The modern construction site is almost like a symphony of heavy machinery, tools, and other equipment, each playing a crucial role in bringing architectural visions to life.
However, the seamless orchestration of these mechanical behemoths requires more than just acquisition and deployment—it demands a strategic approach to equipment management as a whole.
In this article, we delve into five methods of equipment management that every construction business owner, project manager, or site supervisor should be well-versed in.
Some of these tools may already be familiar to you, while others could be completely new to you.
Regardless, you are bound to acquire new insights and improve your proficiency in the art of asset management.
Let’s begin with the most well-known approach.
In this article...
Spreadsheets
Spreadsheets have been used for equipment management for a long time now.
So long, in fact, that some might even call them old-school.
Nevertheless, many industry professionals still regard them as the best way to monitor or manage their assets and, given the benefits that spreadsheets provide, this preference is actually not that surprising.
Not only is everyone already familiar with them to some extent, but they are also fairly budget-friendly, easy to use, and generally require minimal to no special training before implementation.
It wouldn’t be fair, therefore, to dismiss this approach as an unviable solution for some businesses, particularly those that are asset-light.
Keeping track of the home or current location and status of a couple of machines isn’t that challenging anyway, even with Excel.
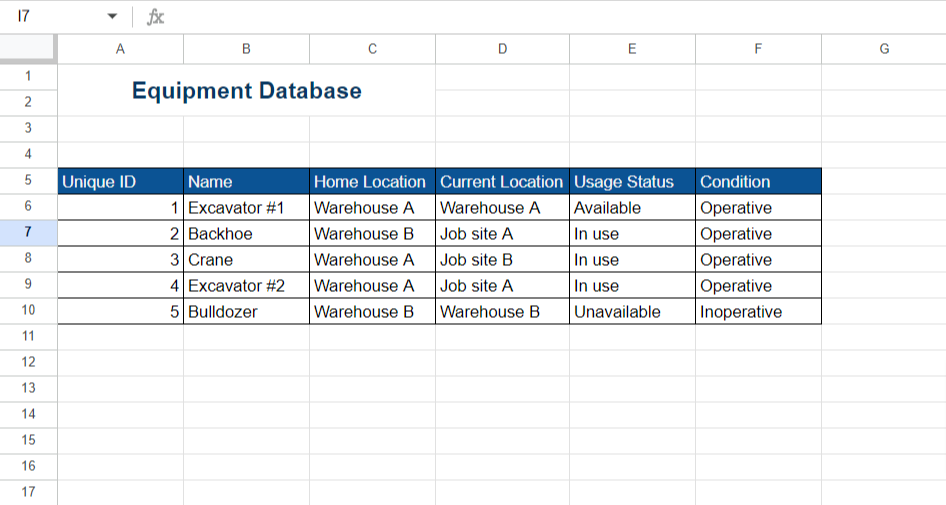
However, this brings us to the first disadvantage of spreadsheets: a lack of scalability.
While they work well for startups or businesses with a modest asset portfolio, asset-intensive companies often encounter challenges when they have to manually update the location, status, user, or condition for every single piece of their equipment.
Spreadsheets simply can’t handle such large volumes of assets.
Moreover, the more equipment a company manages through spreadsheets, the more apparent their second drawback becomes—susceptibility to human error.
