In addition to the long-standing issue of worker shortages, contractors now have to deal with the lack of construction materials, supply chain disruptions, and the rising prices of materials and other inputs, such as fuel, equipment, and labor.
This puts the construction industry squarely in the middle of a perfect storm of issues that are causing significant problems for many contractors.
So, we’ll look at what factors are affecting the availability of construction materials right now and what your business can do to deal with a shortage of materials.
In this article...
What Is Affecting Construction Materials Availability
In short, it all started with the pandemic that led to factory closures and initial supply disruptions.
The resulting shortages and increased demand led to higher material and energy prices, which were then, just as they are now, aggravated by further supply chain issues caused by ongoing geopolitical crises.
Thus, in this section, we’ll cover the four major factors affecting the availability of construction materials—factory closures, price inflation, higher energy prices, and supply chain disruptions.
Factory Closures
It could be said that the source of construction materials shortages can be traced back to February 2020, when the first factories in China and Italy were closed due to the onset of the COVID-19 pandemic, causing them to stop the production of items such as kitchen appliances, floor tiles, and elevator parts.
As the pandemic spread, factories around the world were forced to shut down operations, suffering financial losses and creating a massive backlog of orders for specific materials and components, such as computer chips.
For instance, when the U.S. economy was hit in March 2020, new and ongoing construction projects were delayed, orders were canceled, and material suppliers either lost their workers to the virus or decided to shut down as per government instructions.
This resulted in a major dip in the U.S. GDP rate, as shown below.
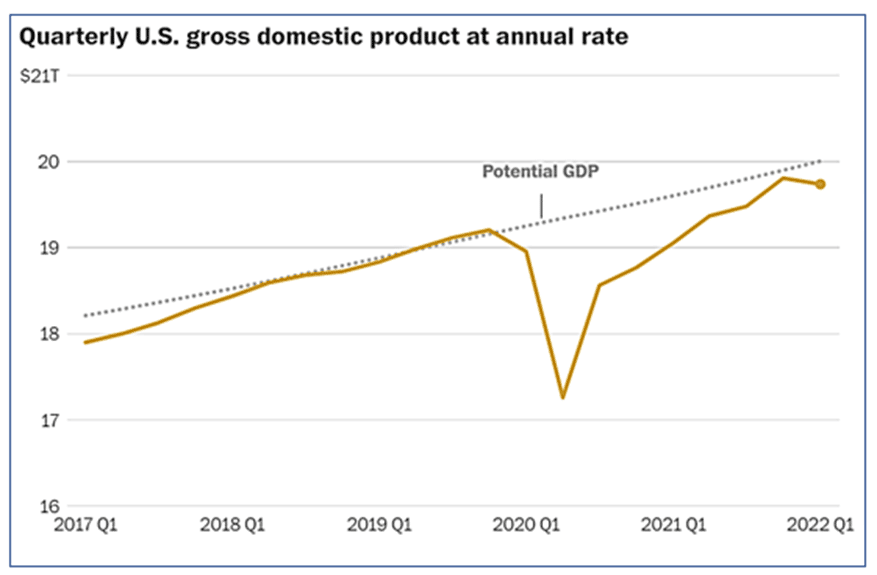
After the first pandemic-induced shocks and lockdowns passed and contractors resumed their ongoing projects or started new ones, the increased demand for construction materials (and other goods) could not be met as most suppliers faced a lack of workers and a growing number of backlog orders.
In addition, climate change has further jeopardized the production of some construction materials by causing severe weather conditions.
One example is the big freeze in Texas that happened in February 2021 and damaged many petrochemical factories that produce resins for various plastic construction products like pipes, insulation, doors, and windows.
Overall, contractors in the U.S. and worldwide are still feeling the consequences of factory closures caused by the pandemic, many of which keep generating shortages of specific construction materials and products.
Price Inflation
When construction materials are in short supply and the demand for them is growing, their prices go up.
When inflation rises at a fast rate, everything associated with supplying construction materials, from fuel and energy to labor and transportation, becomes more expensive, thus jeopardizing the supply of materials even when they’re available.
