If you’re in construction, you’re aware that the safety of your workers and the efficiency of the equipment and tools they’re using are crucial for the success of any building project.
This fact places equipment maintenance—and equipment inspections as one key aspect of effective maintenance—among the top priorities of construction company owners and managers.
However, keeping track of all required equipment inspections and maintenance can be complex, with many potential pitfalls.
That is especially true when construction companies use outdated and time-consuming manual tracking processes.
To help you avoid those issues, we’ll explore five key actions that will allow you to streamline the tracking of equipment inspections, thus ensuring worker safety and equipment efficiency needed for smooth and profitable project delivery.
In this article...
Invest in the Right Tracking Software
The powers of equipment tracking software span much wider than enabling you to keep track of equipment inspections, and that’s precisely why you should invest time and effort into finding one that best meets your needs and budget.
Simply put, tracking software allows you to digitize, integrate, collect, and manage all equipment-related data—inspections included—in a centralized cloud-based database that can be updated in real-time.
After all, there’s no point in tracking equipment inspections if the other data concerning your equipment is not tracked, right?
Moreover, tracking software should enable you to establish a comprehensive equipment tracking system, automate data capture, and provide your staff instant access to critical equipment information, such as its usage, location, condition, and maintenance history.

Of course, in this day and age, all this equipment info should be available on any device with an internet connection, such as a smartphone, tablet, laptop, or desktop.
In other words, all your employees—from jobsite crews to top managers—should be able to access the central database and individual equipment data online, at any time and from any location.
This is useful for everyone involved in construction operations, particularly those who regularly perform equipment inspections—service technicians and equipment operators.
For starters, they can use equipment tracking software to view the info relevant for inspection, such as the equipment’s last maintenance date and repair history, user manuals, and other documentation.

Likewise, they can use the app to enter info about their inspections, such as inspection type, date and time, and location, as well as leave comments and add images (for example, photos of damage found during inspection).
Given all these powers of tracking software solutions and their growing popularity in the construction industry, it’s not surprising that the market offers many options.
Therefore, it’s important to do research, ask other construction professionals about their experience with equipment tracking, and read reviews before selecting the right software.
In doing so, you’ll find only a few solutions that deliver everything we mentioned and are both easy to use and affordable.
One such solution to consider is our equipment tracking app, GoCodes Asset Tracking.

