A big part of good asset management boils down to properly tracking your construction tools across multiple sites and projects.
Construction firms that track their assets unlock numerous benefits, starting with improved efficiency and cost savings.
On the other hand, those who don’t, struggle to meet project deadlines while watching their profits drain.
Whether you’re already tracking your tools or just starting, this article will give you expert pointers on how to step up your asset management game and drive more success.
In this article...
Enable GPS Tracking for High-Value Equipment
Tracking systems that enable GPS tracking give you real-time location data on all your critical, high-value assets, enhancing both security and utilization.
While there are several ways you can keep track of your key equipment, construction companies generally adopt GPS-enabled systems for these reasons:
As the asset’s value increases, so do the risks and potential losses, particularly due to theft or inadequate maintenance.
The 2024 report by UK-based security firm BauWatch confirms the staggering increase in construction equipment theft, showing that one-fifth of construction workers experienced theft multiple times in just one year.
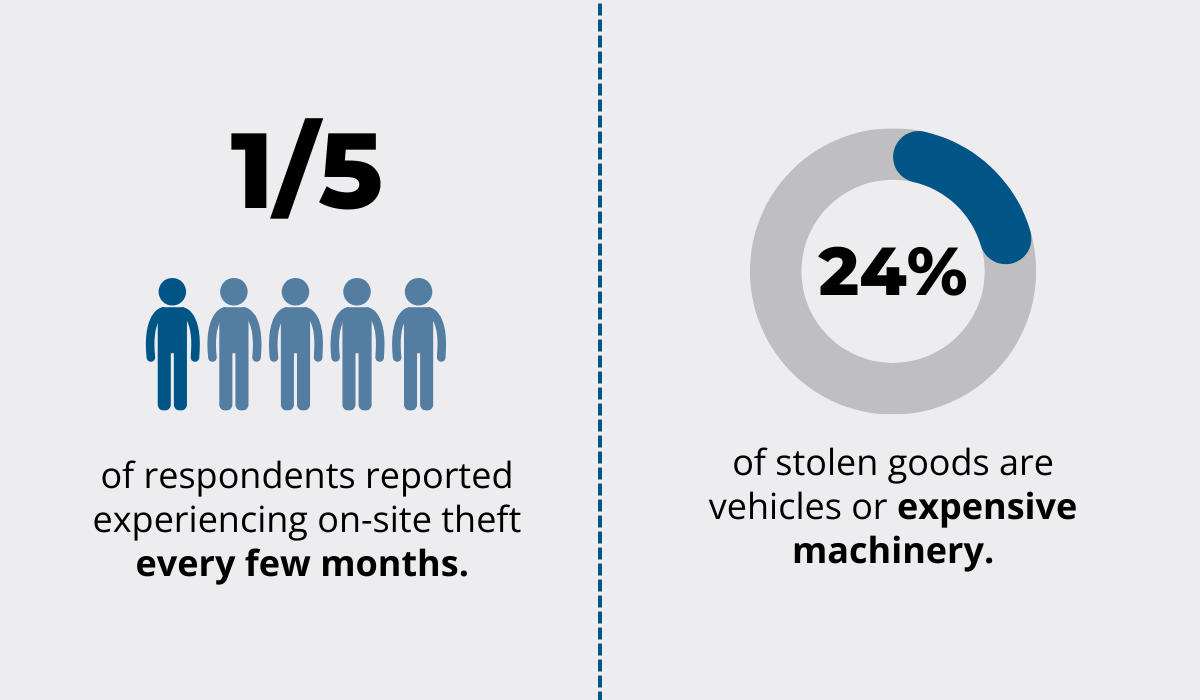
Moreover, expensive machinery was among the most common targets.
This is illustrated by a recent bust in Maryland, U.S., where law enforcement managed to seize and recover 1 million in stolen construction equipment.
The haul included 2 excavators, 13 stolen skid steers, and numerous trailers.
The comment by the police department’s Craig Winegardner on why the crime happened in the first place is particularly telling.
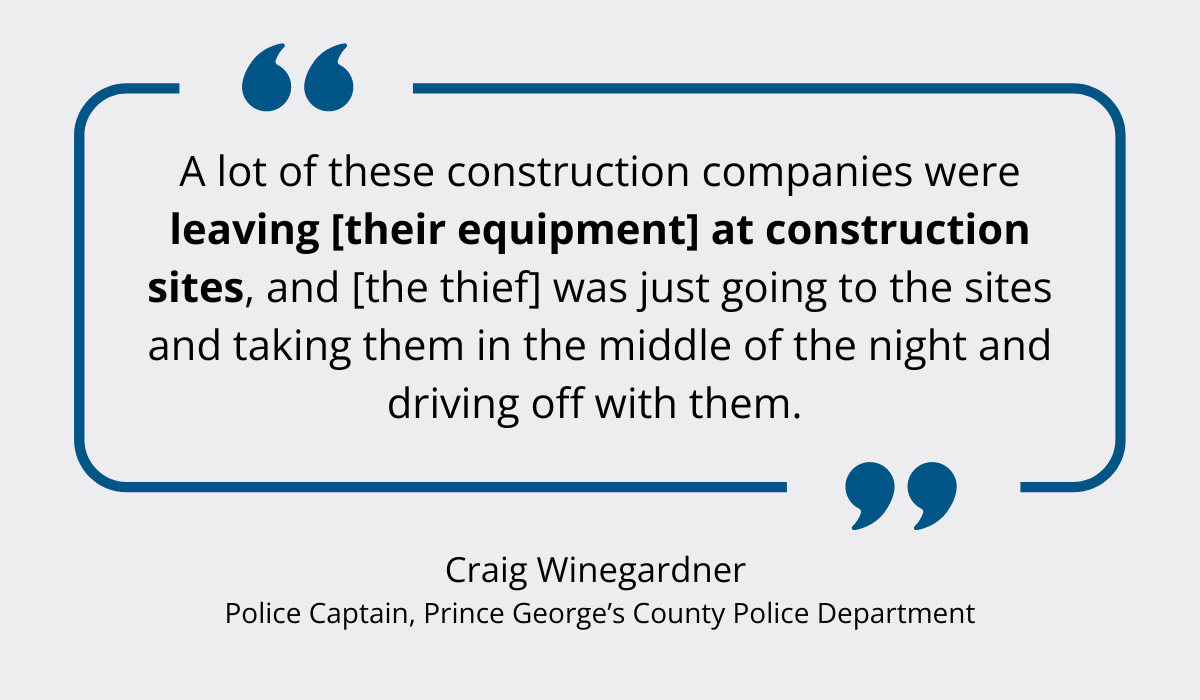
Lax on-site security and the lack of asset-tracking solutions allowed the thief to operate for a long time.
Luckily, the story had a happy ending for several construction companies whose equipment was stolen.
But if you don’t want to leave things to chance, and risk suffering debilitating financial losses, you need to consider equipping your high-value assets with GPS tracking.
For starters, there are two main tracking options:
- Plug-and-play GPS trackers that go into the vehicle’s OBD2 port
- Battery-powered GPS trackers that you attach to the asset
Both types of trackers enable minute-by-minute location updates while helping you record engine hours and mileage, and keep track of equipment usage in general.