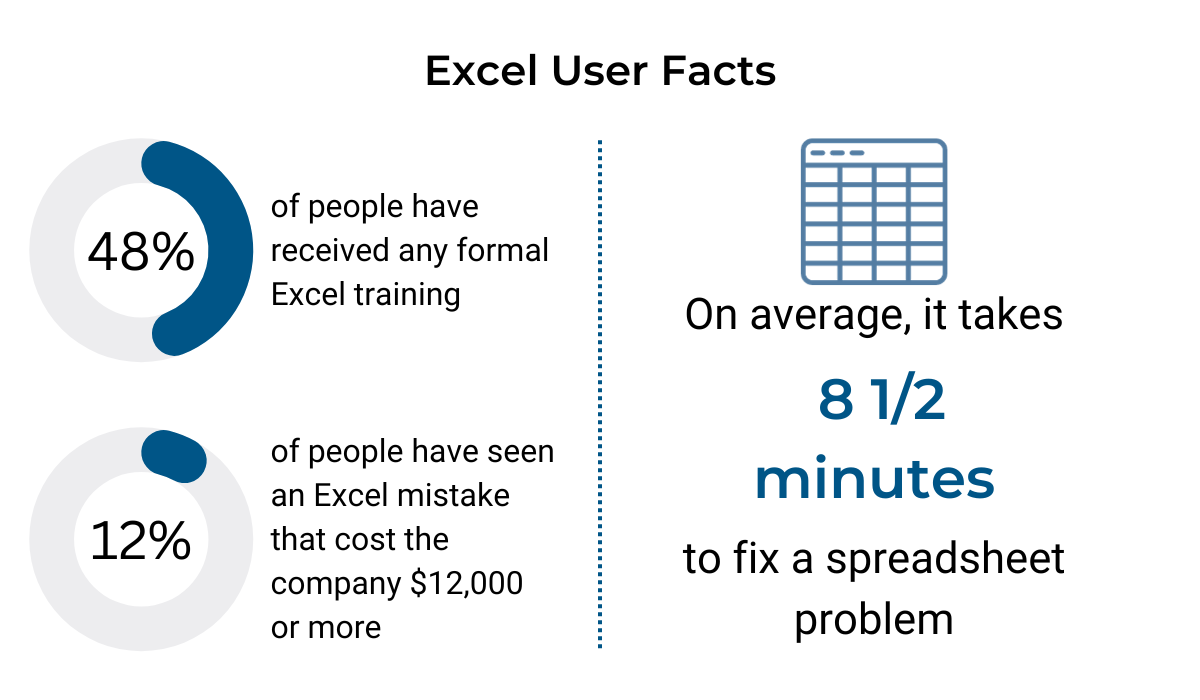
And we’re not talking about a simple typo here or there, but about mistakes that can significantly impact operational efficiency, productivity, and, of course, the profitability of a company.
In short, it all boils down to the fact that this method was never designed with the complexities of construction equipment management in mind.
Kenny Ingram from IFS, an enterprise software company, considers spreadsheets a liability rather than an asset.
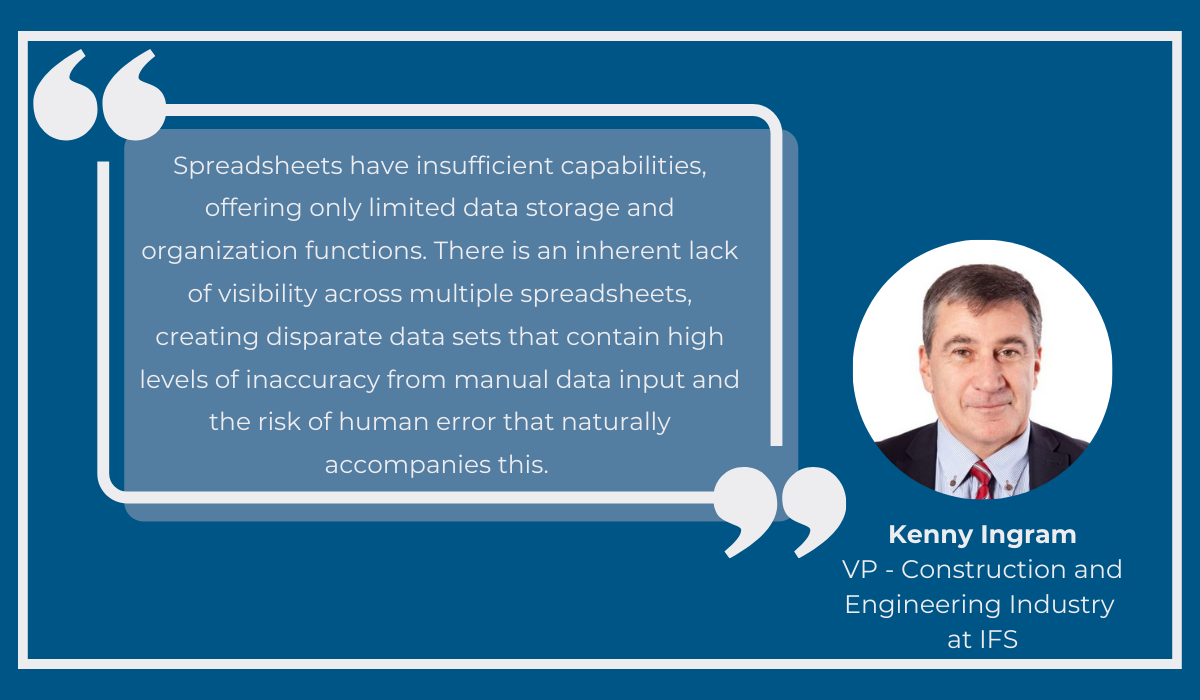
According to him, the lack of complete equipment visibility resulting from inadequate asset management adversely impacts decision-making and, in turn, leads to poor financial health.
So, what’s the best alternative to spreadsheets, then?