GoCodes Asset Tracking combines the power of cloud software, scanner apps, and rugged QR code tags, and you’ll see how they all work together in the next section.
In the meantime, the key point to remember is that investing some time and effort—plus an affordable monthly/yearly subscription—into the tracking software that meets your needs and budget allows you to collect all sorts of equipment data.
In turn, this will enable you to automate and streamline many equipment inspection processes through a centralized cloud-based database that can be updated in real-time and accessed from any location and any device.
Tag Your Construction Equipment
As indicated in the previous section, tagging your construction equipment using asset tags will make it easier to track equipment inspections, as such tags can be scanned to retrieve all equipment data, including inspection information.
As for how tagging works, an asset tag (label) is affixed to every piece of construction equipment you want tracked, and after the initial equipment info is entered, your tracking system is set up and ready to go.
However, the system will work differently depending on the type of asset tags you choose.
For example, you might opt for RFID (Radio Frequency Identification) tags which use radio waves to communicate with a scanner, meaning they can be scanned from a distance and require no direct line of sight.
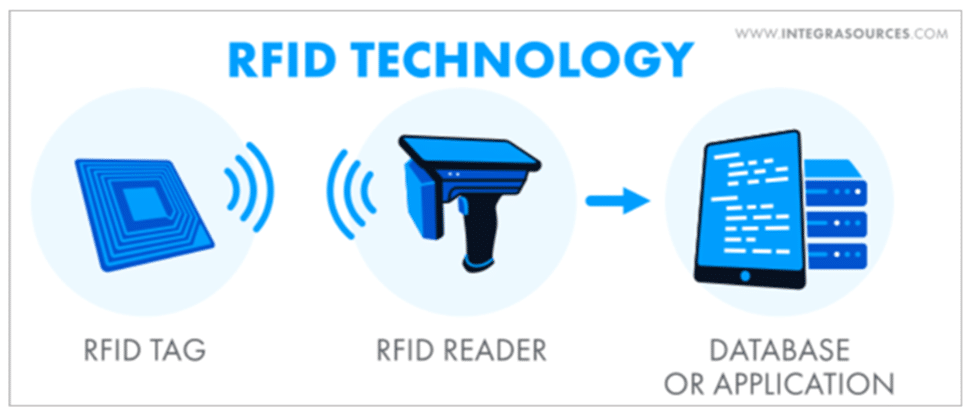
However, RFID tags usually require special scanners, making this solution more expensive than other ways to tag your equipment, such as barcode labels or QR code tags.
The advantage of barcode or QR code tags being attached to your construction equipment for inspection tracking purposes—other than their cost—is the simplicity of their installation.
In other words, you typically receive these asset tags with your tracking software package (or print them yourself), and all you have to do is affix them to the equipment and tools you want to be tracked.
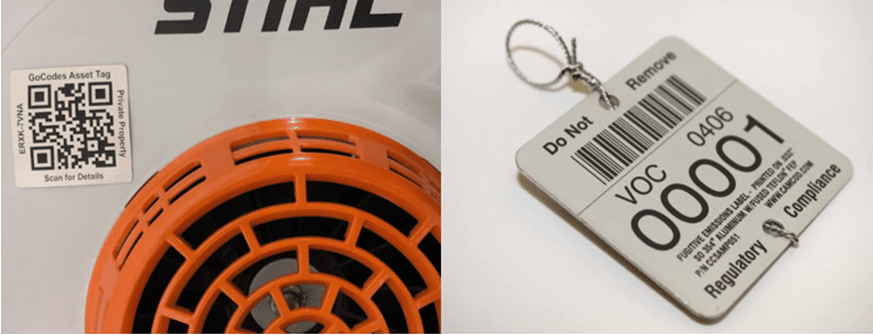
From there on, when it’s time for inspection, service technicians and equipment operators can simply scan the tag—using their smartphone, tablet, or another compatible device—and retrieve all the information about that specific piece of equipment.
This saves them time otherwise spent searching for that particular asset in the software’s database (which may contain more identical pieces of equipment and lead to errors).
In other words, they can instantly access the right asset and its info and proceed with their inspection while their company enjoys other benefits of asset tags.
Therefore, whichever type of asset tag you choose, tagging your construction equipment is integral to keeping track of equipment inspections.
Track Equipment Inspection Assignments
Once your construction equipment is tagged with asset tags and technicians/operators have downloaded the tracking app to their own or company-issued smartphone or tablet, it’s time to assign and start tracking equipment inspection tasks.
Using tracking software allows you to assign inspections to specific staff members or teams, specify what tasks they should perform, set up automated reminders to notify them when inspections are due, and track the completion of inspections in real time.
Naturally, all this is essential for tracking inspection assignments to ensure that equipment inspections are being performed on schedule.
For example, construction companies can use GoCodes Asset Tracking to assign specific inspection tasks, such as “check/change oil and filter.”

After the equipment manager creates a new inspection task, they can choose the type of inspection and set the inspection frequency (daily, weekly, monthly, etc.) and then assign the task to a specific employee or team responsible for inspections.
Furthermore, they can set a due date, add any additional notes or instructions for that inspection, and set up automated notifications of upcoming inspections/maintenance.
Depending on the settings, these notifications will be sent the day before or on the morning of the inspection.

