Cost management plays a crucial role in project management, ensuring adherence to both budget and schedule.
Nevertheless, some fail to grasp just how complex this process can be, lacking both an understanding of its elements and the ability to differentiate between them.
In order to shed some light on cost management and its scope, we’ve chosen to dedicate an entire article to its various components.
Here, we explain what these elements entail, clarify the distinctions between similar ones, and provide practical tips for improving their execution.
Let’s delve into the details.
In this article...
Cost Estimation
Cost estimation, as the term suggests, involves the assessment of the expenses associated with a construction project.
This encompasses both direct costs such as labor, materials, or equipment, as well as indirect costs like insurance, utilities, taxes, and other miscellaneous expenditures.
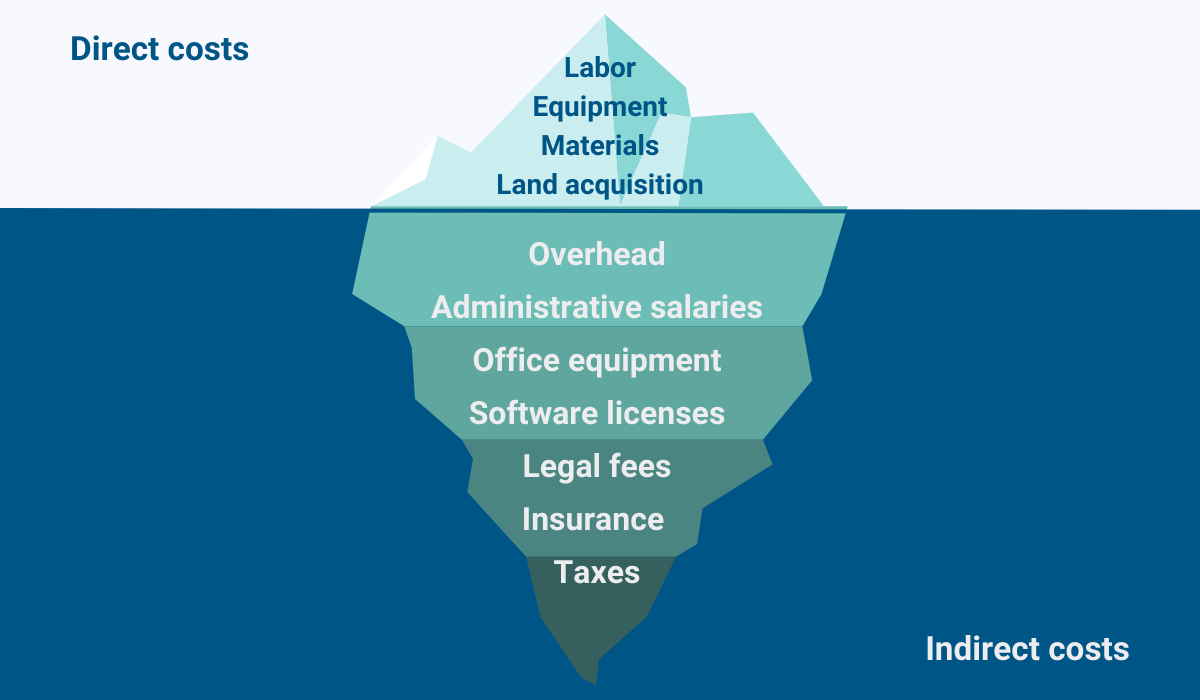
Given that this process lays the groundwork for project success, thoroughness during its execution is a must.
At the earliest stages of project planning, cost estimation plays a key role in determining the feasibility of the endeavor.
By itemizing all anticipated expenses, it offers a transparent overview of what can be accomplished within the allocated budget, thus providing decision-makers with insights into whether the venture is viable and worth pursuing.
Moreover, accurate cost assessment helps create bids that are both competitive and profitable.
As you know, overestimating the project can easily lead to you not winning the bid.
However, if you underestimate it, you might get the job, but you’ll be also losing money.
Cost estimation is precisely the means to strike the right balance, securing the job without compromising the bottom line.
In fact, according to Abe Schainker, Senior Vice President at the global real estate services company JLL, this process can be a make-or-break point for contractors’ success.
