It’s no secret that repeatedly going over budget will leave you strapped for cash, which isn’t ideal when you have a business to run.
The more unplanned expenses you have for a project, the less money there is for future projects, payrolls, equipment maintenance, and other things that make your company safe and productive.
The problem is that an average of 80% of all construction projects run into a delay that’s around 20 months long. In other words, most projects cost a lot more than intended.
Because of this, you should eliminate or at least decrease the number of budget overruns you experience. This article will explain what causes such expenses and how to fix them, giving you a good starting point!
In this article...
Project Estimate Inaccuracies
Project cost calculation starts at the estimation phase, making it extremely important for future budgeting.
Think of it like this: if you estimate incorrectly and assign each project phase less time or a lower budget than you should have, you will inevitably run into delays and spend too much.
Such issues usually snowball and transfer into other project phases, which means a single mistake in the beginning can compromise the entire project.
Therefore, it’s not exactly a surprise that a fifth of all companies find estimates the most complex financial process within a construction project.
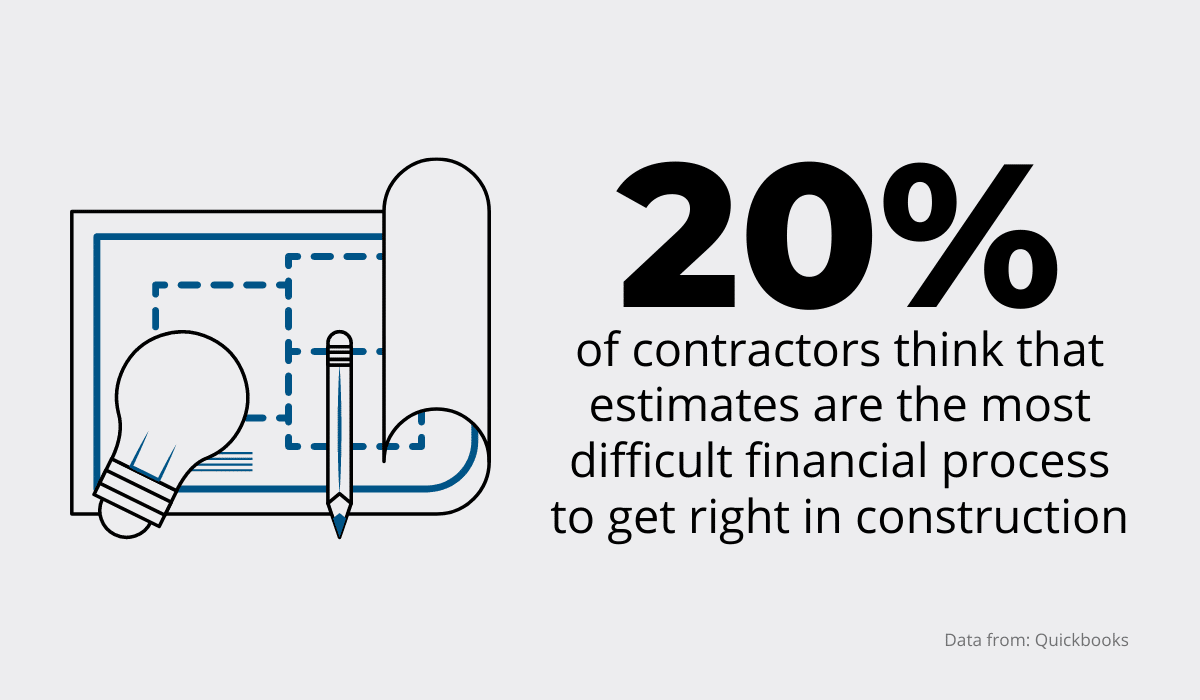
Companies are aware of how quickly things can take a turn for the worse based on one inaccurate estimate, as 29% of them have experienced earning a lot less than expected from a project.
Some of the mistakes that happen during the estimation process include:
- Doing it manually instead of using software
- Failing to include financial experts
- Going forward with the project with imprecise estimates
- Neglecting to rely on data to create new predictions
- Trusting the optimism bias, i.e., predicting the best possible scenario
You can fix most of these mistakes easily. First, don’t try to estimate a project’s costs yourself, especially if finances aren’t one of your strong suits.
Find someone experienced in this line of work and ensure that the person doesn’t give you an overly optimistic estimate, as that could very easily put you into debt.
The finance expert should use existing data, such as past project estimates, current pricing, and the available materials and employees to make their projections.
