In construction, success is measured, at least in part, by how well you adhere to the outlined budget.
This is precisely where cost management comes into play.
This process plays a crucial role in monitoring and controlling expenditures while mitigating potential risks that could jeopardize project profitability and lead to unwarranted overspending.
So, if you are interested in learning more about how to improve the financial management of your construction projects, keep on reading.
In this article, we delve deep into the importance, components, as well as challenges of cost management in today’s modern construction world.
But before that, we must first define what this process actually is.
In this article...
What is Cost Management in Construction
The definition of cost management itself is pretty straightforward.
Cost management involves estimating, controlling, and monitoring all financial processes related to construction work on a specific project.
Its primary objective is to prevent unnecessary additional costs from accumulating and eating into profits, while simultaneously making sure that the specified quality standards and objectives are met.
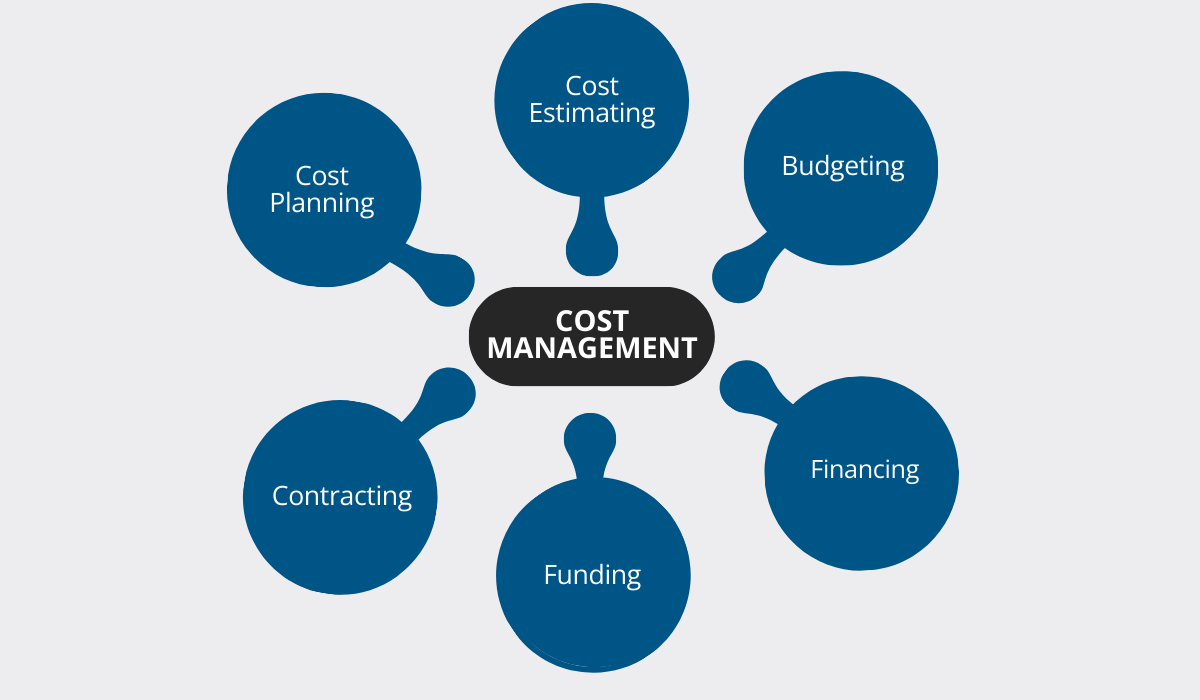
Effective cost management, however, isn’t a one-man job.
It requires collaboration among all the stakeholders, including owners, contractors, subcontractors, and project managers.
It also isn’t a one-time task, but an ongoing process that evolves throughout the different phases and aspects of a project, from initial planning, design, and estimating, to the recruitment of workers, change orders, and more.
All in all, cost management, like any aspect of project management, focuses on ensuring the highest quality of the structure being built, handling cost overruns, and achieving the overall successful completion of the job at hand.
Now, while the definition and the goal of this important process may be simple, implementing it efficiently is anything but.
Let’s explore why that is.
Why It’s So Hard to Manage Cost in Construction
A testament to the complexity of cost management is the unfortunate prevalence of cost overruns in construction projects.
And, judging by the Reddit comments you can see below, they almost feel like a rule rather than an exception.
