Key Takeaways:
- Poor quality control practices and mindset lead to choosing speed over quality.
- By using the right technology, you can avoid unplanned downtime.
- Rethinking hiring practices and investing in training initiatives helps construction companies overcome labor shortages.
Each construction project comes with a set of requirements and specifications that need to be met.
However, getting there often feels like navigating a winding obstacle course of tight deadlines and unforeseen delays.
What sets apart seasoned construction project managers from the rest is their ability to overcome these obstacles.
That is why today, we’ll explore six such challenges in construction project management and share tips on how you, too, can tackle them effectively.
Let’s get started!
In this article...
Preventing Cost Overruns
Cost overruns can endanger not only your projects, but your construction company as a whole.
Whether it’s due to changes in scope, poor communication, market conditions, or all of the above, there’s no denying that cost overruns occur more frequently than we’d like them to.
In fact, McKinsey’s research has shown that a staggering 98% of megaprojects face significant cost overruns or delays, with some notorious cases facing cost overruns of 2 to 14 times the original budget.
One notable example is the Berlin Brandenburg Airport, whose construction was marred by design flaws, poor management, and political interferences.
These combined factors caused the costs to skyrocket from €2.8 billion to €7 billion (approximately $7.63 billion), drawing public criticism and ridicule.
Given the complexity of such large projects, you may be wondering whether such challenges and overruns can happen to construction projects no matter the size.
The answer is: they sure do.
Forbes Georgia recently reported on research about the underlying reasons behind cost overruns in the Georgian construction industry, which featured companies of all sizes.
Based on their frequency and impact, the top 3 identified causes were inflation, delays in getting approval from the project owner, and poor cost estimating in the preconstruction phase.
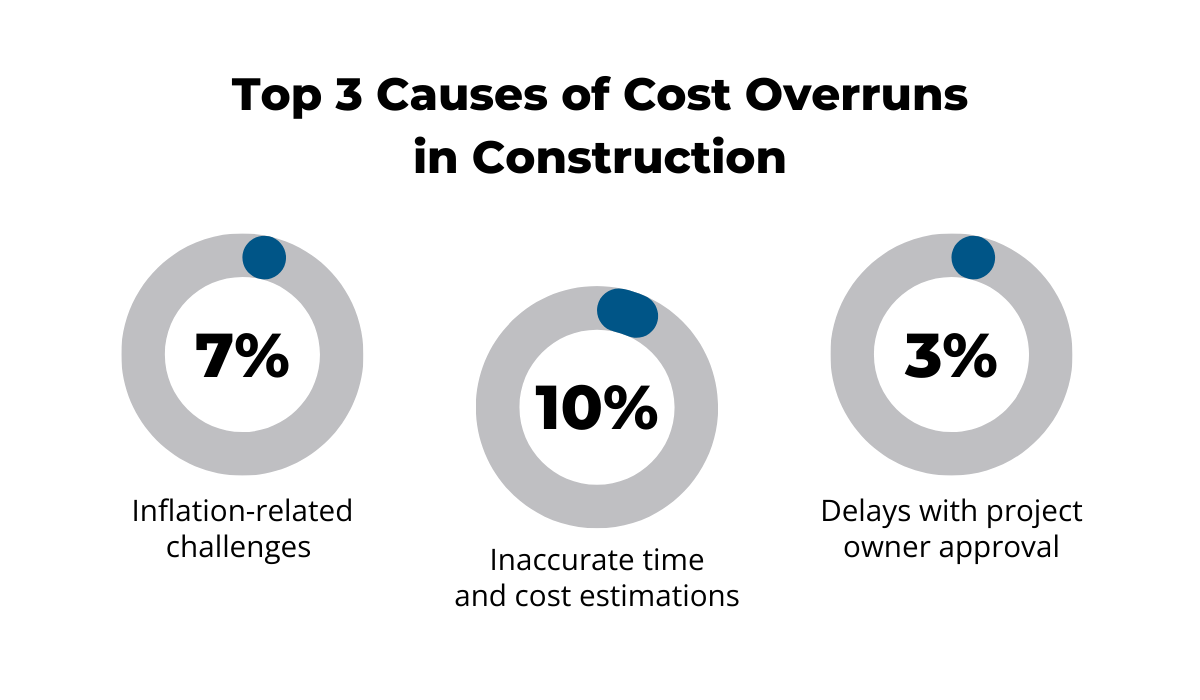
Inaccurate estimations have the most severe impact, but even delays in securing approval can escalate the costs by 3%.
The question is, what can you do to stay on track?
The lessons from a more recent McKinsey research suggest that the answers lie in “preconstruction excellence.”
In other words, it’s vital to invest time and effort in your decision-making process before construction even begins.
This includes defining:
- a robust execution plan,
- an optimized contracting strategy, and
- transparent project delivery systems.
Iftikhar Ali Gaur, Operations Director at ZEC, one of Saudi Arabia’s biggest engineering consultancy firms, echoes this sentiment, but focuses on overcoming cost estimation challenges based on previous experience.
