If you’re in construction, you know that keeping track of consumable inventory (building materials, supplies, spare parts, etc.) is as crucial for smooth project completion as monitoring the location, status, and usage of more durable assets like tools and equipment.
However, doing so effectively in fast-paced environments like construction sites presents various inventory control challenges.
Conversely, an efficient inventory control system will enable your company to minimize inventory costs, eliminate inefficiencies, and maximize profitability.
In this article, we’ll explore seven common challenges construction companies need to overcome and suggest ways to do that.
In this article...
Inefficient Inventory Control Processes
We could say that the first inventory control challenge we cover—inefficient processes due to the lack of automation—is the most common one among construction companies.
Why? Because companies typically start small and, as they grow, keep expanding their initial management systems, thus also scaling the inefficiencies ingrained in them.
In other words, when contractors start out, they’re usually more concerned with growing their business than establishing efficient inventory control processes.
However, using pen and paper, spreadsheets, or outdated software to track construction inventory will sooner or later hurt that contractor’s productivity and bottom line.
For instance, here are just some reasons not to use Excel for inventory control:
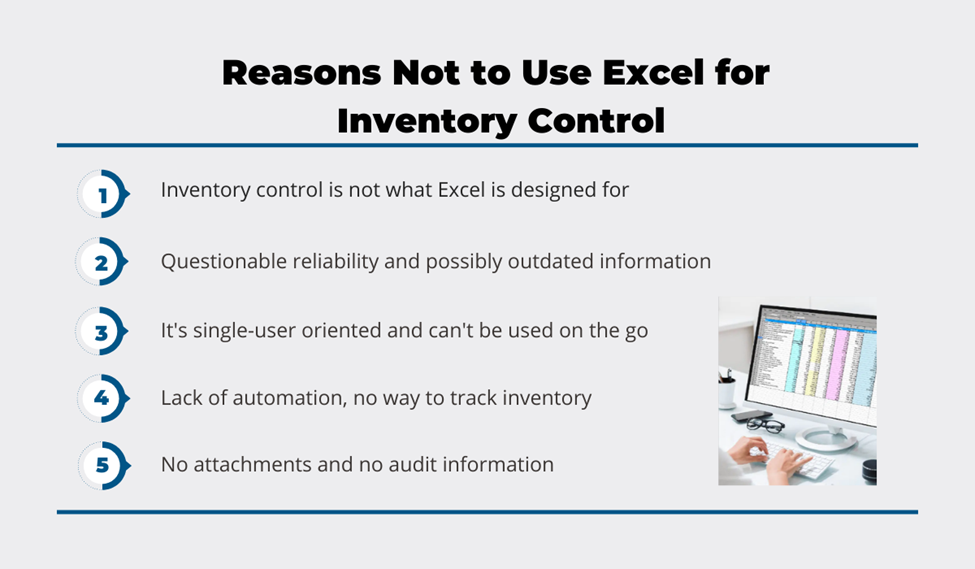
All these downsides can also apply to paper-based methods or switching between different types of inefficient legacy software.
Simply put, these outdated inventory tracking methods heavily rely on manual data entry processes and are, therefore, too time-consuming, resource-intensive, and error-prone.
Conversely, an automated inventory control system can provide the automation and ease of use required to make these processes much easier for your staff to do and for your company to track.
For example, if a jobsite runs out of a specific material (cement, lumber, etc.) for any reason, the site manager can access the inventory management app on their smartphone and instantly check the current stock levels of that material in storage or at other jobsites.
If the material is available, the manager can arrange transport to the jobsite through the app.
If not, they can use the app to generate a purchase request and immediately notify the procurement team.
This is just one of many examples of how transitioning to an automated inventory control system enables companies to make their operations more efficient by centralizing inventory data and allowing for real-time tracking of inventory levels.
As we’ll see, this automation—and the resulting boost in efficiency—can help you address all the other inventory control challenges described here.
Incorrect and Outdated Inventory Data
Another challenge facing construction companies is incorrect and outdated inventory data, which can lead to stockouts and overstocking, increase inventory costs and cause project delays.