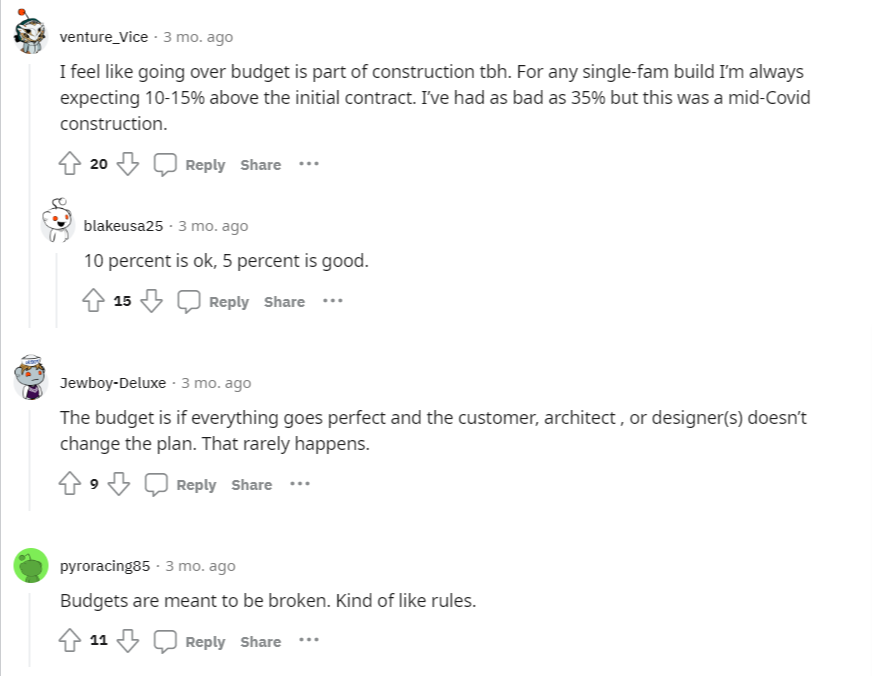
But, why is that?
Well, there are many circumstances, both external and internal, that can make managing expenses an ambitious feat.
The most prominent external factor in this context is the volatile nature of construction material prices.
Since these costs are so hard to predict, it becomes quite difficult to plan around them and create accurate budgets.
Marc Vicano, project manager of Vicano Construction Ltd, concurs, highlighting that it’s not solely the high cost of materials but their continuous fluctuations that pose a significant issue for professionals in the industry:
“Since the pandemic, the cost of construction has increased dramatically. It worked its way across the supply chain affecting both global and local markets. Going into 2023, the increase is tapering off, but the price of supplies won’t remain the same from the time the bid is submitted to the time you need to buy the supplies. Suppliers just can’t hold the price of their products that long.”
This is particularly problematic during critical phases like takeoff and estimation, which are at the core of cost management.
Still, material prices are not the only external factor that impedes cost management.
Some of the other aspects that add an extra layer of uncertainty during projects are:
- Regulatory changes
- Bad weather
- Geopolitical events
- Labor shortages
- Inflation
The challenges, however, do not end there.
Internal elements specific to individual projects, such as inefficient workflows or the nature of the job itself, can impact the overall financial stability as well.
Large and complicated projects, for example, are notoriously hard to manage.
Just take a look at the Channel Tunnel—the largest undersea tunnel in the world.
Despite the initial budget projection of 2.6 billion pounds for this project, the actual costs upon its completion in 1994 reached 4.65 billion pounds, representing a staggering 80% budget overrun.
