Tool management software provides many benefits for construction companies—some more, some less obvious, but all equally important for increasing a company’s profitability and productivity.
If you’re looking into getting this type of software, or even if you’re already using it, but are weighing your options, keep on reading.
In this article, we’ll explore in what ways exactly tool management software can help propel your business forward.
In this article...
Accurate Tool Inventory
The first step in efficient tool inventory control is knowing exactly how many tools you have.
Seems obvious enough.
However, duplicate and ghost assets are real issues in the construction industry.
Both are the result of improper tool inventory management and have serious consequences for many aspects of your operations.
Let’s take a look at some of them.
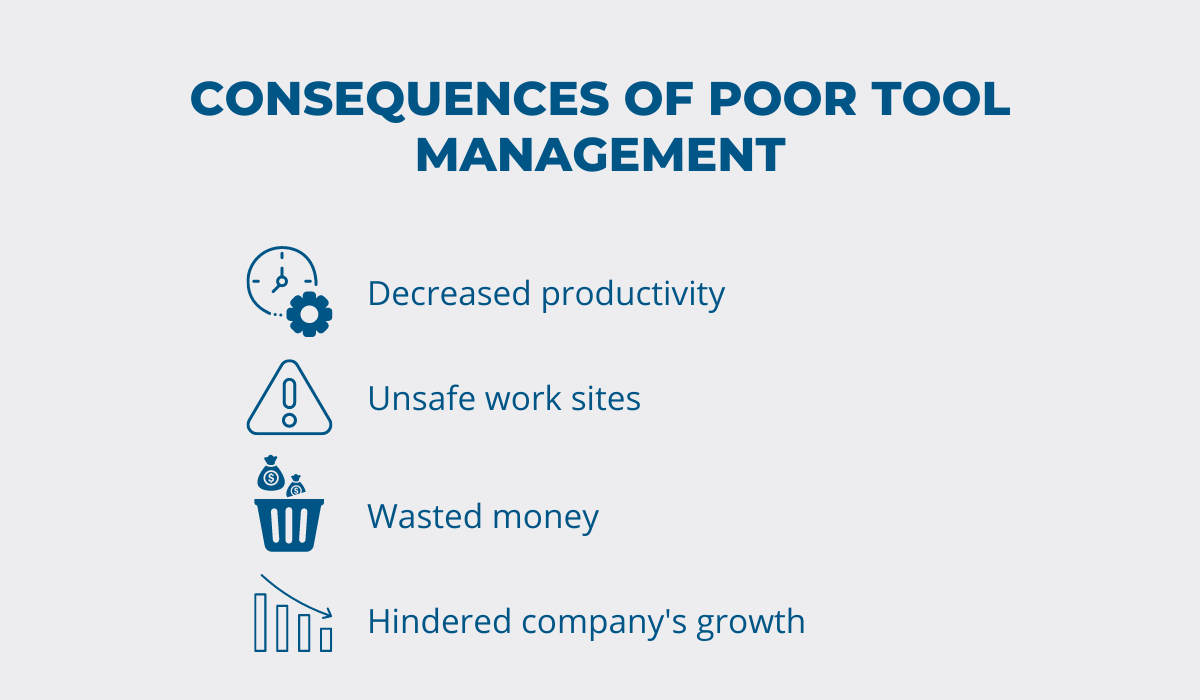
Essentially, having accurate data about your tool inventory saves you money and time, increases your productivity, and generally makes the job sites safer.
Using tool management software is the best way to get the most accurate and up-to-date data about your tools.
Our own solution—GoCodes Asset Tracking—serves as a centralized database for all that information, and it’s incredibly easy to use.

Just attach our customized QR code labels to your tools and then scan them with our scanner app to view or update tool information on the go!
All in all, while managing your inventory seems simple, it’s easy to get bogged down in it, especially if you have a lot of assets and you’re doing it all manually.
Soon enough, you end up with too many—or too few—tools, which are both equally harmful for your productivity and profitability.
On the other hand, tool management software lets you know exactly where you stand when it comes to your assets.
Complete Tool Visibility
Knowing where you stand with your inventory, however, is just the starting point.
Having insight into how your tools are allocated across different job sites is another thing that significantly impacts your operational efficiency.
You already know it’s not uncommon for workers to, for example, forget to return the tools at the end of their work day.
Incidents like that can add up and have far-reaching impact.
For instance, if a worker from job site A forgets to return a tool at the end of the day, the worker from job site B the next day has to take the time to look for that tool, only to discover that the tool is still at the job site A.