If you use digital solutions to leverage the right data in making these estimates, you will see a dramatic increase in accuracy.
Errors in Project Design
Design issues can make or break your entire project.
As the basis of your construction project, its starting point, any deficiencies in the design stage can cause you to bleed money in the long run.
Since we already know that most projects run into overruns and delays, it’s not surprising that design errors are the leading cause of 29% of such overspending.
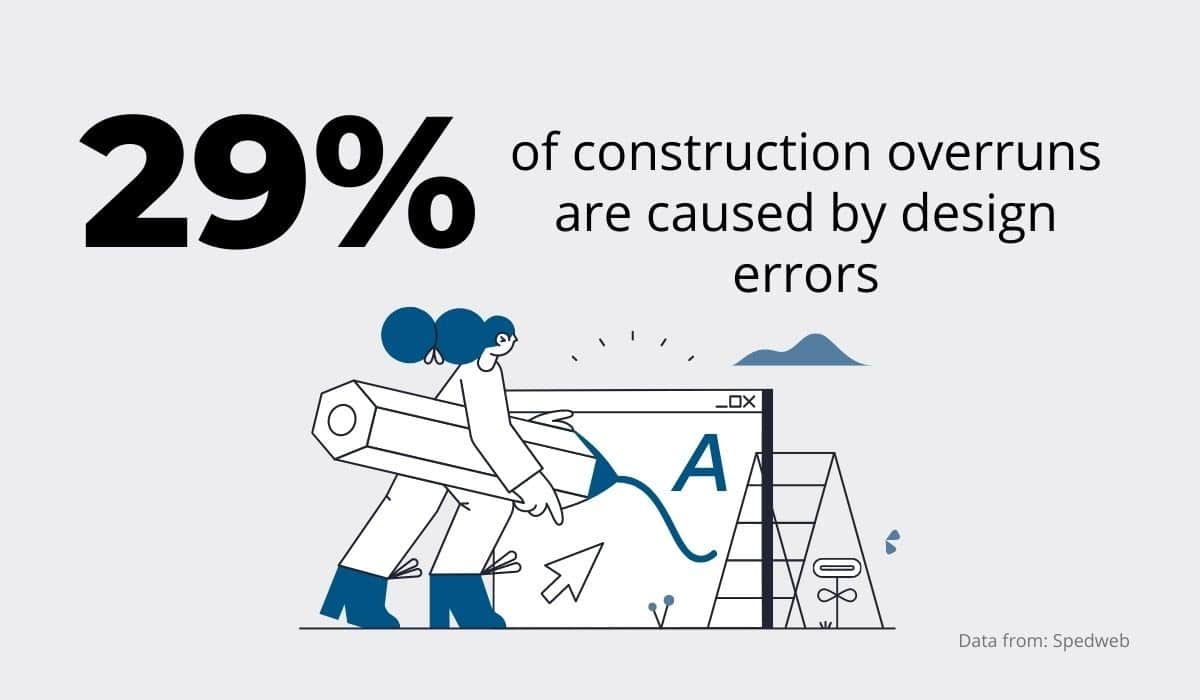
The fault may lie with an incorrect plan, an incomplete one, or poor design to begin with.
The real problems arise when you don’t include a specific parameter into your blueprint, and its later addition costs money.
Entirely omitting a part of the design or misjudging the number of layers necessary will end up costing the owner more than agreed, which can lead to a dispute.
Clearly, the bigger the project, the more can go wrong in the design stage. There’s simply more room for error due to the greater number of variables, from the sheer number of tasks to the people involved.
For example, the latest Chamber of Commerce Q4 2021 report stated that almost all (95%) of construction contractors had experienced at least one product shortage in the past quarter. Such shortages can set them back significantly.