Based on the U.S. Bureau of Labor Statistics (BLS) data, the Associated General Contractors of America (AGC) calculated that the prices of construction inputs grew nearly 20% in 2021 compared to 2020:
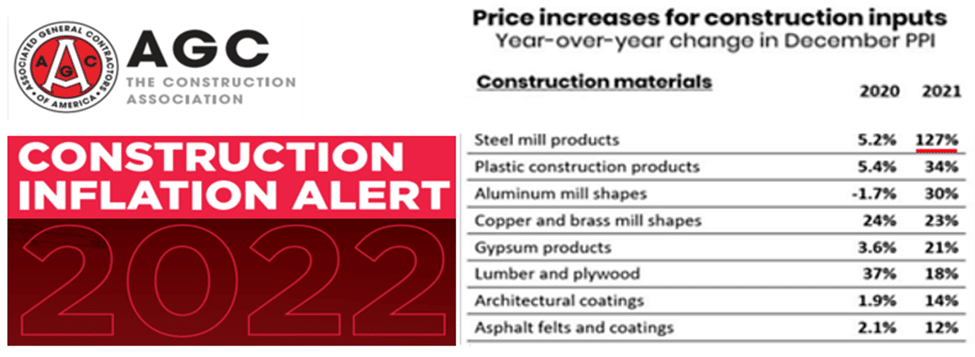
As you can see, the prices of steel mill products jumped by 127% in 2021 compared to 5.2% a year before.
Likewise, the prices of construction plastics and aluminum profiles went up 34% and 30%, respectively.
Consequently, even as the production and supply of construction materials stabilize, contractors are still facing various inflationary pressures that contribute to not purchasing or getting the required materials on time.
Therefore, price inflation caused by lower supply and higher demand can create a vicious circle of higher prices and backlogs that keeps threatening the availability of construction materials.
Higher Energy Prices
As price inflation results in higher energy prices, they are increasingly affecting the availability of construction materials.
Since energy bills are quickly going up (almost 33% higher in July 2022 compared to the same month a year ago), energy-intensive industries that supply the construction sector with materials such as steel, cement, and concrete, have been forwarding the impacts of higher prices to contractors.
This puts more pressure on contractors working on ongoing projects, who are forced to bear the higher costs and decrease their profit margin and on new projects when they’re preparing their bids and defining the project budget and schedule.
Here’s a comparison of the current energy prices with their last year’s counterparts, which posted a forty-year high in June 2022—over 40% compared to June 2021.
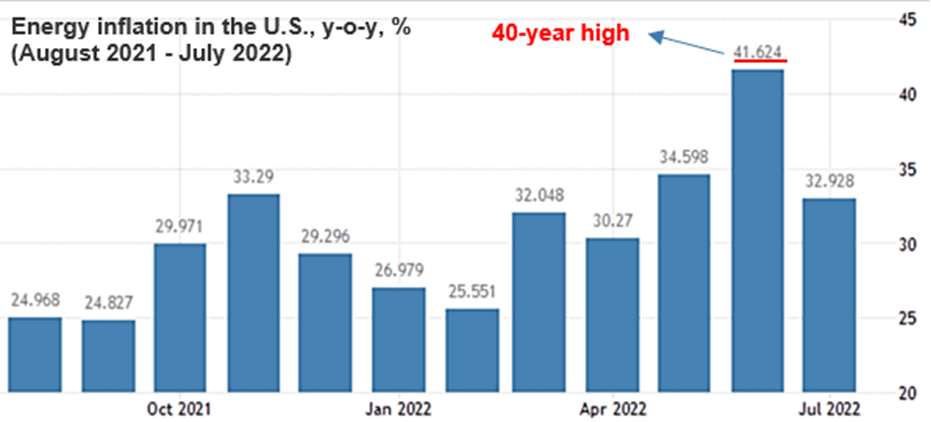
When combined with the fast economic recovery and high demand for construction materials after the pandemic, it’s evident that higher energy costs are affecting the entire global supply chain and causing naturally or artificially created shortages of specific construction materials (or other construction inputs like fuel and transport).
Furthermore, increased energy costs can impact other energy-intensive construction products like plastics, ceramics, and glass.
Thus, rising energy prices, coupled with the recovered demand, place additional pressures on both suppliers and contractors and can cause or aggravate shortages of construction materials.