When situations like that accumulate, they begin to negatively affect your productivity and cause project delays.
In fact, mismanagement of assets is one of the main causes of failing to deliver projects on time.
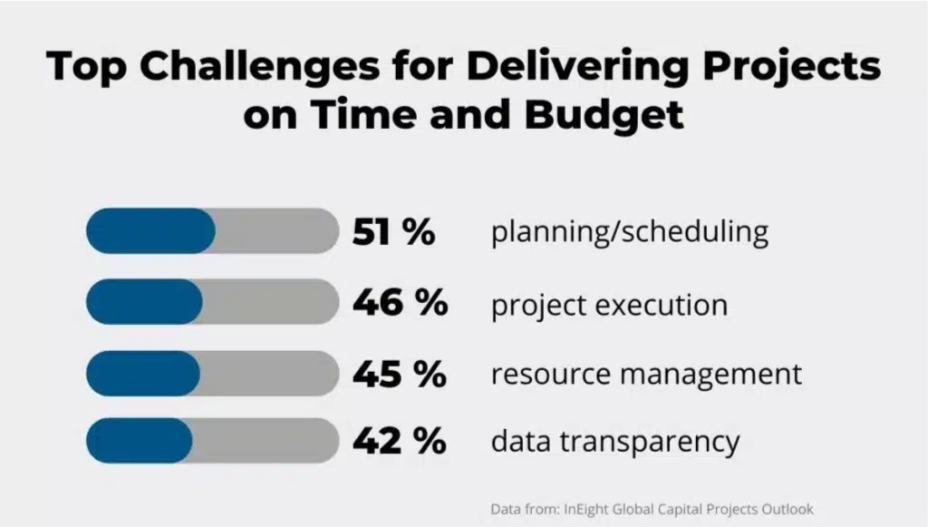
Tool management software enables you to allocate your tools more effectively as it gives you and your whole team insight into which tools are currently available for use, which employees are currently using which tools, and whether those tools have been returned at the end of the day.

All of that decreases the chances of miscommunication and enables workers to better coordinate their work across different locations.
In other words, having complete tool visibility is a powerful thing as it enables you to make better-informed decisions about tool utilization.
Increased Employee Accountability
Tool visibility goes hand in hand with employee accountability.
As a result of tools not being returned when and where they should have been, tool loss or misplacement is a common occurrence in the construction industry, but the cost of these incidents reaches far beyond simply paying for the lost tool’s replacement.
According to various construction equipment maintenance experts, unplanned downtime rates in the range of 20-30% are quite common.
And although tool loss is not the only cause of unplanned downtime, it certainly contributes to it.
After all, when workers can’t find the tools and equipment that they need for a certain task, they can’t complete it on time, which can lead to delays in the project as a whole.
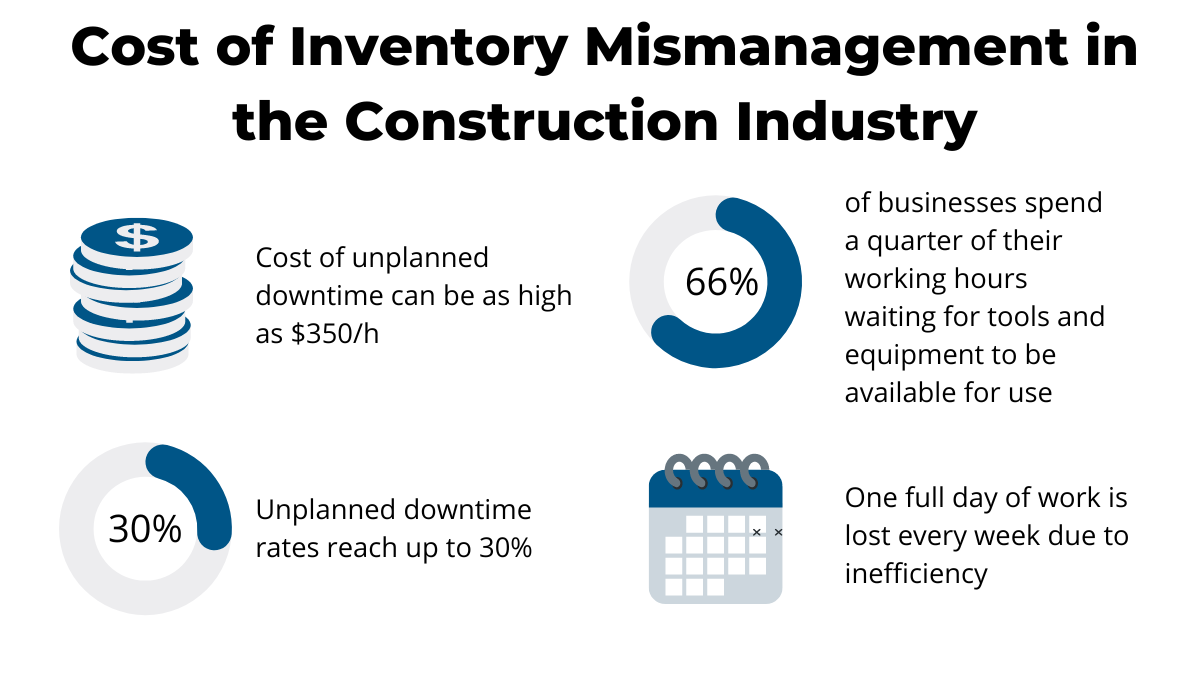
In fact, research shows that construction companies lose more than one full day of work due to inefficiency.
