While the construction industry might be perceived as trailing behind other sectors when it comes to innovations, construction companies are no strangers to embracing technological advancements.
Different technologies have emerged as indispensable allies in streamlining operations and enhancing the safety, and performance of construction equipment.
This article explores six key technologies that should be considered by every forward-thinking equipment manager who wants to revolutionize the way they manage equipment, remove inefficiencies, and minimize equipment theft and loss.
So if you are one, keep reading!
In this article...
QR Codes
QR codes, short for Quick Response codes, were originally designed to replace barcodes used to track automotive components in the car production process.
The inventors wanted to overcome the limitations of traditional barcodes and create a more advanced solution that would provide:
- enhanced scanning flexibility: QR codes of any size can be scanned at any angle using mobile devices like smartphones and tablets or, less often, specialized scanners,
- increased data capacity: QR codes can store about a hundred times more information than classic barcodes,
- improved resilience to damage: QR codes can be read even when partially damaged or distorted.
They succeeded and then introduced QR codes to the world by not protecting their patent, i.e., making them public domain. Here’s an example of such a code, attached to a piece of equipment.
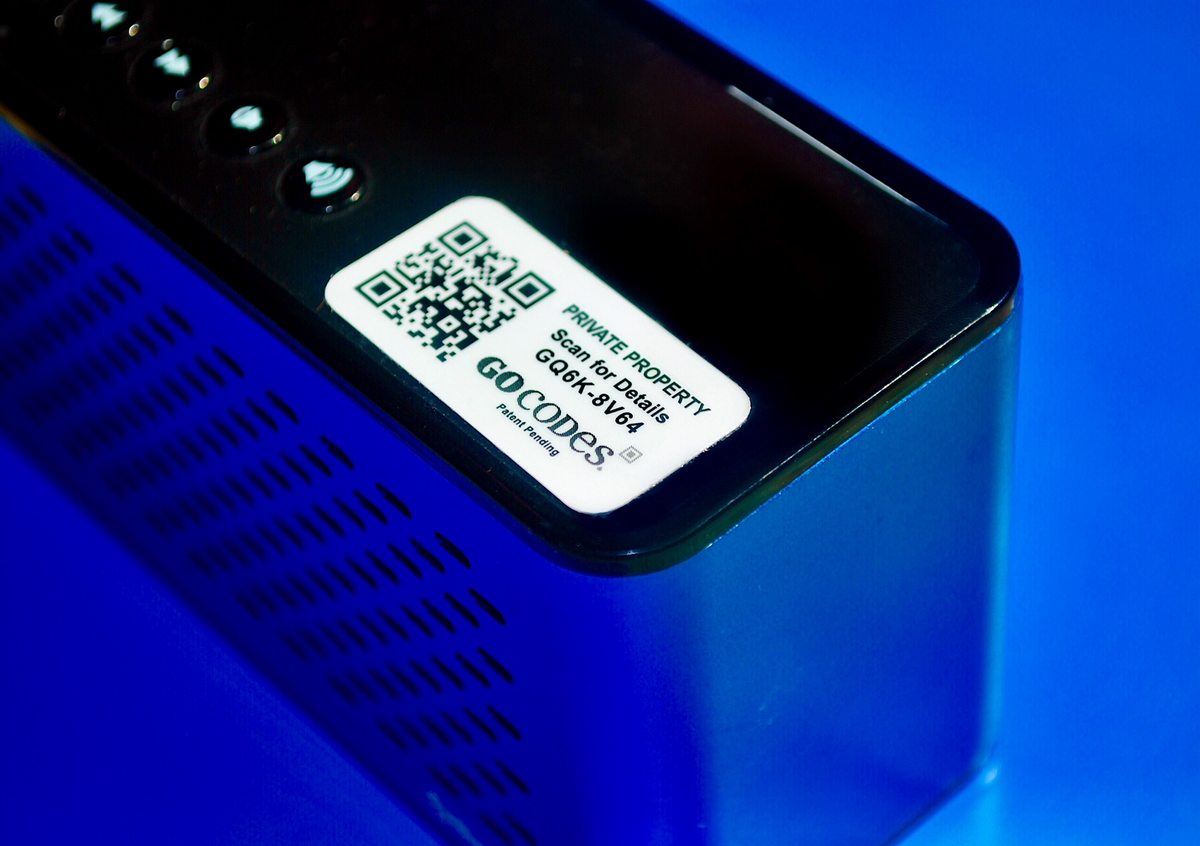
From their component-tracking roots, QR codes slowly but surely conquered the globe, finding their place in a myriad of industries, such as advertising, retail, logistics, healthcare, and, notably, construction.
