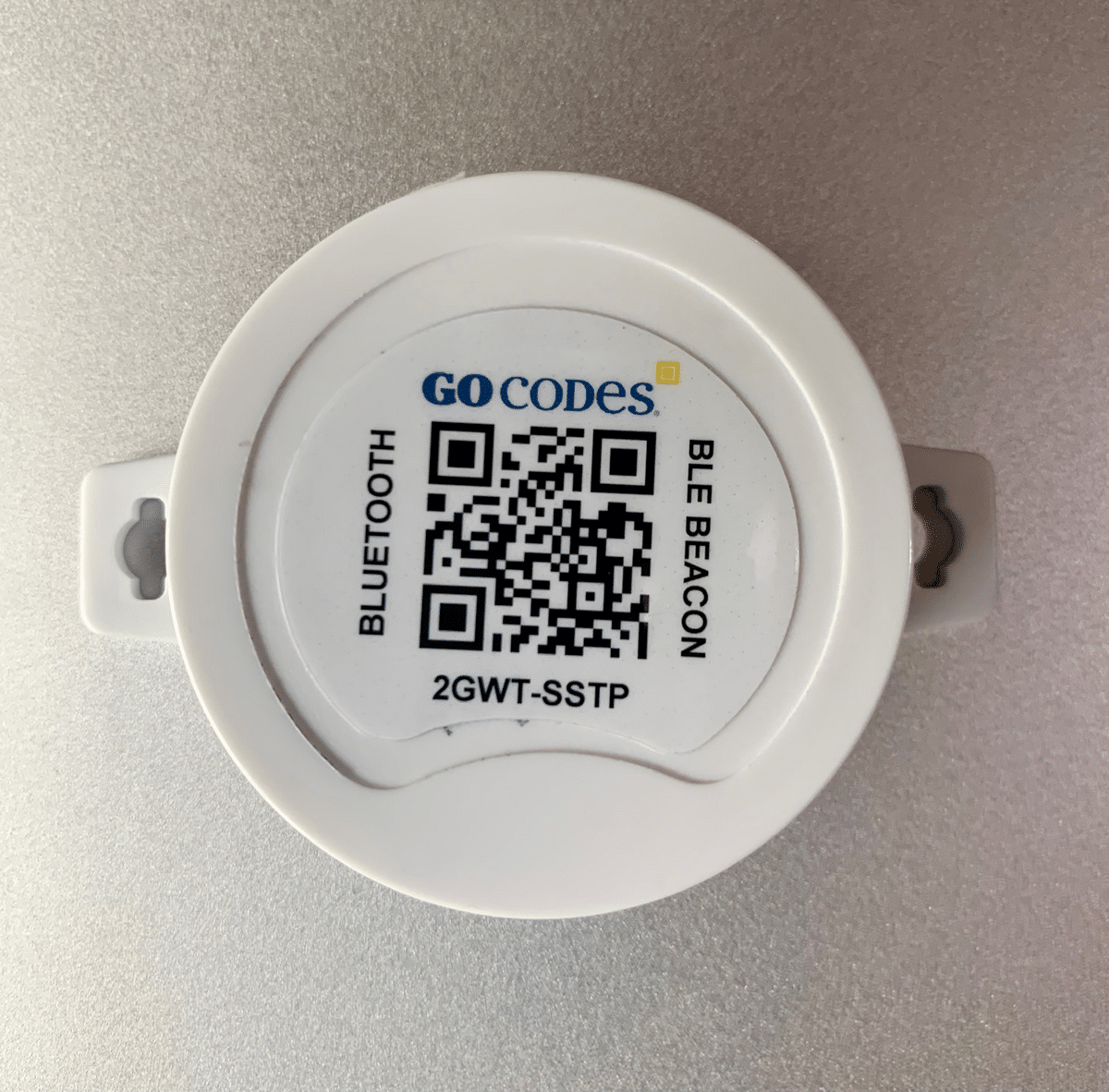
That way, you can easily calculate how much waste you’re recycling or dumping based on how frequently the (fully loaded) waste bins are leaving the site. And you can monitor their movement from anywhere and at any time.
To sum it up, effective waste management means nothing if you don’t have practical ways to separate your construction waste.
Conclusion
As you can see, there are many ways you can tackle waste management.
The most important thing is to make waste management a priority when you’re undertaking any construction project. Planning ahead creates more opportunities for better waste management and you’re actively supporting sustainable efforts.
Even placing several bins for waste separation can go a long way in creating environmental and social benefits for the community and your construction company.