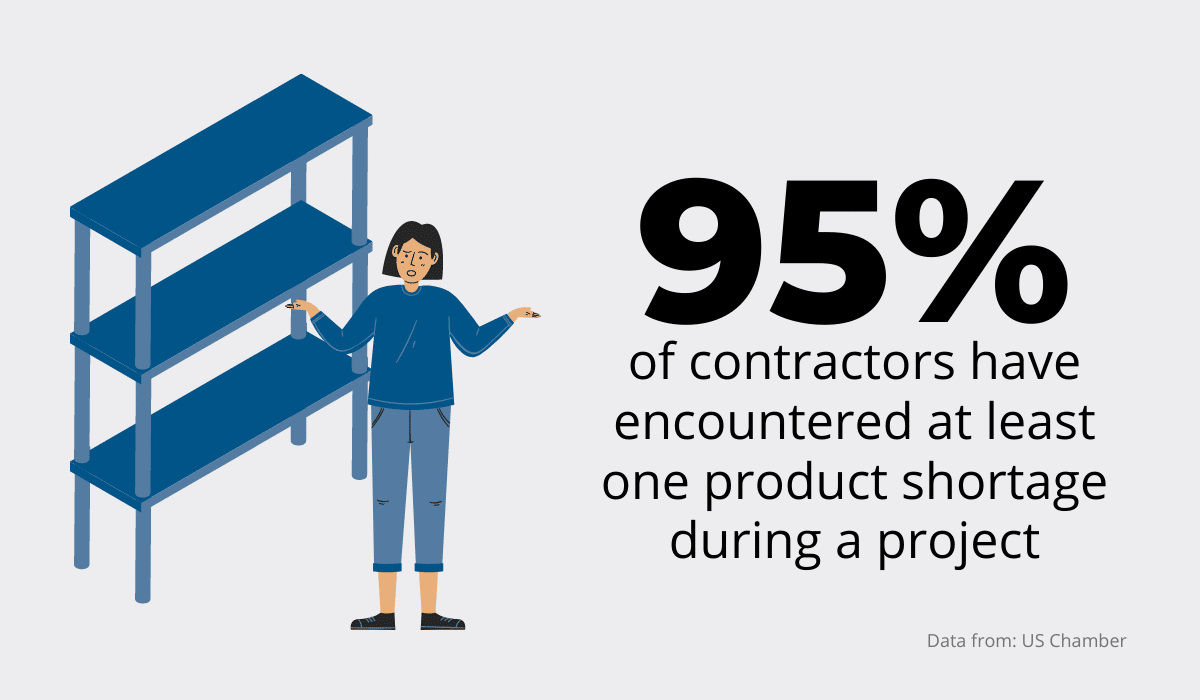
The best way to deal with these issues is to set up a quality control program, so that a second pair of eyes can catch any mistakes or omissions in your designs.
And remember, if there are variable parts, it’s better to overestimate the potential expenses than underestimate them.
Another thing that can benefit you is going digital and using software to plan your projects.
Software solutions can often identify inconsistencies and point out potential issues before they escalate, saving you a lot of time and money down the line.
Not Budgeting for Change Orders
Let’s face it: changes are inevitable, no matter how well you’ve designed and estimated your project.
Something will go wrong somewhere, but if you are sufficiently prepared, it doesn’t have to be the end of the world. After all, as many as a third of construction projects eventually need change orders.
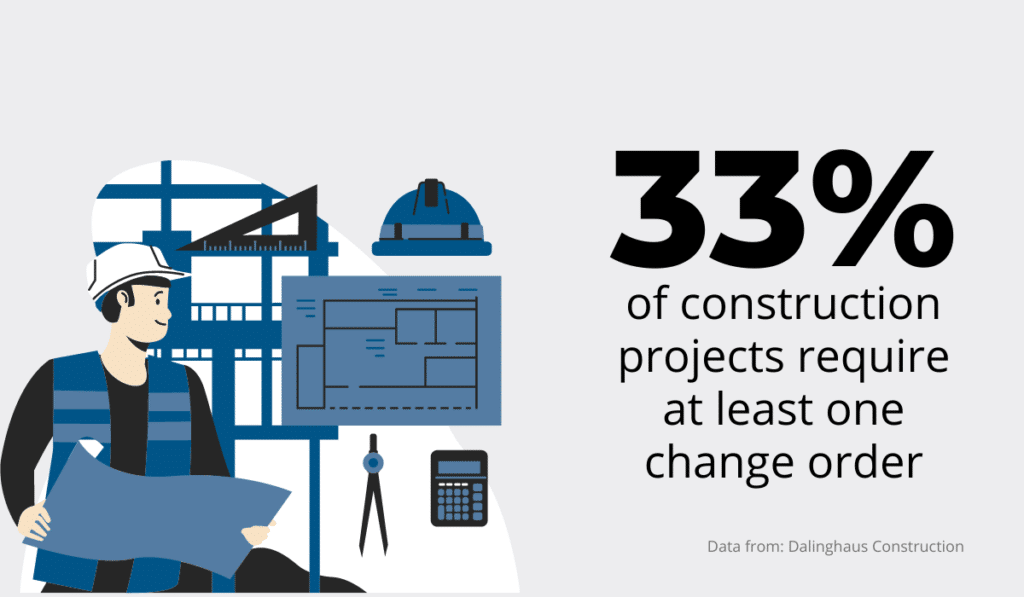
In other words, one-third of contractors have added extra orders to the original plans at some point, whether for material, labor, or work. Along the way, they realized that they needed to modify the basic outline required to finish the project on time.