Even in the construction industry, QR codes have various uses, but we’ll focus on the most relevant ones for equipment managers, which you can see below.
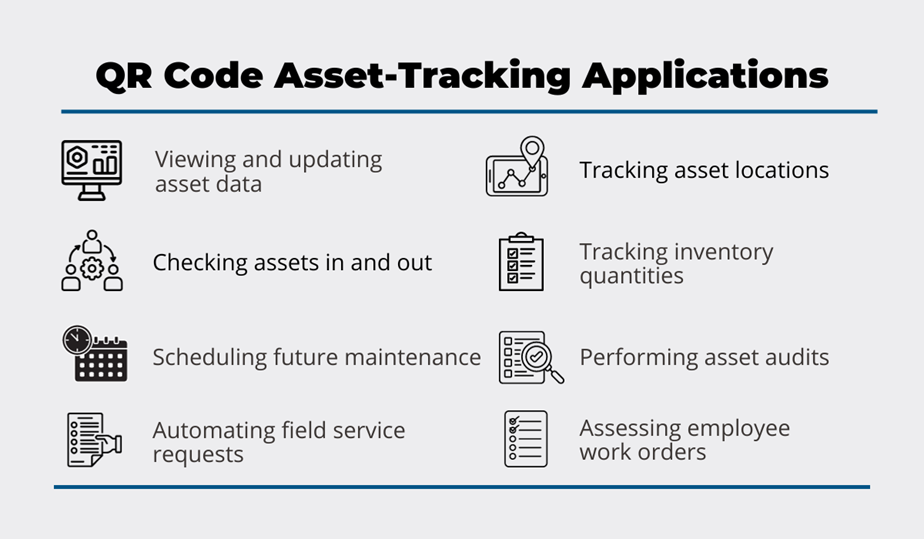
Of course, these applications are not enabled by QR codes alone, but rather by their seamless integration with asset-tracking software.
More specifically, a QR code-based asset-tracking system suitable for construction environments typically consists of:
- QR codes printed on durable, hard-to-remove labels or metal tags affixed to construction equipment, tools, and other assets for identification and tracking purposes,
- cloud software accessible on any internet-connected device at any location,
- built-in scanner for smartphones and tablets, enabling users to easily scan QR code tags to access, view, and update asset info.
To illustrate, we’ll use our asset-tracking solution, GoCodes, as an example.
We solve something that causes a headache for many equipment managers and strains the budget of many construction companies—missing (stolen or misplaced) equipment and tools.
With that in mind, we patented GPS-enabled QR code tags that, when scanned, prompt the software app on the user’s phone or tablet to automatically record the asset’s latest GPS location and show it on a map.
You can see the process here.
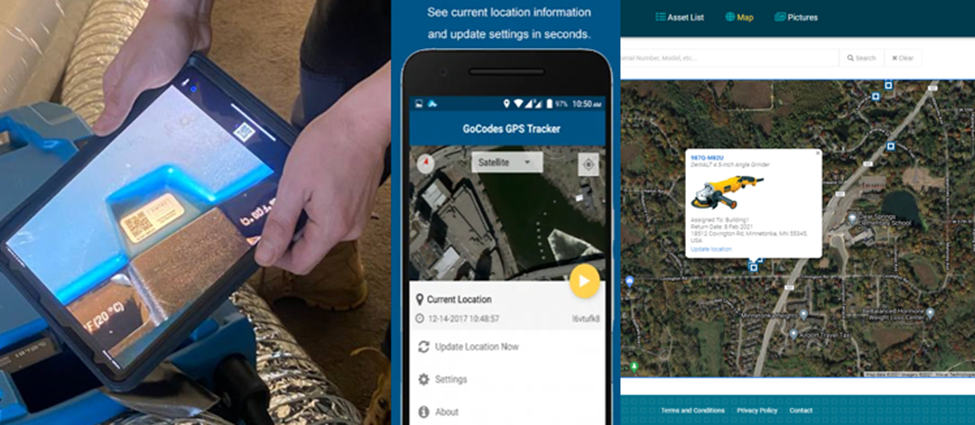
Workers scan the QR code when taking equipment or tools and can scan them back in when returning them, ensuring a clear chain of custody, which increases worker accountability and prevents internal theft, misplacement, or negligence.