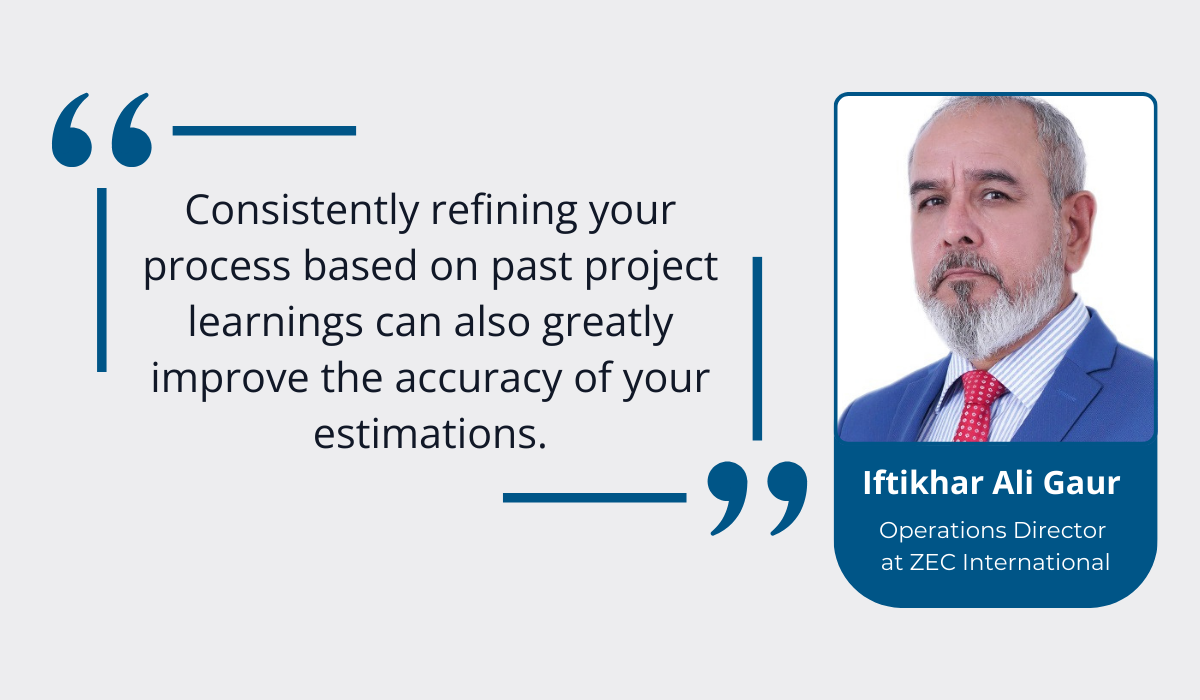
By incorporating historical data and refining processes with future operations in mind, companies can keep costs in check and projects on track.
While cost overruns can have many underlying reasons, thorough planning will ensure your company remains stable and even thrives amid challenges.
Managing Construction Equipment
Many construction companies struggle to effectively track, maintain, and manage their equipment, especially across multiple job sites.
One of the main consequences of poor equipment management is poor asset visibility, which then leads to equipment breakdowns and prolonged idle time.
This, in turn, erodes productivity and profit margins.
In contrast, according to CAT’s estimates, making an effort to reduce idle time by just 17% (from 50% to 33%) can lead to total savings of $92,608.
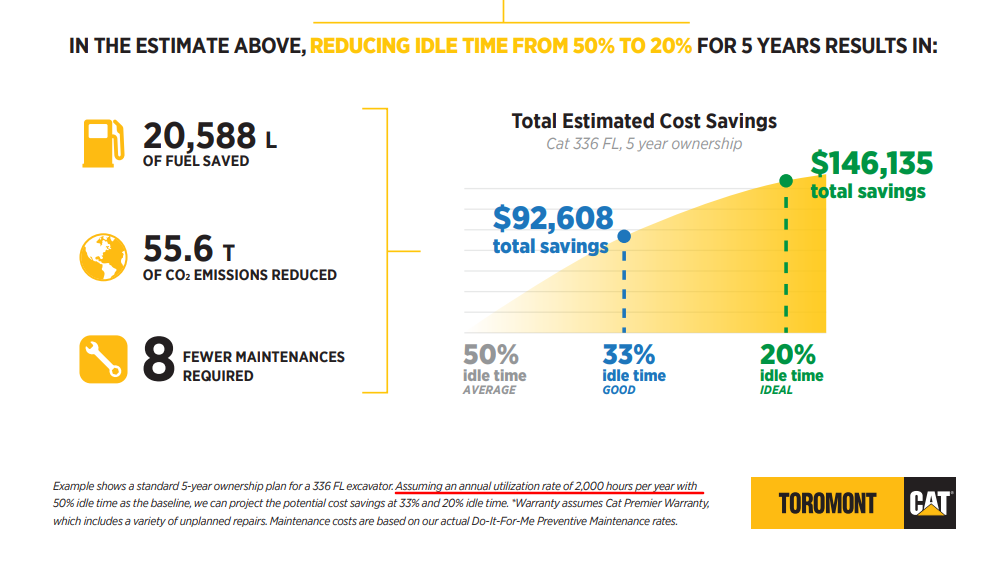
The final figure in the visual above reflects less required maintenance, reduced CO2 emissions, and significant fuel savings.
So, how can you achieve all of this?
It all starts with adopting the right equipment management practices and strategies.
That way, you’re ensuring your equipment:
- is available when needed,
- operates safely, and
- isn’t at risk of failure and costly downtime.
However, even smaller construction businesses find it hard to keep track of all their machinery and small tools, so where do you even start?
Easy: with asset management software.
If your construction projects are suffering because can’t seem to keep an eye on your equipment’s whereabouts and availability, a comprehensive asset management solution is going to be your most trusted ally.
One such example is our very own cloud-based solution, GoCodes Asset Tracking.
With GoCodes Asset Tracking, everyone on-site or in the office can quickly check the availability, location, and status of any asset in the inventory, along with other key information.

On top of that, you can easily access extensive maintenance records and insights from the field using any internet-connected device, but also schedule different service tasks as needed.
Plus, thanks to helpful email reminders, there’s no forgetting them and risking equipment breakdowns.
Finally, a variety of tagging options that GoCodes Asset Tracking offers bolster security on-site and during transport, with real-time GPS trackers available for your most valuable assets.