You have to prepare for change orders, especially during the ongoing pandemic. The Q4 2021 report also states that COVID-19 has had a massive impact on the construction industry, changing many things for the worse.
Construction companies mentioned difficulties in obtaining building products and cost fluctuations. In other words, the pandemic has caused a shortage of construction materials, leading to costly project changes.
The available materials such as steel, wood, and roofing have gone up in price, which many didn’t account for in their plans.
Therefore, your best bet is to budget with change orders in mind, allowing for the possibility of price increases and material shortages down the line.
Administration Mistakes
Mistakes in project administration don’t come cheap, either.
While administration might not seem as crucial as the estimation and project designing at first glance, it is still vital for the success of your project. Any mistakes you make can still leave you out of pocket.
For instance, the most common and often the most detrimental administrative issue is the lack of communication.
The construction industry is notorious for struggling with the proper flow of information.
In fact, a German construction coordinator believes that “the main challenge is always communication between the ones that collect the data and those that use it.”
After all, miscommunication and use of incorrect data caused almost half of US construction rework, costing businesses $31.3 billion in 2018 alone.
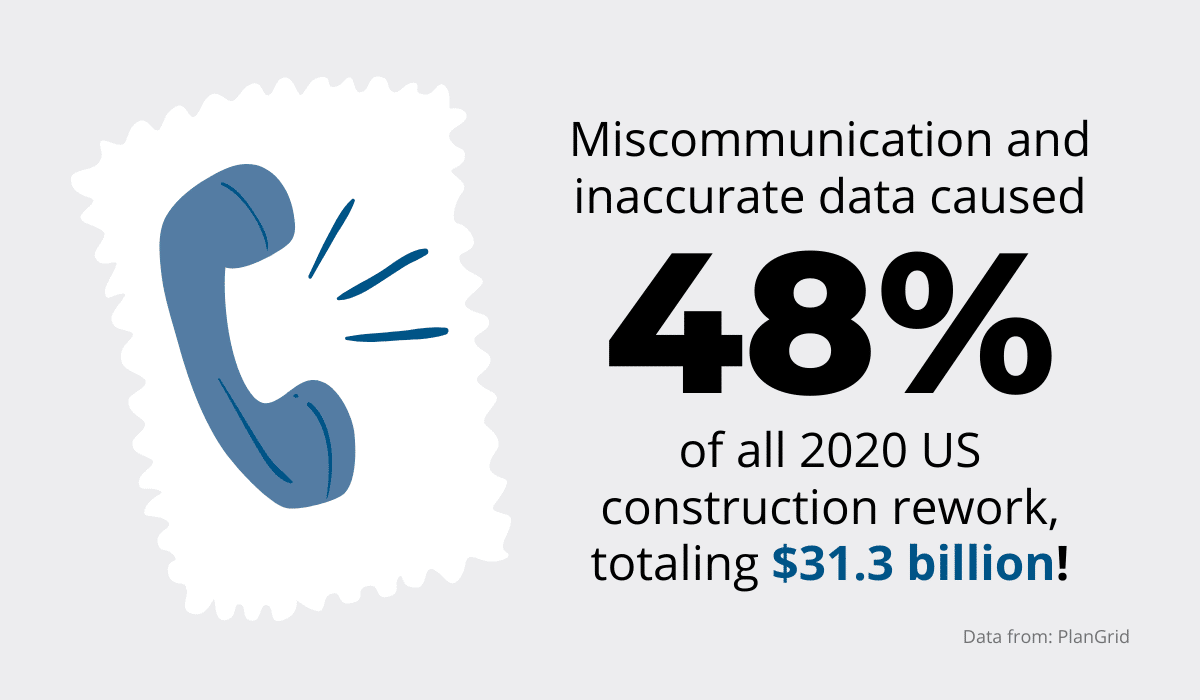
Clearly, incorrect data and poor communication lead to huge losses. Is that a problem in your company? It might be if the teams that gather and process your data are not communicating with your field workers and project managers effectively.