You can therefore allocate equipment and tools according to specific project timelines, even organize them into kits, and assign them to specific construction crews.
Additionally, you can automate overdue reminders, ensuring that checked-out assets are returned on time.
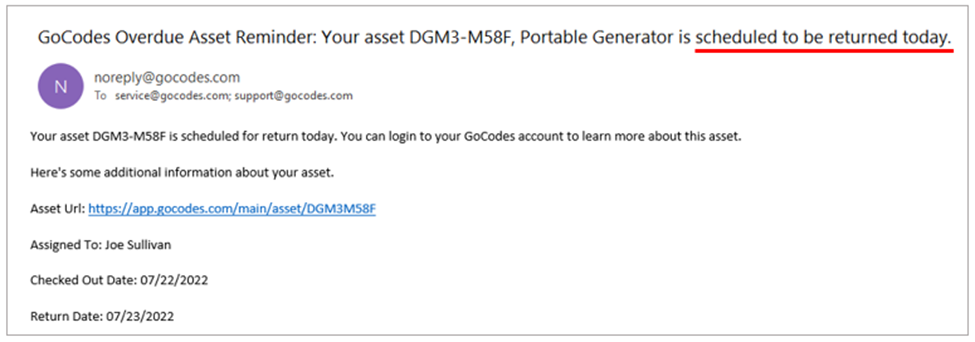
When coupled with the QR code-enabled tracking of equipment users, this scan-based GPS tracking stands out as the simplest and most affordable asset-tracking solution on the market.
Among the many benefits of using a QR code-based tracking system like GoCodes, let’s just highlight that it:
- gives equipment managers complete asset visibility,
- helps minimize theft, loss, and negligent use of equipment and tools,
- increases worker accountability by tracking asset users and locations.
As we’ll see in the next sections, this system also enables various other features, allowing the tracking software to act as an all-in-one equipment maintenance and management solution.
To recap, the versatility and affordability of QR codes and related tracking software systems enable equipment managers to—among other things—streamline asset tracking, enhance security and efficiency, and make data-driven decisions.
Equipment Maintenance Software
Whether as part of an integrated equipment management system or as a standalone specialized solution, maintenance software is another vital technology for equipment managers.
In general terms, its purpose is to enable managers to optimize the maintenance lifecycle of equipment and machinery.
Its features include scheduling regular maintenance, logging service and repair records, and generating alerts for upcoming maintenance tasks.