The causes of inefficiencies are many, but the lack of accountability on the employee’s part is certainly one of them.
Moreover, unplanned downtime is far from insignificant in terms of costs. Although the exact cost is hard to pinpoint, experts estimate it can reach up to $350 an hour.
Tool management software instills good habits and makes sure employees take adequate care of the tools they’re responsible for with its easy-to-use check-in and check-out feature.

The feature requires workers to scan and update tool information when they start using the tool as well as when they’re finished using it.
In conclusion, construction work is full of threats to productivity, and lack of employee accountability is one of them.
Tool management software helps remove that threat by creating awareness of who’s using each tool and, in turn, prevents tool misplacement.
Lower Risk of Tool Theft
An even more severe problem, however, than tool misplacement is tool theft. And it’s quite a common one at that.
For instance, in 2022, a lone thief was able to steal more than $43.500 worth of materials and tools in Concord Township, and the year before, 250 instances of construction site theft worth over one million dollars were reported in The Pikes Peak region of Colorado.
These examples don’t even begin to scratch the surface of the prevalence of construction site theft, but they do start to paint the picture of how costly these thefts can be.
You may think to yourself that this won’t happen to you, but the numbers say otherwise.
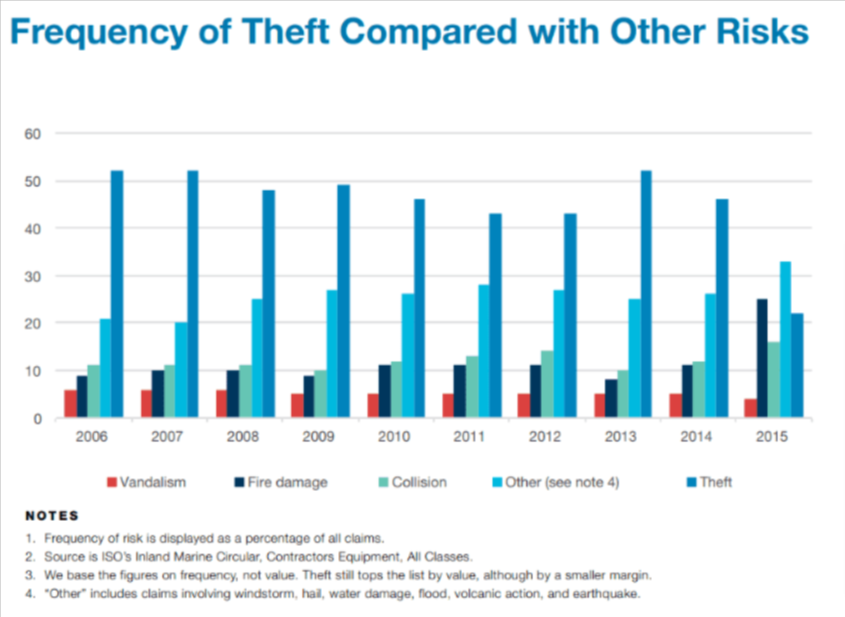
In fact, in construction, there’s a bigger chance of you being the victim of theft than of fire or water damage, vandalism, earthquake, and many other calamities.
Tool management software, luckily, helps mitigate theft in two ways.
Firstly, it deters potential thieves from committing the crime because, when they see a construction company label on a tool, they immediately conclude the item is being tracked.