Your team must act as a whole for the project to run smoothly, even if they do not work on the same task or the same site. For example, your field workers should have a way of notifying the maintenance team if something happens to the equipment.
However, if your service team doesn’t get a notification on time, no one will use the machinery in question until it is fixed, which can happen days from then, once the maintenance staff finally processes the request.
Because of this, many stress the need for the construction industry to turn to digital tools and improve business processes that way.
With software such as GoCodes Asset Tracking, which lets you report an issue after a quick QR code scan, your field workers can report a problem in a couple of minutes, and your maintenance team will get the report instantly, thus minimizing downtime.
Inefficient Site Management
Even if your planning is automated and nearly perfect, the project can fail with poor execution.
Putting the plans into action and building the perfect structure is what the end client will see and value. So, if not done right, your project won’t be efficient.
A big obstacle to successfully executing a project is using incorrect data, which can cause expensive rework and delays. Studies show that project data that lacks quality leads to wrong project decisions 41% of the time.
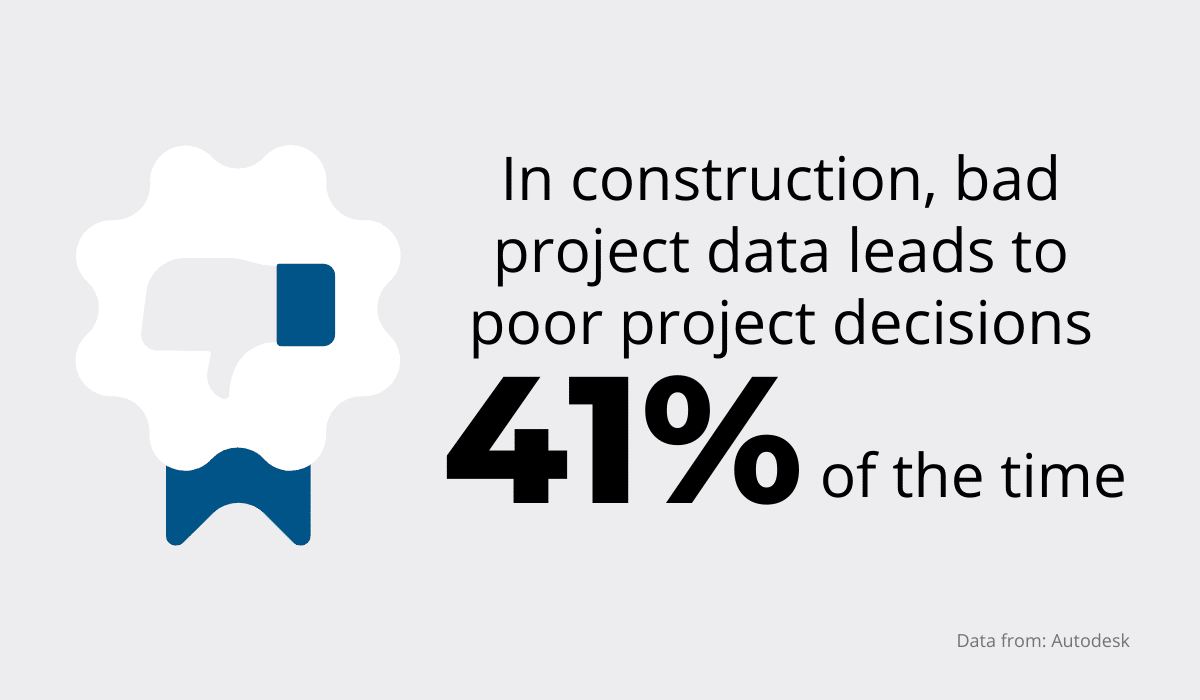
Therefore, if you don’t thoroughly check and use the data you have to your advantage, your project has a good chance of being late and more expensive than planned.
Another thing that often goes wrong in the execution stage is management. If your management practices are outdated, this will affect the quality of your project and its completion.
For example, construction companies often don’t properly manage their equipment, which is vital for project execution.
They fail to schedule the use and the maintenance of the equipment properly, so essential machines are often unavailable when needed. They don’t cooperate with other sites for quicker equipment delivery and fail to monitor use and maintenance.
Not knowing where each machine is, when you can use it, and what condition it’s in can cause significant delays and overruns.