First, let’s point out that the root cause of inaccurate data is human error, often aggravated by extensive manual data entry.
As mentioned above, keeping inventory on paper and spreadsheets doesn’t actually enable you to physically track inventory items like construction materials, supplies, and spare parts.
Instead, all these items (and construction assets like tools and equipment) should have a barcode or a QR code label attached to them, allowing them to be tracked in real time and minimizing the need for manual data entry.
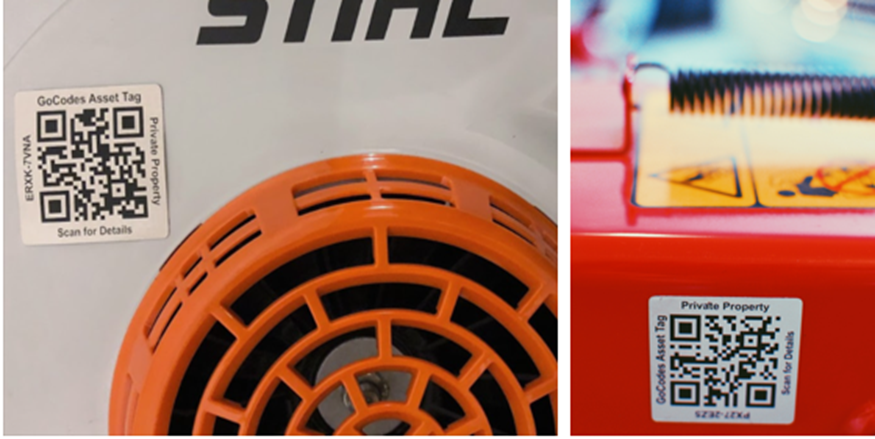
When your inventory is tagged with such labels, workers can simply scan the label on, for example, a pallet of cement or a container with spare parts using their smartphone.
Then they can access the app and record that the cement/spare parts were used or replenished with just a few clicks.
Likewise, since managers can access the central database of inventoried items on their phone or another internet-connected device at any time, they can see the changes in inventory in real time and make appropriate allocation/procurement decisions.
Therefore, pre-ordered or self-printed labels and a mobile app will—by reducing the need for manual entries and updates—significantly increase the accuracy of inventory records and also provide all involved parties with a single source of up-to-date information.
Naturally, this will help avoid many issues, such as delays due to the workers’ lack of access to sufficient amounts of materials and supplies required to do their work, or purchases of unnecessary items because of outdated inventory data.
Lack of Complete Inventory Visibility
Considering an almost endless array of construction inventory items a company can use, not having complete inventory visibility is one of the biggest inventory control challenges.
This issue plagues many construction companies with multiple project sites, storages, or facilities, making it challenging to know how much inventory they currently have.
Of course, this lack of visibility can result in ordering too much of some material while a hefty quantity sits somewhere unused or purchasing equipment, spare parts, and accessories you already have.
In comparison, when your company utilizes inventory control software, you and your team get instant access to a centralized system with complete inventory visibility.
Moreover, such software should allow you to track inventory quantities in real time and prevent inventory shortages (discussed in more detail later).
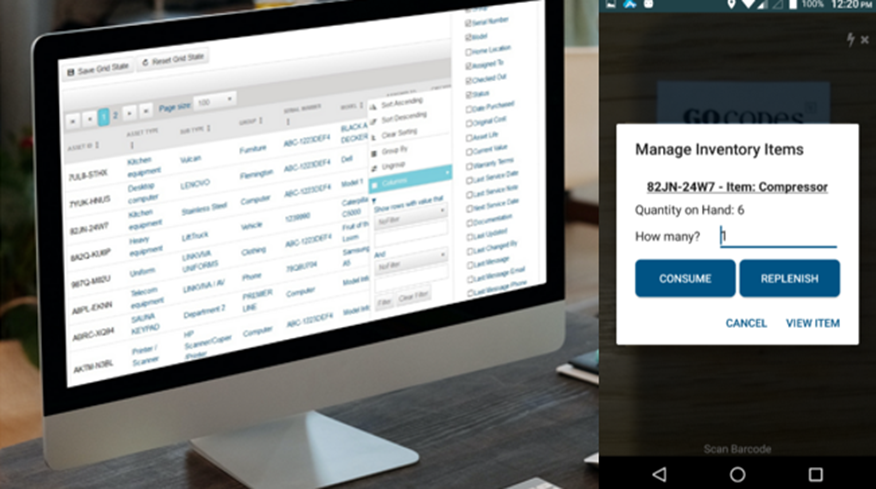
Using such software, you can access the central inventory and see the current stock levels of all your tracked inventory or filter your search parameters to find data on individual inventory items you’re looking for.