The answer lies in adopting methods that address their primary weakness—the manual input of data.
Opting for systems that automatically update crucial equipment information can eliminate errors and enhance the overall efficacy of the equipment management process.
The following sections of this article explore tools that achieve precisely that.
Equipment Management Software
Equipment management software, as the name itself suggests, is a specialized piece of tech precisely developed for the intricate task of overseeing and managing your company’s tools, vehicles, heavy machinery, and more.
What sets these data-rich systems apart from the rest of the solutions we’ll be covering in this article is the fact that they can be relied upon for decision-making at any stage of an asset’s service life, from acquisition to disposal.
They also prove particularly beneficial in addressing one of the industry’s major pain points—the issue of missing equipment.
If you’ve ever experienced this problem, you already know how it can impact your team’s productivity and waste both your precious time and money.
So, when J&M Keystone, Inc., a business specializing in emergency construction services, faced substantial budgetary setbacks due to misplaced tools, instead of resorting to Excel, they turned to GoCodes Asset Tracking, equipment management software.
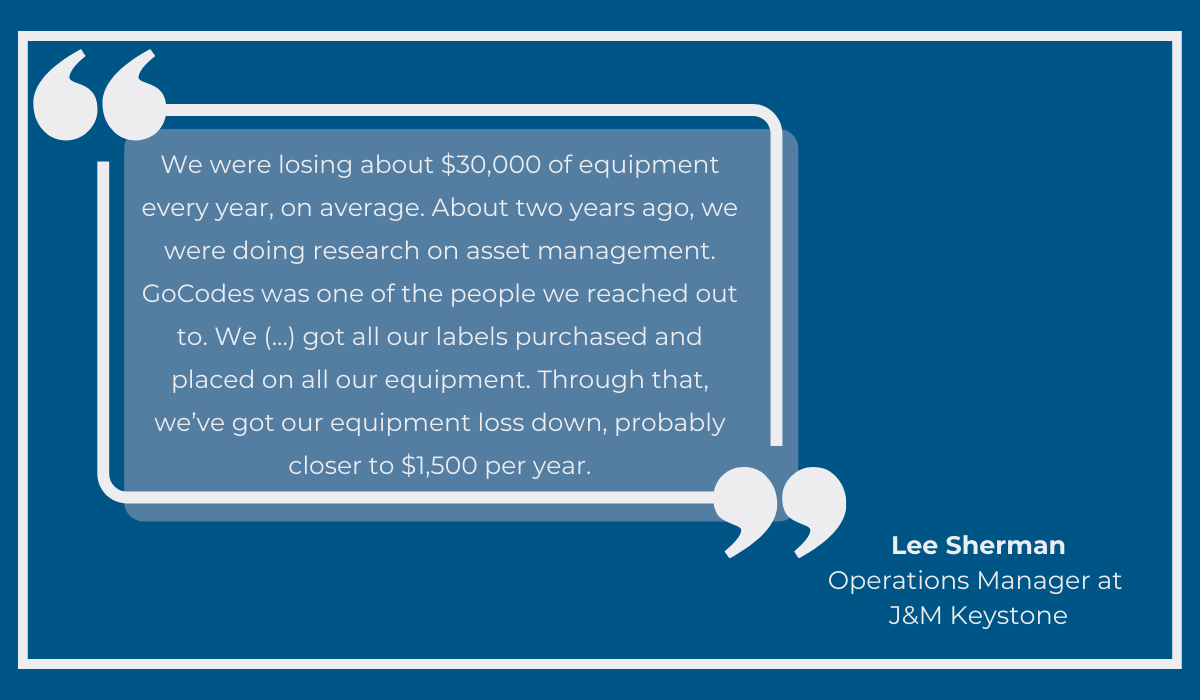
Following a successful free trial, they decided to purchase the system along with our QR code labels—a move that significantly minimized instances of lost tools and, in turn, reduced financial losses for the company.
Wondering how GoCodes Asset Tracking achieved this?
After you attach them to your machines and tools, the QR code labels can then be scanned to check that specific asset in or out, or to simply view asset data.