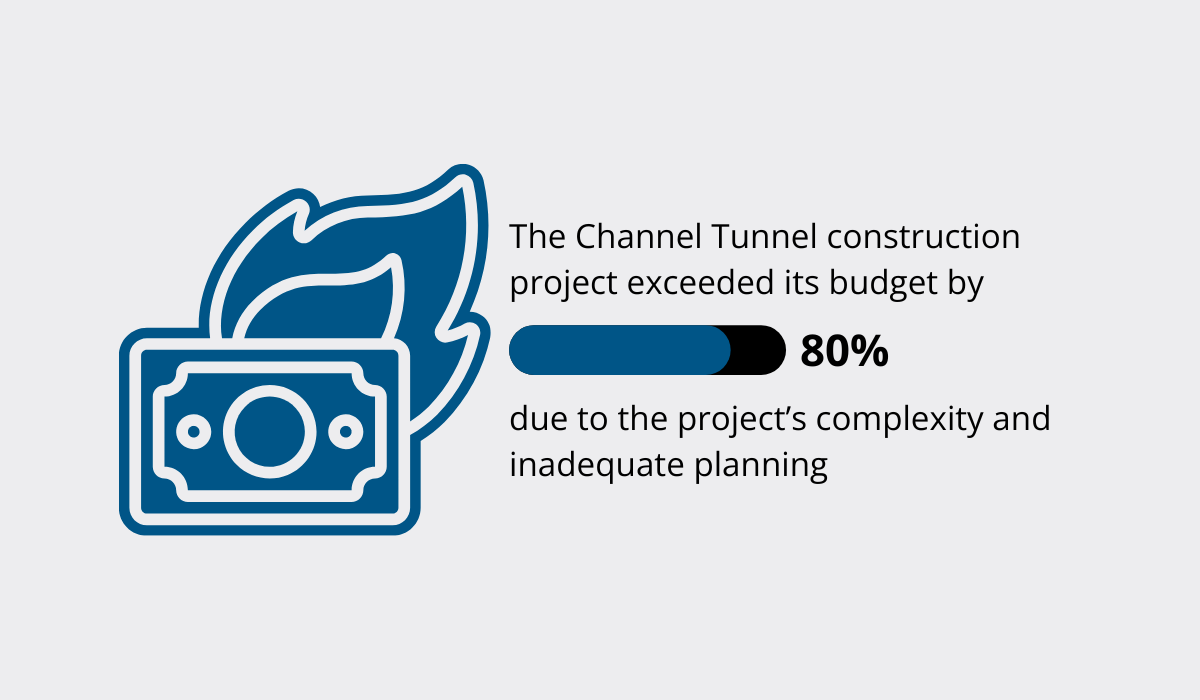
Factors contributing to this overrun included project complexity and lack of precedent for such an endeavor, which, in turn, resulted in optimistic revenue projections that failed to account for potential risks.
In short, it was a lack of preparation that made this venture so challenging.
Now, while the Channel Tunnel’s colossal scale makes it a unique case, smaller projects aren’t immune to similar pitfalls.
Every project has its particular demands in terms of design, site conditions, and architectural features, all of which can contribute to cost uncertainties.
So, to recap, the realm of cost management in construction faces a great deal of challenges from both external forces and internal project-specific factors.
Whether grappling with the unpredictable swings in resource prices, contending with adverse weather conditions, or navigating the intricacies of a complex project, efficiently managing costs remains quite a demanding aspect of project management.
What’s the Effect of Poor Cost Management
Despite its inherent challenges, professionals in the construction industry devote considerable efforts to efficient cost management.
The reason for this is simple: there is no viable alternative.
Poor cost management brings with it a host of undesirable consequences, including:
- Higher risk of errors during construction work
- Costly rework
- Budget overruns
- Project delays
- Reputational damage
An illustrative example highlighting these repercussions is the Sydney Opera House construction project.
Although considered a renowned Australian landmark today, the project commenced without finalized plans and, consequently, lacked a clearly defined budget.
The outcome?
Significant cost overruns and extreme delays due to a destructive cycle of errors and subsequent rework to rectify these errors.