But there are differences.
Simply put, OBD trackers are more affordable and give you a wealth of information on vehicle health and use, but are not meant to counter theft.
Meanwhile, battery-powered GPS trackers are tamper-proof and designed to boost security while making asset retrieval easier.
OBD Trackers | Battery-Powered Trackers | |
---|---|---|
Power Source | Plugged directly into the vehicle’s OBD2 port | Wireless battery (up to 10 years lifespan), mounted on the asset |
Detection & Durability | Easy to access/remove, not as durable | Concealed and tamper-proof |
Ease of Use | Plug-and-play for vehicle diagnostics | Flexible mounting options for different assets |
Cost & Application | More cost-effective, ideal for vehicle tracking | More expensive, but robust for asset security |
The installation process is fairly simple for both options, so it all comes down to your primary business needs.
What’s for sure is that not using GPS tracking means you’re missing out on valuable insights, but also putting yourself at risk.
Use RFID or QR Systems for Small Tools and Inventory
Automated tagging systems like RFID tags and QR Codes are perfect for labeling and tracking small tools and the rest of your inventory.
Since these items are frequently moved or shared among teams, these tracking technologies are designed to improve accountability and minimize losses while staying cost-effective.
The RFID system uses radio waves to enable fast, remote scanning without making physical contact with the RFID tag.
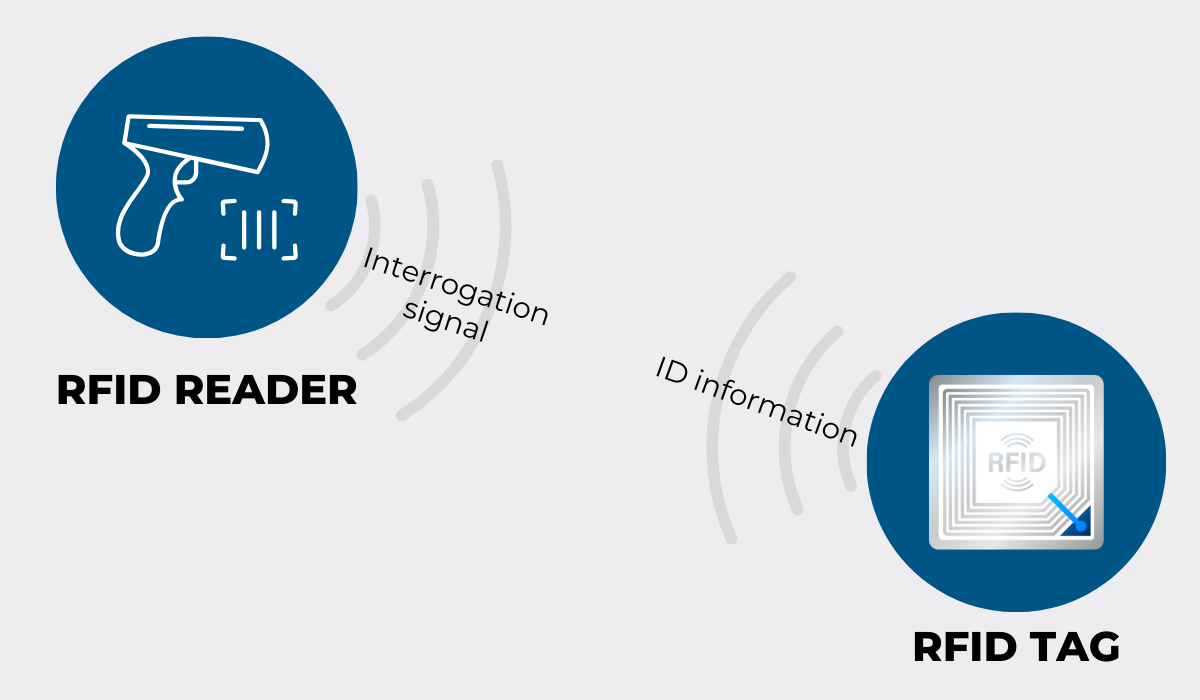
In other words, you can pinpoint and scan the tool’s exact location even when it’s out of sight, which makes it extremely convenient in crowded indoor environments.
However, you need to be prepared for the high upfront costs.
With the price of a single RFID reader close to $3,000, businesses are likely to spend over $100,000 to get an RFID system up and running.
Another option for simplifying asset-tracking processes is QR code labels.
They’re cost-effective and easy to deploy quickly, with customizable labels that fit even the smallest tools.
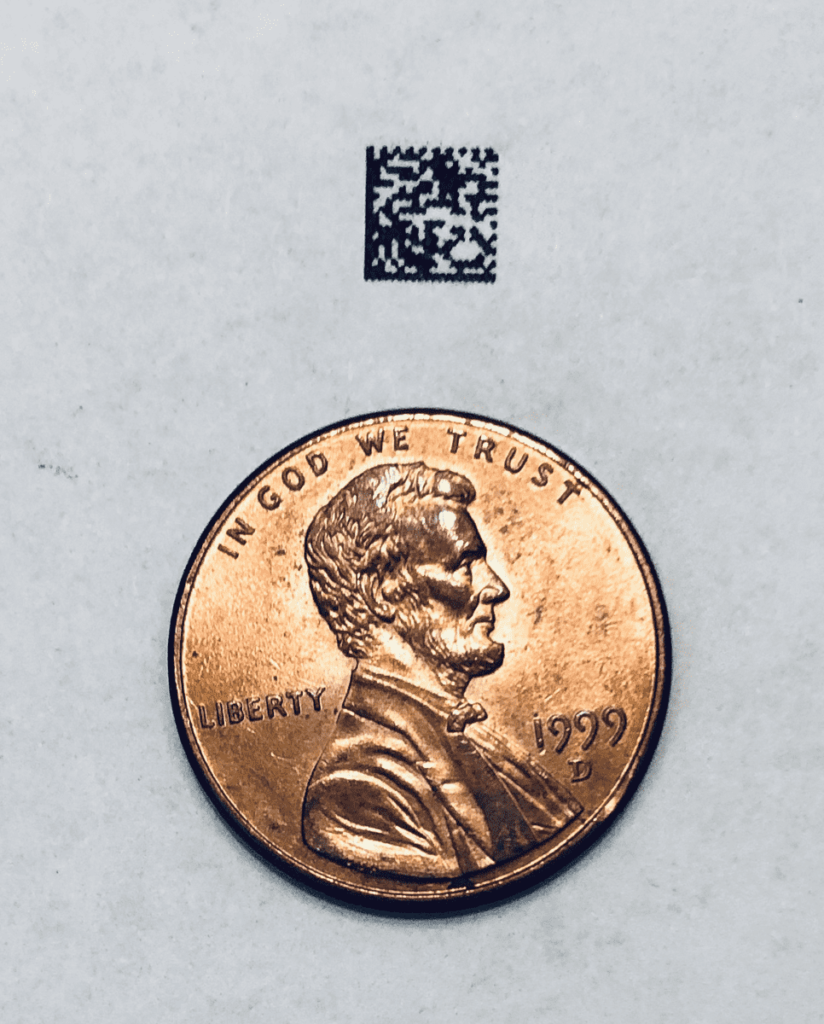
Each QR code stores encoded information that links to a database with key information on all assets, from usage history and maintenance records to purchase dates.