That way, the problem is nipped in the bud.
On the other hand, if the theft does occur, you’re more likely to recover that stolen tool with tool management software because it records and tracks the tool’s GPS location.
To sum up, construction theft can cost your company a lot of money and time. With the right tool management software, you can prevent, or at least mitigate this issue.
Easier Tool Maintenance
Protecting your tools from loss and theft is not enough, though. You also need to maintain them.
Not taking care of your tools shortens their lifespan, which is no good, seeing that they are a big investment and indispensable when it comes to project completion.
Not to mention that the sudden breakage of tools is yet another cause of unplanned downtime.
The problem lies in the fact that a lot of tool maintenance tends to be reactive, instead of preventive, meaning tools are fixed only when already broken.
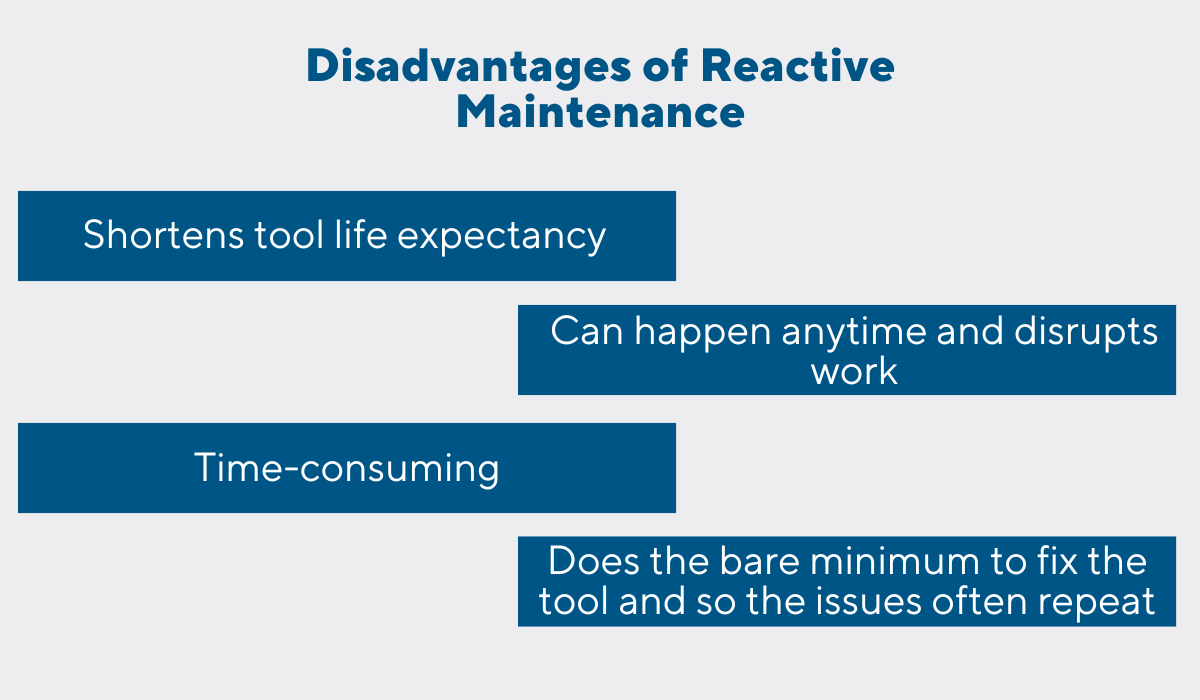
This comes as no surprise because, naturally, everyone at a job site is focused on the task at hand so they pay no attention to tools until they stop working.
It doesn’t have to be that way, though, because tool management software lets you schedule and assign tool inspection and maintenance tasks to your employees.

This way, you can arrange maintenance around planned work so it doesn’t interfere with ongoing projects.
Moreover, tool management software sends you notifications for scheduled maintenance, making it so you never miss tool service again.
To conclude, don’t wait until your equipment breaks down, but prevent any serious malfunctions that’ll put a dent in your project completion time by using tool management software to strategically plan tool maintenance.
Working smarter and not harder is the key to success.
Informed Decision-Making
A big part of working smarter is basing all your short-term and long-term planning on informed, data-driven decision-making.
But not all data is good data. In fact, there is such a thing called bad data and it refers to inaccurate, incomplete, or untimely data. And bad data makes for bad decisions.
If you’ve ever ordered too many or too few tools or incorrectly calculated the project delivery date based on the information you had in front of you, you already know what we’re talking about.