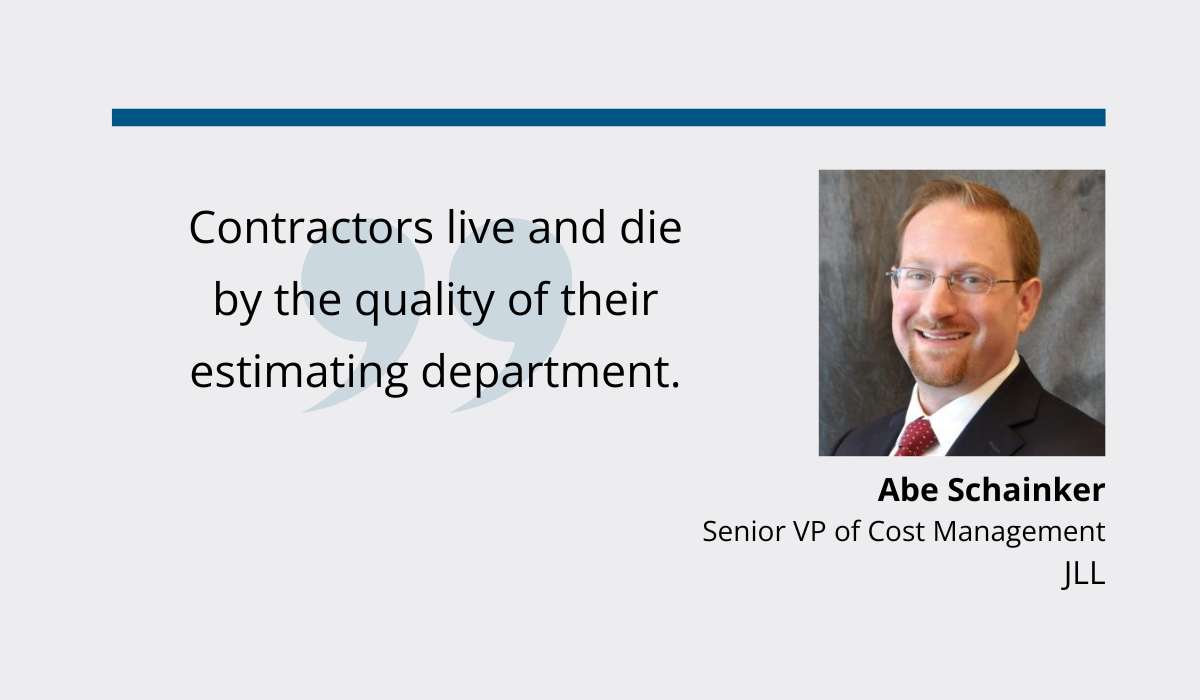
Here, it’s also important to note that construction cost assessment is not a one-time task.
It requires multiple reviews throughout the project’s lifecycle to ensure maximum accuracy.
The American Association of Cost Engineering identifies five phases of estimating, each varying in methodology and intended end usage.
Estimate Class | End Usage | Expected Accuracy Range L=LowH=High |
Class 5 | Concept Screening | L: -20% to -50% H: +30% to +100% |
Class 4 | Study or Feasibility | L: -15% to -30% H: +20% to +50% |
Class 3 | Budget, Authorization, or Control | L: -10% to -20% H: +10% to +30% |
Class 2 | Control or Bid/ Tender | L: -5% to -15% H: +5% to +20% |
Class 1 | Check Estimate or Bid/Tender | L: -3% to -10% H: +3% to +15% |
Here, levels 1 to 5 denote increasing accuracy, with level 1 representing the most accurate estimate.
All in all, accurate cost estimation is extremely important—no two ways about it.
It serves as the foundation for winning bids, ensuring profitability, and, generally, successful project management from start to finish.
Budgeting
Similar to cost estimation, budgeting outlines all the expenses that will be incurred during the construction project.
However, despite sometimes being used interchangeably, the two aren’t the same.
Ideally, an estimate precedes the budgeting process, predicting the labor, equipment, and material costs.
In contrast, the budget is a more finalized figure, representing the amount of money designated for the project after all its requirements have been determined, and all expenses have been evaluated.
In simpler terms, the primary role of budgeting is to set a spending limit for the project.
In a way, an accurate and precise budget acts as a protective shield, safeguarding from:
- delays,
- cost overruns, and
- client dissatisfaction.
But, how does it achieve all that?