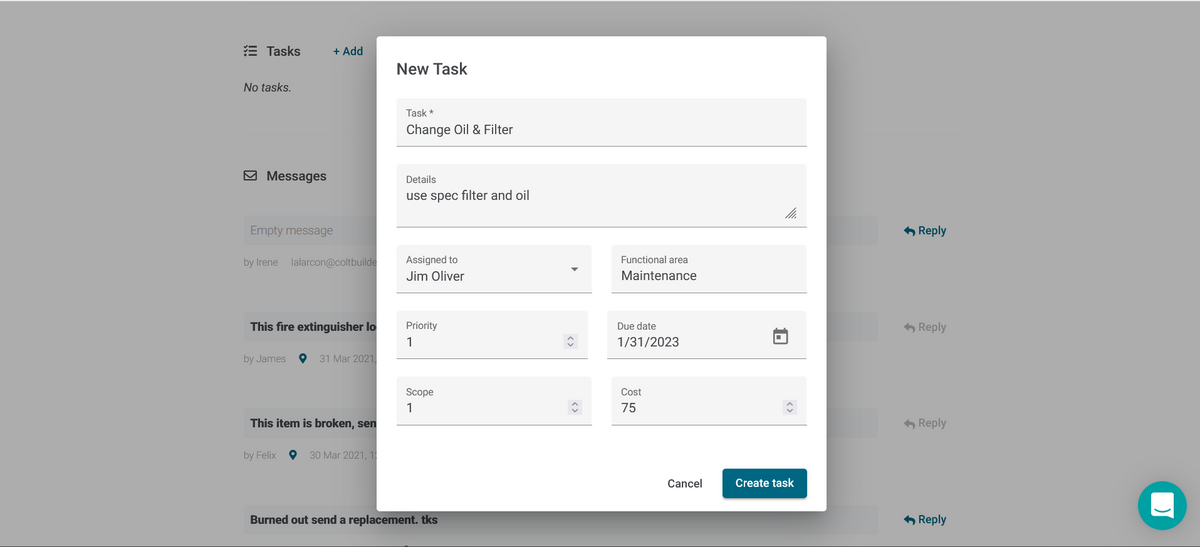
These and other maintenance-related functions are usually enabled by QR code labels attached to individual equipment and used for identification, tracking, and quick data access.
It should be noted that there are other more advanced, sensor-enabled tracking technologies that can further streamline equipment maintenance, which we’ll cover under telematics.
In our example, QR codes provide a unique digital fingerprint for each tagged asset and ensure that maintenance schedules can be linked to specific equipment in the software’s database.
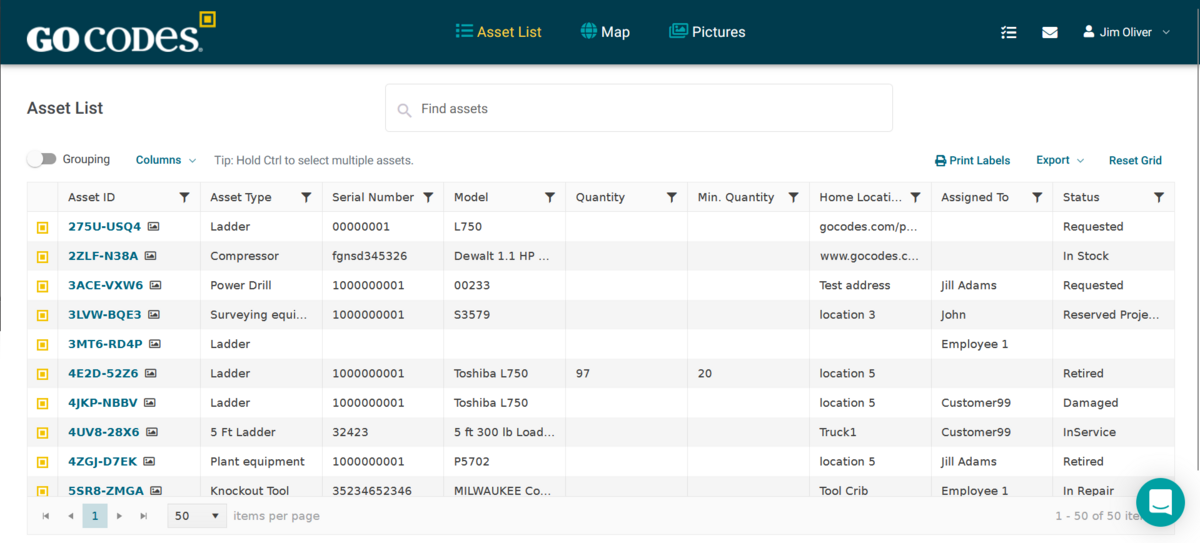
These individual asset info pages can be easily accessed, viewed, and updated by a QR code scan or by logging into the app and searching the central list of all tacked assets.
By leveraging the software’s maintenance features, you can:
- set a preventive maintenance schedule for each piece of equipment,
- assign upcoming maintenance tasks to specific service technicians,
- ensure you’re timely notified via automated email reminders,
- record and document the equipment’s maintenance and repair history.