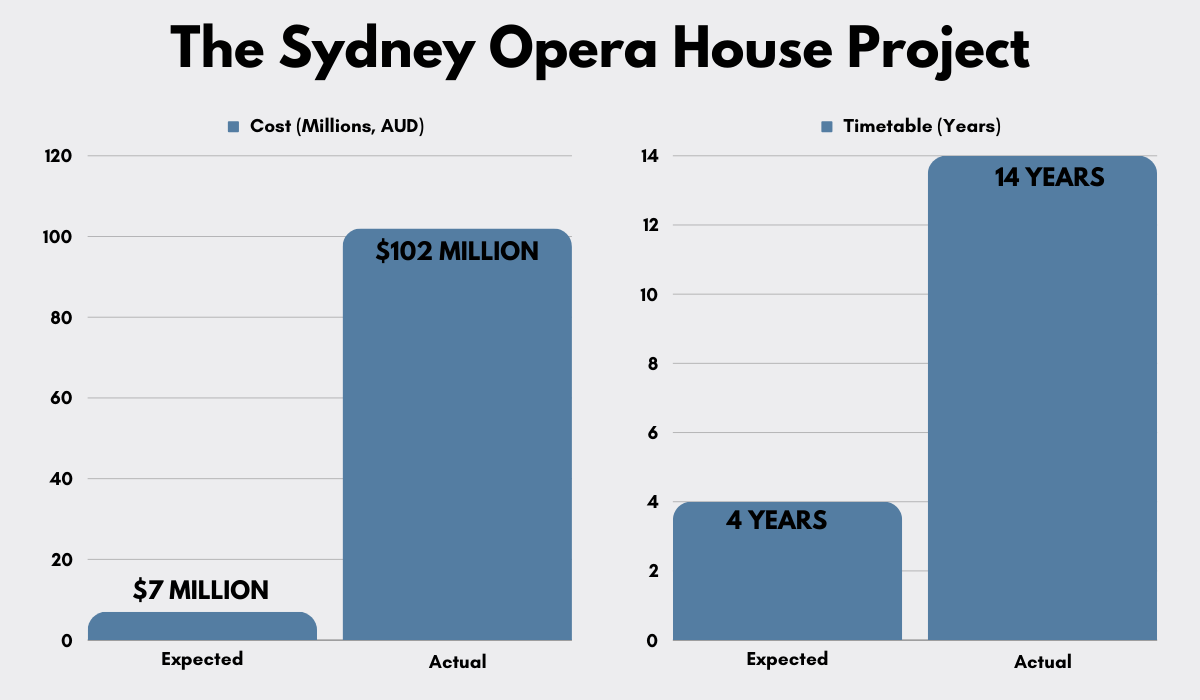
Notably, the initial estimated cost of the project was approximately 7 million Australian dollars, but the final cost skyrocketed to around 102 million, surpassing the original budget by more than 14 times.
This serves as a compelling lesson for industry professionals, emphasizing the importance of realistic budgeting, effective resource planning, and vigilant expense control, all of which constitute efficient cost management.
While the Sydney Opera House project ultimately attained success, other projects may not be as fortunate.
The amalgamation of outlined outcomes—mistakes, delays, overspending, and material wastage—often culminates in a failed project and dissatisfied clients.
Reputational harm then usually follows, potentially leading to the loss of future business opportunities.
In other words, inadequate cost management doesn’t merely affect an individual project but poses a substantial threat to the overall success and credibility of construction companies.
Key Processes of Construction Cost Management
As we previously mentioned, cost management is a complex process, consisting of many different elements.
Let’s briefly go over its four key components and explore why they are so important.
Resource Planning
Resource planning is the core of effective construction cost management. It involves the assessment of project requirements, including elements such as:
- Labor
- Equipment
- Materials
- Time
- Software needs
As any seasoned project manager will attest, being prepared from the get-go is paramount for achieving success in this industry.
The below statement made by a quantity surveyor testifies to that.
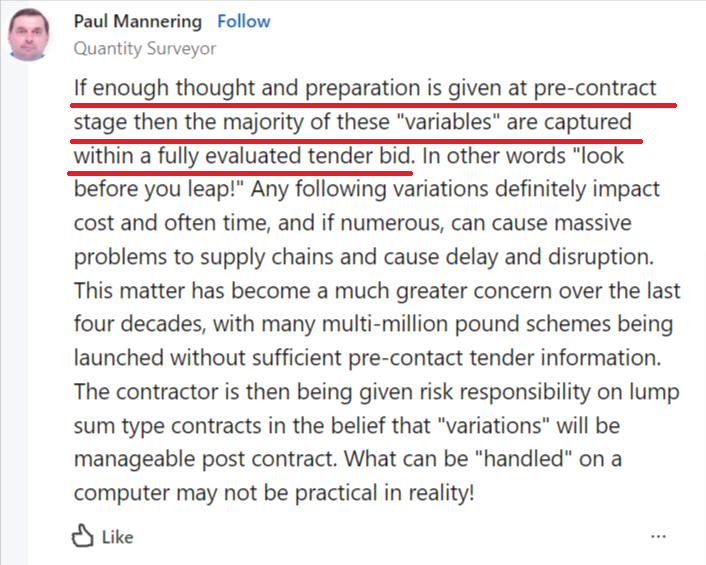
This is where resource planning plays a crucial role.