This real-time access to the software’s database allows you to avoid inventory overstocks, minimize inventory shrinkage (loss and theft), and even identify unreliable suppliers, all of which translate into cost savings.
For instance, our inventory control software, GoCodes, provides construction companies with an affordable all-in-one package (cloud software, in-app scanner, and labels) to quickly set up an efficient inventory control system and gain complete inventory visibility.
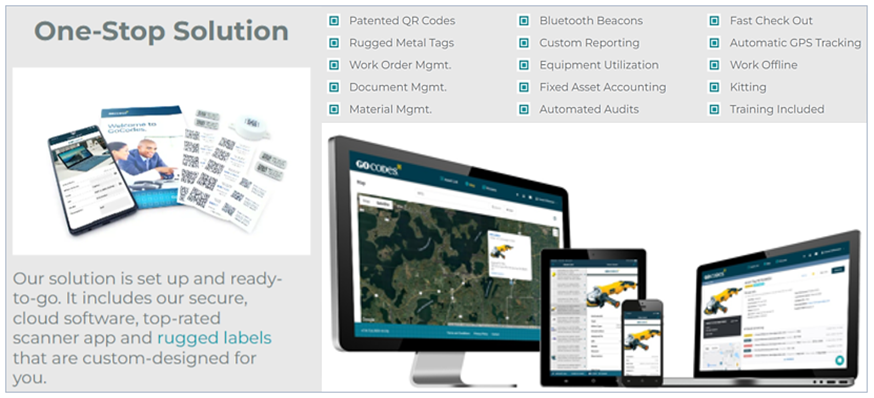
Moreover, the simplicity and versatility of the GoCodes tracking system allow you to use it on any type of inventory, including more durable items like equipment and tools, giving you complete control of your construction inventory management.
That way, you know where all your valuable resources are at all times, how many of them you have, and when and why they’ll be used.
To summarize, inventory tracking software gives you complete inventory visibility, thus successfully addressing this common inventory control challenge.
Problems Tracking Inventory Locations
Another issue that arises when a company relies on outdated tracking methods is that they often have problems tracking inventory locations.
In other words, when there is no central system that is constantly updated and can be accessed from any location at any time, it’s very hard to keep track of inventory as it’s received, stored, and consumed by a construction company.
Conversely, when your inventory can be physically tracked by attaching QR code labels to individual items or containers/pallets, you can track inventory locations from when they’re delivered to when they’re used.
In fact, when these QR labels are GPS-enabled, the software will automatically record their GPS location every time an inventory item/container/pallet is scanned and will show it on a map.