Essentially, the purpose of a budget is to provide a clear picture of what needs to be done, by when, and with what funds.
This information empowers decision-makers to efficiently allocate resources, ensuring there are just enough materials, equipment, and labor to complete the job without any hitches.
Even if certain hiccups do arise, budgeting yet again acts as a safety net by incorporating contingency funds into the final financial plan.
A contingency fund represents a reserve of money set aside to cover additional costs that may occur during the course of a project, whether due to design changes, unforeseen site conditions, weather delays, or other unexpected issues.
As such, it’s an efficient measure against cost overruns.
Lastly, a well-constructed budget helps manage client expectations by establishing clear financial parameters and boundaries.
It informs the clients about how their money is spent and helps them understand the limitations and possibilities within their budget, preventing unrealistic requests regarding the scale or features of the project.
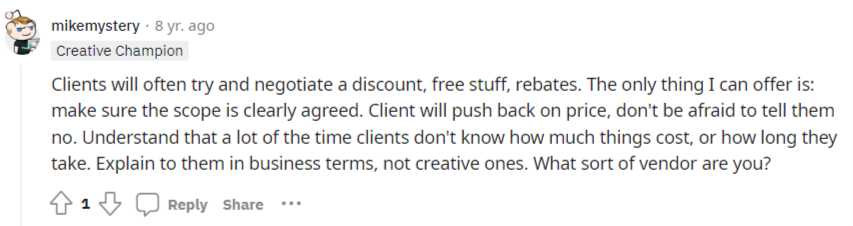
This prevents pushback on the price and potential disputes later on.
At the end of the day, budgeting is a staple when it comes to cost management, serving as a guide for all the parties involved in a project.
It aids the project team in managing resources effectively, thus maintaining adherence to the schedule and staying within the predetermined budgetary constraints.
At the same time, it enables clients to keep up with the project’s complexities and associated expenses, empowering them to set realistic expectations.
Cost Control
Once the budget has been established and the project is underway, it’s necessary to make sure that these budgetary constraints are actually adhered to.
This is done through a process called cost control.
It includes overseeing and managing expenses across all aspects of the project, with the goal of:
- Preventing delays
- Preventing cost overruns
- Enhancing the project’s return on investment (ROI)
- Ensuring the optimal quality of the structure
Successful cost control involves a systematic four-step process, as you can see depicted below.
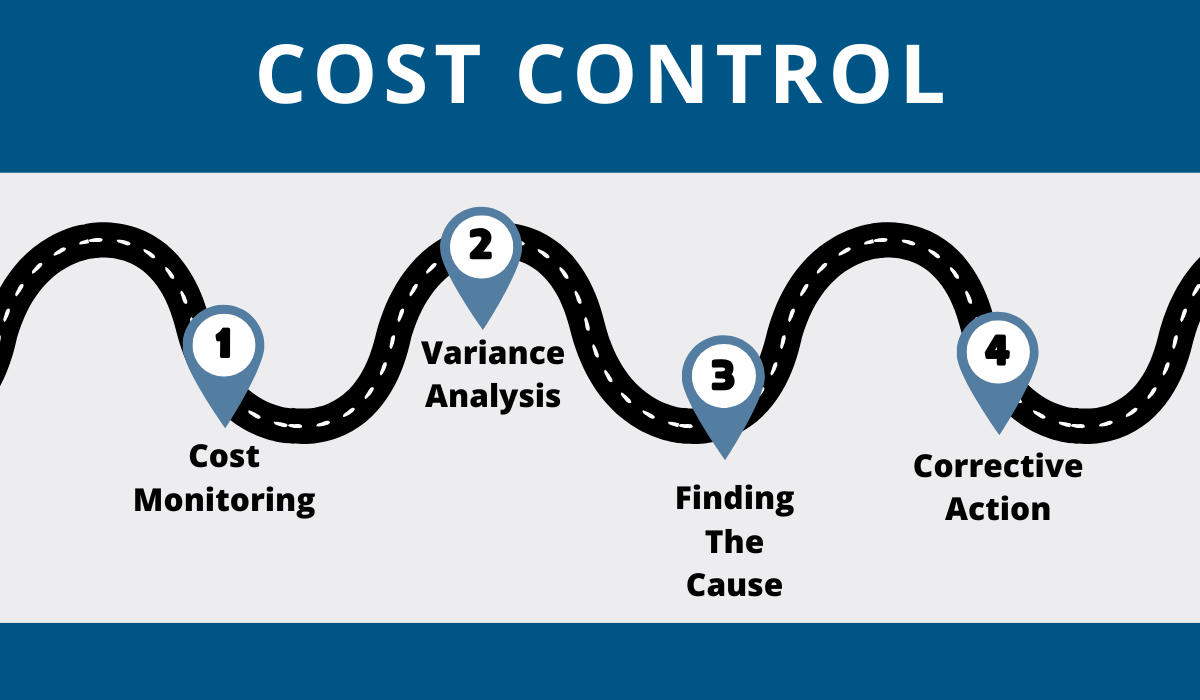
The first step is to monitor all expenses and assess the performance of labor, equipment, and materials.