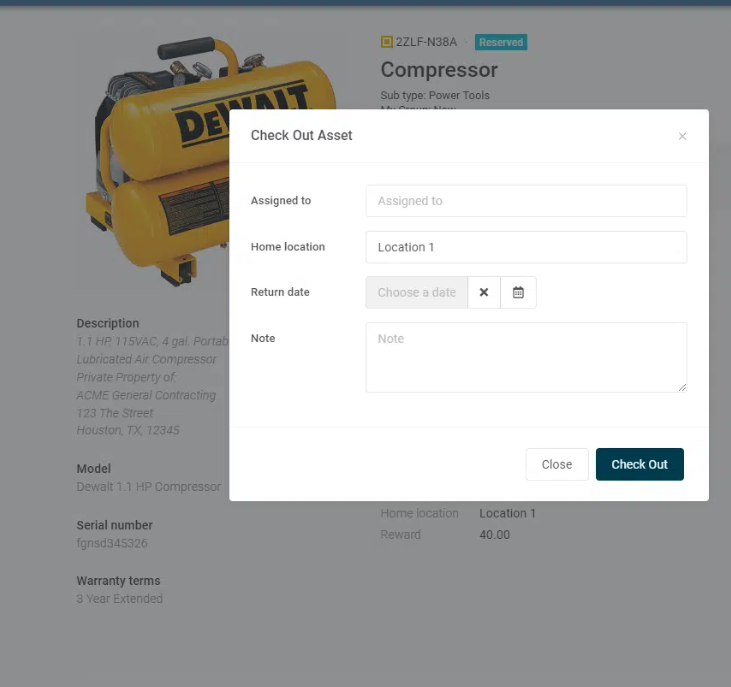
Every time each of these actions is done, the location of the asset is automatically updated.
These check-out/check-in and location monitoring features are exactly what J&M Keystone employees rely on in their daily tasks.
Over time, they were able to establish a detailed and error-free check-out log, providing insights into the assets’ whereabouts, status, and users, thus enabling better coordination among workers and swift retrieval of lost equipment.
Therefore, when a particular item went missing, they would just pull out their phone and confirm its last known location on Google Maps via the GoCodes Asset Tracking app.
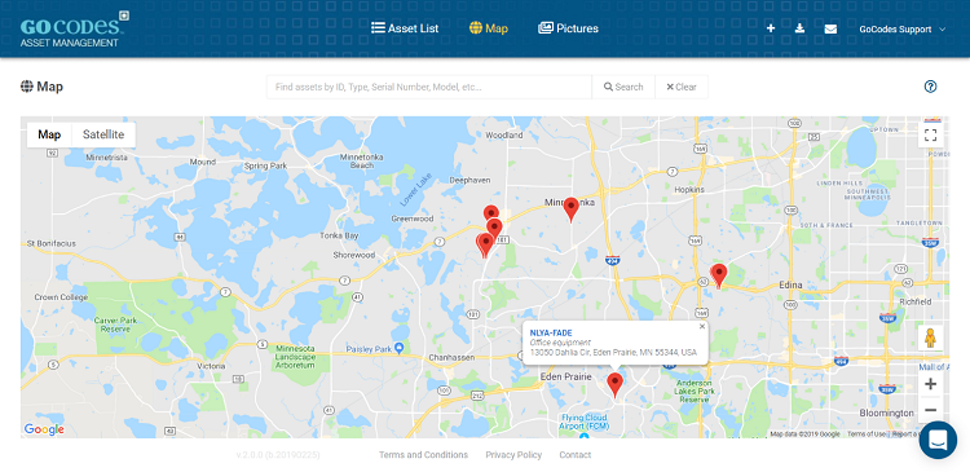
By eliminating the problem of tool misplacement, they didn’t just improve profitability but efficiency as well.
There was no more need to search for the nearest computer and scroll through spreadsheets to find that precious asset data or engage in a detective-like effort to identify the last person to use the missing tool.
All the vital information was already in the system, accessible through only a couple of taps on their phone screen.

Who knew equipment management could be this easy?
Apart from mobile accessibility, the check-out system, and location tracking, GoCodes Asset Tracking boasts numerous other features that elevate business operations to new levels, regardless of a company’s size.
Generally speaking, these management systems have become one of the most popular methods for overseeing assets, not only because of their user-friendliness, but also due to their unique capability to manage equipment throughout its entire life cycle,
Anything from planning maintenance and monitoring equipment utilization to tracking depreciation can be done via such software.
Nevertheless, if you’re in need of solutions that focus on more specific parts of equipment management, then maybe the next two systems will be of more interest to you.
Computerized Maintenance Management System (CMMS)
Computerized Maintenance Management Systems, abbreviated as CMMS, play a crucial role in asset management by focusing on maintenance.
These solutions help enhance businesses’ efficiency in handling equipment upkeep and inspections by organizing and tracking relevant data, overseeing service tasks, and measuring the effectiveness of the work that they are doing.
Common features of CMMS include:
- Work order tracking
- Service task management
- Reporting
- Unplanned downtime monitoring
- Centralized asset registry
With such a robust array of features, the often complex task of equipment maintenance becomes notably more manageable.