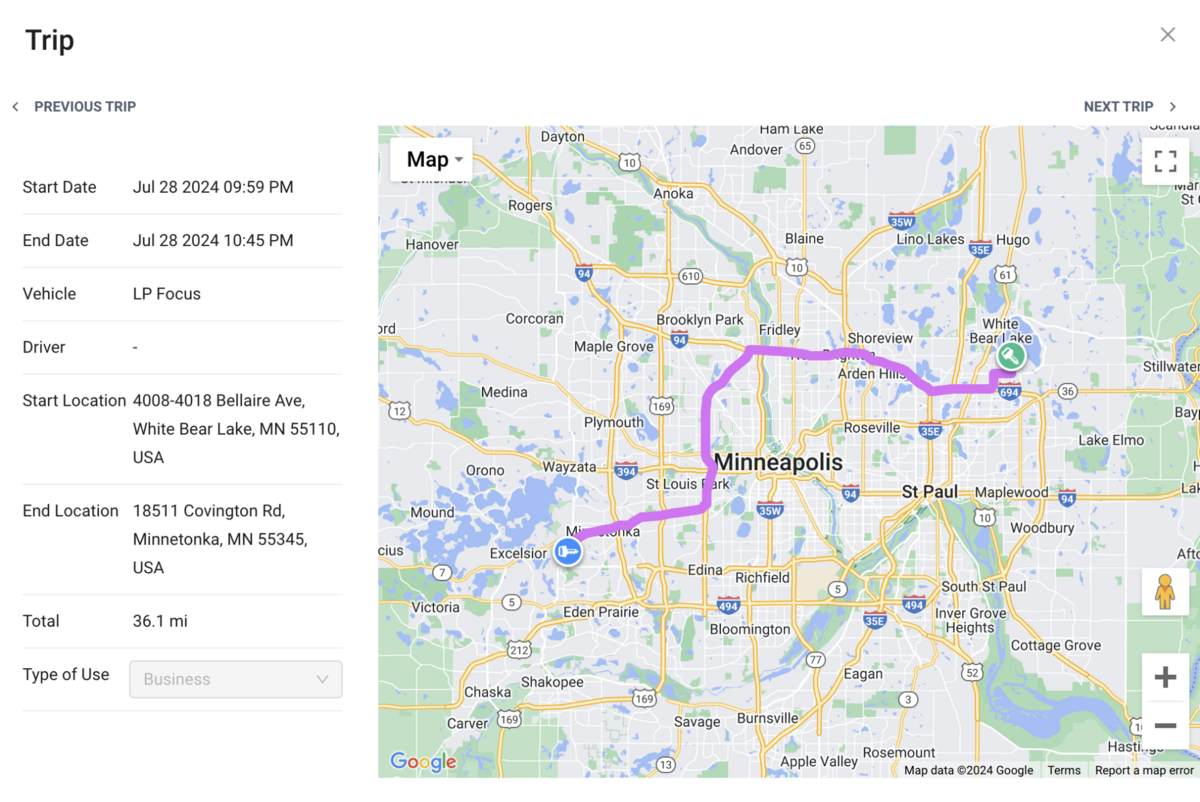
Investing in technology like asset tracking software truly turns equipment management challenges into opportunities.
With a reliable system, you’ll maximize your equipment’s utilization and extend asset lifespan, keeping your projects on track in the process.
Maintaining Consistent Quality of Work
Meeting quality standards consistently is another major construction project management challenge.
Yes, coordinating different subcontractors and multiple crews is tricky in and of itself.
But ensuring the required quality of work across all project phases and areas is often even harder, and the consequences of not doing it successfully can be dire.
For starters, there’s the fact that quality issues significantly contribute to project delays.
Don’t believe us?
Take a look at Finalcad’s research, the findings of which show that 57% of surveyed construction professionals agree with that sentiment.
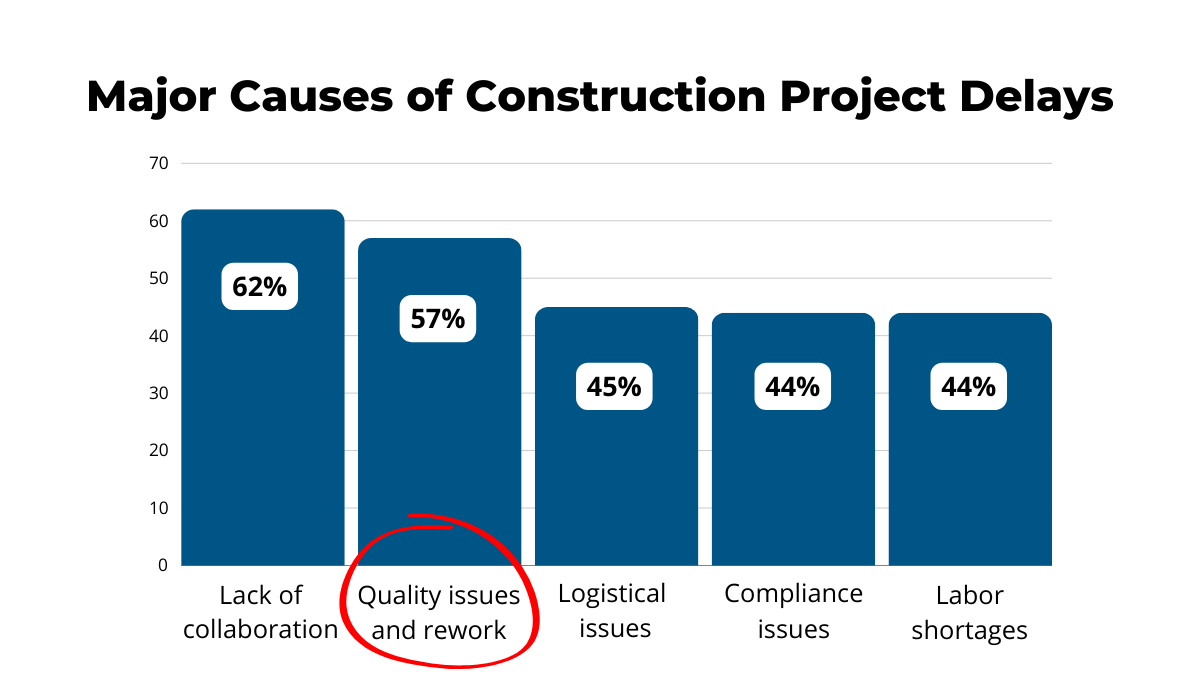
Every construction professional knows what’s at stake here—problems with quality lead to rework, increased costs, project delays, and client dissatisfaction.