Supply Chain Disruptions
Finally, while the global economy was trying to recover from the pandemic, factory closures, and higher prices of all commodities, new geopolitical crises have further disrupted the supply chains and exacerbated the already existing supply issues.
Of course, the biggest current crisis is the war in Ukraine that started in February 2022.
For instance, Russia is among the leading producers of aluminum and copper, whose prices went up 33% and 25%, respectively, even before Russia invaded Ukraine.
In other words, the already hiked-up prices of these metals, including materials and products made from them, went even higher after the war started, causing further delays in ongoing and planned projects.
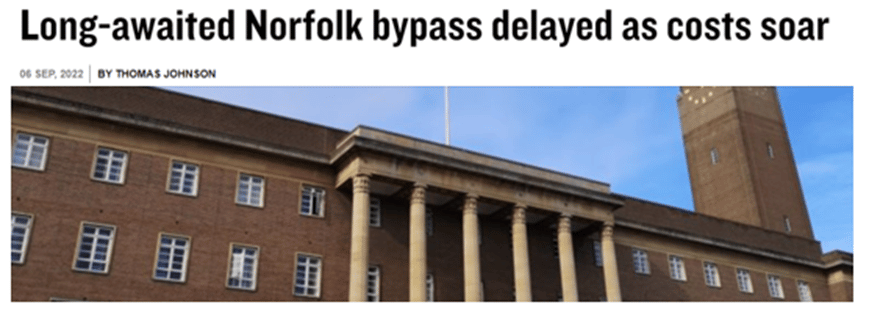
Furthermore, supply issues are also triggered or aggravated by the rising natural gas and oil prices brought on by geopolitical “war games.”
Ken Simonson, AGC’s chief economist, says:
“The conflict is likely to drive fuel, copper, and aluminum prices higher, while cargo ships in the area have been halted or delayed.”
When this is combined with ongoing lockdowns in China due to its zero-Covid policy and the huge backlog in the production of microchips and semiconductors, it’s clear why supply chain disruptions continue to cause price hikes and longer lead times for various construction materials and products.
How to Deal with Construction Materials Shortages
Now that we’ve covered the reasons behind materials shortages, let’s give a few practical tips on how your construction business can deal with them.
The best approach is to stay informed, continually assess your business in light of the latest fluctuations in the availability and price of construction materials (and other inputs), and plan ahead as much as possible.
Pre-order the Materials
As most suppliers are still experiencing issues concerning the timely delivery of certain construction materials in the required quantities, this might be a good time to assess your current and future needs and, when possible, pre-order the materials ahead of time.
In other words. faced with persisting supply disruptions and rising prices, contractors should evaluate their ongoing and future projects and make sure they have a reasonable stockpile of regularly used construction materials, such as concrete, drywall, and framing materials.
To do so, you can utilize different construction management software solutions.
For instance, you could use an inventory tracking system to track the quantities of materials your business has in stock and receive low quantity alerts when restocking is required, thus ensuring you don’t run out of at least those most often used construction materials.
One such cloud-based asset and inventory tracking solution is GoCodes Asset Tracking.

This easy-to-use and affordable solution can give you a clear picture of your inventory and alert you when material stocks are down, thus giving you enough time to pre-order the materials and avoid shortages and delays.
Of course, it’s preferable when the required materials are procured when prices are down, whether because of market price fluctuations or discount opportunities.
For instance, suppliers might offer hefty discounts on materials they overstocked and now need to make room in their warehouses.
Thus, planning ahead as much as you can, monitoring your inventory levels, and pre-ordering supplies can help you keep your projects on schedule and within budget.
Be Honest With Your Clients
Of course, whether your construction business is experiencing difficulties in procuring the materials needed for ongoing or future projects, it’s advisable to openly communicate with your clients about the shortage of construction materials.
This can help you find alternative solutions, manage their expectations about the project deadline, and ultimately improve your business relationship with them.
For instance, if you run into problems when sourcing the required materials for an ongoing project, honest communication with the project owner can help you avoid a myriad of potential issues that can arise depending on the construction contract you agreed on.