And let’s face it, forgetting to, for example, replace the oil or filter on a machine is not that uncommon, but can lead to serious problems down the line.
CMMS prevents such oversights by introducing transparency in everyone’s responsibilities and offering insight into each machine’s condition, all without compromising team efficiency.
In fact, Christopher Lindsay, Senzit’s head of sales, advocates that these automated systems increase productivity.
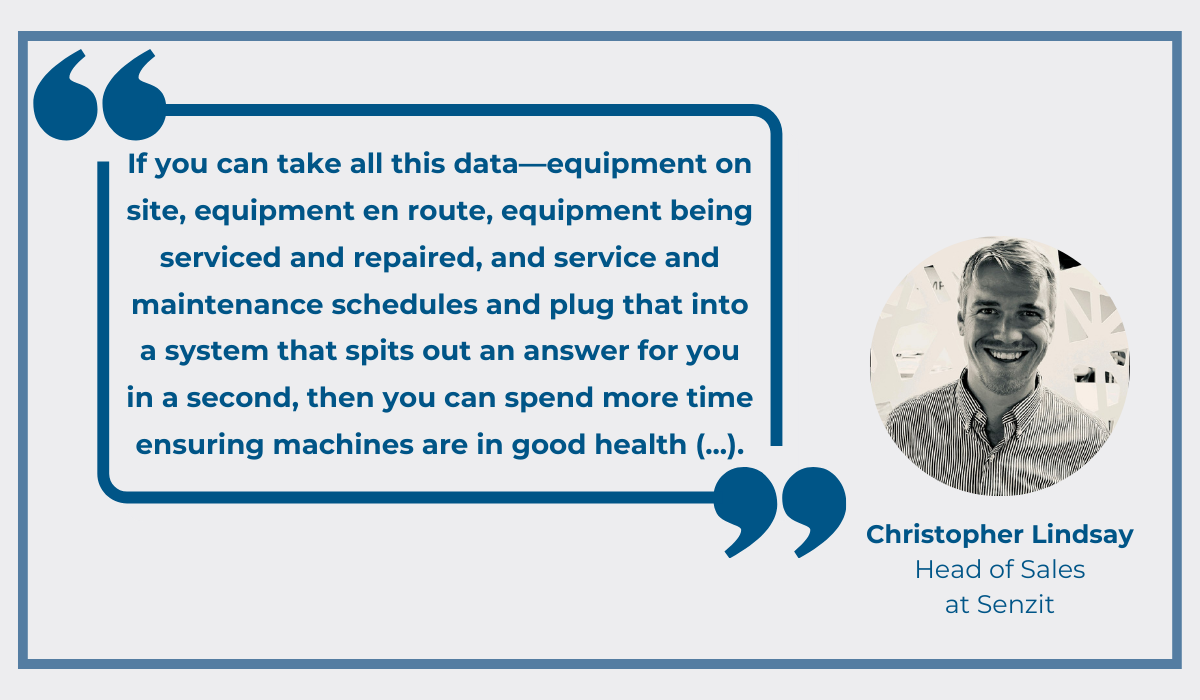
Regular checkups and minor repairs facilitated by CMMS avert larger issues or asset failures, effectively reducing unplanned downtime—an essential consideration, given that 80% of productivity decrease is linked to such workflow disruptions and subpar maintenance practices.
However, as comprehensive as CMMS is in enhancing maintenance processes, its scope is limited when it comes to overall equipment management.
While adept at tracking and managing maintenance, CMMS falls short in providing a holistic approach to asset lifecycle management, as the equipment management systems we mentioned earlier do.
So, is CMMS sufficient for effective asset management?
Alone, probably not.
In most cases, it works much better in combination with other equipment management and tracking solutions, but the “better” choice depends on the particular goals, priorities, and workflows of your company.
Some businesses might even discover that a blend of equipment management software and CMMS meets their specific needs the best.
Equipment Rental and Reservation System
Equipment rental constitutes another significant aspect of asset management—a process that’s optimally managed through the utilization of rental and reservation software.
These systems were developed for tracking rented machinery, maintaining adequate equipment availability for renters, and generally enhancing the efficiency of the entire rental process.
Common features of such systems include:
- Equipment availability records
- Quote and invoice generation
- Tracking equipment across multiple warehouses and locations
Interestingly, the reservation software serves both sides of the process, benefiting rental companies and renters alike.
These solutions meticulously monitor inventory, eliminate the issue of double bookings that rental businesses may face, and provide companies looking to rent out machinery with complete visibility of equipment availability through a user-friendly interface.
This eradicates confusion and ensures they get what they need when they need it.