The tags can be scanned with a mobile app or a handheld scanner, but unlike RFID tags they require direct contact.
Nevertheless, one huge advantage of QR codes is that they provide the geographical position of moving items when scanned with a GPS-enabled device.
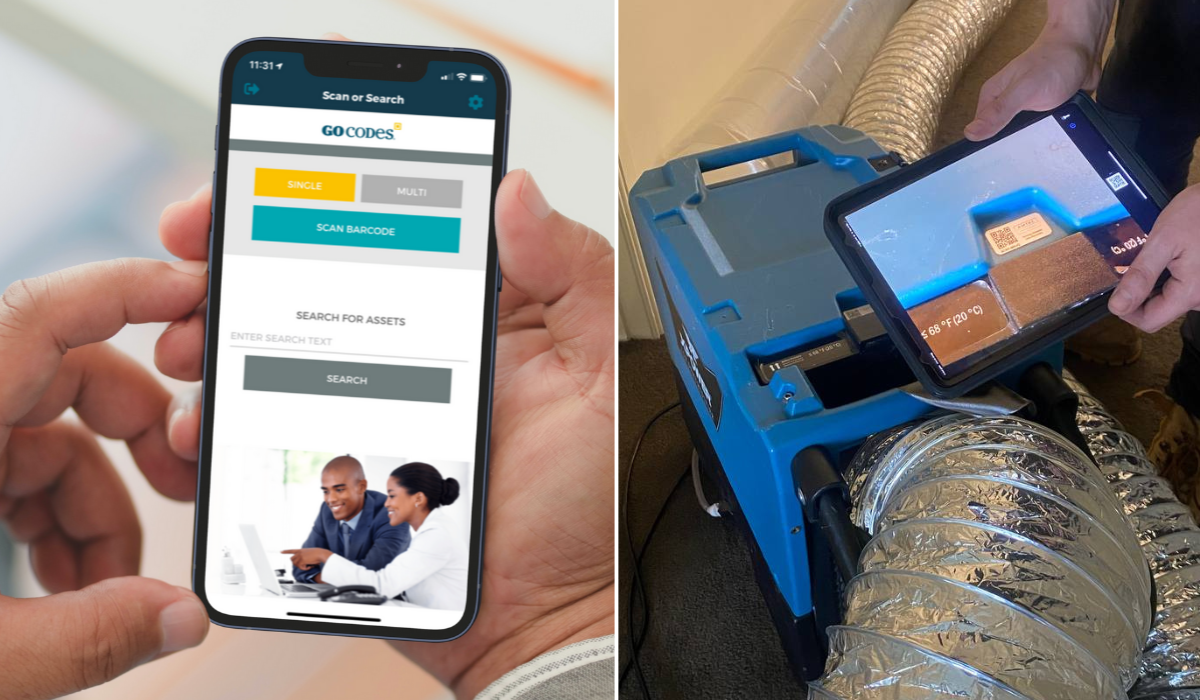
RFID tags lack this capability which is essential for businesses that frequently move equipment between locations.
Here’s a quick breakdown of the main characteristics.
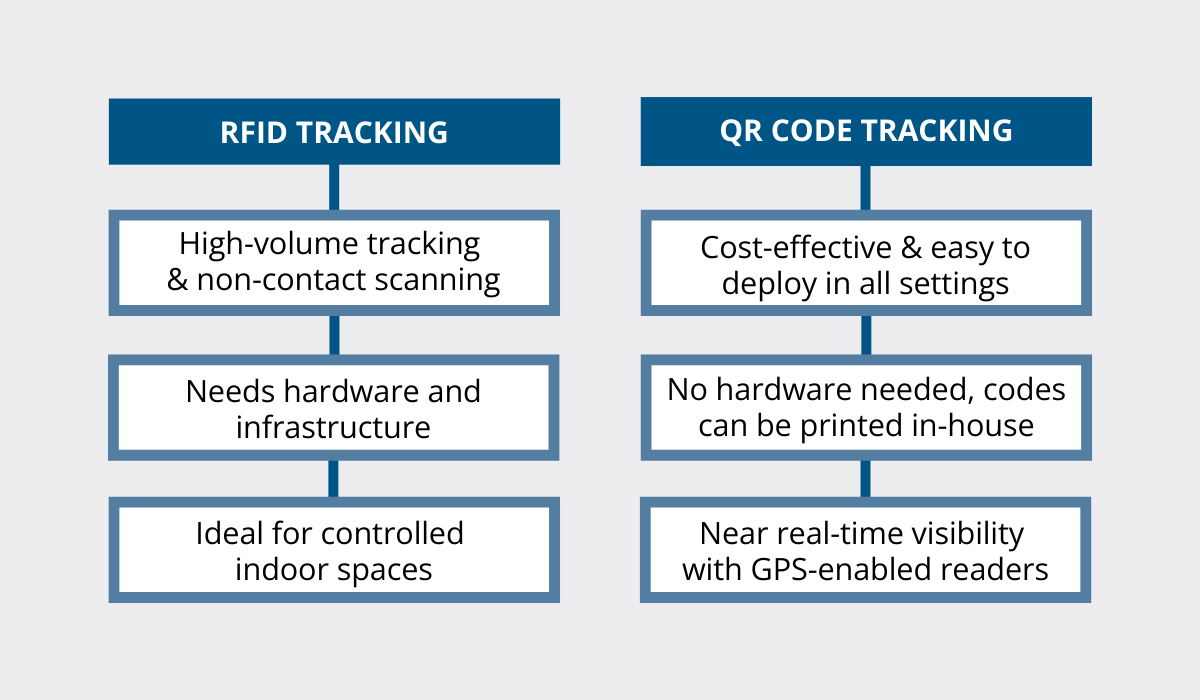
The choice between these two technologies depends on your asset management needs, but once you’ve made it, here’s how the setup will look.
First, you need to assign RFID tags/QR code labels to each tool or batch of materials. Be sure to choose the right material depending on the weather conditions.
For RFID systems, there’s the additional step of placing antennas and fixed readers at different entry points.
Once this is done, you can use RFID readers/mobile devices to scan and record the movement of all tools and equipment in and out of storage, on-site, or between locations.