Moreover, the software’s QR code-based tracking feature extends to equipment inventory needed for regular maintenance, such as spare parts, cables, filters, oils, and other supplies.
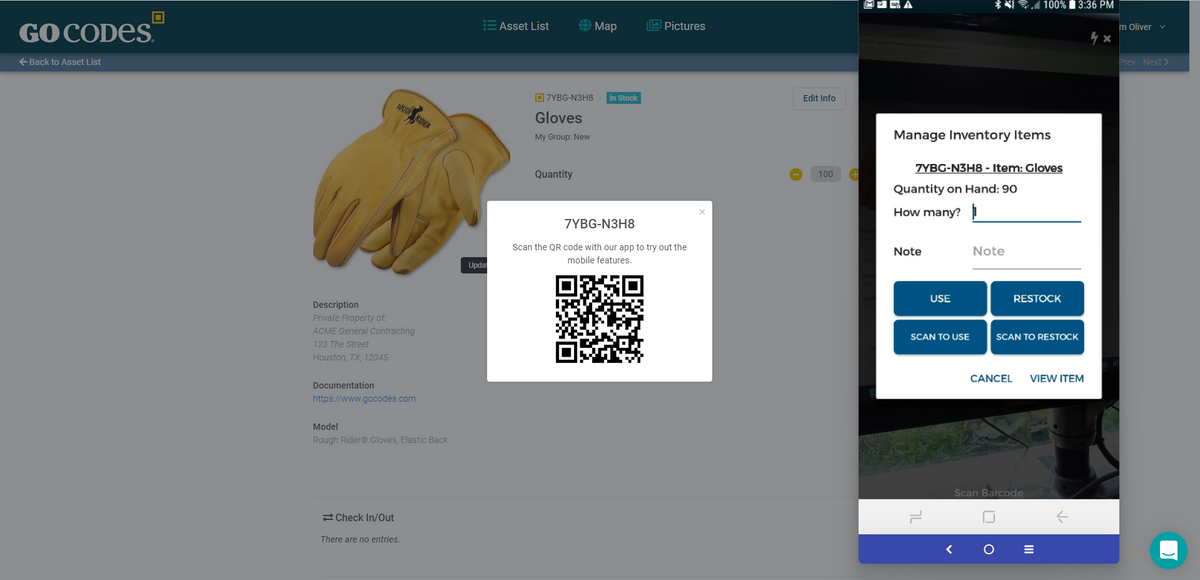
This inventory-tracking feature also comes with low-quantity alerts, ensuring that service technicians will have everything they need for efficient maintenance.
In a nutshell, all the above functionalities help the manager ensure that construction equipment is regularly maintained in line with the manufacturer’s recommendations, warranty conditions, and safety regulations.
This results in less unexpected breakdowns, increased equipment lifespan, improved compliance with various regulations, and enhanced overall reliability of equipment.
These and other benefits make equipment maintenance software an essential technology for managers who want to streamline maintenance operations and ensure that equipment is well-maintained and operating at optimum efficiency.
Equipment Management Software
As explained, some software solutions integrate equipment tracking, maintenance, and management into a centralized platform that you can use to streamline various aspects of your jobs.
This approach simplifies data management, reduces redundancy, and provides a single interface for users.
Alternatively, construction companies may opt to integrate several software solutions using application programming interfaces (APIs) into a single system customized to their specific needs.