The growth in equipment rental revenue, projected to increase in the coming years, underscores the competitiveness of the industry.
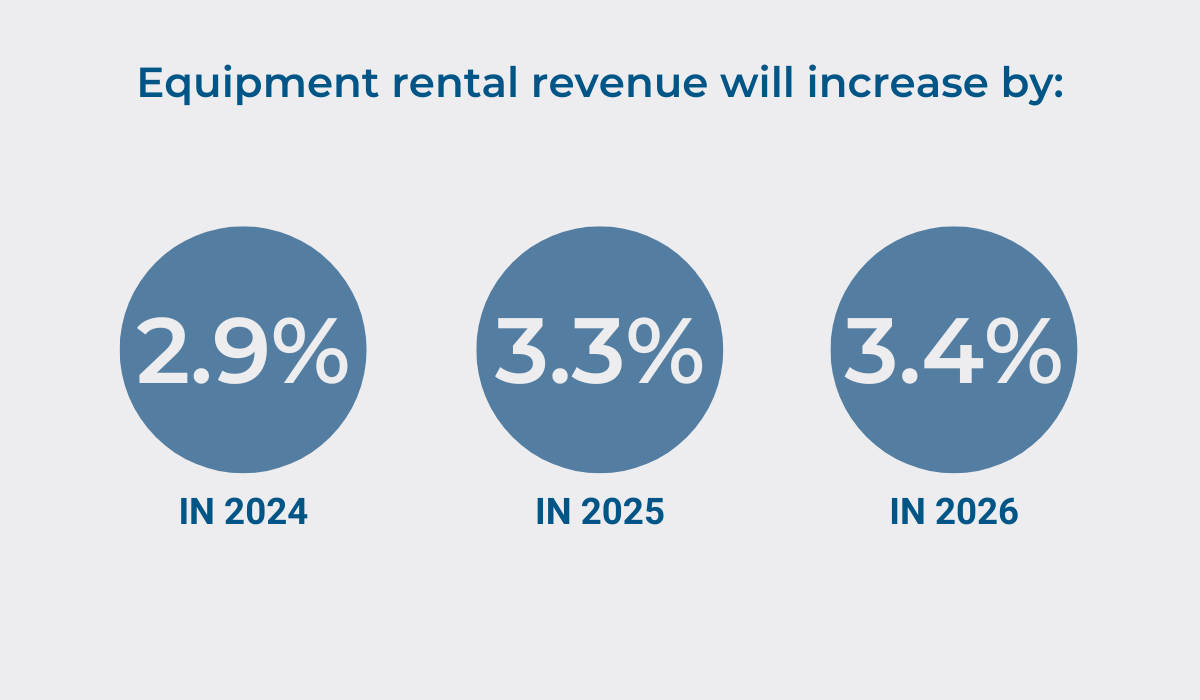
Continuous rental process improvement is essential to stay ahead, and automated reservation solutions play a pivotal role in achieving this.
For Lauri Halonen, CEO of Vanaja Event Solutions, a company specializing in event production and equipment rentals, these systems are not just a tool, but a necessity that helps him and his team stay on top of their valuable assets.
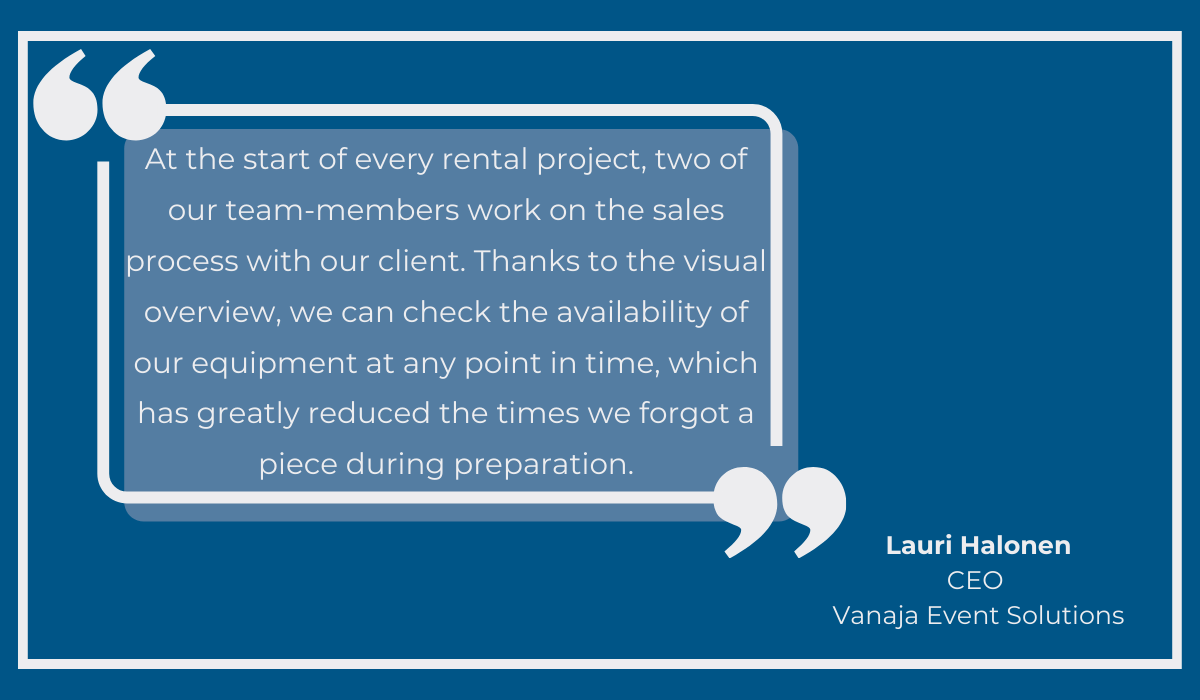
The software makes sure that no piece of equipment is overlooked during the event preparation phase, streamlining many of their daily tasks.