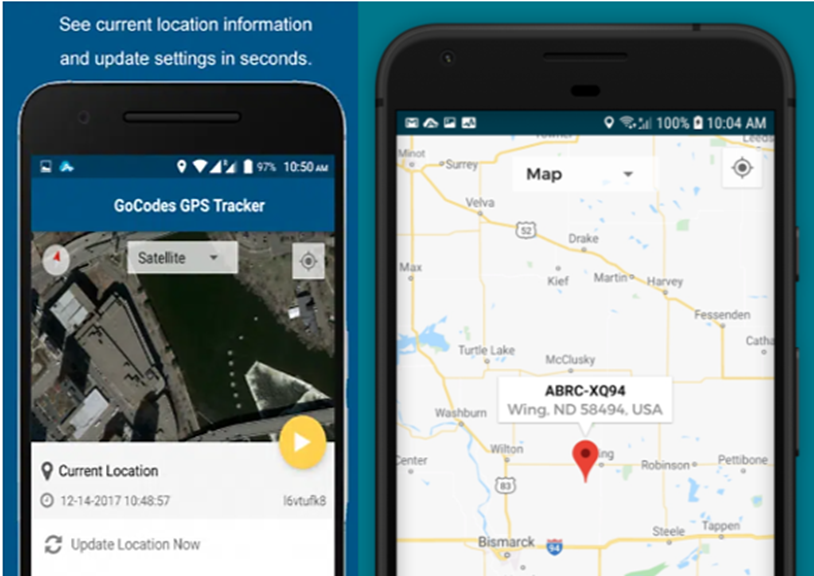
As you can imagine, these automatic GPS location updates can be very helpful in many situations, such as:
- determining not only whether specific inventory is available but also where it’s currently located, allowing for quicker transport and better inventory utilization
- identifying the last known location (and user) of lost or stolen inventory, which can facilitate the internal/police/insurance investigation process
- quickly resolving issues related to inventory left unused/forgotten on-site, helping you prevent inventory waste and reduce costs
To sum up, any problems tracking inventory locations can be efficiently and cost-effectively addressed by implementing inventory control software with a GPS-enabled location tracking feature.
Difficulties Performing Inventory Audits
When inventory control processes are paper- or spreadsheet-based, performing inventory audits is typically a very time-consuming and resource-intensive process for construction companies.
However, inventory audits (confirming that recorded and actual inventory levels match) are crucial for year-end financial reporting, accounting reconciliation, and inventory management purposes.
Moreover, any mistakes made during an inventory count can negatively affect your company’s operations, like potential inventory shortages or overstocking and inaccurate financial forecasting.
On the other hand, when inventory control is automated with the help of software and scannable labels, the system will keep a real-time account of inventory levels, which will make any inventory audits much easier.
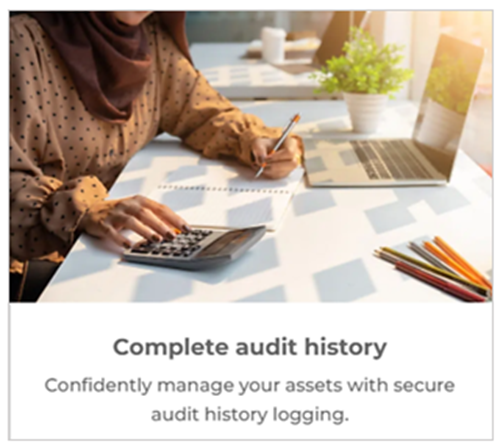
As shown, inventory audits are facilitated by having access to the history of changes in inventory levels, thus helping determine where a discrepancy might’ve occurred.
Furthermore, when doing an actual inventory count, employees can scan multiple inventory items at once, thus significantly simplifying the auditing process.
Overall, using an automated inventory control system helps your company reduce human errors, save valuable time and resources, improve financial transparency, and enhance operational efficiency.
In other words, such a system can eliminate many difficulties typically related to performing inventory audits.
Inability to Accurately Forecast Inventory
Not having access to a central inventory database with past usage history makes it challenging for construction companies to accurately forecast their future inventory needs.
In other words, largely manual inventory control methods mean that records of the specific quantities of materials used on previous projects, their consumption rates, and project-specific factors are dispersed in many data sheets or unavailable at all.
As a result, the construction company has to rely on rough estimations and guesswork to forecast its future inventory needs, which increases the chances of making inaccurate inventory forecasts.
Conversely, when historical data on past projects are kept in a centralized, cloud-based system available to all users, many of these issues are effectively eliminated.
This means managers can use inventory control software to analyze past data, create custom inventory reports, and make data-driven forecasts of future inventory needs.