There’s also the issue of long-term reputational consequences, which can be even more devastating.
One example is the recent legal entanglement of the home construction company Taylor Morrison and home inspector Cy Porter.
Namely, Porter built up a large online following by sharing videos that pointed out flaws in newly built homes.
Since a couple of these were built by Taylor Morrison, the company decided to file a complaint against Porter for alleged targeting, harassing, and bullying.
Ultimately, the company failed to get disciplinary action, which led to its reputation taking an additional, very public hit.
While Taylor Morrison could have handled things differently, the root cause of their issues with Porter goes back to numerous defects.
Simply put, if the company had assessed its quality control processes and introduced necessary changes, the defects perhaps wouldn’t have been there in the first place.
This begs the question, what can you do to enhance your own quality control practices?
You should consider:
- using a quality assurance checklist,
- creating a site inspection plan,
- setting quality expectations, and
- reviewing inspection results.
Investing in quality control enhances compliance and drives efficiency, all while reducing the likelihood of defects that could ultimately result in consequences as serious as loss of life.
Take the deadly 2017 high-rise fire as an example.
Grenfell Tower Inquiry, which has been looking into the matter, rained fire on contractors and subcontractors due to numerous quality issues that contributed to the tragedy.
The fire strategy plans were among the most glaring examples of quality control failures.
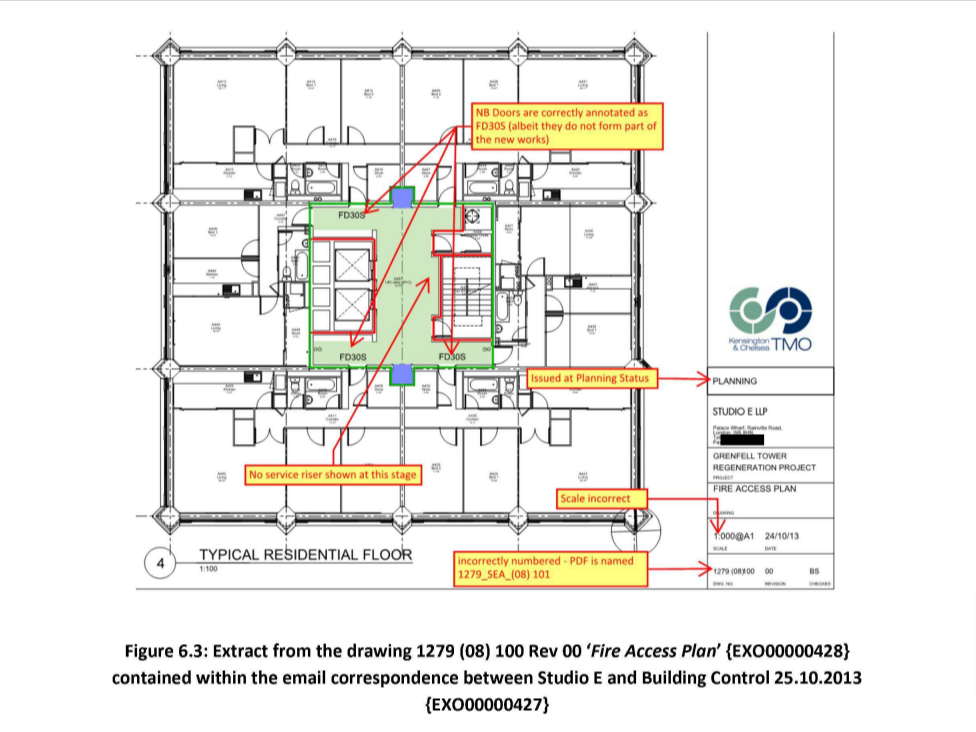
Liam White, a former UK-based site manager, argues that this tragedy highlighted the necessity of stricter regulations and quality control processes, but also a complete shift in contractors’ mindset.
By changing the contractors’ approach to work and priorities, quality-related challenges are sure to become more manageable.
At the same time, sacrificing quality for speed and cost could finally become a thing of the past.
Mitigating Construction Risks
Construction risks pose a constant threat to the success of construction projects.
From construction crime to labor shortages, various construction risk statistics paint the picture of just how easy it is for projects to suffer timeline disruptions and budget drains.
And the lack of proper risk management increases the likelihood of such scenarios, as shown by KPMG’s research.
As you can see below, in 2023, 40% of construction firms reported suffering schedule delays and a cost impact of 20% or more thanks to a lack of effective risk management.
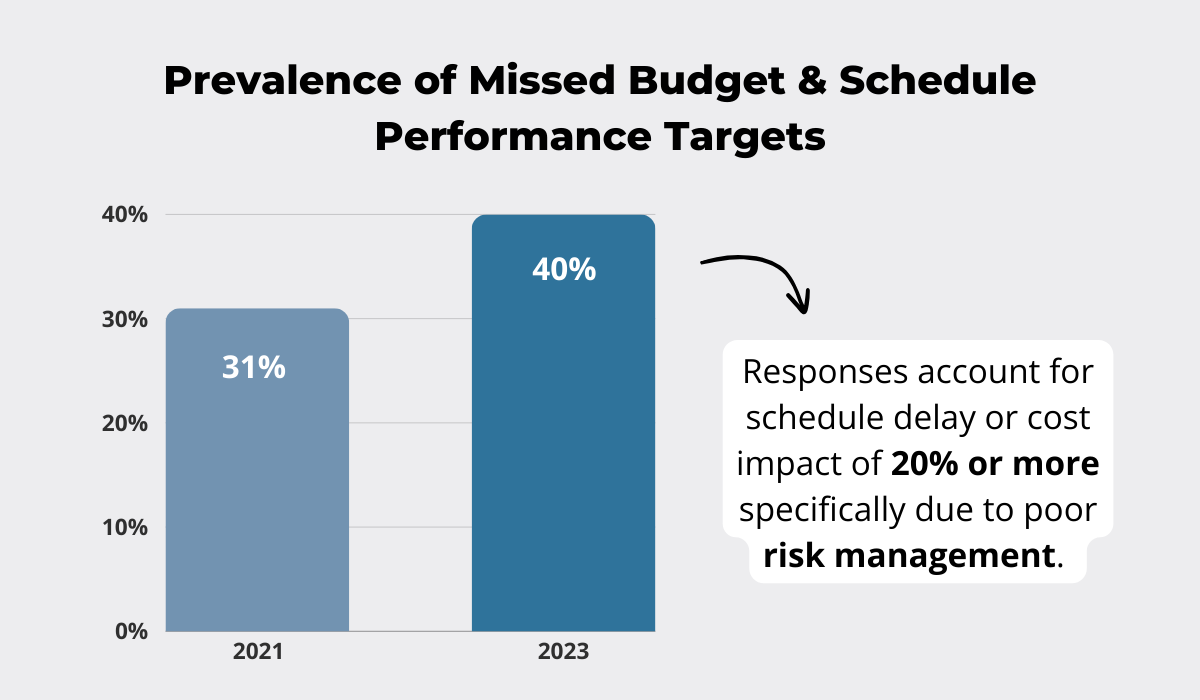
These figures highlight the crucial role of risk management, that much is clear.