From there, they can complete the inspection while the tracking app lets them view relevant equipment info and record inspection results.
The centralized database automatically updates these results, providing real-time insights into the equipment’s condition and maintenance needs.
Therefore, by assigning inspection tasks to their employees using tracking software, construction companies will be able to track the status of in-progress inspection tasks.
Ultimately, this provides them with a detailed record of all completed inspection tasks, including who was responsible for performing them.
Keep a Detailed Maintenance Log
As it’s clear from previous sections, tracking software allows construction companies to keep a detailed log of all inspection/maintenance tasks completed for each piece of equipment.
This automatically updated log is essentially a record of all maintenance activities, repairs, and inspections performed on specific construction equipment.
To give you a better idea, here’s what a typical maintenance log looks like.
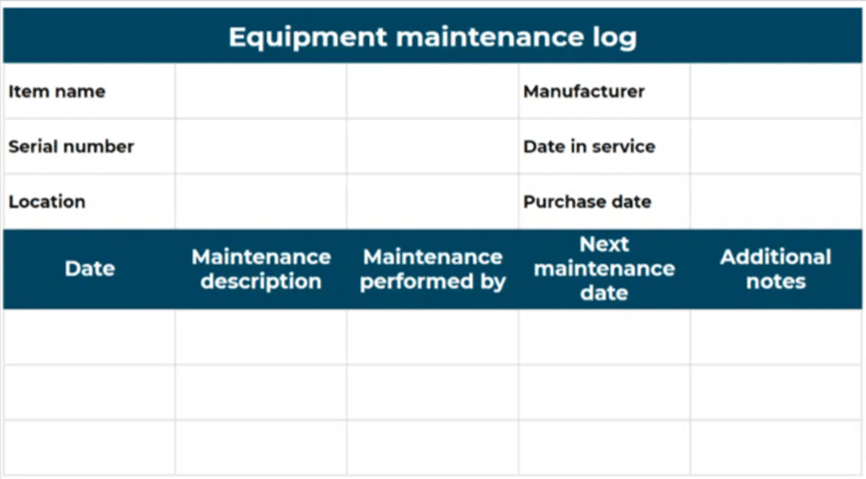
As you can see, some information, such as the item name, manufacturer, and purchase date, are predefined and don’t change.
Other data, such as the equipment’s location, who performed the maintenance, and on which date, are recorded by tracking software automatically when the user scans the asset tag.
Finally, some information will need to be filled out by the person performing the inspection, such as the description, the next maintenance date (if not already set), and any additional notes.
All this information goes into a maintenance log, enabling construction companies to:
- make better-informed equipment management decisions
- demonstrate regulatory compliance for safety inspection purposes
- provide evidence for accident/insurance investigation purposes
For example, based on the log, you can make data-driven decisions on the frequency of the required inspections, as well as determine whether it’s more cost-efficient to repair or replace specific construction equipment.
Another example is when OSHA inspectors show up for a safety inspection of your jobsite.
A detailed maintenance log can show how your company complies with the required equipment maintenance/inspection procedures.
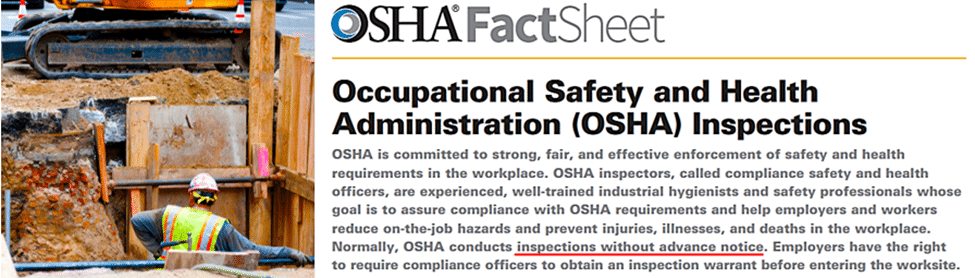
The same applies when equipment breaks down or causes an accident, and the maintenance log can be used to support insurance claims.
Therefore, the right tracking software should allow you to keep a detailed maintenance log of all inspection tasks.
This will enable your company to track completed equipment inspections, make better-informed decisions, and meet safety compliance and insurance requirements.
Perform Regular Equipment Audits
Once all equipment has been tagged, maintenance and inspection tasks can be scheduled and assigned, and their completion tracked in real-time.
All of this makes performing regular equipment audits much easier.
Although equipment audits can have different objectives, we’ll focus on the most typical reasons for performing them, such as:
- verifying that all equipment (on a specific jobsite or in storage) is accounted for and in good working condition
- ensuring that all assigned equipment inspections and maintenance tasks have been performed and recorded
Let’s say you have a list of equipment and tools assigned to a particular jobsite, and you want to check whether they’re still there (not misplaced or stolen) and whether their condition fits your records, including each asset’s inspection and maintenance history.
In that case, when equipment is tagged using asset tags, the audit team would come to the construction site and start scanning the tags using their mobile device.

When an audit team member scans a piece of equipment, they can access relevant information about performed inspections and maintenance and then check its condition against these records.
This audit can yield some interesting results, including:
- identifying missing or stolen equipment, indicating worker accountability and security issues
- detecting equipment whose condition does not reflect the records, indicating safety inspection reporting issues
- flagging equipment due for inspection and maintenance that is not recorded in the tracking system, indicating scheduling issues
Of course, audit team members can enter any discrepancies detected during an audit and actions needed in the tracking app on their phone or tablet.
Finally, the audit team and company management can generate customized audit reports and analyze the audit results, allowing them to make data-driven decisions about future inspection and maintenance requirements, as well as any needed equipment repairs or replacements.
Overall, performing regular equipment audits with the help of tracking software allows construction companies to detect and address inspection-related issues, thus improving employee responsibility, jobsite security, and equipment safety.
Conclusion
To sum up, to keep track of equipment inspections, you need to track equipment.
Therefore, you should find the right tracking software and tag your construction equipment.
Doing so will allow you, among other things, to schedule and track inspection assignments, keep a detailed maintenance log, and easily perform regular equipment audits.
Additionally, maintenance staff and operators will have instant access to equipment info they need to do their job, as well as the ability to record their activities and share it with managers and other users in real time.
The final outcome of these key actions is a streamlined equipment management process that ensures worker safety and equipment efficiency required for efficient and profitable project delivery.