Its main purpose is to precisely define the type, quantity, and quality required for each of the factors outlined above.
So, when executed correctly, it ensures that there are just enough resources where and when you need them to complete the job on time, within budget, and at the highest possible quality, all without overburdening workers or compromising overall job site safety.
As such, it’s not only an integral part of cost management but also the starting point for successful project execution.
Cost Estimation
Cost estimation, as its name suggests, involves assessing the expenses linked to all the items outlined during the resource planning step.
Based on these estimates, a project budget will be created, a crucial component for obtaining funding, securing loans, and ensuring the project’s completion within the available financial resources.
In other words, a lot of things ride on the accuracy of these cost assessments, so a high level of precision is a must during this stage.
However, that may be easier said than done, given the complexity of construction work and its associated costs.
As depicted in the table below, construction expenditures go way beyond just the equipment rental rates and workers’ wages.
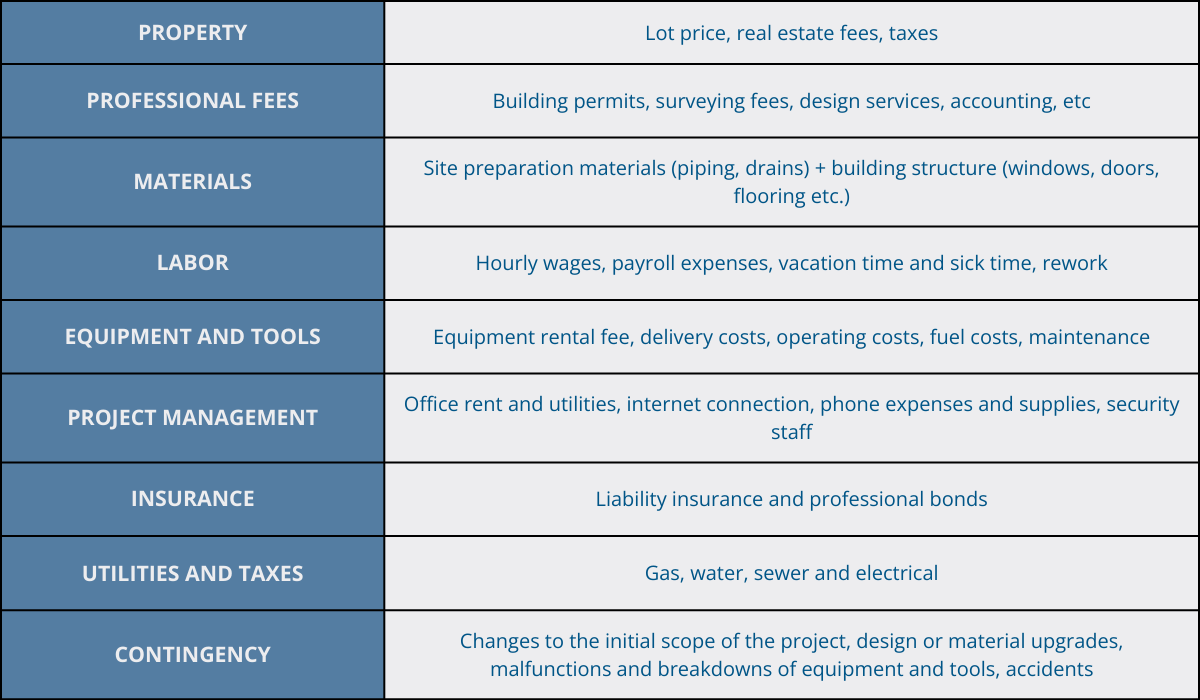
Numerous direct and indirect expenses, integral to transforming a project plan into reality, must be considered in the cost evaluation phase.
As if that weren’t challenging enough, add the complexities of cost management we mentioned earlier, and the task becomes even more formidable.
Fortunately, today there’s a plethora of tools developed precisely to simplify, expedite, and enhance the accuracy of this process.
For example, estimating software can calculate material costs based on the combination of project documents that are uploaded into the system and historical data from previous, similar projects.