But there is another interesting point to address.
In just two years, the number of construction companies that reported significant schedule delays or cost impacts increased by nearly 10%.
This jump underscores the increasing complexity of managing construction projects, in part due to ever-evolving construction risks.
Nowadays, supply chain issues, mounting cybersecurity risks, and an increasing number of catastrophic weather events require proactive risk management.
So, how do you ensure your company’s resilience and flexibility in the face of such challenges?
Start with identifying all construction risks and developing a comprehensive risk management plan.
By identifying, categorizing, and prioritizing potential risks, you’ll be in the best position to employ the right tactics and reap the benefits of effective risk management.
However, even with a solid risk management strategy in place, it can still be very difficult to plan for different construction risk scenarios.
That is where predictive analytics—an example of effective risk mitigation technology—comes in.
With predictive analytics, construction companies can anticipate potential challenges and find the best course of action to stay on track with ongoing projects.
Josh Kanner, an expert in construction safety, explains that the ability to generate hundreds of scenarios is making this technology crucial for enhancing job site safety.
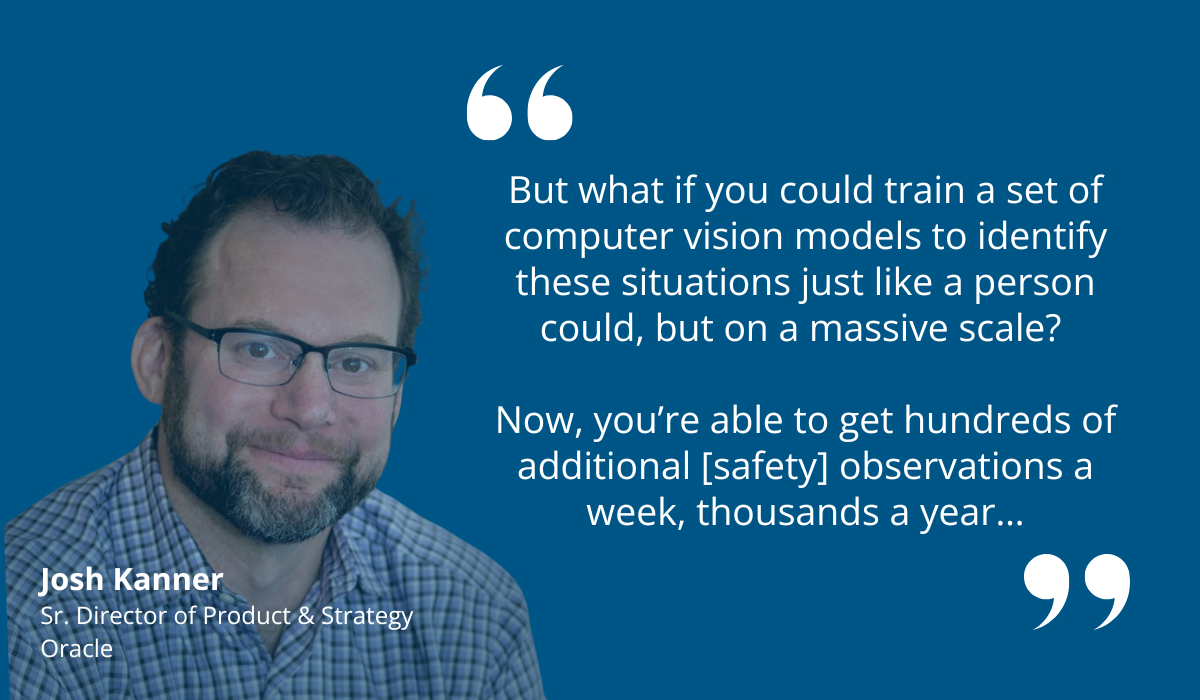
Flagging potential incidents before they happen, and doing so at such a large scale, can help mitigate many of the issues plaguing construction sites worldwide.
One thing is certain: with multiple lines of defense in place, you’ll be in the best position to respond to many of the risks threatening the success of your construction projects.
Dealing with Labor Shortages
The construction industry has been facing labor shortages for a while now.
While construction businesses have found ways to overcome this challenge, the inevitable skill gap and high turnover still pose an active risk to productivity and project timelines.
The latest figures from AGC confirm just how widespread and problematic these issues are, with 62% of respondents claiming that the lack of workers has led them to experience project delays.