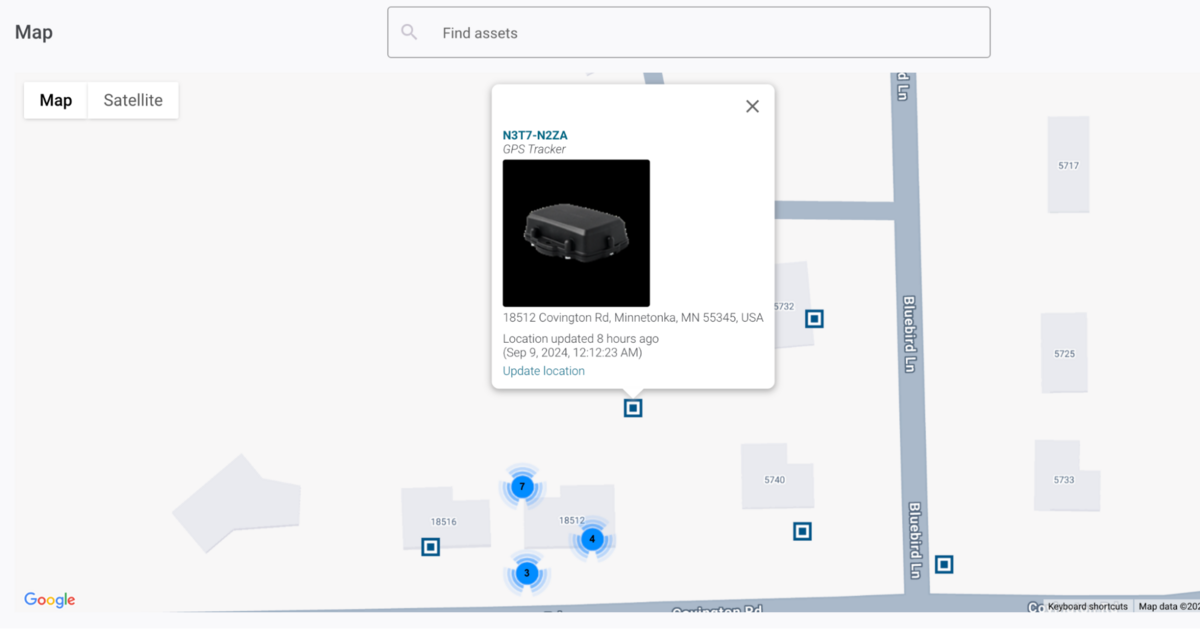
This ensures accountability which is very important because small tools are frequently misplaced or left behind at job sites.
This was also the experience of the specialty contractor J&M Keystone (acquired by ATI Restoration).
The company’s Director of Operations, Lee Sherman, explains how they got their equipment losses down from $30,000 a year to around $1,500 after adopting our asset tracking solution.
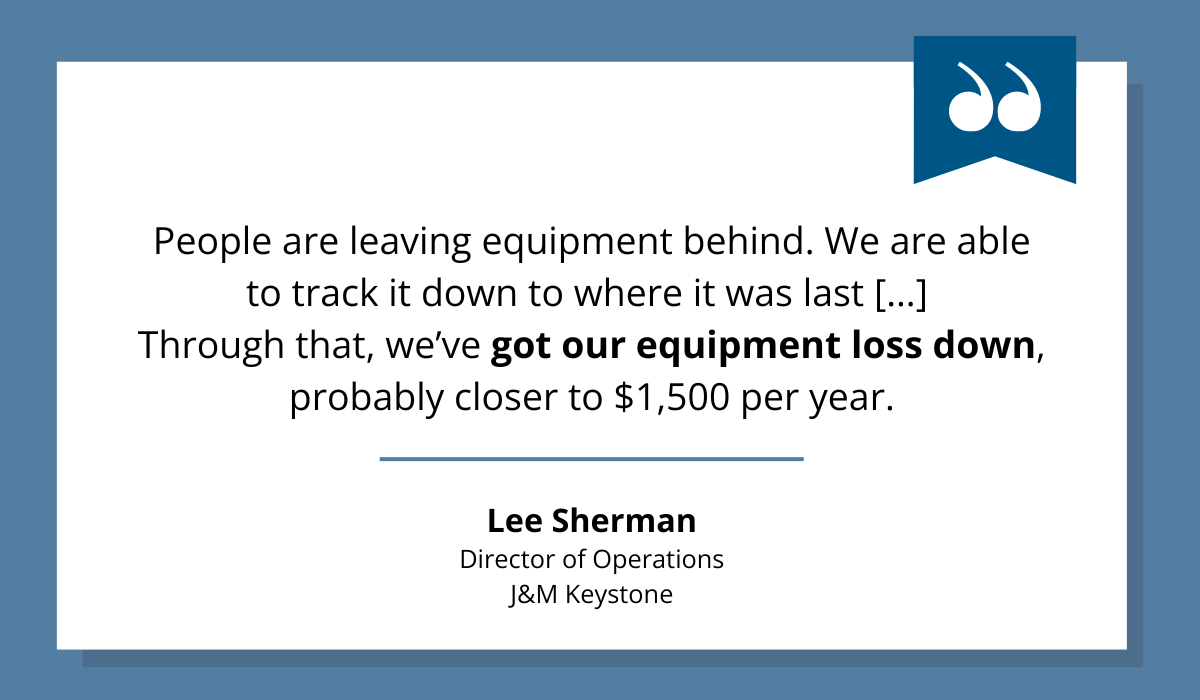
The company’s example demonstrates the impact of asset tracking systems and a substantial return on investment.
You can calculate the potential ROI for your own business by using this free calculator: Asset Tracking ROI Calculator
Still, different tool tracking benefits are even more noticeable through integrations with other software, which brings us to our next section.
Integrate Asset Tracking with Project Management Software
Integrating asset tracking with project management software gives you a comprehensive view of when, where, and how your assets are used across multiple projects.
Project management software is essential for scheduling tasks and tracking the entire project lifecycle, but this can’t be done effectively without the data on relevant assets.
That’s because integrating these tools creates a centralized information hub or a common data environment.
And precisely the lack of a common data environment was one of the findings of FMI’s recent survey.
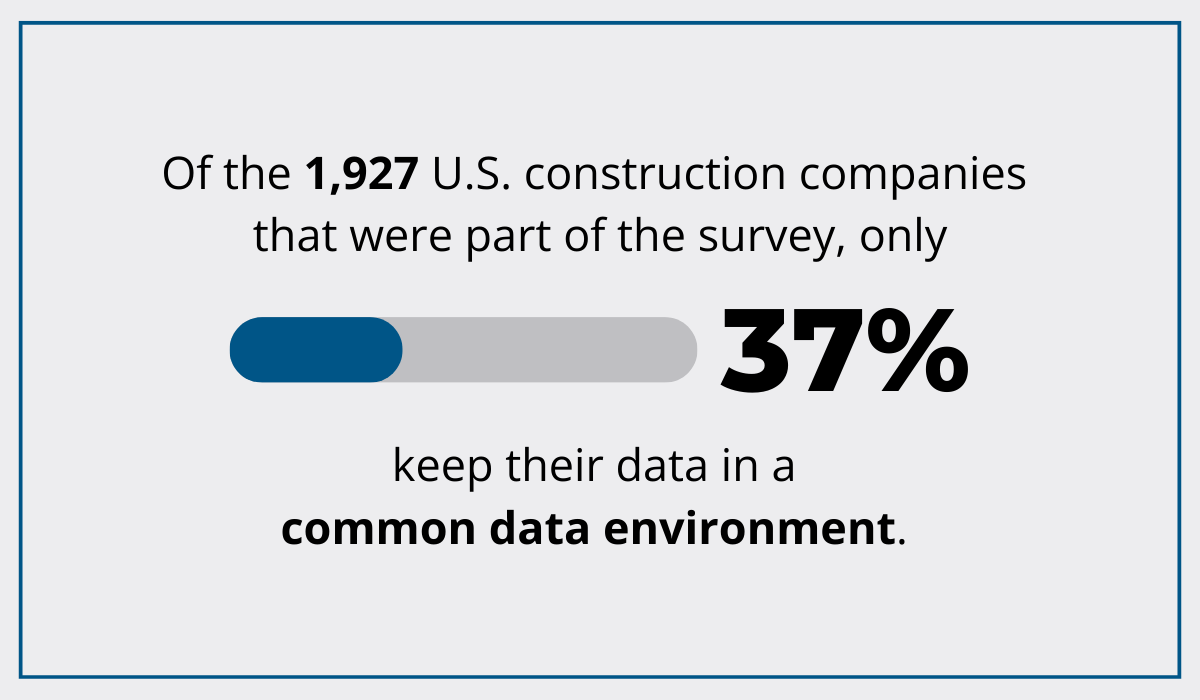
Survey respondents stressed that having a single source of truth, or a few complementary software solutions, enables a steady flow of project data and provides visibility.