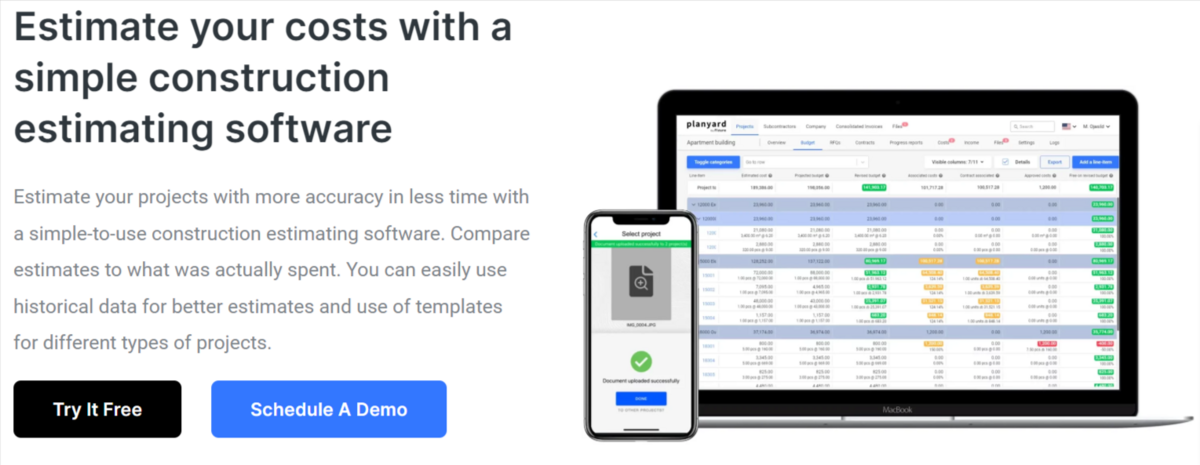
A little pro tip: should you opt for such a digital tool to streamline your efforts, it’s advisable to double-check the results yourself one more time before submitting the documentation.
When it comes to cost management, you can never be too careful.
Cost Budgeting
Budgeting is another critical aspect of cost management, involving the allocation of monetary resources to various components of a project.
Typically, budgets comprise three key elements:
Hard costs | Equipment, materials, labor |
Soft costs | Design, insurance, accounting fees, taxes |
Profit | The difference between money received and actual costs |
The importance of a well-constructed budget can’t be overstated.
It serves as an invaluable reference guide throughout the project lifecycle.
For starters, it plays a pivotal role in establishing clear terms and expectations regarding costs, payment schedules, and deliverables, which, in turn, minimizes the likelihood of disputes during and after construction.
Additionally, it aids in risk mitigation through contingency funds.
A good construction budget always includes a safety buffer, usually ranging from 5 to 10% of the total project cost, to cover unforeseen expenses such as material wastage or unexpected equipment failures.
That way, even if unanticipated issues do arise, the work can continue without delays or overspending.
Post-completion, a budget can be used as a tool for evaluating project success.
By comparing actual costs with budgeted costs, stakeholders can assess the project’s performance and identify areas for improvement in future endeavors.
Abbigail Meah-Ali, a project manager, elaborates on this:
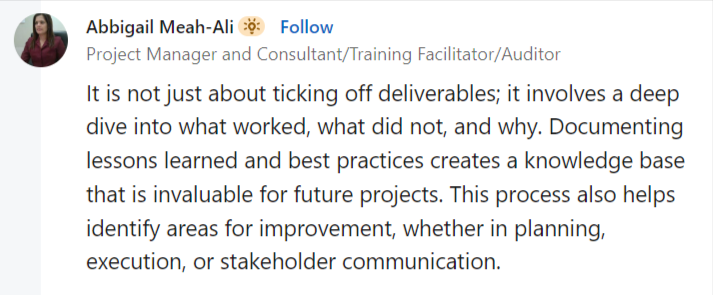
Learning from these past experiences can then help refine both budgeting and project management processes.
All in all, a well-planned budget functions like a compass, guiding decision-makers to make informed choices throughout the entire duration of the project.
Cost Control
Cost control is aimed at overseeing project expenses once the construction work is already in progress.
Despite successfully determining your resource needs, estimating the costs associated with those resources, and incorporating them into the project budget, immunity from overspending is still not guaranteed.
This is where effective cost control can be a real game-changer.
This process focuses on managing labor, equipment, overhead, and material costs during construction to ensure the financial well-being of the project.