In fact, bad data cost contractors 1.8 trillion dollars in 2020, according to the Construction Financial Management Association.
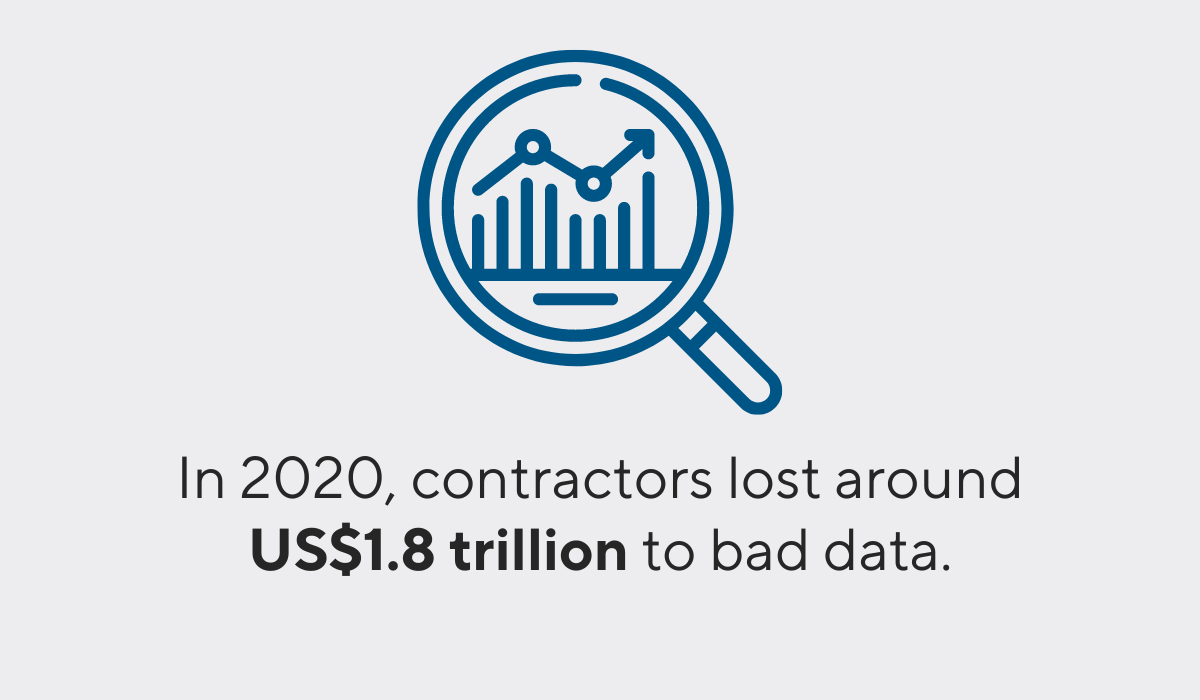
But where does bad data come from? From all sorts of places, it turns out, and that’s what makes it bad in the first place.
Relying on paper forms, spreadsheets, emails, meetings, phone calls, and text messages to transfer information between job sites and offices is extremely time-consuming and subject to mistakes, which creates inconsistent and hard-to-track data.
In other words, having your data scattered all over the place is no good if your goal is to make better-informed decisions about your operations.
Luckily, tool management software provides a centralized database where all your data is securely stored and accessible to everyone on your team in real time.
Not only that, but the software enables you to create different custom reports and charts and then share them with the team via an email or URL link.

This way, you get an insight into, for example, how often certain tools are used, i.e., whether they’re over or underutilized, which enables you to allocate them more effectively.
In conclusion, without tool management software, collecting and tracking data tends to be quite time-consuming and resource-intensive.
Therefore, consider using the software to get data that is actually usable and helps you make better decisions.
Simplified Auditing Process
Another item on the list of things that can be time-consuming and resource-intensive is the auditing process.
It requires detailed inspections that ensure no issue flies under the radar.
Although often tedious, it is necessary to perform audits to ensure everything is operating at its full potential and that your tool inventory is accurate and up-to-date.
With tool management software, the whole process is much more simplified because, by tagging your tools with QR code labels and updating the information on those tools, you create an up-to-date report on that asset, including its acquisition and disposal dates.
The software also provides an audit mode feature, which further helps with updating information on your assets. Take a look at how this feature works with GoCodes Asset Tracking.
Performing audits with the software provides accurate information about what exactly you have and don’t have, as well as the condition of your assets, which means you can now be accurately taxed and insured while your accounting team can track fixed asset depreciation for tax returns and financial statements.