Therefore, integrating asset tracking with project management software ensures exactly that, giving you easy access to key asset information, namely:
- status,
- location, and
- availability.
Real-time equipment insights are essential for project managers because the lack of alignment between resource availability and scheduling quickly leads to bottlenecks and costly delays.
Even a simple check-in process creates a big difference, as LPR Construction’s Director of Equipment and IT, Thad Lutgens, explains.
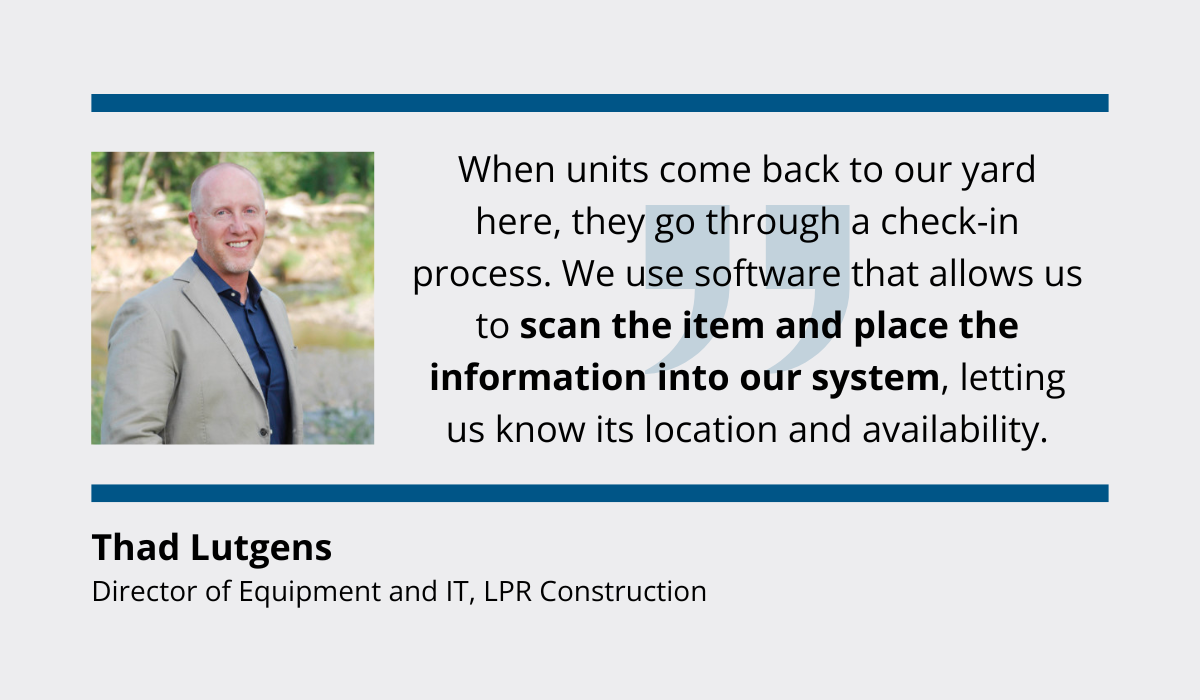
Having all the relevant information at your fingertips increases operational efficiency and productivity, leading to better project outcomes.
Now, how do you make this happen?
There are two ways to integrate asset tracking with project management software: one is via API, and the other is through pre-made integrations.
API integration allows one system to transfer data to another and automate processes.
The result is a tailored solution that can adapt to evolving needs and a wide range of systems.
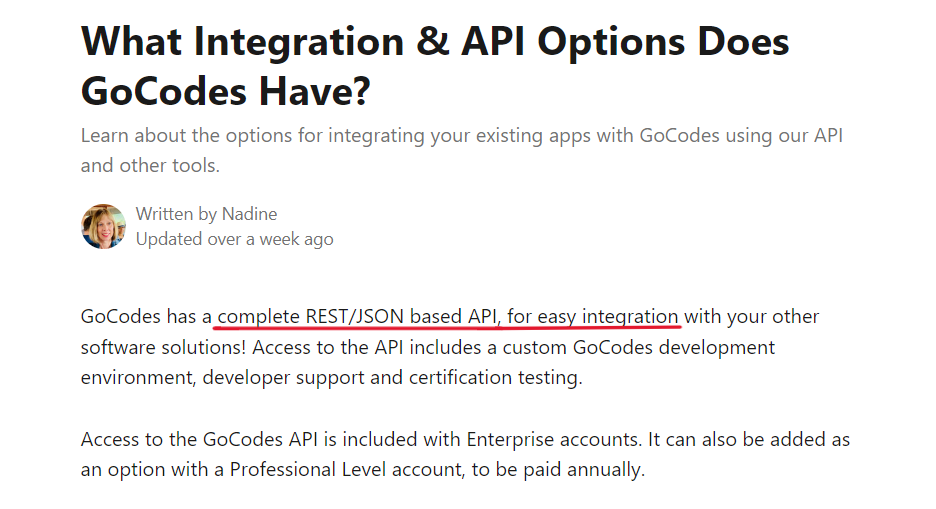
While API can help you meet specific needs and streamline data exchange, keep in mind that deployment and maintenance can be time-consuming, and require technical expertise.
Premade integrations are easier and quicker to implement and are typically more cost-effective to maintain.
Here are some integrations that one asset management solution offers.