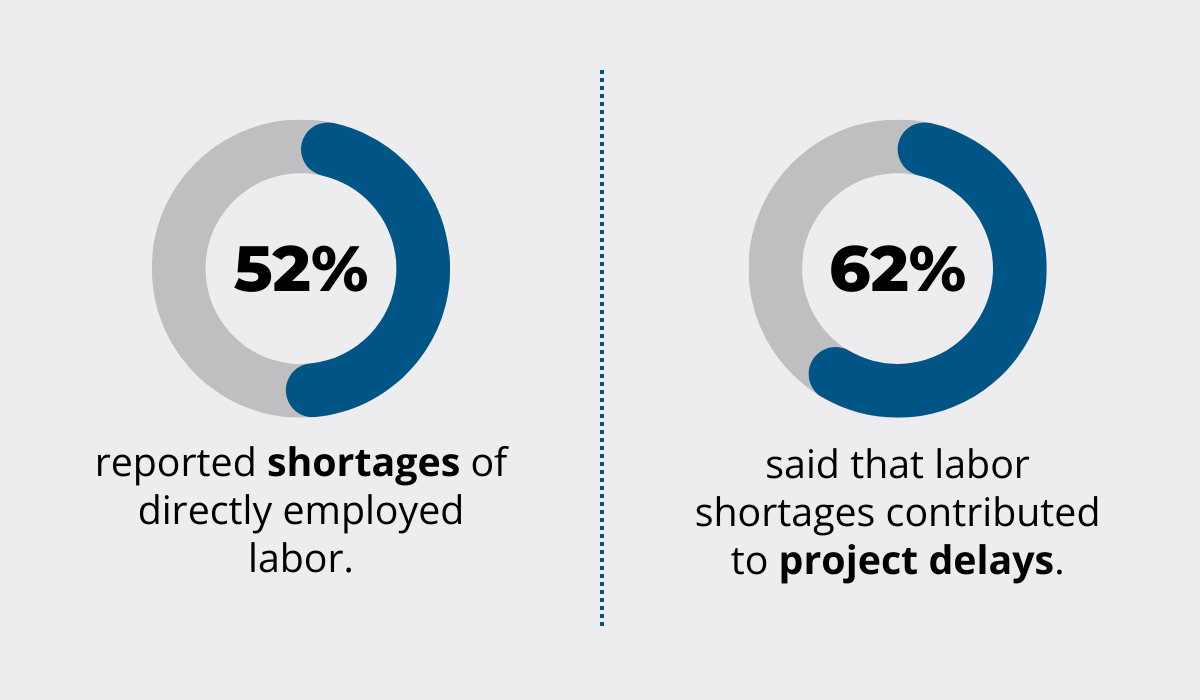
Faced with this reality, many construction companies turned their focus to a still relatively untapped pool of workers— women and minorities.
Filling employment gaps is just one benefit of investing in diversity, but it has definitely contributed to over 1.28 million women working in construction in 2022.
And while these numbers are an improvement, there is still much room for growth.
Turner Construction is one notable example of a company that understands this.
Their 2022-2023 DEI Impact Report showed promising numbers, with women making up nearly 30% of their US staff.
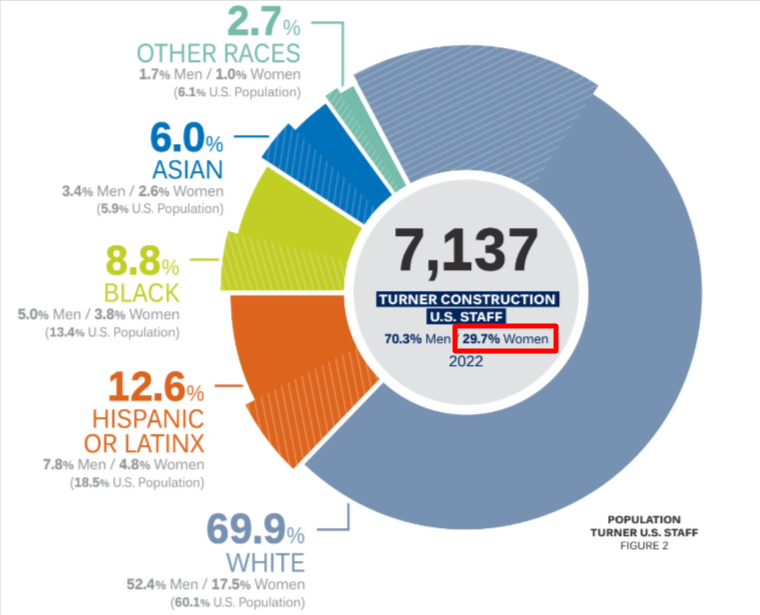
But when we zoom in on trade workers, that percentage drops to 8.8%, which means that the majority of their female workers occupy office roles.
This is why companies like William Charles Construction are introducing scholarship programs as a way of attracting new trade role hires.
The previously mentioned AGC report shows that investing in current or future workforce is gaining momentum, with 41% of companies developing different training programs.