Remember, cost monitoring isn’t just about the amount of money spent on each of these elements, but about their productivity as well.
So, ask yourself questions like “Is there too much material wastage?”, or “Are certain machines underutilized”, to find areas that might need improvement.
The second step entails performing variance analysis, i.e., comparing the planned budget and schedule against the actual situation.
If you notice substantial variance, it may be time to look further into the problem and find its root cause.
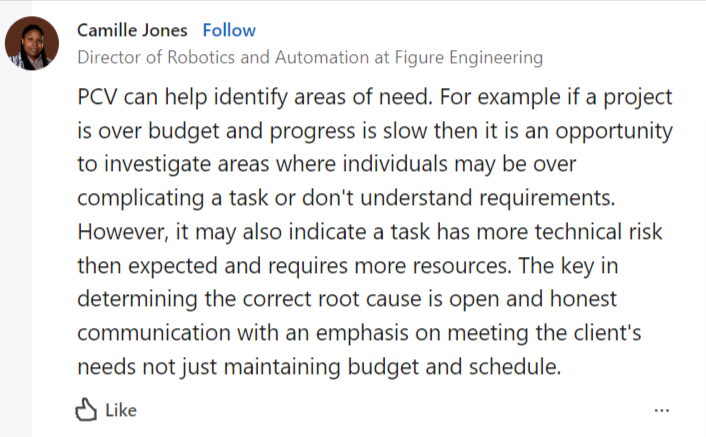
For instance, the absence of an efficient asset management system may lead to machinery hoarding, consequently resulting in overpaying for equipment rental.
The final step is, naturally, to try and get the expenses back under control.
Depending on the situation, this may involve using alternative, cost-effective materials, implementing more efficient construction methods, or employing equipment management software to track and optimize machinery utilization.
To get insight into the most effective course of action, it’s best to consult other project stakeholders.
Leveraging their expertise can be the key to solving these often costly problems.
Overall, consistently following these steps empowers project teams to identify and address issues promptly, preventing them from escalating.
This ensures that the project stays within the budget, sticks to the established schedule, and upholds the required standards of quality.
Cost Reporting
The main focus of cost reporting is assessing the project’s well-being from a financial standpoint.
Conducted on either a monthly, weekly, or sometimes even daily basis, these reports primarily concentrate on the expenditures during a specific period, encompassing:
- Legal fees
- Rent
- Sanitation
- Permit fees
- Agency costs
- Suppliers
- Overtime
- Salaries
They also offer predictions on future expenses and compare the current financial performance to the budgeted costs.
As such, they not only foster transparency and trust among everyone involved in the project, but also provide insights into possible risks, shed light on cost-saving opportunities, and help the detection of theft and fraud.
However, efficient cost reporting can be somewhat challenging.
The main hurdle during this process is obtaining reliable data about the incurred costs.
This is a problem not only because it impacts the quality of the reports themselves but also because it has the potential to affect the overall project outcomes.
Think about it: if expense reports rely on poor data, decisions based on them will be misguided and lead to unfavorable project results.
In fact, research has already shown that 14% of costly global rework stems precisely from inaccurate data.