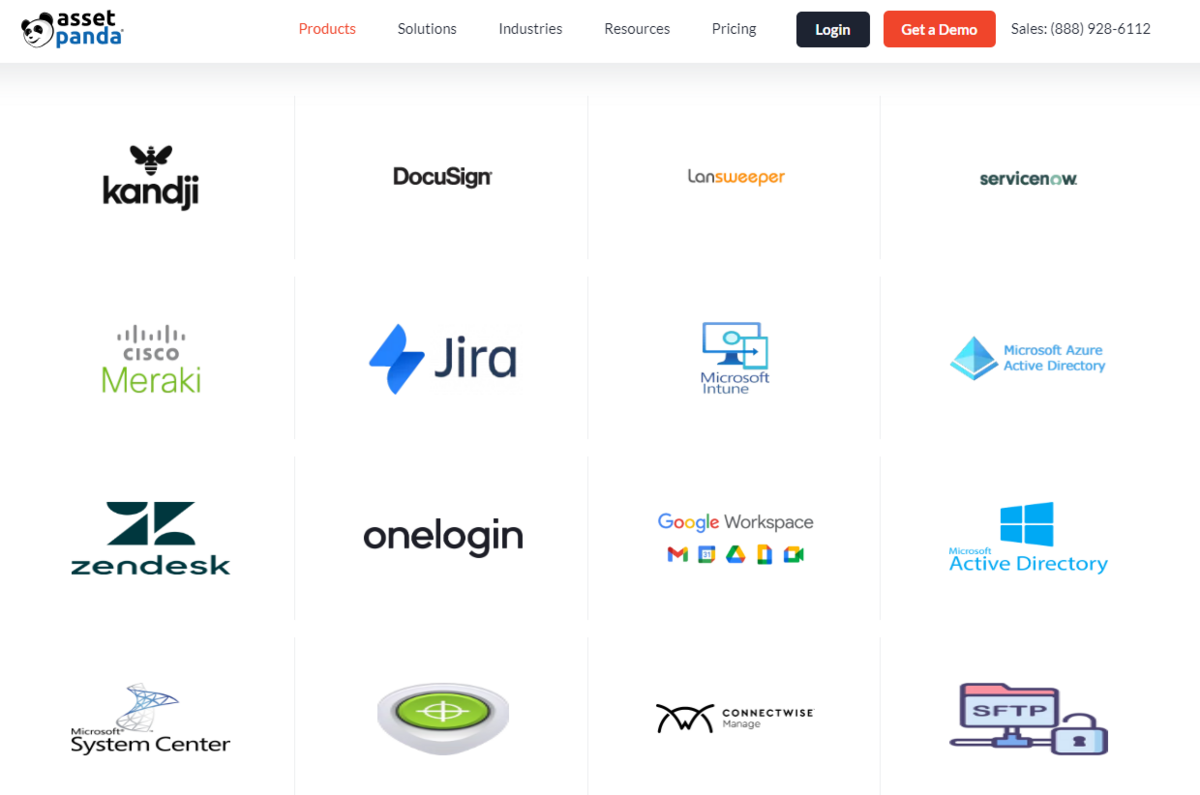
It’s important to note that premade integrations lack customization and flexibility, which can limit functionality and leave some of your needs unanswered.
Besides these two options, you can also explore which asset-tracking software boasts several project management capabilities.
For example, GoCodes enables you to assign assets and work orders and keep track of all ongoing and upcoming tasks and projects using the Agenda View feature.
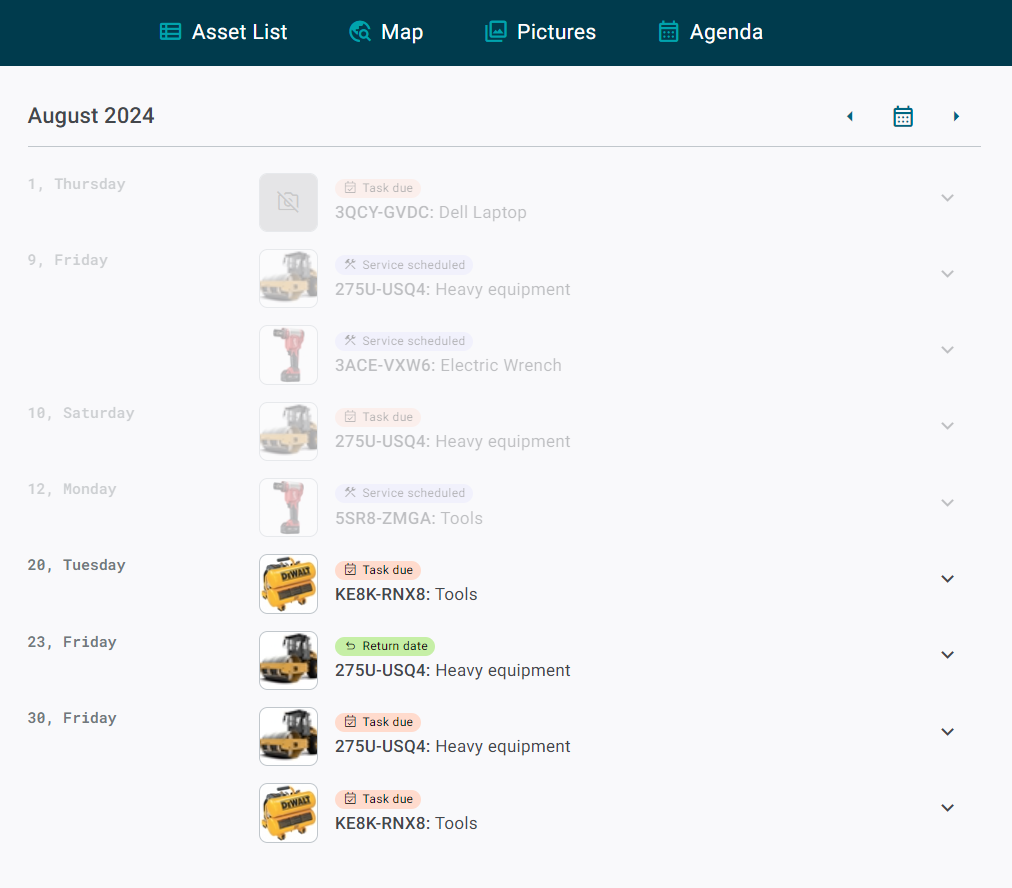
Which means it doubles as a task management tool as well.
There’s no more switching between platforms when you have everything you need in one spot.
Again, no matter which integration option or software you choose, you’re sure to benefit from improved project visibility and higher efficiency resulting from it.
Schedule Regular Maintenance Through Automated Alerts
Maintenance alerts or notifications are a crucial feature of asset management software, enabling you to automate service tasks and establish continuity in your maintenance practices.
They ensure regular maintenance which prolongs the lifespan of your equipment and reduces the risk and costs of unexpected downtime.
Luckily, asset management software goes beyond knowing each tool’s location. It can enable managers to schedule and track the performance of maintenance tasks and manage field service requests.
Maintenance features are integral to these solutions because of the hidden costs of inadequate maintenance.
In Teletrac Navman’s 2024 Telematics survey, nearly half of the 500 construction fleet professionals cited equipment maintenance as their top expense.