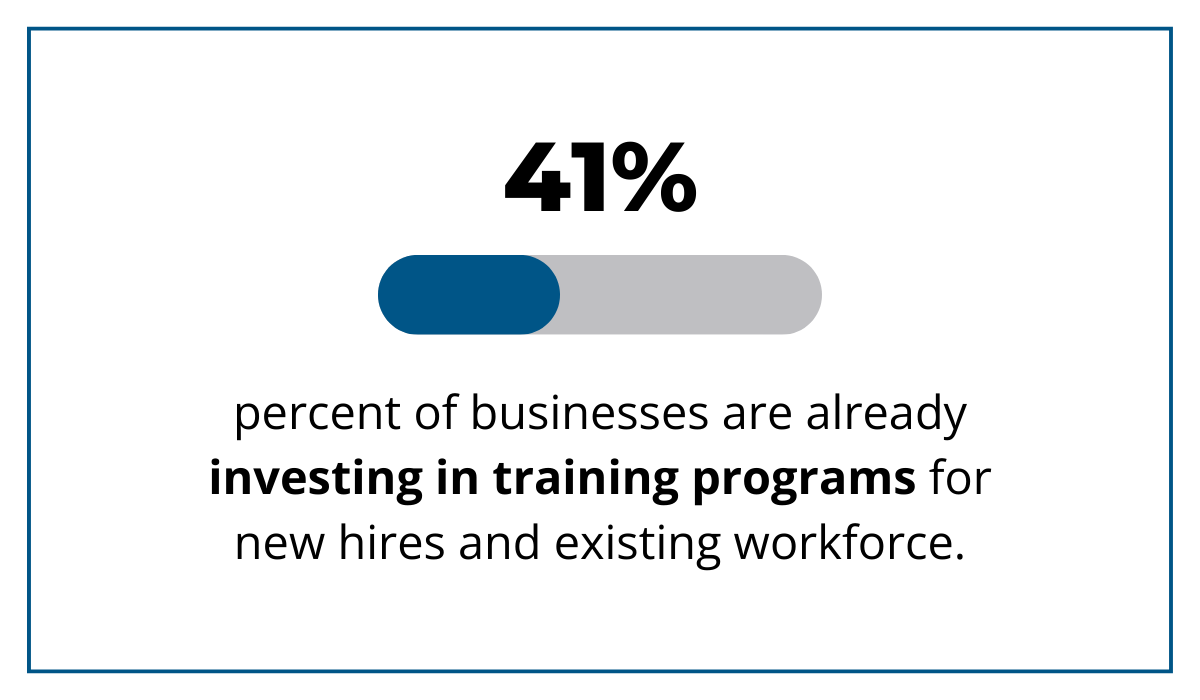
Many of these are geared toward the existing workforce, so you may be wondering why is this proving to be an effective strategy for mitigating labor shortages.
Think about it: optimizing your existing workforce through multi-skilling and cross-training initiatives brings versatility and resilience, helping minimize disruptions to timelines in the process.
Let’s say you’ve invested in cross-training, and now your electricians have picked up basic plumbing skills.
That means they can handle basic plumbing tasks and detect issues on-site without needing to wait for specialized plumbers.
Such flexibility helps you keep projects on schedule while lowering labor costs.
The bottom line is: labor shortages can hinder your operations significantly, but if you rethink your hiring and retention practices, you can mitigate many of the risks!
Preventing Poor Communication
Inadequate communication across teams, contractors, and stakeholders can quickly lead to misunderstandings, missed deadlines, and costly errors—a nightmare for every project manager.
So, why is it necessary to prevent poor jobsite communication?
Well, one clue comes from the Project Management Institute (PMI) research.
As you can see below, there is a stark difference between projects with highly effective communication and those with poor communication.
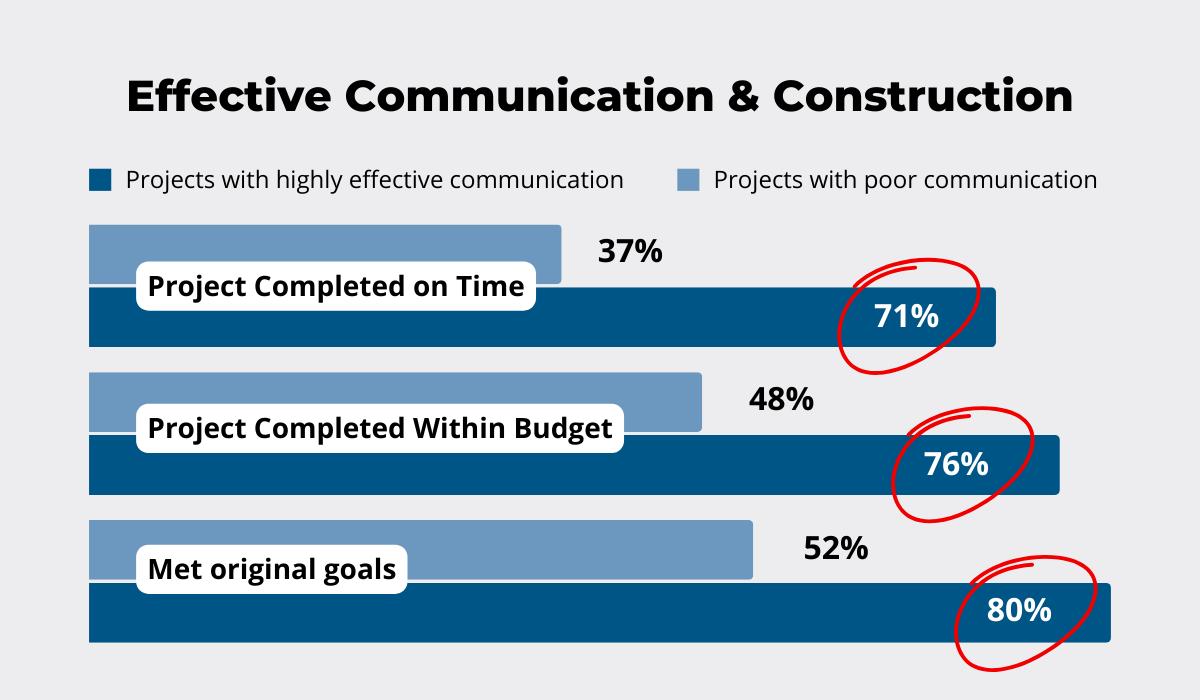
One stunning example of how dangerous even slight miscommunication can be is the 1999 loss of a 125 million-dollar Mars probe.
Teams from NASA and the European Space Agency hadn’t realized they were using different units of measurement, which led to a miscalculation in crucial acceleration data.
In the end, the probe crashed into Mars.
It’s easy to imagine a similar scenario happening on a large-scale international project, resulting in incorrect material orders, incompatible parts, or even structural miscalculations.
Even if someone caught wind of the issue before it caused a major incident, costly delays and rework would still follow.
One way of preventing this horror scenario is by streamlining your communication.
In their reply to a thread on communication problems in construction, a Reddit user emphasized the need for leaving a paper trail covering all communication.

This is a valid point, but construction companies can benefit even more from adopting a central collaboration platform.