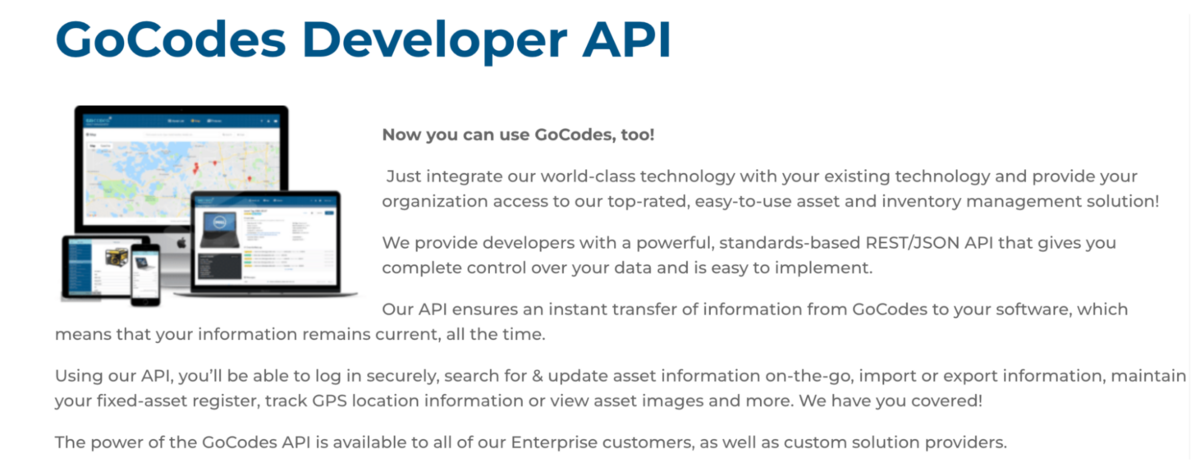
For example, smaller and mid-sized companies might find all-around solutions more convenient and affordable, while larger enterprises might prefer more customized software integrations.
Ultimately, this decision will depend on factors like the scale of company operations (i.e., the size of its equipment fleet), workflow complexity, and budget considerations.
In any case, equipment management software is an umbrella that covers both asset tracking and equipment maintenance functions we described and adds extra features.
These can include:
- establishing an equipment check-in/check-out system, including automated reminders when a checked-out asset is not returned on time,
- scheduling/assigning/reserving equipment and tools in advance, including tool kitting,
- tracking equipment inspections and managing related checklists,
- managing equipment-related work orders,
- calculating and tracking equipment depreciation,
- leveraging equipment data analytics and report generation.
Overall, the versatility of equipment management features gives managers real-time insights into different equipment utilization parameters, which allows them to, for example:
- coordinate equipment use,
- minimize equipment downtime (whether during projects or for maintenance),
- optimize equipment lifecycles, from acquisition to disposal,
- maximize overall equipment effectiveness.
Moreover, the software can be leveraged to track the depreciation cycle of equipment, ensuring accurate financial reporting, and informing repair-or-replace decisions.
Lastly, data analytics and reporting features can be used to analyze equipment usage trends, providing valuable insights for strategic planning and resource optimization.
To recap, equipment management software is a perfect technology for managers to streamline multiple aspects of their role, leading to increased efficiency and informed decision-making.
Equipment Telematics
Until now, we looked at equipment management features arising from using QR codes and cloud software to access info and track equipment users and locations.
This tracking is passive, meaning that an asset has to be scanned for its location to be captured, and any equipment-related observations are entered into the system manually.
With the help of telematics (active GPS trackers and equipment sensors), equipment managers can automate many of these processes and monitor the location, usage, and condition of construction vehicles and equipment in real time.
Here’s how a telematics system works.
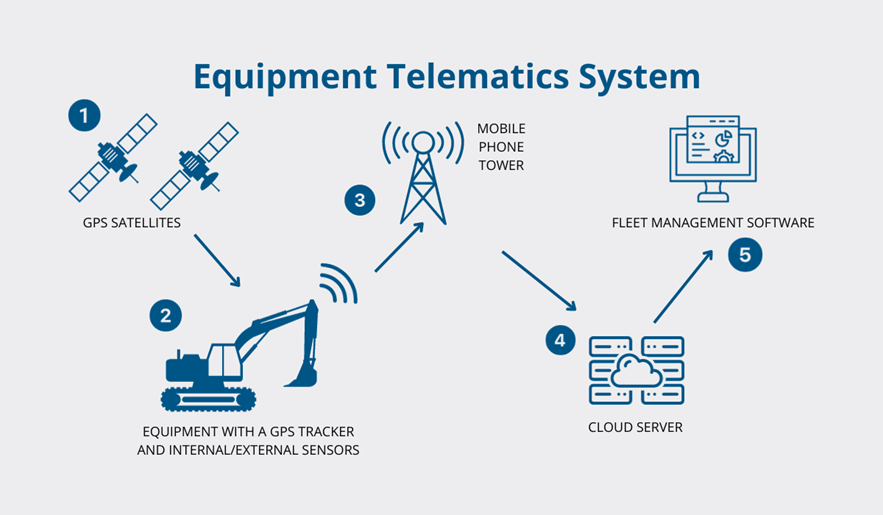
As illustrated, telematics is enabled by GPS trackers and various sensors, whether they come with equipment or were installed later.