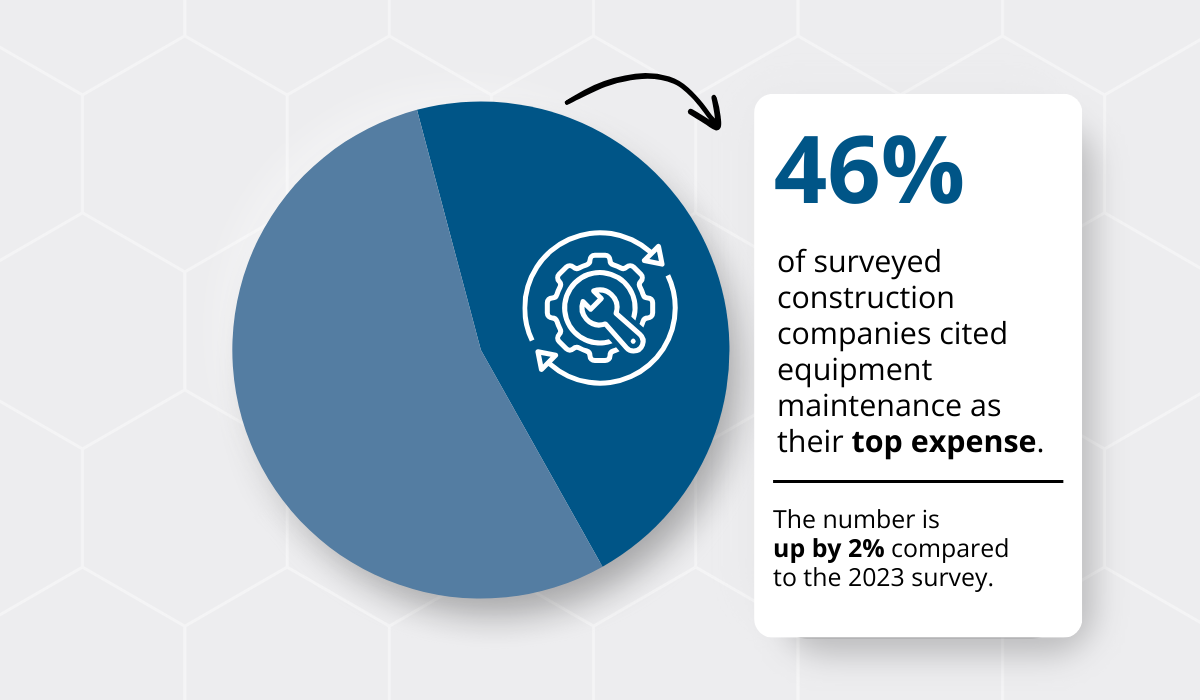
These findings underline the need for adopting regular, proactive maintenance practices to minimize repair costs and prevent equipment breakdown.
And you can start immediately by setting up automated alerts for upcoming maintenance tasks.
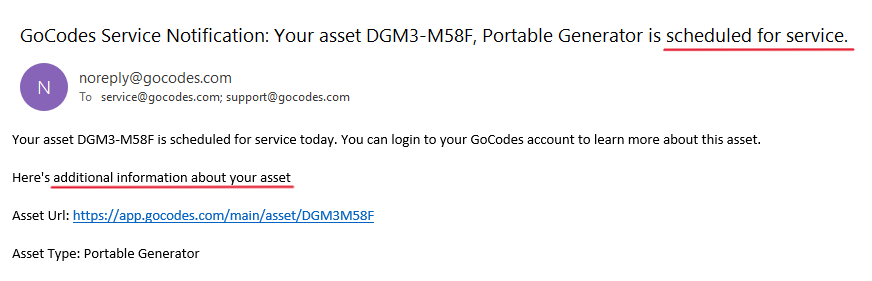
Getting a service notification ensures that no asset is overlooked, even if it hasn’t been used for a longer time.
Now, there are five common types of maintenance triggers:
- Time-based
- Usage-based
- Event-based
- Condition-based
- Breakdown
Time-based maintenance triggers are based on a set schedule and are best for ensuring regular safety checks or similar tasks that don’t depend on equipment usage.
You won’t use them to determine when you should change oil because this depends on usage factors like engine hours, mileage, and general wear and tear.
In a nutshell, time triggers ensure that the assets stay in good condition, but they can also help you catch and fix small problems before they escalate.
On the other hand, usage-based (or meter-based) triggers are set up to ensure maintenance is done after the equipment has been in use for a certain number of hours.
For example, cabin air filters are typically replaced every 1,000 to 1,200 hours, and it wouldn’t make sense to do maintenance at fixed periods.
Additional triggers can be configured based on specific events or emerging conditions, but the idea is to set up alerts in a way that corresponds with equipment specifications, safety concerns, and operational impact.
Daksh Prajapati, Assistant Startup and Commissioning Manager at the oilseed and biofuel technologies supplier Desmet puts it like this:
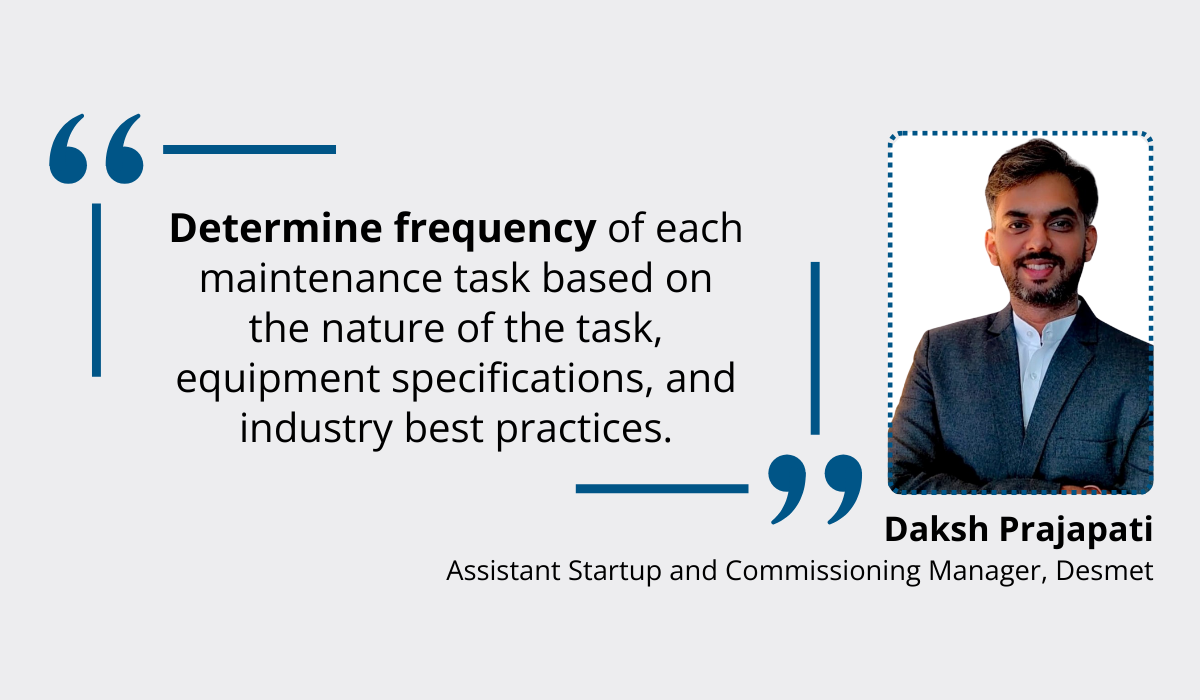
To sum up, regular maintenance offers a surefire way of controlling costs and boosting productivity, and alerts are one of the key tools you can use to do so.
Leverage Data Analytics for Proactive Asset Management
Analyzing available data paves the way for a more proactive approach to asset management.