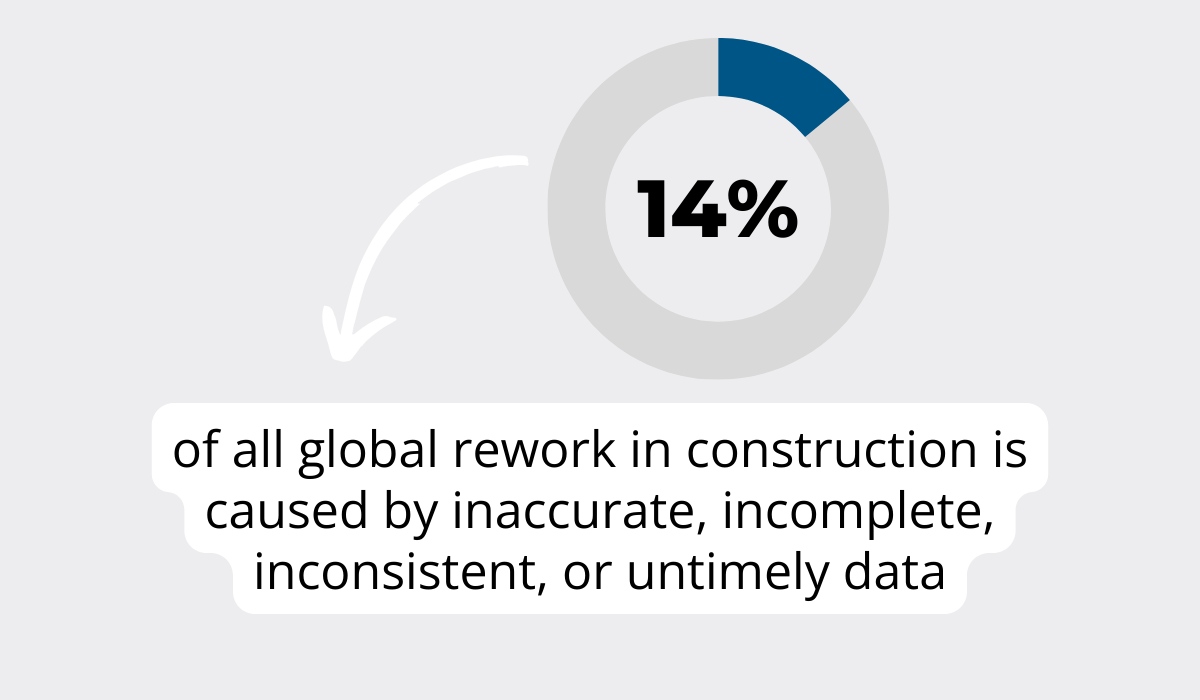
This statistic only goes to show just how expensive poor data can truly be.
Still, the fact remains that, in construction, trustworthy information is sometimes hard to come by.
Data entry errors such as typos, dependence on outdated information sources, software integration issues, and missing datasets can all compromise the accuracy of cost reports.
Luckily, modern construction-industry-specific digital systems provide a solution to this problem.
Take, for example, GoCodes.
It’s an equipment management system that, with its Enterprise Reporting feature, automatically tracks and compiles equipment-related costs (along with other useful information), and then presents them through customized reports.
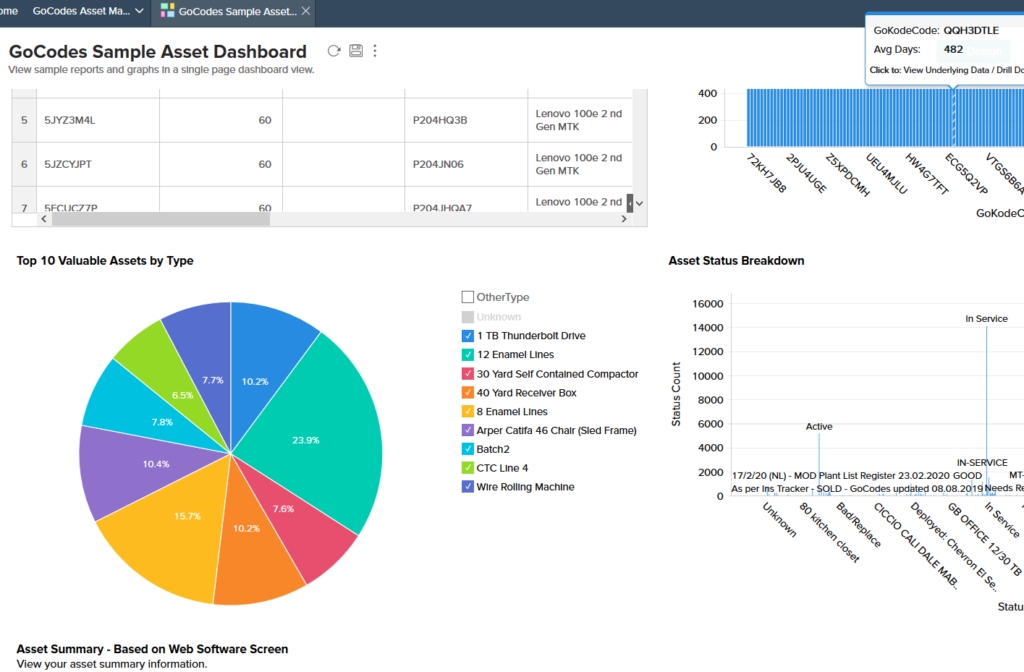
With such tools, you make sure that the data you use is fresh, precise, and can be incorporated into final cost reports without the fear of presenting unreliable information to stakeholders.