Technology boosts construction collaboration in different ways, and cloud-based software tools are ideal for facilitating communication between different project stakeholders.
For instance, comprehensive software like Buildertrend aims to tackle all project needs in one spot, offering solutions for the entire industry—from home builders to specialty and commercial contractors.
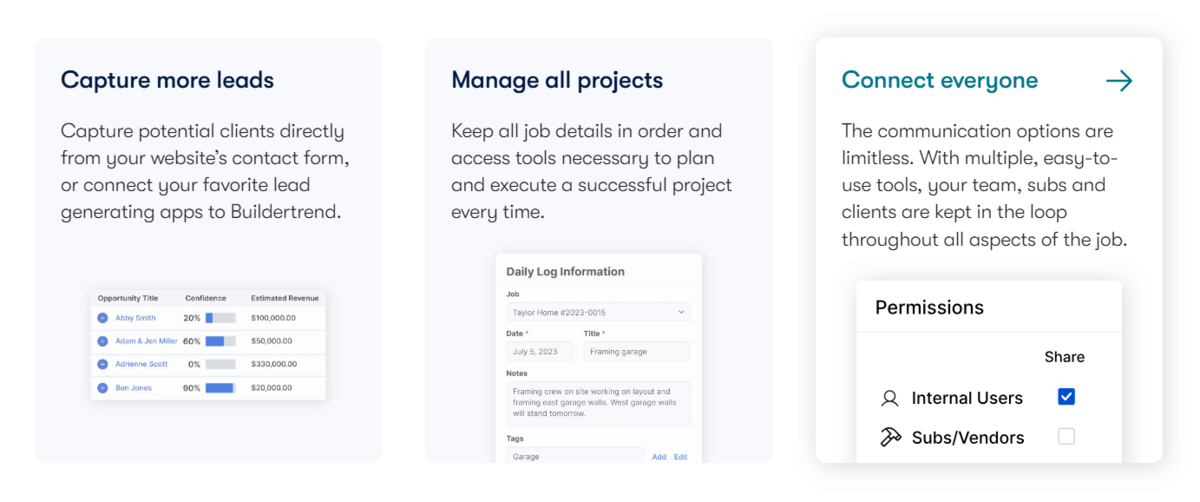
With everyone in the loop and able to access all job details from a single source of truth, Buildertrend, and similar tools are bound to improve your efficiency.
However, not all issues can be solved simply by implementing a communication or collaboration tool.
There are many underlying causes behind communication issues in construction, including fear of speaking out and confusion over roles and responsibilities.
Sue Dyer, an expert on construction collaboration, explains that it’s essential to take the right attitude toward communication issues.
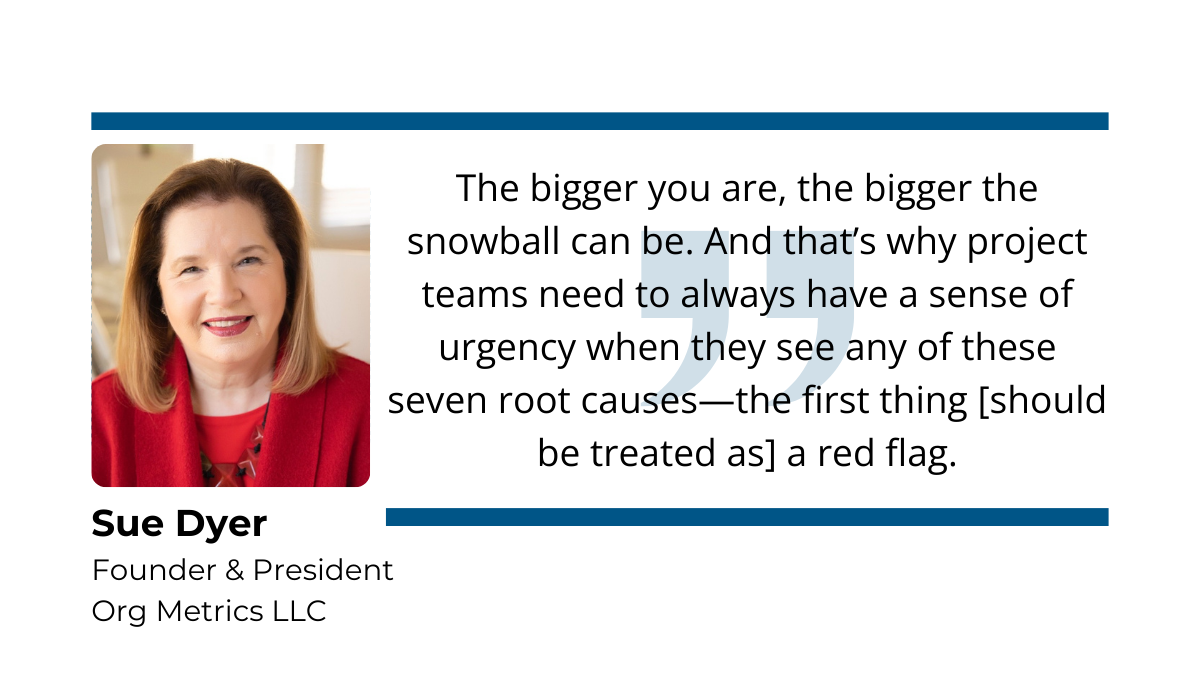
By addressing issues as soon as they arise, you can prevent small communication issues from snowballing into huge problems.
To sum up, the key to overcoming communication challenges and ensuring effective job site communication lies in adopting both the right tools and the right attitude.
Conclusion
Gaining a deeper understanding of the challenges ahead brings you one step closer to overcoming them.
In this deep dive, we focused on the major project management challenges that you’ve surely encountered by now.
While each one is complex, timely planning, proper attitude, and the right tools are all you need to stay on track and pave the road to success.
Feeling ready to tackle these and other construction project management challenges?
With the strategies we explored—and a dose of cautious confidence—you’re bound to come out on top!