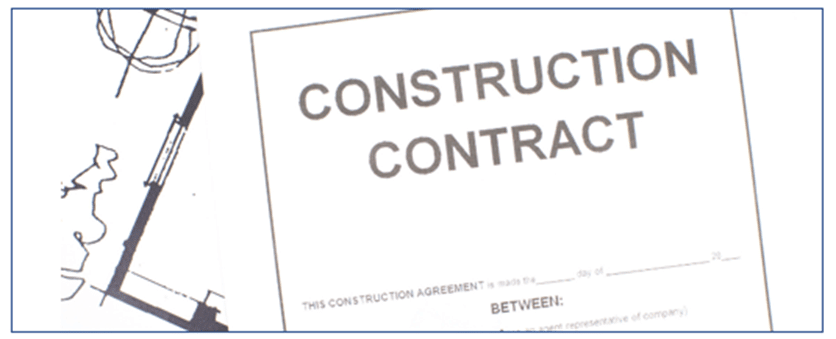
Although there are instances where contractors will have to bear the costs of higher materials prices or delays caused by shortages, most contracts contain force majeure and other provisions that, among other things, regulate what should be done in case of materials shortage.
Likewise, when contracting new projects, you can ensure that the contract lists alternative construction materials to be used if the first-choice ones are unavailable or their price would jeopardize the agreed project budget.
The same applies to any delays caused by external supply chain disruptions, where the contract should clearly define who will cover the costs of such delays.
Overall, openly communicating with your clients about the shortage of construction materials can help you find alternative solutions, avoid delays, conflicts, and even contract penalties, and ultimately improve your business relationship with them.
Map Out the Purchasing Process
As the purchasing process in construction encompasses obtaining all materials, tools, equipment, services, and any other items needed to complete a project, having an organized purchasing path can, among other things, help minimize the risks associated with shortages.
In other words, contractors should map out their entire procurement process, determine who is involved in it and how long each stage takes, as this can help prevent construction material purchase and delivery delays.
Moreover, this will allow them to quickly evaluate the timeline and see what parts of the process could be improved.
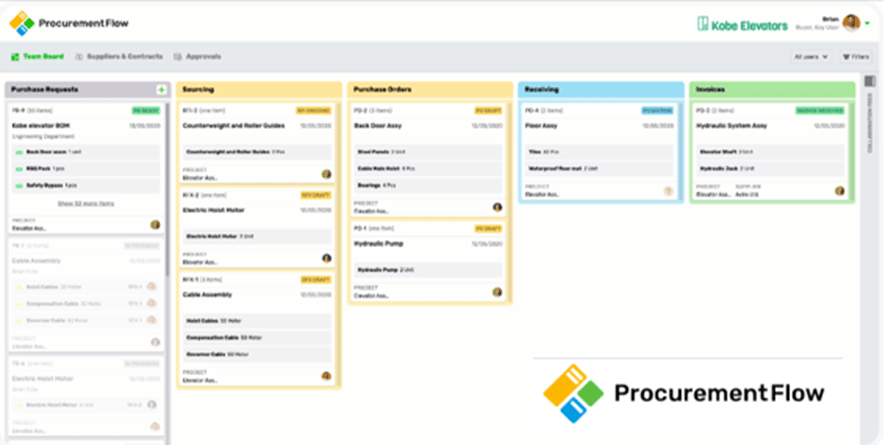
For instance, if a particular material is not available for delivery when planned, a clear view of all procurement processes, roles, and functions can allow you to address that issue by purchasing the material from another supplier in your database or adjusting other procurement aspects, such as transportation and storage.
Mapping out the purchasing process should focus on identifying areas where efficiency can be improved and associated risks, including shortages and/or high prices of construction materials, minimized.
Ultimately, when you can track and analyze the entire procurement process, that can help you prevent late purchases and deliveries of construction materials or find optimal alternatives to ensure your business has all the materials needed to stay within the project budget and schedule.
Conclusion
As said in the opener, the construction industry faces a perfect storm of supply chain disruptions induced by the pandemic, other geopolitical crises, and rising prices of all commodities, including energy.
Thus, it’s clear that construction businesses should focus their efforts on good planning, maintaining strong relationships with their suppliers and clients, staying informed, and seizing opportunities to ensure their projects are not affected by shortages now or in the future.