But although these systems are powerful tools, just like CMMS, they focus on specific aspects of asset management and do not encompass the entire equipment lifecycle.
So, given the multifaceted nature of equipment management, they are most effective when used in conjunction with other asset management methods.
Enterprise Resource Planning System (ERP)
Unlike all the previously mentioned tech solutions, ERP systems are designed to manage whole business operations, encompassing tasks such as accounting, tracking subcontractors and building materials, managing human resources, assets, various project-related costs, and more.
Ben Harrison, vice president of product management at Preferred Strategies, highlights the significant evolution of ERP solutions since their inception in the ’60s and ’70s, progressing from simple accounting tools to complex systems capable of overseeing entire companies.
Here’s how he defined ERP systems on the GroundBreakers podcast.
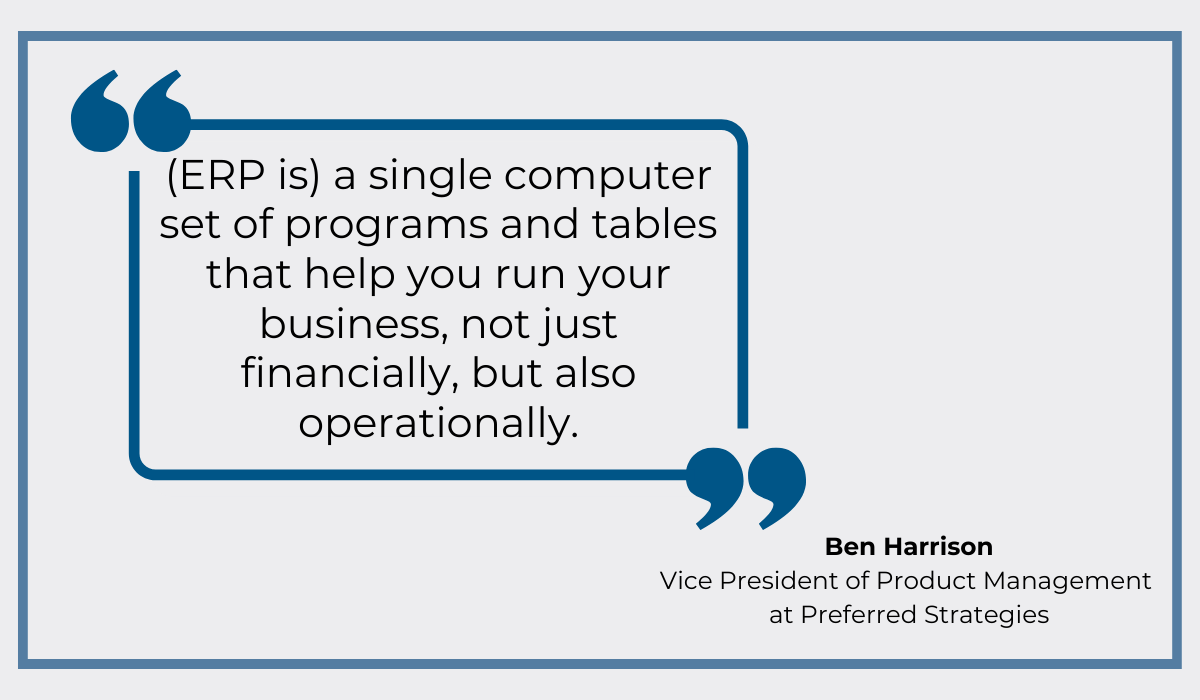
Truly, not many systems can compete with ERPs when it comes to navigating the complexities of construction projects.