In any case, when real-time data generated by equipment trackers and sensors is recorded and processed within a single system, this can catapult the efficiency of equipment management to unprecedented heights.
For example, the software can automatically track a wide range of equipment utilization parameters, such as operating hours, speed, fuel consumption, engine temperature, and idling time.
Furthermore, continuous location tracking improves the security and safety of vehicles and equipment and allows the manager to optimize driving routes and equipment allocation.
Concurrently, on-board diagnostics (OBD) or external sensors can provide real-time data on equipment conditions, enabling predictive maintenance and reducing unplanned downtime.
In summary, equipment telematics (GPS trackers and sensors) allow managers to take advantage of automated, real-time monitoring of equipment movements and conditions, enhancing overall efficiency and control in construction equipment management.
Augmented Reality (AR)
Augmented Reality (AR) and Virtual Reality (VR) technologies are increasingly used in the construction industry for design visualizations, virtual project tours and walkthroughs, site planning, and equipment operation training.
As for their differences, AR overlays digital information onto the physical world, enhancing the user’s perception, while VR creates a completely simulated environment.
For equipment managers, both technologies present unparalleled opportunities to streamline equipment management and training processes, increasing employee performance and safety, and reducing the learning curve for new operators.
For example, by utilizing Vrexa AR construction glasses, operators can receive on-site, real-time instructions or remote jobsite training.
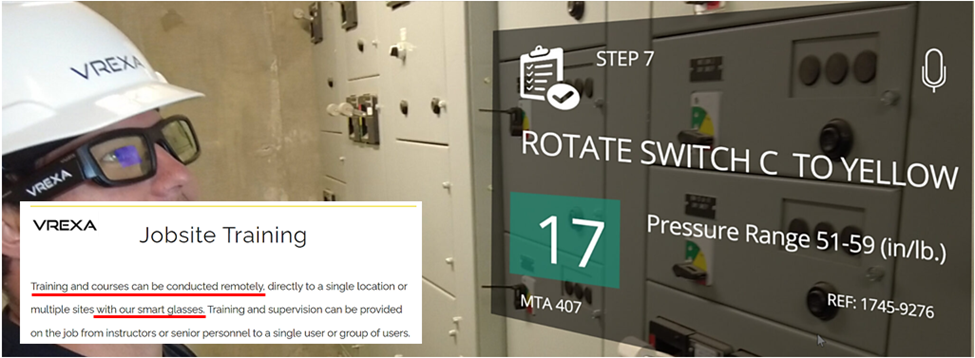
This not only enhances safety during the learning process but also accelerates operator readiness.
Similarly, by leveraging VR-based equipment operation modules, you can ensure that operators (and maintenance technicians) are prepared for a wide range of situations you may encounter.
More specifically, these training simulations aim to familiarize operators with controls, functions, and safety procedures in a virtual setting and take them through complex scenarios involving challenging operating conditions and malfunctions.