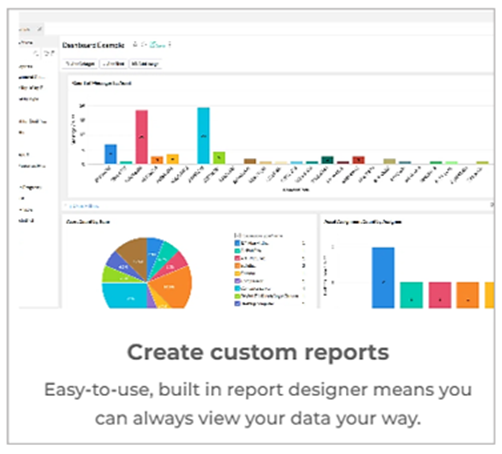
This analytics and reporting feature allows your managers to leverage past data when forecasting inventory for future projects, enabling them to account for variables like project size, duration, and project-specific requirements.
This ability allows your company to improve forecasting accuracy, minimize inventory shortages and excesses, and optimize resource allocation, leading to enhanced efficiency and profitability.
To recap, construction companies can successfully face the challenge of poor inventory forecasting (and budgeting) by adopting an automated inventory control system and leveraging historical data.
Failure to Prevent Inventory Shortages
When workers don’t have enough materials or other supplies necessary for smooth project completion, this typically leads to employee and equipment downtime, project delays, and cost overruns.
And manual, unorganized inventory control processes offer plenty of opportunities for inventory shortages.
For instance, when inventory levels are kept and manually updated in a spreadsheet, it can easily happen that the quantity was updated in one sheet but not in its copies.
Therefore, one manager can inadvertently miscount the available quantity of some material, and that mistake can go unnoticed until it’s determined that actually there is not enough material to work with.
Depending on the material type and availability, this may lead to delays (while the material is ordered and delivered) and higher purchase and delivery costs.
However, inventory shortages can be effectively addressed by, as we mentioned, tracking inventory levels in real time and receiving automated low-quantity alerts.
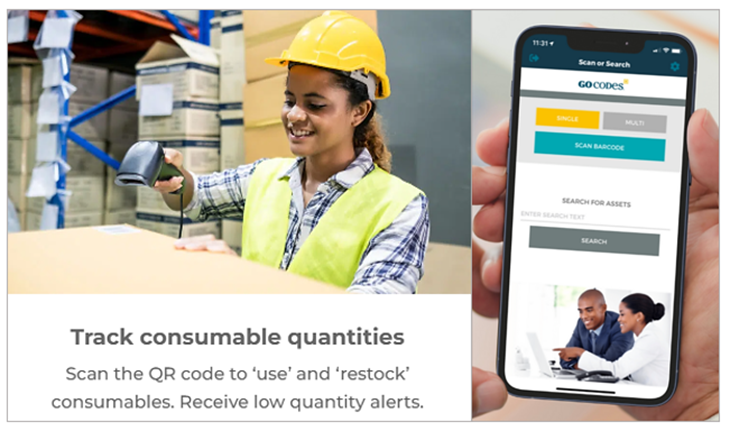
In other words, you can instruct your inventory control software to automatically notify the responsible staff (in the app and by email) when the quantity of a particular inventory item reaches critical levels.
This simple yet powerful function is crucial for preventing inventory shortages, and ensuring that new inventory (supplies, spare parts, materials) is ordered on time.
As such, automated low-quantity alerts are integral to having real-time, end-to-end control over your complete inventory, so your employees always have everything they need to do their job efficiently.
Conclusion
Implementing an automated inventory control system (simple, affordable, and versatile) can help you eliminate or mitigate common inventory control challenges.
Simply put, once the software is configured and the tracking system set up, you’ll be able to track inventory levels in real time, keep inventory data accurate, and have complete inventory visibility, including inventory locations.
This will help you with inventory audits, forecasting, and preventing shortages, all of which allow you to minimize inventory costs and maximize productivity and profitability.