A report by JBKnowledge indicates that enterprise resource planning and accounting are the two areas where industry professionals are most likely to utilize dedicated software.
In this domain, they are simply unwilling to take risks with manual methods like spreadsheets.
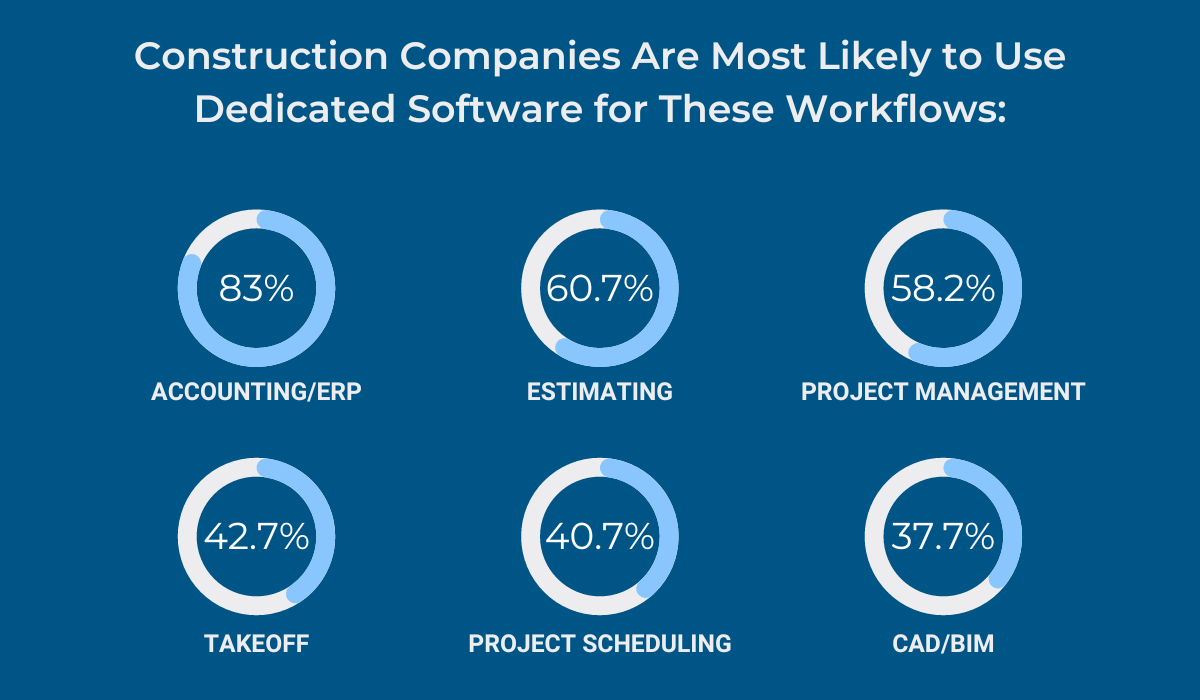
For them, using ERP software is non-negotiable.
However, when specifically addressing asset management, these versatile and functionality-rich software solutions can quickly become too complicated and overwhelming for users.
As a matter of fact, they aren’t something you can just figure out on your own; proper training is required in order to be able to use the software efficiently.
Add to that the steep price of these solutions, and suddenly they become somewhat less appealing.
Still, there is a way to overcome both the complexity and high cost of ERPs: integrating them with equipment management systems.
This approach allows for the monitoring of asset life cycles through a simpler, user-friendly equipment management system, while all that vital data can be transferred and analyzed in the ERP, too.
Essentially, equipment management can be done through the dedicated software, while the rest of the operations can still be handled via ERP.
That way, you simplify the asset tracking process and eliminate the need to purchase unnecessary ERP licenses for every single team member.
In short, by combining the strengths of ERP and asset management systems, you can achieve a streamlined and cost-effective solution for managing diverse aspects of your operations.
Conclusion
All in all, finding the right method for equipment management can make all the difference when it comes to your business’s success.
Not only can you optimize costs and enhance productivity through efficient management of your assets, but you can also improve the longevity of your machinery and ensure compliance, as well as overall job site safety.
So, how do you choose the system that’s best suited for your company?
Well, that’s up to—you guessed it—you.
So, use what you’ve learned from this article, conduct some of your own research, and you’ll be able to find and implement the solution that will take your business to whole new heights in no time.