In any case, when it comes to cost reporting, commitment to accuracy is non-negotiable.
Only that way can you ensure that these reports actually serve their intended purpose and steer projects in the right direction.
Change Order Management
A change order is an agreement between a project owner and a contractor regarding modifications to the original terms of a project.
Various situations can trigger the need for a change order, including:
- Shifts in the project scope
- Unexpected site conditions
- Inaccurate drawings
- Inability to access certain resources
- Client’s change request
Effectively managing change orders involves identifying, defining, and systematically tracking them in a manner acceptable to all parties involved.
Inefficiencies in this process can result in delayed responses, lost profits, unplanned downtime, scope creep, and even reputational damage.
For example, inadequate time allocated to assessing the impact of a change order can lead to rushed work, resulting in low-quality and unsafe structures.
This, in turn, may give rise to worker injuries and significant delays.
Similarly, a lack of communication in the change order management process can lead to disputes between project stakeholders.
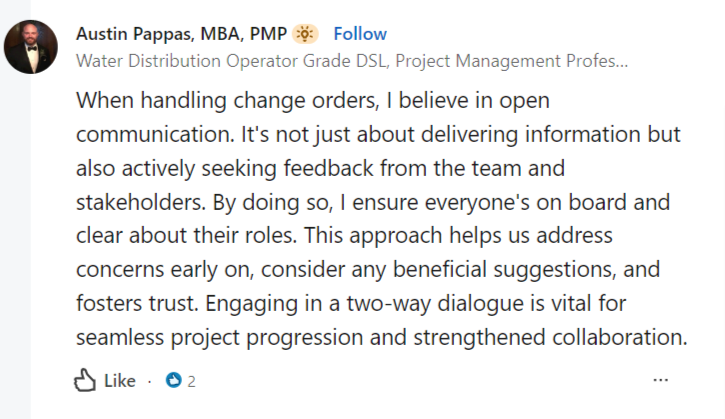
After all, contractors, subcontractors, and clients may all have different expectations and interpretations of these contract alterations.
It’s necessary to have everyone on board at all times to prevent any legal disputes.
This leads us to a question: what makes change order control efficient?
Well, to put it simply, it’s all about having a system in place that addresses these key questions:
- If both parties cannot agree on change orders, what is the procedure for resolving disputes?
- How much time should the contractor take to assess the request and propose a counterproposition?
- At what stage in the process can changes be requested?
- What steps should be followed during the change order process?
In short, handling change orders revolves around establishing streamlined workflows for documentation management, request analysis, communication, and request approval.
Transparency, preparedness, and strict protocols are key in this context, preventing projects from descending into chaos, overspending, delays, and overall suboptimal outcomes.
Conclusion
Each of the components of cost management is unique, presenting its own set of challenges and benefits.
Nevertheless, they all converge towards a common goal: the successful completion of the project.
The key takeaway here is clear—thoroughness is imperative at every stage of the project lifecycle.
Whether it’s estimating and budgeting in the preconstruction phase or overseeing costs and handling change orders during the ongoing project, you must establish clear and effective procedures to ensure the utmost accuracy.
However, don’t be overly concerned if things deviate from the initial plan.
In construction, changes are inevitable.
The best thing you can do is to remain vigilant, keep an eye on potential risks, and maintain open communication with stakeholders.
This is, after all, what cost management is all about.