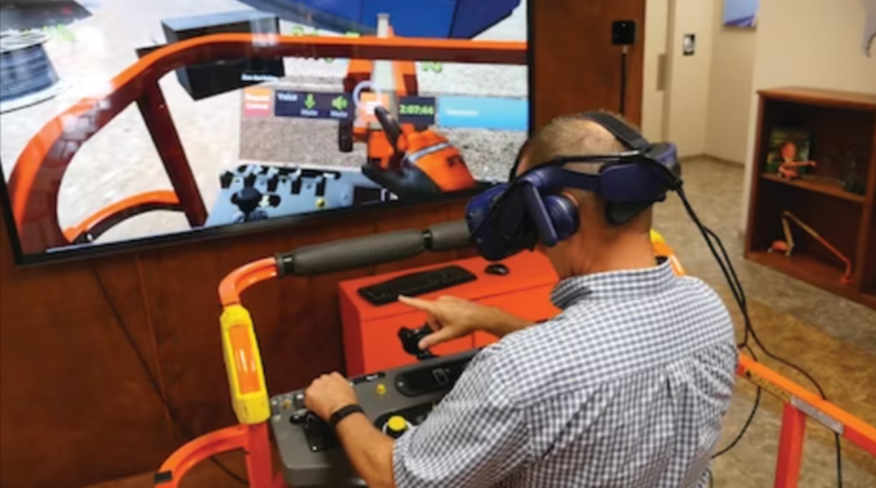
By mimicking real-world scenarios, such VR training simulations allow operators to experience potential operating challenges and safety hazards and learn how to respond to them without actually exposing them to such situations.
Given all the above, it’s clear that you can use various AR and VR applications to enhance equipment safety, training, and equipment management processes.
Drones
Lastly, drones have already become indispensable tools in the construction industry with 37% of companies citing they already use them in construction operations.
The main reason for such high uptake is their ability to capture high-resolution aerial imagery and provide real-time data more efficiently and safely than their human counterparts.
They offer versatile construction applications ranging from site surveying, mapping, and inspections to project progress monitoring, client presentations, and marketing materials.
For example, drones are ideal for inspecting high-rise buildings, like in the case of façade inspections.
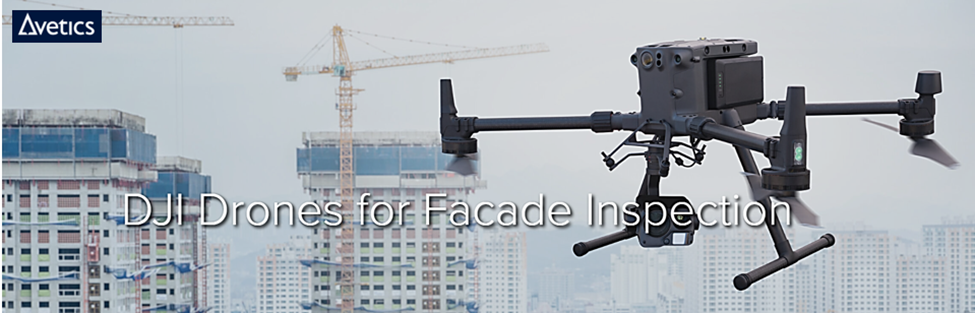
So, assuming their company already uses drones for other purposes or is willing to invest in one or more, how can managers use them to streamline their equipment management processes?
For starters, since drones provide a real-time bird’s-eye view of the entire construction site, you can quickly and accurately survey and catalog the equipment (and other assets) present on-site.
This aids in tracking the location of equipment, assessing its condition, identifying potential issues, and optimizing on-site equipment deployment and movement.
Similarly, you can use drones to conduct aerial surveys of equipment yards or storage areas, helping maintain accurate and up-to-date inventory records.
Additionally, drones can be leveraged during site preparation, enabling managers to assess terrain, plan equipment layouts, and identify potential challenges.
They can also assist in emergency response planning, swiftly assessing the impact on equipment and other on-site infrastructure in cases of extreme weather and natural disasters.
Overall, drones can provide equipment managers with a valuable aerial perspective, facilitating surveys and inspections, enabling real-time data collection, and enhancing safety and efficiency.
Conclusion
To summarize, the options arising from adopting and combining these technologies to streamline equipment management are practically endless.
However, the price and ease of use rule the game, so you should start by identifying your company’s actual needs and researching different software solutions and technologies.
In doing so, you should prioritize simple and user-friendly interfaces, quick and easy system setup and deployment, and the required (and provided) user training and support.
When properly implemented, the right tech solutions can transform equipment-related operations, and make the equipment manager’s job much easier while boosting your company’s overall productivity and profitability.