Data helps construction firms see beyond the present conditions and identify their assets’ usage patterns, performance trends, and maintenance needs.
And it seems that a good percentage of construction companies are already well aware of that.
Currently, 68% of E&C firms rely on advanced data analytics across different processes.
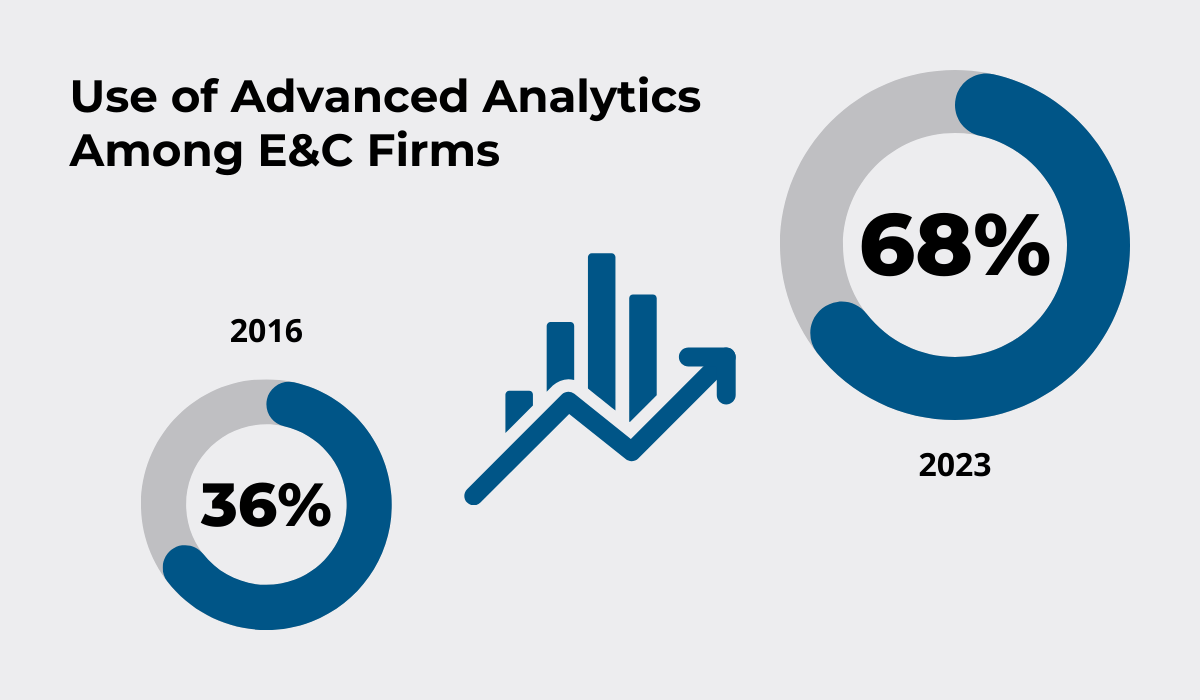
And these figures have nearly doubled compared to just a 36% adoption rate in 2016.
Improved decision-making and better outcomes are among the main reasons why KPMG’s 2023 global construction survey shows a noticeable jump in advanced data analytics use.
Simply put, predictive analytics algorithms can identify anomalies and patterns by drawing upon historical data and real-time readings.
Data analytics expert, Leandro Araque, stresses that the key value here is the ability to act proactively and address conditions as they emerge, minimizing operational risks and losses.
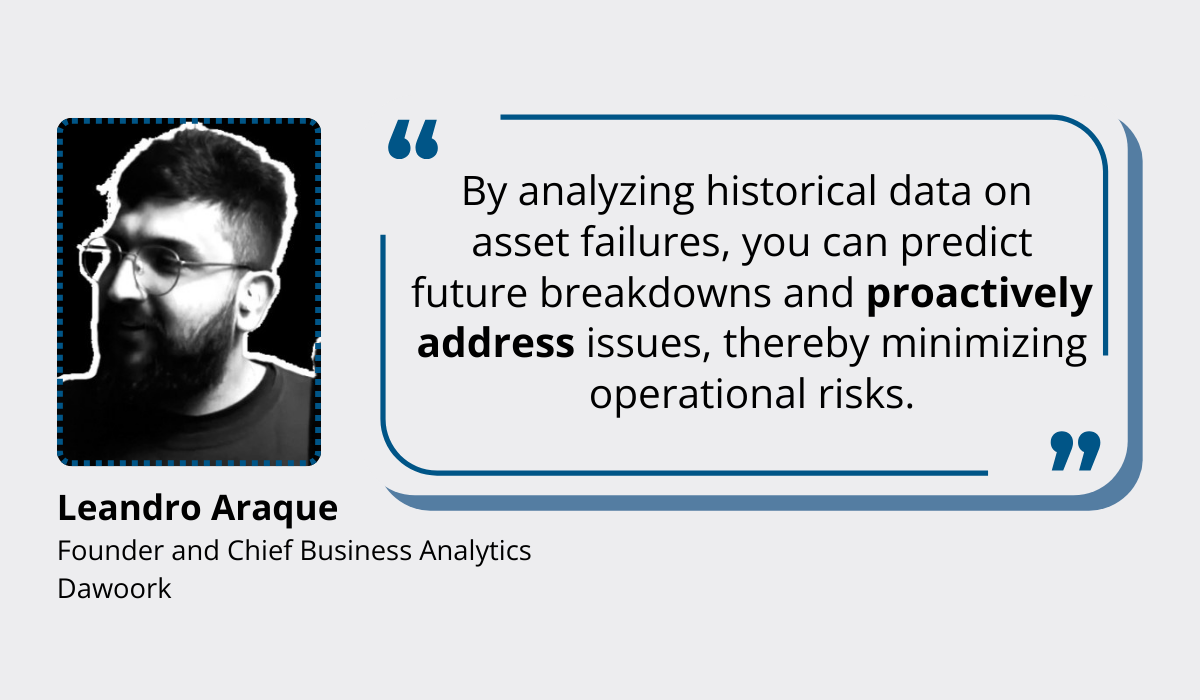
The benefits of this early-intervention approach extend beyond anticipating equipment failures and optimizing maintenance schedules.
Collecting and analyzing data on equipment utilization also maximizes operational efficiency and asset value.
With data analytics, construction firms can easily identify assets that are underutilized or idle.
After assessing each situation, you can make decisions on redeployment, renting, or disposal.
At the same time, making note of which assets are overutilized promotes informed decisions on acquiring new or used equipment, ultimately reducing unnecessary expenditures.
All in all, data analytics are invaluable to construction businesses today because they guide your maintenance efforts, boost performance, and help you cut down on costs.
Conclusion
Today, not having control over your assets is simply unacceptable.
Without comprehensive, ongoing monitoring of all equipment—from high-value assets to small tools—you’re risking scheduling clashes, equipment loss, breakdowns, and costly delays.
Embracing tool tracking, on the other hand, will transform your operations and drive profit.
It starts with choosing the right tracking technologies, teaching the team to use new software, and monitoring the findings for improvement opportunities.
The road ahead may not be easy, but the rewards are huge.
So, time to take the leap and begin your journey to smarter asset management!