However, you can easily fix this with equipment tracking software, such as our own solution, GoCodes Asset Tracking, that lets you track the machinery, its condition, maintenance, and current user, allowing for seamless management.
Unqualified Staff
Last but not least, staff that lacks the necessary skills can be the cause of the project being behind schedule.
In fact, this is the reality for many contractors in the construction industry. The Q4 2021 report states that most of them report having moderate to strenuous difficulty finding skilled people to perform their job.
Moreover, more than half of them are apprehensive about their current workers’ skills.
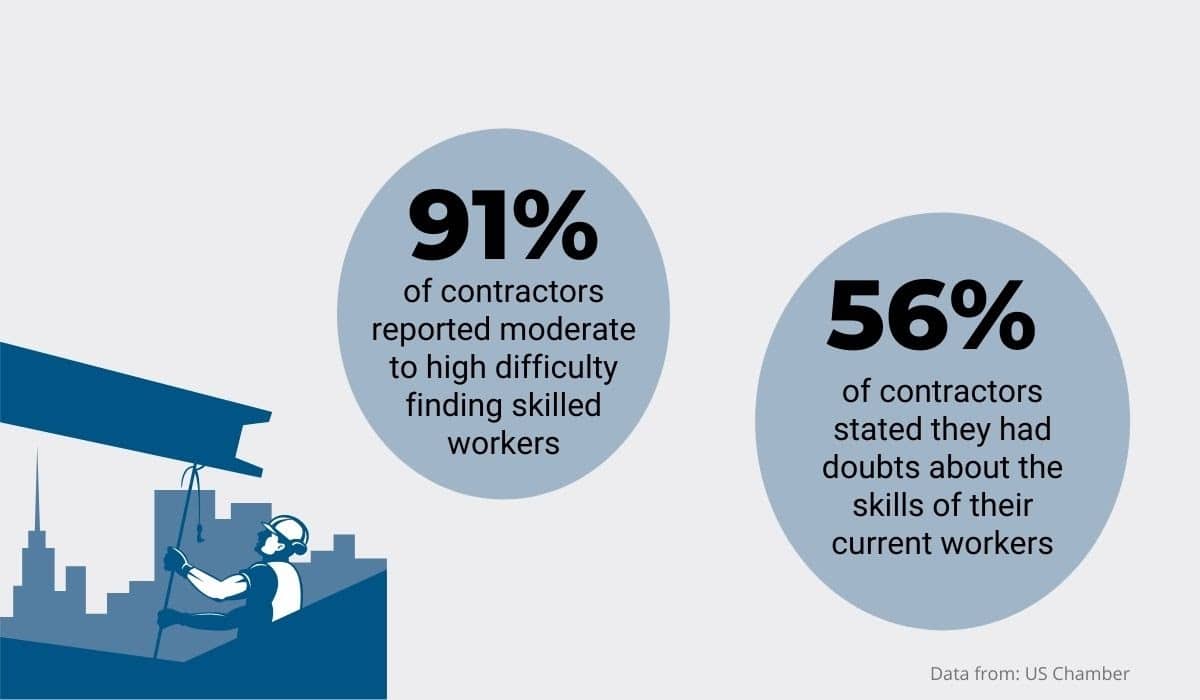
Since more than half of these contractors are planning to hire more people in the first half of the year, it is clear they will have issues finding qualified staff.
So, it doesn’t come as a surprise that around 45% of construction contractors had to turn down projects because they didn’t have enough staff for it.
Clearly, professionals in your industry understand that they can’t just take on work if they don’t have qualified staff to finish it. If you take a job and hire unskilled workers for it, you risk:
- Wasting materials
- Damage to your equipment
- Safety liabilities
- Breaking deadlines
- Expensive rework
When you have to look for construction workers, it’s a good idea to start with your own company database. However, if it’s paper-based, you’ll probably have issues finding precisely the person you need for the job.
On the other hand, if you save employee information in some kind of an automated database, you’ll be able to find the right people instantly.
If you can’t leverage that kind of a database or if you still have trouble finding skilled workers, think about joining a construction association. It can help you network and get in touch with professionals you need on your project.
Conclusion
Project overruns are prevalent in the industry, but you don’t have to accept them as the standard at your construction site.
Instead, put more effort into each part of your project, starting with the estimates, designing the project flawlessly, to project execution itself, and leverage digital solutions to automate processes where you can.
Of course, you should also account for possible change orders to stay within budget.
Finally, pay attention to who you hire, as unqualified staff can make or break the project and increase overruns.