It typically involves four key steps:
- Tracking costs
- Conducting variance analysis
- Identifying the root cause of variances
- Taking corrective action to get back on track
Let’s explore these steps using a specific example.
Suppose you are monitoring your equipment costs, and by comparing the budgeted expenses to the actual ones (variance analysis), you notice that you’re paying for repairs far more than you should be.
Upon investigation, it becomes apparent that there was no adequate upkeep schedule in place, and the machines weren’t regularly inspected, leading to more frequent breakdowns and, naturally, more frequent repairs.
To address this issue and regain control over costs, equipment management software, such as GoCodes, may be implemented.
The software can, by enabling users to set up future service tasks and monitor their progress, help ensure that maintenance is done on time and regularly.
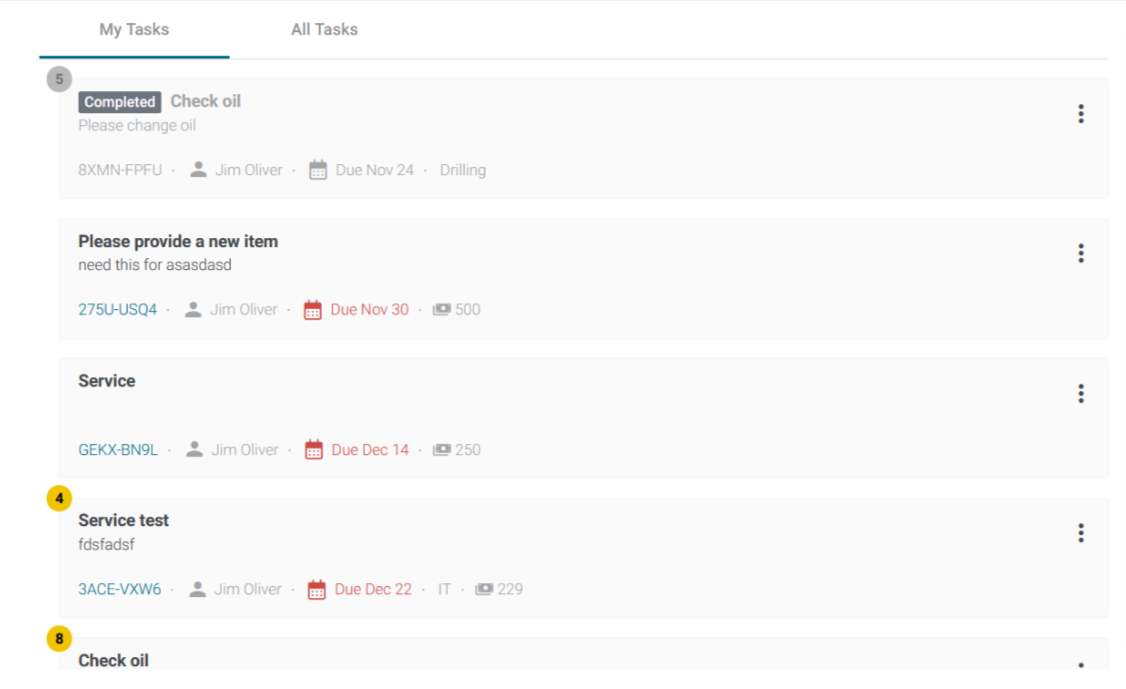
Let’s face it, keeping track of minor tasks like oil changes can easily be overlooked.
Having a tool that does that for you can prove extremely beneficial, particularly in reducing avoidable costs and keeping your machinery operable.
Overall, there’s no denying that successful cost control demands commitment and watchfulness.
However, by adhering to these four steps, the implementation of measures to minimize or even eliminate unnecessary costs becomes considerably more manageable.
Conclusion
Mastering cost management may initially appear as a straightforward process, but in reality, it involves numerous complexities and interconnected components.
Still, there’s no need to get discouraged by that fact.
While achieving proficiency in all these processes demands time and dedication, the rewards are substantial—enhanced profitability, more accurate budgeting, and, most importantly, better project outcomes.
So, think of this article as your guide on the journey towards more efficient cost management.
By arming yourself with insights and strategies outlined here, you can ensure that the projects you undertake turn into success stories rather than cautionary tales of project mismanagement, like some of the projects mentioned throughout this article.