All in all, there’s no denying that audits are a necessary part of owning a construction company. Why not then turn to technology-based solutions to make the process as easy as possible?
Improved Regulatory Compliance
Moreover, auditing is crucial when it comes to regulatory compliance.
Maintaining regulatory compliance, i.e., following certain state and industry standards is yet another crucial part of having successful construction businesses.
What is more, not complying with these regulations is a high-risk practice since it may result in fines, penalties, or business closure.
But how can you be 100% sure you’re doing everything by the books? The standards are ever-changing and there are so many rules and laws regulating every aspect of your operations.
Not to mention that the construction industry is one of the most regulated industries out there.
Negligence is what often causes companies to fail to comply with the standards, but poor documentation and asset tracking are the key challenges that make compliance so difficult.
In fact, in a survey by Autodesk, respondents claimed that they spend up to 35% of working hours on non-project-related tasks, i.e., wasting time looking for missing documentation, correcting mistakes, tracking tools, and so on.
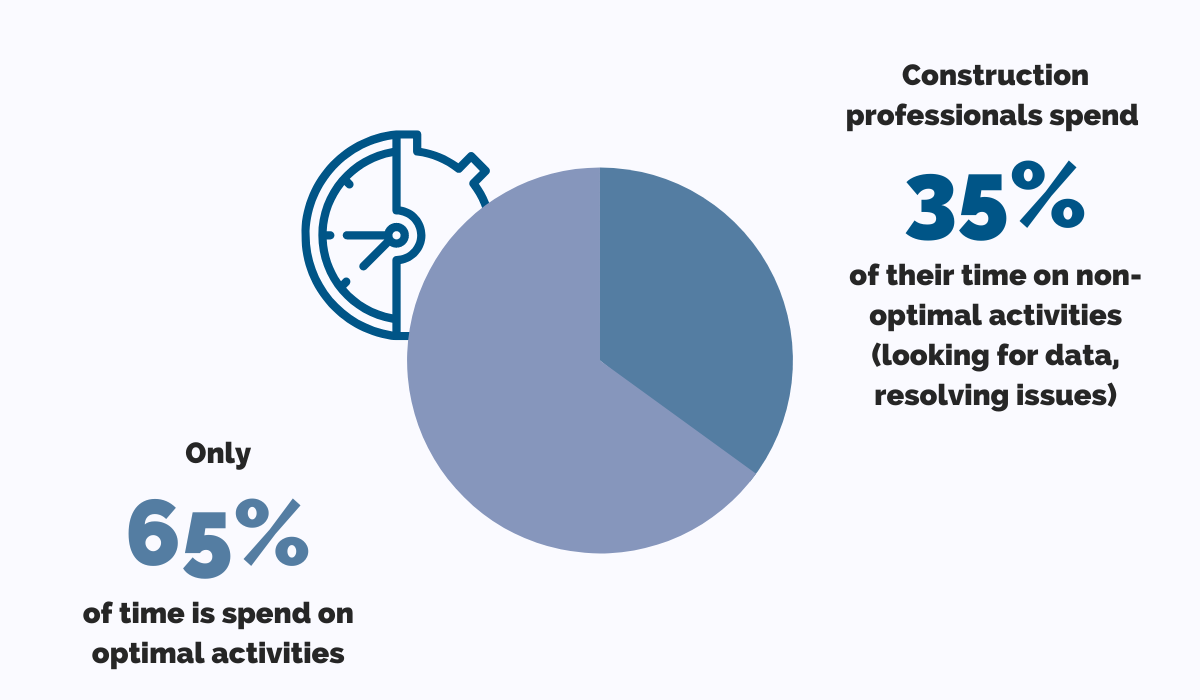
This issue is easily solvable by a centralized database that is a part of tool management solutions.
But not only does the software help with tool tracking, maintenance, and audits—it also includes all the information about your assets’ calibration and testing, which are needed to prove your compliance with all the regulations and laws.
In other words, tool management software equips you with all the necessary documentation, so you’re always ready for an inspection.
And it stores it all in one place, making it easily accessible.
Conclusion
To sum up, the benefits of using tool management software are countless, but they all contribute to one thing, and that’s boosting the success of your business.
From providing you with accurate data about your tools’ quantities, location, and condition to protecting them from loss and theft, tool management software will help you with maintaining industry standards and making better-informed decisions so you can take your company to entirely new heights.